Title of the Thesis
Total Page:16
File Type:pdf, Size:1020Kb
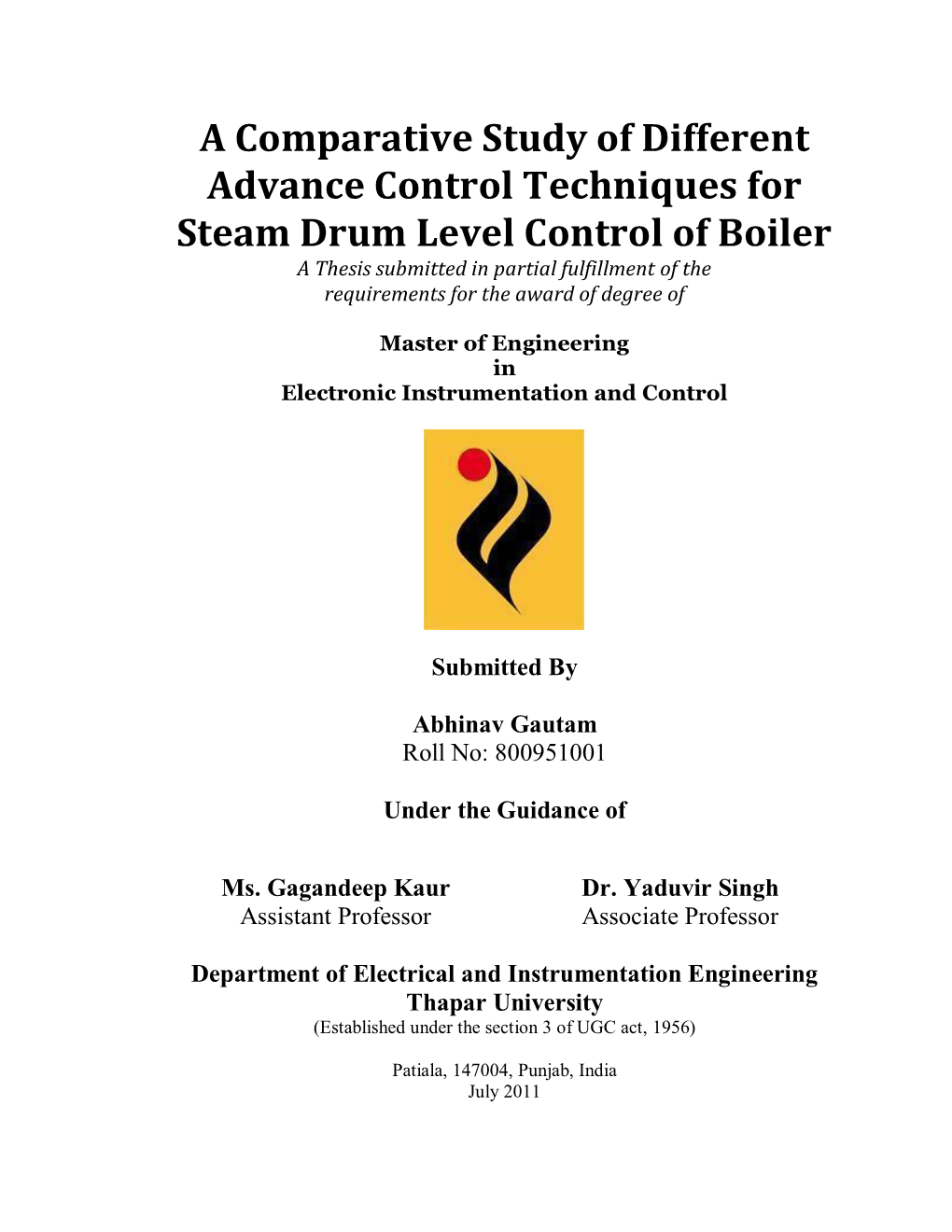
Load more
Recommended publications
-
Module BESTT MS1
Module BESTT MS1 Marine Steam Boiler Types, Construction and Maintenance. Aim This unit introduces learners to the wide variety of fuels which may be encountered in steam launches and small steam ships operating on inland waterways or sheltered coastal waters. The range of types of boilers is explained. In each case, the benefits of each fuel type or boiler type are explored. The reasons for caution when conducting external work on old boilers are explained. INTRODUCTION Boiler types considered Horizontal Fire Tube boilers (including locomotive type) Vertical Fire Tube boilers Horizontal Drum Water Tube boilers Vertical Drum Water Tube boilers Single coil (or Flash) boilers Construction, design and general arrangements Heat transfer Cleaning Considerations for boiler choice and design Options for materials and insulations Boiler cladding materials The sheer variety of boiler types used in marine applications is wider than anything we will encounter for railway locomotives or in road steam applications. Although fire tube boilers from earliest days have been the norm for railway locomotives, water tube boilers could also very occasionally be found in locomotives. The well-known Sentinel shunters had water tube boilers a little bigger but otherwise similar to the company’s steam wagon boilers, and Sir Nigel Gresley on the LNER experimented with a ‘Yarrow’ type boiler but dropped the idea and fitted Britain’s only 4-6-4 express engine with a traditional loco boiler. For shipping, various forms of the classic marine multi-furnace fire tube ‘Scotch’ boiler was a norm to the last, and vertical fire tube types were a standard for small steam launches, but alongside these a huge range of highly efficient water tube types was under constant development resulting in many different configurations. -
Superheated Steam Boiler
A boiler is a closed vessel in which water or other fluid is heated. The heated or vaporized fluid exits the boiler for use in various processes or heating applications. [1][2] Contents [hide ] • 1 Overview o 1.1 Materials o 1.2 Fuel o 1.3 Configurations o 1.4 Safety • 2 Superheated steam boilers • 3 Supercritical steam generators o 3.1 History of supercritical steam generation • 4 Hydronic boilers • 5 Accessories o 5.1 Boiler fittings and accessories o 5.2 Steam accessories o 5.3 Combustion accessories o 5.4 Other essential items • 6 Controlling draft • 7 See also • 8 References • 9 Further reading • 10 External links Overview [edit ] Materials The pressure vessel in a boiler is usually made of steel (or alloy steel), or historically of wrought iron . Stainless steel is virtually prohibited (by the ASME Boiler Code) for use in wetted parts of modern boilers, but is used often in superheater sections that will not be exposed to liquid boiler water. In live steam models, copper or brass is often used because it is more easily fabricated in smaller size boilers. Historically, copper was often used for fireboxes (particularly for steam locomotives ), because of its better formability and higher thermal conductivity; however, in more recent times, the high price of copper often makes this an uneconomic choice and cheaper substitutes (such as steel) are used instead. For much of the Victorian "age of steam", the only material used for boilermaking was the highest grade of wrought iron, with assembly by rivetting . This iron was often obtained from specialist ironworks , such as at Cleator Moor (UK), noted for the high quality of their rolled plate and its suitability for high-reliability use in critical applications, such as high-pressure boilers. -
Boiler a Boiler Is a Closed Vessel in Which Water Or Other Fluid Is Heated
Boiler A boiler is a closed vessel in which water or other fluid is heated. The fluid does not necessarily boil. (In North America the term "furnace" is normally used if the purpose is not actually to boil the fluid.) The heated or vaporized fluid exits the boiler for use in various processes or heating applications, including water heating, central heating, boiler-based power generation,cooking, and sanitation. Contents • 1 Materials • 2 Energy • 3 Configurations • 4 Safety • 5 Superheated steam boilers 5.1 Supercritical steam generator • 6 Accessories 6.1 Boiler fittings and accessories 6.2 Steam accessories 6.3 Combustion accessories 6.4 Other essential items 6.5 Gas safe check • 7 Draught • 8 See also • 9 References • 10 Further reading Materials The pressure vessel of a boiler is usually made of steel (or alloy steel), or historically of wrought iron. Stainless steel, especially of the austenitic types, is not used in wetted parts of boilers due to corrosion and stress corrosion cracking. However, ferritic stainless steel is often used in superheater sections that will not be exposed to boiling water, and electrically-heated stainless steel shell boilers are allowed under the European "Pressure Equipment Directive" for production of steam for sterilizers and disinfectors. In live steam models, copper or brass is often used because it is more easily fabricated in smaller size boilers. Historically, copper was often used for fireboxes(particularly for steam locomotives), because of its better formability and higher thermal conductivity; however, in more recent times, the high price of copper often makes this an uneconomic choice and cheaper substitutes (such as steel) are used instead. -
Boiler (Steam Generator)
Boiler (steam generator) From Wikipedia, the free encyclopedia Jump to: navigation, search It has been suggested that this article or section be merged into Boiler. (Discuss) Contents [hide] 1 Steam generator (component of prime mover) 2 Boiler types o 2.1 Haycock and wagon top boilers o 2.2 Cylindrical fire-tube boiler o 2.3 Multi-tube boilers 3 Structural resistance 4 Combustion o 4.1 Solid fuel firing o 4.2 Firetube boiler o 4.3 Superheater o 4.4 Water tube boiler o 4.5 Supercritical steam generator 5 Water treatment 6 Boiler safety o 6.1 Doble boiler 7 Essential boiler fittings o 7.1 Boiler fittings 8 Steam accessories 9 Combustion accessories 10 Application of steam boilers 11 See also 12 References A boiler or steam generator is a device used to create steam by applying heat energy to water. Although the definitions are somewhat flexible, it can be said that older steam generators were commonly termed boilers and worked at low to medium pressure (1–300 psi/0.069–20.684 bar; 6.895–2,068.427 kPa), but at pressures above this it is more usual to speak of a steam generator. An industrial boiler, originally used for supplying steam to a stationary steam engine A boiler or steam generator is used wherever a source of steam is required. The form and size depends on the application: mobile steam engines such as steam locomotives, portable engines and steam-powered road vehicles typically use a smaller boiler that forms an integral part of the vehicle; stationary steam engines, industrial installations and power stations will usually have a larger separate steam generating facility connected to the point-of-use by piping. -
Materialsedit$
A boiler is a closed vessel in which water or other fluid is heated. The fluid does not necessarily boil. (In North America the term "furnace" is normally used if the purpose is not actually to boil the fluid.) The heated or vaporized fluid exits the boiler for use in various processes or heatin applications! #$ %$ includin water heatin! central heatin! boiler&based power eneration! coo'in! and sanitation. Contents hide$ • # aterials • % nery • * +onfiurations • , -afety • -uperheated steam boilers o .# -upercritical steam enerator • / Accessories o /.# 0oiler fittins and accessories o /.% -team accessories o /.* +ombustion accessories o /., 1ther essential items o /. 2as safe chec' • 3 4rauht • 5 -ee also • 6 7eferences • #8 9urther readin Materialsedit$ The pressure vessel of a boiler is usually made of steel (or alloy steel)! or historically of wrouht iron. -tainless steel! especially of the austenitic types! is not used in wetted parts of boilers due to corrosion and stress corrosion crac'in. *$ :owever! ferritic stainless steel is often used in superheater sections that will not be exposed to boilin water ! and electrically&heated stainless steel shell boilers are allowed under the uropean ";ressure <uipment 4irective" for production of steam for sterilizers and disinfectors.,$ In live steam models! copper or brass is often used because it is more easily fabricated in smaller size boilers. :istorically! copper was often used for fireboxes (particularly for steam locomotives)! because of its better formability and hiher thermal conductivity= however! in more recent times! the hih price of copper often ma'es this an uneconomic choice and cheaper substitutes (such as steel) are used instead. -
Crewe Locomotive Drawings and Microfilm Lists
Crewe Drawings and Microfilm Lists Description: The drawings relate to the period when the Crewe Locomotive works was engaged in the construction and repair of steam locomotives. As well as a selection from the main series of drawings as listed in the Registers from the Crewe Drawing Office the collection includes many drawings that were not allocated numbers. These have been allocated artificial numbers for ease of access. There are also selections of drawings from the Second World War period relating to 2-8-0 locomotives built for the War Department, drawings from the supplier William Beardmore & Company, and a small series of drawings from the former Lancaster & Carlisle Railway Company. The collection includes drawings of machinery such as the tugboat boilers for the Shropshire Union Canal Co. and pumping equipment for Llandovery and Prestatyn Stations and some details of building works such as the drains at the Mechanics Institute. System of arrangement: The drawings have been listed in six separate sequences: Main Series: numbered drawings as per the company drawing register Un-Numbered drawings for which the NRM has provided an artificial number Folded drawings, mainly historical War Department 2-8-0 Drawings William Beardmore & Company drawings Lancaster & Carlisle Railway Company drawings There are also three series of microfilm: Main Series, Prince of Wales Class and Coronation Class (please see seperate list). Further reference may usefully be made to the drawing office registers, which are accessible through Search Engine. Physical Characteristics: The majority of the drawings are on wax linen and are in good condition for their age. A small minority are on untreated paper or tracing paper and are therefore fragile. -
Cibo Energy Efficiency Handbook
CIBO ENERGY EFFICIENCY HANDBOOK COUNCIL OF INDUSTRIAL BOILER OWNERS (CIBO) 6035 BURKE CENTRE PARKWAY, SUITE 360 BURKE, VA 22015 EDITED BY RONALD A. ZEITZ Notice of Disclaimer This Energy Efficiency Handbook has been prepared by the Council of Industrial Boiler Owners (CIBO). Neither CIBO nor any of its members, nor any person acting on behalf of them, make any representation or warranty whatsoever, whether express or implied, or assume any legal liability, regarding the completeness or accuracy of the information contained herein, with respect to the use of any information, apparatus, method, process, or similar item disclosed in this handbook, including merchantability and fitness for a particular purpose; or that any such use does not infringe on or inter fere with privately owned rights, including any party’s intellectual property. Furthermore, neither CIBO nor any of its members, nor any person acting on behalf of them, assume any responsibility resulting from any person’s selection or use of this re- port or of any information, apparatus, method, process, or similar item described in this report. Reference to any specific commercial product, process, or service by trade name, trademark, manufacturer, or otherwise does not constitute or imply its endorse ment, recommendation, or favoring. The views and opinions of the authors expressed herein do not necessarily state or reflect those of the United States Government, any state government, or any federal or state agency thereof. Any person wishing to use the information, technologies, or procedures described herein should consult with a quali fied expert to ascertain their fitness for the intended use. -
Publication SC167.Pub
No 167 January 2021 2½” Gauge Tich John Pickering www.n25ga.org Your contacts in the Association are :- PRESIDENT VICE PRESIDENT Paul Wiese Des Adeley Tel: 07813-595415 Tel : 01722-718463 Email : [email protected] CASTINGS SERVICE DRAWINGS SERVICE & ARCHIVIST Brian Kerens John Baguley ‘Hycroft’ 7 Albert Drive, Deganwy, 121 Western Road, Mickleover, Conway, Gwynedd. LL31 9SP Derby. DE3 9GR. Tel : 01492-592046 Tel : 01332-515284 Email : [email protected] Email : [email protected] MEMBERSHIP & RENEWALS TREASURER Rob Postlethwaite Simon Fish 23, Bedford Crescent, 104 Westenra Avenue, Bristol. BS7 9PP Ellesmere Port, Tel: 01179-513513 South Wirral CH65 3AZ Email: [email protected] Tel : 01513-561246 Email : [email protected] NATIONAL SECRETARY TRANSFERS SERVICE John Baguley David Smith Tel : 01332-515284 Tel: 02084-626799 Email : [email protected] Email : [email protected] BOILER TESTER - SOUTH BOILER TESTER - NORTH William Powell (Dorset) Steve Eaton (Nottinghamshire) Tel: 07852279964 Tel: 07790761235 Email: [email protected] John Baguley (Derbyshire) Tel : 01332-515284 SOUTH EAST & WEST RALLIES MIDLANDS & NORTHERN RALLIES William Powell Steve Eaton Tel: 07852279964 Tel: 07790761235 Email: [email protected] Email: [email protected] Steam Chest Editor & Construction Booklets Cedric Norman 1 Litton Close, Belper, Derbyshire. DE56 1EW Tel: 01773-822408 Email: [email protected] This journal is produced for the Members of the National 21∕2“ Gauge Association. If you wish to distribute or reuse any of the content, please seek -
A Performance Comparison of PID, FLC & MPC Controller
A Performance Comparison Of PID, FLC & MPC Controller: A Comparative Case Study Thesis submitted in partial fulfilment of the requirement for the award of degree of Master of Engineering in Electronics Instrumentation and Control Engineering SUBMITTED By: Sachin Agrahari ROLL NO: 80751020 Under the supervision of: Dr.Yaduvir Singh Dr.Hardeep Singh Assost. Professor, EIED Assist. Professor, ECED DEPARTMENT OF ELECTRICAL AND INSTRUMENTATION ENGINEERING THAPAR UNIVERSITY PATIALA – 147004 JULY 2009 i ii ABSTRACT This work provides the knowledge about the advance technique like Fuzzy Logic controller technique and MPC, Modal Predictive control technique, to get the better response of the system, when input like unit step input and unit ramp input is applied as the set point of the system. A comparative study is made on the performance of the PID,FLC and MPC controller getting better system parameter like Maximum overshoot( M p ),Rise time(t r ),Peak time(t p ) Settling time( t s ),Steady state error( ess ).Finally a simulation block is made using simulink library browser where all the blocks are given. In the response it is found that settling time, rise time steady state error is less in case of MPC controller rather than PID and FLC controller. Study shows more accurate result using Fuzzy controller over PID controller, further better result got in case of MPC controller. iii ORGANIZATION OF THESIS Chapter-1 It includes the background information and overview of thesis report. Chapter-2 This chapter describes the fundamental of boiler is and detailed building blocks of simulation model of three element control. -
Sports Car Sidney Zafran Science Technology
DEVELOPMENT OF A STEAM POWERED SPORTS CAR by WILLIAM B. FLEISCHER AND SIDNEY ZAFRAN SUBMITTED IN PARTIAL FULFILlMENT OF THE REQUIREMENT FOR THE DEGREE OF BACHELOR OF SCIENCE AT THE MASSACHUSETTS INSTITUTE OF TECHNOLOGY May 20, 1957 t:j Signature of Authors ~F"""-.''''''.- • -. .. Certified by •••• _ •••••• /' Thesis Supervisor 379 Marlborough Street Boston, Massachusetts 493 Washington Street Brighton, Massachusetts May 20, 1957 MI. Leicester F. Hamilton Secretary of the Faculty Massachusetts Institute of Technology Cambridge 39, Massachusetts Dear Mr. Hamilton: This thesis, entitled, "Development of a Steam Powered Sports Car", is hereby submitted in partial fulfillment of the requirements for the degree of Bachelor of Science in Mechanical Engineering. Respectfully submitted, , ~ ....'r/i .. William B. Fleischer .~J Sidney zat/an {,/ // i FOREWORD The recent appearance of a quite modern steam car built by Charles F. Keen of Madison, Wisconsin, gave us the idea of attempting to build a steam sports car. Although this particular application may be novel, the idea of a steam powered car is not new. Extensive work was done on it at the turn of the century and many working models were sold. These steam cars co~peted with internal combustion engine designs for a few decades, but suddenly disappeared from the scene. By 1930 the market for steam cars had vanished. Since that time little work has been done on improving older models or building new ones. As a consequence the internal combustion engine car now has tremendous advantages in the field of automobile design. A great wealth of technological knowledge has been poured into the internal combustion engine, thereby putting it in the position where it is now used almost exclusively as the prime mover in automotive applications.