An Application of Pareto Analysis and Cause-And-Effect Diagram (CED) for Minimizing Rejection of Raw Materials in Lamp Production Process
Total Page:16
File Type:pdf, Size:1020Kb
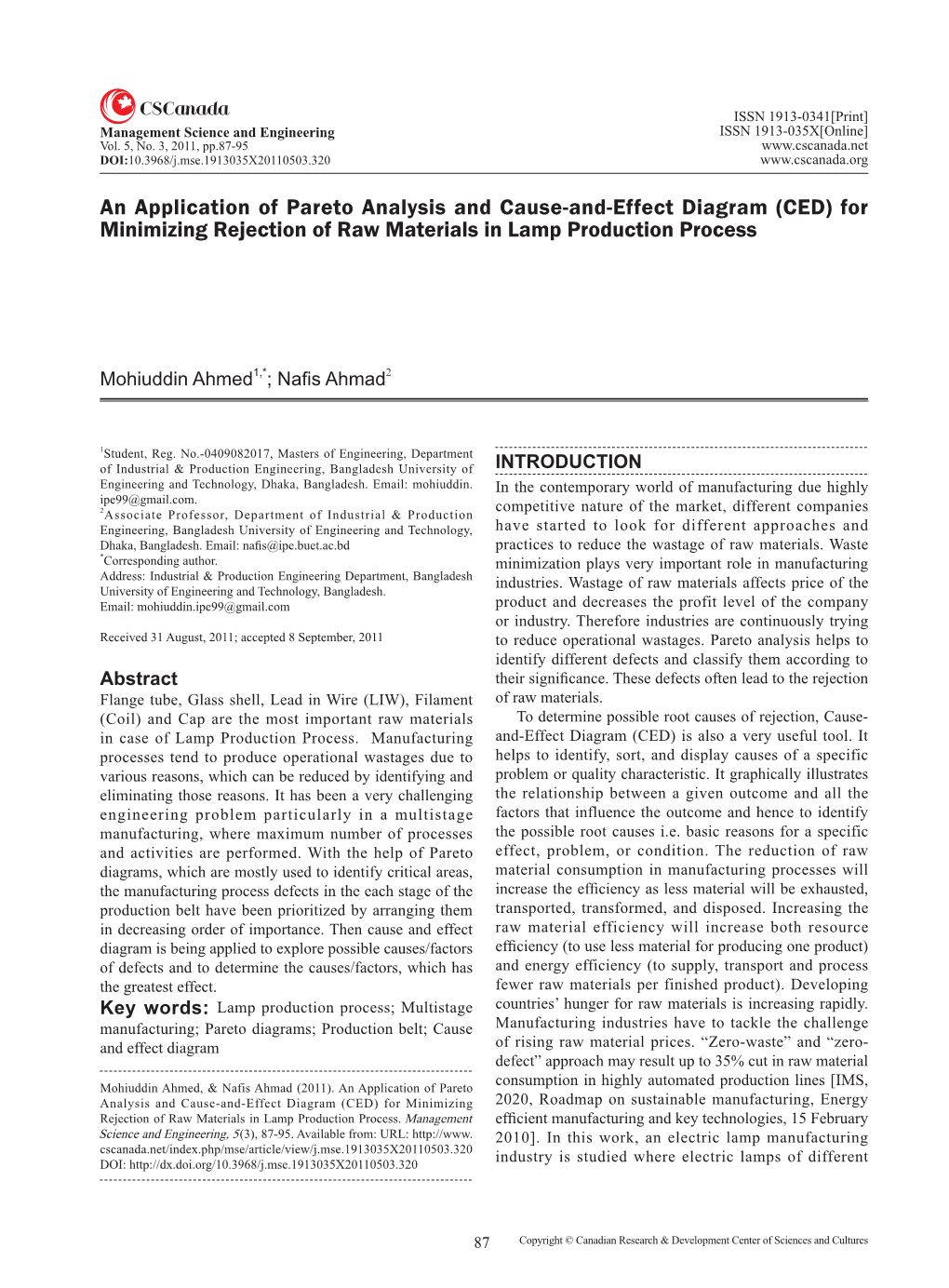
Load more
Recommended publications
-
Statistical Process Control Tools: a Practical Guide for Jordanian Industrial Organizations
Volume 4, Number 6, December 2010 ISSN 1995-6665 JJMIE Pages 693 - 700 Jordan Journal of Mechanical and Industrial Engineering www.jjmie.hu.edu.jo Statistical Process Control Tools: A Practical guide for Jordanian Industrial Organizations Rami Hikmat Fouad*, Adnan Mukattash Department of Industrial Engineering, Hashemite University, Jordan. Abstract The general aim of this paper is to identify the key ingredients for successful quality management in any industrial organization. Moreover, to illustrate how is it important to realize the intergradations between Statistical Process Control (SPC) is seven tools (Pareto Diagram, Cause and Effect Diagram, Check Sheets, Process Flow Diagram, Scatter Diagram, Histogram and Control Charts), and how to effectively implement and to earn the full strength of these tools. A case study has been carried out to monitor real life data in a Jordanian manufacturing company that specialized in producing steel. Flow process chart was constructed, Check Sheets were designed, Pareto Diagram, scatter diagrams, Histograms was used. The vital few problems were identified; it was found that the steel tensile strength is the vital few problem and account for 72% of the total results of the problems. The principal aim of the project is to train quality team on how to held an effective Brainstorming session and exploit these data in cause and effect diagram construction. The major causes of nonconformities and root causes of the quality problems were specified, and possible remedies were proposed. © 2010 Jordan Journal of Mechanical and Industrial Engineering. All rights reserved Keywords: Statistical Process Control, Check sheets, Process Flow Diagram, Pareto Diagram, Histogram, Scatter Diagram, Control Charts, Brainstorming, and Cause and Effect Diagram. -
Cause and Effect Diagrams
Online Student Guide Cause and Effect Diagrams OpusWorks 2019, All Rights Reserved 1 Table of Contents LEARNING OBJECTIVES ....................................................................................................................................4 INTRODUCTION ..................................................................................................................................................4 WHAT IS A “ROOT CAUSE”? ......................................................................................................................................................... 4 WHAT IS A “ROOT CAUSE ANALYSIS”?...................................................................................................................................... 4 ADDRESSING THE ROOT CAUSE .................................................................................................................................................. 5 ROOT CAUSE ANALYSIS: THREE BASIC STEPS ........................................................................................................................ 5 CAUSE AND EFFECT TOOLS .......................................................................................................................................................... 6 FIVE WHYS ...........................................................................................................................................................6 THE FIVE WHYS ............................................................................................................................................................................ -
Root Cause Analysis of Defects in Automobile Fuel Pumps: a Case Study
International Journal of Management, IT & Engineering Vol. 7 Issue 4, April 2017, ISSN: 2249-0558 Impact Factor: 7.119 Journal Homepage: http://www.ijmra.us, Email: [email protected] Double-Blind Peer Reviewed Refereed Open Access International Journal - Included in the International Serial Directories Indexed & Listed at: Ulrich's Periodicals Directory ©, U.S.A., Open J-Gage as well as in Cabell‟s Directories of Publishing Opportunities, U.S.A ROOT CAUSE ANALYSIS OF DEFECTS IN AUTOMOBILE FUEL PUMPS: A CASE STUDY Saurav Adhikari* Nilesh Sachdeva* Dr. D.R. Prajapati** ABSTRACT Quality can be directly measured from the degree to which customer requirements are satisfied. Some problems were reported by the customers of the automobile company under study in the fuel pumps; which is used in an automobile to transfer the fuel from fuel tank to fuel injection system after filtration.This paper presents the implementation of Quality Control tools– Check Sheet, Fishbone Diagram(or Ishikawa Diagram), ParetoChartand 5-Why analysis tools for identification and elimination of the root cause/s responsible for malfunctioning of the fuel pump in customers‟ cars. From the Check sheet and Pareto analysis, two major defects were identified which accounted for more than 80% of the problems being reported. The root causes of these two defects affecting the product quality of the company were then further analyzed using the 5- Why analysis. Keywords: Quality Control Tools, Ishikawa Diagram, Pareto Chart, 5-Why Analysis * Undergraduate Student, Department of Mechanical Engineering, PEC University of Technology, (formerly Punjab Engineering College), Chandigarh ** Associate Professor& Corresponding Author, Department of Mechanical Engineering, PEC University of Technology (formerly Punjab Engineering College), Chandigarh 90 International journal of Management, IT and Engineering http://www.ijmra.us, Email: [email protected] ISSN: 2249-0558Impact Factor: 7.119 1. -
THE 7Th EXPLORATORY WORKHOP "DEFENSE RESOURCES MANAGEMENT - TRENDS and OPORTUNITIES"
REGIONAL DEPARTMENT OF DEFENSE RESOURCES MANAGEMENT STUDIES THE 7th EXPLORATORY WORKHOP "DEFENSE RESOURCES MANAGEMENT - TRENDS AND OPORTUNITIES" ISSN: 2286 - 2781 ISSN- L: 2286 - 2781 COORDINATOR: Junior lecturer Brînduşa POPA National Defense University “Carol I” Publishing House Bucharest 2012 THE 7th EXPLORATORY WORKHOP "DEFENSE RESOURCES MANAGEMENT - TRENDS AND OPORTUNITIES" WORKSHOP COMMITTEE: Col. Senior Lecturer Cezar VASILESCU, PhD. Col. Military Professor Daniel SORA, PhD. University Lecturer Maria CONSTANTINESCU, PhD. Junior Lecturer Aura CODREANU, PhD. Junior Lecturer Brînduşa POPA, PhD candidate SESSION CHAIRMEN Col. Senior Lecturer Cezar VASILESCU, PhD. Col. Military Professor Daniel SORA, PhD. University Lecturer Maria CONSTANTINESCU, PhD. Junior Lecturer Aura CODREANU, PhD. Junior Lecturer Brînduşa POPA, PhD candidate 2 THE 7th EXPLORATORY WORKHOP "DEFENSE RESOURCES MANAGEMENT - TRENDS AND OPORTUNITIES" 08 November 2012 Proceedings of the workshop unfolded during the Defense Resources Management Course for Senior Officials Conducted by the Regional Department of Defense Resources Management Studies 01 October - 23 November 2012 Braşov ROMÂNIA 3 This page is intentionally left blank 4 CONTENTS SECURITY RISK MANAGEMENT NON-GOVERNMENTAL ORGANIZATION APPROACH CPT CDR Călin AVRAM……………………………………………………..………………..7 COMMUNICATION IN MILITARY ORGANIZATIONS CPT CDR Marius BĂNICĂ……………………………………………………………………20 CONSIDERATION ABOUT GROUP DECISION MAKING PROCESS CPT. CDR Marian BOBE…………………………………………………………………...…...39 CONSIDERATION ABOUT POLITICAL -
Chapter 5: Quality Tools for Six Sigma 2
Six Sigma Quality: Concepts & Cases‐ Volume I STATISTICAL TOOLS IN SIX SIGMA DMAIC PROCESS WITH MINITAB® APPLICATIONS Chapter 5 Quality Tools for Six Sigma Basic Quality Tools and Seven New Tools ©Amar Sahay, Ph.D. 1 Chapter 5: Quality Tools for Six Sigma 2 Chapter Highlights This chapter deals with the quality tools widely used in Six Sigma and quality improvement programs. The chapter includes the seven basic tools of quality, the seven new tools of quality, and another set of useful tools in Lean Six Sigma that we refer to –“beyond the basic and new tools of quality.” The objective of this chapter is to enable you to master these tools of quality and use these tools in detecting and solving quality problems in Six Sigma projects. You will find these tools to be extremely useful in different phases of Six Sigma. They are easy to learn and very useful in drawing meaningful conclusions from data. In this chapter, you will learn the concepts, various applications, and computer instructions for these quality tools of Six Sigma. This chapter will enable you to: 1. Learn the seven graphical tools ‐ considered the basic tools of quality. These are: (i) Process Maps (ii) Check sheets (iii) Histograms (iv) Scatter Diagrams (v) Run Charts/Control Charts (vi) Cause‐and‐Effect (Ishikawa)/Fishbone Diagrams (vii) Pareto Charts/Pareto Analysis 2. Construct the above charts using MINITAB 3. Apply these quality tools in Six Sigma projects 4. Learn the seven new tools of quality and their applications: (i) Affinity Diagram (ii) Interrelationship Digraph (iii) Tree Diagram (iv) Prioritizing Matrices (v) Matrix Diagram (vi) Process Decision Program Chart (vii) Activity Network Diagram 5. -
Pareto Chart
Pareto Chart Usage Pareto analysis is a way of organizing data to show what major factor(s) are significantly contributing to the effect being analyzed (i.e., how much each cause contributes to the problem at hand). Such analysis can help you: • choose a starting point for problem solving • identify the Root Cause of a problem • monitor success in a process improvement program A Pareto Chart is a type of histogram in which the height of each bar represents the relative contribution of that element to the overall problem. Consistent with the "80-20" rule ("80% of the results are produced by 20% of the causes"), Pareto Charts usually reveal that a majority of the problematic results of a process can be traced to only a few specific causes. Having identified the Root Causes with a Pareto Chart, you can then make changes to the process, confident that you are working with the "vital few" sources of problems rather than the "trivial many". Instructions To construct a Pareto Chart, follow these instructions: 1. Use data collected in a Checksheet. 2. Select the categories of information to be included, and establish a standard unit of measurement. 3. Rank the data in descending order. 4. Construct a vertical bar chart with the categories listed left to right in descending order: • The horizontal (X) axis represents the categories or defect types. • The left vertical (Y) axis represents the statistic of interest (e.g., cumulative total of occurrences, number of defects). • The right vertical (Y) axis represents a cumulative percent of occurrences. 5. Analyze the pattern displayed: • If the pattern is relatively flat (i.e., different categories contribute equally to the result), reconsider your categories (e.g., restratify the data) and make a new Chart. -
Pareto Analysis and Check Sheets
Performance Excellence in the Wood Products Industry Statistical Process Control Part 3: Pareto Analysis & Check Sheets EM 8771 • January 2002 Scott Leavengood and James E. Reeb art 1 in this series introduced the reader to Statistical Process Control, and Part 2 provided an overview of how and why SPC works. Part 3 begins the step-by-step Pprocess of building the practical skills necessary for hands-on implementation of SPC. This report discusses Pareto analysis, a tool we can use to help decide how and where to begin using SPC. We also discuss check sheets, which are data collection tools that may be used in Pareto analysis. Part 4 discusses flowcharts. Future publications in the series will discuss case histories of wood products firms using SPC, providing real-world evidence of the benefits of SPC and examining pitfalls and successful approaches. Where to begin an SPC program? Most manufacturing processes are sufficiently complex that at first glance it may seem impossible to decide where to begin using SPC techniques. SPC programs that attempt to monitor too many process variables are quickly overwhelmed by the time and labor required to collect, analyze, plot, and interpret the data. In such cases, SPC seems too time consuming and expensive to be of any benefit. The life expectancy of SPC in a company depends heavily on the results of the first few projects undertaken. With this kind of pressure, how do you decide where to begin? Obviously, we cannot measure everything. We must focus initially on the most import- ant quality problems to get the “biggest bang for the buck.” This is especially true in the early stages of an SPC program when personnel are likely to be skeptical of SPC and hesi- tant to make the necessary changes. -
Seven Basic Tools of Quality Control: the Appropriate Techniques for Solving Quality Problems in the Organizations
UC Santa Barbara UC Santa Barbara Previously Published Works Title Seven Basic Tools of Quality Control: The Appropriate Techniques for Solving Quality Problems in the Organizations Permalink https://escholarship.org/uc/item/2kt3x0th Author Neyestani, Behnam Publication Date 2017-01-03 eScholarship.org Powered by the California Digital Library University of California 1 Seven Basic Tools of Quality Control: The Appropriate Techniques for Solving Quality Problems in the Organizations Behnam Neyestani [email protected] Abstract: Dr. Kaoru Ishikawa was first total quality management guru, who has been associated with the development and advocacy of using the seven quality control (QC) tools in the organizations for problem solving and process improvements. Seven old quality control tools are a set of the QC tools that can be used for improving the performance of the production processes, from the first step of producing a product or service to the last stage of production. So, the general purpose of this paper was to introduce these 7 QC tools. This study found that these tools have the significant roles to monitor, obtain, analyze data for detecting and solving the problems of production processes, in order to facilitate the achievement of performance excellence in the organizations. Keywords: Seven QC Tools; Check Sheet; Histogram; Pareto Analysis; Fishbone Diagram; Scatter Diagram; Flowcharts, and Control Charts. INTRODUCTION There are seven basic quality tools, which can assist an organization for problem solving and process improvements. The first guru who proposed seven basic tools was Dr. Kaoru Ishikawa in 1968, by publishing a book entitled “Gemba no QC Shuho” that was concerned managing quality through techniques and practices for Japanese firms. -
Design of Experiments EM 9045 • October 2011 Scott Leavengood and James E
Performance Excellence in the Wood Products Industry Statistical Process Control Part 6: Design of Experiments EM 9045 • October 2011 Scott Leavengood and James E. Reeb ur focus for the first five publications in this series has been on introducing you to Statistical Process Control (SPC)—what it is, how and why it works, and how to Odetermine where to focus initial efforts to use SPC in your company. Experience has shown that SPC is most effective when focused on a few key areas as opposed to measuring anything and everything. With that in mind, we described how tools such as Pareto analysis and check sheets (Part 3) help with project selection by revealing the most frequent and costly problems. Then we emphasized how constructing flowcharts (Part 4) helps build consensus on the actual steps involved in a process, which in turn helps define where quality problems might be occurring. We also showed how cause-and-effect diagrams (Part 5) help quality improvement teams identify the root cause of problems. In Part 6, we continue the discussion of root cause analysis with a brief introduction to design of experiments (DOE). We have yet to cover the most common tool of SPC: con- trol charts. It is important, however, to not lose sight of the primary goal: Improve quality, and in so doing, improve customer satisfaction and the company’s profitability. We’ve identified potential causes, but what’s the true cause? In an example that continues throughout this series, a quality improvement team from XYZ Forest Products Inc. (a fictional company) identified an important quality prob- lem, identified the process steps where problems may occur, and brainstormed potential causes. -
Root Cause Analysis in Post Project Phases As Application of Knowledge Management
sustainability Article Root Cause Analysis in Post Project Phases as Application of Knowledge Management Radek Doskoˇcil 1,* and Branislav Lacko 2 1 Department of Informatics, Faculty of Business and Management, Brno University of Technology, Kolejní 2906/4, 612 00 Brno, Czech Republic 2 Institute of Automation and Computer Science, Faculty of Mechanical Engineering, Brno University of Technology, Technická 2896/2, 616 69 Brno, Czech Republic, [email protected] * Correspondence: [email protected]; Tel.: +420-541-143-722 Received: 20 February 2019; Accepted: 17 March 2019; Published: 19 March 2019 Abstract: This paper is focused on the root cause analysis of post project phases. The research has been linked to the identification of the 21 most common reasons for not executing post project phases. The main aim of this paper is to identify the root causes of not executing selected post project phases. The empirical research was performed as qualitative research employing the observation and inquiry methods in the form of a controlled semi-structured interview. The research was realised in the Czech Republic in 2017 and 2018. The key performances for ensuring a functional, effective and systematic post project process are based on the principles of knowledge management. The identified causes were used as inputs for the proposed measures with the aim to make the post project process more effective. The main contribution of the paper is the overview of techniques that may be recommended for post project analysis. These techniques are demonstrated in detail on particular examples of the analysis of the most common reasons for failure to implement post project phases. -
STAT1010 – Picturing Data 1
STAT1010 – picturing data 3.2 Visualizing Distributions of data ! A frequency table provides information on the distribution of data. " When we discuss the distribution of a variable, we are referring to the possible values, and which of the values occur more (or less) frequently than the others. Political affiliation Frequency Occurred Democrat 517 a lot Possible Republican 371 values Independent 112 Occurred less frequently1 The distribution of the data ! The distribution of data is the way the data values are spread over all possible values. " What values occur frequently? " If the variable is numeric, what is the maximum value? What is the minimum value? " What is the “shape” of the distribution Weight of Contents of Cans of Cola 15 10 y c n e u q e r 5 F 0 330 340 350 360 370 380 390 Weight (grams) 2 Graphical displays of distributions ! As the phrase goes… “a picture is worth 1000 words”, and distributions are often better conveyed using graphics rather than tables. Political affiliation in a 1000 person survey 600 Political Frequency 500 affiliation 400 Democrat 517 300 Republican 371 200 Independent 112 frequency of affiliation 100 0 Democrat Republican Independent 3 politican affiliation 1 STAT1010 – picturing data Pioneer in Statistical Graphics ! Florence Nightingale " See video clip from “Joy of Statistics” 4 Bar graph ! Used to represent frequencies (or relative frequencies) for qualitative or categorical variables. Political affiliation in a 1000 person survey 600 500 400 300 200 frequency of affiliation 100 0 Democrat Republican Independent 5 politican affiliation Bar graph - labels ! Always provide useful labels. -
Pareto Charts Distribution and Causal Analysis Tools
Pareto Charts Distribution and Causal Analysis Tools The Pareto chart is a specialized version of a histogram that ranks the categories in the chart from most frequent to least frequent. A Pareto Chart is useful for non-numeric data, such as "cause", "type", or "classification". This tool helps to prioritize where action and process changes should be focused. If one is trying to take action based upon causes of accidents or events, it is generally most helpful to focus efforts on the most frequent causes. Going after an "easy" yet infrequent cause will probably not reap benefits. There actually was a person named "Pareto" who developed this chart as part of an analysis of economics data more than 100 years ago. He determined that a large portion of the economy was controlled by a small portion of the people within the economy. Likewise, one doing analysis of accidents or events may find that a large portion of the accidents are cause by a small population of causes. The "Pareto Principle" states that 80% of the problems come from 20% of the causes. The Pareto Chart analysis should be performed over a fixed time interval of performance indicator results. The Pareto Chart analysis should only be performed after the control chart analysis is complete. The time interval should be chosen depending on the existence or non-existence of statistically significant trends as follows: Trend Exists on Control Data Points Used Purpose Chart? Use all data in the statistically stable Find Common Cause(s) to apply to No time period process improvement Use only the data for the point(s) Find Special Cause(s) for basis of which have been identified as within corrective actions for declining Yes the significant trend, such as a point trends or reinforcing actions for outside the control limits improving trends This consideration of significant trends is important as the frequency distribution in each category may be different due to the process changes which occurred to cause the significant trend.