Effects of Temperature on the Wave Soldering of Printed Circuit Boards: CFD Modeling Approach
Total Page:16
File Type:pdf, Size:1020Kb
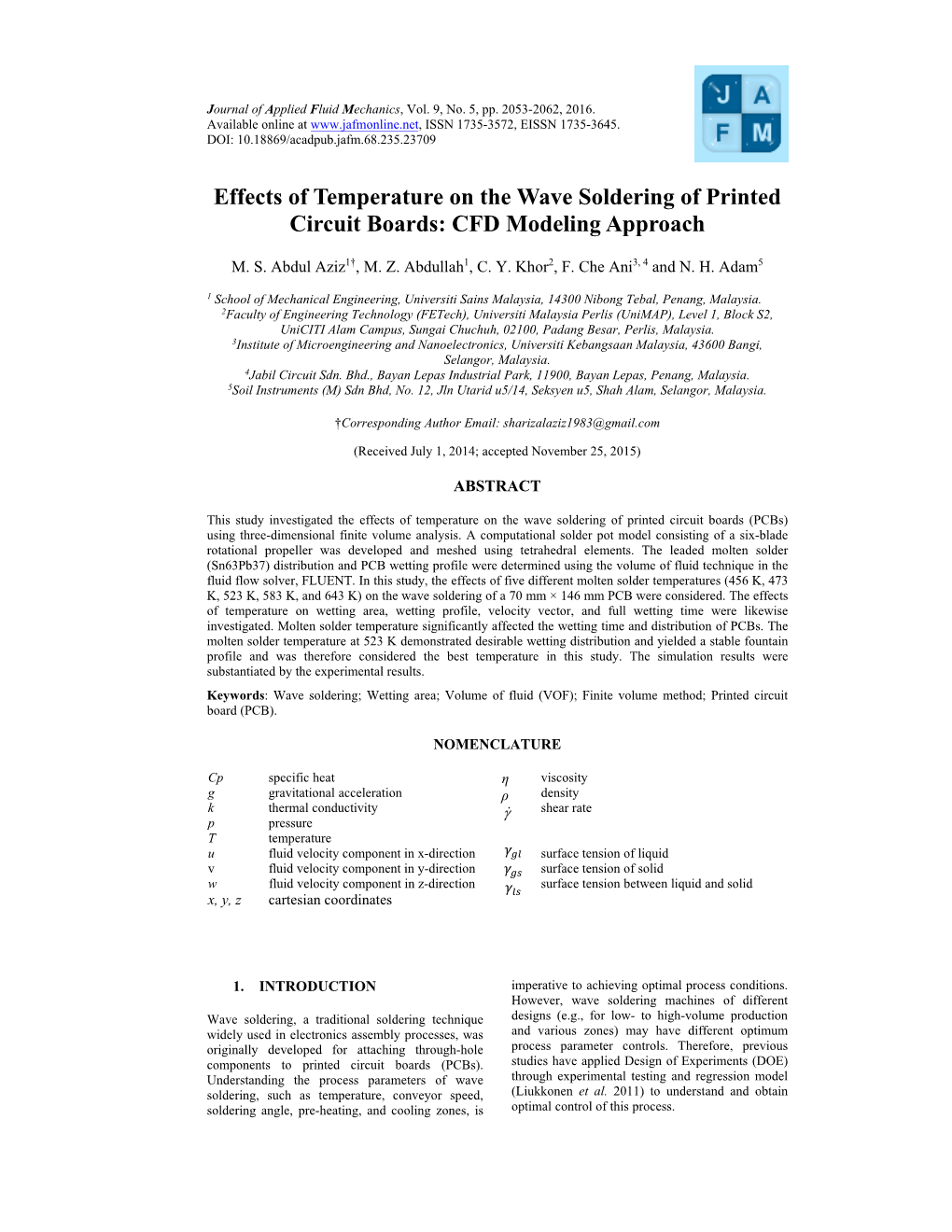
Load more
Recommended publications
-
Case Study on the Validation of SAC305 and Sncu-Based Solders in SMT, Wave and Hand Soldering at the Contract Assembler Level
Case Study on the Validation of SAC305 and SnCu-based Solders in SMT, Wave and Hand Soldering at the Contract Assembler Level Peter Biocca, ITW Kester Itasca, Illinois Carlos Rivas, SMT Dynamics Anaheim, California Abstract: At the contractor level once a product is required to be soldered with lead-free solders all the processes must be assessed as to insure the same quality a customer has been accustomed to with a 63/37 process is achieved. The reflow, wave soldering and hand assembly processes must all be optimized carefully to insure good joint formation as per the appropriate class of electronics with new solder alloys and often new fluxes. The selection of soldering materials and fluxes are important as to insure high quality solder joints with lead-free solders which tend to wet slower than leaded solders but also the process equipment must be lead-free process compatible. Components must be lead-free and able to meet the thermal requirements of the process but also the MSL (moisture sensitivity limits) must be observed. Board finish must be lead- free and the PCB must be able to sustain higher process temperature cycles with no physical damage but also good solderability to enable subsequent soldering at the wave or hand assembly. Tin-silver-copper has received much publicity in recent years as the lead-free solder of choice. SAC305 was endorsed by the IPC Solder Value Product Council as the preferred option for SMT assembly and most assemblers have transitioned to this alloy for their solder paste requirements. The SAC305 alloy due to its 3.0% content of silver is expensive when compared to traditional 63/37 for this reason many contract manufacturers and PCBA assemblers are opting for less costly options such as tin-copper based solders for wave, selective, hand soldering, dip tinning operations. -
'Pin in Paste' Reflow Process with Combination of Solder Preforms To
As originally published in the IPC Printed Circuit Expo, APEX & Designer Summit Proceedings. Investigation for Use of ‘Pin in Paste’ Reflow Process with Combination of Solder Preforms to Eliminate Wave Soldering Guhan Subbarayan, Scott Priore Assembly Sciences and Technology, Cisco Systems, Inc. San Jose, California [email protected] Paul Koep, Scott Lewin*, Rahul Raut Cookson Electronics - Assembly Materials South Plainfield, NJ; *Elgin, IL Sundar Sethuraman Jabil Circuits San Jose, California ABSTRACT The Pin in Paste (PiP) technology is the process of soldering Pin through hole (PTH) components using the Surface Mount Technology (SMT) reflow process. The use of PiP process offers several advantages compared to the traditional wave soldering process. One of the primary advantages is lowering of cost due to the elimination of the wave soldering process and its associated tooling cost and potential handling damage. Another advantage is that with the wave soldering process, it is extremely difficult to achieve adequate holefill on thermally challenging thick Printed Circuit Boards (PCBs). However, by using PiP process with combination of solder preforms, it is possible to achieve adequate holefill and reliable solder joints for soldering PTH components. The objective of this study is to investigate the use and limitations of machine-placed solid solder preforms during the top- side SMT reflow process for PTH components. An experiment was designed to investigate the following problems: 1) How much additional volume is provided by the combination -
Recommendations for Assembly of Infineon to Packages
Additional Information, DS1, March 2008 Recommendations for Assembly of Infineon TO Packages Edition 2008-03 Published by Infineon Technologies AG 81726 München, Germany © 2008 Infineon Technologies AG All Rights Reserved. Legal Disclaimer The information given in this document shall in no event be regarded as a guarantee of conditions or characteristics. With respect to any examples or hints given herein, any typical values stated herein and/or any information regarding the application of the device, Infineon Technologies hereby disclaims any and all warranties and liabilities of any kind, including without limitation, warranties of non-infringement of intellectual property rights of any third party. Information For further information on technology, delivery terms and conditions and prices, please contact the nearest Infineon Technologies Office (www.infineon.com). Warnings Due to technical requirements, components may contain dangerous substances. For information on the types in question, please contact the nearest Infineon Technologies Office. Infineon Technologies components may be used in life-support devices or systems only with the express written approval of Infineon Technologies, if a failure of such components can reasonably be expected to cause the failure of that life-support device or system or to affect the safety or effectiveness of that device or system. Life support devices or systems are intended to be implanted in the human body or to support and/or maintain and sustain and/or protect human life. If they fail, it is reasonable to assume that the health of the user or other persons may be endangered. Assembly & Interconnect Technology Table of Contents 1 Package Description and Thermal Performance . -
Guide to Soldering Jigs and Pallets
Guide to Soldering Jigs and Pallets By Bob Willis Despite the advances in electronic manufacturing which drive companies to the use of reflow soldering, wave soldering will be with us for many years to come. There are still many through hole components which can not be converted to surface mount and many products which do not benefit from changing to SMT. Wave soldering is a simple process Process Guides Bob Willis for through hole parts and less demanding than alternative like intrusive pin in hole reflow techniques. The move to lead-free manufacture also has an impact on pallet and process The soldering pallet, carrier or jig has been used for many years. Initially, a carrier was needed with fixed width chain conveyors to allow different board widths to be soldered. These early carriers were made from stainless steel or titanium, and were adjustable to allow operators to load different width and different size boards. Some of these fixtures were specifically designed to protect the leading edge of the board and prevent solder flowing on to the topside of the board. The front deflectors also provided support for the board during pre-heat and wave contact to minimise warpage. Often the deflector is used to mask the edge of the board when it features a series of gold edge contacts. These are normally used for interconnection to sockets on other boards, typical examples are PC graphic cards or boards for telephone exchanges. Example of front supports Unfortunately many design engineers continue to produce layouts which do not allow the correct support for wave soldering hence the need for soldering pallets. -
Technical Information
TECHNICAL INFORMATION SURFACE MOUNT ZERO DEFECT DESIGN CHECK LIST by John Maxwell AVX Corporation Abstract: Reliable, high-yield SMT assemblies are easily realized if time is taken in the beginning to insure yields and reliability. You cannot slap components down on a PC board with solder and hope for manufacturability; the PC board must be designed to be manufacturable. SURFACE MOUNT ZERO DEFECT DESIGN CHECK LIST by John Maxwell AVX Corporation Introduction Surface mount technology (SMT) has suffered resistors, but can occur with SOTs (small outline transis- through several false starts, but is now a reality due to tors) or even small ICs like an SO-8 resulting in rework. circuit density needs. SMT designs are a radical depar- Inadequate solder is the source of weak or missing ture from their thru-hole counterparts due to trace/ solder joints for passive components and coplanarity component spacings, size, and sensitivity to processing. problems (opens) with ICs. There must be a proper It is mandatory that a design be manufacturable in the balance between non-coplanar parts like ICs that need very beginning as tweeks in the process and rework more solder than small chip components which require must be avoided. ZERO DEFECT SOLDERING must less solder for proper joints and low manufacturing be the goal for all SMT designs, and the path starts with defects. As a side note, the total equivalent wet laydown the design of the board. of solder paste to accommodate both passives and For a board to be manufacturable one must be able to actives should be <10–12 mils and must take the board first assemble (place) components accurately and then solder plating into account. -
Even More Agility for the EMS Service Provider from Erfurt
User report Ertron GmbH enhances product Satisfied with the VERSAFLOW 4/55 (from the left): Reinhard Probandt, Managing Director at Ertron GmbH, Thomas Wohlgemuth, quality with VERSAFLOW 4/55 Quality Assurance and Pjotr Cieslak, the man at the machine. Even more agility for the EMS service provider from Erfurt During the GDR era, Erfurt was one of the Mikroelektronik Erfurt with its parent major Eastern German centres for elec- company Funkwerk Erfurt. One of these is tronics manufacturing – a situation which the EMS service provider Ertron, founded has prevailed through to the present day. in 1992, which has quality and flexibility as Today, the spectrum on offer at the tech- part of its company DNA. For THT man- nology site Erfurt covers micro-system ufacturing, Ertron GmbH has now suc- technology and micro-electronics, sen- cessfully put its first selective soldering sor systems and photovoltaic systems. system VERSAFLOW 4/55 from Ersa into Several successful individual companies operation. Author emerged from the former state combine Mark Birl Area Sales Manager Ersa GmbH published in EPP 09/2019 in Germany Ersa informs 2/5 Offline programming or during machine operation: fast and simple preparation of soldering programs with the Editor CAD Assistant 4. In the background: Live process monitoring using the VERSACAM. In answer to the question as to how an This complete package also includes de- electronics manufacturing company velopment and design services. Ertron can survive these days in a high income has the same claim for every project – country like Germany, the terms quali- the aim is always a product that is easy ty and flexibility are always mentioned. -
Considerations for Choosing Wave Versus Selective Solder
Considerations for Choosing Wave versus Selective Solder Author: Rob Rowland, Operations Engineering Manager February 2017 Two mass soldering methods are used to attach electrical components to a printed circuit board (PCB). Both wave and selective soldering apply flux, preheat the board and transfer molten solder to form the solder joints. Cycle time and access differentiate the two methods. Wave soldering is faster because the board goes over a molten wave of solder, which solders dozens or hundreds of leads at a time. However, wave soldering is not well suited for boards that are densely populated with SMT components on the secondary side. This is where selec- tive soldering usually has the advantage because it can be programmed to selectively solder through-hole components while avoiding the SMT components. WAVE SOLDERING Boards move quickly through this process with a high All soldering processes require flux, heat, and solder level of reliability. But, there are some design compli- application. A wave soldering machine combines these cations that require adding fixtures, at often significant steps into a single machine process. During wave additional cost, for processing the board when: soldering the underside of a board is fluxed, preheated, immersed in molten solder and subsequently cooled • The PCB size is too small to be handled with a during in an in-line continuous process. conveyor • The PCB has an irregular shape, especially Flux along the edges Flux can be applied as a foam or spray. A foam fluxer • SMT components are soldered to the bottom uses air passing through a porous cylinder containing side of the board flux to create foam that is applied to the board above the cylinder as it rolls past. -
Printed Circuit Board Surface Finish Defects
Guide to Printed Circuit Board Surface Finish Defects Contents Page SMART Group Introduction 3 PCB Surface Finish Reference Images 4 PCB Surface Finish Introduction 6 PCB Surface Finish Defects 9 Text Books and Standards on Surface Finishes 30 PCB Surface Finish Training Products 31 PCB Surface Finish & Solderability Training Workshop/Webinars 32 Author’s Profile 33 Copyright and Disclaimer Text and images remain copyright of Bob Willis unless stated in the text and should not be copied or transmitted through any medium without prior agreement in writing from the author Although the author has made every effort to achieve accuracy of the content, no responsibility is assumed for errors or omissions to any of the text or references to other publications and documents This book includes hyperlinks to other websites owned and operated by third parties. These links are not recommendations. We have no control over the contents of third party websites, and we accept no responsibility for them or for any loss or damage that may arise from your use of them © Copyright Bob Willis 2017 V1 Page 2 Guide to Printed Circuit Board Surface Finish Defects Introduction Welcome to this SMART Group Defect Guide Our latest SMART Group Defect Guide, is aimed at final PCB surface finish. These finishes are provided to protect exposed copper and to maintain solderability of the pads and through hole termination points to allow successful soldering in reflow, wave, selective and manual processes The choice of solderable coatings in the industry has grown over the years with multiple vendors offering alternatives for all main coating types. -
Design-Guidelines Kontron Austria Gmbh
Design Guidelines For Manufacturing of Circuit Boards and Modules and for Layout Design Kontron Austria GmbH Freistädter Straße 38 | 4209 Engerwitzdorf Tel: +43 5373 43143-0 Fax: +43 5373 43143-888 Doku-Nr.: PE3086, Version: 15 Design Guidelines Kontron Austria Electronics Version 15 Table of Contents 1 Intro .................................................................................................................................................................................................. 3 1.1 Overview ........................................................................................................................................................................................... 3 Circuit Board ..................................................................................................................................................................................... 3 Surface Mount Technology ............................................................................................................................................................... 3 Through Hole Technology ................................................................................................................................................................. 3 2 PCB / Layout ...................................................................................................................................................................................... 4 2.1 Min/Max PCB and Panel Dimensions ............................................................................................................................................... -
Surface Mount Technology Integration of Device Connection Technology in the SMT Process Let’S Connect
Surface Mount Technology Integration of device connection technology in the SMT process Let’s connect White Paper Surface Mount Technology Integration of device connectivity in the SMT process Today's PCB is a platform for electronic components, creating circuits whose complexity may vary from simple to highly sophisticated. Increasing requirements such as the miniaturisation of components, greater functional densities and lower production costs have resulted in the successive replacement of classic through hole technology (THT) by surface mount technology (SMT) in previous years. Today SMT is the method of choice – it has been widely adopted as the standard production technique for the surface mounting of electronic components. The soldering technique used in the SMT process is reflow soldering, specifically infrared, convection or vapour phase soldering. In contrast to the wave soldering process, a solder deposit applied to the PCB is melted. The device connection technology can be integrated in the SMT process by the through hole reflow (THR) or the surface mount device (SMD) processes. These two processes can also be combined. Surface Mount Device (SMD) Through Hole Reflow (THR) Process steps in surface mount technology In surface mount technology (SMT), contacts are established via connections to the housing side or via the connection surfaces directly under the housing. Unhoused components can also be used which are then directly mounted on the PCB and contacts are established wire links or via the flip chip technique. However, there are still some components, mainly electro-mechanical components like connectors or relays, which are not available in a SMD version; they are therefore mounted on the PCB after the actual SMT process itself by applying the classic THT process. -
Soldering Surface Mount Components
Soldering Surface Mount Components Proper soldering maximizes the strength and conductivity of the connection Introduction separately, just before applying the solder, or simultane- Soldering is the process of using a metal alloy with a low ously when using solder paste or rosincore solder. melting temperature (solder) to fuse the electrical contacts Solder paste typically contains flux, and rosin-core solder of a component to the pads of a circuit board. Proper has a center core of flux. As these types of solder melt, soldering maximizes the strength and conductivity of the flux is released, eliminating the need for a separate flux connection. Poor soldering can result in weak connections, application. higher resistance that causes heat buildup at the connec- tion, and possible failure of the component. General Soldering Guidelines The type of components and the pads to which they will All soldering applications require the following consider- be attached dictate the appropriate soldering method. ations: The correct amount and duration of heat to be applied • Preparation – Clean connections are essential to is a function of the heat transfer characteristics of the soldering. Clean connections maximize the ability of component, the circuit board, the solder pads, the solder the solder to adhere uniformly to the joint surfaces (and flux), and the environment in which the soldering (wetting). takes place. For this reason, effective soldering requires reasonably controlled conditions. Some experimentation • Soldering Method – The component type and size, is usually required to determine the optimal conditions for and your specific application determine the solder- each application. ing method. • Materials Selection – The component contacts, Types of Solder circuit board pads, solder, and flux materials must all be compatible with the soldering method. -
Wave Soldering Troubleshooting Guide
Wave Soldering Troubleshooting Guide Easy-to-use advice for common wave soldering assembly issues. www.alpha.cooksonelectronics.com Alpha Wave Soldering Troubleshooting Guide Table of Contents With this easy-to-use Troubleshooting Guide, you can Bridging 3 learn to troubleshoot common Insufficient Solder wave soldering issues. After using Topside Fillet 4 it a few times, it will become an essential companion for you Insufficient Solder Bottom Side Fillet 5 and anyone in your company responsible for operating a wave De-wetting or Non-wetting 6 soldering line. Solder Voids or Out-gassing This Guide offers trouble shoot ing (Blow Holes and Pin Holes) 7 advice for common wave solder ing Solder Skips 8 assembly issues by process Icicles & Flags (Horns) 9 defect. If your issue is not resolved after follow ing the steps to help Solder Balls and Splatter 10 identify the possible root cause Solder on Mask 12 and solution, please contact your Alpha representative who will be Rough or Disturbed Solder 13 able to provide you with further Grainy or Dull Solder 14 assistance. Components Lifted 15 Flooding 16 Excessive Solder 17 Alpha Confidential – For Authorized Use Only 2 www.alpha.cooksonelectronics.com Bridging Definition: The unwanted formation of a conductive path of solder between conductors. Primary process set-up areas to check • Conveyor speed too slow or other incorrect solder wave settings • Time over preheat is too long causing the flux to be burned off • Dwell time too long causing the flux to burn off before exiting the wave • Topside