Preparation of Conductive Polyester Fibers Using Continuous Two-Step Plating Silver
Total Page:16
File Type:pdf, Size:1020Kb
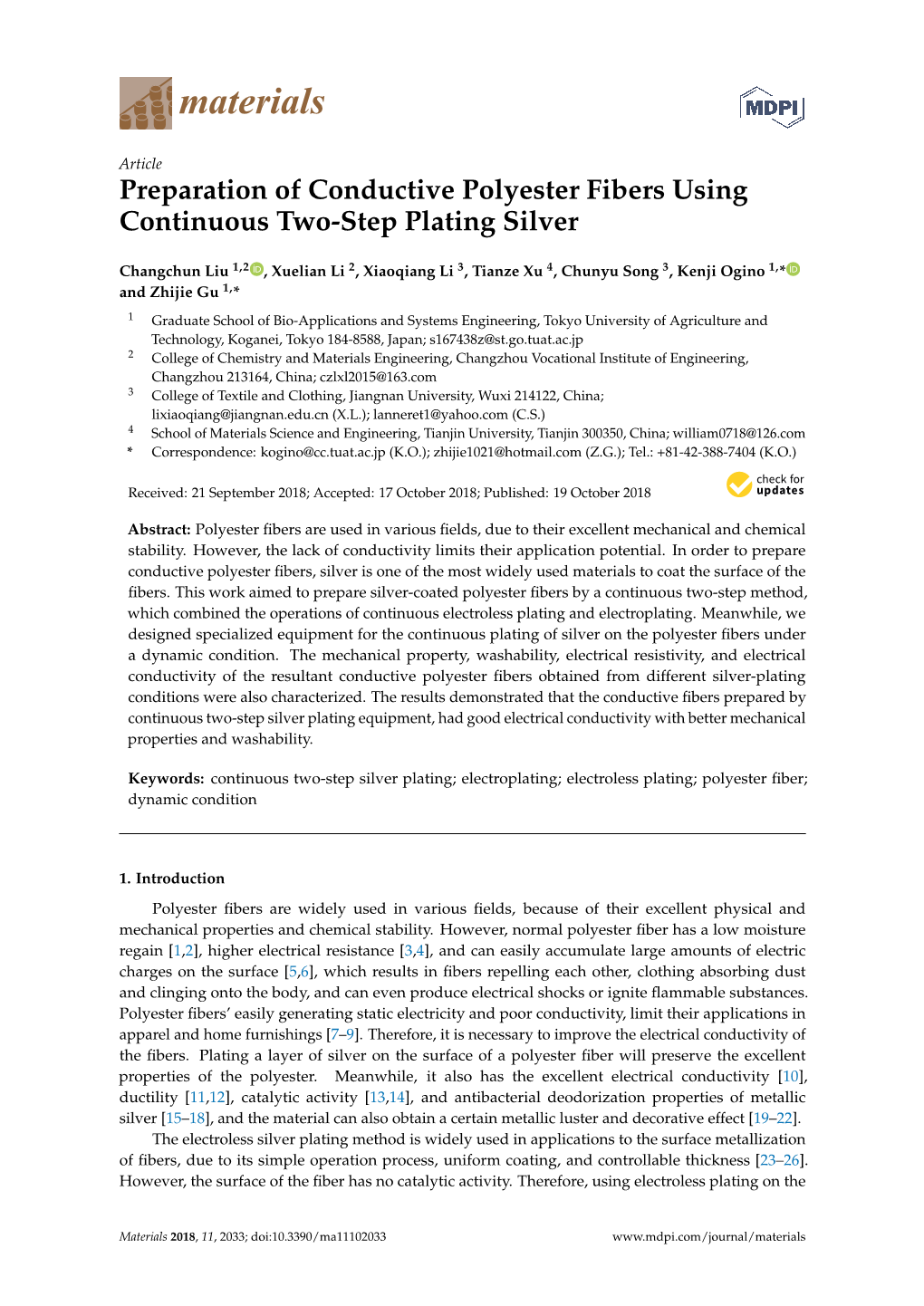
Load more
Recommended publications
-
Dem-Cfd Analysis of Contact Electrification and Electrostatic Interactions During Powder Handling Processes
DEM-CFD ANALYSIS OF CONTACT ELECTRIFICATION AND ELECTROSTATIC INTERACTIONS DURING POWDER HANDLING PROCESSES CHUNLEI PEI BEng A thesis submitted to the University of Birmingham for the degree of DOCTOR OF PHILOSOPHY School of Chemical Engineering University of Birmingham September 2013 University of Birmingham Research Archive e-theses repository This unpublished thesis/dissertation is copyright of the author and/or third parties. The intellectual property rights of the author or third parties in respect of this work are as defined by The Copyright Designs and Patents Act 1988 or as modified by any successor legislation. Any use made of information contained in this thesis/dissertation must be in accordance with that legislation and must be properly acknowledged. Further distribution or reproduction in any format is prohibited without the permission of the copyright holder. ABSTRACT Electrostatic phenomena are pervasive in powder handling processes. In this study, contact electrification and electrostatic interactions during powder handling processes are explored using the discrete element method coupled with computational fluid dynamics (DEM-CFD), in which contact electrification and electrostatic interaction models are developed and implemented. The effects of particle shape on contact electrification are also investigated, for which multi-sphere methods are adapted and implemented into the DEM-CFD. The electrostatic and dynamic behaviours in various powder handling processes are then analyzed, which include contact electrification of spherical particles during fluidization; electrostatic interactions during deposition of mono-charged and bi-charged particles; contact electrification and electrostatic interactions of spherical particles during fluidization; contact electrification of elongated particles in a vibrating container and particles of arbitrary shapes in a rotating drum. -
Integration of Micro-Supercapacitors with Triboelectric Nanogenerators for a Flexible Self-Charging Power Unit
Nano Research 2015, 8(12): 3934–3943 DOI 10.1007/s12274-015-0894-8 Integration of micro-supercapacitors with triboelectric nanogenerators for a flexible self-charging power unit Jianjun Luo1,§, Feng Ru Fan1,2,§, Tao Jiang1, Zhiwei Wang1, Wei Tang1, Cuiping Zhang1, Mengmeng Liu1, Guozhong Cao1,3, and Zhong Lin Wang1,4 () 1 Beijing Institute of Nanoenergy and Nanosystems, Chinese Academy of Sciences, Beijing 100083, China 2 Collaborative Innovation Center of Chemistry for Energy Materials, College of Chemistry and Chemical Engineering, Xiamen University, Xiamen 361005, China 3 Department of Materials Science and Engineering, University of Washington, Seattle, Washington 98195, USA 4 School of Material Science and Engineering, Georgia Institute of Technology, Atlanta, Georgia 30332, USA § These authors contributed equally to this work. Received: 17 July 2015 ABSTRACT Revised: 6 September 2015 The rapid development of portable and wearable electronic devices has Accepted: 8 September 2015 increased demand for flexible and efficient energy harvesting and storage units. Conventionally, these are built and used separately as discrete components. © Tsinghua University Press Herein, we propose a simple and cost-effective laser engraving technique for and Springer-Verlag Berlin fabricating a flexible self-charging micro-supercapacitor power unit (SCMPU), Heidelberg 2015 by integrating a triboelectric nanogenerator (TENG) and a micro-supercapacitor (MSC) array into a single device. The SCMPU can be charged directly by ambient KEYWORDS mechanical motion. We demonstrate the ability of the SCMPU to continuously energy harvesting, power light-emitting diodes and a commercial hygrothermograph. This inves- energy storage, tigation may promote the development of sustainable self-powered systems and triboelectric nanogenerator provide a promising new research application for supercapacitors. -
Influence of Electrostatic Potentials on Rotating Discs for Liquid Spraying Adhemar Brandini Iowa State University
Iowa State University Capstones, Theses and Retrospective Theses and Dissertations Dissertations 1978 Influence of electrostatic potentials on rotating discs for liquid spraying Adhemar Brandini Iowa State University Follow this and additional works at: https://lib.dr.iastate.edu/rtd Part of the Agriculture Commons, and the Bioresource and Agricultural Engineering Commons Recommended Citation Brandini, Adhemar, "Influence of electrostatic potentials on rotating discs for liquid spraying " (1978). Retrospective Theses and Dissertations. 6373. https://lib.dr.iastate.edu/rtd/6373 This Dissertation is brought to you for free and open access by the Iowa State University Capstones, Theses and Dissertations at Iowa State University Digital Repository. It has been accepted for inclusion in Retrospective Theses and Dissertations by an authorized administrator of Iowa State University Digital Repository. For more information, please contact [email protected]. INFORMATION TO USERS This was produced from a copy of a document sent to us for microfilming. While the most advanced technological means to photograph and reproduce this document have been used, the quality is heavily dependent upon the quality of the material submitted. The following explanation of techniques is provided to help you understand markings or notations which may appear on this reproduction. 1. The sign or "target" for pages apparently lacking from the document photographed is "Missing Page(s)". If it was possible to obtain the missing page(s) or section, they are spliced into the film along with adjacent pages. This may have necessitated cutting through an image and duplicating adjacent pages to assure you of complete continuity. 2. When an image on the film is obliterated with a round black mark it is an indication that the film inspector noticed either blurred copy because of movement during exposure, or duplicate copy. -
Nanogenerators As a Sustainable Power Source: State of Art, Applications, and Challenges
nanomaterials Review Nanogenerators as a Sustainable Power Source: State of Art, Applications, and Challenges Sridhar Sripadmanabhan Indira 1 , Chockalingam Aravind Vaithilingam 1,* , Kameswara Satya Prakash Oruganti 1 , Faizal Mohd 1 and Saidur Rahman 2,3 1 School of Engineering, Faculty of Innovation and Technology, Taylor’s University Lakeside Campus, No. 1, Jalan Taylor’s, 47500 Subang Jaya, Selangor, Malaysia; [email protected] (S.S.I.); [email protected] (K.S.P.O.); [email protected] (F.M.) 2 Research Centre for Nano-Materials and Energy Technology (RCNMET), School of Science and Technology, Sunway University, 47500 Subang Jaya, Malaysia; [email protected] 3 American University of Ras Al Khaimah, 31291 Ras Al Khaimah, UAE * Correspondence: [email protected]; Tel.: +00-6012-354-3891 Received: 7 April 2019; Accepted: 13 May 2019; Published: 20 May 2019 Abstract: A sustainable power source to meet the needs of energy requirement is very much essential in modern society as the conventional sources are depleting. Bioenergy, hydropower, solar, and wind are some of the well-established renewable energy sources that help to attain the need for energy at mega to gigawatts power scale. Nanogenerators based on nano energy are the growing technology that facilitate self-powered systems, sensors, and flexible and portable electronics in the booming era of IoT (Internet of Things). The nanogenerators can harvest small-scale energy from the ambient nature and surroundings for efficient utilization. The nanogenerators were based on piezo, tribo, and pyroelectric effect, and the first of its kind was developed in the year 2006 by Wang et al. -
Contact Electrification Induced Interfacial Reactions and Direct
Chemical Science View Article Online EDGE ARTICLE View Journal | View Issue Contact electrification induced interfacial reactions and direct electrochemical nanoimprint Cite this: Chem. Sci.,2017,8,2407 lithography in n-type gallium arsenate wafer† Jie Zhang, Lin Zhang, Wei Wang, Lianhuan Han, Jing-Chun Jia, Zhao-Wu Tian, Zhong-Qun Tian and Dongping Zhan* Although metal assisted chemical etching (MacEtch) has emerged as a versatile micro-nanofabrication method for semiconductors, the chemical mechanism remains ambiguous in terms of both thermodynamics and kinetics. Here we demonstrate an innovative phenomenon, i.e., the contact electrification between platinum (Pt) and an n-type gallium arsenide (100) wafer (n-GaAs) can induce interfacial redox reactions. Because of their different work functions, when the Pt electrode comes into contact with n-GaAs, electrons will move from n-GaAs to Pt and form a contact electric field at the Pt/n-GaAs junction until their electron Fermi levels (EF) become equal. In the presence of an electrolyte, the potential of the Pt/electrolyte interface will À Creative Commons Attribution 3.0 Unported Licence. shift due to the contact electricity and induce the spontaneous reduction of MnO4 anions on the Pt surface. Because the equilibrium of contact electrification is disturbed, electrons will transfer from n-GaAs to Received 12th September 2016 Pt through the tunneling effect. Thus, the accumulated positive holes at the n-GaAs/electrolyte interface Accepted 16th December 2016 make n-GaAs dissolve anodically along the Pt/n-GaAs/electrolyte 3-phase interface. Based on this principle, DOI: 10.1039/c6sc04091h we developed a direct electrochemical nanoimprint lithography method applicable to crystalline www.rsc.org/chemicalscience semiconductors. -
Design and Construction of an Emg Multichannel Acquisition System Prototype
POLITECNICO DI TORINO III Faculty of Engineering Degree in Mechatronics Engineering Master Thesis DESIGN AND CONSTRUCTION OF AN EMG MULTICHANNEL ACQUISITION SYSTEM PROTOTYPE Relator: Prof. Marcello Chiaberge Sebastián Aced López DLR German Aerospace Center Dipl. Inf. Holger Urbanek September 2012 Summary This thesis presents the design and construction of an Electromyography (EMG) high−density acquisition system prototype at the Deutschen Zentrums für Luft und Raumfahrt (DLR) Bionics group in Munich− Germany. It does not intend to come up with new principles of EMG recording, but its scope is to search, compare, simulate, construct and validate nowadays available solutions that fulfill the imposed requirements. The design consists in ten functional blocks that cover all the system aspects from the power supply to the measuring electrodes. In order to construct the circuit prototype, some classical solutions were implemented and some novelty configura- tions were explored, for instance: a novelty DC rejection filter without grounded resistors, to prevent degradation of the front−end amplifier Common Mode rejec- tion (CMR) and the driven shields that solved the problem of amplifying the EMG signal at a considerable distance from the source. This document covers all the way in between the muscles and the computer, that EMG signals go through: electrodes, esd protection, shield cables, DC rejection, amplification, Driven Right Leg feedback, filtering, isolation and digitization. iii Acknowledgements I would like to thank all the people at the DLR in Germany that helped me and thought me so many things during this six intense months. Specially I want to thank to Patrick van der Smagt, for the great opportunity of working in his lab, to Holger my supervisor and Robert my other supervisor. -
Contact Electrification Induced Interfacial Reactions and Direct
Chemical Science View Article Online EDGE ARTICLE View Journal | View Issue Contact electrification induced interfacial reactions and direct electrochemical nanoimprint Cite this: Chem. Sci.,2017,8,2407 lithography in n-type gallium arsenate wafer† Jie Zhang, Lin Zhang, Wei Wang, Lianhuan Han, Jing-Chun Jia, Zhao-Wu Tian, Zhong-Qun Tian and Dongping Zhan* Although metal assisted chemical etching (MacEtch) has emerged as a versatile micro-nanofabrication method for semiconductors, the chemical mechanism remains ambiguous in terms of both thermodynamics and kinetics. Here we demonstrate an innovative phenomenon, i.e., the contact electrification between platinum (Pt) and an n-type gallium arsenide (100) wafer (n-GaAs) can induce interfacial redox reactions. Because of their different work functions, when the Pt electrode comes into contact with n-GaAs, electrons will move from n-GaAs to Pt and form a contact electric field at the Pt/n-GaAs junction until their electron Fermi levels (EF) become equal. In the presence of an electrolyte, the potential of the Pt/electrolyte interface will À Creative Commons Attribution 3.0 Unported Licence. shift due to the contact electricity and induce the spontaneous reduction of MnO4 anions on the Pt surface. Because the equilibrium of contact electrification is disturbed, electrons will transfer from n-GaAs to Received 12th September 2016 Pt through the tunneling effect. Thus, the accumulated positive holes at the n-GaAs/electrolyte interface Accepted 16th December 2016 make n-GaAs dissolve anodically along the Pt/n-GaAs/electrolyte 3-phase interface. Based on this principle, DOI: 10.1039/c6sc04091h we developed a direct electrochemical nanoimprint lithography method applicable to crystalline www.rsc.org/chemicalscience semiconductors. -
Contact Potentials, Fermi Level Equilibration, and Surface Charging Pekka Peljo,*,† Joséa
Article pubs.acs.org/Langmuir Contact Potentials, Fermi Level Equilibration, and Surface Charging Pekka Peljo,*,† JoséA. Manzanares,‡ and Hubert H. Girault† † Laboratoire d’Electrochimie Physique et Analytique, École Polytechnique Fedéralé de Lausanne, EPFL Valais Wallis, Rue de l’Industrie 17, Case Postale 440, CH-1951 Sion, Switzerland ‡ Department of Thermodynamics, Faculty of Physics, University of Valencia, c/Dr. Moliner, 50, E-46100 Burjasot, Spain *S Supporting Information ABSTRACT: This article focuses on contact electrification from thermodynamic equilibration of the electrochemical potential of the electrons of two conductors upon contact. The contact potential difference generated in bimetallic macro- and nanosystems, the Fermi level after the contact, and the amount and location of the charge transferred from one metal to the other are discussed. The three geometries considered are spheres in contact, Janus particles, and core−shell particles. In addition, the force between the two spheres in contact with each other is calculated and is found to be attractive. A simple electrostatic model for calculating charge distribution and potential profiles in both vacuum and an aqueous electrolyte solution is described. Immersion of these bimetallic systems into an electrolyte solution leads to the formation of an electric double layer at the metal−electrolyte interface. This Fermi level equilibration and the associated charge transfer can at least partly explain experimentally observed different electrocatalytic, catalytic, and optical properties of multimetallic nanosystems in comparison to systems composed of pure metals. For example, the shifts in the surface plasmon resonance peaks in bimetallic core−shell particles seem to result at least partly from contact charging. ■ INTRODUCTION of an electric double layer around the particles. -
Study of the Effect of Rubbing Materials on the Tribo-Electrification of Textile Materials
Study of the Effect of Rubbing Materials on the Tribo-electrification of Textile Materials By IieZhao A Thesis Submitted to the Faculty of Graduate Studies in Partial Fulfillment of the Requirernents for the Degree of MASTER OF SCTENCE Department of Clothing and Textiles University of Manitoba Winnipeg, Manitoba @ Copyright by Jie Zhao,2003 THE T]NTYERSITY OF' MANITOBA FACULTY OF GRADUATE STUDIES ***** COPYRIGHT PERMISSION PAGE STI]DY OF TIIE EFF'ECT OF'RUBBING MATERIALS ON THE TRIBO.ELECTRIF'ICATION OF TEXTILE MATERIALS BY JIE ZHAO A ThesisÆracticum submitted to the Faculty of Graduate Studies of The University of Manitoba in partial fulfillment of the requirements of the degree of Master of Science JIE ZIIAO @ 2OO3 Permission has been granted to the Library of The University of Manitoba to lend or sell copies of this thesis/practicum, to the National Library of Canada to microfilm this thesis and to lend or sell copies of the film, and to University Microfilm Inc. to publish an abstract of this thesis/practicum. The author reserves other publication rights, and neither this thesis/practicum nor extensive extracts from it may be printed or otherwise reproduced without the authorrs written permission. Abstract This research describes a study of the effect of rubbing materials on the electrostatic propensity of textile fibers. The fibers included were cellulose-based f,rbers, protein-based fibers, manufactured fibers, and blends. The three rubbing materials were poly-tetra-fluorethylene (PTFE), polyvinyl chloride (PVC) and nylon 6. Peak static charges lvere measured and monitored from tribo-charged fabric surfaces. Experiments were conducted in an environmental chamber at 20'C and 30 o/orelatíve humidity. -
Wafer After Contact Electrification Using Kelvin Force Microscopy
Manila Journal of Science 10 (2017), pp. 114-125 Surface Analysis of Silicon (100) Wafer After Contact Electrification Using Kelvin Force Microscopy Jose M. Esmeria, Jr.,1, 2 Romeric Pobre1 1Physics Department, De La Salle University, 2401 Taft Avenue, Manila 1004, Philippines 2 Reliability Engineering Department, TDK Philippines Corporation (TPC), 119 East Science Avenue, SEPZ, Biñan, Laguna 4024, Philippines. *Corresponding Author: [email protected] ABSTRACT Contact electrification was demonstrated on Si (100) wafer, and surface charge images at submicron scale were analysed using Kelvin force microscopy (KFM). Potential map images have shown carpet-like patterns on the (100) plane of Si wafer. Individual potential spikes that appeared on the surface are indicative of the presence of charges arising from contact electrification. It was clearly shown that positive and negative surface potential maps on Si (100) wafer with low resistivity have minimal change in the order of ±2.5 mV after 4800 seconds of noncontact electrification. The mechanism for the slow discharged on the Si (100) wafer can be modelled like a clamped capacitor direct current (D.C.) electric circuit. Keywords: Surface interfaces, Contact electrification, Triboelectricity. Copyright © 2017 by De La Salle University SURFACE ANALYSIS OF SILICON (100) WAFER ESMERIA & POBRE 115 INTRODUCTION force, room humidity, and ground continuity of the material (Hogue, 2004). A significant number of researches have Triboelectric charging between two been done for the last 50 years in contact different metals is widely accepted as an electrification (CE). CE or triboelectricity has exchange of electrons due to their work function beneficial applications in medical sensors difference. -
An Exploration on Tribo-Charging and Electron Transfer of Ash Forming Minerals in Coal by Contact Angle Goniometry
An exploration on tribo-charging and electron transfer of ash forming minerals in coal by contact angle goniometry R. K. Dwari and K. Hanumantha Rao Division of Mineral Processing, Luleå University of Technology, SE-97187 LULEÅ, Sweden ABSTRACT The electrostatic beneficiation of coal is based on tribo-charging characteristics of ash forming minerals and coal particles. The tribo-charging of quartz and coal particles contacted with various metals and polymer materials have been measured and the charge acquisition is assessed through surface energy calculations from liquid contact angle data. The contact angles, before and after tribo-charging of solids, are measured using Krüss tensiometer and Washburn’s equation where the sample holders in tensiometer are specially constructed with tribo-charger materials. The charge polarity and amount of charge acquired by quartz and carbon with metal tribo- chargers were found in good agreement with the reported work functions of the contacting surfaces. The charge results with polymer materials differed from the work function values, presumably caused by surface contamination. The surface energy of quartz calculated by all the theoretical approaches in the literature showed that the tribo-charging increases the surface energy. Both polar and non-polar components computed from Fowkes and Owens- Wendt-Rabel-Kaelble approaches display that both these components increased after tribo- electrification. However, the polar component divided into acid and base components, as in van Oss approach, manifest decreasing acid part and increasing base part. Since quartz charged negatively during tribo-charging with metal surfaces and therefore accepted electrons, the determined acid-base surface energy components are consistent with charge transfer process. -
Applications of Electrified Dust and Dust Devil Electrodynamics to Martian Atmospheric Electricity
Harrison, R. G., Barth, E., Esposito, F., Merrison, J., Montmessin, F., Aplin, K. L., Borlina, C., Berthelier, J. J., Déprez, G., Farrell, W. M., Houghton, I. M. P., Renno, N. O., Nicoll, K. A., Tripathi, S. N., & Zimmerman, M. (2016). Applications of Electrified Dust and Dust Devil Electrodynamics to Martian Atmospheric Electricity. Space Science Reviews, 203(1-4), 299-345. https://doi.org/10.1007/s11214-016- 0241-8 Publisher's PDF, also known as Version of record License (if available): CC BY Link to published version (if available): 10.1007/s11214-016-0241-8 Link to publication record in Explore Bristol Research PDF-document This is the final published version of the article (version of record). It first appeared online via Springer at https://doi.org/10.1007/s11214-016-0241-8 . Please refer to any applicable terms of use of the publisher. University of Bristol - Explore Bristol Research General rights This document is made available in accordance with publisher policies. Please cite only the published version using the reference above. Full terms of use are available: http://www.bristol.ac.uk/red/research-policy/pure/user-guides/ebr-terms/ Space Sci Rev (2016) 203:299–345 DOI 10.1007/s11214-016-0241-8 Applications of Electrified Dust and Dust Devil Electrodynamics to Martian Atmospheric Electricity R.G. Harrison1 · E. Barth2 · F. Esposito 3 · J. Merrison4 · F. Montmessin5 · K.L. Aplin6 · C. Borlina7 · J.J. Berthelier5 · G. Déprez5 · W.M. Farrell8 · I.M.P. Houghton6 · N.O. Renno7 · K.A. Nicoll1 · S.N. Tripathi9 · M. Zimmerman10 Received: 28 August 2015 / Accepted: 15 February 2016 / Published online: 12 April 2016 © The Author(s) 2016.