Computer Aided Safety Analysis 1989
Total Page:16
File Type:pdf, Size:1020Kb
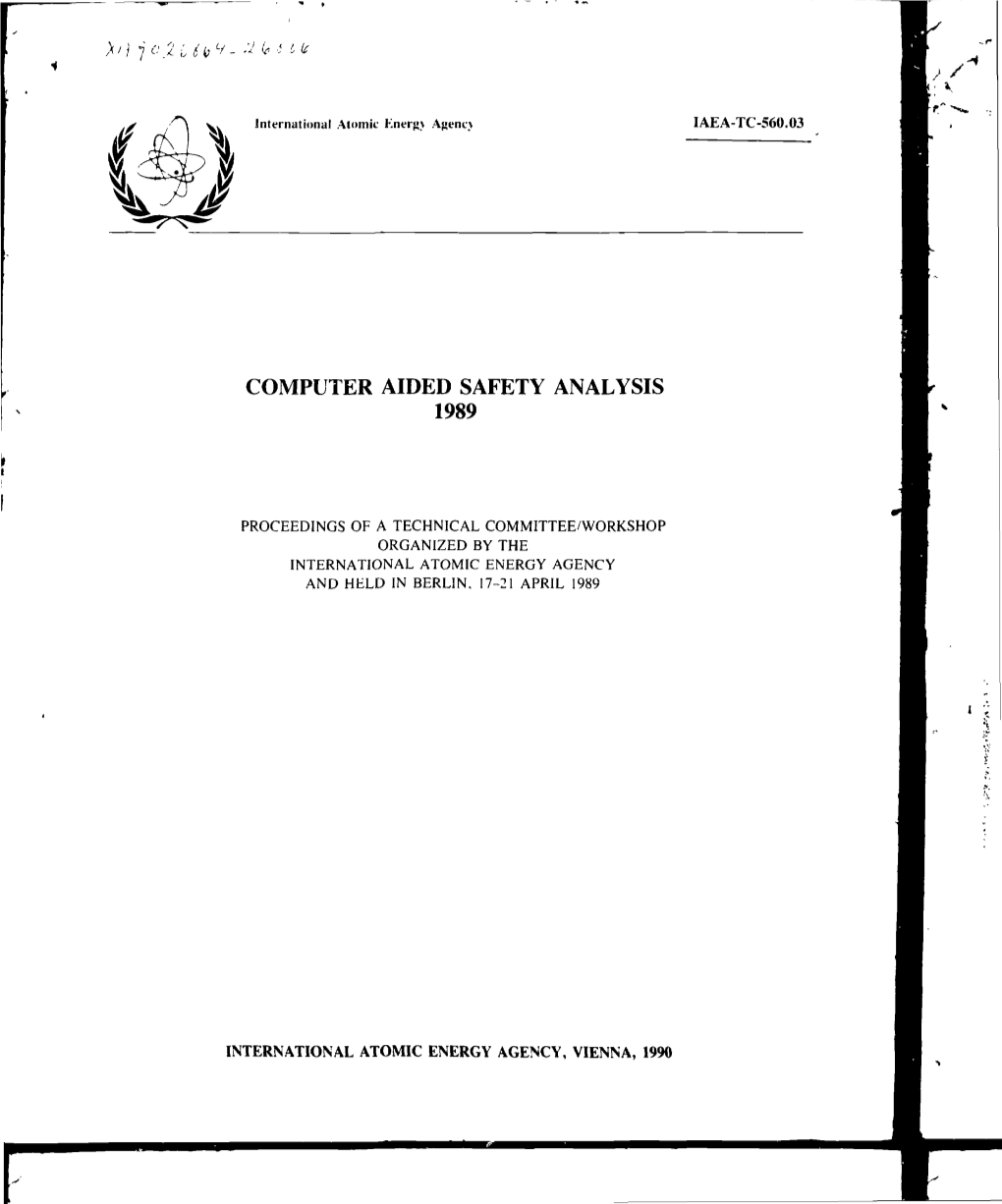
Load more
Recommended publications
-
From Meltdown to Showdown? Challenges and Options for Governance in the Arctic
PRIF-Report No. 113 From Meltdown to Showdown? Challenges and options for governance in the Arctic Christoph Humrich/Klaus Dieter Wolf Translation: Matthew Harris Peace Research Institute Frankfurt (PRIF) 2012 Correspondence to: PRIF (HSFK) Baseler Straße 27-31 60329 Frankfurt am Main Germany Telephone: +49(0)69 95 91 04-0 Fax: +49(0)69 55 84 81 E-mail: [email protected] [email protected] Internet: www.prif.org ISBN: 978-3-942532-41-9 Euro 10,– Summary Over the past few years the Arctic has become the object of intense political interest. Three interacting developments created this interest: first, climate change which is caus- ing the polar ice cap to melt is creating new opportunities and risks. While huge areas open up to resource development, this seems at the same time to also cause new geo- strategic confrontation. The second development is economic change. In Russia, Green- land, Norway and Alaska, economic well-being is highly dependent upon the exploitation of natural resources. Because on the one hand export revenues are rising for natural re- sources and on the other already developed sources further south have transgressed their exploitation peak, the economies of these countries drive them up North into the high Arctic. Thirdly, there has been legal change. The United Nations Convention on the Law of the Sea (UNCLOS) provides a legal framework for exploiting continental shelf re- sources. The Arctic states can and must assert their claims now. Contrary to all alarmist pronouncements, however, the process of delimiting the boundaries of the continental shelf is proceeding in a relatively orderly manner . -
The Next Big Thing in Esports
THE NEXT BIG THING IN ESPORTS eSports Experiences Home to Gamers, eSports Enthusiasts, and Amateur Teams around the World WHITE BOAR: MEDIA & TECHNOLOGY COMPANY White Boar’s Primary Business is that of an online media company curating professional eSports “Social” Network & supporting it with an ecosystem of tangible goods. Facebook is where you keep your photos. LinkedIn is where you keep your résumé. Tribe is where you keep your gaming stats, & eSports teams. Businesses Products include: Business ‒ eSports Community App ( Tribe ) Overview ‒ eSports Tournament Software ‒ eSports Ranking System ‒ eSports Restaurant Chain ( Meltdown) ‒ B2B Modular eSports Clusters/Gamer lounges For Restaurants, Hotels, Casinos, etc (AFK GG) ‒ Will be launching an ICO of our own Cryptocurrency Platforms Revenue Location Mobile Phones $5 million topline revenue in 2017, 27 Locations All Across Europe , Projected 20 million in 2018 HQ with 1 Location in San Jose, Web & Physical Tournaments Ca Live Events at our restaurants or other venues that purchase our eSports Clusters 2 Steven Wade brings 20 years of game industry experience to leading White Boar and it products. While forming White Boar Steve also serves as Managing Director/ Head of Woodside Capital Partners Gaming department where he focuses on M&A activities. Before joining WCP, Steven spent his career launching 45 online games, four gaming payment solutions, and eight game portals alongside Steven Wade many well-known entertainment companies such as Square Enix, VISA/Playspan, SOHU/Changyou, Ty Inc., and Aeria Games as an executive, and angel investor. Founder/Executive Chairman White Boar He is also an entrepreneur, creating and selling three companies: MMOsmart LLC ( to Aeria Games), Zyon Games Inc. -
Beyond Guernica and the Guggenheim
Beyond Guernica and the Guggenheim Beyond Art and Politics from a Comparative Perspective a Comparative from Art and Politics Beyond Guernica and the Guggenheim This book brings together experts from different fields of study, including sociology, anthropology, art history Art and Politics from a Comparative Perspective and art criticism to share their research and direct experience on the topic of art and politics. How art and politics relate with each other can be studied from numerous perspectives and standpoints. The book is structured according to three main themes: Part 1, on Valuing Art, broadly concerns the question of who, how and what value is given to art, and how this may change over time and circumstance, depending on the social and political situation and motivation of different interest groups. Part 2, on Artistic Political Engagement, reflects on another dimension of art and politics, that of how artists may be intentionally engaged with politics, either via their social and political status and/or through the kind of art they produce and how they frame it in terms of meaning. Part 3, on Exhibitions and Curating, focuses on yet another aspect of the relationship between art and politics: what gets exhibited, why, how, and with what political significance or consequence. A main focus is on the politics of art in the Basque Country, complemented by case studies and reflections from other parts of the world, both in the past and today. This book is unique by gathering a rich variety of different viewpoints and experiences, with artists, curators, art historians, sociologists and anthropologists talking to each other with sometimes quite different epistemological bases and methodological approaches. -
Event Date Venue City State Country Winner Name 6/4/2016
Event Date Venue City State Country Winner Name 6/4/2016 Spelletjescafe 2 Klaveren Amsterdam Netherlands IronDwarf 6/4/2016 Like Beer Дубна Московская обл Russia Hroman 6/4/2016 Hearthstone Café Олень Санкт-Петербург Russia Vitkan 6/4/2016 Rocket Labs Aalborg Denmark WhopperJones 6/4/2016 Planet A.s.d. San Donato Milanese Città Metropolitana di Milano Italy Vazh 6/4/2016 EMPIRE GAMES Sevilla Sevilla Spain JAVADABADU 6/5/2016 Молодежный центр "Зеркало" Красноярск Красноярский край Russia VoroG 6/9/2016 Zum Tanzenden Einhorn Hamburg Hamburg Germany Diesel 6/11/2016 The Wall Pub Pistoia Provincia di Pistoia Italy maulghak 6/11/2016 Bar "La Trainera" Bilbao Bizkaia Spain Wolfenair 6/11/2016 Свободное Пространство «ТИПИЧНЫЙ ПИТЕР» Санкт-Петербург Russia Goodwine 6/11/2016 Meltdown London London London United Kingdom Swifty 6/11/2016 Антикафе New York Coffee Ufa Respublika Bashkortostan Russia fthanthiz 6/11/2016 The Batcave Hillcrest Hillcrest South Africa KyubiZA 6/11/2016 Студия "Смена" Минск Belarus Tvist 6/11/2016 Lente&Sotron Bucarest Romania sleepwalkr 6/11/2016 Hearthstone Café Олень Санкт-Петербург Russia Tridevil 6/11/2016 L'Arcaneum Villeurbanne France Guntofire 6/12/2016 Антикафе "Коммуникатор" Екатеринбург Свердловская область Russia senn 6/12/2016 Hobby house "Фронтир" Красноярск Красноярский край Russia Admire 6/12/2016 Магазин-Клуб настольных игр "Лепрекон" Bryansk Bryanskaya oblast' Russia Melman 6/12/2016 Hex Café Kraków Kraków Kraków Poland Dziku 6/12/2016 Hex Wrocław Wrocław Wrocław Poland ZaQ 6/12/2016 Fireplace Москва Russia Truely 6/16/2016 ex casa del fascio Redondesco Provincia di Mantova Italy kiddarkness 6/18/2016 Defcon 2.0 Castellanza Provincia di Pavia Italy fish 6/18/2016 Małe Piwko Sopot Sopot Poland Savio 6/18/2016 Есть кальян Челябинск Челябинская область Russia pantsofluck 6/18/2016 Антикафе 12 комнат Санкт-Петербург Russia 6/18/2016 Dorfkrug Lübeck Germany Pieden 6/18/2016 Planet A.s.d. -
Exploring the Esports Environment
Exploring the eSports environment A marketing-oriented analysis of the biggest unnoticed sponsoring channel Alex Hanz Bachelor's thesis Degree Programme in Business Administration Turku 2020 BACHELOR’S THESIS Author: Alex Hanz Degree Programme: Business Administration Specialization: International Business Supervisor: Helena Nordström Title: Exploring the eSports environment _________________________________________________________________________ Date May 20,2020 Number of pages 53 Appendices 0 _________________________________________________________________________ Abstract Professional video gaming, or “eSports”, has evolved from a leisure activity for nerds to a billion-dollar sport with global reach. This change was unnoticed for years. Now brands are increasingly utilizing professional gaming as a marketing channel and encounter the different rules of gaming culture. The aim of this thesis is to provide a comprehensive overview of the current eSports market and its marketing operations for readers without previous knowledge of gaming. To do this, the thesis begins with an introduction to video games and eSports. The results of theoretical research work are presented in a stakeholder analysis to explain the eSports landscape. Afterwards, a discussion of the current revenue streams and composition of the marketing environment follows. The subsequent guidelines for successful promotion in this industry are supplemented by current examples of excellent campaigns. Supporting data was provided by empirical research in the form of an -
You've Seen the Movie, Now Play The
“YOU’VE SEEN THE MOVIE, NOW PLAY THE VIDEO GAME”: RECODING THE CINEMATIC IN DIGITAL MEDIA AND VIRTUAL CULTURE Stefan Hall A Dissertation Submitted to the Graduate College of Bowling Green State University in partial fulfillment of the requirements for the degree of DOCTOR OF PHILOSOPHY May 2011 Committee: Ronald Shields, Advisor Margaret M. Yacobucci Graduate Faculty Representative Donald Callen Lisa Alexander © 2011 Stefan Hall All Rights Reserved iii ABSTRACT Ronald Shields, Advisor Although seen as an emergent area of study, the history of video games shows that the medium has had a longevity that speaks to its status as a major cultural force, not only within American society but also globally. Much of video game production has been influenced by cinema, and perhaps nowhere is this seen more directly than in the topic of games based on movies. Functioning as franchise expansion, spaces for play, and story development, film-to-game translations have been a significant component of video game titles since the early days of the medium. As the technological possibilities of hardware development continued in both the film and video game industries, issues of media convergence and divergence between film and video games have grown in importance. This dissertation looks at the ways that this connection was established and has changed by looking at the relationship between film and video games in terms of economics, aesthetics, and narrative. Beginning in the 1970s, or roughly at the time of the second generation of home gaming consoles, and continuing to the release of the most recent consoles in 2005, it traces major areas of intersection between films and video games by identifying key titles and companies to consider both how and why the prevalence of video games has happened and continues to grow in power. -
From Le Court to Strasbourg
FFrroomm LLee CCoouurrtt ttoo SSttrraassbboouurrgg:: FFiigghhttiinngg ffoorr IInnddeeppeennddeenntt LLiivviinngg ffoorr 3300 yyeeaarrss AA ttrriibbuuttee ttoo JJoohhnn EEvvaannss OOBBEE CONTENTS Page Foreword by Ian Loynes .......................................................... 2 Introduction and acknowledgements ....................................... 3 Biography - John Evans .......................................................... 7 Reflections on John Evans and Project 81 ............................... 9 John Evans – A Personal Testimony ..................................... 13 Timeline of key events ........................................................... 14 ‘Project 81’ – Le Court and where it all began ....................... 15 On the origins of Independent Living in the UK ..................... 39 On Independent Living and Civil Rights ................................. 66 On the importance of Centres for Independent Living ............ 77 On the impact of Independent Living on government policy and legislation ............................................................. 81 On development of the Independent Living Movement .........100 On the impact of austerity on Disabled People and Independent Living ...............................................................109 On the European Parliament of Disabled People .................116 On being inducted into the ENIL Hall of Fame ......................117 On Independent Living in the UK in 2013 .............................122 On the Strasbourg Freedom Drive ........................................127 -
Research and Development with Regard to Severe Accidents in Pressurised Water Reactors: Summary and Outlook
Research and development with regard to severe accidents in pressurised water reactors: Summary and outlook Rapport IRSN-2007/83 Rapport CEA-2007/351 FOREWORD This report was produced conjointly by the French Institute for Radiological Protection and Nuclear Safety (IRSN) and the French Atomic Energy Commission (CEA). The French electric utility EDF also contributed to Section 8.2. The following individuals participated in writing or editing all or part of the report: For the IRSN: Ahmed Bentaïb, Hervé Bonneville, Cataldo Caroli, Bernard Chaumont, Bernard Clément, Michel Cranga, Florian Fichot, Joëlle Fleurot, Richard Gonzalez, Vincent Koundy, Bruno Laurent, Jean-Claude Micaelli, Renaud Meignen, Frédérique Pichereau, Delphine Plassart, Emmanuel Raimond, Anne Tenaud and Jean- Pierre Van-Dorsselaere. For the CEA: Gérard Ducros, Michel Durin, Christophe Journeau, Daniel Magallon, Jean-marie Seiler, Etienne Studer and Bruno Tourniaire. For EDF: William Ranval and EDF's Severe Accident Teams. CONTENTS CHAPTER 1 : INTRODUCTION .................................................................... 6 1.1 SEVERE ACCIDENTS — DEFINITION AND RESEARCH OBJECTIVES ...................................................... 6 1.2 RESEACH FRAMEWORK ................................................................................................ 7 1.3 REPORT OBJECTIVES .................................................................................................. 8 CHAPTER 2 : SCENARIOS .......................................................................10 -
Curriculum Vitae
Satoshi Utsunomiya, Ph. D. Associate Professor Department of Chemistry, Kyushu University 744 Motooka, Nishi-ku, Fukuoka-shi, 819-0395 JAPAN E-mail: [email protected], Phone&Fax: +81-92-802-4168 URL address: http://www.scc.kyushu-u.ac.jp/ircl/utu-e/index-e.htm EDUCATION Ph.D. Mineralogy, University of Tokyo, March, 2000 M.Sc. Mineralogy, University of Tokyo, March, 1997 B.S. Geology, University of Tokyo, March, 1995 PROFESSIONAL EXPERIENCE April, 2007 – Present Associate Professor at Department of Chemistry, Kyushu University November, 2004 – April, 2007 Assistant Research Scientist at Department of Geological Sciences, University of Michigan August, 2004 – November, 2004 Post-doctoral fellow at Department of Geological Sciences, University of Michigan March, 2004 – July, 2004 Senior research fellow at Department of Nuclear Engineering and Radiological Sciences, University of Michigan September, 2000 – March, 2004 Research fellow at Department of Nuclear Engineering and Radiological Sciences, University of Michigan MEMBERSHIP Mineralogical Society of America (MSA), Geological Society of America (GSA), Japan Association of Mineralogical Sciences, TEACHING EXPERIENCE University of Tokyo; Teaching Assistant for Low-Temperature Geochemistry University of Michigan; GS455 Laboratory Course Kyushu University; Basic Inorganic Materials Chemistry, Radiochemistry I, Basics of Transmission Electron Microscopy, Modern Chemistry, Analytical Chemistry IV, Basic Natural Science Laboratory Course, Inorganic Chemistry Laboratory Course, LANGUAGE SKILL Japanese and English INVITED TALK Ochiai A., Imoto J., Furuki G., Ikehara R., Suetake M., Yamasaki S., Ohnuki T., Law G.T.W., Grambow B., Ewing R.C., and Utsunomiya S. (2018) Nuclear Fuel Fragments Released from the Fukushima Daiichi Nuclear Power Plant. August 19 – 23, 2018, 256th ACS National Meeting, Boston MA, United States. -
Event Date Venue City Country Winner Name 6/4/2016
Event Date Venue City Country Winner Name 6/4/2016 Spelletjescafe 2 Klaveren Amsterdam Netherlands IronDwarf 6/4/2016 Like Beer Дубна Russia Hroman 6/4/2016 Hearthstone Café Олень Санкт-Петербург Russia Vitkan 6/4/2016 Rocket Labs Aalborg Denmark WhopperJones 6/4/2016 Planet A.s.d. San Donato Milanese Italy Vazh 6/4/2016 EMPIRE GAMES Sevilla Spain JAVADABADU 6/5/2016 Молодежный центр "Зеркало" Красноярск Russia VoroG 6/9/2016 Zum Tanzenden Einhorn Hamburg Germany Diesel 6/11/2016 The Wall Pub Pistoia Italy maulghak 6/11/2016 Bar "La Trainera" Bilbao Spain Wolfenair 6/11/2016 Свободное Пространство «ТИПИЧНЫЙ ПИТЕР» Санкт-Петербург Russia Goodwine 6/11/2016 Meltdown London London United Kingdom Swifty 6/11/2016 Антикафе New York Coffee Ufa Russia fthanthiz 6/11/2016 The Batcave Hillcrest Hillcrest South Africa KyubiZA 6/11/2016 Студия "Смена" Минск Belarus Tvist 6/11/2016 Lente&Sotron Bucarest Romania sleepwalkr 6/11/2016 Hearthstone Café Олень Санкт-Петербург Russia Tridevil 6/11/2016 L'Arcaneum Villeurbanne France Guntofire 6/12/2016 Антикафе "Коммуникатор" Екатеринбург Russia senn 6/12/2016 Hobby house "Фронтир" Красноярск Russia Admire 6/12/2016 Магазин-Клуб настольных игр "Лепрекон" Bryansk Russia Melman 6/12/2016 Hex Café Kraków Kraków Poland Dziku 6/12/2016 Hex Wrocław Wrocław Poland ZaQ 6/12/2016 BrownBar Москва Russia Truely 6/16/2016 ex casa del fascio Redondesco Italy kiddarkness 6/18/2016 Defcon 2.0 Castellanza Italy fish 6/18/2016 Małe Piwko Sopot Poland 6/18/2016 Есть кальян Челябинск Russia pantsofluck 6/18/2016 Антикафе 12 комнат Санкт-Петербург Russia 6/18/2016 Dorfkrug Lübeck Germany 6/18/2016 Planet A.s.d. -
5/5 GG Pub Kazan Russia Reported Skyk 5/5 Ciber
Date Venue City Country Status Winner(s) 5/5 GG Pub Kazan Russia Reported Skyk 5/5 Ciber Jarchi Spain Unreported 5/5 Assumption College Worcester, MA United States Unreported 5/5 Residencia Universitaria Gabriela Mistral Antofagasta Chile Reported machine 5/6 FABRIKA Kherson Ukraine Reported Wizard 5/7 Seward County Community College Liberal, KS United States Unreported 5/7 BIZO Baia Mare Romania Unreported 5/8 ELTE Lagymanyosi Campus Budapest Hungary Reported Melkon Quincy Biokit68 5/8 Omega Comics Asuncion Paraguay Reported koveras 5/8 Universitat Politècnica de Catalunya Terrassa Spain Reported SrColmenero 5/8 CSU Computer Science Building Fort Collins, CO United States Unreported 5/9 ManaBreak Gaming Café Beja Portugal Unreported 5/9 Insomnia Video Game Culture Houston, TX United States Reported OneThreeFour 5/9 Bioskop Kupina Nis Serbia Unreported 5/9 Romexpo Exhibition Center Bucharest Romania Reported EQm paulhau2002 Quagger Adam Bogdansky Darkthorn Raziel 5/9 Restaurant zum goldenem Tor Kloten Switzerland Reported Helder Tael Founduecn 5/9 Centro Comercial Arenales Lima Peru Reported botellita 5/9 Moonleaf Tea Shop Los Baños Philippines Reported ellite 5/9 A Store of Fire and Dice Lynbrooke, NY United States Unreported 5/9 Da-Planet Honolulu, HI United States Reported Aruigus808 5/9 Asociacion El Pacto de las Janas Leon Spain Reported Eored 5/9 Revisteria Nippur Ciudad del Este Paraguay Reported Gridor 5/9 Meltdown London London United Kingdom Reported swifty avjuggernaut slightlymike swayno5 5/9 Dark Side Gaming Lounge Long Beach, -
Supporting Young People in Europe Looking to the Future
SUPPORTING YOUNG PEOPLE IN EUROPE The Council of Europe’s 21 international reviews of national youth policy have, over 20 years, produced a significant body LOOKING TO THE FUTURE of knowledge and a respected, innovative methodology. They have considerably enhanced the understanding and the development of “youth policy” throughout Europe. Following the first seven international reviews, a synthesis report was produced that endeavoured to construct a framework for understanding youth policy. A similar synthesis exercise took place after a further seven international reviews, reflecting both on the evolving process of carrying out the reviews and on new themes and issues for youth policy that had not emerged within the initial framework. This book, the third concerned with supporting young people in Europe, is a synthesis of the last seven international reviews, coupled with an overview of the learning that has accrued from all 21 international reviews. It draws together some of the conclusions and challenges that have emerged over two decades and considers some lessons for the future, not least alternative models of engagement in the youth field between the Council of Europe and its member states. PREMS 040817 ENG The Council of Europe is the continent’s leading Howard Williamson Substantive issues, methodological VOLUME III human rights organisation. It comprises 47 member lessons, support measures states, 28 of which are members of the European and youth policy standards: Union. All Council of Europe member states have a reflection on the “third seven” www.coe.int signed up to the European Convention on Human Rights, a treaty designed to protect human rights, Council of Europe democracy and the rule of law.