Applying the Plan-Do-Check-Act (PDCA) Cycle to Reduce the Defects in the Manufacturing Industry
Total Page:16
File Type:pdf, Size:1020Kb
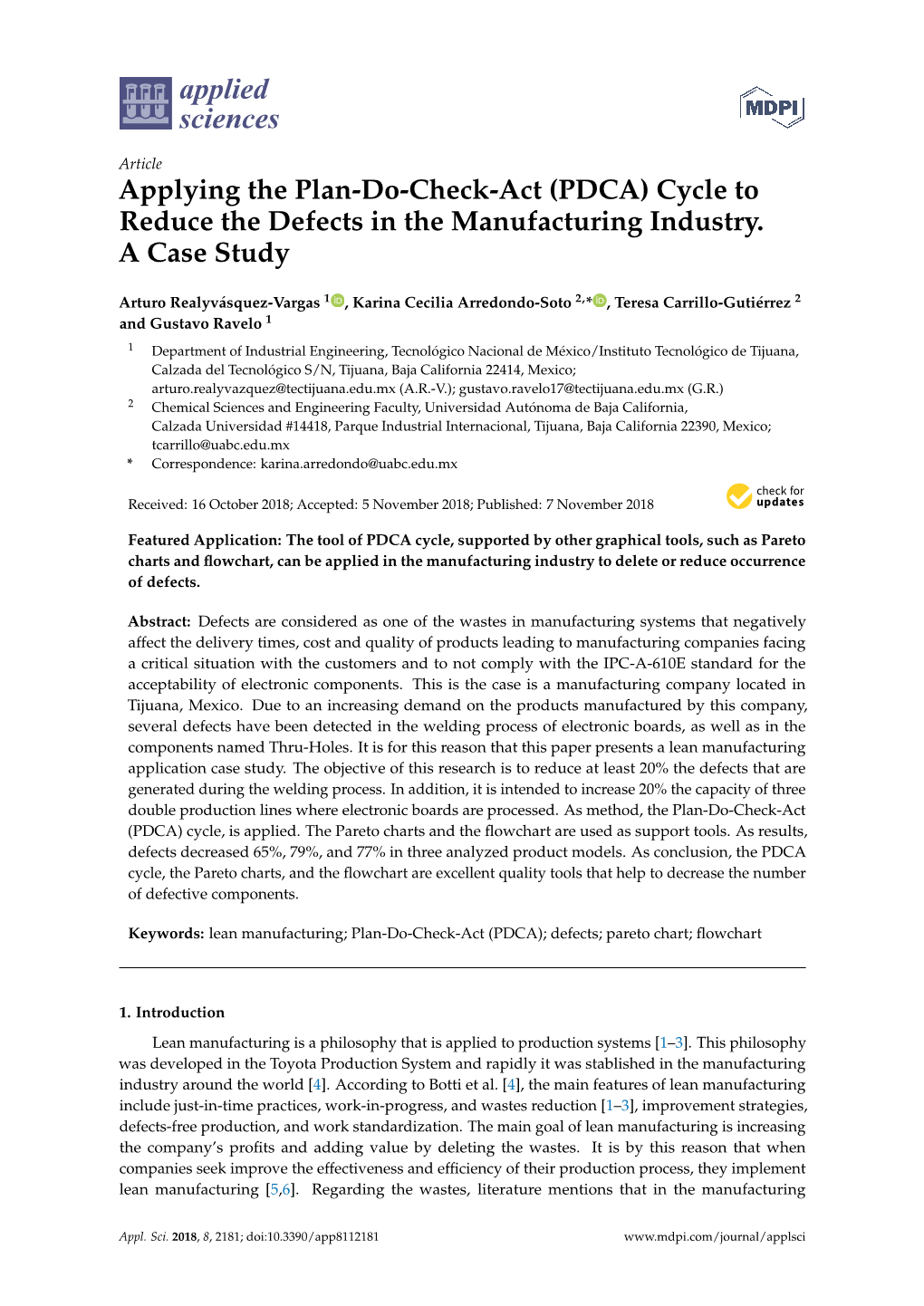
Load more
Recommended publications
-
CONTINUOUS IMPROVEMENT CONSULTING 2 First Choice Pocket Guide First Choice Pocket Guide 3
DHL FIRST CHOICE CONTINUOUS IMPROVEMENT CONSULTING 2 First Choice Pocket Guide First Choice Pocket Guide 3 CONTENTS Introduction 4 Methodologies 6 ACT 8 DMAIC 10 Lean 12 Tools 14 5S Methodology 16 5 Why 18 DILO (Day In Life Of) 20 Effort-Benefit-Matrix 22 Spaghetti Diagram 24 More information 27 To simplify the understanding of each tool a standard structure has been used for all tool deep-dives: Goals/Benefit: reasons for applying the tool / what’s in it for me When: recommendation of when tool can be applied Steps: guide on how to apply tool 4 First Choice Pocket Guide First Choice Pocket Guide 5 INTRODUCTION DHL First Choice is a DHL’s worldwide program to drive continuous improvement of processes and services. ‘Everybody, Every Day and Everywhere a little bit Better’ has enabled us to become and remain the first choice of our customers. This passion for continuous improvement is part of our DNA and is anchored in our corporate culture. It has allowed us to be a global market leader in logistics for many years now. We are happy to share our expertise and experience with you; now you too can experience what the First Choice approach can do for your company and your customers. We have already guided many customers in this process. Goal of DHL First Choice The goal is to create greater efficiency in your services and optimize your processes, with the help of our DHL First Choice experts. Improvements that increase your business performance and strengthen trust in your company. It will also positively impact your customer’s experience with your brand. -
Implementation of Kanban, a Lean Tool, in Switchgear Manufacturing Industry – a Case Study
Proceedings of the International Conference on Industrial Engineering and Operations Management Paris, France, July 26-27, 2018 Implementation of Kanban, a Lean tool, In Switchgear Manufacturing Industry – A Case Study Shashwat Gawande College Of Engineering, Pune Department of Industrial Engineering and management Savitribai Phule Pune University Pune, Maharashtra 44, India [email protected] Prof. J.S Karajgikar College Of Engineering, Pune Department of Industrial Engineering and management Savitribai Phule Pune University Pune, Maharashtra 44, India [email protected] Abstract Kanban is a scheduling system for lean and just in time manufacturing industries or services firms. It is a very effective tool for running a production system as a whole, in this system problem areas are highlighted by measuring lead time and cycle time of the full process the other benefits of the Kanban system is to establish an upper limit to work in process inventory to avoid over capacity. The objective of this case study is to implement a standard Kanban System for a Electrical manufacturing MNC company. With this system, the firm implemented use of just in time to reduce the inventory cost stocked during the process. This case study also shows that the Kanban implementation is not only bounded to the company but to their vendor also, from where, some of the components are been assembled. A replenishment strategy was also developed, tested and improved at the company location. A complete instruction manual is also developed as a reference Keywords Value Steam Mapping, Kanban, Root Cause Analysis, Replenishment Strategy 1. Introduction Lean manufacturing or simply ‘lean’ is a systematic method for waste reduction within a manufacturing system without affecting productivity. -
Sep 0 1 2004
AEROSPACE MERGERS AND ACQUISITIONS FROM A LEAN ENTERPRISE PERSPECTIVE by JUNHONG KIM B.S., Chemical Engineering Seoul National University (1998) SUBMITTED TO THE SYSTEM DESIGN AND MANAGEMENT PROGRAM IN PARTIAL FULFILLMENT OF THE REQUIREMENTS FOR THE DEGREE OF MASTER OF SCIENCE IN ENGINEERING AND MANAGEMENT at the MASSACHUSETTS INSTITUTE OF TECHNOLOGY June 2004 @0 2004 Junhong Kim. All rights reserved The author hereby grants to MIT permission to reproduce and to distribute publicly paper and electronic copies of this thesis document in whole or in part. Signature of Author......... ........................ Junhong Kim /ste7&Ies 'and Management Program February 2004 Certified by ... .........I . ...................... Joel Cutcher-Gershenfeld Executive Director, Engineering Systems Learning Center Senior Research Scientist, Sloan School of Management Accepted by ....................................................... -........................... Thomas J. Allen Co-Director, LFM/SDM Howard W. Johnson Professor of Management r A c c ep te d b y ............................. ......... ............................................................................................ David Simchi-Levi Co-Director, LFM/SDM MASSACHUSETTS INSTITUTE| Professor of Engineering Systems O.F TENL GYL.J SEP 0 1 2004 BARKER LIBRARIES Room 14-0551 77 Massachusetts Avenue Cambridge, MA 02139 Ph: 617.253.2800 MITL-ibries Email: [email protected] Document Services http://Iibraries.mit.eduldocs DISCLAIMER OF QUALITY Due to the condition of the original material, there -
Setting the Stage for Lean Manufacturing Success
Automotive SETTING THE STAGE FOR LEAN MANUFACTURING SUCCESS AUTHOR Despite careful study of lean production, many manufacturers miss out on Ron Harbour lean’s benefits—including lower costs, higher product quality, and greater employee productivity. Why? Beguiled by lean’s business systems and technical tools, they neglect the most important—and least understood— key to executing lean: people systems. Lean manufacturing has been active for a long time, traveling a 30-plus-year journey in the West. While the auto industry has led the effort, lean is now being broadly applied across a multitude of industries, ranging from hospitals and pharmaceuticals to electronics and aerospace. In the automotive production industry alone, a wealth of lean production programs has cropped up, as variations on the renowned Toyota Production System and Ford’s much earlier waste-reduction efforts. (See “Henry Ford’s Philosophy.”) HENRY FORD’S PHILOSOPHY As long as a century ago, Henry Ford embodied lean manufacturing philosophy. He believed that by controlling every link in his industry’s value chain, he could minimize the time it took to transform raw materials into manufactured vehicles. He could thus cut costs and create cars that could be sold at prices accessible to virtually everyone. Ford owned iron ore mines for the production of steel, beaches where sand could be gathered to make glass, even cattle ranches to serve as sources of leather for his autos’ upholstery. In today’s world of fractured value chains, where different entities own different links, few people remember Ford’s approach to taking time and cost out of the auto manufacturing process. -
Extension of the Lean 5S Methodology to 6S with an Additional Layer to Ensure Occupational Safety and Health Levels
sustainability Article Extension of the Lean 5S Methodology to 6S with An Additional Layer to Ensure Occupational Safety and Health Levels Mariano Jiménez 1,2 , Luis Romero 2,* , Jon Fernández 2, María del Mar Espinosa 2 and Manuel Domínguez 2 1 Department of Mechanical Engineering, Technical School of Engineering—ICAI, Comillas Pontifical University, 25, 28015 Madrid, Spain 2 Design Engineering Area, Industrial Engineering School, National Distance Education University (UNED), 38, 28015 Madrid, Spain * Correspondence: [email protected] Received: 12 June 2019; Accepted: 11 July 2019; Published: 12 July 2019 Abstract: This paper proposes an expansion of the Lean 5S methodology, which includes the concept of Safety–Security as 6S. Implementation was done by a standardized process tested in a pilot area that is part of the Integrated Industrial Manufacturing System Laboratory at the Higher Technical School of Engineering (ICAI). The additional 6S phase (Safety-Security) thoroughly reviews all areas of an industrial plant by analyzing the risks at each workstation, which let employees be fitted out with protection resources depending on each of their personal characteristics and to guarantee the safety of the workstation by strictly complying with occupational safety and health and machinery use standards, which must hold a CE certificate of compliance. The main objective was to increase the scope of 5S methodology to respond to the occupational safety and health needs for machines required in optimizing production processes. It is important to remember that companies must guarantee that their employees use personal protection equipment (PPE) at their work posts or stations that protect them properly from risks to their health and safety and that cannot be prevented or sufficiently limited by using collective means of protection or by adopting work organization measures. -
The Extent of Implementation of Lean Six Sigma Within Commercial Banks in Kenya
IOSR Journal of Business and Management (IOSR-JBM) e-ISSN: 2278-487X, p-ISSN: 2319-7668. Volume 18, Issue 12. Ver. II (December. 2016), PP 31-37 www.iosrjournals.org The Extent of Implementation of Lean Six Sigma within Commercial Banks in Kenya Beatrice Chelangat Abstract: The objectives of this study were to find out the extent to which Lean Six Sigma is implemented within commercial banks in Kenya. The respondents were made up of managers from these commercial banks in the Kenyan banking industry. The study adopted exploratory research. Primary data was collected using questionnaires and analyzed using descriptive statistics and factor analysis. The study found that the following application of tools and techniques of Lean and Six Sigma were used to a large extent; Voice of the Customers (VOC), Cause and effect analysis, Total Quality Management (TQM), Cross -functional work teams, Continuous Improvement (Kaizen), –Define- Measure- Analyze-Improve and Control (DMAIC) ,Total Preventive Maintenance and Plan, Do, Check, Act (PDCA). The study also found that two main ways through which the banks knew about Lean Six Sigma were through professional publications and through top management. Key Words: Lean Six Sigma I. Introduction Over the past decades, business organizations have embraced a wide variety of management programmes that they hope will enhance competitiveness. Currently, two of the most popular programmes are Six Sigma and Lean management. According to Wang & Chen (2010), Six Sigma approach is primarily a methodology for improving the capability of business processes by using statistical methods to identify and decrease or eliminate process variation. Its goal is reduction of defects and improvements in profits, employee morale and product quality. -
Decoding the DNA of the Toyota Production System
www.hbrreprints.org The Toyota story has been intensively researched and Decoding the DNA of painstakingly documented, yet what really happens inside the Toyota Production the company remains a mystery. Here’s new insight into the unspoken rules that System give Toyota its competitive edge. by Steven Spear and H. Kent Bowen Included with this full-text Harvard Business Review article: 1 Article Summary The Idea in Brief—the core idea The Idea in Practice—putting the idea to work 2 Decoding the DNA of the Toyota Production System 12 Further Reading A list of related materials, with annotations to guide further exploration of the article’s ideas and applications Reprint 99509 Decoding the DNA of the Toyota Production System The Idea in Brief The Idea in Practice Toyota’s renowned production system (TPS) TPS’s four rules: clude that their demand on the next ma- has long demonstrated the competitive ad- chine doesn’t match their expectations. All work is highly specified in its content, vantage of continuous process improve- They revisit the organization of their pro- sequence, timing, and outcome. ment. And companies in a wide range of duction line to determine why the machine Employees follow a well-defined sequence of industries—aerospace, metals processing, was not available, and redesign the flow steps for a particular job. This specificity en- consumer products—have tried to imitate path. ables people to see and address deviations TPS. Yet most fail. immediately—encouraging continual learn- Any improvement to processes, worker/ Why? Managers adopt TPS’s obvious prac- ing and improvement. -
White Paper the PDCA Cycle and Management System Standards
The PDCA cycle and Management System Standards ISO uses a very simple but powerful tool for quality system standards. This tool is the Plan- Do-Check-Act (PDCA) cycle shown in the figure below. It is also known as the Deming cycle after J.W. Deming, who proposed the concept in the 50s. The entire logic, structure, and sequence of standards like ISO 9001 and ISO 13485 are based on this cycle. Every process or activity needs to pass through these four phases. Plan Phase Perhaps, planning tasks are the most important ones in a management system. ISO recognizes this fact, as well as the fact that the plan phase should be the very first thing we do. To better understand this phase, activities like “establish” and “determine” should be associated to planning. Other words we can use instead are “identify” or “define”. Let´s see what an organization needs to plan. ACT PLAN First, the organization needs to establish its high- level planning. This will set direction and provide a framework for the entire system. We are talking about the organization´s purpose. And also, in CHECK DO terms of quality, about: policy, system´s scope, and objectives. The output of the high-level planning process will provide the necessary guide to the next step. The PDCA Cycle Next the organization needs to identify the processes that will be part of the quality system. It also needs to define how to apply or operate these processes, their sequence and how they interact. Also, the organization must identify risks related to the processes and how to control them according to those risks. -
The Concept and Implementation of Kaizen in an Organization
Global Journal of Management and Business Research: A Administration and Management Volume 19 Issue 1 Version 1.0 Year 201 Type: Double Blind Peer Reviewed International Research Journal Publisher: Global Journals Online ISSN: 2249-4588 & Print ISSN: 0975-5853 The Concept and Implementation of Kaizen in an Organization By Lubna Rahman Lina & Hafiz Ullah University of Dhaka Abstract- For continuous improvement in an organization, Japanese philosophy Kaizen is very popular. Flawless concepts of kaizen methodology and proper implementation of tools can lead to a successful kaizen program in a company. From the reviews of various case studies, it has revealed that most of the companies have implemented kaizen efficiently and observe better performance. Besides, some companies also failed to implement kaizen due to the lacking of proper knowledge about the concepts of kaizen. Keywords: kaizen, 5 why technique, 5s, 7 QC tools, 7 wastes, jidoka, PDCA cycle, poka-yoke. GJMBR-A Classification: JEL Code: M00 TheConceptandImplementationofKaizeninanOrganization Strictly as per the compliance and regulations of: © 2019. Lubna Rahman Lina & Hafiz Ullah. This is a research/review paper, distributed under the terms of the Creative Commons Attribution-Noncommercial 3.0 Unported License http://creativecommons.org/licenses/by-nc/3.0/), permitting all non-commercial use, distribution, and reproduction in any medium, provided the original work is properly cited. The Concept and Implementation of Kaizen in an Organization α σ Lubna Rahman Lina & Hafiz Ullah Abstract - For continuous improvement in an organization, over the longer term, without having to go through any Japanese philosophy Kaizen is very popular. Flawless radical innovation. It can be a much gentler and concepts of kaizen methodology and proper implementation employee-friendly way to institute the changes that must of tools can lead to a successful kaizen program in a occur as a business grows and adapts to its changing company. -
Quality Control
Topic Gateway Series Quality control Quality Control Topic Gateway Series No. 37 1 Prepared by Bill Haskins and Technical Information Service July 2007 Topic Gateway Series Quality control About Topic Gateways Topic Gateways are intended as a refresher or introduction to topics of interest to CIMA members. They include a basic definition, a brief overview and a fuller explanation of practical application. Finally they signpost some further resources for detailed understanding and research. Topic Gateways are available electronically to CIMA members only in the CPD Centre on the CIMA website, along with a number of electronic resources. About the Technical Information Service CIMA supports its members and students with its Technical Information Service (TIS) for their work and CPD needs. Our information specialists and accounting specialists work closely together to identify or create authoritative resources to help members resolve their work related information needs. Additionally, our accounting specialists can help CIMA members and students with the interpretation of guidance on financial reporting, financial management and performance management, as defined in the CIMA Official Terminology 2005 edition. CIMA members and students should sign into My CIMA to access these services and resources. The Chartered Institute of Management Accountants 26 Chapter Street London SW1P 4NP United Kingdom T. +44 (0)20 8849 2259 F. +44 (0)20 8849 2468 E. [email protected] www.cimaglobal.com 2 Topic Gateway Series Quality control Definition Definitions -
Statistical Process Control Tools: a Practical Guide for Jordanian Industrial Organizations
Volume 4, Number 6, December 2010 ISSN 1995-6665 JJMIE Pages 693 - 700 Jordan Journal of Mechanical and Industrial Engineering www.jjmie.hu.edu.jo Statistical Process Control Tools: A Practical guide for Jordanian Industrial Organizations Rami Hikmat Fouad*, Adnan Mukattash Department of Industrial Engineering, Hashemite University, Jordan. Abstract The general aim of this paper is to identify the key ingredients for successful quality management in any industrial organization. Moreover, to illustrate how is it important to realize the intergradations between Statistical Process Control (SPC) is seven tools (Pareto Diagram, Cause and Effect Diagram, Check Sheets, Process Flow Diagram, Scatter Diagram, Histogram and Control Charts), and how to effectively implement and to earn the full strength of these tools. A case study has been carried out to monitor real life data in a Jordanian manufacturing company that specialized in producing steel. Flow process chart was constructed, Check Sheets were designed, Pareto Diagram, scatter diagrams, Histograms was used. The vital few problems were identified; it was found that the steel tensile strength is the vital few problem and account for 72% of the total results of the problems. The principal aim of the project is to train quality team on how to held an effective Brainstorming session and exploit these data in cause and effect diagram construction. The major causes of nonconformities and root causes of the quality problems were specified, and possible remedies were proposed. © 2010 Jordan Journal of Mechanical and Industrial Engineering. All rights reserved Keywords: Statistical Process Control, Check sheets, Process Flow Diagram, Pareto Diagram, Histogram, Scatter Diagram, Control Charts, Brainstorming, and Cause and Effect Diagram. -
Modular Kaizen: Dealing with Disruptions Is a Publication of the Public Health Foundation, with a Limited First Printing in March 2011
Modular kaizen: Dealing with Disruptions is a publication of the Public Health Foundation, with a limited first printing in March 2011. Suggested Citation Bialek, R, Duffy, G, Moran, J. Modular kaizen: Dealing with Disruptions. Washington, DC: the Public Health Foundation; 2011. Additional Resources To find other Quality Improvement publications, please visit the Public Health Foundation bookstore at: http://bookstore.phf.org/ To explore free tools, resources and samples, please visit the Public Health Foundation website at: http://www.phf.org/Pages/default.aspx _______________________________________________________________________ Modular kaizen: Dealing with Disruptions Modular kaizen Table of Contents Acknowledgement ii Preface and Overview iii Chapter 1: The Value of Performance Management 1 Chapter 2: The House of Modular kaizen 13 Chapter 3: Implementing Performance Improvement through Modular kaizen 23 Chapter 4: A System View of the Disrupted Process 31 Chapter 5: Focus on the Disruption – Develop the Response Team 45 Chapter 6: Modular Flow for Rapid Cycle Improvement 55 Chapter 7: Tri-Metric Matrix 69 Chapter 8: Standardizing and Controlling the New System 77 Chapter 9: Change Management 91 Chapter 10: Daily Work Management: Using Quality Improvement Skills in Daily Work 101 Appendices Appendix A: Dr. W. Edwards Deming 111 Appendix B: Additional References 113 Appendix C: Templates and Examples 117 Appendix D: Author Biographies 133 Index 135 i _______________________________________________________________________ Modular kaizen: Dealing with Disruptions Acknowledgements After ten years of practicing and developing the concepts of Modular kaizen, the authors thank the Centers for Disease Control and Prevention (CDC) for making possible the publication of this book, supported by Cooperative Agreement Number 3U38HM000518. The contents of this book are solely the responsibility of the authors and do not necessarily represent the official views of CDC.