Crystallization Fouling Behaviour of Uranium Oxide and Alumnosilicate Scale in High Level Nuclear Waste Medium
Total Page:16
File Type:pdf, Size:1020Kb
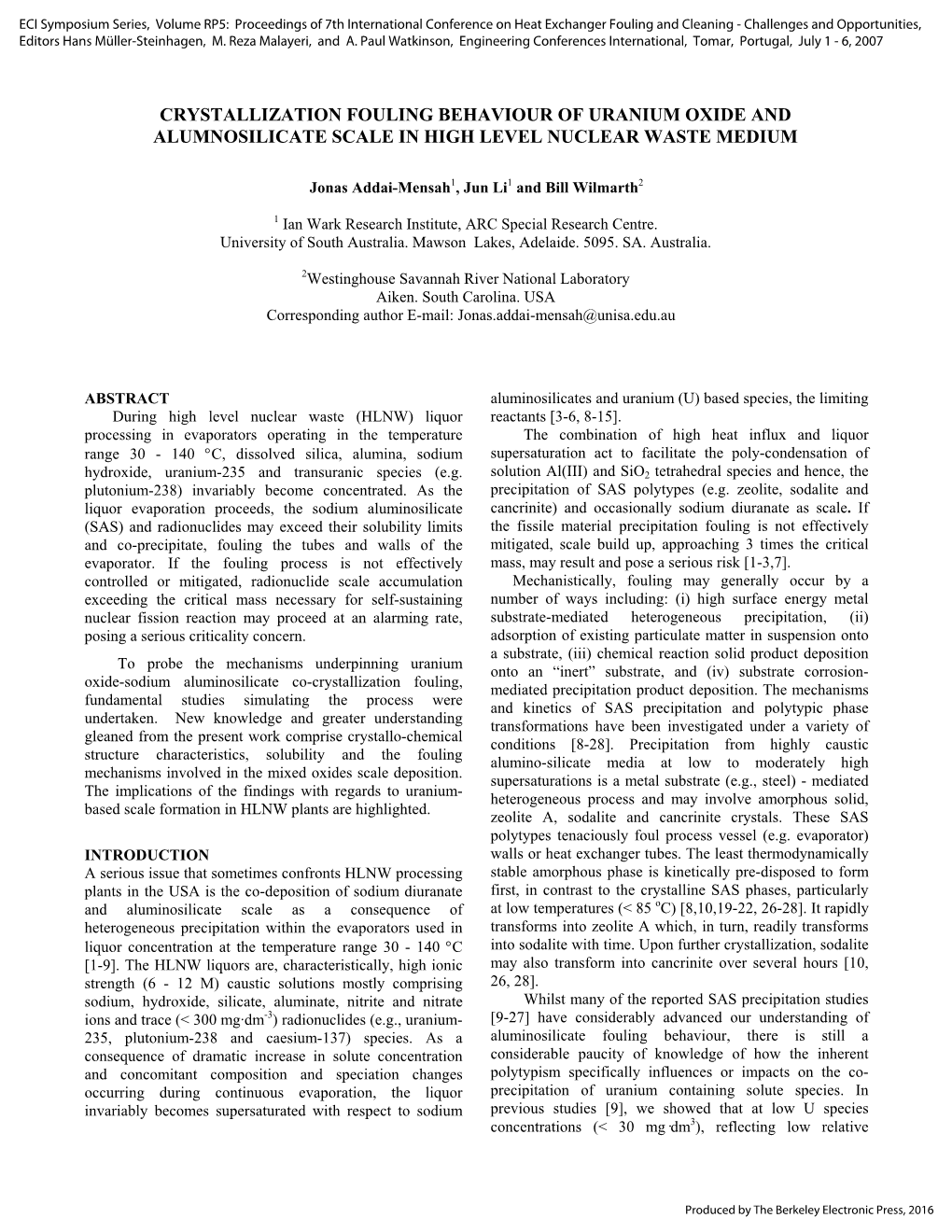
Load more
Recommended publications
-
In Situ Leach (ISL) Mining of Uranium
In Situ Leach (ISL) Mining of Uranium (June 2009) l Most uranium mining in the USA and Kazakhstan is now by in situ leach methods, also known as in situ recovery (ISR). l In USA ISL is seen as the most cost effective and environmentally acceptable method of mining, and Australian experience supports this. l Australia's first ISL uranium mine is Beverley, which started operation late in 2000. The proposal for Honeymoon has government approval and it is expected to be operating in 2008. Conventional mining involves removing mineralised rock (ore) from the ground, breaking it up and treating it to remove the minerals being sought. In situ leaching (ISL), also known as solution mining, or in situ recovery (ISR) in North America, involves leaving the ore where it is in the ground, and recovering the minerals from it by dissolving them and pumping the pregnant solution to the surface where the minerals can be recovered. Consequently there is little surface disturbance and no tailings or waste rock generated. However, the orebody needs to be permeable to the liquids used, and located so that they do not contaminate ground water away from the orebody. Uranium ISL uses the native groundwater in the orebody which is fortified with a complexing agent and in most cases an oxidant. It is then pumped through the underground orebody to recover the minerals in it by leaching. Once the pregnant solution is returned to the surface, the uranium is recovered in much the same way as in any other uranium plant (mill). In Australian ISL mines (Beverley and the soon to be opened Honeymoon Mine) the oxidant used is hydrogen peroxide and the complexing agent sulfuric acid. -
Precipitation of Aluminum Containing Species in Tank Wastes
PNNL-13881 Precipitation of Aluminum Containing Species in Tank Wastes S.V. Mattigod K.E. Parker D.T. Hobbs D.E. McCready April 2002 Prepared for the U.S. Department of Energy under Contract DE-AC06-76RL01830 PNNL-13881 DISCLAIMER This report was prepared as an account of work sponsored by an agency of the United States Government. Neither the United States Government nor any agency thereof, nor Battelle Memorial Institute, nor any of their employees, makes any warranty, express or implied, or assumes any legal liability or responsibility for the accuracy, completeness, or usefulness of any information, apparatus, product, or process disclosed, or represents that its use would not infringe privately owned rights. Reference herein to any specific commercial product, process, or service by trade name, trademark, manufacturer, or otherwise does not necessarily constitute or imply its endorsement, recommendation, or favoring by the United States Government or any agency thereof, or Battelle Memorial Institute. The views and opinions of authors expressed herein do not necessarily state or reflect those of the United States Government or any agency thereof. PACIFIC NORTHWEST NATIONAL LABORATORY operated by BATTELLE for the UNITED STATES DEPARTMENT OF ENERGY under Contract DE-AC06-76RL01830 This document was printed on recycled paper. (8/00 PNNL-13881 Precipitation of Aluminum Containing Species in Tank Wastes S. V. Mattigod D. T. Hobbs K. E. Parker D. E. McCready April 2002 Prepared for the U.S. Department of Energy under Contract DE-AC06-76RL01830 Pacific Northwest National Laboratory Richland, Washington 99352 Summary Aluminisilicate deposit buildup experienced during the tank waste volume-reduction process at the Savannah River Site (SRS) required an evaporator to be shut down in October 1999. -
Comparative Study on Precipitation Methods of Yellow
Precipitation and purification of uranium from rock phosphate Elshafeea H. Y. Abow Slama1, Etemad Ebraheem2 and Adam K. Sam1 1Sudan Atomic Energy Commission P.O. Box 3001, Khartoum-Sudan 2 Sinner University ABSTRACT This study was carried-out to leach uranium from rock phosphate using sulphuric acid in the presence of potassium chlorate as an oxidant and to investigate the relative purity of different forms of yellow cakes produced with ammonia {( NH 4 )2 U2O7 }, magnesia (UO3.xH 2O ) and sodium hydroxide Na2U 2O7 as precipitants, as well as purification of the products with TBP extraction and matching its impurity levels with specifications of the commercial products. Alpha-particle spectrometry was used for determination of activity concentration of uranium isotopes (234U and 238U) in rock phosphate, resulting green phosphoric acid solution, and in different forms of the yellow cake from which the equivalent mass concentration of uranium was deduced. Likewise, atomic absorption spectroscopy (AAS) was used for determination of impurities (Pb, Ni, Cd, Fe, Zn, Mn, and Cu). On the average, the equivalent mass concentration of uranium was 119.38±79.66 ppm (rock phosphate) and 57.85±20.46 ppm (green solution) with corresponding low percent of dissolution (48%) which is considered low. The isotopic ratio (234U: 238U) in all stages of hydrometallurgical process was not much differ from unity indicating lack of fractionation. Upon comparing the levels of impurities in different form of crude yellow cakes, it was found that the lowest levels were measured in UO3.xH2O. This implies that saturated magnesia is least aggressive relative to other precipitants and gives relatively pure crude cake. -
Uranium, Cesium, and Mercury Leaching and Recovery from Cemented Radioactive Wastes in Sulfuric Acid and Iodide Media
Article Uranium, Cesium, and Mercury Leaching and Recovery from Cemented Radioactive Wastes in Sulfuric Acid and Iodide Media Nicolas Reynier 1,*, Rolando Lastra 1, Cheryl Laviolette 1, Jean-François Fiset 1, Nabil Bouzoubaâ 1 and Mark Chapman 2 Received: 28 September 2015 ; Accepted: 10 November 2015 ; Published: 20 November 2015 Academic Editor: Mostafa Fayek 1 CanmetMINING, Natural Resources Canada, 3484 Limebank Rd., Ottawa, ON K1A 0E4, Canada; [email protected] (R.L.); [email protected] (C.L.); jean-francois.fi[email protected] (J.-F.F.); [email protected] (N.B.) 2 Canadian Nuclear Laboratories, Chalk River Laboratories, Plant Road, Chalk River, ON K0J 1 J0, Canada; [email protected] * Correspondence: [email protected]; Tel.: +1-613-954-5602; Fax: +1-613-954-6929 Abstract: The Canadian Nuclear Laboratories (CNL) is developing a long-term management strategy for its existing inventory of solid radioactive cemented wastes, which contain uranium, mercury, fission products, and a number of minor elements. The composition of the cemented radioactive waste poses significant impediments to the extraction and recovery of uranium using conventional technology. The goal of this research was to develop an innovative method for uranium, mercury and cesium recovery from surrogate radioactive cemented waste (SRCW). Leaching using sulfuric acid and saline media significantly improves the solubilization of the key elements from the SRCW. Increasing the NaCl concentration from 0.5 to 4 M increases the mercury solubilization from 82% to 96%. The sodium chloride forms a soluble mercury complex when mercury is present as HgO or metallic mercury but not with HgS that is found in 60 ˝C cured SRCW. -
Modification of Base-Side 99Mo Production Processes for Leu Metal-Foil Targets
MODIFICATION OF BASE-SIDE 99MO PRODUCTION PROCESSES FOR LEU METAL-FOIL TARGETS G. F. Vandegrift, R. A. Leonard, S. Aase, J. Sedlet, Y. Koma, C. Conner, C. R. Clark, and M. K. Meyer Argonne National Laboratory Argonne, Illinois, and Idaho Falls, Idaho, U.S.A. ABSTRACT Argonne National Laboratory is cooperating with the National Atomic Energy Commission of the Argentine Republic (CNEA) to convert their 99Mo production process, which uses high enriched uranium (HEU), to low-enriched uranium (LEU). The program is multifaceted; however, discussed in this paper are (1) results of laboratory experiments to develop means for substituting LEU metal-foil targets into the current process and (2) preparation of uranium-alloy or uranium-metal/aluminum-dispersion targets. Although 99Mo production is a multi-step process, the first two steps (target dissolution and primary molybdenum recovery) are by far the most important in the conversion. Commonly, once molybdenum is separated from the bulk of the uranium, the remainder of the process need not be modified. Our results show that, up to this point in our study, conversion of the CNEA process to LEU appears viable. INTRODUCTION A number of current producers dissolve uranium-aluminide/aluminum-dispersion plates in alkaline solution as an initial step to recovering fission-product 99Mo from irradiated high- enriched uranium (HEU). These producers include Argentine Comisión Nacional de Energía Atómica (CNEA), Institut National des Radioéléments (IRE), Mallinckrodt, and the Atomic Energy Corporation of South Africa Limited (AEC). Argonne National Laboratory (ANL) has begun a cooperation with one of these producers, CNEA, to convert their process to low- enriched uranium (LEU). -
Preparation of Highly Pure Thorium Nitrate Via Thorium Sulfate And
L Journal of Alloys and Compounds 323±324 (2001) 53±56 www.elsevier.com/locate/jallcom Preparation of highly pure thorium nitrate via thorium sulfate and thorium peroxide Alcõdio AbraoÄ * , Antonio Alves de Freitas, Fatima Maria Sequeira de Carvalho Instituto de Pesquisas Energeticas e Nucleares (IPEN), ComissaoÄ Nacional de Energia Nuclear (CNEN), Travessa R, 400 Cidade Universitaria -USP, CEP 05508-900, SaoÄ Paulo, Brazil Abstract A simple alternative and selective method has been proposed for the preparation of thorium nitrate using as raw material a hydrated crystalline technical grade thorium sulfate. This salt was produced industrially [1] from the alkaline chemical processing of monazite sand in S. Paulo. From a crude thorium hydroxide as the raw material containing uranium and rare earth elements was prepared a technical grade thorium sulfate [Th(SO42 ) .9H 2 O]. A typical analysis of this salt had shown the following composition: ThO223 47±53%, R O (rare earth oxides) 0.5±0.9%, and UO3 0.01% and minor amounts of iron, titanium, phosphorus, and silicon oxides. The thorium sulfate is dissolved into water and the thorium peroxide is precipitated from acidic medium by addition of hydrogen peroxide. The thorium peroxide is ®ltered, washed and ®nally dissolved with nitric acid. Samples of the thorium peroxide were dried and ®red to ThO2 and aliquot of the thorium nitrate solution was evaporated to dryness and calcined to obtain the ThO22 . Both ThO have high purity (.99.5%). The content of total rare earth elements is very low (0.23% as oxide). Uranium was not detected. The great majority of the RE is precipitated and recovered from the ®ltrate by oxalic acid. -
Waste Preparation and Transport Chemistry: Results of the FY 2000 Studies
OAKRIDGE ORNL/TM-20001298 NATIONALLABORATORY MANAGED BY UT-BATTELLE FOR THE DEPARTMENT OF ENERGY Waste Preparation and Transport Chemistry: Results of the FY 2000 Studies R. D. Hunt T. A. Dillow J. R. Parrott, Jr. J. C. Schryver C. F. Weber 7. D. Welch Tanks Focus Area ’ - UT-BATTELLE ORNC-27 (4.00) -. ORNL/T-M-20001298 f Chemical Technology Division Waste Preparation and Transport Chemistry: Results of the FY 2000 Studies R. D. Hunt J. C. Schryver* T. A. Dillow C. F. Webert J. R. Parrott, Jr. T. D. Welch *Computer Science and Mathematics Division, ORNL +Computational Physics and Engineering Division, ORNL December 2000 E . Preparedfor the Tanks Focus Area DOE Offke of Science and Technology in fulfillment of Milestones A. 1.1-2 and A.2.1-3 of TTP OR16WT41 Preparedby the OAK RIDGE NATIONAL LABORATORY Oak Ridge, Tennessee3783 l-6285 managed by UT-BATTELLE, LLC . for the U.S. DEPARTMENT OF ENERGY under contract DE-AC05-OOOR22725 CONTENTS LIST OF TABLES . , . v 1 LISTOFFIGURES . v EXECUTIVE SUMMARY ....................................................... vii KEYOBSERVATIONS ......................................................... ix 1. INTRODUCTION ... ..I ...................................................... 1 1.1 PIPELINE PLUGS AT HANFORD ........................................... 1 1.2 PIPELINE PLUG AT THE SAVANNAH RIVER SITE ........................... 1 1.3 PRIOR STUDIES ON SOLIDS FORMATION BY THE TANKS FOCUS AREA ...... 2 2. VISCOSITY TESTS ........................................................... 3 2.1 VISCOSITY SAMPLES .................................................... 3 2.2 VISCOSITY DURING GRADUAL WASTE COOLING .......................... 4 2.3 VISCOSITY AFTER A SIMULATED PUMP FAILURE. ......................... 6 2.4 VISCOSITY AFTER SIMULATED SALTCAKE DISSOLUTION ................. 11 2.5 DISCUSSION OF THE VISCOSITY RESULTS . , . 11 3. MODELING OF THE VISCOSITY RESULTS . , . 14 3.1 PRELIMINARYCONSIDERATIONS ...................................... -
Honeymoon Project
HONEYMOON PROJECT Application Licence to Mine or Mill Radioactive Ore Radiation Protection and Control Act 1982 This information is provided in support of an application for a commercial licence under the Radiation Protection and Control Act 1982 to Mine or Mill Radioactive Ores of the Honeymoon deposit 1 CONTENTS 1 SUMMARY 4 2 PROPONENT DETAILS 6 3 BACKGROUND TO PROJECT 7 4 IN-SITU LEACH 11 5 GEOLOGICAL ENVIRONMENT 14 6 PREVIOUS MINING ACTIVITIES AT HONEYMOON 17 7 THE PROPOSED PROJECT 19 8 PLANT LAYOUT 30 9 RADIONUCLIDE BALANCE 38 10 QUANTITIES OF RADIOACTIVE WASTE PRODUCED 41 11 SUPPORTING DOCUMENTS 41 2 FIGURES 1.1 Honeymoon Project Location 5 4.1 ISL Wellfield Schematic 12 4.2 Schematic of Process Plant Operation 13 5.1 Schematic Section Across Yarramba Paleochannel 14 5.2 Schematic Section Across the Honeymoon Mineralisation 14 5.3 Typical Drill Hole Log Through the Honeymoon Deposit 16 6.1 The 1982 Honeymoon Plant 17 6.2 Layout of the Honeymoon Site, 1999-2000 Leaching Tests 18 7.1 Plan of Proposed Operation 20 7.2 Location of Process Plant and Facilities 25 7.3 Schematic Flowsheet of the Honeymoon Plant 27 8.1 Preliminary Plant Layout 31 8.2 Site Layout Showing Pond Locations 35 8.3 Controlled and Supervised Areas 37 9.1 Radionuclide Balance 40 3 1 SUMMARY Southern Cross Resources Pty Ltd currently holds a Licence to Mine or Mill radioactive ore at the Honeymoon site on a non-commercial basis. This licence was initially issued to allow the company to undertake large scale in-situ leaching trials at Honeymoon. -
From Crude Sodium Diuranate by Interiv[Ediate Complex Formation by N
PREPARATION OF PURE U30. FROM CRUDE SODIUM DIURANATE BY INTERIV[EDIATE COMPLEX FORMATION BY N. S. KaUSm'~hVR~hD ~ V. V. DADAPE (Atomic Energy Establishment, Bombay, India) Rr November 16, 1956 (Communicated by Dr. H. J. Bhabha, v.R.s., v.^.sc.) SEV~~aATION of uranium from va¡ undesirable elements is usually done by solvent extractiorfl '2 and several other complexing proeedures. ~4 Bolton5 and Baker e have reported the formation of soluble complexes of the type M3UO~.F5 (M = K, NH4, whŸ are oxŸ by hydrogen peroxide in aqueous solutions to insoluble per-eompounds 7 of the type M4U40~Fe.xH~O. Preliminary studies have been made for the sep of uranium from thorium, rare e and iron, making use of the above complexes, and the results given below. Nitrate solutions of uranium, thorium, r earths and iron were mixed together and potassium fluoride (of ammonium fluo¡ was added slightly in excess of that required for complexing the above elements. Fluo¡ of tho¡ and rare earths got precipitated while those of uranium and iron remained in solution in the forra of soluble complexes. The precipitate was washed with water to recover aU uranium. Conditions of pH require to prevent precipitation of uranium together with thorium and rare earths fluo¡ were studied and the results given in Table I. The solution after the removal of tho¡ and rare earths was treated with enough hyrogen peroxide to precipitate the per salt (the composition of which is to be established) of the uranium complex M,UO,Fs. The in- fluence of pH on the complete precipitation of uranium free from iron was investigated and the results given in Table II. -
Caustic Soda
austic soda (sodium Insoluble metal hydroxides, hydroxide), often formed by reaction of caustic referred to as caustic soda with wastewater metals, or lye, is the principal are removed physically as part of Cproduct that accompanies the wastewater pre-treatment chlorine production. (For more process. details on chlorine, please see Caustic soda also may be used to the insert Chlorine Chemistry’s neutralize acid mine drainage. Role in our Daily Lives.) When air and water contact newly exposed sulphur- Caustic soda is co-generated with chlorine by electrolysis of containing minerals during mining operations, the minerals sodium chloride brine using one of three rapidly oxidize, releasing damaging quantities most common industrial manufacturing Caustic Soda of acidity, metals and other chemical technologies. (For more details, please see End Uses components to the environment. Acid mine the insert Chlor-Alkali Manufacturing drainage is a major environmental hazard. Processes.) In the electrolysis process, it is Caustic soda is particularly effective for simultaneously produced in a fixed ratio neutralizing low flows of acid mine drainage of 1 tonne of chlorine and 1.12 tonnes of in remote locations and for treating flows caustic. In 1998, worldwide production having high manganese content. capacity of caustic soda was approximately 54 million metric tonnes. Organics 18% Helping keep us clean Pulp & paper 16% Caustic soda is used in a wide variety of Caustic soda plays a significant role in the Inorganics 15% industrial applications. It is valued for its Soap & detergents, 10% manufacture of powder soaps, bar soaps and neutralizing power and is used to control textiles detergents, with a considerable amount being and remediate acidic environmental Alumina 8% used in the production of industrial and pollution. -
Evaluation of the 1943Hto# 1946 Ilid Liquid Effluent Discharge from The
-J-J-.3? _- r, /, i ;. - NY-%-3 / 0 Aerospace Report No. P i ATR-82 (796344-2 Aq, is y !i,’ m ilid F Evaluation of the 1943Hto#1946 Liquid Effluent Discharge P From the Linde Air Products Company F Ceramics Plant ?- December 198 I P m ?- Prepared for c Office of Operational Safety Assistant Secretary for Environmental Protection, Safety, and Emergency Preparedness m U.S. DEPARTMENT OF ENERGY P Prepared by P Environment and Conservation Directorate Eastern Technical Division CII THE AEROSPACE CORPORATION Germantown, Maryland (I Contract No. DE-ACOP-81EV10532 pl F F- Aerospace Report No. ATR-82(7963-04)-2 EVALUATION OF THE 1943-TO-1946 LIQUID EFFLUENT DISCHARGE FROM THE LINDE AIR PRODUCTS COMPANY CERAMICS PLANT December 1981 I- Prepared for Office of Operational Safety Assistant Secretary for Environmental Protection, ,- Safety, and Emergency Preparedness U.S. DEPARTMENT OF ENERGY Prepared by Environment and Conservation Directorate Eastern Technical Division THE AEROSPACE CORPORATION L. German town, Maryland Contract No. DE-ACOl-81EV10532 ---- ,_ - -.- L -- Aerospace Report No. ATR-82(7963-041-2 EVALUATION OF THE 1943-TO-1946 LIQUID EFFLUENT DISCHARGE FROM THE LINDE AIR PRODUCTS COMPANY CERAMICS PLANT Prepared by Approved by ~ZiAz ~~2/3Jm-L- Andrew Wall0 III Frank W o Ho& Project Engineer Systems Director Control Technology Section Environmental Controls and Analysis Office Edmund A. Vierzba A. Might Abbott Control Technology Section Principal Director Environment and Conservation Directorate ~i!L&z- & Gerald N. Roberts Technology Assessments Section .^. _“_ ._ --.. .-. FOREWORD .- This report presents an evaluation of the consequences of using onsite wells and sewers for disposing of liquid wastes from a uranium extraction process operated from 1943 to 1946 by the Linde Air Products Company, Tonawanda, New York. -
Purification of Sodium Diuranate Produced from Gabal Gattar (Gii) Mineralization Using Tri Butyl Phosphate
Eleventh Arab Conference Oil the PeacefuJ Uses of Atomic Energy. Khartoum. Sudan. 16-20 Decanter 2012 PURIFICATION OF SODIUM DIURANATE PRODUCED FROM GABAL GATTAR (GII) MINERALIZATION USING TRI BUTYL PHOSPHATE JK. F. 2G. G. Mohamed 1w. M. Morsi 1Nuclear Materials Authority 2Faculty of Sciences^ Cairo University ABSTRACT Purification of the prepared sodium diuranate product to almost a ue was properly applied ؟nuclear purity grade, the solvent extraction techni to study the various relevant optimum conditions. For this purpose,organophosphorus solvents has been used; namely tri butyl phosphate (TBP). the produced sodium di-uranate contains only a small amount of the deleterious impurities which can be purified by solvent was dissolved in nitric acid so آ ﻣ ﻷ2 س ue. The prepared ؟exfraction techni that the free acidity of the obtained solution attained 3M and its uranium content assayed 202g/L. Nitrate solution from the TBP route used to prepare UO3 from the former, it was first evaporated at 95°c to decrease its volume to only 25% and which would increase uranium concentration. By proper cooling greenish yellow ؛uranyl nifrate hexa hydrate crystals were formed and which were then let ٠ for air drying before denifration at 280-300°C for 4 hr !.INTRODUCTION Several promising uranium occurrences have been discovered in Geble Gattar uranium prospect area in the Eastern Desert and are indeed hosted in younger granites (G-I to G-XII1) except GV occurrence, which is located in El-Hammamat sedimentary rocks. In this mineralization, uranium is mainly found as secondary minerals which are essentially represented by uranophane and beta uranophane .( and N4ahmoud؛J؛Sayyah and Attawiya) Apart from the recently developed dry refining processes which are almost devoted for producing directly the reactor grade UF6 required for the enrichment processes and in which the refining and conversion procedures are combined, the wet refining processes do not involve conversion.