UART Flow Control
Total Page:16
File Type:pdf, Size:1020Kb
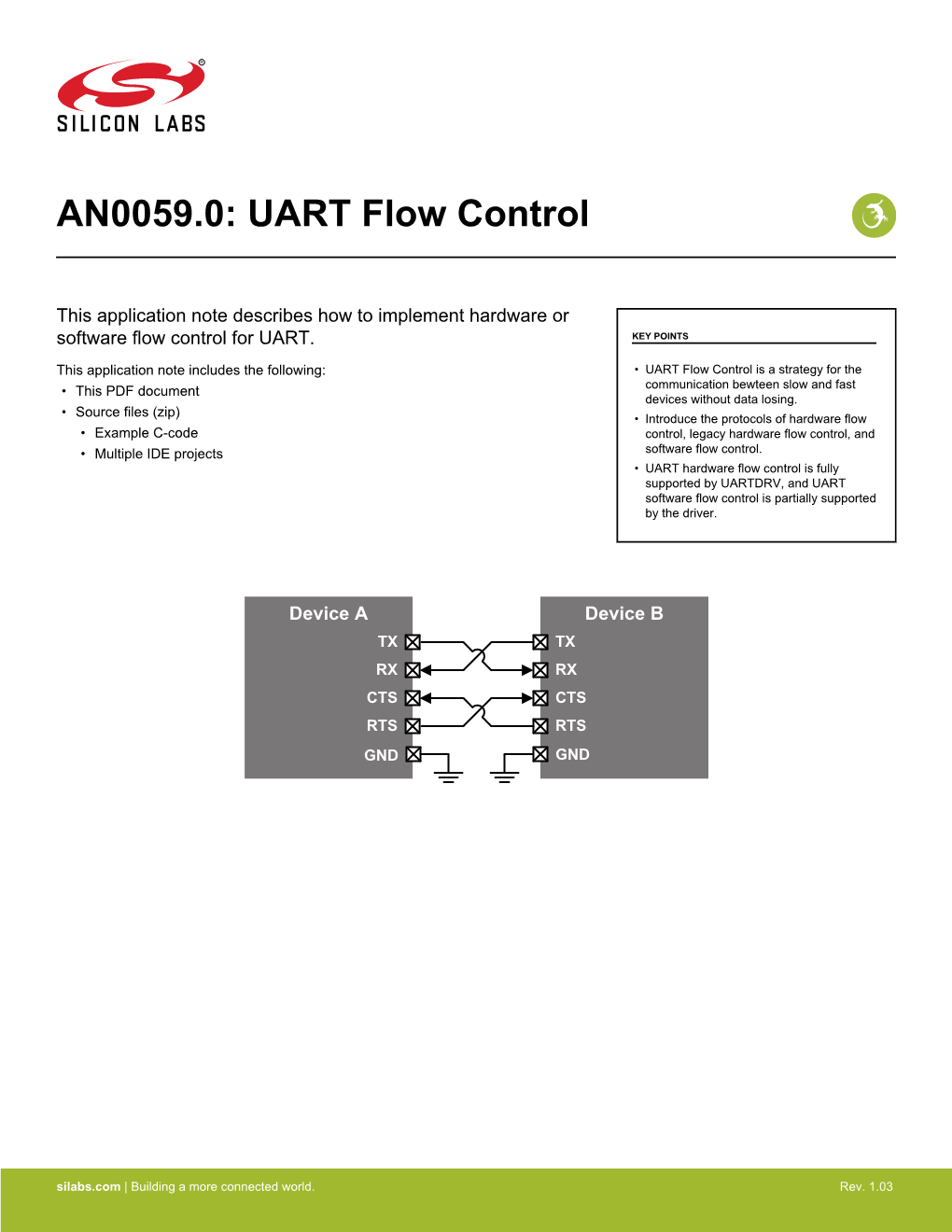
Load more
Recommended publications
-
AN706: EZSP-UART Host Interfacing Guide
AN706: EZSP-UART Host Interfacing Guide This application note describes how to connect a Host processor to a Network Co-Processor (NCP) using the UART-based Em- KEY POINTS berZNet Serial Protocol (EZSP). It assumes that you already • EZSP-UART protocol overview have a basic understanding of the EZSP-UART Gateway proto- • Physical interfaces col, as well as the signals needed by the UART interface. If not, • Command line options for Host refer to UG101: UART Gateway Protocol Reference Guide be- applications fore continuing. This application note has been updated to Em- • Hardware design considerations • Powering up, power cycling, and rebooting berZNet PRO 6.6 to reflect a minor update to the Silicon Labs • Bootloading Zigbee application framework, though the content of the EZSP- UART interface still applies to earlier versions of the EmberZNet PRO stack. silabs.com | Building a more connected world. Rev. 1.2 AN706: EZSP-UART Host Interfacing Guide Protocol Overview 1. Protocol Overview Silicon Labs designed EZSP as a protocol to allow communications between components running pieces of the EmberZNet PRO wire- less mesh stack, namely a Host processor and an NCP. The Host processor runs the application layer and executes on the POSIX platform such as Mac OS, Linux, or a Windows PC running Cygwin or the new Windows 10 BASH shell. You can also run this on an embedded platform like the Raspberry Pi. This lets you develop and test your application on an easy-to-use platform before porting your solution to a different Host processor with few changes. The NCP runs the EmberZNet PRO stack and physical layer (PHY). -
I-Modem Command Reference
U.S. Robotics I-modem Command Reference U.S. Robotics I-modem Command Reference page i U.S. Robotics I-modem Command Reference The material contained in this manual is for information purposes only and is subject to change without notice. No part of this document may be reproduced, transmitted, transcribed, or stored in a retrieval system in any form or by any means, mechanical, magnetic, electronic, optical, chemical, or otherwise without the written permission of U.S. Robotics. U.S. Robotics and the U.S. Robotics logo are registered trademarks of U.S. Robotics. Courier, V.Everything, and I-modem are tradmarks of U.S. Robotics. Microsoft and Win- dows NT are registered trademarks of Microsoft Corporation. V.Fast Class and V.FC are trademarks of Rockwell International. MNP is a registered trademark of Microcom Sys- tems, Inc. Any trademarks, trade names, service marks, or service names owned or registered by any other company and used in this manual are the property of their respective companies. U.S. Robotics assumes no responsibility for errors or omissions in this manual. Nor does U.S. Robotics make any commitment to update the information contained herein. ©1997 U.S. Robotics Corp. 8100 N. McCormick Blvd. Skokie, IL 60076-2999 USA page ii U.S. Robotics I-modem Command Reference Table of Contents Chapter 1 Using the AT Command Set 1-1 General Rules for Using AT Commands 1-1 Basic AT Commands 1-2 S-registers 1-3 Chapter 2 Modes of Operation 2-1 Command and Online Modes 2-1 Controlling Local Echo 2-3 Data and Fax Modes 2-5 Chapter 3 Dialing, Answering, and Hanging Up 3-1 Making International Calls 3-7 Call Detection 3-9 page iii U.S. -
RS-232 Full Modem Interface (8-Wire) Module for Protection Relay, IED, and Substation Automation Reference Design
TI Designs RS-232 Full Modem Interface (8-Wire) Module for Protection Relay, IED, and Substation Automation Reference Design TI Designs Design Features The worldwide electric-power infrastructure is a set of • Can be Configured as DTE or DCE Interface interconnected assets for power generation, • Galvanic Isolation Using Digital Isolators With transmission, conversion, and distribution commonly Modular Options of 2-, 4-, or 8-Wire Interface referred to as "the grid". Protection relays and IEDs (DTE) used in the grid measures a number of electrical • Operates With Single 5.6-V Input parameters. These parameters are collected by • 9-Pin D-Sub Connectors Provided for Easy automation systems for analysis. Data from the IEDs Interface to External DTE or DCE can be collected locally or remotely. For remote • Isolated Power Supply Generated Using SN6501 communication, modems (DCE) are used, which can Transformer Driver be dial-up, GSM, or radio modems. Modems are interfaced to IEDs using an RS-232 interface. The RS- • Tested for the Following Data Rates: 1200, 2400, 232 interface includes data, control, and status 4800, 9600, 19200, and 115000 bps signals. Control and status signals can be hardware or • Tested for ESD ±8-kV Contact Discharge software based. To maintain the data integrity in a • Tested for Surge ±1-kV Common Mode noisy grid environment, galvanic isolation is provided between IEDs and modems. This TI design Featured Applications demonstrates the hardware flow control method for DTE or DCE. This TI design also demonstrates • DTE -
MT5634HD8/16 User Guide MT5634HD8/16 User Guide P/N 82074700, Revision a Copyright © 1997 by Multi-Tech Systems, Inc
MT5634HD8/16 User Guide MT5634HD8/16 User Guide P/N 82074700, Revision A Copyright © 1997 by Multi-Tech Systems, Inc. All rights reserved. This publication may not be reproduced, in whole or in part, without prior expressed written permission from Multi-Tech Systems, Inc. Multi-Tech Systems, Inc. makes no representation or warranties with respect to the contents hereof and specifically disclaims any implied warranties of merchantability or fitness for any particular purpose. Furthermore, Multi-Tech Systems, Inc. reserves the right to revise this publication and to make changes from time to time in the content hereof without obligation of Multi-Tech Systems, Inc., to notify any person or organization of such revisions or changes. Revision Date Description A 11/15/97 Manual released. Multi-Tech, CommPlete, RASExpress, MultiExpress, MultiExpress Fax MultiModem, MultiModemZDX, MultiCommManager, and the Multi-Tech logo are trademarks of Multi-Tech Systems, Inc. Other trademarks and trade names mentioned in this publication belong to their respective owners. Multi-Tech Systems, Inc. 2205 Woodale Drive Mounds View, Minnesota 55112 (612) 785-3500 or (800) 328-9717 U.S. Fax (612) 785-9874 Technical Support (800) 972-2439 BBS (612) 785-3702 or (800) 392-2432 Fax Back (612) 717-5888 Internet Address: http://www.multitech.com Federal Communications Commission Statement This equipment has been tested and found to comply with the limits for a Class A digital device, pursuant to Part 15 of the FCC Rules. These limits are designed to provide reasonable protection against harmful interference when the equipment is operated in a commercial environment. This equipment generates, uses, and can radiate radio frequency energy, and if not installed and used in accordance with the instruction manual, may cause harmful interference to radio communications. -
Series II Modem 336 Series II Modem 336+
AUGUST 2000 MD1640A MD1641A Series II Modem 336 Series II Modem 336+ CUSTOMER Order toll-free in the U.S.: Call 7877-877-BBOX (outside the U.S. call 724-746-5500) SUPPORT FREE technical support 24 hours a day, 7 days a week: Call 724-746-5500 or fax 724-746-0746 INFORMATION Mailing address: Black Box Corporation, 1000 Park Drive, Lawrence, PA 15055-1018 Web site: www.blackbox.com • Email: [email protected] Series II Modems 336 and 336+ Series II Intelligent Data/Fax Modems Model 336 (Product Code MD1641A) Model 336+ (Product Code MD1640A) User Guide SERIES II INTELLIGENT DATA/FAX MODEMS DISCLAIMER This publication may not be reproduced, in whole or in part, without prior expressed written permission from the manufacturer. The manufacturer makes no representations or warranties with respect to the contents hereof and specifically disclaims any implied warranties of merchantability or fitness for any particular purpose. The manufacturer reserves the right to revise this publication and to make changes from time to time in the content hereof without obligation of the manufacturer to notify any person or organization of such revisions or changes. TRADEMARKS USED IN THIS MANUAL MNP and Microcom Network Protocol are trademarks of Microcom Inc. AS/400 and System3x are registered trademarks of IBM. Appletalk, Mac, and Macintosh are registered trademarks of Apple Computer Inc. Unix is a registered trademark of X/Open Co. Ltd. Microsoft and Windows are registered trademarks of Microsoft Corporation. All other trademarks mentioned in this manual -
D: Serial Driver
CHAPTER 7 Serial Driver 7 This chapter describes how you can use the Serial Driver to transfer data to a device connected to a Macintosh modem or printer port. The Serial Driver supports 7 asynchronous serial data communication between applications and serial devices Serial Driver through these ports. The Serial Driver provides low-level support for communicating with serial devices that cannot be accessed through the Communications Toolbox or Printing Manager. For example, a scientific instrument or a printer that does not support QuickDraw. Before you decide to use the Serial Driver, you should determine whether it is the appropriate solution for your communication needs. The Communications Toolbox is the recommended method for integrating modems and other telecommunications devices into the Macintosh environment. The Communications Toolbox provides hardware-independent services and a standard interface that offers compatibility with all Macintosh models. To find out more about the Communications Toolbox, see Inside the Macintosh Communications Toolbox. Likewise, the Printing Manager is the recommended interface for printers and similar output devices. Using the Printing Manager makes your hardware or software product compatible with every other device or application that supports this standard interface. Refer to Inside Macintosh: Imaging With QuickDraw for more information. To use the Serial Driver, you should understand how to open, close, and communicate with device drivers using the Device Manager. You can find this information in -
Serial-HOWTO.Pdf
Serial HOWTO Serial HOWTO Table of Contents Serial HOWTO...................................................................................................................................................1 David S.Lawyer [email protected] original by Greg Hankins.....................................................................1 1. Introduction..........................................................................................................................................1 2. Quick Help...........................................................................................................................................1 3. How the Hardware Transfers Bytes.....................................................................................................1 4. Serial Port Basics.................................................................................................................................1 5. Multiport Serial Boards/Cards/Adapters..............................................................................................2 6. Servers for Serial Ports........................................................................................................................2 7. Configuring Overview.........................................................................................................................2 8. Locating the Serial Port: IO address, IRQs..........................................................................................2 9. Configuring the Serial Driver (high-level) "stty"................................................................................2 -
TELEBIT® When Connectivity Counts
Modem Reference Manual for the Telebit T3000 and WorldBlazer Family of Products 90238-01 ., ' '1IJ TELEBIT® When connectivity counts. Modem Reference Manual for the Telebit T3000 and WorldBlazer Family of Products 90238-01 How to Use This Manual About This Manual This manual is a reference guide for using any of the Telebit T3000 and WorldBlazer modems. It is designed for both new and experienced modem users. To help you install and configure the modem, refer to the User's Guide for your particular modem. It is a separate booklet provided with your modem. If you have special requirements or experience any problems while using. your User's Guide, refer to this manual for additional information. Note: Read your User's Guide before reading this reference manual. Whether you are a first-time or experienced user, install your modem using the instructions in your User's Guide. This manual contains six chapters and four appendices: • Chapter 1, Introduction, describes the main features of the modem. • Chapter 2, Modem Operation and Special Features, describes command mode operations, flow control, RS-232 control signal interpretations, error control, data compression, protocol support, and synchronous support. • Chapter 3, AT Command Descriptions, describes the commands and explains the possible parameters, the range of parameters, and the default settings. 90238-01 How to Use This Manual • Chapter 4, S Register Descriptions, describes the registers used to operate the modem and explains the possible parameters, the range of parameters, and the default settings. • Chapter 5, Troubleshooting, describes the diagnostic tests performed by the modem after it is powered up. -
Modicon Modbus ASCII Serial Driver Guide
Advantech WebAccess Device Driver Guide Modicon Modbus ASCII Serial Modbus ASCII Serial / Modicon Serial Device Driver Guide Version 7.0 rev 0 Advantech Corp., Ltd. page 1-1 Advantech WebAccess Device Driver Guide Modicon Modbus ASCII Serial Table of Contents Modbus ASCII Serial / Modicon Serial Device Driver Guide 1-1 1. Modbus ASCII Serial Device Communications 2 1.1 Introduction to Modbus ASCII Serial .................................................. 2 1.1.1 Modbus ASCII Serial: RS-232, RS-422 and RS485 ............. 2 1.1.2 Wiring and Cabling Requirements ......................................... 3 1.1.3 Ease of Use: Parameters ...................................................... 4 1.1.4 Redundant Comports ............................................................ 5 1.1.5 Modbus Protocols .................................................................. 5 1.1.5.1 Modbus ASCII ...................................................................... 5 1.1.5.2 Modbus RTU ........................................................................ 5 1.1.5.3 Modbus Ethernet / TCP/IP ................................................... 5 1.2 Configure Modicon / Modbus device ................................................. 6 1.3 Serial Comport Properties .................................................................. 7 1.3.1 Comport Number ................................................................... 7 1.3.2 Description ............................................................................. 7 1.3.3 Baud Rate ............................................................................. -
Modicon Modbus Serial Driver Guide
Advantech WebAccess Device Driver Guide Modicon Modbus Serial Modbus RTU Serial / Modicon Serial Device Driver Guide Version 7.0 rev 3 Advantech Corp., Ltd. page 1-1 Advantech WebAccess Device Driver Guide Modicon Modbus Serial Table of Contents Modbus RTU Serial / Modicon Serial Device Driver Guide 1-1 1. Modbus RTU Serial Device Communications 2 1.1 Introduction to Modbus RTU Serial .................................................... 2 1.1.1 Modbus Serial: RS-232, RS-422 and RS485 ........................ 2 1.1.2 Wiring and Cabling Requirements ......................................... 3 1.1.3 Ease of Use: Parameters ...................................................... 4 1.1.4 Redundant Comports ............................................................ 5 1.1.5 Modbus Protocols .................................................................. 5 1.1.5.1 Modbus RTU ........................................................................ 5 1.1.5.2 Modbus ASCII ...................................................................... 5 1.1.5.3 Modbus Ethernet / TCP/IP ................................................... 5 1.2 Configure Modicon / Modbus device ................................................. 6 1.3 Serial Comport Properties .................................................................. 7 1.3.1 Comport Number ................................................................... 7 1.3.2 Description ............................................................................. 7 1.3.3 Baud Rate ............................................................................. -
Serial Ports
Lecture #11 Serial Ports 18-348 Embedded System Engineering Philip Koopman Wednesday, 17-February-2016 Electrical& Computer ENGINEERING © Copyright 2006-2016, Philip Koopman, All Rights Reserved High Tech Hospital Beds Typical features: • Move from flat bed to sitting for meals • In-bed scale • Massage capability for bed sores • Inflatable bladder for bed sores • Power+network for equipment attached to bed [http://www.bedtechs.com/pdf/H.R.TotalCare.pdf] • Battery backup for patient transport with equipment attached Technology inside the bed: • Serial data transmission • Controller Area Network (CAN) via a 16-bit microcontroller • Link from bed to nurse station (wired; wireless) 2 Where Are We Now? Where we’ve been: • Memory bus (back to hardware for a lecture) • Economics / general optimization Where we’re going today: • Serial ports Where we’re going next: • Exam #1 Wed 24-Feb-2016 – See course web page for material included – Bring a single two-sided letter size notes sheet in your own handwriting – NO calculators – We will provide the HC12 reference guide at the test (the “short version” of instruction descriptions, XB encoding table, etc.) » All 32 pages -- please do not mark on it since we re-use from year to year • Second half of course: timers, interrupts, real time operation, I/O, … 3 Preview Sending digital data • How bits go on a wire • RS-232 serial communications Getting serial devices to talk • RS-232 signal and control lines • SCI control and data registers • Some other serial protocols (RS-485, I2C, SPI, USB) Error -
The `Linux Serial Port Programming Mini-HOWTO' Is Posted Automatically by the *** Linux HOWTO Coordinator, Greg Hankins <[email protected]>
*** The `Linux Serial Port Programming mini-HOWTO' is posted automatically by the *** Linux HOWTO coordinator, Greg Hankins <[email protected]>. Please *** direct any comments or questions about this HOWTO to the author, *** Antonino Iannella <[email protected]>. - --- BEGIN Linux Serial Port Programming mini-HOWTO part 1/1 --- Linux Serial Port Programming Mini-Howto Antonino Iannella, [email protected] Version 1.0, March 9th 1997 1. Introduction This document describes how to program the RS-232 ports for serial communications, under PC-Linux. It covers information about the serial ports, RS232 connections, modem issues, and the C programming logic. 2. Background For our final year project, our group had to design a concept World Wide Web browser. Our prototype was a hand-held device which plugged into a PC's COM2 (25-pin) serial port. The user would issue commands to the browser (eg Back, Open, etc) by sending character commands to the PC. The browser software would detect it, and perform the required operation. The method provided in the 'Linux I/O port programming mini-HOWTO' did not act reliably. Often, an incorrect value would be received. The information within provided a 100% reliable, quasi-POSIX-compliant approach to communication. The program provided at the end of this 0 formed the basis of the PC's communication program. This document is written from the 1 needed for the web browser project. It revolves around C programming for Linux, for a 9600 baud device attached to COM2. 3. Acknowledgements The information here comes mainly from these sources - Heavily based on the 'Serial Programming Guide for POSIX Compliant Operating Systems', at http://www.easysw.com/~mike/serial/, by [email protected].