Working Gas Selection for the Closed Brayton Cycle John L
Total Page:16
File Type:pdf, Size:1020Kb
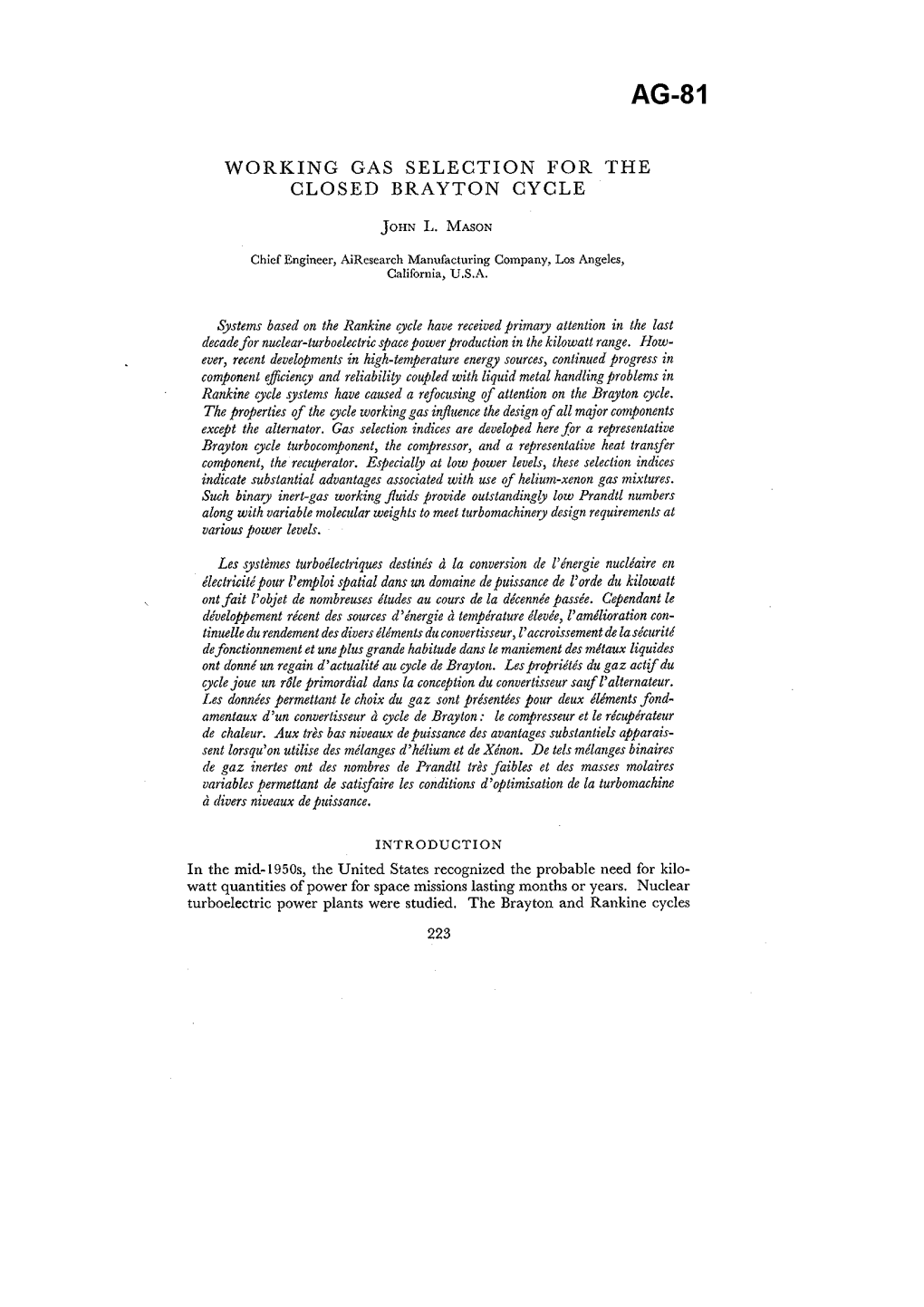
Load more
Recommended publications
-
Blending Hydrogen Into Natural Gas Pipeline Networks: a Review of Key Issues
Blending Hydrogen into Natural Gas Pipeline Networks: A Review of Key Issues M. W. Melaina, O. Antonia, and M. Penev NREL is a national laboratory of the U.S. Department of Energy, Office of Energy Efficiency & Renewable Energy, operated by the Alliance for Sustainable Energy, LLC. Technical Report NREL/TP-5600-51995 March 2013 Contract No. DE-AC36-08GO28308 Blending Hydrogen into Natural Gas Pipeline Networks: A Review of Key Issues M. W. Melaina, O. Antonia, and M. Penev Prepared under Task No. HT12.2010 NREL is a national laboratory of the U.S. Department of Energy, Office of Energy Efficiency & Renewable Energy, operated by the Alliance for Sustainable Energy, LLC. National Renewable Energy Laboratory Technical Report 15013 Denver West Parkway NREL/TP-5600-51995 Golden, Colorado 80401 March 2013 303-275-3000 • www.nrel.gov Contract No. DE-AC36-08GO28308 NOTICE This report was prepared as an account of work sponsored by an agency of the United States government. Neither the United States government nor any agency thereof, nor any of their employees, makes any warranty, express or implied, or assumes any legal liability or responsibility for the accuracy, completeness, or usefulness of any information, apparatus, product, or process disclosed, or represents that its use would not infringe privately owned rights. Reference herein to any specific commercial product, process, or service by trade name, trademark, manufacturer, or otherwise does not necessarily constitute or imply its endorsement, recommendation, or favoring by the United States government or any agency thereof. The views and opinions of authors expressed herein do not necessarily state or reflect those of the United States government or any agency thereof. -
Atmospheric Gases Student Handout Atmospheric Gases
Atmospheric Gases Student Handout Atmospheric Gases Driving Question: What is our atmosphere made of? In this activity you will: 1. Explore the variety and ratio of compounds and elements that make up the Earth’s atmosphere. 2. Understand volumetric measurements of gases in the atmosphere. 3. Visually depict the composition of the atmosphere. Background Information: Understanding Concentration Measurements In this activity, we will investigate the gas composition of our planet’s atmosphere. We use percentages to represent units of gas composition. A percent (%) is equivalent to 1 part out of 100 equal units. 1% = 1 part out of 100 For smaller concentrations scientists use parts per million (ppm) to represent concentrations of gases (or pollutants) in the atmosphere). One ppm is equivalent to 1 part out of 1,000,000 if the volume being measured is separated into 1,000,000 equal units. 1 ppm = 1 part out of 1,000,000 In this activity, you will use graph paper to represent the concentration of different gases in the atmosphere. Copyright © 2011 Environmental Literacy and Inquiry Working Group at Lehigh University Atmospheric Gases Student Handout 2 Here are some examples to help visualize parts per million: The common unit mg/liter is equal to ppm concentration Four drops of ink in a 55-gallon barrel of water would produce an "ink concentration" of 1 ppm. 1 12-oz can of soda pop in a 30-meter swimming pool 1 3-oz chocolate bar on a football field Atmospheric Composition Activity You will be creating a graphic model of the atmosphere composition using the Atmospheric Composition of Clean Dry Air activity sheet. -
Tracer Applications of Noble Gas Radionuclides in the Geosciences
To be published in Earth-Science Reviews Tracer Applications of Noble Gas Radionuclides in the Geosciences (August 20, 2013) Z.-T. Lua,b, P. Schlosserc,d, W.M. Smethie Jr.c, N.C. Sturchioe, T.P. Fischerf, B.M. Kennedyg, R. Purtscherth, J.P. Severinghausi, D.K. Solomonj, T. Tanhuak, R. Yokochie,l a Physics Division, Argonne National Laboratory, Argonne, Illinois, USA b Department of Physics and Enrico Fermi Institute, University of Chicago, Chicago, USA c Lamont-Doherty Earth Observatory, Columbia University, Palisades, New York, USA d Department of Earth and Environmental Sciences and Department of Earth and Environmental Engineering, Columbia University, New York, USA e Department of Earth and Environmental Sciences, University of Illinois at Chicago, Chicago, IL, USA f Department of Earth and Planetary Sciences, University of New Mexico, Albuquerque, USA g Center for Isotope Geochemistry, Lawrence Berkeley National Laboratory, Berkeley, USA h Climate and Environmental Physics, Physics Institute, University of Bern, Bern, Switzerland i Scripps Institution of Oceanography, University of California, San Diego, USA j Department of Geology and Geophysics, University of Utah, Salt Lake City, USA k GEOMAR Helmholtz Center for Ocean Research Kiel, Marine Biogeochemistry, Kiel, Germany l Department of Geophysical Sciences, University of Chicago, Chicago, USA Abstract 81 85 39 Noble gas radionuclides, including Kr (t1/2 = 229,000 yr), Kr (t1/2 = 10.8 yr), and Ar (t1/2 = 269 yr), possess nearly ideal chemical and physical properties for studies of earth and environmental processes. Recent advances in Atom Trap Trace Analysis (ATTA), a laser-based atom counting method, have enabled routine measurements of the radiokrypton isotopes, as well as the demonstration of the ability to measure 39Ar in environmental samples. -
Entropy: Ideal Gas Processes
Chapter 19: The Kinec Theory of Gases Thermodynamics = macroscopic picture Gases micro -> macro picture One mole is the number of atoms in 12 g sample Avogadro’s Number of carbon-12 23 -1 C(12)—6 protrons, 6 neutrons and 6 electrons NA=6.02 x 10 mol 12 atomic units of mass assuming mP=mn Another way to do this is to know the mass of one molecule: then So the number of moles n is given by M n=N/N sample A N = N A mmole−mass € Ideal Gas Law Ideal Gases, Ideal Gas Law It was found experimentally that if 1 mole of any gas is placed in containers that have the same volume V and are kept at the same temperature T, approximately all have the same pressure p. The small differences in pressure disappear if lower gas densities are used. Further experiments showed that all low-density gases obey the equation pV = nRT. Here R = 8.31 K/mol ⋅ K and is known as the "gas constant." The equation itself is known as the "ideal gas law." The constant R can be expressed -23 as R = kNA . Here k is called the Boltzmann constant and is equal to 1.38 × 10 J/K. N If we substitute R as well as n = in the ideal gas law we get the equivalent form: NA pV = NkT. Here N is the number of molecules in the gas. The behavior of all real gases approaches that of an ideal gas at low enough densities. Low densitiens m= enumberans tha oft t hemoles gas molecul es are fa Nr e=nough number apa ofr tparticles that the y do not interact with one another, but only with the walls of the gas container. -
An Analysis of the Brayton Cycle As a Cryogenic Refrigerator
jbrary, E-01 Admin. BJdg. OCT 7 1968 NBS 366 An Analysis of the Brayton Cycle As a Cryogenic Refrigerator ITATIONAL BURSAL' OF iTANDABD8 LIBRABT MAR 6 J973 V* 0F c J* 0a <5 Q \ v S. DEPARTMENT OF COMMERCE in Q National Bureau of Standards %. *^CAU 0? * : NATIONAL BUREAU OF STANDARDS The National Bureau of Standards 1 was established by an act of Congress March 3, 1901. Today, in addition to serving as the Nation's central measurement laboratory, the Bureau is a principal focal point in the Federal Government for assuring maxi- mum application of the physical and engineering sciences to the advancement of tech- nology in industry and commerce. To this end the Bureau conducts research and provides central national services in three broad program areas and provides cen- tral national services in a fourth. These are: (1) basic measurements and standards, (2) materials measurements and standards, (3) technological measurements and standards, and (4) transfer of technology. The Bureau comprises the Institute for Basic Standards, the Institute for Materials Research, the Institute for Applied Technology, and the Center for Radiation Research. THE INSTITUTE FOR BASIC STANDARDS provides the central basis within the United States of a complete and consistent system of physical measurement, coor- dinates that system with the measurement systems of other nations, and furnishes essential services leading to accurate and uniform physical measurements throughout the Nation's scientific community, industry, and commerce. The Institute consists of an Office of Standard Reference Data and a group of divisions organized by the following areas of science and engineering Applied Mathematics—Electricity—Metrology—Mechanics—Heat—Atomic Phys- 2 2 ics—Cryogenics-—Radio Physics-—Radio Engineering —Astrophysics —Time and Frequency. -
On the Equation of State of an Ideal Monatomic Gas According to the Quantum-Theory, In: KNAW, Proceedings, 16 I, 1913, Amsterdam, 1913, Pp
Huygens Institute - Royal Netherlands Academy of Arts and Sciences (KNAW) Citation: W.H. Keesom, On the equation of state of an ideal monatomic gas according to the quantum-theory, in: KNAW, Proceedings, 16 I, 1913, Amsterdam, 1913, pp. 227-236 This PDF was made on 24 September 2010, from the 'Digital Library' of the Dutch History of Science Web Center (www.dwc.knaw.nl) > 'Digital Library > Proceedings of the Royal Netherlands Academy of Arts and Sciences (KNAW), http://www.digitallibrary.nl' - 1 - 227 high. We are uncertain as to the cause of this differencc: most probably it is due to an nncertainty in the temperature with the absolute manometer. It is of special interest to compare these observations with NERNST'S formula. Tbe fourth column of Table II contains the pressUl'es aceord ing to this formula, calc111ated witb the eonstants whieb FALCK 1) ha~ determined with the data at bis disposal. FALOK found the following expression 6000 1 0,009983 log P • - --. - + 1. 7 5 log T - T + 3,1700 4,571 T . 4,571 where p is the pressure in atmospheres. The correspondence will be se en to be satisfactory considering the degree of accuracy of the observations. 1t does riot look as if the constants could be materially improved. Physics. - "On the equation of state oj an ideal monatomic gflS accoJ'ding to tlw quantum-the01'Y." By Dr. W. H. KEEsmr. Supple ment N°. 30a to the Oommunications ft'om the PhysicaL Labora tory at Leiden. Oommunicated by Prof. H. KAl\IERLINGH ONNES. (Communicated in the meeting of May' 31, 1913). -
A Turbo-Brayton Cryocooler for Future European Observation Satellite Generation
C19_078 1 A Turbo-Brayton Cryocooler for Future European Observation Satellite Generation J. Tanchon1, J. Lacapere1, A. Molyneaux2, M. Harris2, S. Hill2, S.M. Abu-Sharkh2, T. Tirolien3 1Absolut System SAS, Seyssinet-Pariset, France 2Ofttech, Gloucester, United Kingdom 3European Space Agency, Noordwijk, The Netherlands ABSTRACT Several types of active cryocoolers have been developed for space and military applications in the last ten years. Performances and reliability continuously increase to follow the requirements evolution of new generations of satellite: less power consumption, more cooling capacity, increased life duration. However, in addition to this increase of performances and reliability, the microvibrations re- quirement becomes critical. In fact, with the development of vibration-free technologies, classical Earth Observation cryocoolers (Stirling, Pulse Tube) will become the main source of microvibra- tions on-board the satellite. A new generation cryocooler is being developed at Absolut System using very high speed turbomachines in order to avoid any generated perturbations below 1000 Hz. This development is performed in the frame of ESA Technical Research Program - 4000113495/15/NL/KML. This paper presents the status of this development project based on Reverse Brayton cycle with very high speed turbomachines. INTRODUCTION The space cryogenics sector is characterized by a large number of applications (detection, im- aging, sample conservation, propulsion, telecommunications etc.) that lead to various requirements (temperature range, microvibration, lifetime, power consumption etc.) that can be met by different solutions (Stirling or JT coolers, mechanical or sorption compressors etc.). The recent years saw, in Europe, the developments of coolers to meet Earth Observation mission UHTXLUHPHQWVWKDWDUHFDSDEOHWRSURYLGHVLJQL¿FDQWFRROLQJSRZHUDWDQRSHUDWLRQDOWHPSHUDWXUH around 50K (for IR detection). -
First and Second Law Evaluation of Combined Brayton-Organic Rankine Power Cycle
Journal of Thermal Engineering, Vol. 6, No. 4, pp. 577-591, July, 2020 Yildiz Technical University Press, Istanbul, Turkey FIRST AND SECOND LAW EVALUATION OF COMBINED BRAYTON-ORGANIC RANKINE POWER CYCLE Önder Kaşka1, Onur Bor2, Nehir Tokgöz3* Muhammed Murat Aksoy4 ABSTRACT In the present work, we have conducted thermodynamic analysis of an organic Rankine cycle (ORC) using waste heat from intercooler and regenerator in Brayton cycle with intercooling, reheating, and regeneration (BCIRR). First of all, the first law analysis is used in this combined cycle. Several outputs are revealed in this study such as the cycle efficiencies in Brayton cycle which is dependent on turbine inlet temperature, intercooler pressure ratios, and pinch point temperature difference. For all cycles, produced net power is increased because of increasing turbine inlet temperature. Since heat input to the cycles takes place at high temperatures, the produced net power is increased because of increasing turbine inlet temperature for all cycles. The thermal efficiency of combined cycle is higher about 11.7% than thermal efficiency of Brayton cycle alone. Moreover, the net power produced by ORC has contributed nearly 28650 kW. The percentage losses of exergy for pump, turbine, condenser, preheater I, preheater II, and evaporator are 0.33%, 33%, 22%, 23%, 6%, and16% respectively. The differences of pinch point temperature on ORC net power and efficiencies of ORC are investigated. In addition, exergy efficiencies of components with respect to intercooling pressure ratio and evaporator effectiveness is presented. Exergy destructions are calculated for all the components in ORC. Keywords: Brayton Cycle, Organic Rankine Cycle, Bottoming Cycle, Pinch Point Temperature, Waste Heat, Energy and Exergy Analysis INTRODUCTION Thermal energy systems as well as corresponding all parts have been challenged to improve overall efficiency due to lack of conventional fuels, reduce climate change and so on for recent years. -
Design of a Cryogenic Turbine for a Hybrid Cryocooler
Design of a Cryogenic Turbine for a Hybrid Cryocooler by Thomas L. Fraser A thesis submitted in partial fulfillment of the requirements for the degree of Master of Science (Mechanical Engineering) at the UNIVERISTY OF WISCONSIN-MADISON 2006 Approved by _____________________________________________ ______________ Professor Gregory F. Nellis Date i Abstract The hybrid pulse tube-reverse Brayton cycle cryocooler has the potential for cooling to temperatures on the order of 10 K. By using the rectifying interface which converts the oscillating pulse tube flow to continuous flow, both vibrations and low temperature regenerator losses are overcome, making the hybrid an ideal candidate for cooling infrared focal plane arrays which demand low temperature and low vibration. However, the turboexpander within the reverse Brayton cycle is complex and its performance is highly dependent on the performance of its subcomponents, thus necessitating a model predicting the turboexpander performance. A model was developed to predict the performance of the reverse Brayton cycle stage including the recuperative heat exchanger and turboexpander components. The turboexpander was numerically modeled in detail to include the sub-models of rotordynamics, the thermal and leakage performance of the seal, and the turboalternator. Where possible, the models were verified against either an analytical model or experimental data. A parametric analysis was carried out to determine the optimal design and conditions for the turboexpander. ii Acknowledgements First and foremost I would like to thank Greg Nellis. Besides being my advisor for this project he is also responsible for sparking an interest in energy science through his heat transfer courses I took as an undergrad. -
Equation of State for Natural Gas Systems
Equation of State for Natural Gas Systems. m A thesis submitted to the University of London for the Degree of Doctor of Philosophy and for the Diploma of Imperial College by Jorge Francisco Estela-Uribe. Department of Chemical Engineering and Chemical Technology Imperial College of Science, Technology and Medicine. Prince Consort Road, SW7 2BY London, United Kingdom. March 1999. Acknowledgements. I acknowledge and thank the sponsorship I received from the following institutions: Fundacion para el Futuro de Colombia, Colfiituro; Pontificia Universidad Javeriana, Seccional Cali; the Committee of Vice-Chancellors and Principal of the Universities of the United Kingdom and Ruhrgas AG. Without their economic support my stay in London and the completion of this work would have been impossible. My greatest gratitude goes to my Supervisor, Dr Martin Trusler. His expert guidance and advice were always fundamental for the success of this research. He helped me with abundant patience and undying commitment and his optimism regarding the possibilities of the project was always inspirational for me. He also worked shoulder by shoulder with me on solving a good number of experimental problems, some of them were just cases of bad luck and for some prominent ones, I was the only one to blame. Others helped me willingly as well. My labmate, Dr Andres Estrada-Alexanders, was quite helpful in the beginning of my research, and has carried on being so. He not only did do well in his role as the senior student in the laboratory, but also became a good fnend of mine. Another good friend of mine, Dr Abdel Fenghour, has always been an endless source of help and information. -
Appendix a Basics of Landfill
APPENDIX A BASICS OF LANDFILL GAS Basics of Landfill Gas (Methane, Carbon Dioxide, Hydrogen Sulfide and Sulfides) Landfill gas is produced through bacterial decomposition, volatilization and chemical reactions. Most landfill gas is produced by bacterial decomposition that occurs when organic waste solids, food (i.e. meats, vegetables), garden waste (i.e. leaf and yardwaste), wood and paper products, are broken down by bacteria naturally present in the waste and in soils. Volatilization generates landfill gas when certain wastes change from a liquid or solid into a vapor. Chemical reactions occur when different waste materials are mixed together during disposal operations. Additionally, moisture plays a large roll in the speed of decomposition. Generally, the more moisture, the more landfill gas is generated, both during the aerobic and anaerobic conditions. Landfill Gas Production and Composition: In general, during anaerobic conditions, the composition of landfill gas is approximately 50 percent methane and 50 percent carbon dioxide with trace amounts (<1 percent) of nitrogen, oxygen, hydrogen sulfide, hydrogen, and nonmethane organic compounds (NMOCs). The more organic waste and moisture present in a landfill, the more landfill gas is produced by the bacteria during decomposition. The more chemicals disposed in a landfill, the more likely volatile organic compounds and other gasses will be produced. The Four Phases of Bacterial Decomposition: “Bacteria decompose landfill waste in four phases. The composition of the gas produced changes with each of the four phases of decomposition. Landfills often accept waste over a 20-to 30-year period, so waste in a landfill may be undergoing several phases of decomposition at once. -
Supercritical Carbon Dioxide(S-CO2) Power Cycle for Waste Heat Recovery: a Review from Thermodynamic Perspective
processes Review Supercritical Carbon Dioxide(s-CO2) Power Cycle for Waste Heat Recovery: A Review from Thermodynamic Perspective Liuchen Liu, Qiguo Yang and Guomin Cui * School of Energy and Power Engineering, University of Shanghai for Science and Technology, Shanghai 200093, China; [email protected] (L.L.); [email protected] (Q.Y.) * Correspondence: [email protected] Received: 11 October 2020; Accepted: 13 November 2020; Published: 15 November 2020 Abstract: Supercritical CO2 power cycles have been deeply investigated in recent years. However, their potential in waste heat recovery is still largely unexplored. This paper presents a critical review of engineering background, technical challenges, and current advances of the s-CO2 cycle for waste heat recovery. Firstly, common barriers for the further promotion of waste heat recovery technology are discussed. Afterwards, the technical advantages of the s-CO2 cycle in solving the abovementioned problems are outlined by comparing several state-of-the-art thermodynamic cycles. On this basis, current research results in this field are reviewed for three main applications, namely the fuel cell, internal combustion engine, and gas turbine. For low temperature applications, the transcritical CO2 cycles can compete with other existing technologies, while supercritical CO2 cycles are more attractive for medium- and high temperature sources to replace steam Rankine cycles. Moreover, simple and regenerative configurations are more suitable for transcritical cycles, whereas various complex configurations have advantages for medium- and high temperature heat sources to form cogeneration system. Finally, from the viewpoints of in-depth research and engineering applications, several future development directions are put forward. This review hopes to promote the development of s-CO2 cycles for waste heat recovery.