Process Evaluation and Characterization of Tungsten
Total Page:16
File Type:pdf, Size:1020Kb
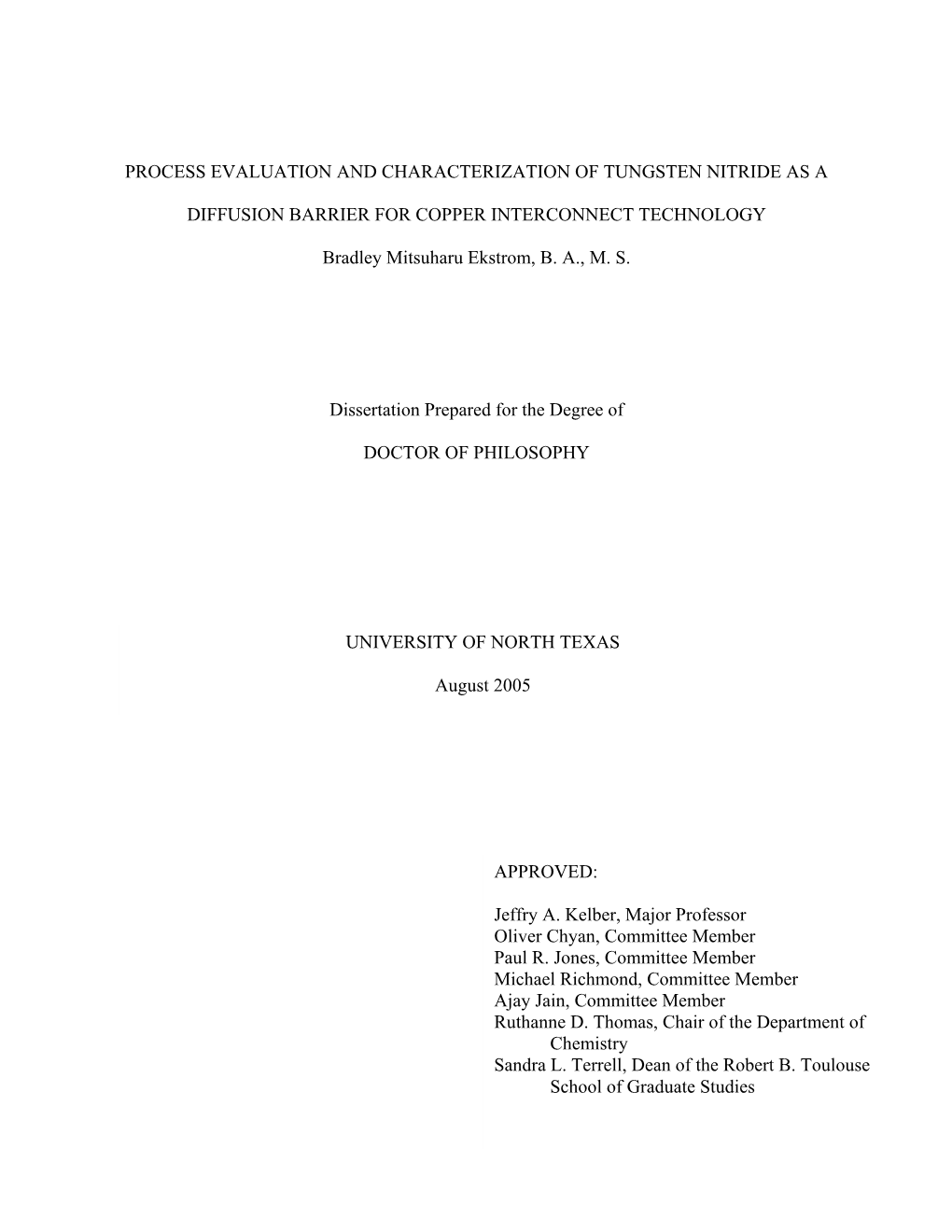
Load more
Recommended publications
-
Safety Data Sheet Material Name: TUNGSTEN HEXAFLUORIDE SDS ID: MAT24560
Safety Data Sheet Material Name: TUNGSTEN HEXAFLUORIDE SDS ID: MAT24560 Section 1 - PRODUCT AND COMPANY IDENTIFICATION Material Name TUNGSTEN HEXAFLUORIDE Synonyms MTG MSDS 85; TUNGSTEN FLUORIDE (WF6), (OC-6-11)-; WOLFRAM HEXAFLUORIDE; HEXAFLUOROTUNGSTEN; TUNGSTEN(6+) FLUORIDE; TUNGSTEN HEXAFLUORIDE (WF6); TUNGSTEN VI FLUORIDE; TUNGSTEN FLUORIDE; UN 2196; F6W Chemical Family Fluoride, inorganic, metal Product Use Industrial and Specialty Gas Applications. Restrictions on Use None known. Details of the supplier of the safety data sheet MATHESON TRI-GAS, INC. 3 Mountainview Road Warren, NJ 07059 General Information: 1-800-416-2505 Emergency #: 1-800-424-9300 (CHEMTREC) Outside the US: 703-527-3887 (Call collect) Section 2 - HAZARDS IDENTIFICATION Classification in accordance with paragraph (d) of 29 CFR 1910.1200. Gases Under Pressure - Liquefied gas Acute Toxicity - Inhalation - Gas - Category 2 Skin Corrosion/Irritation - Category 1 Serious Eye Damage/Eye Irritation - Category 1 Specific target organ toxicity - Repeated exposure - Category 1 GHS Label Elements Symbol(s) Signal Word Danger Hazard Statement(s) Contains gas under pressure; may explode if heated. Fatal if inhaled. Causes severe skin burns and eye damage. Causes damage to organs through prolonged or repeated exposure. (bones ) Precautionary Statement(s) Prevention Do not breathe gas. Use only outdoors or in a well-ventilated area. In case of inadequate ventilation wear respiratory protection. ____________________________________________________________ Page 1 of 9 Issue date: 2021-07-07 Revision 7.0 Print date: 2021-07-07 Safety Data Sheet Material Name: TUNGSTEN HEXAFLUORIDE SDS ID: MAT24560 Do not eat, drink or smoke when using this product. Wear protective gloves/protective clothing/eye protection/face protection. -
Tungsten Hexafluoride WF6 Safety Data Sheet SDS P4855
Tungsten hexafluoride Safety Data Sheet P-4855 This SDS conforms to U.S. Code of Federal Regulations 29 CFR 1910.1200, Hazard Communication. Date of issue: 01/01/1985 Revision date: 10/24/2016 Supersedes: 04/28/2015 SECTION: 1. Product and company identification 1.1. Product identifier Product form : Substance Name : Tungsten hexafluoride CAS No : 7783-82-6 Formula : WF6 Other means of identification : Tungsten hexafluoride 1.2. Relevant identified uses of the substance or mixture and uses advised against Use of the substance/mixture : Industrial use. Use as directed. 1.3. Details of the supplier of the safety data sheet Praxair, Inc. 10 Riverview Drive Danbury, CT 06810-6268 - USA T 1-800-772-9247 (1-800-PRAXAIR) - F 1-716-879-2146 www.praxair.com 1.4. Emergency telephone number Emergency number : Onsite Emergency: 1-800-645-4633 CHEMTREC, 24hr/day 7days/week — Within USA: 1-800-424-9300, Outside USA: 001-703-527-3887 (collect calls accepted, Contract 17729) SECTION 2: Hazard identification 2.1. Classification of the substance or mixture GHS-US classification Liquefied gas H280 Acute Tox. 2 (Inhalation: gas) H330 Skin Corr. 1A H314 Eye Dam. 1 H318 2.2. Label elements GHS-US labeling Hazard pictograms (GHS-US) : GHS04 GHS05 GHS06 Signal word (GHS-US) : DANGER Hazard statements (GHS-US) : H280 - CONTAINS GAS UNDER PRESSURE; MAY EXPLODE IF HEATED H314 - CAUSES SEVERE SKIN BURNS AND EYE DAMAGE H330 - FATAL IF INHALED CGA-HG11 - SYMPTOMS MAY BE DELAYED CGA-HG22 - CORROSIVE TO THE RESPIRATORY TRACT Precautionary statements (GHS-US) : P202 -
Development of High Temperature Diffusion Barriers and a Transient
Development of high temperature diffusion barriers and a transient liquid-phase wafer bonding for thermoelectric MEMS energy harvester Dissertation to achieve the academic degree of Doctor of Engineering (Dr.-Ing.) at the Technical Faculty Christian-Albrechts-University of Kiel authored by Nando Budhiman Kiel, October 2015 iii Date of defense: 02.02.2016 First Reviewer: Prof. Dr. Bernhard Wagner Second Reviewer: Prof. Dr. Lorenz Kienle Abstract In microsystem technology, a thermoelectric generator (TEG) can be fabricated in micro-scale structures (µTEG) using a surface silicon micromachining. In order to convert heat up to 600 ◦C into electrical power, a poly-SiGe semiconductor could be a suitable thermoelectric material. However, to the best of the author’s knowledge, a development of a µTEG for these high temper- ature applications has not been published so far because, for such high temperature applications, the reliability and the stability of incorporating materials, e.g., an electrical interconnection be- tween poly-SiGe structures, can be challenging. The interconnection can be fabricated using a wafer bonding technique, where p-poly-SiGe legs on a wafer are bonded with n-poly-SiGe legs on the other wafer. This technique requires a bond solder, the components of which are deposited on a plating base. In respect to high temperature applications, the bond solder must not up to 600 ◦C heat melt and must remain conductive, and the plating base must have a high thermal stability, i.e., prevents diffusion (diffusion barrier) into the semiconductor layer and must also remain conductive. For this purpose, TiW-based and Ta-based diffusion barriers, which serve as the plating bases, and a Nickel-Tin Transient Liquid-Phase (Ni-Sn TLP) wafer bonding are developed. -
Diffusion Study of Electrodeposited Copper-Nickel Multilayer
View metadata, citation and similar papers at core.ac.uk brought to you by CORE provided by ethesis@nitr Diffusion study of Electrodeposited Copper-Nickel Multilayer A THESIS SUBMITTED IN PARTIAL FULFILLMENT OF THE REQUIREMENTS FOR THE DEGREE OF Master of Technology (Dual Degree) In Metallurgical and Materials Engineering Submitted By Chinmaya Prasad Dakua Roll No: 710MM1170 Department of Metallurgical and Materials Engineering National Institute of Technology Rourkela 2015 Diffusion study of Electrodeposited Copper-Nickel Multilayer A THESIS SUBMITTED IN PARTIAL FULFILLMENT OF THE REQUIREMENTS FOR THE DEGREE OF Master of Technology (Dual Degree) In Metallurgical and Materials Engineering Submitted By Chinmaya Prasad Dakua Roll No: 710MM1170 Under the guidance of Prof. Dr. A. Basu Department of Metallurgical and Materials Engineering National Institute of Technology Rourkela 2015 National Institute of Technology Rourkela CERTIFICATE This is to certify that the thesis entitled, “Diffusion study of Electrodeposited Copper-Nickel Multilayer”, submitted by Chinmaya Prasad Dakua in partial fulfillment of the requirements for the award of Master of Technology Degree in Metallurgical and Materials Engineering at the National Institute of Technology, Rourkela is an authentic work carried out by him under our supervision and guidance. To the best of our knowledge, the matter embodied in the thesis has not been submitted to any other University/ Institute for the award of any degree or diploma. Prof. Dr. Anindya Basu Department of Metallurgical and Materials Engineering National Institute of Technology Date: Rourkela – 769008 i ACKNOWLEDGEMENT With deep regards and profound respect, I avail this opportunity to express my deep sense of gratitude and indebtedness to Dr. -
Diffusion Effect of Intermetallic Layers on Adhesion and Mechanical
Fundamentals of Nanotechnology Golnaz Bassiri Diffusion effect of intermetallic layers on adhesion and mechanical properties of electrical contacts Abstract Multilayer thin films are used as metallic contacts or relays in microelectrome- chanical systems (MEMS). The sublayers of this sandwich are chosen based on the application of the MEMS. The Au, Ag and Cu are commonly used as a conduction layer and Cr, Ti, Pt and etc. are usually employed as an adhesion layer or diffusion barrier. Heat treatment, oxygen treatment, and methods of fabrication have an ef- fect on the diffusion of the central layer into the conduction layer, thus effective the properties of the overall film. While heat treatment of multilayer films increases the diffusion, oxygen treatment in some cases forms a diffusion barrier. While diffusion of intermetallic layers increases the adhesion, it also results in increasing the contact resistance which is not satisfactory. This paper presents the research done on the dif- fusion effect of the intermetallic contact layers on electrical properties, such as contact resistance or resistivity and mechanical properties such as adhesion. It will introduce the importance of the analysis and identification of the optimum combination of the intermetellaic layers, and the motivation of the research in employing it to the MEMS application. Also the literature review, background, and the application of the research will be discussed. 1 Background and Introduction The microelectromechanical systems (MEMS) are employed widely as intelligent integrated electrical systems, such as DC electrical contacts and relays, hybrid circuits (high frequency), optical detectors, mirrors, and radio frequency (RF) switches [1]. Although the micro size the system have many advantages, the small size results in large surface area to volume ratio which increases the effect of the surface forces on the performance of the systems[2]. -
Nanoscale Large-Area Opto/Electronics Via Adhesion Lithography
Introduction Nanoscale Large-Area Opto/Electronics via Adhesion Lithography By Gwenhivir Wyatt-Moon A thesis submitted for the degree of Doctor of Philosophy Imperial College London Department of Physics i ii The work presented in this thesis was carried out in the Experimental Solid State Physics Group of Imperial College London between October 2014 and November 2017 under the supervision of Professor Thomas D. Anthopoulos. The material documented herein, except where explicit references are shown, is my own work. Gwenhivir Wyatt-Moon March 2018 The copyright of this thesis rests with the author and is made available under a Creative Commons Attribution Non-Commercial No Derivatives licence. Researchers are free to copy, distribute or transmit the thesis on the condition that they attribute it, that they do not use it for commercial purposes and that they do not alter, transform or build upon it. For any reuse or redistribution, researchers must make clear to others the licence terms of this work. iii Abstract As the feature size of devices in the electronics industry has hit the nanoscale, device fabrication costs have rapidly increased. Whilst commercial technologies such as photolithography are able to produce nanoscale feature size, they are costly and unsuitable for large area printable electronics. To allow for up-scaling of devices considerable research is now focused on new manufacturing processes. Alongside this, new materials such as organics, metal oxides and 2D materials have been developed, allowing for novel device applications to be realised. The ability to deposit these materials at low cost and on large area flexible substrates has been realised with solution processing techniques such as blade coating, inkjet, gravure and screen printing used to deposit materials. -
Interaction Between Ni/Ti Nanomultilayers and Bulk Ti-6Al-4V During Heat Treatment
metals Article Interaction between Ni/Ti Nanomultilayers and Bulk Ti-6Al-4V during Heat Treatment André João Cavaleiro 1,2,*, Ana Sofia Ramos 1 , Francisco Braz Fernandes 3, Carsten Baehtz 4 and Maria Teresa Vieira 1 1 CEMMPRE, Department of Mechanical Engineering, University of Coimbra, R. Luís Reis Santos, 3030-788 Coimbra, Portugal; sofi[email protected] (A.S.R.); [email protected] (M.T.V.) 2 INEGI, Instituto de Ciência e Inovação em Engenharia Mecânica e Engenharia Industrial–INEGI, Campus da FEUP, 400 4200-465 Porto, Portugal 3 CENIMAT/I3N, Department of Materials Science, Faculty of Sciences and Technology, Universidade Nova de Lisboa, Campus de Caparica, 2829-516 Caparica, Portugal; [email protected] 4 Helmholtz Zentrum Dresden Rossendorf HZDR, Institute of Ion Beam Physics and Materials Research, D-01314 Dresden, Germany; [email protected] * Correspondence: [email protected]; Tel.: +351-239790700 Received: 2 October 2018; Accepted: 25 October 2018; Published: 27 October 2018 Abstract: The diffusion bonding of Ti-6Al-4V to NiTi alloys assisted by Ni/Ti reactive multilayer thin films indicates the diffusion of Ni from the filler material towards bulk Ti-6Al-4V. As a consequence, the fragile NiTi2 intermetallic phase is formed at the joint interface. In this context, the aim of this work is to investigate the occurrence of Ni diffusion from Ni/Ti nanomultilayers towards Ti-6Al-4V substrates. For this purpose, multilayer coated Ti alloys were studied in situ at increasing temperatures using synchrotron radiation. After heat treatment, scanning electron microscopy (SEM) analyses were carried out and elemental map distributions were acquired by electron probe microanalysis (EPMA). -
Alumina As Diffusion Barrier to Intermetallic Formation in Thermal Interface Materials Made from Indium and Copper
ALUMINA AS DIFFUSION BARRIER TO INTERMETALLIC FORMATION IN THERMAL INTERFACE MATERIALS MADE FROM INDIUM AND COPPER By IBRAHIM KHALIFA SALEH A thesis submitted to the Faculty of the Graduate School of the University of Colorado in partial fulfillment of the requirement for the degree of Master of Science Department of Mechanical Engineering 2013 This thesis entitled: Alumina as diffusion barrier to intermetallic formation in thermal interface materials Made from indium and copper written by Ibrahim Khalifa Saleh has been approved for the Department of Mechanical Engineering Rishi Raj Conrad Stoldt Date The final copy of this thesis has been examined by the signatories, and we Find that both the content and the form meet acceptable presentation standards Of scholarly work in the above mentioned discipline. ABSTRACT Ibrahim Khalifa Saleh (M.Sc., Department of Mechanical Engineering) Alumina as diffusion barrier to intermetallic formation in thermal interface materials made from indium and copper. Thesis directed by associate Professor Rishi. Raj Indium and copper react at wide range of temperatures to form intermetallic compounds that have different physical, mechanical and thermal properties. Liquid Phase Sintered indium-copper composite long-term performance as thermal interface material is adversely affected by the evolution of the intermetallic. In this study, i) the effect of intermetallic formation and growth on the performance of Liquid Phase Sintered copper-indium composite, ii) the effectiveness of alumina as diffusion barrier between indium and copper, (iii) the thermal stability and wettability between indium and alumina, iv) indium and quartz wettability, v) indium and tungsten oxide wettability have been studied. Deleterious effect of the intermetallic formation and growth on the thermal and mechanical properties has been observed. -
Gas and Metal Compatibility Guide
Gas & Metal Compatibility Table Chemical Suggested Choosing a Mott High Purity Gas Filter: Gas Formula Filter Media Choosing the best metal filter is not always a simple Ammonia NH 3 SS/Ni matter, because in addition to easily identified variables Argon Ar SS/Ni Arsenic Pentafluoride AsF 5 SS/Ni (i.e., gas, pressure and flow), there are subjective Arsine AsH 3 SS/Ni(1) considerations. Some gases are compatible with more Boron Trichloride BCI 3 Ni/H than one type of metal which allows you a choice when Boron Trifluoride BF 3 Ni/H Carbon Dioxide CO 2 SS/Ni selecting the right filter for your application. Carbon Monoxide * CO SS * Carbon Tetrachloride CCl 4 SS/Ni The information contained in this table is a guideline for Carbon Tetraflouride CF 4 SS/Ni appropriate filter selection. Consultation with your gas Chlorine Cl 2 SS/Ni/H Diborane B2H6 SS/Ni(1) supplier is recommended to ensure Dichlorosilane SiH 2Cl 2 Ni/H gas compatibility. Because so many Diethyltelluride C4H10 Te SS/Ni Fluorine F2 Ni/H factors can affect the chemical Freon 13 CClF 3 SS/Ni resistance of a given product, you Freon 14 Tetrafluoromethane CF 4 SS/Ni should pretest under your own Freon 23 Trifluoromethane/Fluoro-form CHF 3 SS/Ni Freon 115 Chloropentafluoroethane C2ClF 5 SS/Ni operating conditions. Freon 116 Hexafluoroethane C2F6 SS/Ni As with any Germane GeH 4 SS/Ni Helium He SS/Ni chemical Hydrogen H2 SS/Ni application, Hydrogen Bromide HBr Ni/H Hydrogen Chloride HCl Ni/H safety precautions Hydrogen Fluoride HF Ni/H as noted on MSDS Hydrogen Selenide H2Se SS/Ni sheets should be Hydrogen Sulfide H2S SS/Ni Krypton Kr SS/Ni observed . -
Fabrication and Characterisation of Copper Diffusion Barrier Layers for Future Interconnect
Dublin City University School of Physical Sciences Fabrication and characterisation of copper diffusion barrier layers for future interconnect applications Conor Byrne B.Sc. Doctor of Philosophy June 2015 Supervised by Professor Greg Hughes Declaration I hereby certify that this material, which I now submit for assessment on the programme of study leading to the award of doctor of philosophy is entirely my own work, that I have exercised reasonable care to ensure that the work is original, and does not to the best of my knowledge breach any law of copyright, and has not been taken from the work of others save and to the extent that such work has been cited and acknowledged within the text of my work. Signed: ____________________ (Candidate) ID No.: 58363145 Date: ________________ i Dedications and Acknowledgements Firstly I would like to thank my supervisor Greg Hughes, for his support, insight and supervision, without which this project could not have been undertaken, let alone completed. I could not have asked for a better supervisor. A big thanks to the Surface and Interfaces Research Group (SIRG) in DCU, Justin, Anthony, Paddy, Lee, Rob, Anita, Venkat, Conor, Kumar, Tom and Tony Cafolla, you lot really put the “fun” in fundamental research (some of you put the mental in too!) and to everyone else involved. I would like to thank all the staff in DCU that have supported me throughout this study, Lisa Peyton, Pat Wogan, Des Lavelle, to name but a few (I wish I could mention everyone by name). A massive thanks to my girlfriend Xaz, for putting up with me over the past seven years. -
Oxidation Mechanisms of Hafnium Carbide and Hafnium Diboride in the Temperature Range 1400 to 2100°C
C. BRENT BARGERON, RICHARD C. BENSON, ROBB W. NEWMAN, A. NORMAN JETTE, and TERRY E. PHILLIPS OXIDATION MECHANISMS OF HAFNIUM CARBIDE AND HAFNIUM DIBORIDE IN THE TEMPERATURE RANGE 1400 TO 2100°C Two ultra-high-temperature materials, hafnium carbide and hafnium diboride, were oxidized in the temperature range 1400 to 2100°C. The two materials oxidized in distinctly different ways. The carbide formed a three-layer system consisting of a layer of residual carbide, a layer of reduced (partially oxidized) hafnium oxide containing carbon, and a layer of fully oxidized hafnium dioxide. The diboride oxidized into only two layers. For the diboride system, the outer layer, mainly hafnium dioxide, contained several intriguing physical structures. INTRODUCTION Materials that can provide protection at temperatures aspects of research that has been performed over the past above l700°C in an oxidative environment are needed for four or five years.2-5 important applications. To be usefully employed as a turbine blade coating, for example, a substance would EXPERIMENTAL METHODS need to withstand many excursions from normal ambient The experimental arrangement for the oxidation pro conditions into the high-temperature regime and back cess has been described in detail previously.2-4 An induc again without cracking, spalling, or ablating. Other ap tion furnace consisting of two concentric zirconia tubes plications, such as a combustion chamber liner, might with a graphite susceptor between them was used to heat require only one high-temperature exposure. Not only do the specimen. (A susceptor is the heating element in an the chemical properties need to be considered, but the induction furnace.) The specimen temperature was mea physical, microscopic structure of a candidate material sured with an optical pyrometer through a sapphire win can also determine how well it will function under ex dow. -
Comprehensive Electronics Solutions Praxair Offers a Full Suite of Electronics Gases, Equipment and Services
Comprehensive Electronics Solutions Praxair offers a full suite of electronics gases, equipment and services. Applications: Semiconductor From cost effectiveness to supply reliability to product quality – across North LEDs and Photonics America and around the world – Praxair is the gas supply partner with a proven Solar track record of success. Praxair’s experts are uniquely positioned to address the key needs of your operation, helping you remain competitive in today’s Nanotechnology highly complex, global electronics market. Electronics Assembly Product solutions with consistent performance Praxair is your industry-leading electronics solutions provider, backed by the dedicated service and industry know-how of the largest industrial gas company in North America. Whether its cylinder specialty gases for production processes, facility support gases from a microbulk system, or bulk or on-site delivery systems for large quantity demands, electronics manufacturing requires reliable, consistent products and service to get the job done right. Praxair’s complete suite of electronics gases, delivery equipment and services are designed to help you boost productivity and cut costs – crucial to your bottom line. Process gases that support your productivity Praxair’s global track record of supporting electronics producers in semiconductor, LED and electronics assembly markets among others is second to none. Our process gases maximize productivity, reduce process costs and enable new technologies. Count on Praxair for a reliable supply of gases that