Hydrodynamics and Mass Transfer of Rotating Packed Beds for CO2 Capture
Total Page:16
File Type:pdf, Size:1020Kb
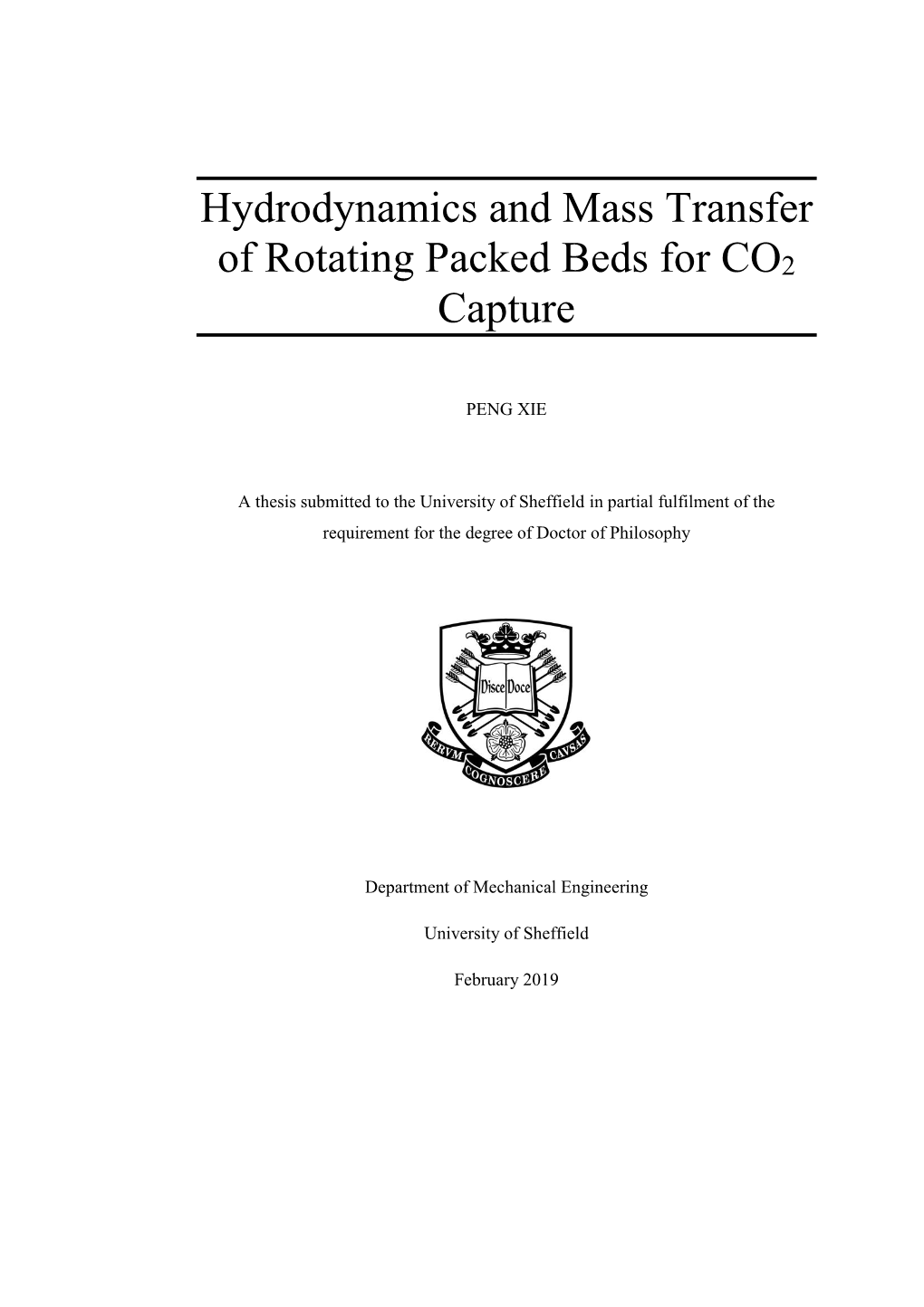
Load more
Recommended publications
-
A Parametric Investigation of Gas Bubble Growth and Pinch-Off Dynamics from Capillary-Tube Orifices in Liquid Pools
A Parametric Investigation of Gas Bubble Growth and Pinch-Off Dynamics from Capillary-Tube Orifices in Liquid Pools A Thesis submitted to the Division of Research and Advanced Studies of the University of Cincinnati in partial fulfillment of the requirements for the degree of MASTER OF SCIENCE In the department of Mechanical, Industrial and Nuclear Engineering of the College of Engineering and Applied Sciences 2012 By Deepak Saagar Kalaikadal B.E. Mechanical Engineering Anna University, Chennai, Tamil Nadu, India, 2007 Committee Chair: Dr. Raj M. Manglik ABSTRACT The air-bubble dynamics phenomena in adiabatic liquid pools has been studied so as to present a better understanding of the parameters which that govern the process of ebullience, bubble growth and departure from a submerged capillary-tube orifice. The orifice diameter is found to directly dictate the bubble departure diameter, and the pinch-off is controlled by a characteristic neck-length. To study the role of orifice size on the growth and departure of adiabatic single bubbles, experiments were performed with different diameter capillary tubes submerged in of distilled de-ionized water as well as some other viscous liquids. A correlation has been developed based on the experimental data of this study along with those reported by several others in the literature. The predictions of this correlation agree very well with measured data for water as well as several other more viscous liquids. It is also found that the bubble departure diameter is the same as the orifice diameter when the latter equals twice the capillary length. The phenomenon of bubble necking and departure was explored experimentally and through a scaling analysis. -
10. Notations
92 10. Notations 10. Notations Latin Symbols A Pre-exponential factor in the Arrhenius equation L/(mol s) A Debye-Hückel parameter kg1/2mol-1/2 2 Afilm Surface area of the liquid film on the tubes m 2 Ajets Surface area of the water jets between the tubes m 2 APh Phase interface area m ai Activity of the component i - b Sum of the ion and gas specific parameters m3/kmol 3 b+ Ion specific parameter for cations m /kmol 3 b- Ion specific parameter for anions m /kmol 3 bG Gas specific parameter m /kmol 3 Ci Concentration of the component i mol/m C2 Constant in equation (5.46) - CF Concentration Factor - Cl Chlorinity g/kg 2 DiL Diffusion coefficient of the component i in the solution L m /s di Inside tube diameter m do Outside tube diameter m djets diameter of the jets m E Enhancement factor - EA Activation energy kJ/mol g Gravitational acceleration m/s2 3 Hij Henry’s law coefficient of the gas i in the solution j mol/(m bar) h Heat transfer coefficient W/(m2 K) h Sum of the ion and gas specific parameters kg/mol, L/mol h+ Ion specific parameter for cations kg/mol, L/mol h- Ion specific parameter for anions kg/mol, L/mol hG Gas specific parameter kg/mol, L/mol I Ionic strength mol/kg [i] Concentration of the component i mol/kg solution [i]SW Concentration of the component i that is free and involved in ion-pairs in seawater mol/kg solution 10. -
Dns of Single Bubble Motion in Liquid Metal and the Influence of a Magnetic Field
DNS OF SINGLE BUBBLE MOTION IN LIQUID METAL AND THE INFLUENCE OF A MAGNETIC FIELD Stephan Schwarz Institute of Fluid Mechanics TU Dresden 01062 Dresden, Germany [email protected] Jochen Frohlich¨ Institute of Fluid Mechanics TU Dresden 01062 Dresden, Germany [email protected] ABSTRACT of the liquid, Dr density difference between the phases, r f The ascent of a single Argon bubble in a column of quies- density of the surrounding fluid and s surface tension. For cent liquid metal is studied by means of direct numerical sim- gas bubbles in liquid metals high Re ≈ 3000 − 5000 and ulation using an immersed boundary method. An additional We ≈ 3 are encountered resulting in an ellipsoidal whobbling magnetic field in the direction of gravity is shown to influ- shape according to the regime map of Clift et al. (1978). ence the bubble dynamics substantially. An increase in time- The strength of a magnetic field can be characterized by the 2 averaged bubble Reynolds number is found for large bubbles magnetic interaction parameter N = se B deq= r f ure f with and a decrease for small bubbles when increasing the mag- se being the electrical conductivity, B the magnetic field p netic interaction parameter. The bubble Strouhal number as a strength and ure f = gdeg the reference velocity for a rising dimensionless frequency is reduced with magnetic field for all bubble. bubbles considered. The zig-zag trajectory in the purely hy- drodynamic case becomes more rectilinear and vortical struc- tures in the bubble wake are considerably damped. COMPUTATIONAL METHOD Simulations were conducted with the multiphase code PRIME (Kempe & Frohlich,¨ 2010a,b) which is based on a INTRODUCTION staggered grid arrangement in cartesian coordinates employ- The combination of multiphase and magneto- ing a second order finite volume method. -
SASO-ISO-80000-11-2020-E.Pdf
SASO ISO 80000-11:2020 ISO 80000-11:2019 Quantities and units - Part 11: Characteristic numbers ICS 01.060 Saudi Standards, Metrology and Quality Org (SASO) ----------------------------------------------------------------------------------------------------------- this document is a draft saudi standard circulated for comment. it is, therefore subject to change and may not be referred to as a saudi standard until approved by the boardDRAFT of directors. Foreword The Saudi Standards ,Metrology and Quality Organization (SASO)has adopted the International standard No. ISO 80000-11:2019 “Quantities and units — Part 11: Characteristic numbers” issued by (ISO). The text of this international standard has been translated into Arabic so as to be approved as a Saudi standard. DRAFT DRAFT SAUDI STANDADR SASO ISO 80000-11: 2020 Introduction Characteristic numbers are physical quantities of unit one, although commonly and erroneously called “dimensionless” quantities. They are used in the studies of natural and technical processes, and (can) present information about the behaviour of the process, or reveal similarities between different processes. Characteristic numbers often are described as ratios of forces in equilibrium; in some cases, however, they are ratios of energy or work, although noted as forces in the literature; sometimes they are the ratio of characteristic times. Characteristic numbers can be defined by the same equation but carry different names if they are concerned with different kinds of processes. Characteristic numbers can be expressed as products or fractions of other characteristic numbers if these are valid for the same kind of process. So, the clauses in this document are arranged according to some groups of processes. As the amount of characteristic numbers is tremendous, and their use in technology and science is not uniform, only a small amount of them is given in this document, where their inclusion depends on their common use. -
Buoyancy-Driven Bubbly Flows: Ordered and Free Rise at Small and Intermediate Volume Fraction Aurore Loisy, Aurore Naso, Peter Spelt
Buoyancy-driven bubbly flows: ordered and free rise at small and intermediate volume fraction Aurore Loisy, Aurore Naso, Peter Spelt To cite this version: Aurore Loisy, Aurore Naso, Peter Spelt. Buoyancy-driven bubbly flows: ordered and free rise at small and intermediate volume fraction. Journal of Fluid Mechanics, Cambridge University Press (CUP), 2017, 816, pp.94-141. 10.1017/jfm.2017.64. hal-01336649v2 HAL Id: hal-01336649 https://hal.archives-ouvertes.fr/hal-01336649v2 Submitted on 28 Mar 2017 HAL is a multi-disciplinary open access L’archive ouverte pluridisciplinaire HAL, est archive for the deposit and dissemination of sci- destinée au dépôt et à la diffusion de documents entific research documents, whether they are pub- scientifiques de niveau recherche, publiés ou non, lished or not. The documents may come from émanant des établissements d’enseignement et de teaching and research institutions in France or recherche français ou étrangers, des laboratoires abroad, or from public or private research centers. publics ou privés. This draft was prepared using the LaTeX style file belonging to the Journal of Fluid Mechanics 1 Buoyancy-driven bubbly flows: ordered and free rise at small and intermediate volume fraction Aurore Loisyyz, Aurore Naso and Peter D. M. Spelt Laboratoire de M´ecaniquedes Fluides et d'Acoustique, CNRS, Universit´eClaude Bernard Lyon 1, Ecole´ Centrale de Lyon, INSA de Lyon 36 avenue Guy de Collongue, 69134 Ecully´ cedex, France (Received xx; revised xx; accepted xx) Various expressions have been proposed previously for the rise velocity of gas bubbles for homogeneous steady bubbly flows, generally a monotonically decreasing function of the bubble volume fraction. -
A Global Stability Approach to Wake and Path Instabilities of Nearly
A global stability approach to wake and path instabilities of nearly oblate spheroidal rising bubbles José Carlos Cano-Lozano, Joël Tchoufag, Jacques Magnaudet, Carlo Martínez-Bazán To cite this version: José Carlos Cano-Lozano, Joël Tchoufag, Jacques Magnaudet, Carlo Martínez-Bazán. A global sta- bility approach to wake and path instabilities of nearly oblate spheroidal rising bubbles. Physics of Fluids, American Institute of Physics, 2016, vol. 28 (n° 1), pp. 014102. 10.1063/1.4939703. hal-01330745 HAL Id: hal-01330745 https://hal.archives-ouvertes.fr/hal-01330745 Submitted on 13 Jun 2016 HAL is a multi-disciplinary open access L’archive ouverte pluridisciplinaire HAL, est archive for the deposit and dissemination of sci- destinée au dépôt et à la diffusion de documents entific research documents, whether they are pub- scientifiques de niveau recherche, publiés ou non, lished or not. The documents may come from émanant des établissements d’enseignement et de teaching and research institutions in France or recherche français ou étrangers, des laboratoires abroad, or from public or private research centers. publics ou privés. Open Archive TOULOUSE Archive Ouverte (OATAO) OATAO is an open access repository that collects the work of Toulouse researchers and makes it freely available over the web where possible. This is an author-deposited version published in: http://oatao.univ-toulouse.fr/ Eprints ID : 15911 To link to this article : DOI:10.1063/1.4939703 URL : http://dx.doi.org/10.1063/1.4939703 To cite this version : Cano-Lozano, José Carlos and Tchoufag, Joël and Magnaudet, Jacques and Martínez-Bazán, Carlo A global stability approach to wake and path instabilities of nearly oblate spheroidal rising bubbles. -
Drag and Lift Forces on Particles in a Rotating Flow
J. Fluid Mech., page 1 of 31 c Cambridge University Press 2009 1 doi:10.1017/S0022112009991881 Drag and lift forces on particles in a rotating flow J. J. B L U E M I N K1, D. LOHSE1†, A. PROSPERETTI1,2 AND L. VAN WIJNGAARDEN1 1Faculty of Science and Technology and J. M. Burgers Centre for Fluid Dynamics, University of Twente, PO Box 217, 7500 AE Enschede, The Netherlands 2Department of Mechanical Engineering, The John Hopkins University, Baltimore, MD 21218, USA (Received 23 December 2008; revised 29 August 2009; accepted 31 August 2009) A freely rotating sphere in a solid-body rotating flow is experimentally investigated. When the sphere is buoyant, it reaches an equilibrium position from which drag and lift coefficients are determined over a wide range of particle Reynolds numbers (2 6 Re 6 1060). The wake behind the sphere is visualized and appears to deflect strongly when the sphere is close to the cylinder axis. The spin rate of the sphere is recorded. In fluids with low viscosity, spin rates more than twice as large as the angular velocity of the cylinder can be observed. By comparing numerical results for a fixed but freely spinning sphere with a fixed non-spinning sphere for Re 6 200, the effect of the sphere spin on the lift coefficient is determined. The experimentally and numerically determined lift and drag coefficients and particle spin rates all show excellent agreement for Re 6 200. The combination of the experimental and numerical results allows for a parameterization of the lift and drag coefficients of a freely rotating sphere as function of the Reynolds number, the particle spin and the location of the particle with respect to the cylinder axis. -
Validation of Dimensionless Parameters for Distinguishing Between Homogeneous and Bubbling Fluidizations
Open Journal of Fluid Dynamics, 2021, 11, 81-97 https://www.scirp.org/journal/ojfd ISSN Online: 2165-3860 ISSN Print: 2165-3852 Validation of Dimensionless Parameters for Distinguishing between Homogeneous and Bubbling Fluidizations Kenya Kuwagi1, Atsuto Kogane1, Yui Sasaki1, Hiroyuki Hirano2 1Department of Mechanical Systems Engineering, Okayama University of Science, Okayama, Japan 2Department of Applied Chemistry and Biotechnology, Okayama University of Science, Okayama, Japan How to cite this paper: Kuwagi, K., Ko- Abstract gane, A., Sasaki, Y. and Hirano, H. (2021) Validation of Dimensionless Parameters for The difference between homogeneous and bubbling fluidization behaviors Distinguishing between Homogeneous and has been studied for the past 70 years, where several researchers have re- Bubbling Fluidizations. Open Journal of ported on the influence of interparticle forces in fluidization. Although inter- Fluid Dynamics, 11, 81-97. https://doi.org/10.4236/ojfd.2021.112006 particle forces such as van der Waals forces are evident in a real system, these forces are not the determinant in homogeneous fluidization, which can be Received: March 26, 2021 simulated without any interparticle forces. In our previous study, the differ- Accepted: June 8, 2021 Published: June 11, 2021 ence in fundamental mechanisms of the two fluidization states was analyti- cally determined with a dimensionless gravity term, comprising the Reynolds Copyright © 2021 by author(s) and number, Archimedes number, and density ratio. Nevertheless, some re- Scientific Research Publishing Inc. searchers insist that interparticle forces are dominant and a hydrodynamic This work is licensed under the Creative Commons Attribution International force is not dominant. In this study, a dimensional analysis was applied to License (CC BY 4.0). -
Dimensionless Numbers in the Analysis of Hydrodynamic Instability of Interface Steel - Slag at Microscale in Refining Processes
FONDATĂ 1976 THE ANNALS OF “DUNAREA DE JOS” UNIVERSITY OF GALATI. FASCICLE IX. METALLURGY AND MATERIALS SCIENCE N0. 4 – 2010, ISSN 1453 – 083X DIMENSIONLESS NUMBERS IN THE ANALYSIS OF HYDRODYNAMIC INSTABILITY OF INTERFACE STEEL - SLAG AT MICROSCALE IN REFINING PROCESSES Petre Stelian NITA ”Dunarea de Jos” University of Galati email: pnita @ugal.ro ABSTRACT In evaluation of the local hydrodynamics of interface, in steel-slag refining processes influenced by solutal effects, adequate scales of length and time satisfying certain conditions are necessary to get a correct and suggestive image of the weight of factors possible to be used in industrial technologies. These could be obtained based on already established common dimensionless numbers but carefully applied in a specific manner, taking into consideration particularities of the established interface and the main involved process. Based of the general philosophy of building dimensionless artificial conglomerates, a new dimensionless group Ni = Ma ⋅ Bo is proposed in this paper as a consequence of needs to evaluate particularly the effects of capillarity actions at interface, especially of solutal origin, in presence of other physico-chemical and physical actions, especially when the effects of capillarity prevail over all others. KEYWORDS: steel refining, hydrodynamic instability of interface, length scale, time scale, dimensionless numbers. 1. Introduction extend because of the final purpose of the applied treatments which is to provide a certain appreciable Despite the fact that capillarity is recognized as high amount of refined steel, presenting a high level an important phenomenon in hydrodynamics of of purity concerning harmful elements. Oxygen, interface, only extremely rare and more than prudent sulphur and phosphorus are the most frequently target approaches of this subject are present in scientific and elements of treatments applied to steels using slags. -
Why a Falling Drop Does Not in General Behave Like a Rising Bubble
OPEN Why a falling drop does not in general SUBJECT AREAS: behave like a rising bubble FLUID DYNAMICS Manoj Kumar Tripathi, Kirti Chandra Sahu & Rama Govindarajan* MECHANICAL ENGINEERING Department of Chemical Engineering, Indian Institute of Technology Hyderabad, Yeddumailaram 502 205, Andhra Pradesh, India. Received 9 January 2014 Is a settling drop equivalent to a rising bubble? The answer is known to be in general a no, but we show that Accepted when the density of the drop is less than 1.2 times that of the surrounding fluid, an equivalent bubble can be 24 March 2014 designed for small inertia and large surface tension. Hadamard’s exact solution is shown to be better for this than making the Boussinesq approximation. Scaling relationships and numerical simulations show a Published bubble-drop equivalence for moderate inertia and surface tension, so long as the density ratio of the drop to 24 April 2014 its surroundings is close to unity. When this ratio is far from unity, the drop and the bubble are very different. We show that this is due to the tendency for vorticity to be concentrated in the lighter fluid, i.e. within the bubble but outside the drop. As the Galilei and Bond numbers are increased, a bubble displays underdamped shape oscillations, whereas beyond critical values of these numbers, over-damped behavior Correspondence and resulting in break-up takes place. The different circulation patterns result in thin and cup-like drops but requests for materials bubbles thick at their base. These shapes are then prone to break-up at the sides and centre, respectively. -
Instabilities in Free-Surface Hartmann Flow at Low Magnetic Prandtl Numbers
J. Fluid Mech. (2009), vol. 000, pp. 1–61. c 2009 Cambridge University Press 1 doi:10.1017/S0022112009007824 Printed in the United Kingdom 1 Instabilities in free-surface Hartmann flow at low 2 magnetic Prandtl numbers 3 D. GIANNAKIS1†, R. ROSNER1,2,3 AND P. F. F I S C H E R3 4 1Department of Physics, University of Chicago, Chicago, IL 60637, USA 5 2Department of Astronomy and Astrophysics, University of Chicago, Chicago, IL 60637, USA 6 3Argonne National Laboratory, Argonne, IL 60439, USA 7 (Received 7 August 2008 and in revised form 15 April 2009) 8 We study the linear stability of the flow of a viscous electrically conducting capillary 9 fluid on a planar fixed plate in the presence of gravity and a uniform magnetic field, 10 assuming that the plate is either a perfect electrical insulator or a perfect conductor. 11 We first confirm that the Squire transformation for magnetohydrodynamics is 12 compatible with the stress and insulating boundary conditions at the free surface but 13 argue that unless the flow is driven at fixed Galilei and capillary numbers, respectively 14 parameterizing gravity and surface tension, the critical mode is not necessarily 15 two-dimensional. We then investigate numerically how a flow-normal magnetic 16 field and the associated Hartmann steady state affect the soft and hard instability 17 modes of free-surface flow, working in the low-magnetic-Prandtl-number regime of − 18 conducting laboratory fluids (Pm 6 10 4). Because it is a critical-layer instability 19 (moderately modified by the presence of the free surface), the hard mode exhibits 20 similar behaviour as the even unstable mode in channel Hartmann flow, in terms 21 of both the weak influence of Pm on its neutral-stability curve and the dependence 22 of its critical Reynolds number Rec on the Hartmann number Ha. -
Numerical Study of the Magnetic Damping Effect on the Sloshing of Liquid Oxygen in a Propellant Tank
fluids Article Numerical Study of the Magnetic Damping Effect on the Sloshing of Liquid Oxygen in a Propellant Tank Yutaro Furuichi *,† and Toshio Tagawa Department of Aeronautics and Astronautics, Tokyo Metropolitan University, Hino, Tokyo 191-0065, Japan; [email protected] * Correspondence: [email protected]; Tel.: +81-90-3735-4211 † Current address: Department of Aeronautics and Astronautics, The University of Tokyo, Bunkyo-ku, Tokyo 113-8656, Japan. Received: 27 April 2020; Accepted: 28 May 2020; Published: 1 June 2020 Abstract: Nowadays, the use of baffle plates is anticipated to be one of potential devices used to dampen the sloshing of propellant in rocket tanks. However, some of previous studies reported that the use of a baffle plate may cause larger pressure fluctuations in the tank. In this study, aiming at damping the sloshing without a baffle plate, we paid attention to the characteristic that liquid oxygen is paramagnetic and numerically investigated damping effect of a magnetic field when liquid oxygen sloshing occurs. An incompressible gas–liquid two-phase flow of gaseous oxygen and liquid oxygen was assumed in a spherical spacecraft tank with a diameter of 1 m in a non-gravitational field, and a triangular impact force was assumed to be imposed as the excitation force. In addition, an electric circular coil was placed outside the spherical tank to generate a static magnetic field. For the sake of simplicity, the effect of heat was not taken into consideration. As a result of computation, the sloshing was damped to a certain extent when the magnetic flux density at the coil center was 1.0 T, and a sufficient damping effect was obtained by setting it to 3.0 T.