SAFETY and ENFORCEMENT DIVISION California Public Utilities Commission
Total Page:16
File Type:pdf, Size:1020Kb
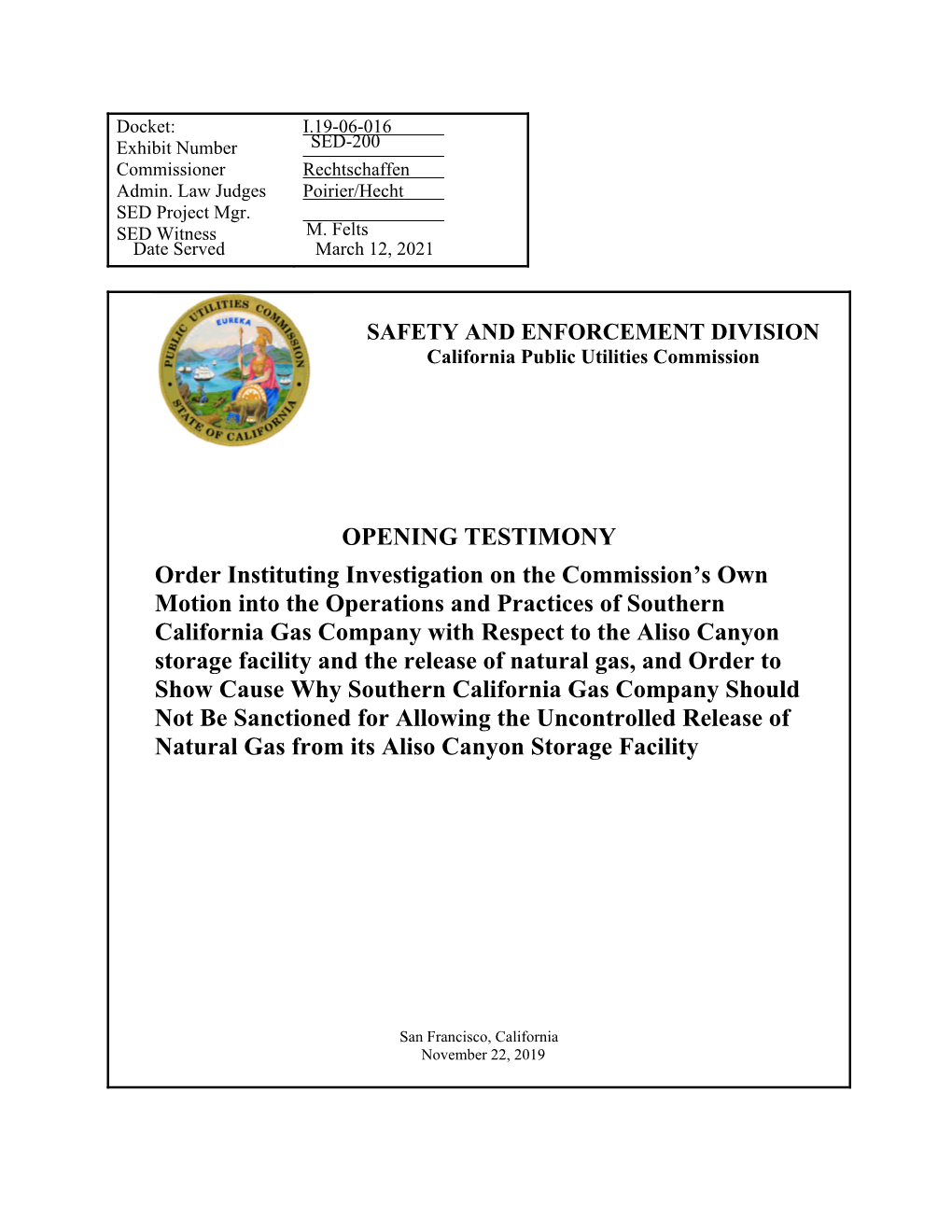
Load more
Recommended publications
-
Wellcap® IADC WELL CONTROL ACCREDITATION PROGRAM WELL SERVICING OPERATIONS – SNUBBING CORE CURRICULUM and RELATED JOB SKILLS
WellCAP® IADC WELL CONTROL ACCREDITATION PROGRAM WELL SERVICING OPERATIONS – SNUBBING CORE CURRICULUM AND RELATED JOB SKILLS FORM WCT-2SS SUPERVISORY LEVEL The purpose of the core curriculum is to identify a body of knowledge and a set of job skills that can be used to provide well control skills for well servicing operations. The curriculum is divided into three certification types: Coiled Tubing, Snubbing, and Wireline (Wireline is presented in document WCT – 2WSW) and within each certification, three levels: Introductory, Fundamental, and Supervisory. Students may complete an individual certification (e.g., Coiled Tubing) or combination certifications (e.g., Coiled Tubing and Snubbing). All knowledge and skills for each individual certification must be addressed when combining certifications. The suggested target students for each core curriculum level are as follows: INTRODUCTORY: New Hires (May also be appropriate for non-technical personnel) FUNDAMENTAL: Helpers, Assistants, “Hands” involved with the operational aspects of the unit and who may act/operate the unit under direct supervision of a certified Unit Operator or Supervisor. SUPERVISORY: Unit Operators, Supervisors, Superintendents, and Project Foreman Upon completion of a well control training course based on curriculum guidelines, the student should be able to perform the job skills in italics identified by a "!" mark (e.g., ! Identify causes of kicks). Form WCT-2SS WellCAP Curriculum Guidelines – Well Servicing - Snubbing Revision 040416 Supervisory Page 1 CORE CURRICULUM -
Ultra-Deepwater Advisory Committee (UDAC) Risk Assessment Technical Support
(U N C L A S S I F I E D ROUGH DRAFT FOR DISCUSSION PURPOSE ONLY) Risk Informed Decision Support for UDW Drilling Ultra-Deepwater Advisory Committee (UDAC) Risk Assessment Technical Support Dasari V. Rao, Division Leader, Decision Applications Division Chris Smith and Elena Melchert, DOE Program Oversight (U N C L A S S I F I E D) Operated by the Los Alamos National Security, LLC for the DOE/NNSA Summary of LANL AnalysesU N C L A S S I F I E D Status update and a review of preliminary findings • Over the past three decades there has been a steady decrease in ‘major’ kick frequency; more recently, frequency is about 1 in 10 wells. A majority of the kicks occur in the shallower regions where the primary hazard is the release of natural gas, some condensates and synthetic mud to the environs. A small fraction (1 in 100 wells) kick while drilling and cementing in the target region where oil and other condensates present blowout hazard. • Ultra-deep water formations stratigraphy and reservoir properties are significantly different compared to previous operational experience. • Our modeling efforts included development of accident progression event trees that enumerated an exhaustive list of possible accident sequences; barrier analyses that quantified reliability of each barrier; and physics-based well dynamics models that explicitly captured timing of events. We have used a generic well design and well operations that are consistent with IADC and API guidance. • Important barriers in place to mitigate a kick (e.g., Lower Marine Riser connection (LMRP), Blowout Preventer (BOP) and Drill Pipe Safety Valves) are vulnerable to control system and design deficiencies. -
Manufacturer Annular BOP: Choke and Kill Valves: Wellhead Connector
Rig Name: Equipment Owner: The purchaser or renter of the equipment to be installed onto the Equipment User: The company that owns the well, wellhead or wellhead assembli Name: Person(s) Completing Name: Document: Name: Name: Time to Complete Document (hours): Number of Shear Rams: Number of Sealing Shear Rams: Test Ram Installed: BOP Classification Size Manufacturer Ram Type BOP: Annular BOP: Choke and Kill Valves: Wellhead Connector: LMRP Connector: Choke Manifold: e wellhead or wellhead assemblies. ies on which the equipment is to be installed. Title: Title: Title: Title: Press. Rating Model 1 Scope 1.1 Purpose 1.1.1 The purpose of this standard is to provide requirements on the installation and testing of blowout prevention equipment systems on land and marine drilling rigs (barge, platform, bottom-supported, and floating). Blowout preventer equipment systems are comprised of a combination of various components. The following components are required for operation under varying rig and well conditions: a) blowout preventers (BOPs); b) choke and kill lines; 1.1.2 c) choke manifolds; d) control systems; e) auxiliary equipment. 1.1.3 The primary functions of these systems are to confine well fluids to the wellbore, provide means to add fluid to the wellbore, and allow controlled volumes to be removed from the wellbore. Diverters, shut-in devices, and rotating head systems (rotating control devices) are not addressed in this standard (see API 64 and API 16RCD, respectively); their primary purpose is to safely divert or direct flow rather than to confine fluids to the 1.1.4 wellbore. 1.2 Well Control 1.2 Procedures and techniques for well control are not included in this standard since they are beyond the scope of equipment systems contained herein. -
Oil and Gas Operator Representative Workover and Intervention Well Control
Oil and Gas Operator Representative Workover and Intervention Well Control Curriculum, Course Delivery Requirements, and Related Learning Objectives Form WSP-02-WS-OGO Revision 0 27 September 2017 © IADC 2017 COPYRIGHT PROTECTED DOCUMENT All rights reserved. No part of this document may be distributed outside of the recipient’s organization unless authorized by the International Association of Drilling Contractors. Related Learning Objectives for WellSharp® Oil and Gas Operator Representative-Workover/Intervention Well Control Contents 1.0 Oil and Gas Operator Representative Course Overview........................................................................................................................................ 3 2.0 Curriculum .............................................................................................................................................................................................................. 5 2.1 Risk Awareness and Management ................................................................................................................................................................. 5 2.2 Organizing a Well Control Operation ............................................................................................................................................................. 7 2.3 Well Control Principles & Calculations ........................................................................................................................................................... 7 2.4 -
Wild Well Global Services Brief
GLOBAL SERVICES BRIEF 2021 wildwell.com V. 04 LOCATIONS Corporate Office Drilling Technology Center 2202 Oil Center Court Houston, Texas 77073 USA Regional Response Locations UNITED STATES Houston, Texas Odessa, Texas Greeley, Colorado Roaring Branch, Pennsylvania INTERNATIONAL Aberdeen, Scotland Dammam, Kingdom of Saudi Arabia Dubai, UAE Kuala Lumpur, Malaysia Port Harcourt, Nigeria Stavanger, Norway Singapore Well Control Training Centers UNITED STATES Houston, Texas Corpus Christi, Texas Odessa, Texas Tyler, Texas Lafayette, Louisiana Oklahoma City, Oklahoma Casper, Wyoming Williston, North Dakota Canonsburg, Pennsylvania Global Services Brief +1.281.784.4700 // wildwell.com TABLE OF CONTENTS Corporate Overview ..................................................................1 Forensic Studies .....................................................................12 Emergency Response Services ............................................5 Design to Industry Standards ..................................................12 Blowout & Well Control Response ............................................5 Fitness for Purpose Assessment .............................................12 Pressure Control ......................................................................5 Risk Management Services ................................................13 Well Control Engineering Services .......................................6 Well Control Emergency Response Plans ................................13 Blowout Rate Modeling (Worst Case Discharge Analysis) -
Dynamic Kill of Underground Blowouts
DYNAMIC KILL OF UNDERGROUND BLOWOUTS ALVARO F. NEGRÃO, PETROBRAS VICTOR GERARDO VALLEJO-ARRIETA, PEMEX ADAM T. BOURGOYNE, JR. LSU JOHN ROGERS SMITH, LSU Table of Contents Non - Newtonian Kill Fluids ................................................. 47 EXECUTIVE SUMMARY ............................... 3 Reservoir Model..................................................................... 53 Formation Fluid Rate Determination.................................... 54 Global Solution Scheme......................................................... 56 INTRODUCTION ............................................ 4 CONCLUSIONS......................................................................... 67 NOMENCLATURE ................................................................... 67 CONCEPT................................................................................... 4 SUMMARY ................................................................................. 8 STEADY-STATE DYNAMIC KILL COMPUTER MODEL FOR DYNAMIC KILL COMPUTER PROGRAM ............................. 71 OF AN UNDERGROUND BLOWOUT COMPUTER PROGRAM IMPLEMENTING THE CONSIDERING FRACTURE PROCEDURE............................................................................. 71 PROPAGATION ............................................. 9 Work Sheet Descriptions...................................................... 71 Input Data................................................................................ 73 INTRODUCTION....................................................................... -
An Introduction to Well Integrity Rev 0, 04 December 2012
An Introduction to Well Integrity Rev 0, 04 December 2012 0 Preface This document has been prepared as a joint project between members of the Norwegian Oil and Gas Association's Well Integrity Forum (WIF) and professors at NTNU and UiS. The intention with the document is to provide a document that can be used in educating personnel in well integrity and especially students at the universities. Authors of this document have been: Hans-Emil Bensnes Torbergsen, Eni Norge Hilde Brandanger Haga, Statoil Sigbjørn Sangesland, NTNU Bernt Sigve Aadnøy, UiS Jan Sæby, Shell Ståle Johnsen, Total Marvin Rausand, NTNU Mary Ann Lundeteigen NTNU 0 04.12.12 Original document Revision Date of issue Reason for Issue 1 Index Preface ................................................................................................................................................ 1 List of Abbreviations ................................................................................................................................ 6 List of figures ............................................................................................................................................ 1 List of Tables ............................................................................................................................................ 4 1. What is well integrity? (Well integrity – concepts and terminology) ........................................... 5 2. Background and History .................................................................................................................. -
Surface Well Test Equipment
Surface well test equipment A unique combination of well testing solutions and aftermarket support About NOV National Oilwell Varco (NOV) is a worldwide leader in the design, manufacture and sale of equipment and components used in oil and gas drilling and production operations and the provision of oilfield services to the upstream oil and gas industry. Through our broad capabilities and vision, our family of companies is positioned and ready to serve the needs of this challenging, evolving industry. We have the technical expertise, advanced equipment and readily available support necessary for our customers’ success. NOV Completion & Production Solutions NOV Completion & Production Solutions integrates technologies for well completions and oil and gas production. We design, manufacture and sell equipment and technologies needed for well stimulation, well intervention and artificial lift systems. In addition, we focus on offshore production with floating production systems and subsea production technologies. In every type of environment, we bring together engineering operational expertise and field-proven solutions with a foundation of safety and risk management that helps you control costs and achieve lasting success. Intervention and Stimulation Equipment (ISE) Our engineering, manufacturing and service expertise delivers field-proven solutions that help you control costs, increase service value and achieve success. We partner with you to address your operational challenges and apply extensive research, testing, state-of-the-art engineering and manufacturing to deliver the field-proven equipment and performance you demand. It isn’t often that you find everything you are looking for in one place. At the Intervention and Stimulation Equipment (ISE) business unit of NOV, we combine years of experience with trusted brand names to deliver complete solutions that maximize efficiency, improve your service value and increase your bottom line. -
Development and Assessment of Well Control Procedures for Extended Reach and Multilateral Wells Utilizing Computer Simulation
Devel opment and Assessment of Well Control Procedures for Extended Reach and Multilateral Wells Utilizing Computer Simulation by Dr. Jerome J. Schubert, Texas A&M University Dr. Jonggeun Choe, Seoul National University, Korea Mr. Bjorn Gjorv, Texas A&M University Mr. Max Long, Texas A&M University Final Project Report Prepared for the Minerals Management Service Under the MMS/OTRC Cooperative Research Agreement 1435-01-99-CA-31003 Task Order 85222 Project Number 440 December 2004 OTRC Library Number: 12/04-A146 “The views and conclusions contained in this document are those of the authors and should not be interpreted as represent ing the opinions or policies of the U.S. Government. Mention of trade names or commercial products does not constitute their endorsement by the U. S. Government”. For more information contact: Offshore Technology Research Center Texas A&M University 1200 Mariner Drive College Station, Texas 77845-3400 (979) 845-6000 or Offshore Technology Research Center The University of Texas at Austin 1 University Station C3700 Austin, Texas 78712-0318 (512) 471-6989 A National Science Foundation Graduated Engineering Research Center DEVELOPMENT AND ASSESSMENT OF WELL CONTROL PROCEDURES FOR EXTENDED REACH AND MULTILATERAL WELLS UTILIZING COMPUTER SIMULATION EXECUTIVE SUMMARY Project Description This project included four tasks. Task 1 - Perform a literature search of the state of the art in well control for vertical, directional, horizontal, extended reach, and multi-lateral wells. Task 2 - Modify an existing Windows-based well control simulator that has been developed by Dr. Jonggeun Choe for use in more conventional wellbores to model extended reach and multilateral wells. -
Service Company Equipment Operator Snubbing Well Control
Service Company Equipment Operator Snubbing Well Control Curriculum, Course Delivery Requirements, and Related Learning Objectives Form WSP-02-WS-SN-EO Revision 0 17 August 2017 © IADC 2017 COPYRIGHT PROTECTED DOCUMENT All rights reserved. No part of this document may be distributed outside of the recipient’s organization unless authorized by the International Association of Drilling Contractors. WellSharp® Service Company Equipment Operator Snubbing Well Control Contents 1.0 Overview of Service Company Equipment Operator Snubbing Well Control ........................................................................................................ 3 2.0 Curriculum .............................................................................................................................................................................................................. 5 2.1 Risk Awareness and Management ................................................................................................................................................................. 5 2.2 Well Control Principles & Calculations ........................................................................................................................................................... 6 2.3 Barriers ......................................................................................................................................................................................................... 10 2.4 Influx Fundamentals.................................................................................................................................................................................... -
NORSOK STANDARD D-010 Well Integrity in Drilling and Well Operations
NORSOK STANDARD D-010 Rev. 3, August 2004 Well integrity in drilling and well operations This NORSOK standard is developed with broad petroleum industry participation by interested parties in the Norwegian petroleum industry and is owned by the Norwegian petroleum industry represented by The Norwegian Oil Industry Association (OLF) and Federation of Norwegian Manufacturing Industries (TBL). Please note that whilst every effort has been made to ensure the accuracy of this NORSOK standard, neither OLF nor TBL or any of their members will assume liability for any use thereof. Standards Norway is responsible for the administration and publication of this NORSOK standard. Standards Norway Telephone: + 47 67 83 86 00 Strandveien 18, P.O. Box 242 Fax: + 47 67 83 86 01 N-1326 Lysaker Email: [email protected] NORWAY Website: www.standard.no/petroleum Copyrights reserved NORSOK Standard D-010 Rev 3, August 2004 Foreword 4 Introduction 4 1 Scope 6 2 Normative and informative references 6 2.1 Normative references 6 2.2 Informative references 7 3 Terms, definitions and abbreviations 7 3.1 Terms and definitions 8 3.2 Abbreviations 12 4 General principles 13 4.1 General 13 4.2 Well barriers 13 4.3 Well design 19 4.4 Risk assessment and risk verification methods 20 4.5 Simultaneous and critical activities 20 4.6 Activity and operation shut-down criteria 21 4.7 Activity programmes and procedures 22 4.8 Contingency plans 24 4.9 Personnel competence and supervision 24 4.10 Experience transfer and reporting 25 5 Drilling activities 26 5.1 General 26 -
WCS-BROCHURE.Pdf
ABOUT US Well Control School (WCS) is a leading provider of accredited well control training. Since our inception in 1979, we have trained over 85,000 students globally through our training centers and proprietary System 21 e-Learning program. Our approach to ensuring positive student engagement is to deliver the latest standards and methodologies using expert knowledge, case studies and realistic, hands-on simulations to help adult learners navigate everyday oilfield situations successfully. Since our founding, we have been at the forefront of developing well control standards in support of competency- based training and enhanced personnel safety. Our organization collaborated with the United States Minerals Management Systems (now BOEM and BSEE) to develop the well control training section of the standard known currently as “Subpart O”. As a result, we launched the Well Control School Accreditation Program, a curriculum- based training standard that provides oil and gas training for drilling, well control and well servicing operations, and complies with IOGP 476 standards and US Bureau of Safety and Environmental Enforcement (BSEE) Subpart O (30 CFR Part 250.1504). For more information, visit www.wellcontrol.com. ACCREDITATIONS AND ASSOCIATION MEMBERSHIPS • The Well Control School Accreditation • International Standard ISO 9001 (ISO) • International Well Control Forum (IWCF) • International Coiled Tubing Association (ICoTA) • International Association of Drilling Contractors (IADC) • Society of Petroleum Engineers (SPE) • Association of Energy Services Companies (AESC) REGISTRATION Instructor-led and System 21 e-learning courses are offered at three training centers in Houston, Texas; Lafayette, Louisiana and Laurel, Mississippi. For instructor-led and computer-based courses: Web: www.wellcontrol.com For System 21 e-Learning web-based courses: Phone: 1.713.849.7400 Web: www.wcsonlineuniversity.com e-Mail: [email protected] e-Mail: [email protected] Instructor-led classes begin at 7:00 a.m.