Two-Phase Flow Modelling of Metal Vaporisation Under Static Laser Shot Using a Double Domain ALE Method – a Feasibility Study
Total Page:16
File Type:pdf, Size:1020Kb
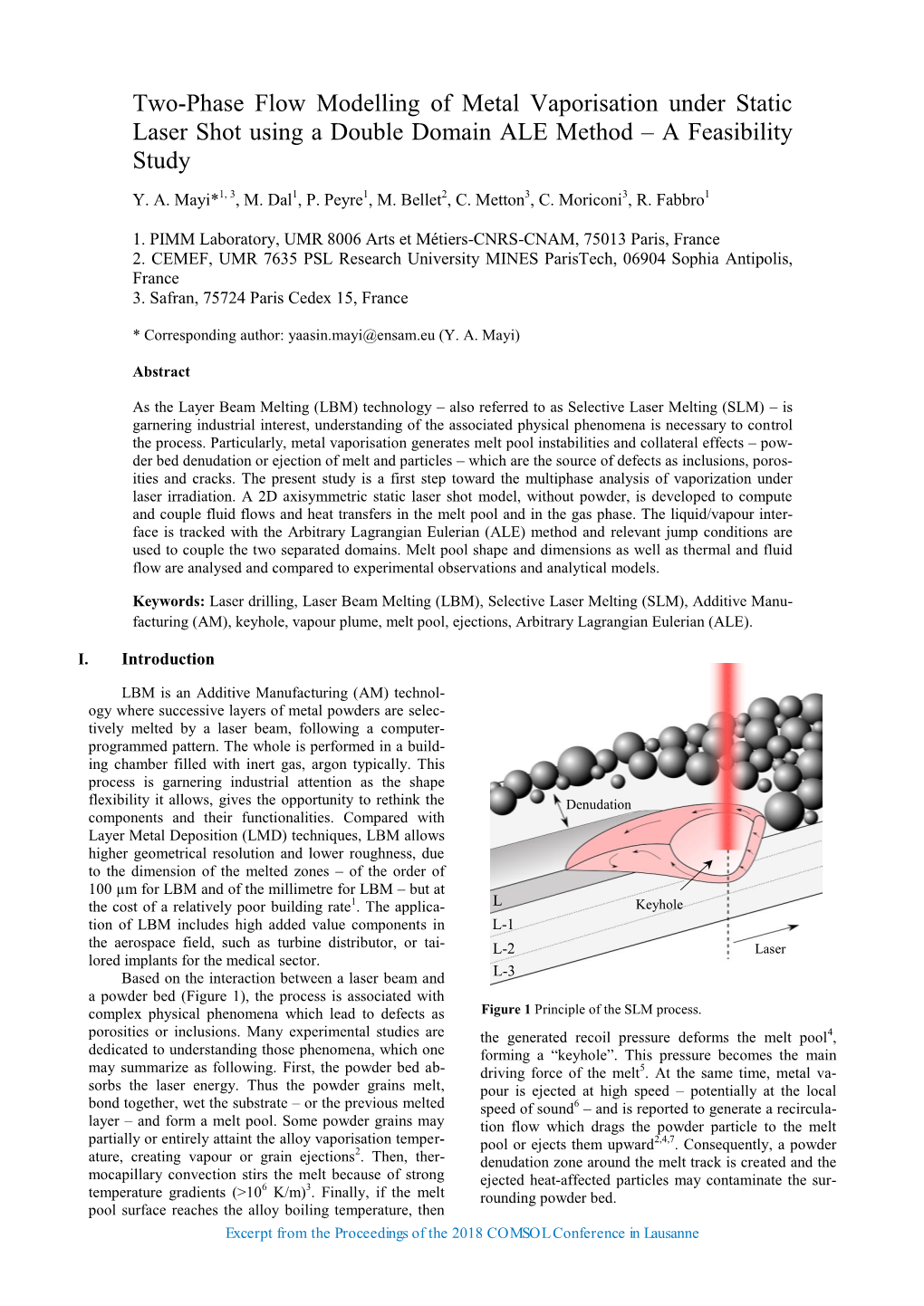
Load more
Recommended publications
-
Using Lasers to Improve Manufacturing Competitiveness Pg.6
LIA TODAY THE OFFICIAL NEWSLETTER OF THE LASER INSTITUTE OF AMERICA The international society dedicated to fostering lasers, laser applications and laser safety worldwide. FOCUS: LASERS FOR MANUFACTURING VOLUME 20 NO. 2 MARCH / APRIL 2012 Using Lasers to Improve Manufacturing Competitiveness pg.6 Courtesy Fraunhofer Institute for Laser Technology ILT, Aachen, Germany ILT, Technology Institute for Laser Courtesy Fraunhofer Ultrafast Lasers in Medical Applications - pg. 8 The Future of Manufacturing Presented at LAM 2012 - pg. 10 13501 Ingenuity Drive, Suite 128 Orlando, FL 32826 Phone: +1.407.380.1553 Fax: +1.407.380.5588 www.lia.org LIA TODAY CVR MarApr-12_3.indd 1 4/3/12 10:58:12 PM IN THIS ISSUE LIATHE OFFICIAL NEWSLETTER TODAY OF THE LASER INSTITUTE OF AMERICA LIA TODAY is published bimonthly to educate and inform laser professionals in laser safety and new trends related to laser technology. LIA members receive a free subscription to LIA TODAY and the Journal of Laser Applications® in addition to FEATURES discounts on all LIA products and services. LME 2012 – Using Lasers to Improve The editors of LIA TODAY welcome input from readers. Please submit news-related Manufacturing Competitiveness 6 releases, articles of general interest and letters to the editor. Mail us at LIA TODAY, 13501 Ingenuity Drive, Suite 128, Orlando, FL 32826, fax +1.407.380.5588, or send Ultrafast Lasers in Medical material by e-mail to [email protected]. Applications 8 The Future of Manufacturing Presented at LAM 2012 10 2012 LIA OFFICERS Plasmonic Devices Fabricated by President – Reinhart Poprawe CALENDAR OF EVENTS Fraunhofer Institute for Laser Femtosecond Laser Nanowelding 14 Technology Laser Safety Officer Training President-Elect – Klaus Löffler June 26-28, 2012 | Chicago, IL TRUMPF Laser & Systems GmbH Dec. -
Uva-DARE (Digital Academic Repository)
UvA-DARE (Digital Academic Repository) Design and fabrication through additive manufacturing of devices for multidimensional LC based on computational insights Adamopoulou, T. Publication date 2020 Document Version Other version License Other Link to publication Citation for published version (APA): Adamopoulou, T. (2020). Design and fabrication through additive manufacturing of devices for multidimensional LC based on computational insights. General rights It is not permitted to download or to forward/distribute the text or part of it without the consent of the author(s) and/or copyright holder(s), other than for strictly personal, individual use, unless the work is under an open content license (like Creative Commons). Disclaimer/Complaints regulations If you believe that digital publication of certain material infringes any of your rights or (privacy) interests, please let the Library know, stating your reasons. In case of a legitimate complaint, the Library will make the material inaccessible and/or remove it from the website. Please Ask the Library: https://uba.uva.nl/en/contact, or a letter to: Library of the University of Amsterdam, Secretariat, Singel 425, 1012 WP Amsterdam, The Netherlands. You will be contacted as soon as possible. UvA-DARE is a service provided by the library of the University of Amsterdam (https://dare.uva.nl) Download date:25 Sep 2021 Symbols and Abbreviations PFHDA 1H,1H,6H,6H-Perfluoro-1,6-hexyl diacrylate 1 D first dimension 1D one-dimensional 2 D second dimension 2DLC two-dimensional LC 2D-PAGE 2D – poly(acryl -
A Light Over All Processes Cnc-Powered Laser Innovation Laser Use in Manufacturing Grows Welding Applications Expand
LASER FOCUS — A SPECIAL SECTION I R O M G M D of esy urt Co LASERS TODAY: A LIGHT OVER ALL PROCESSES CNC-POWERED LASER INNOVATION LASER USE IN MANUFACTURING GROWS WELDING APPLICATIONS EXPAND A laser cutting head, mounted to the end effector of a robot, is robust and compact to withstand the challenging environment while having internal sensors and mechanisms that provide accuracy and feature capabilities that are beyond the normal capacity of the robot. Courtesy of Laser Mechanisms Inc. LASERS: A LIGHT OVER ALL PROCESSES AND MARKETS SME’s Industrial Laser Community Geoff Shannon, PhD, Laser Technology Manager—Miyachi America, and Mark Taggart, President—Laser Mechanisms Inc. s we approach the 50-year anniversary of laser use in manu- facturing, the use of lasers to make things is accelerating and expanding. Laser applications that just a few years ago were thought to be impossible or too expensive are Abecoming feasible and cost effective. Lasers, in fact, touch all of our lives on a daily basis. With great preci- sion and efficiency, lasers: • cut the glass for our smartphone and tablet screens; • weld the hard disk drives in our PCs and laptops; • cut airbag material and weld airbag detonators in our cars; • drill the fuel injectors in our engines to increase fuel economy; and • cut medical stents that enhance our lives. MfgEngMedia.com LF3 What’s more, remarkable, fast-paced advances in specialized optics and high-speed beam delivery computers, sensor technologies, and wireless com- systems, and non-metals welding and processing. munications are creating increasingly sophisticated Advancements in the field of laser additive manufac- tools such as process monitors and system diagnostics turing have also caught the attention of the public that are enhancing the performance, reliability and and the media. -
A Review on Selective Laser Sintering/Melting (SLS/SLM) of Aluminium Alloy Powders: Processing, Microstructure, and Properties
This is a repository copy of A review on selective laser sintering/melting (SLS/SLM) of aluminium alloy powders: Processing, microstructure, and properties. White Rose Research Online URL for this paper: http://eprints.whiterose.ac.uk/90338/ Version: Accepted Version Article: Olakanmi, EO, Cochrane, RF and Dalgarno, KW (2015) A review on selective laser sintering/melting (SLS/SLM) of aluminium alloy powders: Processing, microstructure, and properties. Progress in Materials Science, 74. 401 - 477. ISSN 0079-6425 https://doi.org/10.1016/j.pmatsci.2015.03.002 © 2015, Elsevier. Licensed under the Creative Commons Attribution-NonCommercial-NoDerivatives 4.0 International http://creativecommons.org/licenses/by-nc-nd/4.0/ Reuse Unless indicated otherwise, fulltext items are protected by copyright with all rights reserved. The copyright exception in section 29 of the Copyright, Designs and Patents Act 1988 allows the making of a single copy solely for the purpose of non-commercial research or private study within the limits of fair dealing. The publisher or other rights-holder may allow further reproduction and re-use of this version - refer to the White Rose Research Online record for this item. Where records identify the publisher as the copyright holder, users can verify any specific terms of use on the publisher’s website. Takedown If you consider content in White Rose Research Online to be in breach of UK law, please notify us by emailing [email protected] including the URL of the record and the reason for the withdrawal request. [email protected] https://eprints.whiterose.ac.uk/ Number of manuscript folios: One hundred and ninety-two (192) pages. -
Flow Diagnostics Produced by Selective Laser Melting of Cutting Nozzles
Lasers in Manufacturing Conference 2015 Flow diagnostics produced by selective laser melting of cutting nozzles S.Ulricha, S.Lorenza S. Jahna, S.Sändiga, B.Fleckb aGünter-Köhler-Institut für Fügetechnik und Werkstoffprüfung GmbH bErnst-Abbe-Hochschule Jena Abstract The increasing spread of laser technology in materials processing leads inter alia increasingly individual solution strategies in order to cope with the growing demands on the process control. The focus of this work is the fluidic analysis of the cutting nozzles, which were usually produced either by selective laser melting or conventional methods. The Schlieren measurement was utilized in order to visualize flows. Through the adjustment of optical components, the Schlieren-Aufnahmegerät 80 was coupled with a high speed camera. Based on these measurement results, the influence of manufacturing technology has been evaluated on the flow behaviour. With the help of cutting tests a direct proof of the achievable quality of the cutting edge has been evaluated. The results from both research methods provide a statement on the quality of the gas stream and the achievable cutting quality of manufacturing technology. Keywords: laser cutting, selektiv laser melting, nozzle, flow visualization 1. Introduction Nowadays, the decisive factors for financial success are on the one hand innovative products, and on the other hand the acquisition of knowledge through research and development. In materials processing, the application of lasers in technological fields like cutting and welding, enables shorter lead times. The understanding of the process plays a crucial role for the quality of the component. Regarding cutting, the quality of the cut edge and the dimensional accuracy is affected by many parameters. -
The Effect of Laser Scanning Strategies on Texture, Mechanical Properties, and Site-Specific Grain Orientation in Selective Laser Melted 316L SS
Materials and Design 193 (2020) 108852 Contents lists available at ScienceDirect Materials and Design journal homepage: www.elsevier.com/locate/matdes The effect of laser scanning strategies on texture, mechanical properties, and site-specific grain orientation in selective laser melted 316L SS Jithin James Marattukalam a,⁎, Dennis Karlsson b, Victor Pacheco b, Přemysl Beran c,e, Urban Wiklund d, Ulf Jansson b, Björgvin Hjörvarsson a, Martin Sahlberg b a Department of Physics, Materials Physics, Uppsala University, Box 530, SE-75121 Uppsala, Sweden b Department of Chemistry- Ångström Laboratory, Uppsala University, Box 523, 75120 Uppsala, Sweden c Department of Neutron Physics, Nuclear Physics Institute, ASCR, CZ -25068 Řež, Czech Republic d Department of Engineering Sciences, Applied Materials Science, Uppsala University, Box 534, 75121 Uppsala, Sweden e European Spallation Source ERIC, Box 176, 22100 Lund, Sweden HIGHLIGHTS GRAPHICAL ABSTRACT • Laser scanning strategies strongly influ- ence the crystallographic texture in as- printed components. • A ⟨100⟩ single crystalline-like texture is obtained in the direction of laser writ- ing. • Site-specific texture control is achieved by selectively switching laser scanning strategies. article info abstract Article history: Selective laser melting has been used to demonstrate the striking effect of laser scanning strategies on the crys- Received 13 December 2019 talline texture in 316L SS. The aligned crystal orientation along the tensile direction (Z-axis) could be varied using Received in revised form 1 June 2020 the scanning strategy. A strong 〈100〉 single crystalline-like texture is obtained in the direction of the laser scan Accepted 2 June 2020 and a 〈110〉 texture was observed in the build direction when using a bidirectional scan without rotation. -
Feasibility Study of Selective Laser Melting for Metal Matrix Diamond Tools
crystals Communication Feasibility Study of Selective Laser Melting for Metal Matrix Diamond Tools Xiaohong Fang 1 , Zhan Yang 2, Songcheng Tan 1,* and Longchen Duan 1 1 Faculty of Engineering, China University of Geosciences, Wuhan 430074; China; duyaoff@163.com (X.F.); [email protected] (L.D.) 2 School of Mechanical Engineering and Electronic Information, China University of Geosciences, Wuhan 430074, China; fi[email protected] * Correspondence: [email protected] Received: 17 June 2020; Accepted: 7 July 2020; Published: 10 July 2020 Abstract: Metal matrix diamond composite samples were fabricated by selective laser melting (SLM) at different forming parameters to investigate the feasibility and new challenges when SLM is applied to diamond tools manufacturing. The surface topographies, Rockwell hardness, compactness, microstructure, and diamond thermal damage of the samples were investigated in this study. The fabricated samples had high porosity and relatively low Rockwell hardness and compactness, and some ridge-shaped bulges and textures were observed at the edges and surfaces. Microstructure analyses showed that diamond particles were homogeneously distributed and metallurgically bonded within the metal matrix. The thermal damage pits on the diamond crystals along the scanning direction were the dominant damage type for SLM, which was completely different from conventional vacuum brazing and hot-pressing sintering. Although some challenges need to be further studied, our results demonstrate that SLM has great potential to propel the development of metal matrix diamond tools. Keywords: metal matrix composites; particle reinforcement; 3-D printing, microstructure; thermal damage 1. Introduction Diamond tools refer to products that contain diamond in their texture as a key element [1–3]. -
Laser Re‑Scanning Strategy in Selective Laser Melting for Part Quality Enhancement : a Review
This document is downloaded from DR‑NTU (https://dr.ntu.edu.sg) Nanyang Technological University, Singapore. Laser re‑scanning strategy in selective laser melting for part quality enhancement : a review Huang, Sheng; Yeong, Wai Yee 2018 Huang, S., & Yeong, W. Y. (2018). Laser re‑scanning strategy in selective laser melting for part quality enhancement : a review. Proceedings of the 3rd International Conference on Progress in Additive Manufacturing (Pro‑AM 2018), 413‑419. doi:10.25341/D4GP4J https://hdl.handle.net/10356/88649 https://doi.org/10.25341/D4GP4J © 2018 Nanyang Technological University. Published by Nanyang Technological University, Singapore. Downloaded on 29 Sep 2021 16:55:26 SGT LASER RE-SCANNING STRATEGY IN SELECTIVE LASER MELTING FOR PART QUALITY ENHANCEMENT: A REVIEW S+(1*HUANG Singapore Centre for 3D Printing, School of Mechanical and Aerospace Engineering, Nanyang Technological University, 50 Nanyang Avenue, Singapore 639798. W$, Y(( YEONG Singapore Centre for 3D Printing, School of Mechanical and Aerospace Engineering, Nanyang Technological University, 50 Nanyang Avenue, Singapore 639798. ABSTRACT: The selective laser melting (SLM) process is a powder bed fusion additive manufacturing process that can produce near full-density parts for many high value applications in research and industry. Due to the use of laser, the laser re-scanning strategy (LRS) can be employed in SLM. LRS can be defined as the scanning strategy ZKHQDQ\RQHRIWKHSDUW¶VOD\HUKDYHPRUHWKDQRQHSDVVHVRIODVHUVFDQ LQVWHDGRIMXVW one pass under normal scanning circumstances). The laser re-scan can be of any extent, e.g. point, contour, or area. This comprehensive review covers the applications of LRS to enhance bulk properties, improve surface quality, relieve residual stresses, minimize GHIHFWVDQGLPSURYHSDUW¶VDFFXUDF\7KHFKDOOHQJHVDQGIXWXUHWUHQGVIRU LRS are also discussed. -
Multi-Beam Strategies for the Optimization of the Selective Laser Melting Process
Solid Freeform Fabrication 2016: Proceedings of the 26th27th Annual International Solid Freeform Fabrication Symposium – An Additive Manufacturing Conference Reviewed Paper Multi-Beam Strategies for the Optimization of the Selective Laser Melting Process T. Heeling, L. Zimmermann, K. Wegener Institute of Machine Tools and Manufacturing, ETH Zurich, 8092 Zurich, Switzerland Abstract The additive manufacturing of metal parts is of increasing importance for various industry sectors, but processes like selective laser melting are still lacking of robustness especially in the case of hard to process materials. The local adjustment of temperature fields around the melt pool seems promising to decrease melt pool and stress related defects because the boundary conditions can be tailored to positively influence the melt pool dynamics and lifetime as well as the temperature gradients which are the main reason for distortion and cracking. Therefore a selective laser melting laboratory machine was built up which features two independent lasers and beam deflection units which are adapted to synchronization. To discuss the usability of different synchronized multi-beam strategies for further process improvement, computational and experimental evaluations are used to investigate the strategies‘ influences on the process dynamics of the selective laser melting process. Keywords: Selective Laser Melting, Multi-Beam Strategies, 316L Introduction Additive manufacturing processes enable the production of parts of nearly unlimited complexity without the need for specific tools. The selective laser melting (SLM) process uses laser sources to irradiate and melt powder particles which were previously distributed onto a building plate in a layer wise manner. Therefore the part is built up step by step until the final height is reached. -
The Influence of Divergent Laser Beams on the Laser Powder Bed Fusion of a High Reflectivity Aluminium Alloy
The influence of divergent laser beams on the laser powder bed fusion of a high reflectivity aluminium alloy Sagar Patel1, Haoxiu Chen2, Mihaela Vlasea1, Yu Zou2 1-University of Waterloo, Department of Mechanical and Mechatronics Engineering, Waterloo, ON N2L 3G1, Canada 2-University of Toronto, Department of Materials Science and Engineering, Toronto, ON M5S3E4, Canada Abstract The laser powder bed fusion (LPBF) of aluminium alloys is associated with numerous challenges when compared to other commonly used alloys (e.g., steels and titanium alloys) due to their higher reflectivity and thermal conductivity. This leads to a higher defect density in the final parts, commonly related to melt pool instabilities in the transition and keyhole melting modes. In this work, a laser beam defocusing strategy using a divergent beam is proposed to achieve a stable conduction mode microstructure in AlSi10Mg, a eutectic Al composition that is most studied in LPBF. The effects of conduction, transition, and keyhole melting modes on the final part are studied in detail using processing diagrams, metallography, and X-ray computed tomography. The conduction mode LPBF of AlSi10Mg leads to parts with densities of over 99.98%, with close to no porous defects in the subsurface regions, which are known to directly affect the fatigue life of the final parts. The threshold between conduction and transition mode melt pools is also observed to be at a melt pool aspect ratio (ratio of melt pool depth to width) of about 0.4, which differs from the conventionally assumed 0.5. Additionally, a significant difference is observed in the standard deviation of the melt pool depths for the transition and keyhole mode melt pools, when compared to the conduction mode melt pools. -
Fiber Laser Chirped Pulse Amplifier
Fiber Laser Chirped Pulse Amplifier Overview Fiber lasers are known to offer advantages in maintaining stable operation over years, low total cost of ownership, and predictable operation in a small package. Few mirrors need aligning. At high power, the fiber laser provides simpler heat removal of high powers in a long thin fiber. The simplicity of a fiber removes the need for water cooling, and usually air cooling or conduction cooling is sufficient. The fiber laser can usually be more compact, important for embedded applications. For these and other reasons, industrial and medical laser sources have been migrating to fiber lasers where possible. Ultrashort pulses are a new technology with many applications from sampling to non-thermal machining and surgery. Fiber lasers provide a stable and reliable mode-locked platform for generation of these pulses. These ultrashort pulse fiber lasers are the primary expertise of Calmar Laser. Rather than higher average power, higher energy pulses are sometimes required for applications such as non-thermal machining or surgery. But the small optical mode diameter in a fiber limits short pulse energy throughput due to nonlinear optical mechanisms. The Fiber Laser Chirped Pulse Amplifier (FLCPA) is an excellent method for increasing the energy output of a fiber to many µJ and above. Ultrafast fiber lasers with higher energy pulses and small diameter fibers are dominated by nonlinear optical effects, unlike free-space optics with very much large diameter beams. The first nonlinear problem is self phase modulation where the light power itself will change the index of refraction, disrupting the pulse form. -
Micro-Hole Drilling on Glass Substrates—A Review
micromachines Review Micro-Hole Drilling on Glass Substrates—A Review Lucas A. Hof 1 and Jana Abou Ziki 2,* 1 Department of Mechanical & Industrial Engineering, Concordia University, 1455 de Maisonneuve Blvd. West, Montreal, QC H3G 1M8, Canada; [email protected] 2 Bharti School of Engineering, Laurentian University, Sudbury, ON P3E 2C6, Canada * Correspondence: [email protected]; Tel.: +1-705-675-1151 (ext. 2296) Academic Editors: Hongrui Jiang and Nam-Trung Nguyen Received: 14 November 2016; Accepted: 3 February 2017; Published: 13 February 2017 Abstract: Glass micromachining is currently becoming essential for the fabrication of micro-devices, including micro- optical-electro-mechanical-systems (MOEMS), miniaturized total analysis systems (µTAS) and microfluidic devices for biosensing. Moreover, glass is radio frequency (RF) transparent, making it an excellent material for sensor and energy transmission devices. Advancements are constantly being made in this field, yet machining smooth through-glass vias (TGVs) with high aspect ratio remains challenging due to poor glass machinability. As TGVs are required for several micro-devices, intensive research is being carried out on numerous glass micromachining technologies. This paper reviews established and emerging technologies for glass micro-hole drilling, describing their principles of operation and characteristics, and their advantages and disadvantages. These technologies are sorted into four machining categories: mechanical, thermal, chemical, and hybrid machining (which combines several machining methods). Achieved features by these methods are summarized in a table and presented in two graphs. We believe that this paper will be a valuable resource for researchers working in the field of glass micromachining as it provides a comprehensive review of the different glass micromachining technologies.