Fly-By-Wire for Experimental Aircraft? a Vision Based on Canaerospace/AGATE Data Bus Technology
Total Page:16
File Type:pdf, Size:1020Kb
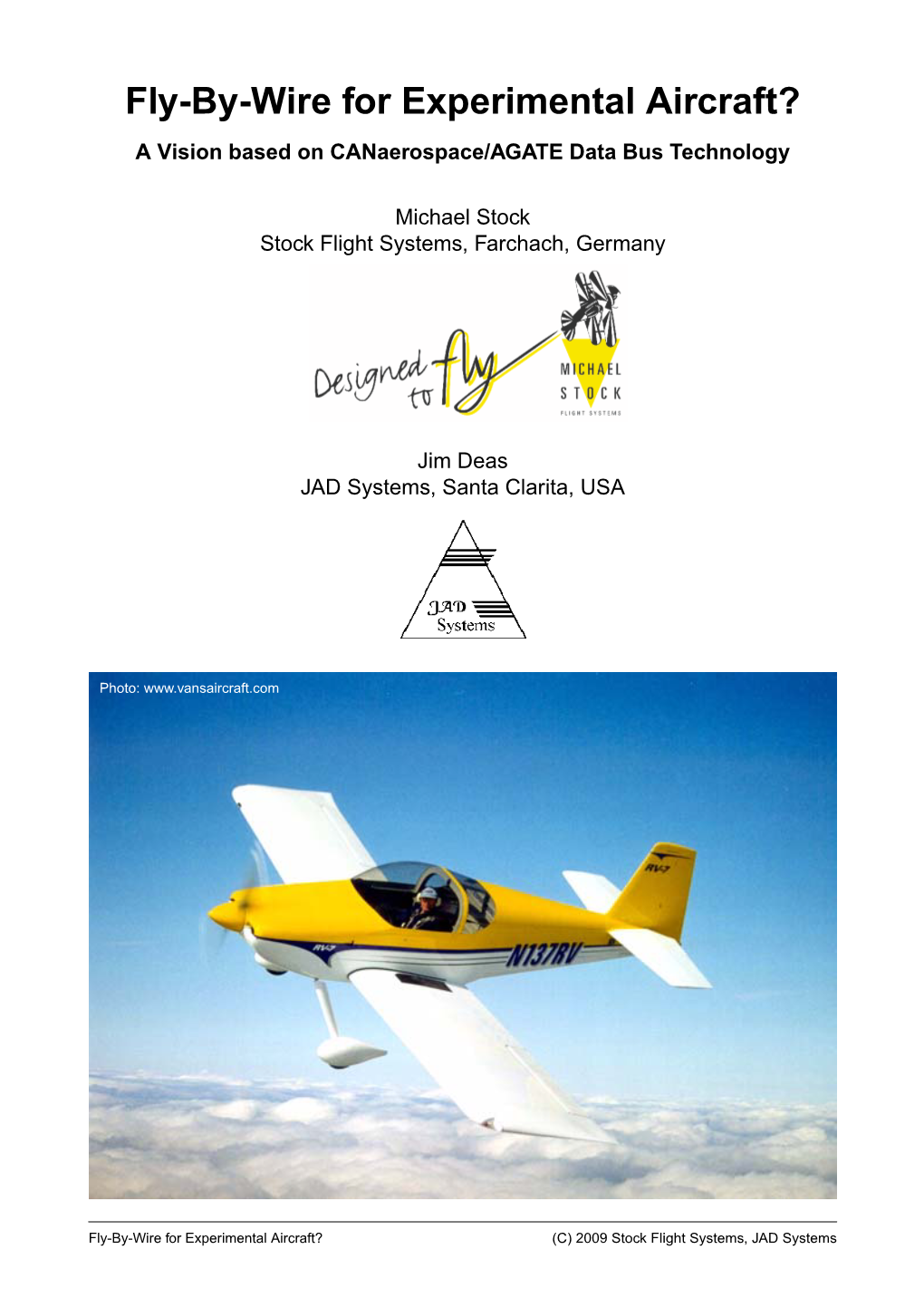
Load more
Recommended publications
-
Easy Access Rules for Auxiliary Power Units (CS-APU)
APU - CS Easy Access Rules for Auxiliary Power Units (CS-APU) EASA eRules: aviation rules for the 21st century Rules and regulations are the core of the European Union civil aviation system. The aim of the EASA eRules project is to make them accessible in an efficient and reliable way to stakeholders. EASA eRules will be a comprehensive, single system for the drafting, sharing and storing of rules. It will be the single source for all aviation safety rules applicable to European airspace users. It will offer easy (online) access to all rules and regulations as well as new and innovative applications such as rulemaking process automation, stakeholder consultation, cross-referencing, and comparison with ICAO and third countries’ standards. To achieve these ambitious objectives, the EASA eRules project is structured in ten modules to cover all aviation rules and innovative functionalities. The EASA eRules system is developed and implemented in close cooperation with Member States and aviation industry to ensure that all its capabilities are relevant and effective. Published February 20181 1 The published date represents the date when the consolidated version of the document was generated. Powered by EASA eRules Page 2 of 37| Feb 2018 Easy Access Rules for Auxiliary Power Units Disclaimer (CS-APU) DISCLAIMER This version is issued by the European Aviation Safety Agency (EASA) in order to provide its stakeholders with an updated and easy-to-read publication. It has been prepared by putting together the certification specifications with the related acceptable means of compliance. However, this is not an official publication and EASA accepts no liability for damage of any kind resulting from the risks inherent in the use of this document. -
Exec Summary (PDF)
BEECHCRAFT® AT-6 The Future of Light Attack is Here. Capable. Affordable. Sustainable. Interoperable. One platform with multiple missions: initial pilot training, weapons training, operational NetCentric ISR and Light Attack capabilities for irregular warfare. The Beechcraft AT-6 is a multi-role, multi-mission aircraft system designed to meet a wide spectrum of warfighter needs: • Based on the proven Beechcraft USAF T-6A and USN T-6B • Designed to accommodate 95% of the aircrew population; widest range in its class • Lockheed Martin plug-and-play mission system architecture adapted from A-10C • Sensor suite adapted from the MC-12W • Flexible, reconfigurable hardpoints with six external store stations Unparalleled attributes with • Long persistence with two aircrew and weapons; up to 1,485 nm self-deployment range a wide range of options. • Extensive variety of weapons including general purpose, laser guided and inertially-aided munitions AIRFRAME AND POWERPLANT • 1,600 shaft horsepower engine • The only fixed-wing aircraft to fire laser guided rockets • ISR suite and six external store hardpoints • Light armor COMBAT MISSION SYSTEMS • Mission systems by Lockheed Martin • NVIS cockpit • Helmet-mounted cueing system • Infrared missile warning and countermeasures COMMUNICATIONS SUITE • Secure voice and data • Rover-compatible full motion video • SADL/Link-16 compatible • SATCOM ISR SUITE • MX-15Di WEAPONS INTEGRATION • 17 60 capable stores management system • .50 Cal Gun • 20mm Gun • 250/500 lb. laser guided GPS or GP bombs • Laser guided missiles • Laser guided rockets • Small 1760 weapons Learn more. Call +1.316.676.0800 or visit Beechcraft.com 13LSAT6HW Specifications and performance are subject to change without notice. -
Mise En Page 1
Military EC725 002 EC725 EC725 003 EC725 DESIGNED FOR THE MOST DEMANDING MISSIONS A COMBAT PROVEN MULTI-ROLE HELICOPTER Introduced in 2005, the EC725 has proven itself in combat service worldwide: Afghanistan, Lybia and Mali. An evolution from the experience gained with the Cougar family, the EC725 is the latest version of this medium lift (11-ton class) helicopter. The EC725 is equipped with: • Two latest generation Turbomeca Makila 2A1 engines • A five-blade rotor providing high levels of maneuverability • A state-of the-art glass cockpit and avionics • The most advanced Automatic Flight Control System. The EC725 excels in a full range of military missions: • Special Operations • Combat Search and Rescue • Tactical transport • Casualty / medical evacuation. As well as in public service missions: • Search and Rescue • Firefighting • Coast Guard • Exclusive Economic Zone (EEZ) protection. The EC725 - a truly multi-purpose, versatile military asset – has the capability to operate both from ships and from ashore. 004 EC725 The most demanding missions Special Ops, Combat SAR and Personal Recovery missions require performance, precise navigation and survivability; qualities for which the EC725 is outstanding. The French Forces are successfully operating the EC725 in the harshest environments. The success of the EC725 demonstrated in Afghanistan and Libya, reflects its excellent capabilities as a Force Multiplier and the ability of this aircraft to offer decisive tactical advantage to any operator. EC725 005 Mission Capabilities Major mission -
Lighting up to 7 Times Brighter Than Other LED Landing Lights!
Lighting FAA-PMA Approved AeroLEDs Lighting Increase safety and reduce operating cost! See the Difference... Lighting Know the Difference... • Increased safety • Direct replacement • Up to 80% reduced power consumption • Long life - over 50,000 hours! • Lighter weight - no heavy power supply - save up to 3 lbs • Reduced drag • Zero maintenance • 10x more efficient than incandescent! Increased Safety AeroLED lights allow you to comply with the latest FAA recommendations (Operation Lights On) regarding extended use of taxi, landing, and anti-collision lights without fear of reduced light performance or life. They all feature optimized light color (6500k sunlight equivalent) for proven superior air-to-air recognition. The landing and taxi lights also feature an optional pulsed recognition light mode. Reduced Power Consumption High efficiency LED lights use less than 1/3 the power of halogen bulbs. They significantly reduce the load on the electrical system and they won't dim due to low voltage, typical of low RPM final approaches when you need them most! Postition lights aerodynamic design results in less drag than original equipment! Longer Life - Zero Maintenance All AeroLED products are designed to be a "lifetime buy". They last over 50,000 hours when properly installed and do not degrade with on/off cycles. They are extremely rugged and hardened against all kinds of electrical damage, shock, and vibration. Up to 7 times brighter than other LED landing lights! PAR36 Landing Light Comparison Measured Brightness at 50 Ft. Manufacturer Intensity -
Development and Flight Test Experiences with a Flight-Crucial Digital Control System
NASA Technical Paper 2857 1 1988 Development and Flight Test Experiences With a Flight-Crucial Digital Control System Dale A. Mackall Ames Research Center Dryden Flight Research Facility Edwards, Calgornia I National Aeronautics I and Space Administration I Scientific and Technical Information Division I CONTENTS Page ~ SUMMARY ................................... 1 I 1 INTRODUCTION . 1 2 NOMENCLATURE . 2 3 SYSTEM SPECIFICATION . 5 3.1 Control Laws and Handling Qualities ................. 5 3.2 Reliability and Fault Tolerance ................... 5 4 DESIGN .................................. 6 4.1 System Architecture and Fault Tolerance ............... 6 4.1.1 Digital flight control system architecture .......... 6 4.1.2 Digital flight control system computer hardware ........ 8 4.1.3 Avionics interface ...................... 8 4.1.4 Pilot interface ........................ 9 4.1.5 Actuator interface ...................... 10 4.1.6 Electrical system interface .................. 11 4.1.7 Selector monitor and failure manager ............. 12 4.1.8 Built-in test and memory mode ................. 14 4.2 ControlLaws ............................. 15 4.2.1 Control law development process ................ 15 4.2.2 Control law design ...................... 15 4.3 Digital Flight Control System Software ................ 17 4.3.1 Software development process ................. 18 4.3.2 Software design ........................ 19 5 SYSTEM-SOFTWARE QUALIFICATION AND DESIGN ITERATIONS ............ 19 5.1 Schedule ............................... 20 5.2 Software Verification ........................ 21 5.2.1 Verification test plan .................... 21 5.2.2 Verification support equipment . ................ 22 5.2.3 Verification tests ...................... 22 5.2.4 Reverifying the design iterations ............... 24 5.3 System Validation .......................... 24 5.3.1 Validation test plan . ............... 24 5.3.2 Support equipment ....................... 25 5.3.3 Validation tests ....................... 25 5.3.4 Revalidation of designs ................... -
Air Force Airframe and Powerplant (A&P) Certification Program
Air Force Airframe and Powerplant (A&P) Certification Program Introduction: Most military aircraft maintenance technicians are eligible to pursue the Federal Aviation Administration (FAA) Airframe & Powerplant (A&P) certification based on documented evidence of 30 months practical aircraft maintenance experience in airframe and powerplant systems per Title 14, Code of Federal Regulations (CFR), Part 65- Certification: Airmen Other Than Flight Crew Members; Subpart D-Mechanics. Air Force education, training and experience and FAA eligibility requirements per Title 14, CFR Part 65.77. This FAA-approved program is a voluntary program which benefits the technician and the Air Force, with consideration to professional development, recruitment, retention, and transition. Completing this program, outlined in the program Qualification Training Package (QTP), will assist technicians in meeting FAA eligibility requirements and being better-prepared for the FAA exams. Three-Tier Program: The program is a three-tier training and experience program. These elements are required for program completion and are important for individual development, knowledge assessment, meeting FAA certification eligibility, and preparation for the FAA exams: Three Online Courses (02AF1-General, 02AF2-Airframe, & 02AF3-Powerplant). On the Job Training (OJT) Qualification Training Package(QTP). Documented evidence of 30 months practical experience in airframe and powerplant systems. Program Eligibility: Active duty, guard and reserve technicians who possess at least a 5-skill level in one of the following aircraft maintenance AFSCs are eligible to enroll: 2A0X1, 2A090, 2A2X1, 2A2X2, 2A2X3, 2A3X3, 2A3X4, 2A3X5, 2A3X7, 2A3X8, 2A390, 2A300, 2A5X1, 2A5X2, 2A5X3, 2A5X4, 2A590, 2A500, 2A6X1, 2A6X3, 2A6X4, 2A6X5, 2A6X6, 2A690, 2A691, 2A600 (except AGE), 2A7X1, 2A7X2, 2A7X3, 2A7X5, 2A790, 2A8X1, 2A8X2, 2A9X1, 2A9X2, and 2A9X3. -
Final Report RL 2017:10E
Final report RL 2017:10e Serious incident after take-off from Gothenburg/Landvetter Airport on 7 November 2016 involving SE-DSV an aeroplane of the model AVRO-RJ 100, operated by Braathens Regional Aviation AB. File no. L-112/16 7 December 2017 RL 2017:10e SHK investigates accidents and incidents from a safety perspective. Its investigations are aimed at preventing a similar event from occurring in the future, or limiting the effects of such an event. The investigations do not deal with issues of guilt, blame or liability for damages. The report is also available on SHK´s web site: www.havkom.se ISSN 1400-5719 This document is a translation of the original Swedish report. In case of discrepancies between this translation and the Swedish original text, the Swedish text shall prevail in the interpretation of the report. Photos and graphics in this report are protected by copyright. Unless other- wise noted, SHK is the owner of the intellectual property rights. With the exception of the SHK logo, and photos and graphics to which a third party holds copyright, this publication is licensed under a Creative Commons Attribution 2.5 Sweden license. This means that it is allowed to copy, distribute and adapt this publication provided that you attribute the work. The SHK preference is that you attribute this publication using the following wording: “Source: Swedish Accident Investigation Authority”. Where it is noted in the report that a third party holds copyright to photos, graphics or other material, that party’s consent is needed for reuse of the material. -
The Difference Between Higher and Lower Flap Setting Configurations May Seem Small, but at Today's Fuel Prices the Savings Can Be Substantial
THE DIFFERENCE BETWEEN HIGHER AND LOWER FLAP SETTING CONFIGURATIONS MAY SEEM SMALL, BUT AT TODAY'S FUEL PRICES THE SAVINGS CAN BE SUBSTANTIAL. 24 AERO QUARTERLY QTR_04 | 08 Fuel Conservation Strategies: Takeoff and Climb By William Roberson, Senior Safety Pilot, Flight Operations; and James A. Johns, Flight Operations Engineer, Flight Operations Engineering This article is the third in a series exploring fuel conservation strategies. Every takeoff is an opportunity to save fuel. If each takeoff and climb is performed efficiently, an airline can realize significant savings over time. But what constitutes an efficient takeoff? How should a climb be executed for maximum fuel savings? The most efficient flights actually begin long before the airplane is cleared for takeoff. This article discusses strategies for fuel savings But times have clearly changed. Jet fuel prices fuel burn from brake release to a pressure altitude during the takeoff and climb phases of flight. have increased over five times from 1990 to 2008. of 10,000 feet (3,048 meters), assuming an accel Subse quent articles in this series will deal with At this time, fuel is about 40 percent of a typical eration altitude of 3,000 feet (914 meters) above the descent, approach, and landing phases of airline’s total operating cost. As a result, airlines ground level (AGL). In all cases, however, the flap flight, as well as auxiliarypowerunit usage are reviewing all phases of flight to determine how setting must be appropriate for the situation to strategies. The first article in this series, “Cost fuel burn savings can be gained in each phase ensure airplane safety. -
Faa Ac 20-186
U.S. Department Advisory of Transportation Federal Aviation Administration Circular Subject: Airworthiness and Operational Date: 7/22/16 AC No: 20-186 Approval of Cockpit Voice Recorder Initiated by: AFS-300 Change: Systems 1 GENERAL INFORMATION. 1.1 Purpose. This advisory circular (AC) provides guidance for compliance with applicable regulations for the airworthiness and operational approval for required cockpit voice recorder (CVR) systems. Non-required installations may use this guidance when installing a CVR system as a voluntary safety enhancement. This AC is not mandatory and is not a regulation. This AC describes an acceptable means, but not the only means, to comply with Title 14 of the Code of Federal Regulations (14 CFR). However, if you use the means described in this AC, you must conform to it in totality for required installations. 1.2 Audience. We, the Federal Aviation Administration (FAA), wrote this AC for you, the aircraft manufacturers, CVR system manufacturers, aircraft operators, Maintenance Repair and Overhaul (MRO) Organizations and Supplemental Type Certificate (STC) applicants. 1.3 Cancellation. This AC cancels AC 25.1457-1A, Cockpit Voice Recorder Installations, dated November 3, 1969. 1.4 Related 14 CFR Parts. Sections of 14 CFR parts 23, 25, 27, 29, 91, 121, 125, 129, and 135 detail design substantiation and operational approval requirements directly applicable to the CVR system. See Appendix A, Flowcharts, to determine the applicable regulations for your aircraft and type of operation. Listed below are the specific 14 CFR sections applicable to this AC: • Part 23, § 23.1457, Cockpit Voice Recorders. • Part 23, § 23.1529, Instructions for Continued Airworthiness. -
Bell 429 Product Specifications
BELL 429 SPECIFICATIONS BELL 429 SPECIFICATIONS Publisher’s Notice The information herein is general in nature and may vary with conditions. Individuals using this information must exercise their independent judgment in evaluating product selection and determining product appropriateness for their particular purpose and requirements. For performance data and operating limitations for any specific mission, reference must be made to the approved flight manual. Bell Helicopter Textron Inc. makes no representations or warranties, either expressed or implied, including without limitation any warranties of merchantability or fitness for a particular purpose with respect to the information set forth herein or the product(s) and service(s) to which the information refers. Accordingly, Bell Helicopter Textron Inc. will not be responsible for damages (of any kind or nature, including incidental, direct, indirect, or consequential damages) resulting from the use of or reliance on this information. Bell Helicopter Textron Inc. reserves the right to change product designs and specifications without notice. © 2019 Bell Helicopter Textron Inc. All registered trademarks are the property of their respective owners. FEBRUARY 2019 © 2019 Bell Helicopter Textron Inc. Specifications subject to change without notice. i BELL 429 SPECIFICATIONS Table of Contents Bell 429 ..................................................................................................................................1 Bell 429 Specification Summary (U.S. Units) ........................................................................4 -
Glider Handbook, Chapter 2: Components and Systems
Chapter 2 Components and Systems Introduction Although gliders come in an array of shapes and sizes, the basic design features of most gliders are fundamentally the same. All gliders conform to the aerodynamic principles that make flight possible. When air flows over the wings of a glider, the wings produce a force called lift that allows the aircraft to stay aloft. Glider wings are designed to produce maximum lift with minimum drag. 2-1 Glider Design With each generation of new materials and development and improvements in aerodynamics, the performance of gliders The earlier gliders were made mainly of wood with metal has increased. One measure of performance is glide ratio. A fastenings, stays, and control cables. Subsequent designs glide ratio of 30:1 means that in smooth air a glider can travel led to a fuselage made of fabric-covered steel tubing forward 30 feet while only losing 1 foot of altitude. Glide glued to wood and fabric wings for lightness and strength. ratio is discussed further in Chapter 5, Glider Performance. New materials, such as carbon fiber, fiberglass, glass reinforced plastic (GRP), and Kevlar® are now being used Due to the critical role that aerodynamic efficiency plays in to developed stronger and lighter gliders. Modern gliders the performance of a glider, gliders often have aerodynamic are usually designed by computer-aided software to increase features seldom found in other aircraft. The wings of a modern performance. The first glider to use fiberglass extensively racing glider have a specially designed low-drag laminar flow was the Akaflieg Stuttgart FS-24 Phönix, which first flew airfoil. -
Using an Autothrottle to Compare Techniques for Saving Fuel on A
Iowa State University Capstones, Theses and Graduate Theses and Dissertations Dissertations 2010 Using an autothrottle ot compare techniques for saving fuel on a regional jet aircraft Rebecca Marie Johnson Iowa State University Follow this and additional works at: https://lib.dr.iastate.edu/etd Part of the Electrical and Computer Engineering Commons Recommended Citation Johnson, Rebecca Marie, "Using an autothrottle ot compare techniques for saving fuel on a regional jet aircraft" (2010). Graduate Theses and Dissertations. 11358. https://lib.dr.iastate.edu/etd/11358 This Thesis is brought to you for free and open access by the Iowa State University Capstones, Theses and Dissertations at Iowa State University Digital Repository. It has been accepted for inclusion in Graduate Theses and Dissertations by an authorized administrator of Iowa State University Digital Repository. For more information, please contact [email protected]. Using an autothrottle to compare techniques for saving fuel on A regional jet aircraft by Rebecca Marie Johnson A thesis submitted to the graduate faculty in partial fulfillment of the requirements for the degree of MASTER OF SCIENCE Major: Electrical Engineering Program of Study Committee: Umesh Vaidya, Major Professor Qingze Zou Baskar Ganapathayasubramanian Iowa State University Ames, Iowa 2010 Copyright c Rebecca Marie Johnson, 2010. All rights reserved. ii DEDICATION I gratefully acknowledge everyone who contributed to the successful completion of this research. Bill Piche, my supervisor at Rockwell Collins, was supportive from day one, as were many of my colleagues. I also appreciate the efforts of my thesis committee, Drs. Umesh Vaidya, Qingze Zou, and Baskar Ganapathayasubramanian. I would also like to thank Dr.