In-Flight Loss of the Left Main Landing Gear Door, Collision of Door with Fuselage
Total Page:16
File Type:pdf, Size:1020Kb
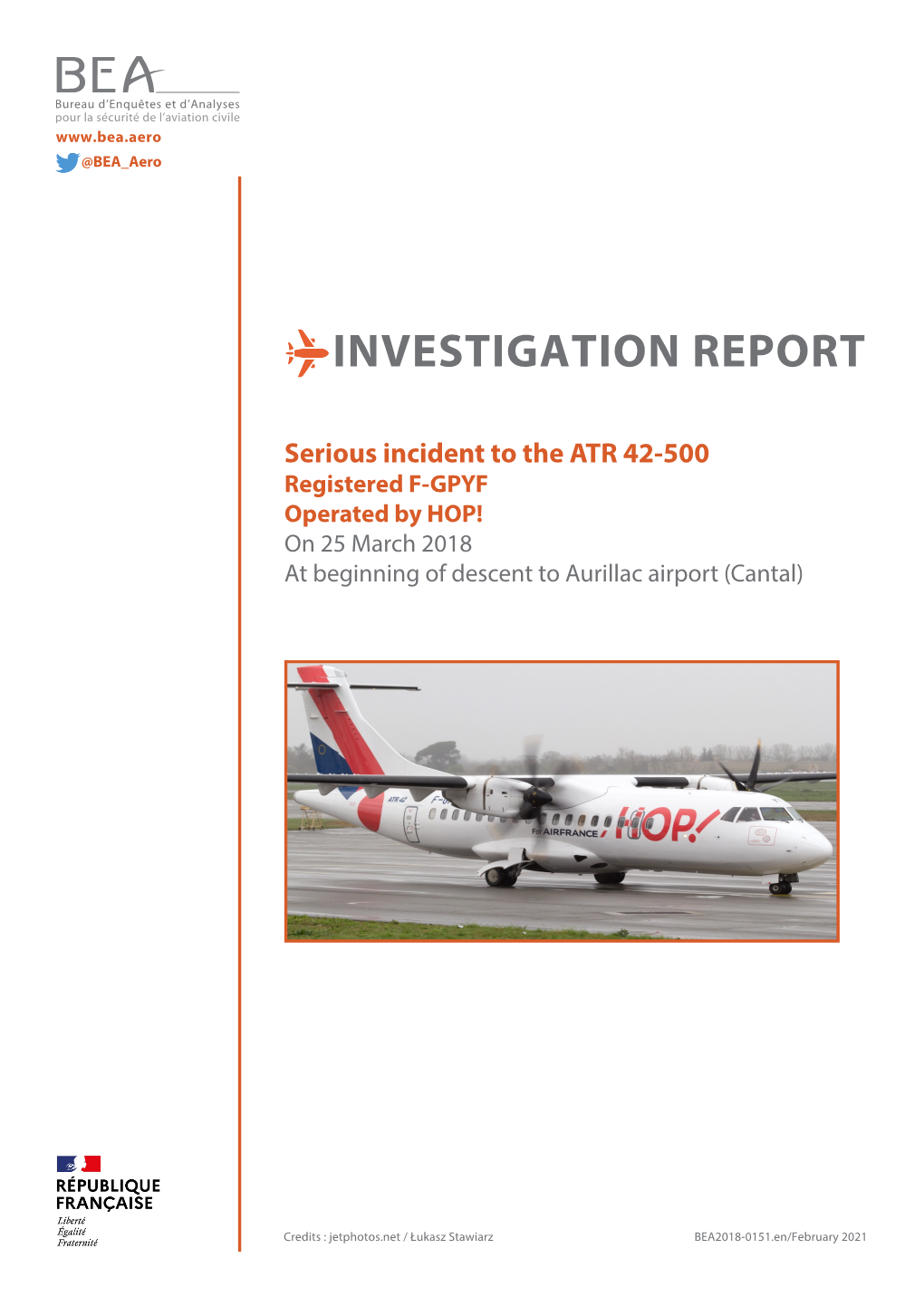
Load more
Recommended publications
-
WORLD AVIATION Yearbook 2013 EUROPE
WORLD AVIATION Yearbook 2013 EUROPE 1 PROFILES W ESTERN EUROPE TOP 10 AIRLINES SOURCE: CAPA - CENTRE FOR AVIATION AND INNOVATA | WEEK startinG 31-MAR-2013 R ANKING CARRIER NAME SEATS Lufthansa 1 Lufthansa 1,739,886 Ryanair 2 Ryanair 1,604,799 Air France 3 Air France 1,329,819 easyJet Britis 4 easyJet 1,200,528 Airways 5 British Airways 1,025,222 SAS 6 SAS 703,817 airberlin KLM Royal 7 airberlin 609,008 Dutch Airlines 8 KLM Royal Dutch Airlines 571,584 Iberia 9 Iberia 534,125 Other Western 10 Norwegian Air Shuttle 494,828 W ESTERN EUROPE TOP 10 AIRPORTS SOURCE: CAPA - CENTRE FOR AVIATION AND INNOVATA | WEEK startinG 31-MAR-2013 Europe R ANKING CARRIER NAME SEATS 1 London Heathrow Airport 1,774,606 2 Paris Charles De Gaulle Airport 1,421,231 Outlook 3 Frankfurt Airport 1,394,143 4 Amsterdam Airport Schiphol 1,052,624 5 Madrid Barajas Airport 1,016,791 HE EUROPEAN AIRLINE MARKET 6 Munich Airport 1,007,000 HAS A NUMBER OF DIVIDING LINES. 7 Rome Fiumicino Airport 812,178 There is little growth on routes within the 8 Barcelona El Prat Airport 768,004 continent, but steady growth on long-haul. MostT of the growth within Europe goes to low-cost 9 Paris Orly Field 683,097 carriers, while the major legacy groups restructure 10 London Gatwick Airport 622,909 their short/medium-haul activities. The big Western countries see little or negative traffic growth, while the East enjoys a growth spurt ... ... On the other hand, the big Western airline groups continue to lead consolidation, while many in the East struggle to survive. -
To Readers of the Attached Code-Share List
TO READERS OF THE ATTACHED CODE-SHARE LIST: The U.S. Air Carrier Licensing Division’s code-share list is an informal compilation of code-share relationships between U.S. and foreign air carriers for the sole purpose of transporting passengers, mail and property. As such, it does not represent a complete compilation of all code shares e.g. cargo and mail only. New code-share relationships are continually being negotiated, and the ones reflected in the attached listing may or may not be still in place or be of a continuing nature. Similarly, the list may not reflect all existing code shares of a particular type, or all existing types of code shares. This list is not an official document of the Department of Transportation and, accordingly, should not be relied upon or cited as such. NOTE: THIS LIST IS COMPRISED OF ONLY THOSE CARRIERS WHOSE CODE-SHARE RELATIONSHIPS ARE OF A NEW OR CONTINUING BASIS. DORMANT CODE-SHARE RELATIONSHIPS TO THE EXTENT KNOWN HAVE BEEN DELETED. Block descriptions of certain code-share arrangements approved for the same term may have been compressed into one block description to conserve space. If the authorities are not new or changed, but only compressed, the compressed descriptions will not appear in bold type. Carriers must notify the Department no later than 30-day before they begin any new code-share service under the code-share services authorized. This report is current through March 31, 2019. Changes from the previous reports are noted in bold type. Regional carriers operating for for large carriers (e.g. -
Are European Regionals' Successful Days Numbered?
2013 Are European ReJLRQDOV· Successful Days Numbered? Copyright @ 2013 PROLOGIS AG & ch-aviation GmbH Authors: All rights reserved. This study or any portion thereof may not be reproduced or used in any manner whatsoever Hanna Schaal (PROLOGIS) without the express written permission of the publisher [email protected] except for the use of brief quotations embodied in critical Max Oldorf (ch-aviatIon) reviews and certain other noncommercial uses permitted by [email protected] copyright law. $UH (XURSHDQ 5HJLRQDOV· Successful Days Numbered? 33.33% of all regional carriers in Europe went out of business between 2008 and today, nearly one fourth of the employees lost their jobs. PROLOGIS and ch- Figure 1 DYLDWLRQKDYHVFUXWLQL]HG(XURSH·V regional airline market. 'RHVQ·W LW VRPHWLPHV IHHO OLNH (XURSH·V UHJLRQDO DLUOLQHV· PDUNHW H[LWV DUH as FRPPRQ DV WKHLU HQWULHV" 'RQ·W \RX occasIonally wonder If thIs Industry still bears any potential? In order to gaIn clarIty In thIs matter, PROLOGIS and ch- Figure 2 aviation conducted a study of the European regIonal market, comparIng The Affiliates ² Dwindling data from 2008 with data from 2013. Partnerships The results are quIte frIghtenIng: 44 new It all started In the early days with the aIrlInes were founded from 2008 on, 22 traditional regIonal carrIer model, whIch of them have already vanIshed. The Is still very popular today. AffIlIated overall mortalIty rate was 33.33% (see DLUOLQHV VXSSO\ RU ¶IHHG· ODUJH QHWZRUN Figure 1). But the most concernIng FDUULHUV· KXEV ZLWK SDVVHQJHUV IURP number Is probably a job loss rate of 23 small, nearby regIonal aIrports. -
World Air Transport Statistics, Media Kit Edition 2021
Since 1949 + WATSWorld Air Transport Statistics 2021 NOTICE DISCLAIMER. The information contained in this publication is subject to constant review in the light of changing government requirements and regulations. No subscriber or other reader should act on the basis of any such information without referring to applicable laws and regulations and/ or without taking appropriate professional advice. Although every effort has been made to ensure accuracy, the International Air Transport Associ- ation shall not be held responsible for any loss or damage caused by errors, omissions, misprints or misinterpretation of the contents hereof. Fur- thermore, the International Air Transport Asso- ciation expressly disclaims any and all liability to any person or entity, whether a purchaser of this publication or not, in respect of anything done or omitted, and the consequences of anything done or omitted, by any such person or entity in reliance on the contents of this publication. Opinions expressed in advertisements ap- pearing in this publication are the advertiser’s opinions and do not necessarily reflect those of IATA. The mention of specific companies or products in advertisement does not im- ply that they are endorsed or recommended by IATA in preference to others of a similar na- ture which are not mentioned or advertised. © International Air Transport Association. All Rights Reserved. No part of this publication may be reproduced, recast, reformatted or trans- mitted in any form by any means, electronic or mechanical, including photocopying, recording or any information storage and retrieval sys- tem, without the prior written permission from: Deputy Director General International Air Transport Association 33, Route de l’Aéroport 1215 Geneva 15 Airport Switzerland World Air Transport Statistics, Plus Edition 2021 ISBN 978-92-9264-350-8 © 2021 International Air Transport Association. -
Bulletin Statistique Trafic Commercial Annee 2002
ãáåáëí≠êÉ=ÇÉ== äÛ°èìáéÉãÉåí== ÇÉë=qê~åëéçêíë== Çì=içÖÉãÉåí= = Çì=qçìêáëãÉ= Éí=ÇÉ=ä~=jÉê= = = = = = = = = ÇáêÉÅíáçå== Ö¨å¨ê~äÉ= ÇÉ=äÛ^îá~íáçå= ÅáîáäÉ= = ÇáêÉÅíáçå== ÇÉë=qê~åëéçêíë= ~¨êáÉåë = ëçìëJÇáêÉÅíáçå= ÇÉë=¨íìÇÉë= ¨ÅçåçãáèìÉë= Éí=ÇÉ= ä~=éêçëéÉÅíáîÉ= = ÄìêÉ~ì=ÇÉ= BULLETIN STATISTIQUE äÛlÄëÉêî~íáçå= ¨ÅçåçãáèìÉ= = TRAFIC COMMERCIAL ANNEE 2002 = RMI=êìÉ=eÉåêóJc~êã~å= TRTOM=m~êáë=ÅÉÇÉñ=NR= í¨ä¨éÜçåÉ=W= AVRIL 2003 MN=RU=MV=QV=UN= í¨ä¨ÅçéáÉ=W= MN=RU=MV=QU=UP= = = = = ÇáêÉÅíáçå== ÇÉë=qê~åëéçêíë= ~¨êáÉåë= Le Bulletin Statistique de la Direction Générale de l'Aviation Civile est élaboré à partir des statistiques de trafic commercial provenant de l'ensemble des plates-formes françaises. Il regroupe un ensemble de statistiques essentielles pour la connaissance du transport aérien en France. L'édition de ce bulletin repose sur la fourniture par chacun des aéroports français de ses propres données. Ces données sont harmonisées, puis analysées suivant l’origine- destination du vol par numéro de vol. Des corrections nécessaires sont ensuite apportées en concertation avec les services aéroportuaires et/ou les Directions de l’Aviation Civile qui communiquent les résultats de trafic. La date de parution de ce bulletin dépend donc des délais de transmission des données par l’ensemble des fournisseurs de statistiques. Ce bulletin comprend cinq chapitres : • le premier est une synthèse des résultats de l’année civile, • le deuxième regroupe le trafic des compagnies françaises (tel qu’il ressort des informations communiquées à la Direction Générale de l’Aviation Civile), • le troisième est consacré aux trafics des relations entre la France et les pays étrangers, • les deux derniers regroupent le trafic des relations de la Métropole ou de l’Outre-Mer avec les pays étrangers ainsi que le trafic des aéroports de ces deux espaces. -
Air France-KLM Group for the Year Ended Activity AFR 33 December 31, 2012
Selected fi nancial information 2 Highlights of the 2012 fi nancial year AFR 4 4.6 Note on the methodology for the reporting Corporate governance AFR 5 of the environmental indicators 129 1.1 The Board of Directors 6 4.7 Environmental indicators 132 1.2 The CEO Committee 30 4.8 Statutory Auditor’s Attestation report on the social, environmental and corporate 1 1.3 The Group Executive Committee 30 citizenship information disclosed in the 2012 management report 136 4.9 Statutory Auditor’s Assurance report on a selection of environmental and social indicators of Air France-KLM group for the year ended Activity AFR 33 December 31, 2012. 137 2.1 Market and environment 34 2.2 Strategy 42 2 Activities Financial r eport 139 2.3 Passenger business 45 2.4 Cargo business 53 5.1 Investments and fi nancing 140 2.5 Maintenance business 57 5.2 Property, plant and equipment 143 2.6 Other businesses 62 5 5.3 Comments on the fi nancial statements 146 2.7 Fleet 64 5.4 Key fi nancial indicators 150 2.8 Highlights of the beginning Financial statements AFR of the 2013 fi nancial year 71 5.5 Consolidated fi nancial statements 156 5.6 Notes to the consolidated fi nancial statements 163 5.7 Statutory auditors’ report on the consolidated fi nancial statements 245 Risks and risk 5.8 Statutory fi nancial statements 247 5.9 Five-year results summary 259 management AFR 73 5.10 Statutory Auditor’s report 3.1 Risk management process 74 on the fi nancial statements 260 3 3.2 Risk factors and their management 75 5.11 Statutory Auditors’ special report on regulated agreements and commitments 261 3.3 Market risks and their management 83 3.4 Report of the Chairman of the Board of Directors on corporate governance, internal control and risk management for the 2012 fi nancial year 87 3.5 Statutory auditors’ report prepared in accordance Other information 265 with article L.225-235 of the French Commercial Code (Code de commerce) on the report prepared 6.1 History 266 by the Chairman of the Board of Directors of Air France-KLM S.A. -
AFI KLM E&M Steps up Presence on ATR Market
AFI KLM E&M Steps Up Presence On ATR Market European regional carrier HOP! signs new turboprop fleet component support deal with AFI KLM E&M. Paris Le Bourget, Amstelveen, 18 June 2013 - Following talks with several MROs earlier this year, HOP!-AIRLINAIR has signed a long-term component support contract with AFI KLM E&M covering a total 23 aircraft: 17 ATR 42s and 6 ATR 72s. The per flight hour contract includes repairs and access to a spares pool. The contract renews a previous agreement between AFI KLM E&M and Airlinair signed in 2009. In early 2013, Airlinair formed an alliance with Brit Air and Regional, to create HOP!, the new European regional carrier. Optimized ATR offer A special feature has been introduced to adapt the service rates according to the components removal rate. Reflecting AFI KLM E&M’s outstanding adaptability, this solution guarantees substantial savings for clients, in addition to the shorter TAT delivered by the MRO. Franck Terner, AFI President, said: “The trust Hop! has placed in us sends a strong signal to the market confirming the competitiveness and cost-effectiveness of our ATR components services.” Lionel Guérin, Chairman and CEO of HOP!, said: “It is important for us to be able to rely on a major MRO like AFI KLM E&M as over time, we have been able to measure the service quality, close relations and responsiveness.” About HOP! HOP! is a 100% subsidiary of Air France. HOP! controls 100% of the three airlines HOP!-REGIONAL, HOP!-BRIT AIR and HOP!-AIRLINAIR which operate on its behalf. -
Study on Airport Ownership and Management and the Ground Handling Market in Selected Non-European Union (EU) Countries
Study on airport DG MOVE, European ownership and Commission management and the ground handling market in selected non-EU countries Final Report Our ref: 22907301 June 2016 Client ref: MOVE/E1/SER/2015- 247-3 Study on airport DG MOVE, European ownership and Commission management and the ground handling market in selected non-EU countries Final Report Our ref: 22907301 June 2016 Client ref: MOVE/E1/SER/2015- 247-3 Prepared by: Prepared for: Steer Davies Gleave DG MOVE, European Commission 28-32 Upper Ground DM 28 - 0/110 London SE1 9PD Avenue de Bourget, 1 B-1049 Brussels (Evere) Belgium +44 20 7910 5000 www.steerdaviesgleave.com Steer Davies Gleave has prepared this material for DG MOVE, European Commission. This material may only be used within the context and scope for which Steer Davies Gleave has prepared it and may not be relied upon in part or whole by any third party or be used for any other purpose. Any person choosing to use any part of this material without the express and written permission of Steer Davies Gleave shall be deemed to confirm their agreement to indemnify Steer Davies Gleave for all loss or damage resulting therefrom. Steer Davies Gleave has prepared this material using professional practices and procedures using information available to it at the time and as such any new information could alter the validity of the results and conclusions made. The information and views set out in this report are those of the authors and do not necessarily reflect the official opinion of the European Commission. -
Assemblée Nationale
N° 1198 ______ ASSEMBLÉE NATIONALE CONSTITUTION DU 4 OCTOBRE 1958 TREIZIÈME LÉGISLATURE Enregistré à la Présidence de l'Assemblée nationale le 16 octobre 2008 RAPPORT FAIT AU NOM DE LA COMMISSION DES FINANCES, DE L’ÉCONOMIE GÉNÉRALE ET DU PLAN SUR LE PROJET DE loi de finances pour 2009 (n° 1127), PAR M. GILLES CARREZ, Rapporteur Général, Député. —— ANNEXE N° 15 ÉCOLOGIE, DÉVELOPPEMENT ET AMÉNAGEMENT DURABLES TRANSPORTS AÉRIENS ET MÉTÉOROLOGIE CONTRÔLE ET EXPLOITATION AÉRIENS Rapporteur spécial : M. Charles de COURSON Député ____ — 3 — SOMMAIRE ___ Pages SYNTHÈSE ......................................................................................................................... 7 I.– LE BUDGET DES TRANSPORTS AÉRIENS ET DE LA MÉTÉOROLOGIE ................................... 9 A.– L’EXÉCUTION BUDGÉTAIRE 2008 : BILAN AU 31 AOÛT.................................................... 9 1.– L’exécution du programme Transports aériens se déroule normalement................... 9 2.– L’exécution de la mission Contrôle et exploitation aériens est marquée par un risque de dépassement des crédits de personnel..................................................... 10 3.– L’exécution du programme Météorologie est particulièrement tendue ....................... 11 B.– LE PROJET DE BUDGET POUR 2009 ............................................................................. 12 1.– L’architecture budgétaire évolue considérablement ................................................. 12 a) Le programme Transports aériens est supprimé de la maquette..................................... -
Air France-Klm
AIR FRANCE-KLM GENERAL SHAREHOLDERS’ MEETING OF THURSDAY MAY 16, 2013 ANSWERS TO THE QUESTIONS IN WRITING FROM SHAREHOLDERS Preliminary remarks Note that, to be admissible, questions in writing must: - Relate to the agenda for the Shareholders' Meeting. - Be sent to the Chairman by registered letter with acknowledgement of receipt no later than four business days before the Meeting. - Be accompanied by a securities account registration certificate. To be able to devote more time to the questions from shareholders attending the Meeting, the answers to questions in writing have been posted on our www.airfranceklm-finance.con website in a special section pursuant to law. Article L225-108 of the French Code of Commerce provides that "the answer to a question in writing is deemed to have been given when it figures on the company's website". Shareholders may request a copy of the answers posted on our website from the Secretary to the Meeting. In the same spirit, the questions have been summarized (without changing their meaning) whenever their full wording is not required for the purposes of proper understanding. Long-haul activity Page 2 Short and medium-haul activity Page 4 Fuel bill Page 7 Alliances/Partnerships Page 7 Cargo Page 8 Maintenance Page 8 New organization Page 9 Board of Directors and compensation Page 9 Shareholder structure and the General Shareholders’ Meeting Page 11 1/12 Long-haul activity 1) In view of the existing threat from the Gulf State and South-East Asian airlines which are arriving and are set to arrive in Lyons, Mr. Tupinier asks if the new management plans to create a mini long-haul network of ten or so destinations on departure from Lyons. -
HIVER / WINTER / INVIERNO / INVERNO 2007 28 Octobre 2007 > 29 Mars 2008 October 28, 2007 > March 29, 2008
HORAIRES / TIMETABLE / FLUGPLAN / HORARIOS / ORARIO HIVER / WINTER / INVIERNO / INVERNO 2007 28 octobre 2007 > 29 mars 2008 October 28, 2007 > march 29, 2008 www.airfrance.com www.klm.com COMMENT UTILISER L'HORAIRE / HOW TO USE THIS TIMETABLE ZEICHENERKLÄRUNG / COMO UTILIZAR ESTE HORARIO / COME UTILIZZARE L’ORARIO GUIDE VILLE DE DESTINATION / DESTINATION CITY / ZIELORT / CIUDAD DE LLEGADA / CITTÀ DI DESTINAZIONE. CODE VILLE ARRIVÉE / ARRIVAL CITY CODE / CODE DES ZIELORTES / CÓDIGO DE LA CIUDAD DE LLEGADA / CODICE CITTÀ DI ARRIVO. UTC (Universal Time Coordinated) ± HEURE LOCALE / LOCAL TIME / ORTSZEIT / HORA LOCAL / ORA LOCALE. Variation de l’heure locale par rapport à UTC / Difference between local time and UTC / Zeitunterschied zu UTC - Zeit / Diferencia horaria respecto a UTC / Variazione dell’ora locale rispetto all’UTC. CODE VILLE DE DÉPART / DEPARTURE CITY CODE / CODE DES ABFLUGSORTES / CÓDIGO DE LA CIUDAD DE SALIDA / CODICE CITTÀ DI PARTENZA. JOURS DE FONCTIONNEMENT / OPERATING DAYS / VERKEHRSTAGE / DÍAS DE OPERACIÓN / GIORNI OPERATIVI : 1 Lundi / Monday / Montag / Lunes / Lunedì 5 Vendredi / Friday / Freitag / Viernes / Venerdì 2 Mardi / Tuesday / Dienstag / Martes / Martedì 6 Samedi / Saturday / Samstag / Sábado / Sabato 3 Mercredi / Wednesday / Mittwoch / Miércoles / Mercoledì 7 Dimanche / Sunday / Sonntag / Domingo / Domenica 4 Jeudi / Thursday / Donnerstag / Jueves / Giovedì HEURE DE DÉPART / DEPARTURE TIME / ABFLUGZEIT / HORA DE SALIDA / ORARIO DI PARTENZA. HEURE D’ARRIVÉE / ARRIVAL TIME / ANKUNFTSZEIT / HORA DE LLEGADA / ORARIO DI ARRIVO. DURÉE, temps de vol / DURATION, time of flight / DAUER, Flugzeit / DURATA, tempo di volo / DURAÇION, tiempo de vuelo. PÉRIODE DE VALIDITÉ / FLIGHT VALIDITY PERIOD / GÜLTIG VON…BIS… / PERIODO DE VALIDEZ / PERIODO DI VALIDITÀ. AÉROGARE DE DÉPART / DEPARTURE AIRPORT / ABFLUGHAFE / AEROPUERTO DE SALIDAN / AEROSTAZIONE DI PARTENZA. -
Recent Developments in Aviation Liability Law Blanca I
Journal of Air Law and Commerce Volume 66 | Issue 1 Article 3 2001 Recent Developments in Aviation Liability Law Blanca I. Rodriguez Follow this and additional works at: https://scholar.smu.edu/jalc Recommended Citation Blanca I. Rodriguez, Recent Developments in Aviation Liability Law, 66 J. Air L. & Com. 21 (2001) https://scholar.smu.edu/jalc/vol66/iss1/3 This Article is brought to you for free and open access by the Law Journals at SMU Scholar. It has been accepted for inclusion in Journal of Air Law and Commerce by an authorized administrator of SMU Scholar. For more information, please visit http://digitalrepository.smu.edu. RECENT DEVELOPMENTS IN AVIATION LIABILITY LAW BLANCA I. RODRIGUEZ* ** TABLE OF CONTENTS I. INTRODUCTION .................................. 24 II. THE MONTREAL CONVENTION OF 1999 ....... 25 A. THE PASSENGER CAUSE OF ACTION UNDER ARTICLE 17 ..................................... 27 B. JOINT AND SEVERAL LIABILITY ................... 29 C. ELIMINATION OF DAMAGES LIMITATIONS AND ADOPTION OF A Two-TIERED COMPENSATION SCH EM E ......................................... 29 D. ADVANCE PAYMENTS AND AUTOMATIC REVIEW OF TIER ONE PAYMENT AMOUNTS .................. 31 E. PASSENGER'S CONTRIBUTORY FAULT ............. 31 F. COURT COSTS AND LEGAL EXPENSES ............ 32 G. PUNITIVE DAMAGES ............................. 32 H. ADDITION OF THE FIFTH PLACE OF TREATY JURISDICTION ................................... 33 I. TICKET DELIVERY ............................... 34 J. RECOURSE AGAINST THIRD PARTIES AT FAULT ... 34 K. STATUTE OF LIMITATIONS ....................... 34 L. ACTS OF AGENTS AND SERVANTS OF THE C ARRIER ........................................ 34 III. LIABILITY OF AIR CARRIERS UNDER THE 1929 WARSAW CONVENTION .......................... 35 A. THE UNITED STATES ADOPTS THE 1975 MONTREAL PROTOCOL No. 4 ................... 35 * A partner in the New York City law firm of Kreindler & Kreindler, concentrating in aviation accident law and complex tort litigation.