Annexure-EIA/EMP
Total Page:16
File Type:pdf, Size:1020Kb
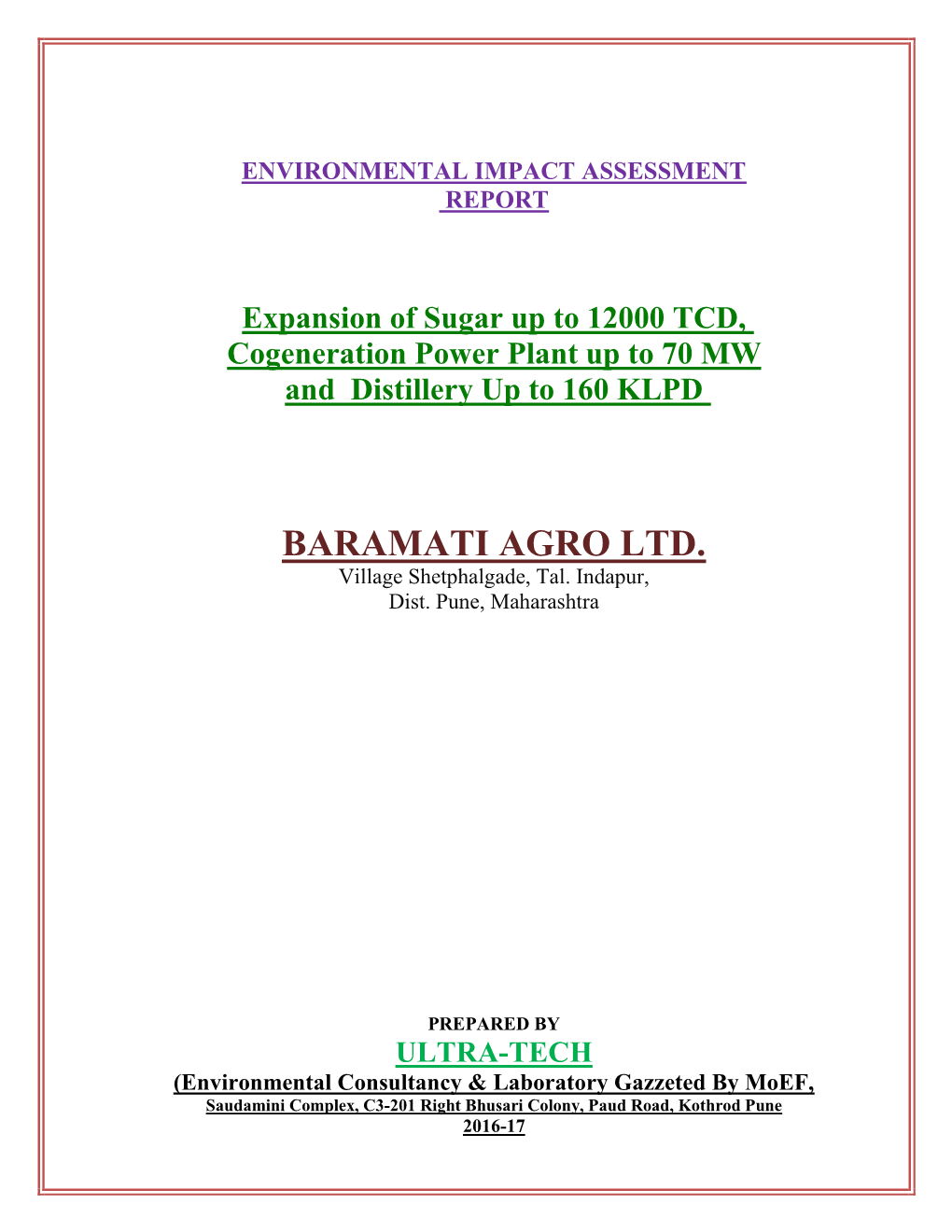
Load more
Recommended publications
-
By Thesis Submitted for the Degree of Vidyavachaspati (Doctor of Philosophy) Faculty for Moral and Social Sciences Department Of
“A STUDY OF AN ECOLOGICAL PATHOLOGICAL AND BIO-CHEMICAL IMPACT OF URBANISATION AND INDUSTRIALISATION ON WATER POLLUTION OF BHIMA RIVER AND ITS TRIBUTARIES PUNE DISTRICTS, MAHARASHTRA, INDIA” BY Dr. PRATAPRAO RAMGHANDRA DIGHAVKAR, I. P. S. THESIS SUBMITTED FOR THE DEGREE OF VIDYAVACHASPATI (DOCTOR OF PHILOSOPHY) FACULTY FOR MORAL AND SOCIAL SCIENCES DEPARTMENT OF SOCIOLOGY TILAK MAHARASHTRA VIDHYAPEETH PUNE JUNE 2016 CERTIFICATE This is to certify that the entire work embodied in this thesis entitled A STUDY OFECOLOGICAL PATHOLOGICAL AND BIOCHEMICAL IMPACT OF URBANISATION AND INDUSTRILISATION ON WATER POLLUTION OF BHIMA RIVER AND Its TRIBUTARIES .PUNE DISTRICT FOR A PERIOD 2013-2015 has been carried out by the candidate DR.PRATAPRAO RAMCHANDRA DIGHAVKAR. I. P. S. under my supervision/guidance in Tilak Maharashtra Vidyapeeth, Pune. Such materials as has been obtained by other sources and has been duly acknowledged in the thesis have not been submitted to any degree or diploma of any University or Institution previously. Date: / / 2016 Place: Pune. Dr.Prataprao Ramchatra Dighavkar, I.P.S. DECLARATION I hereby declare that this dissertation entitled A STUDY OF AN ECOLOGICAL PATHOLOGICAL AND BIO-CHEMICAL IMPACT OF URBANISNTION AND INDUSTRIALISATION ON WATER POLLUTION OF BHIMA RIVER AND Its TRIBUTARIES ,PUNE DISTRICT FOR A PERIOD 2013—2015 is written and submitted by me at the Tilak Maharashtra Vidyapeeth, Pune for the degree of Doctor of Philosophy The present research work is of original nature and the conclusions are base on the data collected by me. To the best of my knowledge this piece of work has not been submitted for the award of any degree or diploma in any University or Institution. -
A Review of Chiropterological Studies and a Distributional List of the Bat Fauna of India
Rec. zool. Surv. India: Vol. 118(3)/ 242-280, 2018 ISSN (Online) : (Applied for) DOI: 10.26515/rzsi/v118/i3/2018/121056 ISSN (Print) : 0375-1511 A review of Chiropterological studies and a distributional list of the Bat Fauna of India Uttam Saikia* Zoological Survey of India, Risa Colony, Shillong – 793014, Meghalaya, India; [email protected] Abstract A historical review of studies on various aspects of the bat fauna of India is presented. Based on published information and study of museum specimens, an upto date checklist of the bat fauna of India including 127 species in 40 genera is being provided. Additionaly, new distribution localities for Indian bat species recorded after Bates and Harrison, 1997 is also provided. Since the systematic status of many species occurring in the country is unclear, it is proposed that an integrative taxonomic approach may be employed to accurately quantify the bat diversity of India. Keywords: Chiroptera, Checklist, Distribution, India, Review Introduction smallest one being Craseonycteris thonglongyai weighing about 2g and a wingspan of 12-13cm, while the largest Chiroptera, commonly known as bats is among the belong to the genus Pteropus weighing up to 1.5kg and a 29 extant mammalian Orders (Wilson and Reeder, wing span over 2m (Arita and Fenton, 1997). 2005) and is a remarkable group from evolutionary and Bats are nocturnal and usually spend the daylight hours zoogeographic point of view. Chiroptera represent one roosting in caves, rock crevices, foliages or various man- of the most speciose and ubiquitous orders of mammals made structures. Some bats are solitary while others are (Eick et al., 2005). -
Final Feasibility Report National Waterways-21, Region VI - Bheema River Gundloor to Hippargi (138.9Km)
Final Feasibility Report National Waterways-21, Region VI - Bheema River Gundloor to Hippargi (138.9km) SURVEY PERIOD: 07 JAN 2016 - 18 FEB 2016 Volume - I Prepared for: Inland Waterways Authority of India (Ministry of Shipping, Govt. of India) A-13, Sector – 1, NOIDA Distt. Gautam Budh Nagar, Uttar Pradesh – 201 301 Document Distribution Date Revision Distribution Hard Copy Soft Copy INLAND WATERWAYS 20 Nov 2016 Rev – 0 01 01 AUTHORITY OF INDIA 13 Jan 2017 Rev – 1.0 INLAND WATERWAYS 01 01 AUTHORITY OF INDIA INLAND WATERWAYS 15 Sep 2017 Rev – 1.1 04 04 AUTHORITY OF INDIA INLAND WATERWAYS 23 Nov 2017 Rev – 1.2 01 01 AUTHORITY OF INDIA INLAND WATERWAYS 26 Oct 2018 Rev – 1.3 04 04 AUTHORITY OF INDIA IWAI, Region VI, Bheema River Final Feasibility Report Page II ACKNOWLEDGEMENT IIC Technologies Ltd. expresses its sincere gratitude to IWAI for awarding the work of carrying out detailed hydrographic surveys in the New National Waterways in NW-21 in Region VI – Bheema River from Gundloor to Hippargi. We would like to use this opportunity to pen down our profound gratitude and appreciations to Shri Pravir Pandey, IA&AS, Chairman IWAI for spending his valuable time and guidance for completing this Project. IIC Technologies Ltd., would also like to thank, Shri Alok Ranjan, ICAS, Member (Finance), Shri Shashi Bhushan Shukla, Member (Traffic), Shri S.K. Gangwar, Member (Technical) for their valuable support during the execution of project IIC Technologies Ltd, wishes to express their gratitude to Capt. Ashish Arya, Hydrographic Chief IWAI, Cdr. P.K. Srivastava ex-Hydrographic Chief and Shri SVK Reddy, Chief Engineer-I for their guidance and inspiration for this project. -
State Disaster Management Plan
Disaster Management Plan Maharashtra State Disaster Management Plan State Disaster Management Authority Mantralaya, Mumbai April, 2016 Disaster Management Unit Relief and Rehabilitation Department Government of Maharashtra Contents PART – I Chapter – 1 1. Introduction Page No 1.1 Background ............................................................................................... 1 1.2 Vision ....................................................................................................... 1 1.3 Objective of the Plan ................................................................................. 2 1.4 Themes ..................................................................................................... 2 1.5 Approach ................................................................................................... 2 1.6 Strategy ..................................................................................................... 3 1.7 Scope of the Plan ...................................................................................... 3 1.8 Authority and Reference ........................................................................... 4 1.9 Level of Disasters ..................................................................................... 4 1.10 Plan Development and Activation ............................................................. 4 1.11 Review/update of DM Plan ....................................................................... 5 1.12 Plan Testing ............................................................................................. -
General and Social Sector, Government of Maharashtra
Report of the Comptroller and Auditor General of India on General and Social Sector for the year ended March 2018 GOVERNMENT OF MAHARASHTRA Report No. 1 of the year 2019 Table of Contents TABLE OF CONTENTS Reference Paragraph Page No. Preface v CHAPTER I INTRODUCTION About this Report 1.1 1 Audited Entity Profile 1.2 1 Authority for Audit 1.3 2 Organisational Structure of the Offices of the 1.4 2 Principal Accountant General (Audit)-I, Mumbai and the Accountant General (Audit)-II, Nagpur Planning and Conduct of Audit 1.5 3 Significant Audit Observations 1.6 3 Responsiveness of Government to Audit 1.7 7 CHAPTER II PERFORMANCE AUDITS Minorities Development Department 2.1 9 Functioning of Minorities Development Department Home Department Administration of Prison and Correctional Centers in 2.2 38 Maharashtra Medical Education and Drugs Department Implementation of Healthcare and Academics 2.3 75 Management Information System CHAPTER III AUDIT OF TRANSACTIONS Revenue and Forest Department 3.1 95 Preparedness for Disaster Management Social Justice and Special Assistance Department 3.2 114 Functioning of Hostels for Backward Class Students Revenue and Forest Department Management of leases of Government land given to 3.3 135 Gymkhanas in Mumbai Women and Child Development Department 3.4 137 Idling of Government State Home building Housing Department 3.5 138 Unoccupied tenements iii Report No. 1 (General and Social Sector) for the year ended March 2018 Housing Department 3.6 140 Undue benefit to Developers Housing Department 3.7 142 Undue benefit to Developers Urban Development Department 3.8 143 Loss of Revenue Urban Development Department/ Housing Department 3.9 145 Release of Excess Transfer of Development Rights to Developer Tribal Development Department 3.10 147 Avoidable expenditure Higher and Technical Education Department 3.11 148 Avoidable payment of Electricity duty Reference APPENDICES Appendix Page No. -
19333 STD Code of INDIA
STD Code of INDIA Home Page Place State STDCode A B Palem Andhra Pradesh 08594 A Chettipalli Tamil Nadu 04344 A Khurd Maharashtra 02342 A Koduru Andhra Pradesh 08924 A Kondapuram Andhra Pradesh 08558 A Laddivadi Tamil Nadu 04282 A Long NE 037832 A Mallavaram Andhra Pradesh 08869 A Nalroad Tamil Nadu 04552 A Pudur Tamil Nadu 0428356 A S Peta Andhra Pradesh 08627 A V Nagaram Andhra Pradesh 08854 A Vellalapatti Tamil Nadu 0452 A.r. -
Maharashtra State Disaster Management Plan Draft Copy
Maharashtra State Disaster Management Plan Any feedback may send at [email protected] Draft Copy Disaster Management Unit Relief and Rehabilitation Department Government of Maharashtra 0 Part –I General information of the State Vulnerabilty Assessment and Risk Analysis Preventive and Mitigation Measures Response Mechanism Partnership with Other Stakeholders Recovery Plan Financial Arrangement 1 Chapter -1 Introduction 1.1 Background India is prone to a large number of natural as well as man-made disasters. 58.6 per cent of the landmass is prone to earthquakes of moderate to very high intensity; over 40 million hectares (12 per cent of land) is prone to floods and river erosion; of the 7,516 km long coastline, close to 5,700 km is prone to cyclones and tsunamis; 68 per cent of the cultivable area is vulnerable to drought and hilly areas are at risk from landslides and avalanches. Vulnerability to disasters/ emergencies of Chemical, Biological, Radiological and Nuclear (CBRN) origin also exists. Heightened vulnerabilities to disaster risks can be related to expanding population, terrorism, urbanization and industrialization, development within high-risk zones, environmental degradation and climate change to ensuring clarity about roles and responsibilities of the State, District and local authorities. Disasters disrupt progress and destroy the hard-earned fruits of painstaking developmental efforts in quest for progress. Maharashtra State has a profile of varied hazards and was first in India to start a Disaster Management Unit (DMU) after the Latur earthquake. Since 1993, Disaster Management (DM) in Maharashtra is fast evolving from a reactive response oriented to proactive strategy based system. -
Annual Report Cover Design
College of Engineering, Pune Forerunners in Technical Education COLLEGE OF ENGINEERING PUNE ANNUAL REPORT 2018-2019 College of Engineering, Pune Forerunners in Technical Education College of Engineering, Pune Forerunners in Technical Education Vision, Mission and Goals Vision To be a Value based globally recognized Institution ensuring academic excellence and fostering Research, Innovation and Entrepreneurial Attitude. Mission • To be a student centric institute imbibing experiential, innovative and lifelong learning skills, addressing societal problems. • To promote and undertake all-inclusive research and development. • To inculcate entrepreneurial attitude and values amongst Learners. • To strengthen National and International, Industrial and institutional collaborations for symbiotic relations. • To mentor aspiring Institutions to unleash their potential, towards nation building. Core Values (S T E E R) • Strength • Truth • Endurance • Ethics • Reverence for All Goals: COEP @ 2022 • To be a globally recognized Engineering institution in top 500 bracket. • To attain 25 % growth in terms of intake capacity with UG:PG ratio of 50:50 and 200 % Growth in research leading to Ph.D’s • To accomplish 200 % growth in research outcomes in terms of Quality Publications in Tier-I journals & conferences, Patents, Sponsored R&D Projects, Technology Products, Books & Monograms etc. • To establish 5 collaborative Finishing Schools to impart high-end technical skills for enhancing employability and 2 industry-partnered Incubation Centers for encouraging entrepreneurship. • To have a 25 % of Student Population opting to be either the First Generation Entrepreneurs and/or pursuing higher studies at Institutes of repute. • To be a Multi-faculty Campus, establishing 5 multidisciplinary research centers in diversified areas, and 5 interdisciplinary academic programs. -
A Review of the Distribution of Bats in Southwestern Region of Deccan, Maharashtra - India and Conservation Recommendations
TAPROBANICA , ISSN 1800-427X. April, 2012. Vol. 04, No. 01: pp. 27-36, 1 pl. © Taprobanica Private Limited, Jl. Kuricang 18 Gd.9 No.47, Ciputat 15412, Tangerang, Indonesia. A REVIEW OF THE DISTRIBUTION OF BATS IN SOUTHWESTERN REGION OF DECCAN, MAHARASHTRA - INDIA AND CONSERVATION RECOMMENDATIONS Sectional Editor: Colin Chapman Submitted: 06 September 2011, Accepted: 23 May 2012 Mahesh C. Gaikwad1, Sujit S. Narwade2, Kamlakar M. Fartade3 and Vishakha S. Korad4 1 Nimblak, Faltan, District Satara, Maharashtra, India 2 Utkarsh Nagar, Vijapur road, Solapur, India; E-mail: [email protected] 3 At post Satwaiwadi, Tal-Vashi, District Osmanabad, Maharashtra, India 4 Department of Zoology, Fergusson College, Pune, Maharashtra, India Abstract In present survey carried out in the South-West region of Maharashtra, India, 11 bat species were reported from the study area. The area comprised four districts of Maharashtra namely Pune, Satara, Solapur and Osmanabad. It was also found that all the bat species mentioned in this paper are much more widely distributed than was previously recorded and populations occur in areas for which only single or scattered records were previously available. Conversion of habitats of bats for various purposes by humans was found as one of the important threats to bats in region. Keywords: Chiroptera, fruit bat, leaf-nosed bat, false vampire, flying fox, Pipistrelle, ecology. Introduction Bats form some of the largest non-human of Microchiropteran bats found in India are aggregations of mammals, and may be among the insectivorous. They are important components of most abundant groups of mammals when measured forest as well as agricultural ecosystems. -
Data Entry Operator-1
List of candidates for interview for the post of Data Entry Operator, NCD under NRHM, Assam Sl. Name Address Date of Interview 1 Abdul Hakim C/o. Nur Islam, Chapgarh Pt. I, PO. Khudimari, Dist. Dhubri, Pin. 783331 13/06/2013 C/o. Jobbul Hussain, Jhagrar Par Pt. III ( G.P. Office), PO. Jhagrar Par, Dist. 2 Abdul Malek Ali 13/06/2013 Dhubri, Pin. 783324 C/o Nizam Uddin Mazumder, Vill.- Barnagad, P.O.- Kalibari Bazar, P.S.- 3 Abdul Quiyam Mazumder 13/06/2013 Algapur, Dist.- Hailakandi, Pin-788150 C/o - Nabibur Rahman, House No - 33 Vill: Hedayetpur, PO: Silpukhuri 4 Abdus Samad Dewan 13/06/2013 PS: Latasil, Dist: Kamrup (M) PIN: 781003 5 Abhijit Dutta C/o. Satosh Kr. Dutta, HnO. 646, PO. Boiragi math, Dist. Dibrugarh, Pin. 786003 13/06/2013 C/O. Jatin Hazarika, Vill. Jamirah Tepor Gaon 6 Abhijit Hazarika P.O. Dhamal Gaon, P.S. Barbaruah 13/06/2013 Dist. Dibrugarh, Pin-786004 C/o- Ambu Ram Nath Vill- Nabheti, Ward No.-5 P.O./P.S./Dist.- Morigaon, Pin- 7 Abhijit Nath 13/06/2013 782105 C/O. Dhiren Nath, H.No.231 Town. Kalaha Bhanga, W/No.03, 8 Abhijit Nath 13/06/2013 P.O. & P.S. Barpeta Road Dist. Barpeta, Assam, Pin-781315 C/o. Lachit Saikia, Konwarpur Karigaon, PO. Karigaon, Dist. Sivasagar, Pin. 9 Abhijit Saikia 13/06/2013 785667 C/o - Tarun Saikia House No - W.N.o -3 10 Abhijit Saikia Town - Rangia 13/06/2013 PO & PS: Rangia PIN: 781354 C/O: Mr Ghanashyam Medhi 11 Abhijit Saikia H No: 15, Town: Sarvodaya Nagar, Chandmari 13/06/2013 PO: Silpukhuri, PS: Chandmari, Dist: Kamrup(Assam), PIN: 781021 C/o. -
Delineation of Recharging Zones for Groundwater in Bhima River Basin, Pandharpur, Maharashtra 1 2 1 Nishad Patki , V.R.Ghodke , and N
Proceeding of International Conference SWRDM-2012 Delineation Of Recharging Zones For Groundwater In Bhima River Basin, Pandharpur, Maharashtra 1 2 1 Nishad Patki , V.R.Ghodke , and N. J. Sathe 1Department of Civil Engg., Sinhgad College Of Engineering, Pune. 2 Dept. of Applied Geology, Solapur University, Solapur. [email protected] Abstract The ground water behaviour in the Indian sub-continent is highly complicated due to the occurrence of diversified geological formations with considerable litho-logical and chronological variations, complex tectonic framework, climate- logical dissimilarities and various hydro-chemical conditions. Occurrence of groundwater in hard rock terrain is mainly controlled by structures, landforms, litho-logy and recharge conditions. The Deccan Trap area in Maharashtra generally comes in this category. The study area considered is the Bhima Basin (Nira-Narsinghpur to Pandharpur) where ground water is a major source of usable water due to drought conditions. Electrical resistivity distribution at different depth horizons for Bhima River basin in Solapur District, Maharashtra has been delineated and represented by contour maps at different electrode spacing. These are correlated with local Geology for semi quantitative interpretation to detect potential zones of groundwater. Keywords: Groundwater, Lithology, Deccan Trap, Pandharpur, Electrical Resistivity Introduction: Electrical Resistivity distribution studies were Weathered zeolitic/fragmentary lithounit is made for Bhima basin between Narsinghpur to exposed near Babulgaon and is overlain by redbole of 1m Pandharpur in Solapur District, Maharashtra located on thickness, around Umbre representing oldest flow in the the Toposheets 47O/1, 47O/4 & 47O/5. The area is basin. The thickness of the flow is 21m. IInd flow consists of considered along meanders of Bhima river, and is selected lower 8m thick weathered basalt clinker and starts by keeping 3 km buffer distance on both side of flood between Mire and Umbre Velapur. -
CIN/BCIN Company/Bank Name Investor First Name Investor Middle
Note: This sheet is applicable for uploading the particulars related to the amount credited to Investor Education and Protection Fund. Make sure that the details are in accordance with the information already provided in e-form IEPF-1 CIN/BCIN L29120PN2009PLC133351 Prefill Company/Bank Name KIRLOSKAR OIL ENGINES LIMITED Sum of unpaid and unclaimed dividend 666520.00 Sum of interest on matured debentures 0.00 Validate Sum of matured deposit 0.00 Sum of interest on matured deposit 0.00 Sum of matured debentures 0.00 Clear Sum of interest on application money due for refund 0.00 Sum of application money due for refund 0.00 Redemption amount of preference shares 0.00 Sales proceed for fractional shares 0.00 Sum of Other Investment Types 0.00 Date of event (date of declaration of dividend/redemption date Is the of preference shares/date Date of Birth(DD-MON- Investment Investor First Investor Middle Investor Last Father/Husband Father/Husband Father/Husband Last DP Id-Client Id- Amount of maturity of Joint Holder Address Country State District Pin Code Folio Number Investment Type PAN YYYY) Aadhar Number Nominee Name Remarks (amount / Name Name Name First Name Middle Name Name Account Number transferred bonds/debentures/applicat Name shares )under ion money any litigation. refundable/interest thereon (DD-MON-YYYY) 39/44 PRABHAT RD 9TH GALLI KIRL000000000A001 Amount for unclaimed and NO A A KHANDEKAR NA PUNE 411004 PUNE INDIA Maharashtra 411004 950 unpaid dividend 12.00 24-Aug-2019 11 78 RAMNIVAS MIRJALGUDA MALKAJGIRI HYDERABAD-47 KIRL000000000A000 Amount for unclaimed and NO A BHASKER RAO NA HYDERABAD INDIA Andhra Pradesh 500047 995 unpaid dividend 4.00 24-Aug-2019 C/O SAKAL OFFICE, 595 BUDHWAR KIRL000000000A002 Amount for unclaimed and NO A JASVANTLAL NA PETH, PUNE PUNE INDIA Maharashtra 411002 602 unpaid dividend 56.00 24-Aug-2019 15/469 NEHRU NAGAR KURLA KIRL000000000A000 Amount for unclaimed and NO A P KARNIK NA BOMBAY-70 MUMBAI INDIA Maharashtra 400070 347 unpaid dividend 4.00 24-Aug-2019 PLOT NO.