Power Semiconductor Contributing in Energy and Environment Region
Total Page:16
File Type:pdf, Size:1020Kb
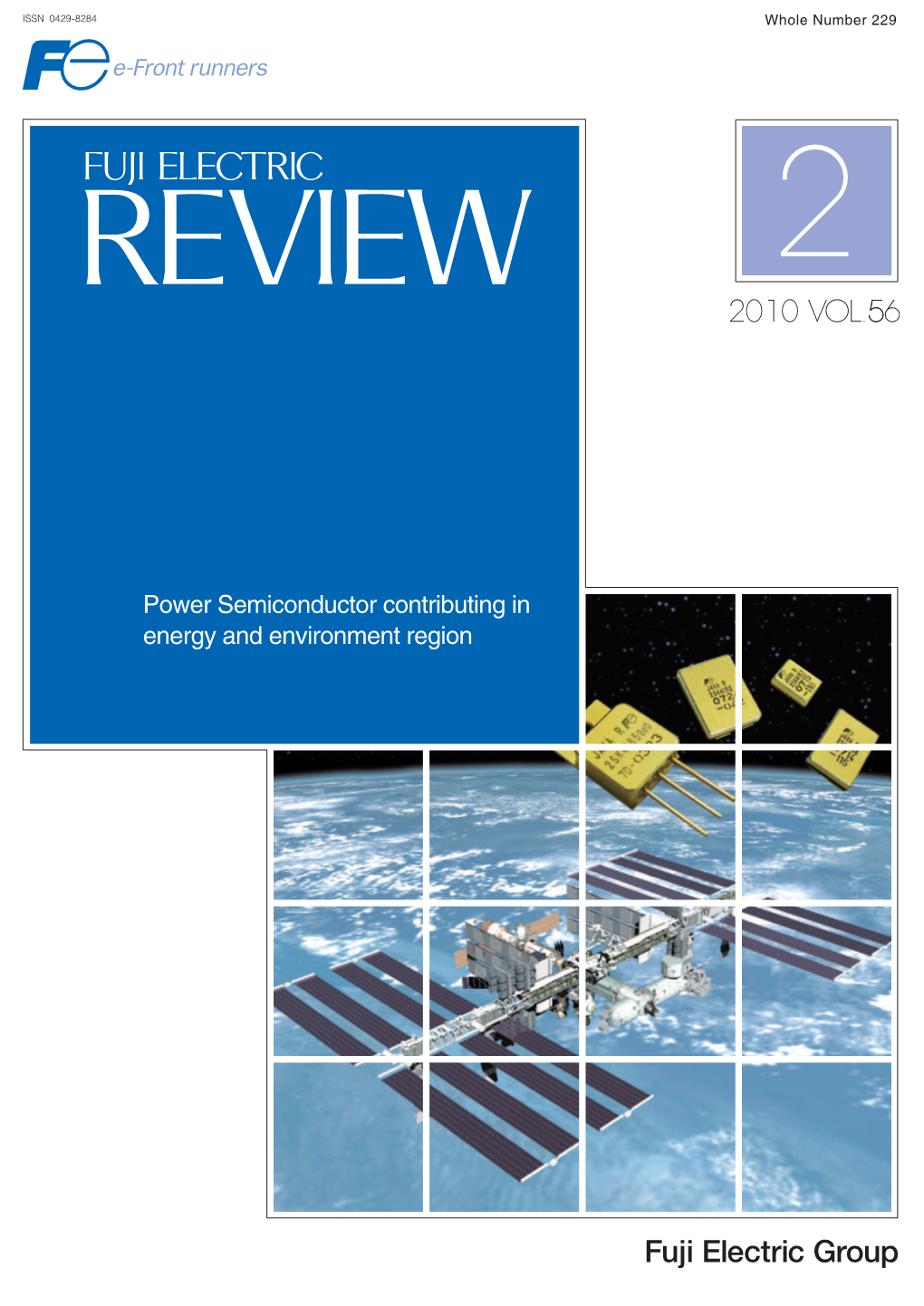
Load more
Recommended publications
-
Corporate Profile
2013 : Epsilon Launch Vehicle 2009 : International Space Station 1997 : M-V Launch Vehicle 1955 : The First Launched Pencil Rocket Corporate Profile Looking Ahead to Future Progress IHI Aerospace (IA) is carrying out the development, manufacture, and sales of rocket projectiles, and has been contributing in a big way to the indigenous space development in Japan. We started research on rocket projectiles in 1953. Now we have become a leading comprehensive manufacturer carrying out development and manufacture of rocket projectiles in Japan, and are active in a large number of fields such as rockets for scientific observation, rockets for launching practical satellites, and defense-related systems, etc. In the space science field, we cooperate with the Japan Aerospace Exploration Agency (JAXA) to develop and manufacture various types of observational rockets named K (Kappa), L (Lambda), and S (Sounding), and the M (Mu) rockets. With the M rockets, we have contributed to the launch of many scientific satellites. In 2013, efforts resulted in the successful launch of an Epsilon Rocket prototype, a next-generation solid rocket which inherited the 2 technologies of all the aforementioned rockets. In the practical satellite booster rocket field, We cooperates with the JAXA and has responsibilities in the solid propellant field including rocket boosters, upper-stage motors in development of the N, H-I, H-II, and H-IIA H-IIB rockets. We have also achieved excellent results in development of rockets for material experiments and recovery systems, as well as the development of equipment for use in a space environment or experimentation. In the defense field, we have developed and manufactured a variety of rocket systems and rocket motors for guided missiles, playing an important role in Japanese defense. -
Hdtv) on Board Selene (Kaguya)
40th Lunar and Planetary Science Conference (2009) 2540.pdf RESULTS OF HIGH-DEFINITION TELEVSION SYSTEM (HDTV) ON BOARD SELENE (KAGUYA) . R. Honda1, J. Yamazaki2, S. Mitsuhashi2, J. Tachino3 , M. Yamauchi4, M. Shirao5, 1Kochi University, Akebono-cyo 2-5-1, Kochi, JAPAN, 780-8520 ([email protected]) , 2 NHK (Japan Broadcasting Corporation), 3 NHK En- gineering Service, 4 NHK Mito Broadcasting Station, 5Planetary Geological Society of Japan Introduction: High Definition Television System Imaging of the full Earth : HDTV’s primary ob- ( HDTV) on board KAGUYA/SELENE is the camera jective is to obtain the moving images of the “full” system composed of a wide angle camera (HDTV- Earth rising from the lunar horizon and setting to the WIDE) and a telephoto camera (HDTV-WIDE), that lunar horizon. We have succeeded in the acquisition aims to acquire the moving images of the moon and of these images on April 5 th and September 30 th in the Earth from the moon for the public outreach and 2008. Figure 2 shows a snapshot extracted from the the broadcasting. HDTV has succeeded in obtaining moving images of the full Earth rise from the lunar the moving images of the Earth rising from the moon South Pole obtained by HDTV-TELE on April 5th, and setting to the lunar horizon and other prominent 2008. These moving images are taken at the smallest features on the lunar surface. The data obtained frame rate among the four frame rates of 30fps, 15fps, amounts to 1.37 GB as of the end of November, 2008, 7.5dps, and 3.75fps . -
Securing Japan an Assessment of Japan´S Strategy for Space
Full Report Securing Japan An assessment of Japan´s strategy for space Report: Title: “ESPI Report 74 - Securing Japan - Full Report” Published: July 2020 ISSN: 2218-0931 (print) • 2076-6688 (online) Editor and publisher: European Space Policy Institute (ESPI) Schwarzenbergplatz 6 • 1030 Vienna • Austria Phone: +43 1 718 11 18 -0 E-Mail: [email protected] Website: www.espi.or.at Rights reserved - No part of this report may be reproduced or transmitted in any form or for any purpose without permission from ESPI. Citations and extracts to be published by other means are subject to mentioning “ESPI Report 74 - Securing Japan - Full Report, July 2020. All rights reserved” and sample transmission to ESPI before publishing. ESPI is not responsible for any losses, injury or damage caused to any person or property (including under contract, by negligence, product liability or otherwise) whether they may be direct or indirect, special, incidental or consequential, resulting from the information contained in this publication. Design: copylot.at Cover page picture credit: European Space Agency (ESA) TABLE OF CONTENT 1 INTRODUCTION ............................................................................................................................. 1 1.1 Background and rationales ............................................................................................................. 1 1.2 Objectives of the Study ................................................................................................................... 2 1.3 Methodology -
MIT Japan Program Working Paper 01.10 the GLOBAL COMMERCIAL
MIT Japan Program Working Paper 01.10 THE GLOBAL COMMERCIAL SPACE LAUNCH INDUSTRY: JAPAN IN COMPARATIVE PERSPECTIVE Saadia M. Pekkanen Assistant Professor Department of Political Science Middlebury College Middlebury, VT 05753 [email protected] I am grateful to Marco Caceres, Senior Analyst and Director of Space Studies, Teal Group Corporation; Mark Coleman, Chemical Propulsion Information Agency (CPIA), Johns Hopkins University; and Takashi Ishii, General Manager, Space Division, The Society of Japanese Aerospace Companies (SJAC), Tokyo, for providing basic information concerning launch vehicles. I also thank Richard Samuels and Robert Pekkanen for their encouragement and comments. Finally, I thank Kartik Raj for his excellent research assistance. Financial suppport for the Japan portion of this project was provided graciously through a Postdoctoral Fellowship at the Harvard Academy of International and Area Studies. MIT Japan Program Working Paper Series 01.10 Center for International Studies Massachusetts Institute of Technology Room E38-7th Floor Cambridge, MA 02139 Phone: 617-252-1483 Fax: 617-258-7432 Date of Publication: July 16, 2001 © MIT Japan Program Introduction Japan has been seriously attempting to break into the commercial space launch vehicles industry since at least the mid 1970s. Yet very little is known about this story, and about the politics and perceptions that are continuing to drive Japanese efforts despite many outright failures in the indigenization of the industry. This story, therefore, is important not just because of the widespread economic and technological merits of the space launch vehicles sector which are considerable. It is also important because it speaks directly to the ongoing debates about the Japanese developmental state and, contrary to the new wisdom in light of Japan's recession, the continuation of its high technology policy as a whole. -
Allocation of Commercial Space Industry Components 1
May 2018 Allocation of Commercial S pace Industry Components A Virtual Think Tank (ViTTa)® Report Deeper Analyses Clarifying Insights Better Decisions Produced in support of the Strategic Multilayer Assessment (SMA) Office (Joint Staff, J39) www.NSIteam.com Allocation of Commercial Space Industry Components 1 Authors Dr. Belinda Bragg Dr. Sabrina Pagano Please direct inquiries to Belinda Bragg at [email protected] ViTTa® Project Team Dr. Allison Astorino-Courtois Sarah Canna Nicole Peterson Executive VP Principal Analyst Analyst Weston Aviles Dr. Larry Kuznar George Popp Analyst Chief Cultural Sciences Officer Senior Analyst Dr. Belinda Bragg Dr. Sabrina Pagano Dr. John A. Stevenson Principal Research Scientist Principal Research Scientist Principal Research Scientist Interview Team1 Weston Aviles Nicole Peterson Analyst Analyst Sarah Canna George Popp Principal Analyst Senior Analyst What is ViTTa®? NSI’s Virtual Think Tank (ViTTa®) provides rapid response to critical information needs by pulsing our global network of subject matter experts (SMEs) to generate a wide range of expert insight. For this SMA Contested Space Operations project, ViTTa was used to address 23 unclassified questions submitted by the Joint Staff and US Air Force project sponsors. The ViTTa team received written and verbal input from over 111 experts from National Security Space, as well as civil, commercial, legal, think tank, and academic communities working space and space policy. Each Space ViTTa report contains two sections: 1) a summary response to the question asked; and 2) the full written and/or transcribed interview input received from each expert contributor organized alphabetically. Biographies for all expert contributors have been collated in a companion document. -
Motorcycles, Spares and Memorabilia Bicester Heritage | 14 - 16 August 2020
The Summer Sale | Live & Online Including The Morbidelli Motorcycle Museum Collection Collectors’ Motorcycles, Spares and Memorabilia Bicester Heritage | 14 - 16 August 2020 The Summer Sale | Live & Online Including The Morbidelli Motorcycle Museum Collection Collectors’ Motorcycles, Spares and Memorabilia Hangar 113, Bicester Heritage, OX26 5HA | Friday 14, Saturday 15 & Sunday 16 August 2020 VIEWING SALE NUMBER MOTORCYCLE ENQUIRIES CUSTOMER SERVICES In light of the current government 26111 ON VIEW AND SALE DAYS Monday to Friday 8:30am - 6pm guidelines and relaxed measures +44 (0) 330 3310779 +44 (0) 20 7447 7447 we are delighted to welcome CATALOGUE viewing, strictly by appointment. £30.00 + p&p ENQUIRIES Please see page 2 for bidder All the lots will be on view at Ben Walker information including after-sale Bicester Heritage in our traditional +44 (0) 20 8963 2819 collection and shipment Hangar 113. We will ensure social BIDS ENQUIRIES INCLUDING [email protected] distancing measures are in place, VIEW AND SALE DAYS Please see back of catalogue with gloves and sanitiser available +44 (0) 330 3310778 James Stensel for important notice to bidders for clients wishing to view [email protected] +44 (0) 20 8963 2818 motorcycle history files. Please [email protected] IMPORTANT INFORMATION email: motorcycles@bonhams. LIVE ONLINE BIDDING IS The United States Government com or call +44 (0) 20 8963 2817 AVAILABLE FOR THIS SALE Bill To has banned the import of ivory to book an appointment. Please email [email protected] +44 (0) 20 8963 2822 into the USA. Lots containing with “Live bidding” in the subject [email protected] ivory are indicated by the VIEWING TIMES line no later than 6pm the day symbol Ф printed beside the Wednesday 12 August before the relevant auction Andy Barrett lot number in this catalogue. -
Introduction of NEC Space Business (Launch of Satellite Integration Center)
Introduction of NEC Space Business (Launch of Satellite Integration Center) July 2, 2014 Masaki Adachi, General Manager Space Systems Division, NEC Corporation NEC Space Business ▌A proven track record in space-related assets Satellites · Communication/broadcasting · Earth observation · Scientific Ground systems · Satellite tracking and control systems · Data processing and analysis systems · Launch site control systems Satellite components · Large observation sensors · Bus components · Transponders · Solar array paddles · Antennas Rocket subsystems Systems & Services International Space Station Page 1 © NEC Corporation 2014 Offerings from Satellite System Development to Data Analysis ▌In-house manufacturing of various satellites and ground systems for tracking, control and data processing Japan's first Scientific satellite Communication/ Earth observation artificial satellite broadcasting satellite satellite OHSUMI 1970 (24 kg) HISAKI 2013 (350 kg) KIZUNA 2008 (2.7 tons) SHIZUKU 2012 (1.9 tons) ©JAXA ©JAXA ©JAXA ©JAXA Large onboard-observation sensors Ground systems Onboard components Optical, SAR*, hyper-spectral sensors, etc. Tracking and mission control, data Transponders, solar array paddles, etc. processing, etc. Thermal and near infrared sensor for carbon observation ©JAXA (TANSO) CO2 distribution GPS* receivers Low-noise Multi-transponders Tracking facility Tracking station amplifiers Dual- frequency precipitation radar (DPR) Observation Recording/ High-accuracy Ion engines Solar array 3D distribution of TTC & M* station image -
Dust Phenomena Relating to Airless Bodies
Space Sci Rev (2018) 214:98 https://doi.org/10.1007/s11214-018-0527-0 Dust Phenomena Relating to Airless Bodies J.R. Szalay1 · A.R. Poppe2 · J. Agarwal3 · D. Britt4 · I. Belskaya5 · M. Horányi6 · T. Nakamura7 · M. Sachse8 · F. Spahn 8 Received: 8 August 2017 / Accepted: 10 July 2018 © Springer Nature B.V. 2018 Abstract Airless bodies are directly exposed to ambient plasma and meteoroid fluxes, mak- ing them characteristically different from bodies whose dense atmospheres protect their surfaces from such fluxes. Direct exposure to plasma and meteoroids has important con- sequences for the formation and evolution of planetary surfaces, including altering chemical makeup and optical properties, generating neutral gas and/or dust exospheres, and leading to the generation of circumplanetary and interplanetary dust grain populations. In the past two decades, there have been many advancements in our understanding of airless bodies and their interaction with various dust populations. In this paper, we describe relevant dust phenomena on the surface and in the vicinity of airless bodies over a broad range of scale sizes from ∼ 10−3 km to ∼ 103 km, with a focus on recent developments in this field. Keywords Dust · Airless bodies · Interplanetary dust Cosmic Dust from the Laboratory to the Stars Edited by Rafael Rodrigo, Jürgen Blum, Hsiang-Wen Hsu, Detlef Koschny, Anny-Chantal Levasseur-Regourd, Jesús Martín-Pintado, Veerle Sterken and Andrew Westphal B J.R. Szalay [email protected] A.R. Poppe [email protected] 1 Department of Astrophysical Sciences, Princeton University, Princeton, NJ 08540, USA 2 Space Sciences Laboratory, U.C. Berkeley, Berkeley, CA, USA 3 Max Planck Institute for Solar System Research, Göttingen, Germany 4 University of Central Florida, Orlando, FL 32816, USA 5 Institute of Astronomy, V.N. -
Data Archives and Standards for Japanese Planetary Missions
Informatics and Data Analytics (2018) 6026.pdf DATA ARCHIVES AND STANDARDS FOR JAPANESE PLANETARY MISSIONS. Y. Yamamoto1,2, Y. Ishihara1, and S. Murakami1, 1Japan Aerospace Exploration Agency (3-1-1 Yoshinodai, Chuo-ku, Sagamihara, Kanagawa 252-5210, JAPAN). 2SOKENDAI, The Graduate University for Advanced Studies, School of Physical Science, Space and Aeronautical Science (3-1-1 Yoshinodai, Chuo-ku, Sagamihara, Kanagawa 252-5210, JAPAN). Introduction: Considering the long-term preser- Table 1 Data of Japanese planetary explorers vation of data, it is important to follow standards. Alt- Name Launch Target Archives hough the history of planetary explorations in Japan is Sakigake Jan.1985 Comet DARTS over 30 years, standardization of data archives has just Suisei Halley PDS/SBN begun(Table 1). In the 1990s, Japanese planetary explo- Hagoromo Jan. 1990 Moon - ration programs did not notice the importance of data Hiten archiving. Recently discussions of data archives be- Nozomi Jul. 1998 Mars - come active, and long-term preservation is one of the topics in the planetary exploration programs. There are Hayabusa May 2003 Asteroid DARTS several standards to be followed making planetary data Itokawa PDS/SBN archives. Kaguya Sep. 2007 Moon DARTS Archiving standards: Japan Aerospace Explora- tion Agency (JAXA) has applied the Planetary Data Akatsuki May 2010 Venus DARTS System (PDS)[1] as a standard to the data archives of PDS/Atmos. planetary explorations. The PDS is not just a format Hayabusa2 Dec. 2012 Asteroid DARTS definition, it is the system as its name. It specifies di- Ryugu PDS/SBN rectory structure and essential files to be provided. BepiColombo Oct. -
Field Experiment for Gpm Ground Validation Using the Dual Ka-Radar System
FIELD EXPERIMENT FOR GPM GROUND VALIDATION USING THE DUAL KA-RADAR SYSTEM Shuji Shimizu* Japan Aerospace Exploration Agency, Japan Kenji Nakamura, Masanori Nishikawa, Haruya Minda Nagoya University, Japan Katsuhiro Nakagawa, Hiroshi Hanado National Institute of Information and Communications Technology 1. INTRODUCTION 2. KA-RADAR SYSTEM Global Precipitation Measurement (GPM) started The simultaneous observations using the two as an international mission and follow-on mission Ka-radars and precipitation particle observation of the Tropical Rainfall Measuring Mission (TRMM) systems will provide the combination of the project to obtain more accurate and frequent information of the precipitation particles and scatter observations of precipitation. Japan Aerospace and attenuation. This idea has been proposed by Li Exploration Agency (JAXA) is in charge of et al. (2001), Srivastava and Tian (1996), and Tian developing GPM/Dual-frequency Precipitation and Srivastava (1997).These information are very Radar (DPR) algorithms as the sensor provider and useful for the development of DPR and GMI producing and delivering hourly global precipitation algorithms as scattering tables. Ka-radar map to make useful for various research and observation with C/X-band radar can verify the application areas. In order to secure the quality of dual-frequency algorithm of GPM/DPR. precipitation estimates, ground validation (GV) of satellite data and retrieval algorithms is essential. End-to-end comparisons between instantaneous precipitation data observed by satellite and ground-based instruments are not enough to develop and improve the algorithms. In order to estimate the error of various physical parameters in the precipitation retrieval algorithms of DPR, we have started to conduct intensive observations using several instruments for measuring precipitation. -
Bepicolombo Science Investigations During Cruise and Flybys at the Earth, Venus and Mercury Valeria Mangano, Melinda Dósa, Markus Fränz, Anna Milillo, Joana S
BepiColombo Science Investigations During Cruise and Flybys at the Earth, Venus and Mercury Valeria Mangano, Melinda Dósa, Markus Fränz, Anna Milillo, Joana S. Oliveira, Yeon Joo Lee, Susan Mckenna-Lawlor, Davide Grassi, Daniel Heyner, Alexander S. Kozyrev, et al. To cite this version: Valeria Mangano, Melinda Dósa, Markus Fränz, Anna Milillo, Joana S. Oliveira, et al.. BepiColombo Science Investigations During Cruise and Flybys at the Earth, Venus and Mercury. Space Science Reviews, Springer Verlag, 2021, 217, pp.23. 10.1007/s11214-021-00797-9. insu-03139759 HAL Id: insu-03139759 https://hal-insu.archives-ouvertes.fr/insu-03139759 Submitted on 12 Feb 2021 HAL is a multi-disciplinary open access L’archive ouverte pluridisciplinaire HAL, est archive for the deposit and dissemination of sci- destinée au dépôt et à la diffusion de documents entific research documents, whether they are pub- scientifiques de niveau recherche, publiés ou non, lished or not. The documents may come from émanant des établissements d’enseignement et de teaching and research institutions in France or recherche français ou étrangers, des laboratoires abroad, or from public or private research centers. publics ou privés. Distributed under a Creative Commons Attribution| 4.0 International License Space Sci Rev (2021) 217:23 https://doi.org/10.1007/s11214-021-00797-9 BepiColombo Science Investigations During Cruise and Flybys at the Earth, Venus and Mercury Valeria Mangano1 · Melinda Dósa2 · Markus Fränz3 · Anna Milillo1 · Joana S. Oliveira4,5 · Yeon Joo Lee 6 · Susan McKenna-Lawlor7 · Davide Grassi1 · Daniel Heyner8 · Alexander S. Kozyrev9 · Roberto Peron1 · Jörn Helbert10 · Sebastien Besse11 · Sara de la Fuente12 · Elsa Montagnon13 · Joe Zender4 · Martin Volwerk14 · Jean-Yves Chaufray15 · James A. -
Operation Status for the Asteroid Explorer, Hayabusa2, in the Vicinity of Ryugu
Operation status for the asteroid explorer, Hayabusa2, in the vicinity of Ryugu July 19, 2018 JAXA Hayabusa2 Project Today’s Topics Regarding Hayabusa2: • Current status of the mission • Science (remote sensing, sample, TIR) • Mission schedule 2 Table of Contents 0.Hayabusa2 overview: outline of the mission flow. 1.Current status and overall schedule of the project. 2.Anticipated scientific achievements 3.Expectation for the sample analysis 4.Initial observational results with the mid-infrared camera (TIR). 5.Mission schedule 6.Future plans 3 Overview of Hayabusa2 Objective We will explore and sample the C-type asteroid Ryugu, which is a more primitive type than the S-type asteroid Itokawa that Hayabusa explored, and elucidate interactions between minerals, water, and organic matter in the primitive solar system. By doing so, we will learn about the origin and evolution of Earth, the oceans, and life, and maintain and develop the technologies for deep-space return exploration (as demonstrated with Hayabusa), a field in which Japan leads the world. Expected results and effects ・By exploring a C-type asteroid, which is rich in water and organic materials, we will clarify interactions between the building blocks of Earth and the evolution of its oceans and life, thereby developing solar system science. ・ Japan will further its worldwide lead in this field by taking on the new challenge of obtaining samples from a crater produced by an impacting device. ・We will establish stable technologies for return exploration of solar- system bodies. Features: ・World’s first sample return mission to a C-type asteroid. ・World’s first attempt at a rendezvous with an asteroid and performance of observation before and after projectile impact from an impactor.