The Effect of Microwave Fields on the Interaction of Hydrogen with Hydride
Total Page:16
File Type:pdf, Size:1020Kb
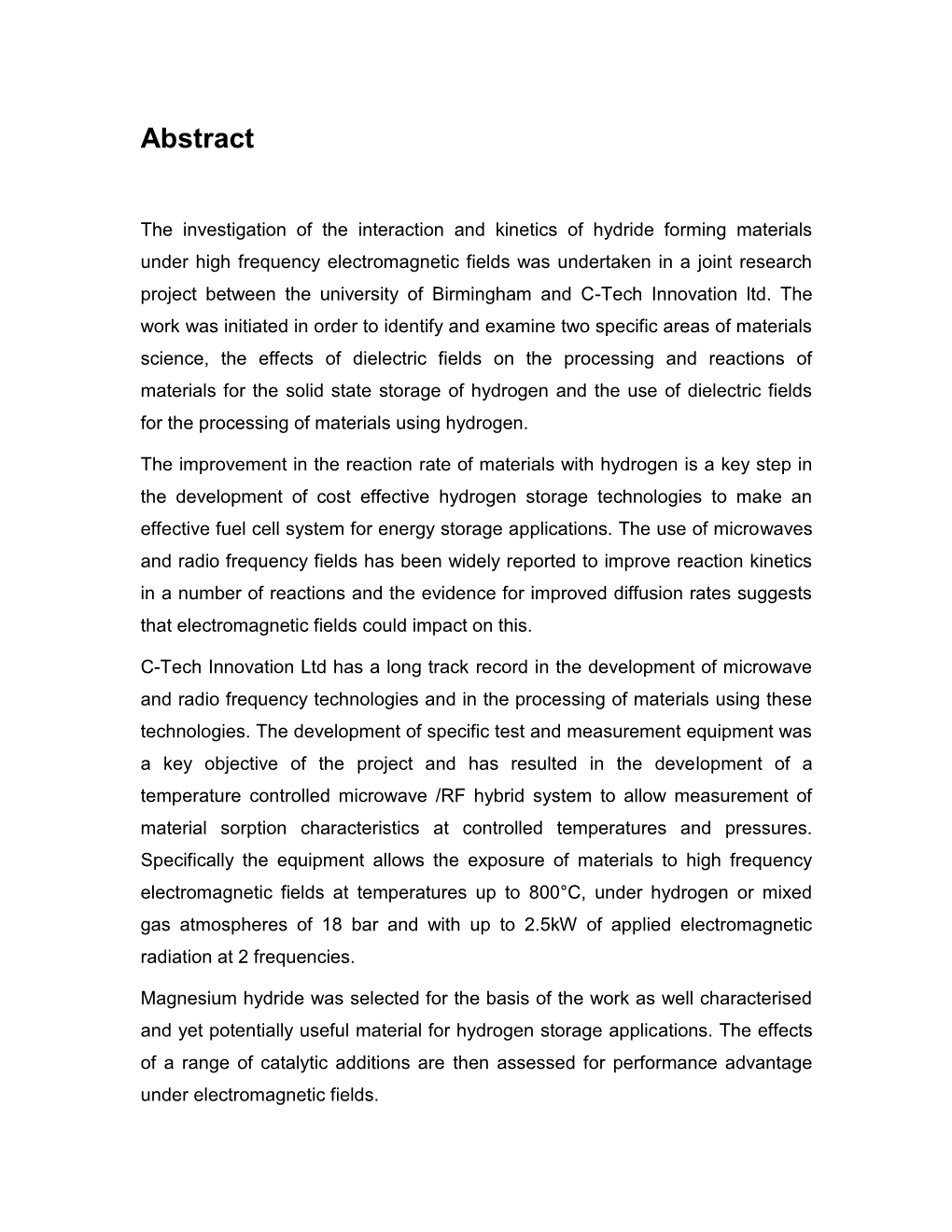
Load more
Recommended publications
-
Hydrogen Generation from Magnesium Hydride by Using Organic Acid Yen-Hsi Ho University of Wisconsin-Milwaukee
University of Wisconsin Milwaukee UWM Digital Commons Theses and Dissertations August 2013 Hydrogen Generation from Magnesium Hydride By Using Organic Acid Yen-Hsi Ho University of Wisconsin-Milwaukee Follow this and additional works at: https://dc.uwm.edu/etd Part of the Mechanical Engineering Commons, and the Oil, Gas, and Energy Commons Recommended Citation Ho, Yen-Hsi, "Hydrogen Generation from Magnesium Hydride By Using Organic Acid" (2013). Theses and Dissertations. 286. https://dc.uwm.edu/etd/286 This Thesis is brought to you for free and open access by UWM Digital Commons. It has been accepted for inclusion in Theses and Dissertations by an authorized administrator of UWM Digital Commons. For more information, please contact [email protected]. HYDROGEN GENERATION FROM MAGNESIUM HYDRIDE BY USING ORGANIC ACID by Yen-Hsi Ho A Thesis Submitted in Partial Fulfillment of the Requirements for the Degree of Master of Science in Engineering at The University of Wisconsin-Milwaukee August 2013 ABSTRACT HYDROGEN GENERATION FROM MAGNESIUM HYDRIDE BY USING ORGANIC ACID by Yen-Hsi Ho The University of Wisconsin-Milwaukee, 2013 Under the Supervision of Professor Tien-Chien Jen In this paper, the hydrolysis of solid magnesium hydride has been studied with the high concentration of catalyst at the varying temperature. An organic acid (acetic acid, CH3COOH) has been chosen as the catalyst. The study has three objectives: first, using three different weights of MgH2 react with aqueous solution of acid for the hydrogen generation experiments. Secondly, utilizing acetic acid as the catalyst accelerates hydrogen generation. Third, emphasizing the combination of the three operating conditions (the weight of MgH2, the concentration of acetic acid, and the varying temperature) influence the amount of hydrogen generation. -
Mechanochemical Synthesis of Hydrogen-Storage Materials Based on Aluminum, Magnesium and Their Compounds Ihor Z
Iowa State University Capstones, Theses and Graduate Theses and Dissertations Dissertations 2015 Mechanochemical synthesis of hydrogen-storage materials based on aluminum, magnesium and their compounds Ihor Z. Hlova Iowa State University Follow this and additional works at: https://lib.dr.iastate.edu/etd Part of the Materials Science and Engineering Commons, Mechanics of Materials Commons, and the Oil, Gas, and Energy Commons Recommended Citation Hlova, Ihor Z., "Mechanochemical synthesis of hydrogen-storage materials based on aluminum, magnesium and their compounds" (2015). Graduate Theses and Dissertations. 14573. https://lib.dr.iastate.edu/etd/14573 This Dissertation is brought to you for free and open access by the Iowa State University Capstones, Theses and Dissertations at Iowa State University Digital Repository. It has been accepted for inclusion in Graduate Theses and Dissertations by an authorized administrator of Iowa State University Digital Repository. For more information, please contact [email protected]. Mechanochemical synthesis of hydrogen-storage materials based on aluminum, magnesium and their compounds by Ihor Z. Hlova A dissertation submitted to the graduate faculty in partial fulfillment of the requirements for the degree of DOCTOR OF PHILOSOPHY Major: Materials Science and Engineering Program of Study committee: Vitalij K. Pecharsky, Major Professor Karl A. Gschneidner, Jr. Marek Pruski Duane Johnson Scott Chumbley Iowa State University Ames, Iowa 2015 Copyright © Ihor Z. Hlova, 2015. All rights reserved. ii -
Hydrogen Embrittlement of Magnesium and Magnesium Alloys: a Review Mariano Kappes,A,B,∗ Mariano Iannuzzi,A,Z and Ricardo M
C168 Journal of The Electrochemical Society, 160 (4) C168-C178 (2013) 0013-4651/2013/160(4)/C168/11/$31.00 © The Electrochemical Society Hydrogen Embrittlement of Magnesium and Magnesium Alloys: A Review Mariano Kappes,a,b,∗ Mariano Iannuzzi,a,z and Ricardo M. Carranzab aNational Center for Education and Research on Corrosion and Materials Performance (NCERCAMP), The University of Akron, Akron, Ohio 44325, USA bComision´ Nacional de Energ´ıa Atomica,´ Instituto Sabato (UNSAM/CNEA), Buenos Aires 1650, Argentina Magnesium and magnesium alloys are susceptible to stress corrosion cracking in various environments, including distilled water. There is compelling evidence to conclude that SCC is assisted, at least in part, by hydrogen embrittlement. This paper reviews the thermodynamics of the Mg-H system and the kinetics of hydrogen transport. Aspects of magnesium corrosion relevant to hydrogen absorption are also discussed. Crack growth mechanisms based on delayed hydride cracking, hydrogen adsorption dislocation emission, hydrogen enhanced decohesion, and hydrogen enhanced localized plasticity have been proposed and evidence for each of them is reviewed herein. © 2013 The Electrochemical Society. [DOI: 10.1149/2.023304jes] All rights reserved. Manuscript submitted October 22, 2012; revised manuscript received January 16, 2013. Published February 26, 2013. Pure magnesium is inherently susceptible to stress corrosion crack- The nucleation and growth of MgH2 during exposure of magne- 1–3 ing (SCC) and many of its alloys suffer SCC in environments con- sium to gaseous H2 at high pressure and temperature (∼5MPaand sidered innocuous for most other engineering alloys, e.g. distilled ∼300–400◦C) has been extensively studied29–32 due to its application water.4,5 In order to prevent SCC, some authors suggest that the ap- as a solid state hydrogen storage medium. -
Electrochemical and Optical Properties of Magnesium-Alloy Hydrides Reviewed
Crystals 2012, 2, 1410-1433; doi:10.3390/cryst2041410 OPEN ACCESS crystals ISSN 2073-4352 www.mdpi.com/journal/crystals Review Electrochemical and Optical Properties of Magnesium-Alloy Hydrides Reviewed Thirugnasambandam G. Manivasagam 1,*, Kamil Kiraz 1 and Peter H. L. Notten 1,2 1 Department of Chemical Engineering and Chemistry, Eindhoven University of Technology, MB Eindhoven 5600, The Netherlands; E-Mails: [email protected] (K.K.); [email protected] (P.H.L.N.) 2 Department of Electrical Engineering, Eindhoven University of Technology, MB Eindhoven 5600, The Netherlands * Author to whom correspondence should be addressed; E-Mail: [email protected]; Tel.: +31-40-247-2369; Fax: +31-40-247-3481. Received: 18 April 2012; in revised form: 30 July 2012 / Accepted: 10 August 2012 / Published: 15 October 2012 Abstract: As potential hydrogen storage media, magnesium based hydrides have been systematically studied in order to improve reversibility, storage capacity, kinetics and thermodynamics. The present article deals with the electrochemical and optical properties of Mg alloy hydrides. Electrochemical hydrogenation, compared to conventional gas phase hydrogen loading, provides precise control with only moderate reaction conditions. Interestingly, the alloy composition determines the crystallographic nature of the metal- hydride: a structural change is induced from rutile to fluorite at 80 at.% of Mg in Mg-TM alloy, with ensuing improved hydrogen mobility and storage capacity. So far, 6 wt.% (equivalent to 1600 mAh/g) of reversibly stored hydrogen in MgyTM(1-y)Hx (TM: Sc, Ti) has been reported. Thin film forms of these metal-hydrides reveal interesting electrochromic properties as a function of hydrogen content. -
2020 Emergency Response Guidebook
2020 A guidebook intended for use by first responders A guidebook intended for use by first responders during the initial phase of a transportation incident during the initial phase of a transportation incident involving hazardous materials/dangerous goods involving hazardous materials/dangerous goods EMERGENCY RESPONSE GUIDEBOOK THIS DOCUMENT SHOULD NOT BE USED TO DETERMINE COMPLIANCE WITH THE HAZARDOUS MATERIALS/ DANGEROUS GOODS REGULATIONS OR 2020 TO CREATE WORKER SAFETY DOCUMENTS EMERGENCY RESPONSE FOR SPECIFIC CHEMICALS GUIDEBOOK NOT FOR SALE This document is intended for distribution free of charge to Public Safety Organizations by the US Department of Transportation and Transport Canada. This copy may not be resold by commercial distributors. https://www.phmsa.dot.gov/hazmat https://www.tc.gc.ca/TDG http://www.sct.gob.mx SHIPPING PAPERS (DOCUMENTS) 24-HOUR EMERGENCY RESPONSE TELEPHONE NUMBERS For the purpose of this guidebook, shipping documents and shipping papers are synonymous. CANADA Shipping papers provide vital information regarding the hazardous materials/dangerous goods to 1. CANUTEC initiate protective actions. A consolidated version of the information found on shipping papers may 1-888-CANUTEC (226-8832) or 613-996-6666 * be found as follows: *666 (STAR 666) cellular (in Canada only) • Road – kept in the cab of a motor vehicle • Rail – kept in possession of a crew member UNITED STATES • Aviation – kept in possession of the pilot or aircraft employees • Marine – kept in a holder on the bridge of a vessel 1. CHEMTREC 1-800-424-9300 Information provided: (in the U.S., Canada and the U.S. Virgin Islands) • 4-digit identification number, UN or NA (go to yellow pages) For calls originating elsewhere: 703-527-3887 * • Proper shipping name (go to blue pages) • Hazard class or division number of material 2. -
Magnesium Hydride for Energy Storage Applications: the Kinetics of Dehydrogenation Under Different Working Conditions
Magnesium hydride for energy storage applications: The kinetics of dehydrogenation under different working conditions Antonio Perejóna,b,*, Pedro E. Sánchez-Jiméneza, José M. Criadoa, Luis A. Pérez- Maquedaa,* aInstituto de Ciencia de Materiales de Sevilla, (C.S.I.C.-Univ. Sevilla). C. Américo Vespucio 49, Sevilla 41092. Spain bDepartamento de Química Inorgánica, Facultad de Química, Universidad de Sevilla, Sevilla 41071, Spain *Corresponding authors: [email protected] Instituto de Ciencia de Materiales de Sevilla (C.S.I.C.-Univ. Sevilla). C. Américo Vespucio 49, Sevilla 41092. Spain Tel. (+34) 95 448 95 00 Fax (+34) 95 446 01 65 [email protected] Instituto de Ciencia de Materiales de Sevilla (C.S.I.C.-Univ. Sevilla). C. Américo Vespucio 49, Sevilla 41092. Spain Tel. (+34) 95 448 95 48 Fax (+34) 95 446 01 65 1 Magnesium hydride for energy storage applications: The kinetics of dehydrogenation under different working conditions Antonio Perejóna,b,*, Pedro E. Sánchez-Jiméneza, José M. Criadoa, Luis A. Pérez- Maquedaa,* aInstituto de Ciencia de Materiales de Sevilla (C.S.I.C.-Univ. Sevilla). C. Américo Vespucio 49, Sevilla 41092. Spain bDepartamento de Química Inorgánica, Facultad de Química, Universidad de Sevilla, Sevilla 41071, Spain Abstract A new approach to the kinetics of magnesium hydride dehydrogenation is considered. A model able to predict the dehydrogenation under different experimental conditions has been proposed. A new combined kinetic analysis method, which considers the thermodynamic of the process according to the microreversibility principle, has been used for performing the kinetic analysis of data obtained under different thermal schedules at hydrogen pressures ranging from high vacuum up to 20 bar. -
Metal Hydride Materials for Solid Hydrogen Storage: a Reviewଁ
International Journal of Hydrogen Energy 32 (2007) 1121–1140 www.elsevier.com/locate/ijhydene Review Metal hydride materials for solid hydrogen storage: A reviewଁ Billur Sakintunaa,∗, Farida Lamari-Darkrimb, Michael Hirscherc aGKSS Research Centre, Institute for Materials Research, Max-Planck-Str. 1, Geesthacht D-21502, Germany bLIMHP-CNRS (UPR 1311), Université Paris 13, Avenue J. B. Clément, 93430 Villetaneuse, France cMax-Planck-Institut für Metallforschung, Heisenbergstr. 3, D-70569 Stuttgart, Germany Received 31 July 2006; received in revised form 21 November 2006; accepted 21 November 2006 Available online 16 January 2007 Abstract Hydrogen is an ideal energy carrier which is considered for future transport, such as automotive applications. In this context storage of hydrogen is one of the key challenges in developing hydrogen economy. The relatively advanced storage methods such as high-pressure gas or liquid cannot fulfill future storage goals. Chemical or physically combined storage of hydrogen in other materials has potential advantages over other storage methods. Intensive research has been done on metal hydrides recently for improvement of hydrogenation properties. The present review reports recent developments of metal hydrides on properties including hydrogen-storage capacity, kinetics, cyclic behavior, toxicity, pressure and thermal response. A group of Mg-based hydrides stand as promising candidate for competitive hydrogen storage with reversible hydrogen capacity up to 7.6 wt% for on-board applications. Efforts have been devoted to these materials to decrease their desorption temperature, enhance the kinetics and cycle life. The kinetics has been improved by adding an appropriate catalyst into the system and as well as by ball-milling that introduces defects with improved surface properties. -
Lithium, Sodium and Potassium Magnesiate Chemistry: a Structural
Lithium, Sodium and Potassium Magnesiate Chemistry: A Structural Overview Antonio J. Martínez-Martínez and Charles T. O’Hara WestCHEM, Department of Pure and Applied Chemistry, University of Strathclyde, 295 Cathedral Street, Glasgow, G1 1XL, UK Until recently, deprotonative metalation reactions have been performed using organometallic compounds that contain only a single metal (e.g., organolithium reagents). Since the turn of the millennium, bimetallic compounds such as alkali metal magnesiates have begun to emerge as a new class of complementary metalating reagents. These have many benefits over traditional lithium compounds, including their enhanced stability at ambient temperatures, their tolerance of reactive functional groups and their stability in common reaction solvents. In recent years lots of attention has been focused on understanding the structure of alkali metal magnesiates in an effort to maximize synthetic efficiency and thus shed insight into approaches for future rational design. In this chapter, the diverse structural chemistry of alkali metal magnesiate compounds reported since 2007 will be summarized. KEY WORDS: Lithium, Sodium, Potassium, Magnesium, Magnesiate, X-ray Crystallography, Inverse Crowns 1.1 Introduction 1.2 Lithium magnesiate complexes 1.2.1 Alkyl/Aryl lithium magnesiate complexes 1.2.2 Amido lithium magnesiate complexes 1.2.3 Heteroleptic lithium magnesiate complexes 1.3 Sodium magnesiate complexes 1.3.1 Donor-free homo- and heteroleptic sodium magnesiate complexes 1.3.2 Introducing donors to sodium magnesiate -
Reactivity of a Ruthenium Bis(Dinitrogen) Complex
Reactivity of a Ruthenium Bis(Dinitrogen) Complex By Samantha Lau July 2018 Department of Chemistry Imperial College London A thesis submitted for Doctorate of Philosophy Declaration of Originality The work discussed in this thesis was conducted in the Department of Chemistry, Imperial College London, between October 2014 and April 2018. Unless stated otherwise, all the work is entirely my own and has not been submitted for a previous degree at this, or any other university. Copyright Declaration The copyright of this thesis rests with the author and is made available under a Creative Commons Attribution Non-Commercial No Derivatives licence. Researchers are free to copy, distribute or transmit the thesis on the condition that they attribute it, that they do not use it for commercial purposes and that they do not alter, transform or build upon it. For any reuse or redistribution, researchers must make clear to others the licence terms of this work. [1] Abstract This thesis investigated the reactivity of the ruthenium bis(dinitrogen) complex [Ru(H)2(N2)2(PCy3)2] 2 (1), an analogue of the ruthenium bis(dihydrogen) complex [Ru(H)2(η -H2)2(PCy3)2]. It was demonstrated that 1 was able to effect the sp2C–X (X= H, O) bond cleavage of acetophenone substrates to generate 5-membered organometallic intermediates. The by-products from the C–O cleavage reactions were identified as alcohols which also react with 1 at a faster or equal rate to the substrates. The mechanism of these C–X cleavage reactions were probed experimentally and computationally to show that the C–H bond cleavage pathway was operating through a σ-complex assisted metathesis pathway whereas the C–O cleavage pathway was operating through a Ru(II)/Ru(IV) redox mechanism. -
Magnesium Hydride for Energy Storage Applications: the Kinetics of Dehydrogenation Under Different Working Conditions
View metadata, citation and similar papers at core.ac.uk brought to you by CORE provided by idUS. Depósito de Investigación Universidad de Sevilla Magnesium hydride for energy storage applications: The kinetics of dehydrogenation under different working conditions Antonio Perejóna,b,*, Pedro E. Sánchez-Jiméneza, José M. Criadoa, Luis A. Pérez- Maquedaa,* aInstituto de Ciencia de Materiales de Sevilla (C.S.I.C.-Univ. Sevilla). C. Américo Vespucio 49, Sevilla 41092. Spain bDepartamento de Química Inorgánica, Facultad de Química, Universidad de Sevilla, Sevilla 41071, Spain Abstract A new approach to the kinetics of magnesium hydride dehydrogenation is considered. A model able to predict the dehydrogenation under different experimental conditions has been proposed. A new combined kinetic analysis method, which considers the thermodynamic of the process according to the microreversibility principle, has been used for performing the kinetic analysis of data obtained under different thermal schedules at hydrogen pressures ranging from high vacuum up to 20 bar. The kinetic analysis shows that the dehydrogenation mechanism of magnesium hydride depends on the experimental conditions. Thus, the reaction follows a first order kinetics, equivalent to an Avarmi-Erofeev kinetic model with an Avrami coefficient equal to 1, when carried out under high vacuum, while a mechanism of tridimensional growth of nuclei previously formed (A3) is followed under hydrogen pressure. An explanation of the change of mechanism is given. It has been shown that the activation energy is closed to the Mg-H bond breaking energy independently of the hydrogen pressure surrounding the sample, which suggests that the breaking of this bond would be the rate limiting step of the process. -
Soluble Magnesium Hydrides, Method of Preparing Them, and Use Thereof
Europaisches Patentamt 0 299 352 European Patent Office 00 Publication number: A2 Office europeen des brevets EUROPEAN PATENT APPLICATION © Application number: 88110824.5 © intCl/hCOIB 6/04 © Date of filing: 07.07.88 © Priority: 11.07.87 DE 3722993 © Applicant: Studiengesellschaft Kohle mbH Kaiser-Wilhelm-Platz 1 @ Date of publication of application: D-4330 MUIheim/Ruhr(DE) 18.01.89 Bulletin 89/03 © Inventor: Bogdanovic, Borislav ® Designated Contracting States: Kaiser-Wilhelm-Platz 1 AT BE CH DE ES FR GB IT LI LU NL D-4330 Mu!heim/Ruhr(DE) Inventor: Schwickardi, Manfred Kaiser-Wilhelm-Platz 1 D-4330 Mulheim/Ruhr(DE) © Representative: von Kreisler, Alek, Dipl.-Chem. et al Patentanwaite Von Kreisler-Selting-Werner Deichmannhaus am Hauptbahnhof D-5000K6ln 1(DE) © Soluble magnesium hydrides, method of preparing them, and use thereof. © Organic-solvent soluble magnesium hydrides of the formulas M < CM W CO O> O) CM LU Xerox Copy Centre EP 0 299 352 A2 ' (MgH2)n MgQ (ID ' (MgH2)n RM9* (III) ' (MgH2)n Mg/Qj (IV) ^.ngx (MgH-)_ • ( (V) • (MgH2)n /Tn^*R <vi> • (MgH2)n MQnX3_. (VII) • and (MgH2)n ^jj^ ■*,_. (VIID are prepared by catalytically hydrogenating finely powdered magnesium, optionally in the presence of a magnesium halide, in an organic solvent in the presence of their MgH2-free counterparts in which Q is an alkyl, alkenyl, alkoxy, dialkylamide, aralkyl, aryl or diarylamide group, each with up to 18 carbon atoms. R is an alkenyl, aralkyl or aryl group, each with up to 18 carbon atoms, X is chlorine, bromine, or iodine, E~*b -* is a chelating ligand, E is -CH2, -N(R)- or -O-, ^ is an alkylene radical of the formula -(CH2)P, D is a dialkylamide, diarylamide or alkoxy group, each with up to 18 carbon atoms, M is aluminum or boron, m is 1 , 2, or 3, and 1 < n £ 50. -
Magnesium and Zinc Hydride Complexes Intemann, Julia
University of Groningen Magnesium and zinc hydride complexes Intemann, Julia IMPORTANT NOTE: You are advised to consult the publisher's version (publisher's PDF) if you wish to cite from it. Please check the document version below. Document Version Publisher's PDF, also known as Version of record Publication date: 2014 Link to publication in University of Groningen/UMCG research database Citation for published version (APA): Intemann, J. (2014). Magnesium and zinc hydride complexes: From fundamental investigations to potential applications in hydrogen storage and catalysis. [S.n.]. Copyright Other than for strictly personal use, it is not permitted to download or to forward/distribute the text or part of it without the consent of the author(s) and/or copyright holder(s), unless the work is under an open content license (like Creative Commons). The publication may also be distributed here under the terms of Article 25fa of the Dutch Copyright Act, indicated by the “Taverne” license. More information can be found on the University of Groningen website: https://www.rug.nl/library/open-access/self-archiving-pure/taverne- amendment. Take-down policy If you believe that this document breaches copyright please contact us providing details, and we will remove access to the work immediately and investigate your claim. Downloaded from the University of Groningen/UMCG research database (Pure): http://www.rug.nl/research/portal. For technical reasons the number of authors shown on this cover page is limited to 10 maximum. Download date: 07-10-2021 Magnesium and Zinc Hydride Complexes From Fundamental Investigations to Potential Applications in Hydrogen Storage and Catalysis Julia Intemann The work described in this thesis was performed at the Faculty for Chemistry at the University of Duisburg-Essen, Germany, the Stratingh Institute for Chemistry at the University of Groningen, The Netherlands and at the Department of Chemistry and Pharmacy at the Friedrich-Alexander University Erlangen-Nürnberg, Germany.