CPRR "Buffalo" Ten-Wheeler
Total Page:16
File Type:pdf, Size:1020Kb
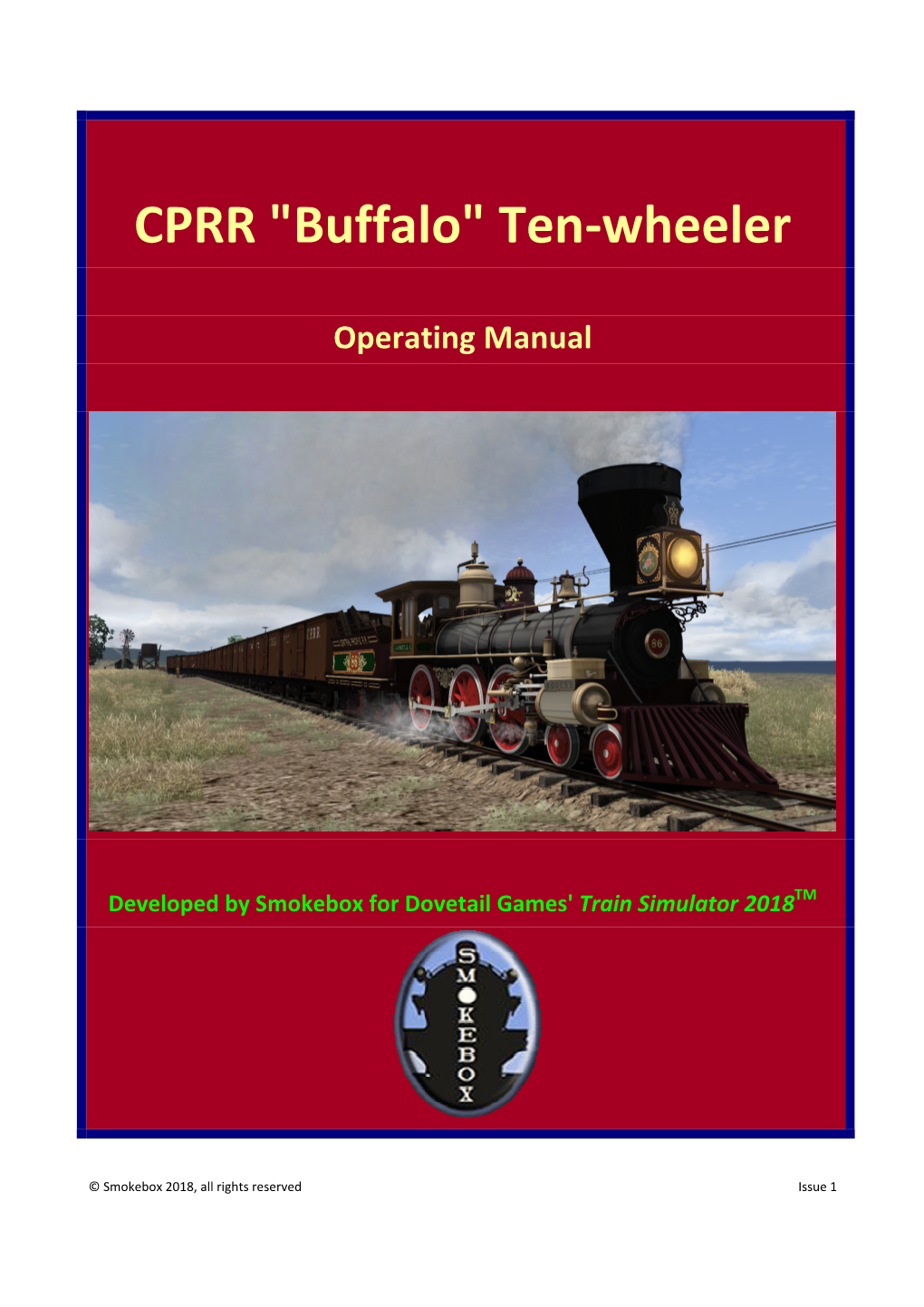
Load more
Recommended publications
-
Walschaerts Valve-Gear 2 Return Cranks with Steel Screws & Nuts
This pack contains the following parts: - Walschaerts Valve-Gear 2 Return Cranks with steel screws & nuts. 2 Expansion links with bushes & This kit contains parts to construct 2BA nuts. a set of Walschaerts type valve- 2 Lifting arms with grub screws & Allen key. gear as used on ROUNDHOUSE 2 Lifting links. locomotives. It is of a simplified 4 M2 steel screws & nuts. design, which does not use a 6 5BA steel washers. combination lever and is intended 2 Radius rods. for use with the ROUNDHOUSE 2 Weigh shaft brackets 1 Weigh shaft. Cylinder set. 2 Starlock washers 2 Roll pins. NOTE:- Frames, Cylinders, 6 Short crank pins. Coupling Rods, Connecting Rods, 2 Plain crank pins Axles and Outside Cranks are not included with this set of parts. 1 Push Rod Connector, Screw & Starlock. 1 Stainless Steel spring & Long Crank Pin. 1 Reversing lever handle. 1 Reversing lever base. 3 M2 screws and nuts. 2 M3 mounting screws. 1 Steel push rod & quicklink connector. Roundhouse Engineering Co. Ltd 2 Eccentric rods. Units 6 to 9, Churchill Business Park, Churchill Road, Wheatley, Doncaster. DN1 2TF. England. Tel 01302 328035 Fax 01302 761312 Email: [email protected] www.roundhouse-eng.com 1 Walschaerts Valve-Gear Part Number WVG Assembly of Walschaerts type valve-gear 1). Radius Rod. 2). Lifting Link. 3). Lifting Arm. Diagram4). Expansion showing Linkgeneral Bush. arrangement 5). Weigh of Walschaerts Shaft Bracket valve (Penguin). gear. NOTE:- Frames, Coupling rods, connecting rods and outside cranks are not included6). Weigh with this Shaft. set of 7). parts. Starlock Washer. 8). 2BA Nut. -
Subject: Supplement to Upper Engine and Fuel Injector Cleaner Label Models: All GM Vehicles Equipped with a Gasoline Engine
7/11/2018 #PIP4753: Supplement To Upper Engine And Fuel Injector Cleaner Label - (Dec 11, 2009) • 2003 GMC Truck Yukon 4WD • MotoLogic 2003 Yukon 4WD Report a problem with this article Subject: Supplement to Upper Engine and Fuel Injector Cleaner Label All GM Vehicles Models: Equipped with a Gasoline Engine The following diagnosis might be helpful if the vehicle exhibits the symptom(s) described in this PI. Condition/Concern: Some service procedures, service bulletins, or PIs may advise to decarbon the engine with GM Upper Engine and Fuel Injector Cleaner to remove valve deposits but the label that is on the back of the bottle does not include any instructions that explain how to use the cleaner. Recommendation/Instructions: If a service procedure, service bulletin, or PI does not include decarboning instructions and the GM Vehicle Care 3 Step Induction Cleaning Kit (E-957-001) is not available, the guidelines below supplement the label and explain how the cleaner can be used to clean the intake valves: Important: Extreme care must be taken not to hydrolock the engine when inducing the cleaner. If too much cleaner is induced at too low of a RPM, or if you force the engine to stall by inducing too much cleaner at once, the engine may hydrolock and bend a connecting rod(s). 1. In a well-ventillated area with the engine at operating temperature, slowly/carefully induce a bottle of GM Upper Engine and Fuel Injection Cleaner into the engine with RPM off of idle enough to prevent it from stalling (typically around 2,000 RPM or so). -
QUIZ: Boiler System Components
9707 Key West Avenue, Suite 100 Rockville, MD 20850 Phone: 301-740-1421 Fax: 301-990-9771 E-Mail: [email protected] Part of the recertification process is to obtain Continuing Education Units (CEUs). One way to do that is to review a technical article and complete a short quiz. Scoring an 80% or better will grant you 0.5 CEUs. You need 25 CEUs over a 5-year period to be recertified. The quiz and article are posted below. Completed tests can be faxed (301-990-9771) or mailed (9707 Key West Avenue, Suite 100, Rockville, MD 20850) to AWT. Quizzes will be scored within 2 weeks of their receipt and you will be notified of the results. Name: ______________________________________________ Company: ___________________________________________ Address: ____________________________________________ City: ______________________ State: _____ Zip: ________ Phone: ______________________ Fax: __________________ E-mail: _____________________________________________ Boiler Systems – Boiler Components By Irvin J. Cotton, Arthur Freedman Associates, Inc. and Orin Hollander, Holland Technologies, Inc. This is part two of a three-part series on boilers. In part one, the authors discussed boiler design and classification. Part two will discuss boiler components, and part three will describe the various chemistries used in boiler water treatment. Boiler Components The main components in a boiler system are the boiler feedwater heaters, deaerator, boiler, feed pump, economizer, boiler, superheater, attemperator, steam system, condenser and the condensate pump. In addition there are sets of controls to monitor water and steam flow, fuel flow, airflow and chemical treatment additions. Water sample points may exist at a number of places. Most typically the condensate, deaerator outlet, feedwater (often the economizer inlet), boiler, saturated steam and superheated steam will have sample points. -
Swampʼs Diesel Performance Tips to Help Remove and Install Power
Injectors-Chips-Clutches-Transmissions-Turbos-Engines-Fuel Systems Swampʼs Diesel Performance Competition Parts For Your Diesel 304-A Sand Hill Rd. La Vergne, TN 37086 Tel 615-793-5573 or (866) 595-8724/ Fax 615-793-5572 Email: [email protected] Tips to help remove and install Power Stroke injectors. Removal: After removing the valve covers and the valve cover gaskets, but before removing any injectors, drain the oil rails by removing the drain plugs inside the valve cover. On 94-97 trucks theyʼre just under where the electrical connectors are on the gasket. These plugs are very tight; give them a sharp blow with a hammer and punch to help break them loose, then use a 1/8" Allen wrench. The oil will drain out into the valve train area and from there into the crankcase. Donʼt drop the plugs down the push rod holes! Also remove one of the plugs on top of each oil rail, (beside where the lines from the High Pressure Oil Pump enter) for a vent to allow air to enter so the oil can drain. The plugs are 5/8”. Inspect the plug O-rings and replace if necessary. If the plugs under the covers leak, it will cause a substantial loss of performance. When removing the injectors, oil and fuel from the passages in the cylinder head drains down through the injector bore into the cylinders. If not removed, this can hydro-lock the engine when cranking. There is a ~40cc dish in the center of each piston. Fluid accumulates in it, as well as in the corner on the outside of the piston between the piston top and the cylinder wall, due to the 45* slope of the cylinder bank. -
The Mikado Messenger | Issue No. 66| April 2020 Ian Matthews Sanding the Filler, on the Tender Tank, Before It Is Painted
The Mikado Messenger | Issue No. 66| April 2020 Ian Matthews sanding the filler, on the tender tank, before it is painted - A1SLT Welcome to edition No. 66 of The Mikado Messenger, our monthly eNewsletter which aims to provide a regular progress update on the construction of new Gresley class No. 2007 Prince of Wales. Thanks to our supporters’ continued generosity, over £3.5m has now been donated or pledged – this equates to over 70% of the required £5m. This month see the launch of a brand new club - The Pony (Truck) Club - please see below for more information. Stephenson Engineering Ltd have sent us a fabulous video of the CNC machining programme that will be carried out on the coupling rods - it can be found in the Motion Update section, below. We are following Government guidelines with regards to the coronavirus, and whilst our office-based staff are now working from home, our workshop staff are continuing to work at Darlington Locomotive Works where they are taking all necessary precautions. However, as many of our supporters and volunteers are from vulnerable groups, the Works is currently closed to non-essential staff. In addition, Nene Valley Railway have cancelled all their events until the end of May 2020 so this means we can no longer hold the P2 Roadshow on Saturday 23rd May 2020 and the Supporters’ and Tornado Team day on Sunday 24th May 2020. We are sorry to have to make these changes. We hope you understand that the circumstances are beyond our control and the restrictions are very necessary at this challenging time. -
BACKTRACK 22-1 2008:Layout 1 21/11/07 14:14 Page 1
BACKTRACK 22-1 2008:Layout 1 21/11/07 14:14 Page 1 BRITAIN‘S LEADING HISTORICAL RAILWAY JOURNAL VOLUME 22 • NUMBER 1 • JANUARY 2008 • £3.60 IN THIS ISSUE 150 YEARS OF THE SOMERSET & DORSET RAILWAY GWR RAILCARS IN COLOUR THE NORTH CORNWALL LINE THE FURNESS LINE IN COLOUR PENDRAGON BRITISH ENGLISH-ELECTRIC MANUFACTURERS PUBLISHING THE GWR EXPRESS 4-4-0 CLASSES THE COMPREHENSIVE VOICE OF RAILWAY HISTORY BACKTRACK 22-1 2008:Layout 1 21/11/07 15:59 Page 64 THE COMPREHENSIVE VOICE OF RAILWAY HISTORY END OF THE YEAR AT ASHBY JUNCTION A light snowfall lends a crisp feel to this view at Ashby Junction, just north of Nuneaton, on 29th December 1962. Two LMS 4-6-0s, Class 5 No.45058 piloting ‘Jubilee’ No.45592 Indore, whisk the late-running Heysham–London Euston ‘Ulster Express’ past the signal box in a flurry of steam, while 8F 2-8-0 No.48349 waits to bring a freight off the Ashby & Nuneaton line. As the year draws to a close, steam can ponder upon the inexorable march south of the West Coast Main Line electrification. (Tommy Tomalin) PENDRAGON PUBLISHING www.pendragonpublishing.co.uk BACKTRACK 22-1 2008:Layout 1 21/11/07 14:17 Page 4 SOUTHERN GONE WEST A busy scene at Halwill Junction on 31st August 1964. BR Class 4 4-6-0 No.75022 is approaching with the 8.48am from Padstow, THE NORTH CORNWALL while Class 4 2-6-4T No.80037 waits to shape of the ancient Bodmin & Wadebridge proceed with the 10.00 Okehampton–Padstow. -
Lima 2-8-0 “Consolidation”, Developed for TS2013, by Smokebox
Union Pacific 4000 Class 4884-1 "Big Boy" circa 1948-49 Developed by Smokebox TM for Dovetail Games' Train Simulator © Smokebox 2021, all rights reserved Issue 1 Union Pacific 4000 Class 4884-1 "Big Boy" Steam Locomotive Page 2 Contents Introduction ....................................................................................................................................................... 7 32- and 64-bit TS ................................................................................................................................................ 7 Expert or Simple Controls mode, HUD and Automatic Fireman ....................................................................... 7 "All-in-one" .................................................................................................................................................... 7 Standard TS Automatic Fireman .................................................................................................................... 8 F4 HUD ........................................................................................................................................................... 8 High Detail (HD) and Standard Detail (SD) ........................................................................................................ 8 Recommended Settings ..................................................................................................................................... 9 Cab Layout ...................................................................................................................................................... -
Steam Locomotive Firebox Explosion on the Gettysburg Railroad Near Gardners, Pennsylvania
Steam Locomotive Firebox Explosion on the Gettysburg Railroad near Gardners, Pennsylvania Leadership ViTS Meeting 6 September 2005 Bryan O’Connor, Chief Office of Safety and Mission Assurance Accident Timeline Place: Gettysburg Railroad near Gardners, PA Accident Date: June 16, 1995 Gettysburg 1278 @ Gettysburg Oct 1988 The Accident: • Steam locomotive 1278 with six passenger cars had completed two excursions and was preparing for a third and final excursion for the day. • During slow climb up moderate grade, the boiler exploded, seriously burning the engineer and two firemen. • . (2) Events Associated with Proximate Cause • Operators began climb with too little water in boiler • Water-level continued to drop and by the time the locomotive had crested the grade the crownsheet of boiler was not covered by water and failed due to thermal overstress. • Failure of crownsheet opened boiler to the firebox (atmosphere) and the water in boiler flashed into high pressure steam. • Steam exploded through firebox door into the locomotive cab, seriously burning the engineer (third degree burns over 65% of body) and two firemen. (3) Events Associated with Proximate Cause Approx. 175 psi This figure is exaggerated to show low water conditions, in locomotive 1278 the lowest gage cock was 3.25 inches above the highest point of the crownsheet and the water glass was 3.125 inches above the highest point of the crownsheet (4) Contributing Factors • Prior to operation the feed pump gauge had been removed. • Preparing to ascend grade first fireman shut off the feed pump to the boiler because a leaking check valve between the feed-pump and the boiler could potentially cause slippage on driving wheels. -
Bryan® Boilers
Form No. 7510 (Rev. 6/05) Bryan “Flexible Water Tube” AB Series Steam & Water Boilers 900,000 to 3,000,000 BTUH Forced draft gas, oil or dual fuel fi red Water Boiler AB120-W-FDGO Steam Boiler AB250-S150-FDG BRYAN® BOILERS Originators of the “Flexible Water Tube” design Low initial cost, high operating effi ciency deliver substantial return on investment • True “fl exible water tube” design guaranteed shock free F • Longer lasting with better A M performance J C • Full fi ve sq ft of heating K surface per BHP G Quality Construction Features: A. Water side or steam side interior ac cessible for B clean out and inspection, front and rear open ings, D upper and lower drums. H B. Large volume water leg downcomers promote rapid internal circulation, temperature equalization and L effi cient heat transfer. I C. Boiler tube and furnace area access panels: heavy E gauge steel casing with 2" high-temperature ceramic fi ber insulation, bolted and tightly sealed to boiler frame. D. Flame observation port in access door at rear of boiler. E. Single side access; combustion chamber, tubes and burner head are completely accessible from one side simplifying K. Bryan bent water tubes maintenance and minimizing fl oor space. are fl exible, individually F. Minimum sized fl ue vent. replaceable without welding or rolling. Never more than G. Control panel: all controls installed with connections to two tube confi gurations. terminal strip. L. Pressurized design H. Forced draft, fl ame retention head type burner. Effi cient fi rebox with internal water- combustion of oil or gas, plus quiet operation. -
Interstate Commerce Commission Washington
INTERSTATE COMMERCE COMMISSION WASHINGTON REPORT NO. 3483 wTRAL OF GSOLTIA RAILWAY COMPANY IN RE ACCJ DENT AT MCINTIRE , OA.f ON ATJVAJS: 29, 1952 Report No. 3483 SUMMARY Date: August 29, 1952 Rail road: Central of Georgia Location: Mcli-tyre, G&. Kino oi' accident: Boiler explosion Train Number: Gordon svnitch local Locomotive number: g 00 Conn 1st: Ltjht, at time of accident Speed: Standing Operation: Local si\ri telling Track: On house track Tire : 1:20 p. m, g, nidl!-|c3: 2 Injured Cause : Overheated crown sheet result ing from low water INTERSTATE CONNERCE COMMISSION REPORT NO. 3483 IN THE NATTER OP MAKING ACCIDENT INVESTIGATION UNDER THE LOCOMOTIVE INSPECTION ACT OF FEBRUARY 17, 1911, AS AMENDED CENTRAL OF GEORGIA RAILWAY November 10, 1952 Acoident (boiler explosion) at Hclntyre, Ga,, on August 29, 1952, caused, by overheated, crown sheet due to low water. REPORT OF THE COMMISSION1 PATTERSON, Commissioner: On August ?9, 1952, about 1:10 p.m., at Mclntyre, Ga., the boiler of Central of Georgia Railway locomotive 6?S exploded while the locomotive was standing on the house track. The engi neer and. fireman were seriously injured. lUnder authority of sect: on 17 (2) of the Interstate Commerce Act the above-entitled proceeding was referred by the Commission to Commissioner Patterson for consideration and disposition. - 3 - DESCRIPTION OF ACCIDENT Central of Georgia Railway locomotive 629 wan placed in service at Gordon, Ga,, at 7:30 a.m., August 29, 1952, on the Gordon switch local which regularly performs switching service at four kaolin mines at and between Gordon ana Mclntyre, Ga,, a station 8.9 miles ca?t of Gordon, After switching at two mines the train proceeded, without any known unusual incident, one mile to Nolntyre where the train, consisting of 3 loaded ana 4 empty cars, was placed-on a siding and the locomotive moved to the house track. -
Union Pacific No. 119
Union Pacific No. 119 Operating Manual Developed by Smokebox for Dovetail Games' Train Simulator 2018TM © Smokebox 2018, all rights reserved Issue 1 Train Simulator - Union Pacific No. 119 - Operating Manual Page 2 Contents Introduction....................................................................................................................................................... 4 Locomotive Technical Specifications................................................................................................................. 4 Positions of the Controls and Gauges in the Cab .............................................................................................. 5 Key Assignments................................................................................................................................................ 9 Animations....................................................................................................................................................... 12 Lights................................................................................................................................................................ 13 Sanding ............................................................................................................................................................ 13 Particle Effects................................................................................................................................................. 14 Other Special Effects ...................................................................................................................................... -
Preliminary Evaluation of a Compound Cycle Engine for Shipboard Gensets
U.S. Navy DTNSRDC-PASD-CR-1886 U.S. Army AVSCOM TR-86-C-20 NASA CR-179451 PRELIMINARY EVALUATION OF A COMPOUND CYCLE ENGINE FOR SHIPBOARD GENSETS June 1986 (NASA-CB-179451) PHEIIMINASY EVALUATION OF N86-26629 A COHPOUND CYCLE ENGINE FOE SHIEECAED GENSETS (Garrett Turbine Engine Co.) 29 p HC A03/MF A01 CSCL 131 Dnclas G3/37 43436 Jere G. Castor Garrett Turbine Engine Co. 111 S. 34th Street Phoenix, AZ 85010 William T. Wintucky NASA-Lewis Research Center 21000 Brookpark Rd. Cleveland, OH 44135 Contract NAS3-24346 21-5869 Prepared for David Taylor Naval Ship R&D Center Annapolis, MD 21402 1. Report NO. OINSRDC-PASD-CR-1886 2. Government Accession No. 3. Recipient's Catalog No. AVSCOM TR-86-C-20 NASA CR-179451 4. Title and Subtitle 5. Report Date Preliminary Evaluation of a Compound Cycle June 1986 Engine for Shipboard Gensats 6. Performing Organization Code f- Authors) 8. Performing Organization Report No. Jere G. Castor Garrett Turbine Engine Co. Garrett 21-5869 William T. Wintucky 10. Work Unit No. NASA Lewis Research Center 9. Performing Organization Name and Address Garrett Turbine Engine Co. 11. Contract or Grant No. Ill S. 34th Street MAS 3-24346 P.O. Box 52170 Mn 13. Type of Report and Period Covered sr A7. 85010 12. Sponsoring Agency Name and Address Contractor Report David Taylor Naval Ship Research and Development Center 14. Sponsoring Agenc^&MWork Jiiemen Engines Branch, Code 2721 PE6254 3N Annapolis, MD 21402 Task Area SF43-432 15. Supplementary Notes Program Manager - Propulsion Directorate U.S.