Prototyping the Environmental Impacts of 3D Printing: Claims and Realities of Additive Manufacturing Valerie B
Total Page:16
File Type:pdf, Size:1020Kb
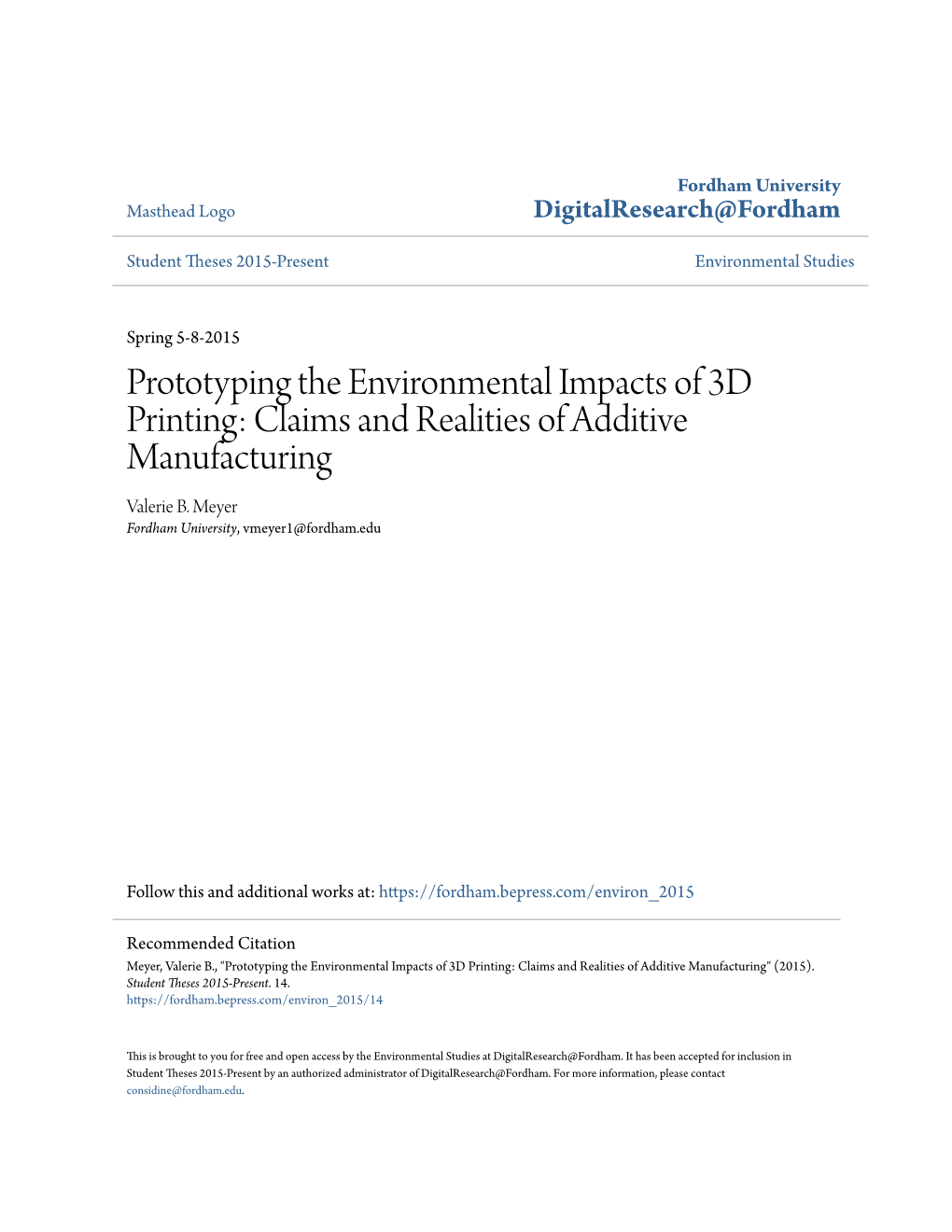
Load more
Recommended publications
-
Wire Embedding 3D Printer
Wire Embedding 3D Printer Jacob Bayless, Mo Chen, Bing Dai Engineering Physics University of British Columbia April 12, 2010 Preface This project began when, seeking a self-sponsored project, we decided to pursue the concept of open-source hardware. While searching for a project to develop, we happened upon the RepRap 3D printer. The potential to close the gap between software and hardware that a 3D printer could offer was apparent, and we immediately set out in search of ways to improve the device. Thus began what would become the SpoolHead project, but we three may not claim all of the credit. A large share of the credit goes to the inventors of the RepRap itself, primarily Adrian Bowyer and Ed Sells, but also many other contributors. We also should thank Sebastien Bailard for promoting our project and helping us manage documentation. All of our work on the RepRap would never have been possible if we had not come across Wade Bortz, an inventive and unbelievably generous Vancouver RepRap developer who offered to print us a full set of Darwin parts. When we found that our extruder didn't have enough torque, Wade gave us one of his own geared extruders to \test out". He patiently bore our nagging questions and bicycled all the way to the University of British Columbia campus to attend our presentations. Wade represents the best example of how a community can build itself up around a project and bring people together. It was already near to the end of February when we came into contact with Mr. -
Neonate: Reinventing Open Source 3D Printers NEONATE: REINVENTING OPEN SOURCE 3D PRINTERS
Neonate: Reinventing Open Source 3d Printers NEONATE: REINVENTING OPEN SOURCE 3D PRINTERS 1AMEY BAVISKAR, 2AMEYA JHAWAR, 3SOHAN MALEGAONKAR, 4ARTH VASAVADA 1,2,3,4Pravara Rural Engineering College, Loni, Maharastra Abstract— In this paper we are presenting a open source software Neonate, which is combination of two existing open source software OpenSCAD and Printrun using Slic3r and OCP (One Click Print) Paradigm. Neonate that allows the fast development of 3D objects for fabrication on 3D printers. Fabricating with Neonate helps user to easily modify, share or print the 3D objects. Usage of three different software just to print an object is an arduous job. Instead of choosing strenuous path for printing an object this paper allows user to use a single software. As a non searched result, we have observed that Neonate also helps users to save their time. Keywords—Neonate, 3D Printer, Open Source, OpenSCAD, Printrun, OCP Paradigm I. INTRODUCTION later, in May 29th the first replication was achieved. Since then, the reprap community (original reprap 3D printing is a technique of creating 3D solid objects machines and derived designs) has been growing of practically any shape from its digital model and exponentially. The current estimated population is using almost any material. With the use of additive around 4500 machines. The second reprap generation, manufacturing, it refers to creation of objects using called Mendel, was finished in September 2009. Some sequential layering. It is exactly opposite of traditional of the main advantages of the Mendel printers over subtractive process such as drilling, boring and many Darwin are bigger print area, better axis efficiency, other similar processes. -
Paste Deposition Modelling, Deconstructing the Additive Manufacturing Process: Development of Novel Multi- Material Tools and Techniques for Craft Practitioners
PASTE DEPOSITION MODELLING, DECONSTRUCTING THE ADDITIVE MANUFACTURING PROCESS: DEVELOPMENT OF NOVEL MULTI- MATERIAL TOOLS AND TECHNIQUES FOR CRAFT PRACTITIONERS A thesis submitted for the degree of Doctor of Philosophy by Esteban Schunemann Department of Engineering and Design, Brunel University London 2015 ii I. Abstract A novel paste deposition process was developed to widen the range of possible materials and applications. This experimental process developed an increasingly complex series of additive manufacturing machines, resulting in new combinations of novel materials and deposition paths without sacrificing many of the design freedoms inherit in the craft process. The investigation made use of open-source software together with an approach to programming user originated infill geometries to form structural parts, differing from the somewhat automated processing by 'closed' commercial RP systems. A series of experimental trials were conducted to test a range of candidate materials and machines which might be suitable for the PDM process. The combination of process and materials were trailed and validated using a series of themed case studies including medical, food industry and jewellery. Some of the object created great interest and even, in the case of the jewellery items, won awards. Further evidence of the commercial validity was evidenced through a collaborative partnership resulting in the development of a commercial version of the experimental system called Newton3D. A number of exciting potential future directions having been opened up by this project including silicone fabrics, bio material deposition and inclusive software development for user originated infills and structures. iii II. Acknowledgments First and foremost I would like to extend my deepest gratitude to both my supervisors, Dr. -
3D Printing at the Florida Public Library
Prepared by-Robert Persing April 2017 1 • What is 3D “printing” • A bit of HISTORY • Types of 3D printing technology • Really Interesting 3D printing Applications! • Bringing it Home Prepared by-Robert Persing April 2017 2 • “A process for making a physical object from a three-dimensional digital model, typically by laying down successive thin layers of a material”. • 3D Printing is also referred to as- “ADDITIVE MANUFACTURING” Prepared by-Robert Persing April 2017 3 A “Three-Dimensional Digital Model” (Paper ‘n Pencil holder designed by students in recent FPL class) Prepared by-Robert Persing April 2017 4 Finished product printed with the library’s 3D printer Student Product Prepared by-Robert Persing April 2017 5 • Invented in 1983, 3D printing is not all that new • Chuck Hull, recognized as the “inventor” of 3D printing, filed for a patent August 8, 1986 • Hull coined the phrase “Stereo Lithography” for the technology used in his 3D printer when applying for the patent (granted March 11, 1986) • Let’s watch a brief CNN interview with Chuck Hull Prepared by-Robert Persing April 2017 6 • The year 2005 is a notable point in the history of 3D printing. This marks the start of the RepRap Project by Dr. Adrian Bowyer at Bath University in England • RepRap is short for replicating rapid prototyper. RepRaps are 3D printers with the additional ability to produce most of the parts necessary to assemble another identical printer. Prepared by-Robert Persing April 2017 7 “Darwin” The First RepRap Printer Prepared by-Robert Persing April 2017 8 • With the history lesson covered, let’s look at 3D Printing in the 21st century • What Technology is used to print 3D? • How do you actually make a 3D printed object? Prepared by-Robert Persing April 2017 9 Concrete Type Technologies Materials Thermoplastics (e.g. -
A Low-Cost Open-Source Metal 3-D Printer Gerald Anzalone, Chenlong Zhang, Bas Wijnen, Paul Sanders, Joshua Pearce, Chenlong Zhang
A Low-Cost Open-Source Metal 3-D Printer Gerald Anzalone, Chenlong Zhang, Bas Wijnen, Paul Sanders, Joshua Pearce, Chenlong Zhang To cite this version: Gerald Anzalone, Chenlong Zhang, Bas Wijnen, Paul Sanders, Joshua Pearce, et al.. A Low- Cost Open-Source Metal 3-D Printer. IEEE Access, IEEE, 2013, 1, pp.803-810. 10.1109/AC- CESS.2013.2293018. hal-02119701 HAL Id: hal-02119701 https://hal.archives-ouvertes.fr/hal-02119701 Submitted on 4 May 2019 HAL is a multi-disciplinary open access L’archive ouverte pluridisciplinaire HAL, est archive for the deposit and dissemination of sci- destinée au dépôt et à la diffusion de documents entific research documents, whether they are pub- scientifiques de niveau recherche, publiés ou non, lished or not. The documents may come from émanant des établissements d’enseignement et de teaching and research institutions in France or recherche français ou étrangers, des laboratoires abroad, or from public or private research centers. publics ou privés. Received November 5, 2013, accepted November 20, 2013, published 00 xxxx, 0000. Digital Object Identifier 10.1109/ACCESS.2013.2293018 A Low-Cost Open-Source Metal 3-D Printer GERALD C. ANZALONE1, CHENLONG ZHANG1, BAS WIJNEN1, PAUL G. SANDERS1, AND JOSHUA M. PEARCE2 1Department of Materials Science and Engineering, Michigan Technological University, Houghton, MI 49931, USA 2Department of Materials Science and Engineering and the Department of Electrical and Computer Engineering, Michigan Technological University, Houghton, MI 49931, USA Corresponding author: G. C. Anzalone ([email protected]) ABSTRACT Technical progress in the open-source self replicating rapid prototyper (RepRap) community has enabled a distributed form of additive manufacturing to expand rapidly using polymer-based materials. -
3D Printing and the New Shape of Industrial Manufacturing
3D printing and the new shape of industrial manufacturing June 2014 In conjunction with Table of contents 1 Introduction: 3D printing’s growth spurt 2 3DP-powered R&D 4 The longest mile: From prototyping to final product 7 Reaching the 99%: Small and medium manufacturers 10 Can 3DP shrink the supply chain? 15 3DP and the industrial worker: Awkward bedfellows? 16 Shaping your 3DP strategy What is 3DP? 3D printing, also known as additive manufac- turing, is the process through which hundreds or even thousands of layers of material are Introduction: 3D printing’s growth spurt “printed,” layer upon layer, using a range of materials, or “inks,” most commonly plastic polymers and metals. The additive process, which manufacturers have been using for prototyping since the 1980s, contrasts with traditional subtractive manufacturing processes based on the removal of material Surely, the potential of 3D printing (3DP) surrounding the economics of 3DP, we to create products. But recent advancements has captured the popular imagination. explore how and why companies are in speed, capabilities and lowering prices From jet engine parts to made-to-fit bikinis, bringing this technology closer to an effec- in printers and feedstock have broadened the technology is being hailed as a revo- tual tipping point of adoption. the use and popularity of the technology. 3D lution in how products are manufactured. printers range from small personal hobbyist According to estimates, the global 3DP There are signs that the technology is on the machines (under $200) to industrial printers printer market is poised to hit $6 billion cusp of being mainstreamed and thus there (hundreds of thousands of dollars and more). -
Factors Effecting Real-Time Optical Monitoring of Fused Filament 3D Printing Siranee Nuchitprasitchai, Michael Roggemann, Joshua Pearce
Factors effecting real-time optical monitoring of fused filament 3D printing Siranee Nuchitprasitchai, Michael Roggemann, Joshua Pearce To cite this version: Siranee Nuchitprasitchai, Michael Roggemann, Joshua Pearce. Factors effecting real-time optical monitoring of fused filament 3D printing. Progress in Additive Manufacturing, Springer Verlag, 2017, 2 (3), pp.133-149. 10.1007/s40964-017-0027-x. hal-02111406 HAL Id: hal-02111406 https://hal.archives-ouvertes.fr/hal-02111406 Submitted on 26 Apr 2019 HAL is a multi-disciplinary open access L’archive ouverte pluridisciplinaire HAL, est archive for the deposit and dissemination of sci- destinée au dépôt et à la diffusion de documents entific research documents, whether they are pub- scientifiques de niveau recherche, publiés ou non, lished or not. The documents may come from émanant des établissements d’enseignement et de teaching and research institutions in France or recherche français ou étrangers, des laboratoires abroad, or from public or private research centers. publics ou privés. Preprint: Nuchitprasitchai, S., Roggemann, M. & Pearce, J.M. Factors effecting real-time optical monitoring of fused filament 3D printing. Progress in Additive Manufacturing. 2(3), pp 133–149 (2017). doi:10.1007/s40964-017-0027-x • Open source code for Matlab https://osf.io/hwdzm/ Factors Effecting Real Time Optical Monitoring of Fused Filament 3-D Printing Siranee Nuchitprasitchai 1, Michael Roggemann 1, Joshua M. Pearce 1,2,* 1. Department of Electrical & Computer Engineering, Michigan Technological University, Houghton MI 2. Department of Materials Science & Engineering, Michigan Technological University, Houghton MI * corresponding author: [email protected] Abstract This study analyzes a low-cost reliable real-time optimal monitoring platform for fused filament fabrication-based open source 3-D printing. -
A Study on Business Ecosystem of 3D Printing Contents Distribution Platform : Using Service Value Network Analysis
International Journal of Applied Engineering Research ISSN 0973-4562 Volume 12, Number 24 (2017) pp. 15580-15591 © Research India Publications. http://www.ripublication.com A Study on Business Ecosystem of 3D Printing Contents Distribution Platform : Using Service Value Network Analysis Hyeog In Kwon 1, Seol Hee Kim2*, Jong-Seok Park3 and Moo Goong Hong3 1First Author, Professor, Chung-Ang University, Seoul, Korea. 2*Corresponding Author, Chung-Ang University, Seoul, Korea. 3Co-author, Chung-Ang University, Seoul, Korea. *Corresponding author ORCID 0000-0001-7179-8185 Abstract market showed a growth of 83.5% between the years 2014 and 2015, a significantly higher growth than the product-focused This study is a research on ecosystems focused on activating market, predicting the acceleration of the 3D printing industry the domestic 3D printing contents distribution platform and aims to promote the industry by suggesting service strategies would result in an amplified growth. Also, in international and an ideal ecosystem model for the platform. As the next markets, the service market show trends of increasing expansion, with service-focused markets more effective than generation growth power, 3D printing industry has low the product-focused markets in creating higher value added. In accessibility resulting from low demand and difficulties in such service-focused markets, 3D printing Contents market expansion due to its product-focused market. In order Distribution Platform will not only distribute its services but to solve these issues, high value service market expansion is necessary. 3D printing contents distribution platform is able to increase accessibility to consumers as a platform, a necessity in market expansion. -
New 3D Printable Polymeric Materials for Fused Filament Fabrication (FFF)
NEW 3D PRINTABLE POLYMERIC MATERIALS FOR FUSED FILAMENT FABRICATION (FFF) by Gayan Adikari Appuhamillage APPROVED BY SUPERVISORY COMMITTEE: ___________________________________________ Ronald A. Smaldone, Chair ___________________________________________ John P. Ferraris ___________________________________________ Walter E. Voit ___________________________________________ Mihaela C. Stefan Copyright 2018 Gayan Adikari Appuhamillage All Rights Reserved To my family and friends NEW 3D PRINTABLE POLYMERIC MATERIALS FOR FUSED FILAMENT FABRICATION (FFF) by GAYAN ADIKARI APPUHAMILLAGE, BS, MS DISSERTATION Presented to the Faculty of The University of Texas at Dallas in Partial Fulfillment of the Requirements for the Degree of DOCTOR OF PHILOSOPHY IN CHEMISTRY THE UNIVERSITY OF TEXAS AT DALLAS May 2018 ACKNOWLEDGMENTS It was a wonderful experience for me to work in Dr. Smaldone lab for the past five years. I would like to acknowledge my research advisor Dr. Ronald A. Smaldone, for letting me carry out my graduate research work under his supervision. I sincerely appreciate all of his support, guidance, and immense encouragement throughout my graduate studies. I would like to acknowledge the members of my advisory committee- Dr. John P. Ferraris, Dr. Walter E. Voit, and Dr. Mihaela C. Stefan for their valuable suggestions and support. I also appreciate all the valuable help and training given to me by Dr. Christina Thompson for organic synthesis and reaction mechanisms; Dr. Hien Nguyen for nuclear magnetic resonance (NMR) spectroscopy and inductively coupled plasma (ICP) analysis; Dr. Benjamin Batchelor for Thermogravimetric analysis (TGA), differential scanning calorimetry (DSC), and dynamic mechanical analysis (DMA); Dr. Faisal Mahmood for gel permeation chromatography (GPC); Dr. Layne Winston for the Universal Testing Machine-Instron, and finally, thanks to the clean-room staff. -
3D Printing Quarterly Report—Q32018 3D PRINTING–A FAST MOVING MARKET Developments in 3D Printing a Sector by Sector Overview
3D Printing Quarterly Report—Q32018 3D PRINTING–A FAST MOVING MARKET Developments in 3D Printing A Sector by Sector Overview Overview This report explores developments in 3D printing across several sectors and categories for the quarterly period of July 1 to October 10, 2018. For more information, Table of Contents please contact: Overview ................................... 2 Patents & Copyright ................. 12 Food ....................................... 21 Mark E. Avsec General ..................................... 2 Auto & Transportation ............... 12 Consumer Goods & Retail ......... 22 (216) 363-4151 Materials ................................... 4 Aviation & Aerospace ............... 13 Education ................................ 23 [email protected] Printing Techniques & Health & Life Sciences ............. 14 Environmental Efforts ............... 24 Capabilities .............................. 5 Manufacturing & Construction... 17 Arts & Entertainment ................ 25 M&A and Investments ................ 9 Clothing & Wearables ............... 20 Sports ..................................... 25 www.beneschlaw.com Miscellaneous Partnerships ...... 11 3D PRINTING–A FAST MOVING MARKET 3D Printing Quarterly Report—Q3 A Sector by Sector Overview General Aurora Group to market Nano Dimension 3D printers in China The deal expands Nano Dimension’s already active presence in Asia Pacific beyond Hong Kong, South Korea, Singapore and Taiwan. Founded in 2012, Nano Dimensions develops and manufactures 3D printers for the electronics -
Additive Manufacturing, Cloud-Based 3D Printing and Associated Services—Overview
Journal of Manufacturing and Materials Processing Review Additive Manufacturing, Cloud-Based 3D Printing and Associated Services—Overview Felix W. Baumann 1,2,* and Dieter Roller 2 1 TWT GmbH Science & Innovation, Stuttgart 70565, Germany 2 Institute of Computer-aided Product Development, University of Stuttgart, Stuttgart 70569, Germany; [email protected] * Correspondence: [email protected]; Tel.: +49-711-215-777-1207 Received: 22 September 2017; Accepted: 13 October 2017; Published: 17 October 2017 Abstract: Cloud Manufacturing (CM) is the concept of using manufacturing resources in a service-oriented way over the Internet. Recent developments in Additive Manufacturing (AM) are making it possible to utilise resources ad-hoc as replacements for traditional manufacturing resources in case of spontaneous problems in the established manufacturing processes. In order to be of use in these scenarios, the AM resources must adhere to a strict principle of transparency and service composition in adherence to the Cloud Computing (CC) paradigm. With this review, we provide an overview of CM, AM and relevant domains as well as presenting the historical development of scientific research in these fields, from 2002 to 2016. Part of this work is also a meta-review on the domain to further detail its development and structure. Keywords: additive manufacturing; cloud manufacturing; 3D printing service 1. Introduction Cloud Manufacturing (here CM, in other works also CMfg) as a concept is not new and has been executed in enterprises for many years [1], under different terms, e.g., Grid Manufacturing [2] or Agile Manufacturing [3]. The decision to have a globally distributed production process with many contractors or partners interconnected and related supply chains is a luxurious one. -
Major Update to Adobe Photoshop CC Brings 3D Printing to the Design World
Press Contacts Marissa Lee Adobe Systems Incorporated 415-832-5378 [email protected] Reagan Crossley Edelman 650-762-2955 [email protected] FOR IMMEDIATE RELEASE Major Update to Adobe Photoshop CC Brings 3D Printing to the Design World First 2014 Creative Cloud Release Also Includes Amazing Perspective Warp Capability in Photoshop CC SAN JOSE, Calif., — January 16, 2014 — Adobe (Nasdaq:ADBE) today unveiled new 3D printing capabilities in Adobe® Photoshop® CC. By radically simplifying the 3D print process, Photoshop CC will become the go-to tool for anyone who wants to print a 3D model. Available immediately, as part of a major update to Adobe Creative Cloud™, the new 3D printing capabilities integrated in Photoshop CC enable Creative Cloud members to easily and reliably build, refine, preview, prepare and print 3D designs, setting the stage for explosive growth in the 3D printing market. The new 3D printing capabilities also help creatives to design in 3D from scratch or refine an existing 3D model and produce beautiful, print-ready 3D models using familiar Photoshop tools. Automated mesh repair and support structure generation ensure models will be produced reliably, while accurate previews allow creatives to submit print jobs with confidence. “The new 3D print capabilities in Photoshop CC take the guess work out of printing 3D models for everyone,” said Winston Hendrickson, vice president products, Creative Media Solutions, Adobe. “Before today there was a gap between the content produced by 3D modeling tools and what 3D printers need in order to deliver high quality results. Now, by simply clicking ‘Print’ in Photoshop CC, creatives can bring 3D designs to the physical world.” Photoshop CC Turbocharges Emerging 3D Print Ecosystem With today’s release of Photoshop CC, designs can be printed to a locally connected 3D printer or via built-in access to popular online 3D print services.