Objectives and Constraints for Wind Turbine Optimization
Total Page:16
File Type:pdf, Size:1020Kb
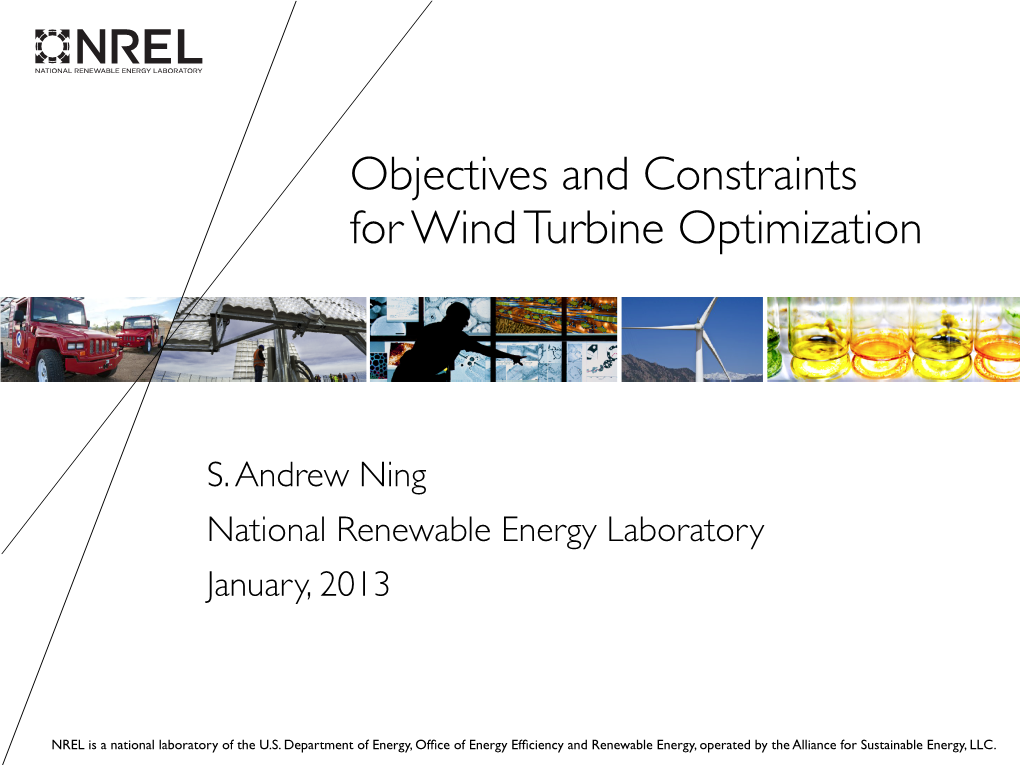
Load more
Recommended publications
-
CHAPTER 7 Design and Development of Small Wind Turbines
CHAPTER 7 Design and development of small wind turbines Lawrence Staudt Center for Renewable Energy, Dundalk Institute of Technology, Ireland. For the purposes of this chapter, “small” wind turbines will be defi ned as those with a power rating of 50 kW or less (approximately 15 m rotor diameter). Small electricity-generating wind turbines have been in existence since the early 1900s, having been particularly popular for providing power for dwellings not yet con- nected to national electricity grids. These turbines largely disappeared as rural electrifi cation took place, and have primarily been used for remote power until recently. The oil crisis of the 1970s led to a resurgence in small wind technology, including the new concept of grid-connected small wind technology. There are few small wind turbine manufacturers with a track record spanning more than a decade. This can be attributed to diffi cult market conditions and nascent technol- ogy. However, the technology is becoming more mature, energy prices are rising and public awareness of renewable energy is increasing. There are now many small wind turbine companies around the world who are addressing the growing market for both grid-connected and remote power applications. The design fea- tures of small wind turbines, while similar to large wind turbines, often differ in signifi cant ways. 1 Small wind technology Technological approaches taken for the various components of a small wind turbine will be examined: the rotor, the drivetrain, the electrical systems and the tower. Of course wind turbines must be designed as a system, and so rotor design affects drivetrain design which affects control system design, etc. -
Implementation and Validation of an Advanced Wind Energy Controller in Aero-Servo-Elastic Simulations Using the Lifting Line Free Vortex Wake Model
energies Article Implementation and Validation of an Advanced Wind Energy Controller in Aero-Servo-Elastic Simulations Using the Lifting Line Free Vortex Wake Model Sebastian Perez-Becker *, David Marten, Christian Navid Nayeri and Christian Oliver Paschereit Chair of Fluid Dynamics, Hermann Föttinger Institute, Technische Universität Berlin, Müller-Breslau-Str. 8, 10623 Berlin, Germany; [email protected] (D.M.); [email protected] (C.N.N.); [email protected] (C.O.P.) * Correspondence: [email protected] Abstract: Accurate and reproducible aeroelastic load calculations are indispensable for designing modern multi-MW wind turbines. They are also essential for assessing the load reduction capabilities of advanced wind turbine control strategies. In this paper, we contribute to this topic by introducing the TUB Controller, an advanced open-source wind turbine controller capable of performing full load calculations. It is compatible with the aeroelastic software QBlade, which features a lifting line free vortex wake aerodynamic model. The paper describes in detail the controller and includes a validation study against an established open-source controller from the literature. Both controllers show comparable performance with our chosen metrics. Furthermore, we analyze the advanced load reduction capabilities of the individual pitch control strategy included in the TUB Controller. Turbulent wind simulations with the DTU 10 MW Reference Wind Turbine featuring the individual pitch control strategy show a decrease in the out-of-plane and torsional blade root bending moment fatigue loads of 14% and 9.4% respectively compared to a baseline controller. Citation: Perez-Becker, S.; Marten, D.; Nayeri, C.N.; Paschereit, C.O. -
The Prediction Model of Characteristics for Wind Turbines Based on Meteorological Properties Using Neural Network Swarm Intelligence
sustainability Article The Prediction Model of Characteristics for Wind Turbines Based on Meteorological Properties Using Neural Network Swarm Intelligence Tugce Demirdelen 1 , Pırıl Tekin 2,* , Inayet Ozge Aksu 3 and Firat Ekinci 4 1 Department of Electrical and Electronics Engineering, Adana Alparslan Turkes Science and Technology University, 01250 Adana, Turkey 2 Department of Industrial Engineering, Adana Alparslan Turkes Science and Technology University, 01250 Adana, Turkey 3 Department of Computer Engineering, Adana Alparslan Turkes Science and Technology University, 01250 Adana, Turkey 4 Department of Energy Systems Engineering, Adana Alparslan Turkes Science and Technology University, 01250 Adana, Turkey * Correspondence: [email protected]; Tel.: +90-322-455-0000 (ext. 2411) Received: 17 July 2019; Accepted: 29 August 2019; Published: 3 September 2019 Abstract: In order to produce more efficient, sustainable-clean energy, accurate prediction of wind turbine design parameters provide to work the system efficiency at the maximum level. For this purpose, this paper appears with the aim of obtaining the optimum prediction of the turbine parameter efficiently. Firstly, the motivation to achieve an accurate wind turbine design is presented with the analysis of three different models based on artificial neural networks comparatively given for maximum energy production. It is followed by the implementation of wind turbine model and hybrid models developed by using both neural network and optimization models. In this study, the ANN-FA hybrid structure model is firstly used and also ANN coefficients are trained by FA to give a new approach in literature for wind turbine parameters’ estimation. The main contribution of this paper is that seven important wind turbine parameters are predicted. -
Qblade Guidelines V0.6
QBlade Guidelines v0.6 David Marten Juliane Wendler January 18, 2013 Contact: david.marten(at)tu-berlin.de Contents 1 Introduction 5 1.1 Blade design and simulation in the wind turbine industry . 5 1.2 The software project . 7 2 Software implementation 9 2.1 Code limitations . 9 2.2 Code structure . 9 2.3 Plotting results / Graph controls . 11 3 TUTORIAL: How to create simulations in QBlade 13 4 XFOIL and XFLR/QFLR 29 5 The QBlade 360◦ extrapolation module 30 5.0.1 Basics . 30 5.0.2 Montgomery extrapolation . 31 5.0.3 Viterna-Corrigan post stall model . 32 6 The QBlade HAWT module 33 6.1 Basics . 33 6.1.1 The Blade Element Momentum Method . 33 6.1.2 Iteration procedure . 33 6.2 The blade design and optimization submodule . 34 6.2.1 Blade optimization . 36 6.2.2 Blade scaling . 37 6.2.3 Advanced design . 38 6.3 The rotor simulation submodule . 39 6.4 The multi parameter simulation submodule . 40 6.5 The turbine definition and simulation submodule . 41 6.6 Simulation settings . 43 6.6.1 Simulation Parameters . 43 6.6.2 Corrections . 47 6.7 Simulation results . 52 6.7.1 Data storage and visualization . 52 6.7.2 Variable listings . 53 3 Contents 7 The QBlade VAWT Module 56 7.1 Basics . 56 7.1.1 Method of operation . 56 7.1.2 The Double-Multiple Streamtube Model . 57 7.1.3 Velocities . 59 7.1.4 Iteration procedure . 59 7.1.5 Limitations . 60 7.2 The blade design and optimization submodule . -
Selection Guidelines for Wind Energy Technologies
energies Review Selection Guidelines for Wind Energy Technologies A. G. Olabi 1,2,*, Tabbi Wilberforce 2, Khaled Elsaid 3,* , Tareq Salameh 1, Enas Taha Sayed 4,5, Khaled Saleh Husain 1 and Mohammad Ali Abdelkareem 1,4,5,* 1 Department of Sustainable and Renewable Energy Engineering, University of Sharjah, Sharjah 27272, United Arab Emirates; [email protected] (T.S.); [email protected] (K.S.H.) 2 Mechanical Engineering and Design, School of Engineering and Applied Science, Aston University, Aston Triangle, Birmingham B4 7ET, UK; [email protected] 3 Chemical Engineering Program, Texas A & M University at Qatar, Doha P.O. Box 23874, Qatar 4 Centre for Advanced Materials Research, University of Sharjah, Sharjah 27272, United Arab Emirates; [email protected] 5 Chemical Engineering Department, Faculty of Engineering, Minia University, Minya 615193, Egypt * Correspondence: [email protected] (A.G.O.); [email protected] (K.E.); [email protected] (M.A.A.) Abstract: The building block of all economies across the world is subject to the medium in which energy is harnessed. Renewable energy is currently one of the recommended substitutes for fossil fuels due to its environmentally friendly nature. Wind energy, which is considered as one of the promising renewable energy forms, has gained lots of attention in the last few decades due to its sustainability as well as viability. This review presents a detailed investigation into this technology as well as factors impeding its commercialization. General selection guidelines for the available wind turbine technologies are presented. Prospects of various components associated with wind energy conversion systems are thoroughly discussed with their limitations equally captured in this report. -
2012JRC Wind Status Report
2012 JRC wind status report Technology, market and economic aspects of wind energy in Europe Roberto Lacal Arántegui, main author. Teodora Corsatea and Kiti Suomalainen, contributing authors. 2012 Report EUR 25647 EN Cover picture: Sunset wind farm. © Jos Beurskens. European Commission Joint Research Centre Institute for Energy and Transport Contact information Roberto Lacal Arántegui Address: Joint Research Centre, Institute for Energy and Transport. Westerduinweg 3, NL-1755 LE Petten, The Netherlands E-mail: [email protected] Tel.: +31 224 56 53 90 Fax: +31 224 56 56 16 http://iet.jrc.ec.europa.eu http://www.jrc.ec.europa.eu This publication is a Reference Report by the Joint Research Centre of the European Commission. Legal Notice Neither the European Commission nor any person acting on behalf of the Commission is responsible for the use which might be made of this publication. Europe Direct is a service to help you find answers to your questions about the European Union Freephone number (*): 00 800 6 7 8 9 10 11 (*) Certain mobile telephone operators do not allow access to 00 800 numbers or these calls may be billed. A great deal of additional information on the European Union is available on the Internet. It can be accessed through the Europa server http://europa.eu/ JRC77895 EUR 25647 EN ISBN 978-92-79-27956-0 (print) ISBN 978-92-79-27955-3 (pdf) ISSN 1018-5593 (print) ISSN 1831-9424 (online) doi:10.2790/72509 Luxembourg: Publications Office of the European Union, 2013 © European Union, 2013 Reproduction is authorised provided the source is acknowledged. -
Design and Simulation of a Wind Turbine for Electricity Generation
International Journal of Applied Engineering Research ISSN 0973-4562 Volume 13, Number 23 (2018) pp. 16409-164717 © Research India Publications. http://www.ripublication.com Design and Simulation of a Wind Turbine for Electricity Generation 1Daniyan, I. A., 2Daniyan, O. L., 3Adeodu, A. O., 3Azeez, T. M. and 3Ibekwe, K. S. 1Department of Industrial Engineering, Tshwane University of Technology, Pretoria, South Africa. 2Centre for Basic Space Science, University of Nigeria, Nsukka, Nigeria. 3Department of Mechanical & Engineering, Afe Babalola University, Ado Ekiti, Nigeria. Abstract per square meter of swept area of a turbine. The wind power density, measured in watts per square meter, shows how much This study is focuses on the design of a cost effective wind energy is accessible at the site for transformation by a wind turbine for electricity generation using locally sourced turbine Wind turbine can be vertical, horizontal upward or materials. The design of the turbine takes into the reduction in downward (; Gordan et al., 2001; Gasch et al., 2002; Horikiri, the weight and size of the turbine thereby lowering production 2011). Aerodynamic lift is the force that overcomes gravity and and installation costs. This increases the efficiency by is in a right angled direction to the wind flow. It occurs due to increasing the resistance from dynamic loads and reduction of the uneven at pressure on the upper and lower aerofoil surfaces acoustic noise discharge. The locally sourced materials (Gosh, 2002) while aerodynamic drag force is parallel to the employed include the; blades, hub, a permanent magnet motor direction of oncoming wind motion (Dabiri, 2011). Drag occurs as generator, tower, electric starter and fan as well as a due to uneven pressure on the upper and lower aerofoil surfaces controller. -
The Mechanical Design, Analysis, and Testing of a Two-Bladed Wind Turbine Hub
June 2002 • NREL/TP-500-26645 The Mechanical Design, Analysis, and Testing of a Two-Bladed Wind Turbine Hub J. Cotrell National Renewable Energy Laboratory 1617 Cole Boulevard Golden, Colorado 80401-3393 NREL is a U.S. Department of Energy Laboratory Operated by Midwest Research Institute • Battelle • Bechtel Contract No. DE-AC36-99-GO10337 June 2002 • NREL/TP-500-26645 The Mechanical Design, Analysis, and Testing of a Two-Bladed Wind Turbine Hub J. Cotrell Prepared under Task No. WER2.1460 National Renewable Energy Laboratory 1617 Cole Boulevard Golden, Colorado 80401-3393 NREL is a U.S. Department of Energy Laboratory Operated by Midwest Research Institute • Battelle • Bechtel Contract No. DE-AC36-99-GO10337 NOTICE This report was prepared as an account of work sponsored by an agency of the United States government. Neither the United States government nor any agency thereof, nor any of their employees, makes any warranty, express or implied, or assumes any legal liability or responsibility for the accuracy, completeness, or usefulness of any information, apparatus, product, or process disclosed, or represents that its use would not infringe privately owned rights. Reference herein to any specific commercial product, process, or service by trade name, trademark, manufacturer, or otherwise does not necessarily constitute or imply its endorsement, recommendation, or favoring by the United States government or any agency thereof. The views and opinions of authors expressed herein do not necessarily state or reflect those of the United States government or any agency thereof. Available electronically at http://www.osti.gov/bridge Available for a processing fee to U.S. -
Never Installed Vestas V90 3 MW Brochure
Never Used Turbine! -technical brochure- ! !VESTAS! !V90 3MW Proven technology to safeguard your investment ! ! ! !What is Never Installed Turbine?! !Included in the scope! What’s in a name. Never Used Turbines are brand The Never Used Turbine is supplied consisting of new wind turbines, produced few years ago and the following main components: delivered by OEM’s to the hands of project • Nacelle owners. Due to some reasons, such as legislation • Hub change, difficulties with finalization of the project • 1 set of blades development and others, the project owners were • 80 m tower not able to erect these turbines and made a • Elevator decision to offer them for sale. • Foundation ring ! • Transport frames (nacelle and blades) In order to keep the turbines in good shape till the • 60 days of free storage and security moment they get commissioned, the owners have ! been taking a very good care over the equipment The following items are not included in the scope of by investing money in proper and secure storage our basic offer, please consult our team to proceed conditions, as well as in the conservation and with a request: maintenance services during all period of storage ! in accordance with OEM’s recommendations. • Technical survey ! • Customized retrofit As the result, the turbines are present in «as new» • Customized upgrade (SCADA, etc.) visual and technical condition, while the level of • Loading investment is almost half than for similar new • Transportation turbines. In order to guarantee the safety of • Installation & Commissioning your investments, technical inspection and visit • Switchgear supply can be scheduled on request. -
Proposed Design of Small-Scale Wind Turbine to Run Low-Power
Proposed Design of Small‐Scale Wind Turbine to Run Low‐Power Application for Humanitarian Aid Air Breeze [1] Devon Heston Samantha Bonner Pei Chan ME 340 and ME 297, Spring 2018 Mechanical Engineering Department Pennsylvania State University 22 April 2018 Proposed Design of Small‐Scale Wind Turbine to Run Low‐Power Application for Humanitarian Aid Devon Heston Samantha Bonner Pei Chan ME 340 and ME 297, Spring 2018 Mechanical Engineering Department Pennsylvania State University 22 April 2018 Summary This document proposes a small-scale wind turbine as a potential solution for the heat stroke epidemic in sub-Saharan Africa. In sub-Saharan Africa, rising global temperatures have caused the number of deaths due to heat stroke and other heat related illnesses to dramatically increase in recent years [2]. For sub-Saharan nations like Guinea, limited access to electricity makes the problem even worse, preventing most residents from using central cooling systems in their homes. With that in mind, our team will develop and test a small-scale wind turbine that can power a portable fan, improving in-home ventilation on as-needed basis. Since wind conditions can be unpredictable, our product will incorporate a battery back-up, allowing for consistent performance regardless of weather conditions. Using well-established concept generation techniques, our team selected a design for the small-scale turbine that will power our cooling system. Our selected design uses a horizontal- axis configuration with three blades and a yaw bearing. That bearing will allow the blades to maximize wind currents, regardless of their direction. For durability, our bearing will interface with a metal post and weatherproof enclosure. -
Design Tool for Offshore Wind Farm Clusters
Downloaded from orbit.dtu.dk on: Dec 21, 2017 Design tool for offshore wind farm clusters Hasager, Charlotte Bay; Giebel, Gregor; Waldl, Igor; Schepers, Gerard Published in: DEWEK 2015, 12th German Wind Energy Conference. Book of Abstracts Publication date: 2015 Document Version Publisher's PDF, also known as Version of record Link back to DTU Orbit Citation (APA): Hasager, C. B., Giebel, G., Waldl, I., & Schepers, G. (2015). Design tool for offshore wind farm clusters. In DEWEK 2015, 12th German Wind Energy Conference. Book of Abstracts (pp. 70). DEWI. General rights Copyright and moral rights for the publications made accessible in the public portal are retained by the authors and/or other copyright owners and it is a condition of accessing publications that users recognise and abide by the legal requirements associated with these rights. • Users may download and print one copy of any publication from the public portal for the purpose of private study or research. • You may not further distribute the material or use it for any profit-making activity or commercial gain • You may freely distribute the URL identifying the publication in the public portal If you believe that this document breaches copyright please contact us providing details, and we will remove access to the work immediately and investigate your claim. organised by: 19 / 20 May 2015 Bremen, Germany 12th German Wind Energy Conference Book of Abstracts Message of GreetinG By sigmar GABriel PATRON DeWeK 2015 Wind power is the workhorse of the German Energiewende (energy transi- tion). It accounts for every third kilowatt hour of electricity generated from renewable energy sources in Germany. -
Design Tool for Offshore Wind Farm Clusters
Downloaded from orbit.dtu.dk on: Oct 04, 2021 Design tool for offshore wind farm clusters Hasager, Charlotte Bay; Giebel, Gregor; Waldl, Igor; Schepers, Gerard Published in: DEWEK 2015, 12th German Wind Energy Conference. Book of Abstracts Publication date: 2015 Document Version Publisher's PDF, also known as Version of record Link back to DTU Orbit Citation (APA): Hasager, C. B., Giebel, G., Waldl, I., & Schepers, G. (2015). Design tool for offshore wind farm clusters. In DEWEK 2015, 12th German Wind Energy Conference. Book of Abstracts (pp. 70). DEWI. General rights Copyright and moral rights for the publications made accessible in the public portal are retained by the authors and/or other copyright owners and it is a condition of accessing publications that users recognise and abide by the legal requirements associated with these rights. Users may download and print one copy of any publication from the public portal for the purpose of private study or research. You may not further distribute the material or use it for any profit-making activity or commercial gain You may freely distribute the URL identifying the publication in the public portal If you believe that this document breaches copyright please contact us providing details, and we will remove access to the work immediately and investigate your claim. organised by: 19 / 20 May 2015 Bremen, Germany 12th German Wind Energy Conference Book of Abstracts Message of GreetinG By sigmar GABriel PATRON DeWeK 2015 Wind power is the workhorse of the German Energiewende (energy transi- tion). It accounts for every third kilowatt hour of electricity generated from renewable energy sources in Germany.