Combustion Valve Wear
Total Page:16
File Type:pdf, Size:1020Kb
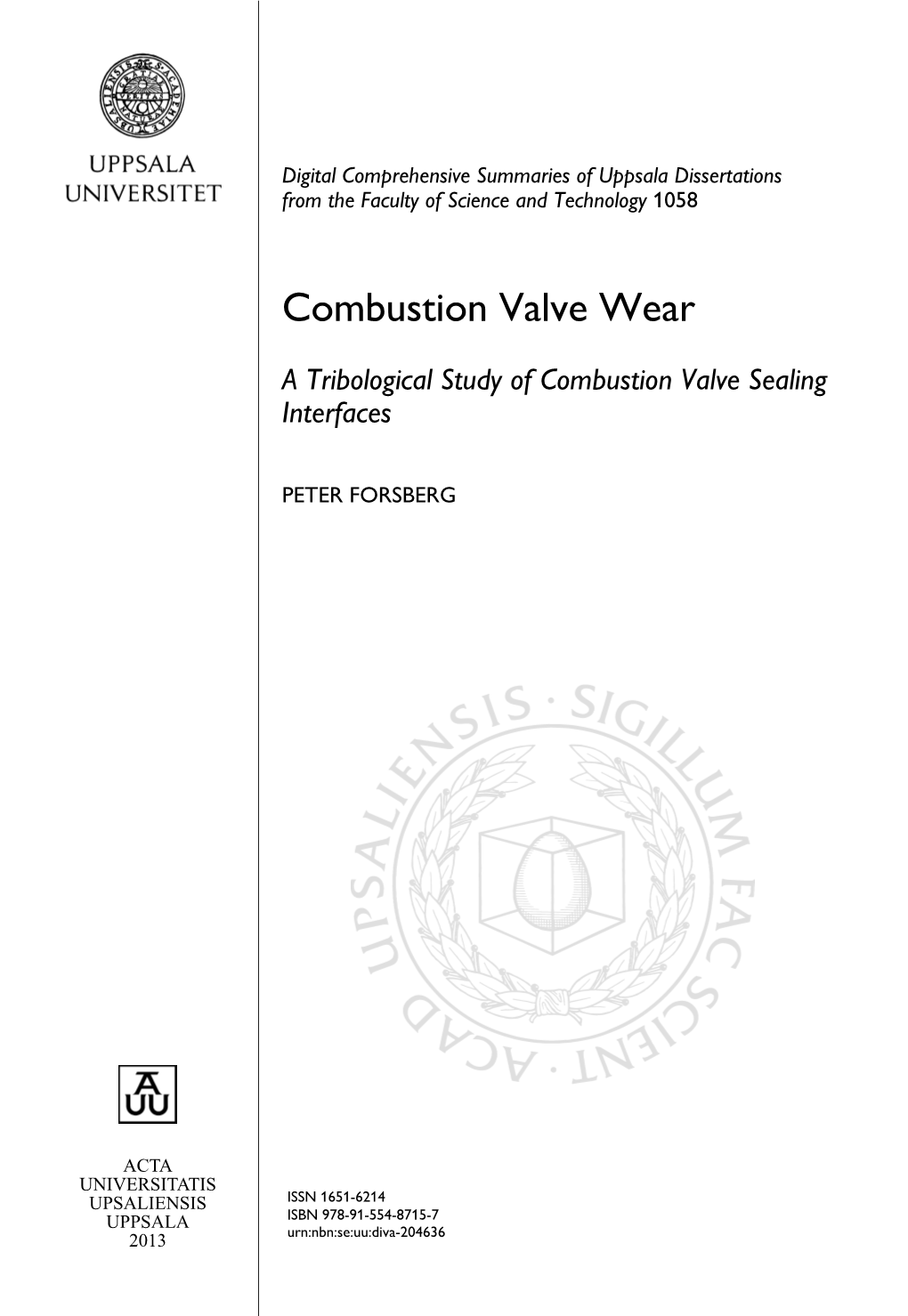
Load more
Recommended publications
-
A Wear Model for Diesel Engine Exhaust Valves
ORNL/TM-2009/259 A WEAR MODEL FOR DIESEL ENGINE EXHAUST VALVES November 24, 2009 Peter J. Blau Materials Science and Technology Division Oak Ridge National Laboratory DOCUMENT AVAILABILITY Reports produced after January 1, 1996, are generally available free via the U.S. Department of Energy (DOE) Information Bridge. Web site http://www.osti.gov/bridge Reports produced before January 1, 1996, may be purchased by members of the public from the following source. National Technical Information Service 5285 Port Royal Road Springfield, VA 22161 Telephone 703-605-6000 (1-800-553-6847) TDD 703-487-4639 Fax 703-605-6900 E-mail [email protected] Web site http://www.ntis.gov/support/ordernowabout.htm Reports are available to DOE employees, DOE contractors, Energy Technology Data Exchange (ETDE) representatives, and International Nuclear Information System (INIS) representatives from the following source. Office of Scientific and Technical Information P.O. Box 62 Oak Ridge, TN 37831 Telephone 865-576-8401 Fax 865-576-5728 E-mail [email protected] Web site http://www.osti.gov/contact.html This report was prepared as an account of work sponsored by an agency of the United States Government. Neither the United States Government nor any agency thereof, nor any of their employees, makes any warranty, express or implied, or assumes any legal liability or responsibility for the accuracy, completeness, or usefulness of any information, apparatus, product, or process disclosed, or represents that its use would not infringe privately owned rights. Reference herein to any specific commercial product, process, or service by trade name, trademark, manufacturer, or otherwise, does not necessarily constitute or imply its endorsement, recommendation, or favoring by the United States Government or any agency thereof. -
Group 3K – Saloon Cars
2021 MOTORSPORT AUSTRALIA MANUAL SPECIFICATIONS OF AUTOMOBILES motorsport.org.au 3rd Category – Touring Cars Group 3K – Saloon Cars Modified Article Date of Application Date of Publication 8.9 Front Brakes 01/01/2021 01/01/2021 Appendix C Dorian Transmitter location - removed 01/01/2021 01/01/2021 Appendix F Drivers Seat Mount - Removed 01/01/2021 01/01/2021 1. GENERAL 1.1 These regulations are based on Holden Commodore V6-3.8 litre sedans and Ford Falcon six cylinder 3.9 and 4.0 litre sedans marketed and manufactured in Australia by General Motors Holden and the Ford Motor Company respectively, and restricted in specification to those listed herein. The vehicles are to be representative of mass-produced family sedans with limited modifications permitted. The intention of these regulations is to use large scale production-based vehicles with limited modifications designed to make the cars more suitable for competition use, therefore producing a relatively affordable entry to motor sport. It is intended that the vehicles shall have even performance and thus emphasise driver ability over vehicle tuning and preparation. 1.2 All vehicle parts and specifications are to remain consistent with the nominated model as supplied by the vehicle manufacturer or authorised supplier at any one time, except as otherwise permitted or specified in these regulations. Each modification or alteration must be undertaken with application of automotive engineering standards. 1.3 Any aspect relating to the construction and/or modification of the vehicle which is not expressly permitted in these regulations is forbidden. Modifications permitted are allowed only on the condition that the weights, specifications and/or dimensions as documented in the relevant Appendices of these regulations and relevant Motorsport Australia Vehicle Homologation Documents are adhered to. -
Introduction to Engine Valvetrains List of Chapters
Introduction to Engine Valvetrains List of Chapters Chapter 1 Introduction and 2.3.5 Variable Valve Chapter 3 Valvetrain Components Overview of Engines Actuation by Cam 3.1 Overview 1.1 Engine Fundamentals Phasing and Variable 3.2 Valves 1.1.1 Definition of an Engine Lift 3.2.1 Valve Nomenclature 1.1.2 Types of Internal 2.3.6 Variable Valve and Construction Combustion Engines Actuation by Varying 3.2.2 Valve Operating 1.1.3 Typical Internal the Rocker Ratio Characteristics Combustion Engine 2.4 Variable Valve Actuation— 3.2.3 Valve Design Structure Camless System 3.2.4 Valve Materials 1.2 Principles of the Four-Stroke 2.4.1 Electromagnetic Valve 3.3 Cams Combustion Cycle Actuation 3.3.1 Cam Nomenclature and 1.2.1 Spark Ignition Engines 2.4.2 Electrohydraulic Valve Design Considerations 1.2.2 Compression Ignition Actuation 3.3.2 Cam Profile Engines 2.4.3 Comparison of Characteristics 1.3 Two-Stroke Engines Various Variable Valve 3.3.3 Cam Profile Design 1.4 Engine Displacement and Actuation Systems 3.3.4 Considerations in Cam Compression Ratio 2.5 Engine Brake and Valvetrains Profile Determination 1.5 Engine Performance 2.6 Types of Valvetrain 3.3.5 Lightweight Cam Design 1.5.1 Torque 2.6.1 Type I Valvetrain— 3.3.6 Cam Lobe Surface 1.5.2 Horsepower Direct Acting, Finishes and Tolerances 1.6 Internal Combustion Engine Overhead Cam 3.3.7 Cam Materials Efficiency 2.6.2 Type II Valvetrain—End- 3.4 Valvetrain Lash Compensators 1.6.1 Mechanical Efficiency Pivot Rocker Arm, 3.4.1 Lash and Mechanical 1.6.2 Thermal Efficiency Overhead Cam Lash Adjusters -
Engine Reconditioning Consumables Tools Workshop Supplies
Engine Reconditioning Consumables Tools Workshop Supplies JUNE 2017 Phone 1300 662 766 Fax 1300 762 766 Introducing to our Range Timing Tool Kits INDEX DESCRIPTION PAGE DESCRIPTION PAGE AA GASKETS 36 ENGINE TOOLS 14,15 ACCESSORY BOLTS 37 FASTENER ASSEMBLY LUBE 45 ACL RACE BEARINGS 3 FLAP WHEELS 11 APRONS 12,13 FLEX HONES 25,26 ASSEMBLY GREASE 46 FLEXIGAUGE 3 ASSEMBLY LUBE 45 FLYWHEEL GRINDING COOLANT 16 BASKETS PARTS HOT TANK 13 FORD FUEL PUMP ECCENTRIC KIT 16 BEADS GLASS 12 GASKET MATERIAL 32 TO 36 BLOCK FLEX HONE 26 GATES STRETCH BELT TOOLS 21 BRASS TAGS 36 GLASS BEAD GLOVES 12 BRONZE GUIDE LINERS 19 GLASS BEADS 12 BRUSHES 8,9,10 GLOVES HOT TANK 13 BUCKET SHIMS 37 HEAD CHECK TEE JAY 37 CARBON REMOVAL BRUSH 8 HEAT TAB ADHESIVE 37 CARTRIDGE ROLLS 11 HEAT TABS 37 CLEANING PRODUCTS 12,13 HONE STONES 5,6,7 COMBUSTION LEAK DETECTION 37 HONES FLEX 25,26 CON ROD BOLT SLEEVES 37 HONING OIL 5,26 CRANKSHAFT POLISHING BELTS 7 HOT TANK BASKETS 13 CYLINDER HONES 7 HOT TANK GLOVES 13 CYLINDER HEAD DOWELS 18 HOT TANK PARTS TAGS 36 CYLINDER HEAD HOLDER 14 HYLOMAR PRODUCTS 17 CYLINDER RIDGE REMOVER 14 MAGNECTIC POWDER 16 CYLINDER WASHING BRUSH 9 METALLIC SEAL UP (1008) 22 DRIVEN PRODUCTS 45,46,47 MOLY LUBE 45 DOWEL PULLER 14 OIL GALLERY BRUSHES 9 ENGINE BOLTS 37 OPTI BELT STRECH BELT TOOLS 22 ENGINE CLEANING BRUSHES 9,10 ORGINAL RADIATOR LEAK STOPPER 22 ENGINE ENAMELS 30 PAINT 27 TO 29 ENGINE OIL ADDITIVES 45 PAPER TAGS HOT TANK 36 ENGINE SLEEVES 38,39,40 PARTS CLEANING BRUSHES 10 1 INDEX DESCRIPTION PAGE DESCRIPTION PAGE PASTE VALVE GRINDING 15 VALVE -
CAM TERMINOLOGY ABDC: After Bottom Dead Center
The following information is provided to help you understand some of the terminology related to camshaft specifications, and information. 1. Max Lift or Nose 2. Flank 3. Opening Clearance Ramp 4. Closing Clearance Ramp 5. Base Circle 6. Exhaust Opening Timing Figure 7. Exhaust Closing Timing Figure 8. Intake Opening Timing Figure 9. Intake Closing Timing Figure 10. Lobe Separation CAM TERMINOLOGY ABDC: After Bottom Dead Center. Measured in degrees. ASYMMETRICAL: Not identical on both sides of the lobe. In most cases, the opening side of the lobe being much more aggressive than the closing side. This difference is only visible in some overhead cams. ATDC: After Top Dead Center. Measured in degrees. BASE CIRCLE: The concentric or round portion of the cam lobe where the valve lash adjustments are made. A high spot in this area is called BASE CIRCLE RUNOUT. BBDC: Before Bottom Dead Center. Measured in degrees. BILLETS: The blank shafts that the camshafts are made from. BTDC: Before Top Dead Center. Measured in degrees. CAM FOLLOWER / TAPPET: Usually a flat faced or roller companion to the camshaft that transfers the action of the camshaft to the rest of the valve train by sliding or rolling on the cam lobe. CAM LIFT: This is the maximum distance that the cam pushes the follower when the valve is open. This is different from valve lift. See Gross Valve Lift. CAM LOBE: The parts of the camshaft that create the valve movement. CAM MASTER: Design of the cam transferred to a template or master. The master is then installed in the cam grinding machine to generate the shape of the lobes of the production cam. -
Protective Tribofilms on Combustion Engine Valves
Digital Comprehensive Summaries of Uppsala Dissertations from the Faculty of Science and Technology 1635 Protective Tribofilms on Combustion Engine Valves ROBIN ELO ACTA UNIVERSITATIS UPSALIENSIS ISSN 1651-6214 ISBN 978-91-513-0243-0 UPPSALA urn:nbn:se:uu:diva-342549 2018 Dissertation presented at Uppsala University to be publicly examined in Polhemsalen, Lägerhyddsvägen 1, Uppsala, Friday, 13 April 2018 at 13:15 for the degree of Doctor of Philosophy. The examination will be conducted in English. Faculty examiner: Dr Mikael Åstrand (Infranord AB). Abstract Elo, R. 2018. Protective Tribofilms on Combustion Engine Valves. Digital Comprehensive Summaries of Uppsala Dissertations from the Faculty of Science and Technology 1635. 83 pp. Uppsala: Acta Universitatis Upsaliensis. ISBN 978-91-513-0243-0. Inside the complex machinery of modern heavy-duty engines, the sealing surfaces of the valve and valve seat insert have to endure. Right next to the combustion, temperatures are high and high pressure deforms the components, causing a small relative motion in the interface. The wear rate of the surfaces has to be extremely low; in total every valve opens and closes up to a billion times. The minimal wear rate is achieved thanks to the formation of protective tribofilms on the surfaces, originating from oil residues that reach the surfaces - even though these are not intentionally lubricated. The increasing demands on service life, fuel efficiency and clean combustion, lead to changes that may harm the formation of tribofilms, which would lead to dramatically reduced service lives of the valves. This calls for an improved understanding of the formation of tribofilms and how their protective effects can be promoted. -
OPTIMIZATION of VALVETRAIN MECHANISM for THREE CYLINDER TURBOCHARGED INTERCOOLED GASOLINE ENGINE Mr
[Nikate* et al., 5(7): July, 2016] ISSN: 2277-9655 IC™ Value: 3.00 Impact Factor: 4.116 IJESRT INTERNATIONAL JOURNAL OF ENGINEERING SCIENCES & RESEARCH TECHNOLOGY OPTIMIZATION OF VALVETRAIN MECHANISM FOR THREE CYLINDER TURBOCHARGED INTERCOOLED GASOLINE ENGINE Mr. Chetan Nikate*, Prof. Dattatray Kotkar, Mr. Hemant Malekar, Prof. Ketan Dhumal * P.G. Student, M.E. Machine Design Engineering, IV Semester, Mechanical Engineering Department, Dhole Patil college of Engineering Wagholi, Pune, India. Department of Mechanical Engineering, Dhole Patil College Of Engineering, Wagholi, Pune, India. DGM, Engineering Research Centre (Engines), TATA Motors LTD.,Pune, India. Professor, Department of Mechanical Engineering, Dhole Patil College Of Engineering, Wagholi, Pune, India DOI: ABSTRACT Present work descries the effect of in-cylinder pressure in turbocharged gasoline engine, on valvetrain analysis. Consideration of cylinder pressure gives corrected stresses and also it gives scope for reduction in moving masses in valvetrain. Reduction in moving mass and valve spring stiffness has significant impact in valvetrain kinematics & dynamics. These parameters are analysed in detail in this work. Initially, kinematic and dynamic analysis on the benchmark three cylinder naturally aspirated engine valve train is performed. The impacts of in cylinder pressure (P-Ɵ) on kinematic parameters are analysed. The boundary conditions are modified suitable to TCIC engine and the impact on valvetrain kinematic parameters such as valve lift, velocity, acceleration, contact stress between cam and follower at idle speed and high speed, inertia and spring force safety factor, dynamic valve lift and valve bouncing are analysed & tabulated. These analyses revealed that there is the scope to reduce the contact stresses by 5% at least. -
Engine Valve Designs by Ted Tunnecliffe
Engine Valve Designs By Ted Tunnecliffe Over the years, valve heads have come in all sizes and shapes. There has been everything from domed heads to flat heads to cupped heads. There have been many contours including different angles and radii on these domes and the same on the cups. Presumably, they all made sense to the designer at the time. In my experience, the main justification for dome shapes was to resist the combustion pressure by stopping the head from deflecting as much. On the contrary, the cupped head designs took advantage of that combustion pressure to assist in the sealing of the valve at the seat face. At one time, they were called "flexible head valves." They were designed with the head and cup angles diverging from one another at a rate of from 3° to 6° as you went from the O.D. toward the center of the head. Based on work done at Eaton many years ago, that gave a reasonably constant stress across the valve head which could then be designed to be whatever the maximum stress was already. So, effectively you had a design that was lower in weight but had no greater stress than the original design. That was a major point in the high performance days of the ‘60s. Also, if you had a tendency for a non-cupped design to leak and possibly burn at the seat face, you could try a cupped head shape. If you had a cracking problem in the underhead area, you might try a domed head. -
Camshafts, Valve Trains, Intake and Exhaust Systems
9 Camshafts, Valve Trains, Intake and Exhaust Systems Cam lobe shape has more control over engine per- OBJECTIVES: After studying Chapter 9, you should formance characteristics than does any other single be able to: engine part. Engines identical in every way except cam lobe shape may have completely different oper- 1. Prepare for the interprovincial Red Seal certification ating characteristics and performance. See Figure examination in Appendix I (Engine Repair) on the 9–1. The camshaft may also operate the following: topics covered in this chapter. 2. Describe how camshafts and valve trains function. ■ Mechanical fuel pump 3. Discuss valve train noise and its causes. ■ Oil pump 4. Explain how a hydraulic lifter works. ■ Distributor 5. Discuss the operation of variable-length intake manifolds. See Figures 9–2 and 9–3. 6. Explain the differences between air cleaners for “wet” and “dry” manifolds. 7. Explain the relationship of valve timing to intake CAMSHAFT LOCATION runner length. Pushrod engines have the cam located in the block.The camshaft is supported in the block by camshaft bear- ings and driven by the crankshaft with a gear or The cam is driven by timing gears, chains, or belts lo- sprocket and chain drive. See Figure 9–4. Many over- cated at the front of the engine. The gear or sprocket on the camshaft has twice as many teeth, or notches, as the CAMSHAFT one on the crankshaft. This results in two crankshaft rev- BEARING olutions for each revolution of the camshaft. The JOURNAL camshaft turns at one-half the crankshaft speed in all four- stroke-cycle engines. -
Modeling and Verification of Valve Train Dynamics in Engines
Modeling and Verification of Valve Train Dynamics in Engines by M Husselman Thesis presented at the University of Stellenbosch in partial fulfilment of the requirements for the degree of Master of Science in Mechanical Engineering Department of Mechanical Engineering Stellenbosch University Private Bag X1, 7602 Matieland, South Africa Study leader: Mr. K. van der Westhuizen Dr. A.B. Taylor December 2005 Copyright © 2005 University of Stellenbosch All rights reserved. Declaration I, the undersigned, hereby declare that the work contained in this thesis is my own original work and that I have not previously in its entirety or in part submitted it at any university for a degree. Signature: . M. Husselman Date: . ii Abstract Modeling and Verification of Valve Train Dynamics in Engines M. Husselman Department of Mechanical Engineering Stellenbosch University Private Bag X1, 7602 Matieland, South Africa Thesis: MScEng (Mech) December 2005 This study involved the modeling and verification of the finger follower valve train arrangement with the focus on the non-linear behaviour of high speed valve springs. The project was divided into three phases namely; the measuring of valve train dy- namics, modeling of the valve train and the verification of the dynamic models by com- paring the results from the two aforementioned two phases. Acceleration and force were measured on a running engine. A force transducer was specially developed for this purpose. Digital signal processing was used in the analysis and implementation of all measured data. The spring model was developed systematically from a solid model, into a finite ele- ment model, and finally into a dynamic model. -
High Performance Valve Seat Materials for CNG Powered Combustion Engines
materials Article High Performance Valve Seat Materials for CNG Powered Combustion Engines Andrzej Roma ´nski 1,* and Elzbieta˙ Cygan-B ˛aczek 2 1 Faculty of Metals Engineering and Industrial Computer Science, AGH University of Science and Technology, 30 Mickiewicz Avenue, 30-059 Krakow, Poland 2 Center of Advanced Manufacturing Technology, Łukasiewicz Research Network—Krakow Institute of Technology, Zakopia´nska73 Str., 30-418 Krakow, Poland; [email protected] * Correspondence: [email protected] Abstract: The conventional copper infiltrated high speed steel (HSS) valve seats used in gasoline engines are not suitable for CNG combustion because the exhaust gas temperature is at least 80 ◦C higher, which drastically shortens the service life of the engine valves. Therefore, a proprietary high- alloy HSS-base material was designed to combat hot corrosion and mechanical wear of valve seat faces in CNG fuelled engines. A batch of −100 mesh water atomized HSS powder was commissioned. The powder was vacuum annealed in order to reduce oxygen content and increase its compressibility. To improve the final part machinability, 1.2% MnS was admixed to the HSS powder prior to compaction. The green compacts were sintered at 1135 ◦C in nitrogen to around 83% TD and subsequently infiltrated with a copper alloy. After installing the valve seat components on a cylinder head, the engine was tested for 100 h according to the automotive industry valve seat wear test procedures. Both the periodic 8-h checks as well as the final examination of the valve seats showed very slow Citation: Roma´nski,A.; wear, indicating their suitability for CNG powered engines. -
Valve and Valve Seat
Valve train control the gas flowing into and out of the engine cylinder. The camshaft and valve spring make up the mechanism that lifts and closes the valves. The valve train determines the performance characteristics of four stroke- cycle engines. Figure 4.7: Cylinder head with the valve train The valve train consists mainly of valves, valve springs and camshafts. At low camshaft revolutions, the valve spring can follow the valve lift easily so that the valve moves regularly. At high revolutions, it is more difficult for the valve and valve spring to follow the cam. Valve float is the term given to unwanted movements of the valve and valve spring due to their inertial weights. To avoid this, the load of the valve spring should be set high. The load applied at the longest length is called the set load, and the valve spring is always set to have a high compressive stress above set load conditions. Valve Type There are two types of valve: Inlet valves Figure 4.1: Exhaust valve. Exhaust valves Note: The commonly used poppet valve is mushroom-shaped. Figure 4.2: Nomenclatures of the valves Note: A cotter which fixes the valve spring retainer to the valve, is inserted into the cotter groove. Figure 4.3: Rough sketch of a valve train showing valve lift distance in the valve timing diagram. The lift distance (vertical arrow) given by the cam lobe is the displacement along the axial direction of the valve. Note: One revolution of the camshaft gives the amount of valve lift shown in Figure 4.3 Figure 4.5: Temperature distribution (°C) of valves during operation.