Quality Tools for Six Sigma
Total Page:16
File Type:pdf, Size:1020Kb
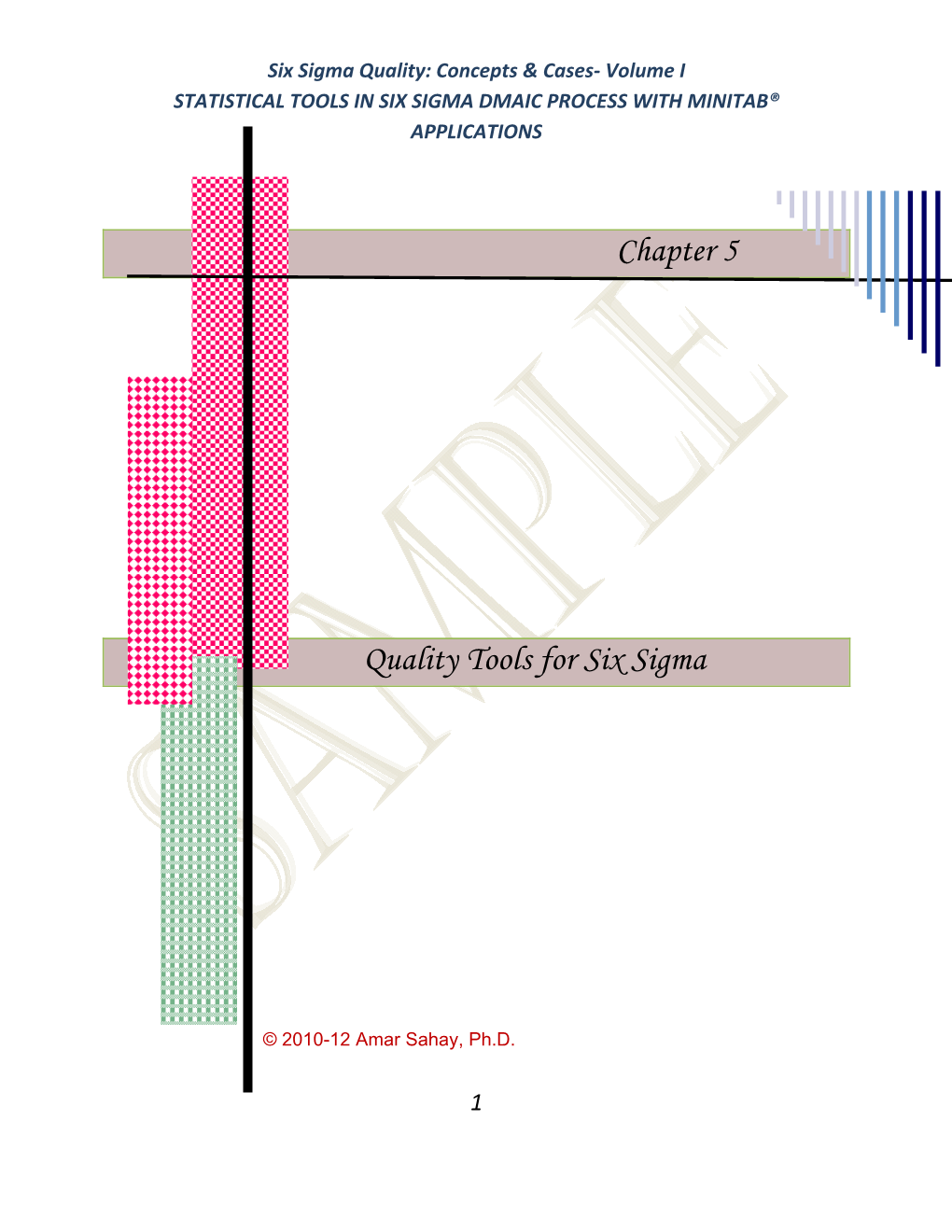
Load more
Recommended publications
-
Implementing SPC for Non-Normal Processes with the I-MR Chart: a Case Study
Implementing SPC for non-normal processes with the I-MR chart: A case study Axl Elisson Master of Science Thesis TPRMM 2017 KTH Industrial Engineering and Management Production Engineering and Management SE-100 44 STOCKHOLM Acknowledgements This master thesis was performed at the brake manufacturer Haldex as my master of science degree project in Industrial Engineering and Management at the Royal Institute of Technology (KTH) in Stockholm, Sweden. It was conducted during the spring semester of 2017. I would first like to thank my supervisor at Haldex, Roman Berg, and Annika Carlius for their daily support and guidance which made this project possible. I would also like to thank the quality department, production engineers and operators at Haldex for all insight in different subjects. Finally, I would like to thank my supervisor at KTH, Jerzy Mikler, for his support during my thesis. All of your combined expertise have been very valuable. Stockholm, July 2017 Axl Elisson Abstract The application of statistical process control (SPC) requires normal distributed data that is in statistical control in order to determine valid process capability indices and to set control limits that reflects the process’ true variation. This study examines a case of several non-normal processes and evaluates methods to estimate the process capability and set control limits that is in relation to the processes’ distributions. Box-Cox transformation, Johnson transformation, Clements method and process performance indices were compared to estimate the process capability and the Anderson-Darling goodness-of-fit test was used to identify process distribution. Control limits were compared using Clements method, the sample standard deviation and from machine tool variation. -
Statistical Process Control Tools: a Practical Guide for Jordanian Industrial Organizations
Volume 4, Number 6, December 2010 ISSN 1995-6665 JJMIE Pages 693 - 700 Jordan Journal of Mechanical and Industrial Engineering www.jjmie.hu.edu.jo Statistical Process Control Tools: A Practical guide for Jordanian Industrial Organizations Rami Hikmat Fouad*, Adnan Mukattash Department of Industrial Engineering, Hashemite University, Jordan. Abstract The general aim of this paper is to identify the key ingredients for successful quality management in any industrial organization. Moreover, to illustrate how is it important to realize the intergradations between Statistical Process Control (SPC) is seven tools (Pareto Diagram, Cause and Effect Diagram, Check Sheets, Process Flow Diagram, Scatter Diagram, Histogram and Control Charts), and how to effectively implement and to earn the full strength of these tools. A case study has been carried out to monitor real life data in a Jordanian manufacturing company that specialized in producing steel. Flow process chart was constructed, Check Sheets were designed, Pareto Diagram, scatter diagrams, Histograms was used. The vital few problems were identified; it was found that the steel tensile strength is the vital few problem and account for 72% of the total results of the problems. The principal aim of the project is to train quality team on how to held an effective Brainstorming session and exploit these data in cause and effect diagram construction. The major causes of nonconformities and root causes of the quality problems were specified, and possible remedies were proposed. © 2010 Jordan Journal of Mechanical and Industrial Engineering. All rights reserved Keywords: Statistical Process Control, Check sheets, Process Flow Diagram, Pareto Diagram, Histogram, Scatter Diagram, Control Charts, Brainstorming, and Cause and Effect Diagram. -
Cause and Effect Diagrams
Online Student Guide Cause and Effect Diagrams OpusWorks 2019, All Rights Reserved 1 Table of Contents LEARNING OBJECTIVES ....................................................................................................................................4 INTRODUCTION ..................................................................................................................................................4 WHAT IS A “ROOT CAUSE”? ......................................................................................................................................................... 4 WHAT IS A “ROOT CAUSE ANALYSIS”?...................................................................................................................................... 4 ADDRESSING THE ROOT CAUSE .................................................................................................................................................. 5 ROOT CAUSE ANALYSIS: THREE BASIC STEPS ........................................................................................................................ 5 CAUSE AND EFFECT TOOLS .......................................................................................................................................................... 6 FIVE WHYS ...........................................................................................................................................................6 THE FIVE WHYS ............................................................................................................................................................................ -
Root Cause Analysis of Defects in Automobile Fuel Pumps: a Case Study
International Journal of Management, IT & Engineering Vol. 7 Issue 4, April 2017, ISSN: 2249-0558 Impact Factor: 7.119 Journal Homepage: http://www.ijmra.us, Email: [email protected] Double-Blind Peer Reviewed Refereed Open Access International Journal - Included in the International Serial Directories Indexed & Listed at: Ulrich's Periodicals Directory ©, U.S.A., Open J-Gage as well as in Cabell‟s Directories of Publishing Opportunities, U.S.A ROOT CAUSE ANALYSIS OF DEFECTS IN AUTOMOBILE FUEL PUMPS: A CASE STUDY Saurav Adhikari* Nilesh Sachdeva* Dr. D.R. Prajapati** ABSTRACT Quality can be directly measured from the degree to which customer requirements are satisfied. Some problems were reported by the customers of the automobile company under study in the fuel pumps; which is used in an automobile to transfer the fuel from fuel tank to fuel injection system after filtration.This paper presents the implementation of Quality Control tools– Check Sheet, Fishbone Diagram(or Ishikawa Diagram), ParetoChartand 5-Why analysis tools for identification and elimination of the root cause/s responsible for malfunctioning of the fuel pump in customers‟ cars. From the Check sheet and Pareto analysis, two major defects were identified which accounted for more than 80% of the problems being reported. The root causes of these two defects affecting the product quality of the company were then further analyzed using the 5- Why analysis. Keywords: Quality Control Tools, Ishikawa Diagram, Pareto Chart, 5-Why Analysis * Undergraduate Student, Department of Mechanical Engineering, PEC University of Technology, (formerly Punjab Engineering College), Chandigarh ** Associate Professor& Corresponding Author, Department of Mechanical Engineering, PEC University of Technology (formerly Punjab Engineering College), Chandigarh 90 International journal of Management, IT and Engineering http://www.ijmra.us, Email: [email protected] ISSN: 2249-0558Impact Factor: 7.119 1. -
Use Process Capability to Ensure Product Quality
Use Process Capability to Ensure Product Quality Lawrence X. Yu, Ph.D. Director (acting) Office of Pharmaceutical Science, CDER, FDA FDA/ PQRI Conference on Evolving Product Quality September 16-17, 2104, Bethesda, MD 1 2 Quality by Testing vs. Quality by Design Quality by Testing – Specification acceptance criteria are based on one or more batch data (process capability) – Testing must be made to release batches Quality by Design – Specification acceptance criteria are based on performance – Testing may not be necessary to release batches L. X. Yu. Pharm. Res. 25:781-791 (2008) 3 ICH Q6A: Test Procedures and Acceptance Criteria… 4 5 Pharmaceutical QbD Objectives Achieve meaningful product quality specifications that are based on assuring clinical performance Increase process capability and reduce product variability and defects by enhancing product and process design, understanding, and control Increase product development and manufacturing efficiencies Enhance root cause analysis and post-approval change management 6 Concept of Process Capability First introduced in Statistical Quality Control Handbook by the Western Electric Company (1956). – “process capability” is defined as “the natural or undisturbed performance after extraneous influences are eliminated. This is determined by plotting data on a control chart.” ISO, AIAG, ASQ, ASTM ….. published their guideline or manual on process capability index calculation 7 Nomenclature Four indices: – Cp: process capability index – Cpk: minimum process capability index – Pp: process -
Mistakeproofing the Design of Construction Processes Using Inventive Problem Solving (TRIZ)
www.cpwr.com • www.elcosh.org Mistakeproofing The Design of Construction Processes Using Inventive Problem Solving (TRIZ) Iris D. Tommelein Sevilay Demirkesen University of California, Berkeley February 2018 8484 Georgia Avenue Suite 1000 Silver Spring, MD 20910 phone: 301.578.8500 fax: 301.578.8572 ©2018, CPWR-The Center for Construction Research and Training. All rights reserved. CPWR is the research and training arm of NABTU. Production of this document was supported by cooperative agreement OH 009762 from the National Institute for Occupational Safety and Health (NIOSH). The contents are solely the responsibility of the authors and do not necessarily represent the official views of NIOSH. MISTAKEPROOFING THE DESIGN OF CONSTRUCTION PROCESSES USING INVENTIVE PROBLEM SOLVING (TRIZ) Iris D. Tommelein and Sevilay Demirkesen University of California, Berkeley February 2018 CPWR Small Study Final Report 8484 Georgia Avenue, Suite 1000 Silver Spring, MD 20910 www. cpwr.com • www.elcosh.org TEL: 301.578.8500 © 2018, CPWR – The Center for Construction Research and Training. CPWR, the research and training arm of the Building and Construction Trades Department, AFL-CIO, is uniquely situated to serve construction workers, contractors, practitioners, and the scientific community. This report was prepared by the authors noted. Funding for this research study was made possible by a cooperative agreement (U60 OH009762, CFDA #93.262) with the National Institute for Occupational Safety and Health (NIOSH). The contents are solely the responsibility of the authors and do not necessarily represent the official views of NIOSH or CPWR. i ABOUT THE PROJECT PRODUCTION SYSTEMS LABORATORY (P2SL) AT UC BERKELEY The Project Production Systems Laboratory (P2SL) at UC Berkeley is a research institute dedicated to developing and deploying knowledge and tools for project management. -
Chapter 6: Process Capability Analysis for Six Sigma
Six Sigma Quality: Concepts & Cases‐ Volume I STATISTICAL TOOLS IN SIX SIGMA DMAIC PROCESS WITH MINITAB® APPLICATIONS Chapter 6 PROCESS CAPABILITY ANALYSIS FOR SIX SIGMA © Amar Sahay, Ph.D. Master Black Belt 1 Chapter 6: Process Capability Analysis for Six Sigma CHAPTER HIGHLIGHTS This chapter deals with the concepts and applications of process capability analysis in Six Sigma. Process Capability Analysis is an important part of an overall quality improvement program. Here we discuss the following topics relating to process capability and Six Sigma: 1. Process capability concepts and fundamentals 2. Connection between the process capability and Six Sigma 3. Specification limits and process capability indices 4. Short‐term and long‐term variability in the process and how they relate to process capability 5. Calculating the short‐term or long‐term process capability 6. Using the process capability analysis to: assess the process variability establish specification limits (or, setting up realistic tolerances) determine how well the process will hold the tolerances (the difference between specifications) determine the process variability relative to the specifications reduce or eliminate the variability to a great extent 7. Use the process capability to answer the following questions: Is the process meeting customer specifications? How will the process perform in the future? Are improvements needed in the process? Have we sustained these improvements, or has the process regressed to its previous unimproved state? 8. Calculating process -
Lean Six Sigma Rapid Cycle Improvement Agenda
Lean Six Sigma Rapid Cycle Improvement Agenda 1. History of Lean and Six Sigma 2. DMAIC 3. Rapid Continuous Improvement – Quick Wins – PDSA – Kaizen Lean Six Sigma Lean Manufacturing Six Sigma (Toyota Production System) DMAIC • T.I.M.W.O.O.D • PROJECT CHARTER • 5S • FMEA • SMED • PDSA/PDCA • TAKT TIME • SWOT • KAN BAN • ROOT CAUSE ANALYSIS • JUST IN TIME • FMEA • ANDON • SIPOC • KAIZEN • PROCESS MAP • VALUE STREAM MAP • STATISTICAL CONTROLS Process Improvement 3 Lean Manufacturing • Lean has been around a long time: – Pioneered by Ford in the early 1900’s (33 hrs from iron ore to finished Model T, almost zero inventory but also zero flexibility!) – Perfected by Toyota post WWII (multiple models/colors/options, rapid setups, Kanban, mistake-proofing, almost zero inventory with maximum flexibility!) • Known by many names: – Toyota Production System – Just-In-Time – Continuous Flow • Outwardly focused on being flexible to meet customer demand, inwardly focused on reducing/eliminating the waste and cost in all processes Six Sigma • Motorola was the first advocate in the 80’s • Six Sigma Black Belt methodology began in late 80’s/early 90’s • Project implementers names includes “Black Belts”, “Top Guns”, “Change Agents”, “Trailblazers”, etc. • Implementers are expected to deliver annual benefits between $500,000 and $1,000,000 through 3-5 projects per year • Outwardly focused on Voice of the Customer, inwardly focused on using statistical tools on projects that yield high return on investment DMAIC Define Measure Analyze Improve Control • Project Charter • Value Stream Mapping • Replenishment Pull/Kanban • Mistake-Proofing/ • Process Constraint ID and • Voice of the Customer • Value of Speed (Process • Stocking Strategy Zero Defects Takt Time Analysis and Kano Analysis Cycle Efficiency / Little’s • Process Flow Improvement • Standard Operating • Cause & Effect Analysis • SIPOC Map Law) • Process Balancing Procedures (SOP’s) • FMEA • Project Valuation / • Operational Definitions • Analytical Batch Sizing • Process Control Plans • Hypothesis Tests/Conf. -
THE 7Th EXPLORATORY WORKHOP "DEFENSE RESOURCES MANAGEMENT - TRENDS and OPORTUNITIES"
REGIONAL DEPARTMENT OF DEFENSE RESOURCES MANAGEMENT STUDIES THE 7th EXPLORATORY WORKHOP "DEFENSE RESOURCES MANAGEMENT - TRENDS AND OPORTUNITIES" ISSN: 2286 - 2781 ISSN- L: 2286 - 2781 COORDINATOR: Junior lecturer Brînduşa POPA National Defense University “Carol I” Publishing House Bucharest 2012 THE 7th EXPLORATORY WORKHOP "DEFENSE RESOURCES MANAGEMENT - TRENDS AND OPORTUNITIES" WORKSHOP COMMITTEE: Col. Senior Lecturer Cezar VASILESCU, PhD. Col. Military Professor Daniel SORA, PhD. University Lecturer Maria CONSTANTINESCU, PhD. Junior Lecturer Aura CODREANU, PhD. Junior Lecturer Brînduşa POPA, PhD candidate SESSION CHAIRMEN Col. Senior Lecturer Cezar VASILESCU, PhD. Col. Military Professor Daniel SORA, PhD. University Lecturer Maria CONSTANTINESCU, PhD. Junior Lecturer Aura CODREANU, PhD. Junior Lecturer Brînduşa POPA, PhD candidate 2 THE 7th EXPLORATORY WORKHOP "DEFENSE RESOURCES MANAGEMENT - TRENDS AND OPORTUNITIES" 08 November 2012 Proceedings of the workshop unfolded during the Defense Resources Management Course for Senior Officials Conducted by the Regional Department of Defense Resources Management Studies 01 October - 23 November 2012 Braşov ROMÂNIA 3 This page is intentionally left blank 4 CONTENTS SECURITY RISK MANAGEMENT NON-GOVERNMENTAL ORGANIZATION APPROACH CPT CDR Călin AVRAM……………………………………………………..………………..7 COMMUNICATION IN MILITARY ORGANIZATIONS CPT CDR Marius BĂNICĂ……………………………………………………………………20 CONSIDERATION ABOUT GROUP DECISION MAKING PROCESS CPT. CDR Marian BOBE…………………………………………………………………...…...39 CONSIDERATION ABOUT POLITICAL -
Chapter 15 Statistics for Quality: Control and Capability
Aaron_Amat/Deposit Photos Statistics for Quality: 15 Control and Capability Introduction CHAPTER OUTLINE For nearly 100 years, manufacturers have benefited from a variety of statis tical tools for the monitoring and control of their critical processes. But in 15.1 Statistical Process more recent years, companies have learned to integrate these tools into their Control corporate management systems dedicated to continual improvement of their 15.2 Variable Control processes. Charts ● Health care organizations are increasingly using quality improvement methods 15.3 Process Capability to improve operations, outcomes, and patient satisfaction. The Mayo Clinic, Johns Indices Hopkins Hospital, and New York-Presbyterian Hospital employ hundreds of quality professionals trained in Six Sigma techniques. As a result of having these focused 15.4 Attribute Control quality professionals, these hospitals have achieved numerous improvements Charts ranging from reduced blood waste due to better control of temperature variation to reduced waiting time for treatment of potential heart attack victims. ● Acushnet Company is the maker of Titleist golf balls, which is among the most popular brands used by professional and recreational golfers. To maintain consistency of the balls, Acushnet relies on statistical process control methods to control manufacturing processes. ● Cree Incorporated is a market-leading innovator of LED (light-emitting diode) lighting. Cree’s light bulbs were used to glow several venues at the Beijing Olympics and are being used in the first U.S. LED-based highway lighting system in Minneapolis. Cree’s mission is to continually improve upon its manufacturing processes so as to produce energy-efficient, defect-free, and environmentally 15-1 19_psbe5e_10900_ch15_15-1_15-58.indd 1 09/10/19 9:23 AM 15-2 Chapter 15 Statistics for Quality: Control and Capability friendly LEDs. -
Statistical Quality Control and Process Capability Analysis for Variability
ering & ine M g a et al., n n E Rábago-Remy Ind Eng Manage 2014, 3:4 a l g a i e r m t s DOI: 10.4172/2169-0316.1000137 e u n d t n I Industrial Engineering & Management ISSN: 2169-0316 Research Article Open Access Statistical Quality Control and Process Capability Analysis for Variability Reduction of the Tomato Paste Filling Process Dulce María Rábago-Remy, Edith Padilla-Gasca and Jesús Gabriel Rangel-Peraza* Departamento de Estudios de Posgrado e Investigación, Instituto Tecnológico de Culiacán, Juan de Dios Batiz 310 Pte. Col. Guadalupe. Culiacán Sinaloa, México Abstract In this research some techniques for process statistical control were applied, such as frequency histograms, Pareto diagrams, process capability analysis and control charts. The purpose of this investigation was to reduce the variability of the canned tomato paste filling process coming from a tomato processing food industry that has problems with the net weight of their processed product. The results of the process capability analysis showed that 35.52% of the observations were out of the specifications during the months in study, which generates a real capability of the process (Cpk) of 0.124, and it indicates that the process does not have enough ability to fulfill the required specifications by the firm. The process potential capability (Cp) is 0.676. Given that Cpk < Cp, then it is concluded that the process is not centered, indicating that the measurement of the filling process is away from the center of the specifications. The process fits 0.371 sigma between the process mean and the nearest specification limit. -
Poka-Yoke and Quality Control on Traub Machine for Kick Starter Driven Shaft
Journal of Material Science and Mechanical Engineering (JMSME) Print ISSN: 2393-9095; Online ISSN: 2393-9109; Volume 2, Number 7; April-June, 2015 pp. 10-15 © Krishi Sanskriti Publications http://www.krishisanskriti.org/jmsme.html Poka-Yoke and Quality Control on Traub Machine for Kick Starter Driven Shaft Atif Jamal 1, Ujjwal Kumar 2, Aftab A. Ansari 3, Balwant Singh 4 1,2,3,4 M.Tech Scholar, SET, Sharda University, GN, U.P [email protected], [email protected] [email protected], [email protected] Abstract: This study was conducted in manufacturing creation of process stoppages, and provides tools and methods environment and focused at machining operation. Fair Products for designing them. India, which manufactures auto ancillaries, was selected for this research. Fair Products has been facing tremendous pressure of In study Chen et al. (1996) , has also considers that a Poka- quality level and in house rejection due to under sizing of the parts manufactured on Traub Machine. After sometime the yoke is a mechanism for detecting, eliminating, and correcting process begins to fail as number of defects begins to increase as errors at their source, before they reach the customer. such the management has thrown challenge to the manufacturing team to find ways to improve the outgoing quality at machining C M Hinckley (2003) although the occurrence of mistakes is operation. Thus, Error Proofing method was adopted for inevitable, non-conformances and defects is not. To prevent implementation at Traub Machining operation. Experimental defects caused by mistakes, our approach to quality control research was carried out to see the effectiveness of Error must include several new elements.