Nanoelectromechanical Systems ͒ K
Total Page:16
File Type:pdf, Size:1020Kb
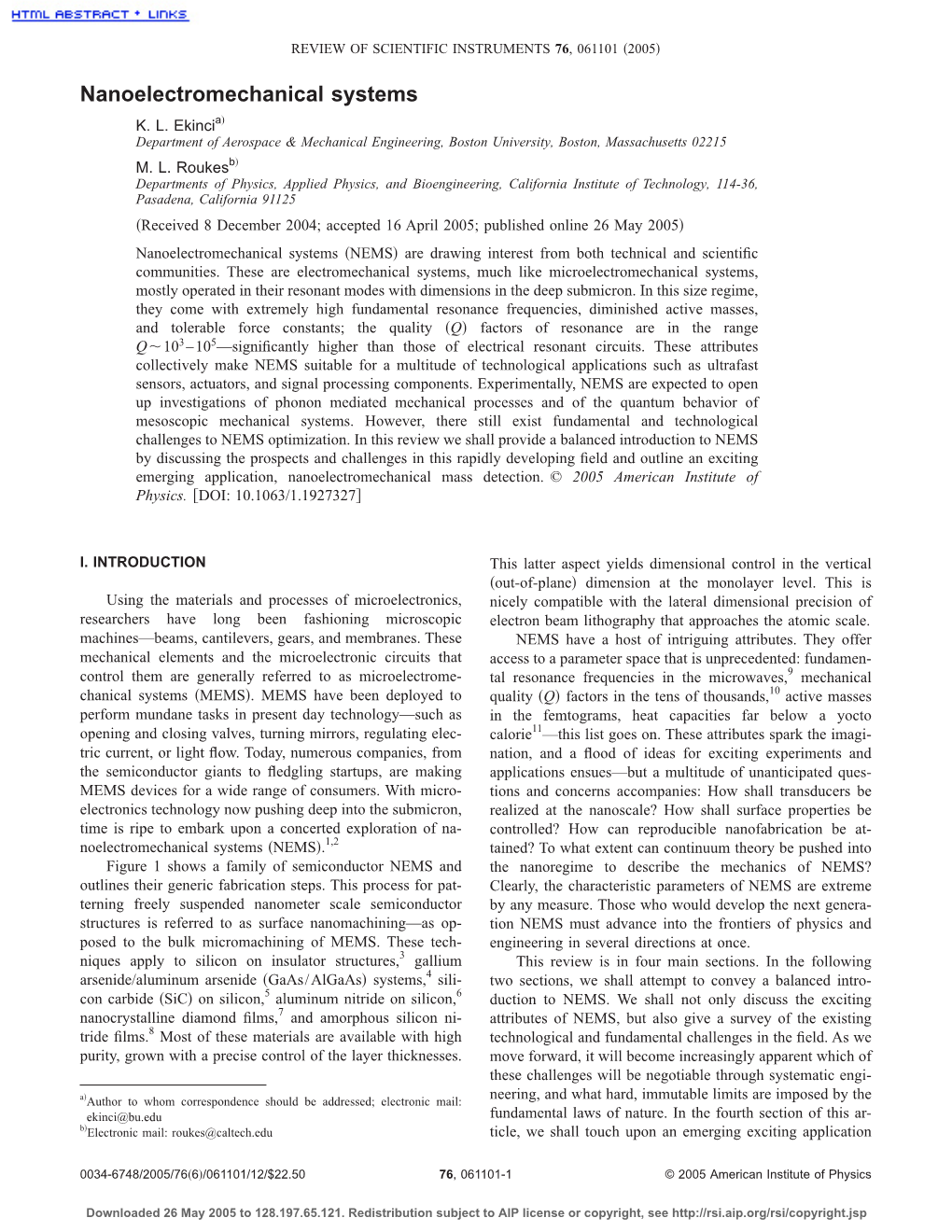
Load more
Recommended publications
-
Challenges for Nanomechanics of Biological Systems
NNI Interagency Workshop : Instrumentation and Metrology for Nanotechnology Grand Challenge Workshop National Institute of Standards and Technology, Gaithersburg, MD Jan 27-29, 2004 Challenges for Nanomechanics of Biological Systems Christine Ortiz, Assistant Professor Massachusetts Institute of Technology Department of Materials Science and Engineering WWW : http://web.mit.edu/cortiz/www/ Biological systems are one of the most difficult classes of materials to study mechanically at the nanoscale.1-3 Their complex multilevel and multicomponent structures (e.g. tissues, cells, proteins) need to be highly purified and characterized with minimal sample preparation damage (if possible, with no polishing and chemical treatments) so as to still give information relevant to in vivo function. Nanomechanical testing can be challenging due to the need for near-physiological conditions (i.e. aqueous salt solutions, ionic strength=0.15M, pH=7.4), the existence of varied 3-dimensional geometries and multiple buried interfaces, and their dynamic and sometimes, extremely soft, fluid-like nature. Following is a summary of a few new areas which I believe represent the most significant new paths in this field. I. Integration of Nanomechanical Testing Methods with Nanoscale Chemical/Structural Characterization Techniques Down to the Single Molecule Level in Near-Phys iological Conditions. One promising example of this is the combination of atomic force microscopy (AFM) and surface enhanced Raman spectroscopy (SERS)(Figure 1).4-8 SERS is a higher resolution version of traditional Raman spectroscopy, in which the wavelength and intensity of inelastically scattered light from molecules is measured. These wavelengths are shifted from the incident light by the energies of molecular vibrations and hence, allow for chemical identification and characterization of substances. -
Engineered Carbon Nanotubes and Graphene for Nanoelectronics And
Engineered Carbon Nanotubes and Graphene for Nanoelectronics and Nanomechanics E. H. Yang Stevens Institute of Technology, Castle Point on Hudson, Hoboken, NJ, USA, 07030 ABSTRACT We are exploring nanoelectronic engineering areas based on low dimensional materials, including carbon nanotubes and graphene. Our primary research focus is investigating carbon nanotube and graphene architectures for field emission applications, energy harvesting and sensing. In a second effort, we are developing a high-throughput desktop nanolithography process. Lastly, we are studying nanomechanical actuators and associated nanoscale measurement techniques for re-configurable arrayed nanostructures with applications in antennas, remote detectors, and biomedical nanorobots. The devices we fabricate, assemble, manipulate, and characterize potentially have a wide range of applications including those that emerge as sensors, detectors, system-on-a-chip, system-in-a-package, programmable logic controls, energy storage systems, and all-electronic systems. INTRODUCTION A key attribute of modern warfare is the use of advanced electronics and information technologies. The ability to process, analyze, distribute and act upon information from sensors and other data at very high- speeds has given the US military unparalleled technological superiority and agility in the battlefield. While recent advances in materials and processing methods have led to the development of faster processors and high-speed devices, it is anticipated that future technological breakthroughs in these areas will increasingly be driven by advances in nanoelectronics. A vital enabler in generating significant improvements in nanoelectronics is graphene, a recently discovered nanoelectronic material. The outstanding electrical properties of both carbon nanotubes (CNTs) [1] and graphene [2] make them exceptional candidates for the development of novel electronic devices. -
Springer Handbook of Nanotechnology
Springer Handbook of Nanotechnology Springer Handbooks provide a concise compilation of approved key information on methods of research, general principles, and functional relationships in physi- cal sciences and engineering. The world’s leading experts in the fields of physics and engineer- ing will be assigned by one or several renowned editors to write the chapters comprising each vol- ume. The content is selected by these experts from Springer sources (books, journals, online content) and other systematic and approved recent publications of physical and technical information. The volumes are designed to be useful as readable desk reference books to give a fast and comprehen- sive overview and easy retrieval of essential reliable key information, including tables, graphs, and bibli- ographies. References to extensive sources are provided. HandbookSpringer of Nanotechnology Bharat Bhushan (Ed.) 3rd revised and extended edition With DVD-ROM, 1577 Figures and 127 Tables 123 Editor Professor Bharat Bhushan Nanoprobe Laboratory for Bio- and Nanotechnology and Biomimetics (NLB2) Ohio State University 201 W. 19th Avenue Columbus, OH 43210-1142 USA ISBN: 978-3-642-02524-2 e-ISBN: 978-3-642-02525-9 DOI 10.1007/978-3-642-02525-9 Springer Heidelberg Dordrecht London New York Library of Congress Control Number: 2010921002 c Springer-Verlag Berlin Heidelberg 2010 This work is subject to copyright. All rights are reserved, whether the whole or part of the material is concerned, specifically the rights of translation, reprinting, reuse of illustrations, recitation, broadcasting, reproduction on microfilm or in any other way, and storage in data banks. Duplication of this publication or parts thereof is permitted only under the provisions of the German Copyright Law of September 9, 1965, in its current version, and permission for use must always be obtained from Springer. -
Scale Effects of Nanomechanical Properties and Deformation Behavior of Au Nanoparticle and Thin Film Using Depth Sensing Nanoindentation
Scale effects of nanomechanical properties and deformation behavior of Au nanoparticle and thin film using depth sensing nanoindentation Dave Maharaj and Bharat Bhushan* Full Research Paper Open Access Address: Beilstein J. Nanotechnol. 2014, 5, 822–836. Nanoprobe Laboratory for Bio-& Nanotechnology and Biomimetics doi:10.3762/bjnano.5.94 (NLBB), The Ohio State University, 201 W.19th Avenue, Columbus, Ohio 43210-1142, USA Received: 14 January 2014 Accepted: 14 May 2014 Email: Published: 11 June 2014 Bharat Bhushan* - [email protected] This article is part of the Thematic Series "Advanced atomic force * Corresponding author microscopy techniques II". Keywords: Guest Editors: T. Glatzel and T. Schimmel gold (Au); Hall–Petch; hardness; nanoindentation; nano-objects © 2014 Maharaj and Bhushan; licensee Beilstein-Institut. License and terms: see end of document. Abstract Nanoscale research of bulk solid surfaces, thin films and micro- and nano-objects has shown that mechanical properties are enhanced at smaller scales. Experimental studies that directly compare local with global deformation are lacking. In this research, spherical Au nanoparticles, 500 nm in diameter and 100 nm thick Au films were selected. Nanoindentation (local deformation) and compression tests (global deformation) were performed with a nanoindenter using a sharp Berkovich tip and a flat punch, respec- tively. Data from nanoindentation studies were compared with bulk to study scale effects. Nanoscale hardness of the film was found to be higher than the nanoparticles with both being higher than bulk. Both nanoparticles and film showed increasing hardness for decreasing penetration depth. For the film, creep and strain rate effects were observed. In comparison of nanoindentation and compression tests, more pop-ins during loading were observed during the nanoindentation of nanoparticles. -
“Nanomechanics: Elasticity and Friction in Nano-Objects”
“NanoMechanics : Elasticity and Friction in Nano-Objects” Start Date: August 2006 Applicant: Elisa Riedo Institution: Georgia Institute of Technology PI: Elisa Riedo Address: School of Physics, 837 State St, Atlanta GA 30332-0430Email: [email protected] DOE Division of Materials Sciences and Engineering, Office of Basic Energy Sciences Mechanical Behavior and Radiation Effects Program DOE Office of Science Program Manager Contact: John S. Vetrano 1. Introduction Nanosheets, nanotubes, nanowires, and nanoparticles are gaining a large interest in the scientific community for their exciting properties, and they hold the potential to become building blocks in integrated nano-electronic and photonic circuits, nano-sensors, batteries electrodes, energy harvesting nano-systems, and nano-electro-mechanical systems (NEMS). While several experiments and theoretical calculations have revealed exciting novel phenomena in these nanostructures, many scientific and technological questions remain open. A fundamental objective guiding the study of nanoscale materials is to understanding what are the new rules governing nanoscale properties and at what extent well-known physical macroscopic laws still apply in the nano-world. The vision of this DoE research program is to understand the mechanical properties of nanoscale materials by exploring new experimental methods and theoretical models at the boundaries between continuum mechanics and atomistic models, with the overarching goal of defining the basic laws of mechanics at the nanoscale. The group of the PI has developed in the last years several studies on the mechanical properties of Carbon nanotubes and oxide nanobelts, more recently the PI and her collaborators have focused their attention on the properties of two-dimensional (2D) materials, such as graphene and MoS2, which are a few-atomic- layer thick films with strong in-plane bonds and weak interactions between the layers. -
Research Article Nanomechanics of Single Crystalline Tungsten Nanowires
Hindawi Publishing Corporation Journal of Nanomaterials Volume 2008, Article ID 638947, 9 pages doi:10.1155/2008/638947 Research Article Nanomechanics of Single Crystalline Tungsten Nanowires Volker Cimalla,1 Claus-Christian Rohlig,¨ 1 Jorg¨ Pezoldt,1 Merten Niebelschutz,¨ 1 Oliver Ambacher,1 Klemens Bruckner,¨ 1 Matthias Hein,1 Jochen Weber,2 Srdjan Milenkovic,3 Andrew Jonathan Smith,3 and Achim Walter Hassel3 1 Institut fur¨ Mikro- und Nanotechnologien, Technische Universitat¨ Ilmenau, Gustav-Kirchhoff-Strasse 7, 98693 Ilmenau, Germany 2 Max-Planck-Institut fur¨ Festkorperforschung,¨ HeisenbergStrasse 1, 70569 Stuttgart, Germany 3 Max-Planck-Institut fur¨ Eisenforschung, Max-Planck-Strasse 1, 40237 Dusseldorf,¨ Germany Correspondence should be addressed to Achim Walter Hassel, [email protected] Received 2 September 2007; Accepted 29 January 2008 Recommended by Jun Lou Single crystalline tungsten nanowires were prepared from directionally solidified NiAl-W alloys by a chemical release from the resulting binary phase material. Electron back scatter diffraction (EBSD) proves that they are single crystals having identical crys- tallographic orientation. Mechanical investigations such as bending tests, lateral force measurements, and mechanical resonance measurements were performed on 100–300 nm diameter wires. The wires could be either directly employed using micro tweezers, as a singly clamped nanowire or in a doubly clamped nanobridge. The mechanical tests exhibit a surprisingly high flexibility for such a brittle material resulting from the small dimensions. Force displacement measurements on singly clamped W nanowires by an AFM measurement allowed the determination of a Young’s modulus of 332 GPa very close to the bulk value of 355 GPa. Doubly clamped W nanowires were employed as resonant oscillating nanowires in a magnetomotively driven resonator running at 117 kHz. -
NSF Summer Institute on Nanomechanics, Nanomaterials
NSF Summer Institute on Nanomechanics, Nanomateriials and Micro/Nanomanufacturing NSF Summer Institute Short Course on Materiomics—Merging Biology and Engineering in Multiscale Structures and Materials Location: Massachusetts Institute of Technology, LeMeridien Hotel (former Hotel@MIT) Chair: Markus J. Buehler, Massachusetts Institute of Technology ([email protected]) Dates: May 30 (Wednesday) morning to June 1 (Friday) evening, 2012 Course Objectives: Theme-based introduction into emerging science at the interface of engineering and biology This course will provide an introduction into the emerging science at the interface of engineering and biology, with a focus on the integration of multiscale modeling and experiment. Applying material design principles derived from biology—and specifically, the concept of developing diverse hierarchical structures composed of universal and simple design elements, used to derive sustainable and robust materials—is crucial for the next-generation engineering materials that are highly functional while satisfying multiple design constraints. This finds practical applications for example in regenerative medicine for de novo tissue growth, advanced carbon-based materials that are not only strong and tough, and self-learning material systems whose properties can be tailored by solely changing the structure without a need to introduce new building blocks. This Summer Institute features experimental, computational and theoretical instructors from various areas of science, dealing with multiple length-scales, from nano to macro. Participants and instructors will engage in in- depth discussions on the frontiers, challenges, and opportunities in this emerging field referred to as materiomics. A unique feature of this short course is the participation of scientists from disparate fields that includes engineering mechanics, synthetic biology and architecture. -
Nanomechanics and Nanoelectronics: Molecule-Size Machines
Report Number 11 February, 2004 Nanomechanics and Nanoelectronics: Molecule-Size Machines Executive Summary Nanotechnology research is aimed at building minuscule machines and electronics and constructing materials molecule- by-molecule. The technology promises to open the way to faster and lower-power electronics, jewelry-size computers, data storage densities in the realm of several terabits per square centimeter, ultrahigh-bandwidth communications devices, microscopic transmitters and receivers, new types of devices like handheld biological sensors, and inexpensive manufacturing processes. Near-term nanotech developments will make materials tougher and lubricants slipperier. Longer-term research is largely focused on developing the basic building blocks of nanoscale technology — components that are hundreds of times smaller than a red blood cell. Nanoelectronics researchers are working to develop tiny transistors, memory devices, switches, wires, light emitters and networks. What to Look For Nanomechanics researchers are working to develop ratchets, actuators, motors, shuttles, springs, pistons and bearings. Nanotube electronics: There are two approaches to building both types of devices: the top- Carbon nanotubes sensors down method of today’s microelectronics manufacturing and the Hybrid nanotube-silicon chips bottom-up techniques of biology, chemistry and materials engineering. Carbon nanotube logic circuits Raw materials include inorganic matter like metals and Mass production of nanoelectronics semiconductors, molecules like polymers and carbon nanotubes, and biological molecules like DNA and proteins. Nanowire electronics: Carbon nanotubes and nanowires are especially promising because Nanowire memory chips they can be exceedingly small, assembled chemically, and have the Nanowire LEDs and lasers potential to be grown in place and en mass. Carbon nanotubes are Nanowire processor chips also very strong mechanically. -
Nanomechanics – Quantum Size Effects, Contacts, and Triboelectricity Martin Olsen
Nanomechanics – Quantum Size Effects, Contacts, and Triboelectricity Martin Olsen Department of Natural Sciences Mid Sweden University Doctoral Thesis No. 299 Sundsvall, Sweden 2019 Mittuniversitetet Institutionen for¨ Naturvetenskap ISBN 978-91-88947-02-4 SE-851 70 Sundsvall ISSN 1652-893X SWEDEN Akademisk avhandling som med tillstand˚ av Mittuniversitetet framlagges¨ till of- fentlig granskning for¨ avlaggande¨ av teknologie doktorsexamen onsdagen den 5:e juni 2019 klockan 10:15 i O102, Mittuniversitetet, Holmgatan 10, Sundsvall. c Martin Olsen, maj 2019 Tryck: Tryckeriet Mittuniversitetet To my parents iv Abstract Nanomechanics is different from the mechanics that we experience in everyday life. At the nano-scale, typically defined as 1 to 100 nanometers, some phenomena are of crucial importance, while the same phenomena can be completely neglected on a larger scale. For example, the feet of a gekko are covered by nanocontacts that yield such high adhesion forces that the animal can run up on walls and even on the ceiling. At small enough distances, matter and energy become discrete, and the description of the phenomena occurring at this scale requires quantum mechanics. However, at room temperature the transitions between quantized energy levels may be concealed by the thermal vibrations of the system. As two surfaces approach each other and come into contact, electrostatic forces and van der Waals forces may cause redistribution of matter at the nano level. One effect that may occur upon contact between two surfaces is the triboelectric effect, in which charge is transferred from one surface to the other. This effect can be used to generate electricity in triboelectric nanogenerators (TENGs), where two surfaces are repeatedly brought in and out of contact, and where the charge transfer is turned into electrical energy. -
Nanomechanics of Organic Layers and Biomenbranes
Nanomechanics of Organic Layers and Biomenbranes Gerard Oncins Marco ADVERTIMENT. La consulta d’aquesta tesi queda condicionada a l’acceptació de les següents condicions d'ús: La difusió d’aquesta tesi per mitjà del servei TDX (www.tesisenxarxa.net) ha estat autoritzada pels titulars dels drets de propietat intel·lectual únicament per a usos privats emmarcats en activitats d’investigació i docència. No s’autoritza la seva reproducció amb finalitats de lucre ni la seva difusió i posada a disposició des d’un lloc aliè al servei TDX. No s’autoritza la presentació del seu contingut en una finestra o marc aliè a TDX (framing). Aquesta reserva de drets afecta tant al resum de presentació de la tesi com als seus continguts. En la utilització o cita de parts de la tesi és obligat indicar el nom de la persona autora. ADVERTENCIA. La consulta de esta tesis queda condicionada a la aceptación de las siguientes condiciones de uso: La difusión de esta tesis por medio del servicio TDR (www.tesisenred.net) ha sido autorizada por los titulares de los derechos de propiedad intelectual únicamente para usos privados enmarcados en actividades de investigación y docencia. No se autoriza su reproducción con finalidades de lucro ni su difusión y puesta a disposición desde un sitio ajeno al servicio TDR. No se autoriza la presentación de su contenido en una ventana o marco ajeno a TDR (framing). Esta reserva de derechos afecta tanto al resumen de presentación de la tesis como a sus contenidos. En la utilización o cita de partes de la tesis es obligado indicar el nombre de la persona autora. -
Electromagnetoelastic Actuator for Nanomechanics and Nanotechnology
Crimson Publishers Mini Review Wings to the Research Electromagnetoelastic Actuator for Nanomechanics and Nanotechnology Afonin SM* National Research University of Electronic Technology, MIET, Russia Abstract The characteristics of an electromagnetoelastic actuator for nanomechanics and nanotechnology ISSN: 2640-9690 are received. The structural diagram of an electromagnetoelastic actuator for nanomechanics and nanotechnology is obtained. The structural diagram of an electromagnetoelastic actuator has a difference in the visibility of energy conversion from Cady and Mason electrical equivalent circuits of a piezo vibrator.Keywords: The Electromagnetoelasticmatrix transfer function actuator; of an electromagnetoelastic Characteristics; Structural actuator is obtained.diagram; Piezo actuator; Deformation; Matrix transfer function; Nanomechanics and nanotechnology Introduction An electromagnetoelastic actuators in the form of piezo actuators or magnetostriction actuators are used in nanomechanics and nanotechnology for nanomanipulators, laser systems, nano pumps, scanning microscopy [1-5]. The piezo actuator is used for nano displacements in photolithography, microsurgical operations, optical-mechanical devices, adaptive optics *Corresponding author: Afonin Sergey Mikhailovich, National Research University of Electronic Technology, MIET, systems and adaptive telescopes, fiber-optic systems [6-15]. The electromagnetoelasticity 124498, Moscow, Russia electromagnetoelastic actuator. The structural diagram of an electromagnetoelastic actuator equation and the differential equation are solved to obtain the structural model of an Submission: Published: June 3, 2021 has a difference for from Cady and Mason electrical equivalent circuits of a piezo vibrator April 06, 2021 in the visibility of energy conversion. The structural diagram of an electromagnetoelastic electromagnetoelasticity [4-12]. Volume 3 - Issue 4 actuator for nanomechanics and nanotechnology is obtained by applying the theory of How to cite this article: Afonin SM. -
Nanomechanics of Low-Dimensional Materials for Functional Applications
Nanoscale Horizons View Article Online FOCUS View Journal | View Issue Nanomechanics of low-dimensional materials for functional applications Cite this: Nanoscale Horiz., 2019, 4,781 Sufeng Fan, †a Xiaobin Feng, †a Ying Han, †a Zhengjie Fanab and Yang Lu *acd When materials’ characteristic dimensions are reduced to the nanoscale regime, their mechanical properties will vary significantly to that of their bulk counterparts. Recently low-dimensional materials, including one-dimensional (1D) and two-dimensional (2D) nanomaterials, have attracted the widespread attention of academia and industry because of their unique (e.g., thermal, optical, electrical, catalytic) properties. These outstanding properties give them a wide variety of functional applications; however, reliable devices and practical applications call for high structural reliability and mechanical robustness of these nanoscale building blocks. Therefore, there is a need to investigate and characterize the nanomechanical properties and deformation mechanisms of low-dimensional materials but this remains highly challenging. In this Focus article, we summarize the recent progress made in the nanomechanical studies on some representative 1D/2D crystalline nanomaterials, with a special emphasis on experimental research. Furthermore, the unconventional mechanical properties, such as the significantly enhanced elasticity, of these low-dimensional crystals can lead to unprecedented physical and chemical property changes, which may fundamentally change the way such materials conduct