Properties of Fuels
Total Page:16
File Type:pdf, Size:1020Kb
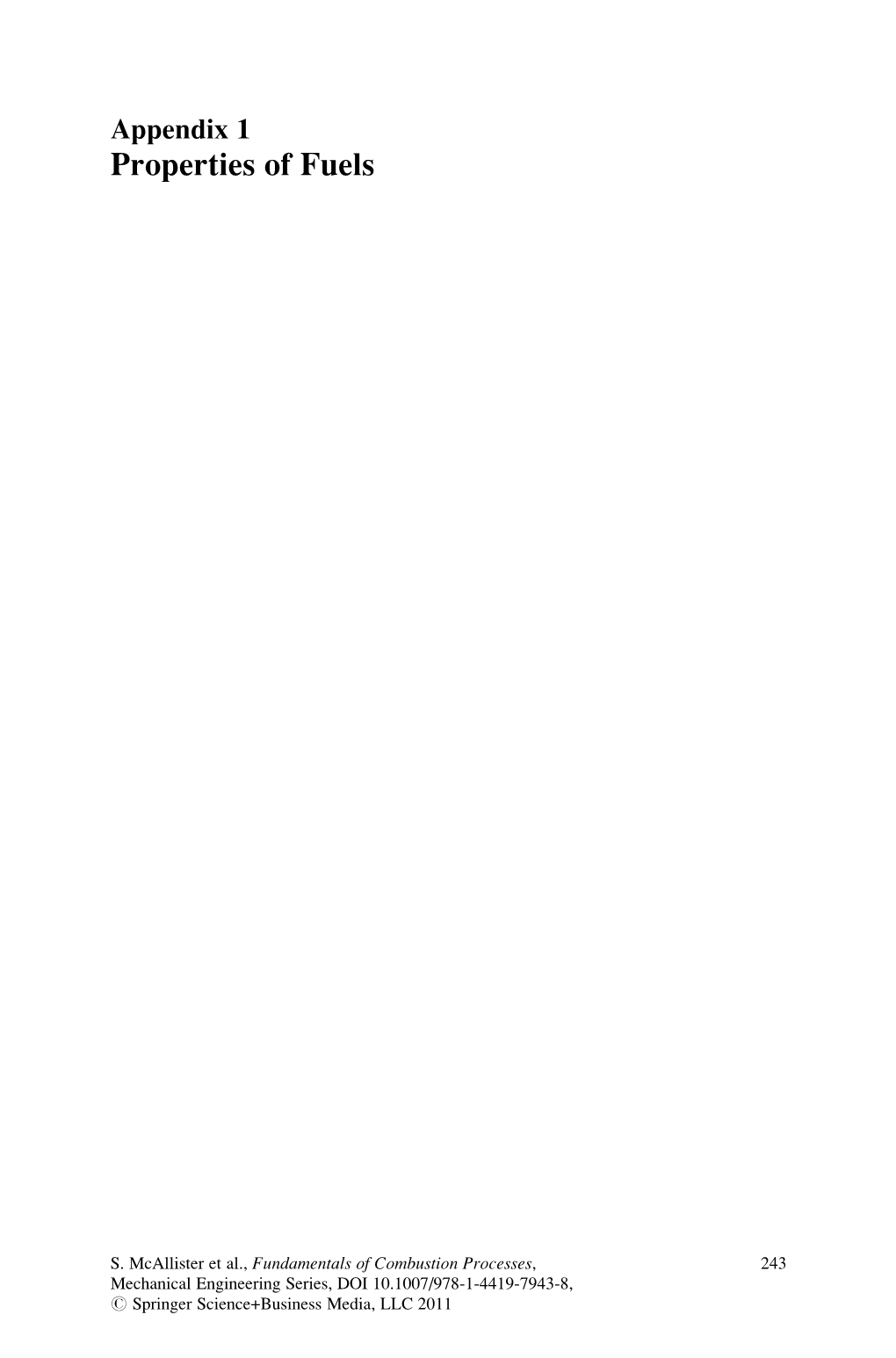
Load more
Recommended publications
-
Review of Market for Octane Enhancers
May 2000 • NREL/SR-580-28193 Review of Market for Octane Enhancers Final Report J.E. Sinor Consultants, Inc. Niwot, Colorado National Renewable Energy Laboratory 1617 Cole Boulevard Golden, Colorado 80401-3393 NREL is a U.S. Department of Energy Laboratory Operated by Midwest Research Institute • Battelle • Bechtel Contract No. DE-AC36-99-GO10337 May 2000 • NREL/SR-580-28193 Review of Market for Octane Enhancers Final Report J.E. Sinor Consultants, Inc. Niwot, Colorado NREL Technical Monitor: K. Ibsen Prepared under Subcontract No. TXE-0-29113-01 National Renewable Energy Laboratory 1617 Cole Boulevard Golden, Colorado 80401-3393 NREL is a U.S. Department of Energy Laboratory Operated by Midwest Research Institute • Battelle • Bechtel Contract No. DE-AC36-99-GO10337 NOTICE This report was prepared as an account of work sponsored by an agency of the United States government. Neither the United States government nor any agency thereof, nor any of their employees, makes any warranty, express or implied, or assumes any legal liability or responsibility for the accuracy, completeness, or usefulness of any information, apparatus, product, or process disclosed, or represents that its use would not infringe privately owned rights. Reference herein to any specific commercial product, process, or service by trade name, trademark, manufacturer, or otherwise does not necessarily constitute or imply its endorsement, recommendation, or favoring by the United States government or any agency thereof. The views and opinions of authors expressed herein do not necessarily state or reflect those of the United States government or any agency thereof. Available electronically at http://www.doe.gov/bridge Available for a processing fee to U.S. -
APPENDIX M SUMMARY of MAJOR TYPES of Carfg2 REFINERY
APPENDIX M SUMMARY OF MAJOR TYPES OF CaRFG2 REFINERY MODIFICATIONS Appendix M: Summan/ of Major Types of CaRFG2 Refinery Modifications: Alkylation Units A process unit that combines small-molecule hydrocarbon gases produced in the FCCU with a branched chain hydrocarbon called isobutane, producing a material called alkylate, which is blended into gasoline to raise the octane rating. Alkylate is a high octane, low vapor pressure gasoline blending component that essentially contains no olefins, aromatics, or sulfur. This plant improves the ultimate gasoline-making ability of the FCC plant. Therefore, many California refineries built new or modified existing units to increase alkylate production to blend and to produce greater amounts of CaRFG2. Alkylate is produced by combining C3, C4, and C5 components with isobutane (nC4). The process of alkylation is the reverse of cracking. Olefins (such as butenes and propenes) and isobutane are used as feedstocks and combined to produce alkylate. This process enables refiners to utilize lighter components that otherwise could not be blended into gasoline due to their high vapor pressures. Feed to alkylation unit can include pentanes from light cracked gasoline treaters, isobutanes from butane isomerization unit, and C3/C4 streams from delayed coking units. Isomerization Units - C4/C5/C6 A refinery that has an alkylation plant is not likely to have exactly enough is-butane to match the proplylene and butylene (olefin) feeds. The refiner usually has two choices - buy iso-butane or make it in a butane isomerization (Bl) plant. Isomerization is the rearrangement of straight chain hydrocarbon molecules to form branched chain products or to convert normal paraffins to their isomer. -
Methane Hydrocarbon Compounds During Wintertime in Beijing
Atmos. Chem. Phys. Discuss., doi:10.5194/acp-2016-783, 2016 Manuscript under review for journal Atmos. Chem. Phys. Published: 16 December 2016 c Author(s) 2016. CC-BY 3.0 License. The levels, variation characteristics and sources of atmospheric non- methane hydrocarbon compounds during wintertime in Beijing, China Chengtang Liu1,3, Yujing Mu1,2 *, Junfeng Liu1,3, Chenglong Zhang1,3, Yuanyuan Zhang1,3, Pengfei 5 Liu1,3, Hongxing Zhang1,4 1Research Center for Eco-Environmental Sciences, Chinese Academy of Sciences, Beijing 100085, China 2Center for Excellence in Regional Atmospheric Environment, Institute of Urban Environment, Chinese Academy of Sciences, Xiamen 361021, China 3University of Chinese Academy of Sciences, Beijing 100085, China 10 4Beijing Urban Ecosystem Research Station, Beijing, 100085, China Correspondence to: Yujing Mu ([email protected]) Abstract. Atmospheric non-methane hydrocarbon compounds (NMHCs) were measured at a sampling site in Beijing city from 15 December 2015 to 14 January 2016 to recognize their pollution levels, variation characteristics and sources. Fifty- 15 three NMHCs were quantified and the proportions of alkanes, alkenes, acetylene and aromatics to the total NMHCs were 49.8% ~ 55.8%, 21.5% ~ 24.7%, 13.5% ~ 15.9% and 9.3% ~ 10.7%, respectively. The variation trends of the NMHCs concentrations were basically identical and exhibited remarkable fluctuation, which were mainly ascribed to the variation of meteorological conditions, especially wind speed. The diurnal variations of NMHCs in clear days exhibited two peaks during the morning and evening rush hours, whereas the rush hours’ peaks diminished or even disappeared in the haze days, 20 implying that the relative contribution of the vehicular emission to atmospheric NMHCs depended on the pollution status. -
Isopentane Ipt
ISOPENTANE IPT CAUTIONARY RESPONSE INFORMATION 4. FIRE HAZARDS 7. SHIPPING INFORMATION 4.1 Flash Point: -70°F C.C. 7.1 Grades of Purity: Research: 99.99%; pure: Common Synonyms Watery liquid Colorless Gasoline-like odor (approx.) 99.4%; technical: 97% 2-Methylbutane 4.2 Flammable Limits in Air: 1.4%-8.3% 7.2 Storage Temperature: Ambient Floats on water. Flammable, irritating vapor is produced. Boiling point 4.3 Fire Extinguishing Agents: Dry 7.3 Inert Atmosphere: No requirement chemical, foam, or carbon dioxide is 82°F. 7.4 Venting: Open (flame arrester) or pressure- 4.4 Fire Extinguishing Agents Not to Be vacuum Evacuate. Used: Water may be ineffective 7.5 IMO Pollution Category: C Keep people away. 4.5 Special Hazards of Combustion Wear goggles and self-contained breathing apparatus. Products: Not pertinent 7.6 Ship Type: 3 Shut off ignition sources and call fire department. 4.6 Behavior in Fire: Highly volatile liquid. 7.7 Barge Hull Type: Currently not available Avoid contact with liquid and vapor. Vapors may explode when mixed with air. Stay upwind and use water spray to ``knock down'' vapor. Notify local health and pollution control agencies. 4.7 Auto Ignition Temperature: 800°F 8. HAZARD CLASSIFICATIONS 4.8 Electrical Hazards: Not pertinent 8.1 49 CFR Category: Flammable liquid FLAMMABLE. Fire 4.9 Burning Rate: 7.4 mm/min. 8.2 49 CFR Class: 3 Flashback along vapor trail may occur. 4.10 Adiabatic Flame Temperature: Currently 8.3 49 CFR Package Group: I Vapor may explode if ignited in an enclosed area. -
Kinetic Modeling for PAH Formation in a Counterflow Diffusion Flame of Isobutane
27th ICDERS July 28th – August 2nd, 2019 Beijing, China Kinetic modeling for PAH formation in a counterflow diffusion flame of isobutane Wei-Kai Chiua, Hairong Taob, Kuang C. Linc,* aDepartment of Mechanical and Electro-Mechanical Engineering,Kaohsiung 80424, National Sun Yat-Sen University, Taiwan bCollege of Chemistry, Beijing Normal University, Beijing 100875, China cEngineering and System Science,Hsinchu 30013, National Tsing Hua University, Taiwan 1 Abstract In the purpose of understanding the complex chemistry of aromatic hydrocarbon formation in diffusion flames of isobutane oxidation, mechanism that consists of 300 species and 11790 reactions is employed for verifying experimental measurements. The kinetic mechanism is incorporated into a 1-D axisymmetric laminar finite-rate model of a counterflow flame to compute the species profiles. Furthermore, the reaction pathway diagram produced by rate of production analysis illustrates the correlation between the decomposition of isobutane and formation of the target species. Keywords: isobutane, counterflow diffusion flame, paromatic hydrocarbon, chemical kinetic modeling 2 Introduction Isobutane (iC4H10) is an isomer of butane and flammable gas. Although it is not ideal fuel on its own, this species plays a role in the oxidation of large hydrocarbon fuels and is used in liquified natural gas (LNG) [1]. The detailed kinetic mechanism of isobutane combustion contains dozens of species and hundreds of reactions. When a kinetic mechanism is applied to a reaction source term of species transport equations, the computational solutions can be used to describe reactive flows and species distribution in multidimensional reactors. This kind of numerical modeling permits designers and analysts to evaluate emissions and performance of fuels in reactors or combustors. -
Process Synthesis
PROCESS SYNTHESIS DALE F. RUDD University of Wisconsin Madison, Wisconsin 53706 INTRODUCTION In the words of Webster, synthesis is "the proper way to approach process development. In combining of often diverse conceptions into a co these theories of process development, each syn herent whole" and analysis is "an examination thesis step defines an analysis problem the solu of a complex, its elements and their relations." tion of which provides data required for further Synthesis refers to the more inventive aspects of synthesis steps. Further, it became apparent that engineering and analysis to the more scientific. this organization of alternating synthesis and Both are required in the development of industrial analysis steps begs the development of educational processes. material for the early stages of engineering edu Since World War II engineering education has cation. moved strongly towards analysis, with the intro In this report we examine the development of duction of courses which analyse individual pro a first course in engineering in which synthesis cess operations and phenome,na. rransport phe and analysis are taught simultaneously. Elemen nomena, unit operations, process control, thermo tary new principles of process synthesis are com dynamics and other engineering science courses bined with the classic analysis techniques of greatly strengthened engineering education by material and energy balancing. Emphasis is on showing how things are and how they work. the development of process technology rather than Unfortunately, there was not a parallel de on the analysis of existing processes. velopment in the teaching of synthesis. The teach ing of how things ought to be rather than how RESEARCH IN PROCESS SYNTHESIS they are. -
Isobutylene Polymer Having Unsaturated Group and Preparation
Europaisches Patentamt European Patent Office Office europeen des brevets (11) EP 0 452 875 B2 (12) NEW EUROPEAN PATENT SPECIFICATION (45) Date of publication and mention (51) |nt CI.6: C08F 10/10, C08F 2/42 of the opposition decision: 18.08.1999 Bulletin 1999/33 (45) Mention of the grant of the patent: 09.08.1995 Bulletin 1995/32 (21) Application number: 91106042.4 (22) Date of filing: 16.04.1991 (54) Isobutylene polymer having unsaturated group and preparation thereof Isobutylenpolymer mit ungesattigter Gruppe und seine Herstellung Polymere de I'isobutylene ayant un groupe insature et sa preparation (84) Designated Contracting States: (74) Representative: BE CH DE ES FR GB IT LI NL SE Hansen, Bernd, Dr. Dipl.-Chem. et al Hoffmann Eitle, (30) Priority: 16.04.1990 JP 10102990 Patent- und Rechtsanwalte, 29.11.1990 JP 33636490 Postfach 81 04 20 81904 Miinchen (DE) (43) Date of publication of application: 23.10.1991 Bulletin 1991/43 (56) References cited: EP-A- 0 265 053 EP-B- 0 322 241 (73) Proprietor: Kanegafuchi Chemical Industry Co., CA-A- 467 049 GB-A- 1 059 580 Ltd. US-A- 4 31 6 973 US-A- 4 327 201 Kita-ku Osaka-shi Osaka-fu (JP) US- A- 4 524 1 88 US-A- 4 758 63 1 US-A- 4 929 683 (72) Inventors: • Noda, Koji Remarks: Kobe-shi, Hyogo-ken (JP) The file contains technical information submitted • Fujisawa, Hiroshi after the application was filed and not included in this Kobe-shi, Hyogo-ken (JP) specification • Yonezawa, Kazuya Kobe-shi, Hyogo-ken (JP) CM DO 10 Is- 00 CM IO ^- o a. -
Ammonia, Anhydrous Ama
AMMONIA, ANHYDROUS AMA CAUTIONARY RESPONSE INFORMATION 4. FIRE HAZARDS 7. SHIPPING INFORMATION 4.1 Flash Point: 7.1 Grades of Purity: Commercial, industrial, Common Synonyms Liquefied compressed Colorless Ammonia odor Not flammable under conditions likely to refrigeration, electronic, and metaflurgical Liquid ammonia gas be encountered grades all have purity greater than 99.5% 4.2 Flammable Limits in Air: 15.50%- 7.2 Storage Temperature: Ambient for pressurized 27.00% ammonia; low temperature for ammonia at Floats and boils on water. Poisonous, visible vapor cloud is produced. 4.3 Fire Extinguishing Agents: Stop flow of atmospheric pressure Avoid contact with liquid and vapor. Keep people away. gas or liquid. Let fire burn. 7.3 Inert Atmosphere: No requirement Wear goggles, self-contained breathing apparatus, and rubber overclothing (including gloves). 4.4 Fire Extinguishing Agents Not to Be 7.4 Venting: Safety relief 250 psi for ammonia Stop discharge if possible. Used: None under pressure. Pressure-vacuum for Stay upwind and use water spray to ``knock down'' vapor. 4.5 Special Hazards of Combustion ammonia at atmospheric pressure. Call fire department. Products: Not pertinent Isolate and remove discharged material. 7.5 IMO Pollution Category: Currently not available 4.6 Behavior in Fire: Not pertinent Notify local health and pollution control agencies. 7.6 Ship Type: 2 4.7 Auto Ignition Temperature: 1204°F Protect water intakes. 7.7 Barge Hull Type: 2 4.8 Electrical Hazards: Class I, Group D Combustible. 4.9 Burning Rate: 1 mm/min. Fire 8. HAZARD CLASSIFICATIONS Wear goggles, self-contained breathing apparatus, and rubber over- 4.10 Adiabatic Flame Temperature: Currently clothing (including gloves). -
HEATS of COMBUSTION of DIAMOND and of GRAPHITE by Ralph S
r---------------___........,._ . _____~ ~_ U. S. DEPARTMENT OF COMMERCE NATIONAL BUREAU OF STANDARDS RESEARCH PAPER RP1140 Part of Journal of Research of the }.{ational Bureau of Standards, Volume 21, October 1938 HEATS OF COMBUSTION OF DIAMOND AND OF GRAPHITE By Ralph S. Jessup ABSTRACT Measurements were made of the heats of combustion of one artificial graphite, two natural graphites, and two samples of diamond. The bomb calorimeter used was calibrated electrically and by means of benzoic acid. The amount of reaction in each combustion experiment was determined from the mass of carbon dioxide formed. This method of determining the amount of reaction automatically eliminates the effect of unburned carbon and of some impurities. It was found, however, that results for different samples did not agree unless the samples were purified. Two methods of purification were used: (a) heating in vacuo to 1,800° C and (b) treatment with hydrochloric and hydrofluoric acids and subsequent heating in vacuo to 200° C to remove traces of the acids. Both methods yielded graphite containing only small amounts of impurities. The mean value obtained for the heat of combustion (-/lH) of the purified graphites in oxygen at 25° C and a constant pressure of 1 atmosphere to form gaseous carbon dioxide at the same temperature and pressure was 393.396 international kilojoules per mole (44.010 g of CO2). The maximum deviation of the mean value for anyone of the purified samples from this value was 0.021 percent. The two samples of diamond, purified by treatment with aqueous hydrochloric and hydrofluoric acids and subsequently heated in vacuo to about 570° C, had average particle sizes of 2.5 I'- and 39.5 1'-, respectively, and yielded the following respective mean values for the heat of combustion (-/lH) at 25° C and 1 atmos phere, in oxygen to form gaseous carbon dioxide: 395.771 and 395.287 interna tional kilojoules per mole. -
Model Vulcanization Systems for Butyl Rubber and Halobutyl Rubber Manual
Exxon™ butyl and halobutyl rubber Model vulcanization systems for butyl rubber and halobutyl rubber manual Country name(s) 2 - Model vulcanization systems for butyl rubber and halobutyl rubber manual Model vulcanization systems for butyl rubber and halobutyl rubber manual - 3 Abstract The vulcanization of isobutylene-co-isoprene rubber (IIR), brominated isobutylene-co-isoprene rubber (BIIR), chlorinated isobutylene-co-isoprene rubber (CIIR), and brominated isobutylene-co-para-methylstyrene elastomer (BIMSM) differs from that of general-purpose rubbers (GPR). Butyl rubber has approximately 2% unsaturation in the backbone. Halobutyl rubber (BIIR and CIIR) incorporates the butyl backbone with either bromine or chlorine, which significantly increases the chemical reactivity of the isoprenyl units located in the butyl backbone. Similarly, in BIMSM the bromine atom is bonded to the para-methylstyrene (PMS) group, thus affording the completely saturated polymer backbone a site of chemical reactivity. Utilization of the unique attributes of butyl rubber and halobutyl rubbers with their minimal backbone unsaturation and of BIMSM elastomers with no backbone unsaturation is found in many areas of industry. These properties are excellent vapor impermeation, resistance to heat degradation, and improved chemical resistance as compared to general-purpose rubbers. However, this low amount of reactivity requires special consideration to vulcanize these isobutylene-based polymers. The type of vulcanization system selected is a function of the composite structure in which it is used, and the cured product performance requirements. Therefore, vulcanization systems vary and may include an accelerator package along with resins, zinc oxide, zinc oxide and sulfur, and quinoid systems. This review will discuss the types and selection of appropriate vulcanization systems for isobutylene-based elastomers. -
Chemistry Grade Span 9/10
Chemistry Grade Span 9/10 Carbon and Carbon Compounds Subject Matter and Methodological Competencies • name the allotropes of carbon and use them to explain the relationship between its structure and properties • state the characteristics of the oxides of carbon • conduct experiments to o detect evidence of carbon dioxide o detect evidence of carbonates (using carbon dioxide detection) o describe the natural formation and decay processes of carbonates and hydrogen carbonates and use this to explain a simple model of the carbon cycle Natural Gas and Crude Oil Subject Matter and Methodological Competencies • identify natural gas, crude oil and coal as fossil fuels • explain the causes and consequences of increasing carbon dioxide concentrations in the atmosphere • discuss the economic and ecological consequences of the production and transport of natural gas and crude oil • apply knowledge of substance mixtures and substance separation using the example of fractional distillation of petroleum • describe the molecular structure of the gaseous alkanes using chemical formulas, structural formulas and simplified structural formulas • conduct experiments to o examine the flammability and solubility of selected alkanes o determine that water and carbon dioxide are the products of combustion o explain the relationship between the construction, properties and uses of important alkanes (e.g. methane - natural gas, propane and butane - liquid gas, octane - gasoline, decane - diesel, octadecane - paraffin candle wax) o explain the cohesion of alkane -
Emissions from Small-Scale Combustion of Biomass Fuels - Extensive Quantification and Characterization
Emissions from small-scale combustion of biomass fuels - extensive quantification and characterization Christoffer Boman Anders Nordin Marcus Öhman Dan Boström Energy Technology and Thermal Process Chemistry Umeå University Roger Westerholm Analytical Chemistry, Arrhenius Laboratory Stockholm University _______________________________________________________________ Emissions from small-scale combustion of biomass fuels - extensive quantification and characterization Christoffer Boman1, Anders Nordin1, Roger Westerholm2, Marcus Öhman1, Dan Boström1 1Energy Technology and Thermal Process Chemistry, Umeå University, SE-901 87 Umeå, Sweden 2Analytical Chemistry, Arrhenius Laboratory, Stockholm University, SE-106 91 Stockholm, Sweden STEM-BHM (P12648-1 and P21906-1) Umeå, February 2005 SUMMARY This work was a part of the Swedish national research program concerning emissions and air quality ("Utsläpp och Luftkvalitet") with the sub-programme concerning biomass, health and environment ("Biobränlen, Hälsa, Miljö" - BHM). The main objective of the work was to systematically determine the quantities and characteristics of gaseous and particulate emissions from combustion in residential wood log and biomass fuel pellet appliances and report emission factors for the most important emission components. The specific focus was on present commercial wood and pellet stoves as well as to illustrate the potentials for future technology development. The work was divided in different sub- projects; 1) a literature review of health effects of ambient wood