A Catalog of Performance Objectives, Performance Conditions, and Performance Guides for Machine Tool Operations
Total Page:16
File Type:pdf, Size:1020Kb
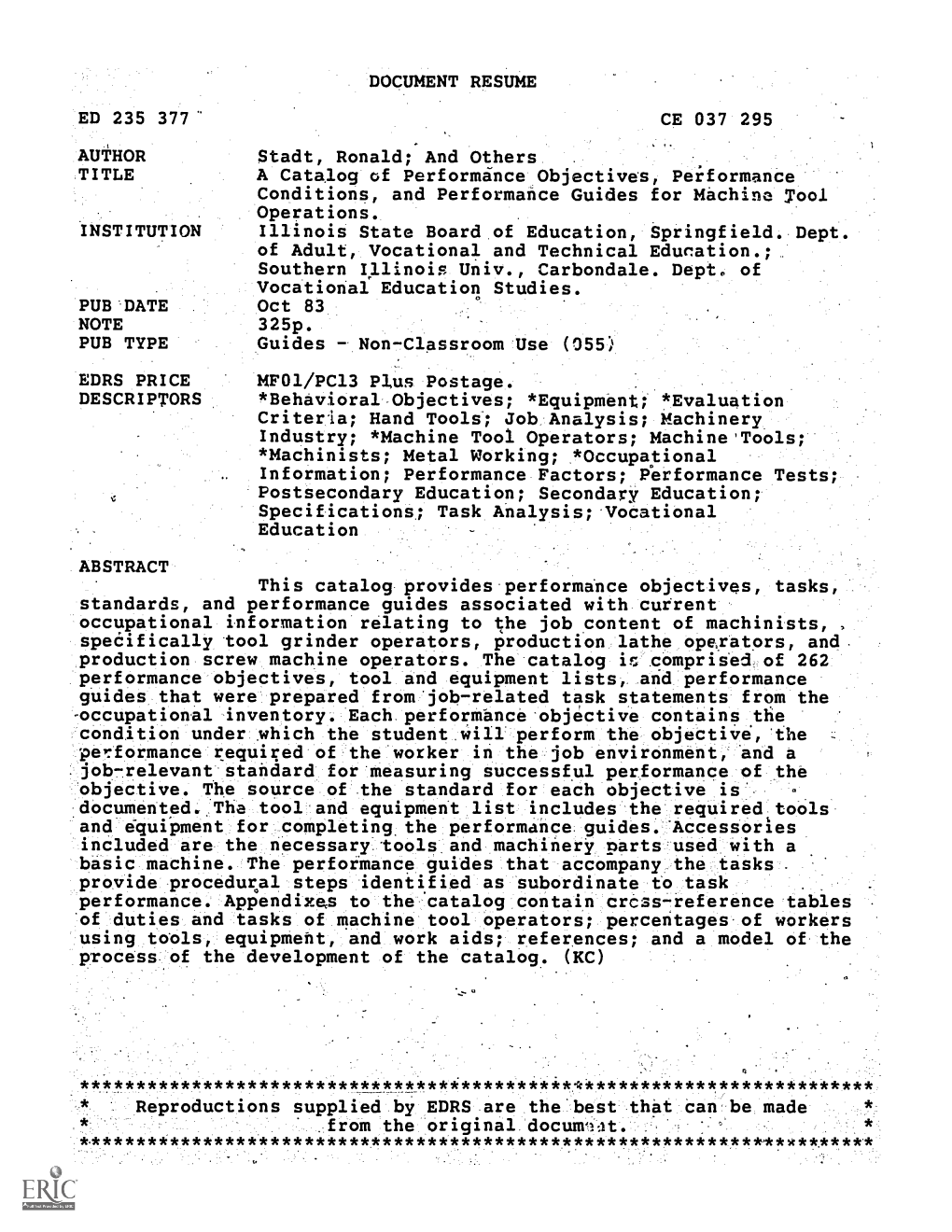
Load more
Recommended publications
-
The Essential Block Plane How to Choose and Use Woodworking’S Most Popular Trimmer
The Essential Block Plane How to choose and use woodworking’s most popular trimmer By Craig Bentzley It’s no secret that I love hand plane. Available in a variety of What to look for planes and own way too many in a block plane of them–about 250 at last it’s small, relatively inexpensive, As shown in Figure 1 and count. Many of them perform andconfigurations even kind of (as cute. shown But above),it’s Photo A, a block plane is a highly specialized tasks and fairly basic tool. That said, for don’t see use very often. But up and tuned, a good quality good performance, avoid cheap, there’s one type of plane that’s blockdefinitely plane not is aadept toy. Properly at handling set rudimentary hardware store a stand-out exception: the block all sorts of shop chores and is versions. The most important plane. In fact, when I’m asked likely to become one of your most features to look for in a good by beginning woodworkers used hand tools. I’ll discuss what what plane they should to look for in a good block plane, reliable and easy-to-use depth-of- start out with, that’s the one how to set one up, and how to cutblock adjustment, plane include and a an flat adjustable sole, a that always tops the list. use it to your best advantage. throat. You’ll also want the tool The ubiquitous block plane Once you make friends with to feel comfortable in your hand. is probably owned by more a block plane, you’ll wonder Unlike most bench planes, the people than any other hand how you did without one. -
Numerical Control (NC) Fundamentals
Lab Sheet for CNC Laboratory Department of Production Engineering and Metallurgy Prepared by: Dr. Laith Abdullah Mohammed Production Engineering – CNC Lab Lab Sheet Numerical Control (NC) Fundamentals What is Numerical Control (NC)? Form of programmable automation in which the processing equipment (e.g., machine tool) is controlled by coded instructions using numbers, letter and symbols - Numbers form a set of instructions (or NC program) designed for a particular part. - Allows new programs on same machined for different parts. - Most important function of an NC system is positioning (tool and/or work piece). When is it appropriate to use NC? 1. Parts from similar raw material, in variety of sizes, and/or complex geometries. 2. Low-to-medium part quantity production. 3. Similar processing operations & sequences among work pieces. 4. Frequent changeover of machine for different part numbers. 5. Meet tight tolerance requirements (compared to similar conventional machine tools). Advantages of NC over conventional systems: Flexibility with accuracy, repeatability, reduced scrap, high production rates, good quality. Reduced tooling costs. Easy machine adjustments. More operations per setup, less lead time, accommodate design change, reduced inventory. Rapid programming and program recall, less paperwork. Faster prototype production. Less-skilled operator, multi-work possible. Limitations of NC: · Relatively high initial cost of equipment. · Need for part programming. · Special maintenance requirements. · More costly breakdowns. Advantages -
Surveying and Drawing Instruments
SURVEYING AND DRAWING INSTRUMENTS MAY \?\ 10 1917 , -;>. 1, :rks, \ C. F. CASELLA & Co., Ltd II to 15, Rochester Row, London, S.W. Telegrams: "ESCUTCHEON. LONDON." Telephone : Westminster 5599. 1911. List No. 330. RECENT AWARDS Franco-British Exhibition, London, 1908 GRAND PRIZE AND DIPLOMA OF HONOUR. Japan-British Exhibition, London, 1910 DIPLOMA. Engineering Exhibition, Allahabad, 1910 GOLD MEDAL. SURVEYING AND DRAWING INSTRUMENTS - . V &*>%$> ^ .f C. F. CASELLA & Co., Ltd MAKERS OF SURVEYING, METEOROLOGICAL & OTHER SCIENTIFIC INSTRUMENTS TO The Admiralty, Ordnance, Office of Works and other Home Departments, and to the Indian, Canadian and all Foreign Governments. II to 15, Rochester Row, Victoria Street, London, S.W. 1911 Established 1810. LIST No. 330. This List cancels previous issues and is subject to alteration with out notice. The prices are for delivery in London, packing extra. New customers are requested to send remittance with order or to furnish the usual references. C. F. CAS ELL A & CO., LTD. Y-THEODOLITES (1) 3-inch Y-Theodolite, divided on silver, with verniers to i minute with rack achromatic reading ; adjustment, telescope, erect and inverting eye-pieces, tangent screw and clamp adjustments, compass, cross levels, three screws and locking plate or parallel plates, etc., etc., in mahogany case, with tripod stand, complete 19 10 Weight of instrument, case and stand, about 14 Ibs. (6-4 kilos). (2) 4-inch Do., with all improvements, as above, to i minute... 22 (3) 5-inch Do., ... 24 (4) 6-inch Do., 20 seconds 27 (6 inch, to 10 seconds, 403. extra.) Larger sizes and special patterns made to order. -
MICHIGAN STATE COLLEGE Paul W
A STUDY OF RECENT DEVELOPMENTS AND INVENTIONS IN ENGINEERING INSTRUMENTS Thai: for III. Dean. of I. S. MICHIGAN STATE COLLEGE Paul W. Hoynigor I948 This]: _ C./ SUPP! '3' Nagy NIH: LJWIHL WA KOF BOOK A STUDY OF RECENT DEVELOPMENTS AND INVENTIONS IN ENGINEERING’INSIRUMENTS A Thesis Submitted to The Faculty of MICHIGAN‘STATE COLLEGE OF AGRICULTURE AND.APPLIED SCIENCE by Paul W. Heyniger Candidate for the Degree of Batchelor of Science June 1948 \. HE-UI: PREFACE This Thesis is submitted to the faculty of Michigan State College as one of the requirements for a B. S. De- gree in Civil Engineering.' At this time,I Iish to express my appreciation to c. M. Cade, Professor of Civil Engineering at Michigan State Collegeafor his assistance throughout the course and to the manufacturers,vhose products are represented, for their help by freely giving of the data used in this paper. In preparing the laterial used in this thesis, it was the authors at: to point out new develop-ants on existing instruments and recent inventions or engineer- ing equipment used principally by the Civil Engineer. 20 6052 TAEEE OF CONTENTS Chapter One Page Introduction B. Drafting Equipment ----------------------- 13 Chapter Two Telescopic Inprovenents A. Glass Reticles .......................... -32 B. Coated Lenses .......................... --J.B Chapter three The Tilting Level- ............................ -33 Chapter rear The First One-Second.Anerican Optical 28 “00d011 ‘6- -------------------------- e- --------- Chapter rive Chapter Six The Latest Type Altineter ----- - ................ 5.5 TABLE OF CONTENTS , Chapter Seven Page The Most Recent Drafting Machine ........... -39.--- Chapter Eight Chapter Nine SmOnnB By Radar ....... - ------------------ In”.-- Chapter Ten Conclusion ------------ - ----- -. -
Drafting Machines and Parts Threof from Japan
DRAFTING MACHINES AND PARTS THEREOF FROM JAPAN Determination of the Commission in Investigation No. 731-T A-432 (Final} Under the Tariff Act of 1930, Together With the Information Obtained in the Investigation USITC PUBLICATION 2247 DECEMBER 1989 United States International Trade Commission Washington, DC 20436 UNITED STATES INTERNATIONAL TRADE COMMISSION COMMISSIONERS Anne E. Brunsdale, Chairman Ronald A. Cass, Vice Chairman Alfred E. Eckes Seeley G. Lodwick David B. Rohr Don E. Newquist Staff assigned: Elizabeth Haines, Investigator Catherine DeFilippo, Economist Marshall Wade, Financial Analyst Ruben Moller, Industry Analyst William Kane, Attorney George Deyman, Supervisory Investigator Address all communications to Kenneth R. Mason, Secretary to the Commission United States International Trade Commission Washington, DC 20436 CONTENTS Determination and Views of the Commission: Determination ..........•........... ~. .... 1 Views of the Conunission •••••••••••••.•••• ............. 3 Views of Chairman Anne E. Brunsdale •••••• . • . .. .. ... .. ... 21 Additional Views of Vice Chairman Ronald A. Cass •••• ....... • _35 Additional Views of Conunissioner Eckes ••••• .. • ......... ............ 67 Information obtained in the investigation: Introduction •••••• .................. ·• ........ A-1 Background ••••••••• ..... •· .. A-2 Nature and extent of sales at LTFV •••• .............. ............ A"."'2 The product: Description and uses .••••••••••• . .. ............. A-3 Track drafting machine •••••••. .. .. ..... ...... A-3 Band-and-pulley -
Blacksmith's Journal Index
BLACKSMITH’S JOURNAL INDEX VOLUME 1 - 19 EXTENDABLE, WALL 1827 146 MAR-03 13 TOPIC PAGE ISSUE DATE VOL HINGED 1983 158 MAR-04 14 SQUARE CANDLE, FOR A 2011 160 MAY-04 14 ABANA 2k GATE PROJECT CANDLESTICK 695 56 APR-95 5 OVERVIEW 1182 95 JUL-98 8 TOM LATANE’S 1351 110 OCT-99 10 IDEA DRAWINGS 1197 97 SEP-98 9 4-PART BUNDLE 2287 180 JAN-06 16 CONCEPTUAL DRAWINGS 1221 99 NOV-98 9 CHAIN 839 68 APR-96 6 CHANGES 1261 102 FEB-99 9 DECORATIVE 1997 84 AUG-97 8 IMPROVEMENTS 1288 104 APR-99 9 DECORATIVE 2024 161 JUN-04 14 JOINERY DETAILS 1319 107 JUL-99 9 DECORATIVE 1662 134 MAR-02 12 FOUNDATION 1358 109 SEP-99 10 CHANDELIER 690 56 APR-95 5 UPDATE 1454 118 JUN-00 10 CHANNEL HEEL BAR 1464 119 JUL-00 10 FORGING 13 1 SEP-90 1 WORKSHOP PHOTOS 1466 119 JUL-00 10 CHISEL ANCHOR PLATE, OFFSET 2691 209 JUN-08 18 MASON’S 1437 117 MAY-00 10 ANDIRON 385 32 APR-93 3 SCULPTOR’S 487 40 DEC-93 4 ASYMMETRICAL 2757 214 NOV-08 18 CLAMP COLLARED BRACKET 2311 182 MAR-06 16 BAR 1287 105 MAY-99 9 ANGLE IRON QUICK C 2297 181 FEB-06 16 SCALE (FOR WEIGHING) 2527 197 JUN-07 17 SCROLL JIG 2364 185 JUN-06 16 VARIATIONS 415 34 JUN-93 3 SPRING 2231 176 SEP-05 15 ANIMALS SPLIT-CAUL C 2300 181 FEB-06 16 ANGLE IRON EAGLE 1335 108 AUG-99 10 CLEVIS 1399 114 FEB-00 10 LIZARD 1273 103 MAR-99 9 COAT RACK 1545 126 FEB-01 11 SERPENT HEAD 1081 87 NOV-97 8 SWIVEL TOP 2304 181 FEB-06 16 ANVIL COLD SHUTS 341 28 DEC-92 3 ACCESSORIES 1167 94 JUN-98 8 COLLARS 209 18 FEB-92 2 MINIATURE 1402 114 FEB-00 10 CHANNEL 219 19 MAR-92 2 RAIL 519 42 FEB-94 4 CUT/BEND & FABRICATED 1681 136 MAY-02 12 SOUND -
Cutting Tools Columbus Fleet Industrial Supply Canton Fleet Industrial Supply Canton First Aid & Safety
Cutting Tools Columbus Fleet Industrial Supply Canton Fleet Industrial Supply Canton First Aid & Safety www.cfisgroup.com Phone: 614-332-7464 1 Cutting Tools Full Sets Part # TYPE 330-040 29 PC Set Flip-Out (64th) 330-039 29 PC Set Orange Round 330-030 1-60 Set 330-032 A-Z Set 330-045 29 PC Reduced Shank 330-070 29 PC Cobalt Set Empty Drill Index Empty Index Part # TYPE 330-001 Drill Guage 330-002 15 PC Empty (32nd) 330-003 29 PC Empty (64th) 330-005 1-60 Empty 330-007 A-Z Empty www.cfisgroup.com Phone: 614-332-7464 2 Cutting Tools Drill Sets & Empty Index Full Sets Part # TYPE 330-048 S&D Drill Set 4-PC 330-050 S&D Drill Set 8-PC 9/16, 13/16, 5/8, 7/8, 11/16, 15/16, 3/4, 1” Empty Index Part # TYPE 330-015 S&D Drill Empty Drill Sets & Empty Index Full Sets Empty Index Part # TYPE Part # TYPE 330-042 56 Piece Drill Set 330-020 56 Piece Drill Empty 3 ea 1/16” – 1/4” 2 ea 17/64” – 3/8” 1 ea 11/16” – 1/2” Drill Sets & Empty Index Full Sets Part # TYPE 330-043 115 pc Drill Set www.cfisgroup.com Phone: 614-332-7464 3 Cutting Tools Accu-Lube Gold Cutting / Tapping UltraS-tCicukt Gold SLtuibcrikcants Part # QTY 252-000 Ea 2.2 oz Accu-Lube Gold Spray • High performance cutting tool lubricants in an easy to apply, easy to Part # QTY carry solid stick applicator or spray. -
Hand Saw Restoration
NUMBER 175 MARCH 2014 A Journal of Tool Collecting published by CRAFTS of New Jersey Hand Saw Restoration A Presentation by Bob Garay The November CRAFTS Written by Dave Nowicki dle doesn’t make the saw perfect, it can meeting featured a presentation on and does make the saw more comforta- saw restoration by CRAFTS Presi- ble to use. It’s the steel used in these dent Bob Garay. Following is most of the key elements in saws that makes them special. It was highly tempered, the presentation that collectors and woodworkers can use enabling it to hold an edge for a very long time before in the selection and restoration of quality hand saws. resharpening is required. Regardless of any other en- The first rule of thumb is to start with a good hancements it’s the steel that makes a saw. What’s a good saw? In this case we’re talking saw good. With regard to other enhance- about good usable saws. Many times just knowing the ments, just about any saw with a rose- maker of the saw will tell you whether you have a good wood handle is a good indicator of a high saw. According to Bob, when he sees a Disston, a Si- quality saw, where premium materials monds or an Atkins saw he knows it’s a good saw. were used to enhance the product. For When it comes to value, Disston‘s are the ones to look example the Atkins #400 and #401 saws for. They were all made to a consistent high quality had rosewood handles. -
Common Course Outline CAMM 252 CNC Milling Machine Operation 3 Credits
Common Course Outline CAMM 252 CNC Milling Machine Operation 3 Credits Community College of Baltimore County Description CAMM 252 – CNC Milling Machine Operation discusses theory and operation of Computerized Numerical Control (CNC) milling equipment in a production environment, which includes machine control alignment, fixed cycle subroutine usage, CRT layout, hands on operation, and demonstrations on CNC Machining Centers. 3 Credits Prerequisites: CAMM 111 with a passing grade of “C” or higher or NIMS “Measurement, Material and Safety” certification and CAMM 101 with a passing grade of “C” or higher. Overall Course Objectives Upon completion of this course, students will be able to: 1. set part zero using fixture offsets; 2. set tool height and tool diameter offsets; 3. safely operate a CNC machining center; 4. write a working part program for a CNC machining center using absolute and incremental positioning; 5. construct programs using subroutines and canned cycles; 6. write a program using cutter compensation; 7. demonstrate safe and practical machining techniques; 8. use formulas to calculate RPM, IPR, IPM, HP, and radial engagement factors and circular interpolation reduction factors; 9. identify the 3 basic machine axis; 10. identify tools used on a CNC mill in a production setting; 11. identify the G and M codes used to program a CNC machining center; 12. have the opportunity to earn the NIMS Level 1 “CNC Milling Operations” certification; and 13. prepare for the National Institute of Metalworking Skills (NIMS) Level 1 CNC Milling: Programming and Operations” certification. Major Topics I. Principles of CNC Milling A. Linear interpolation B. Speeds and feeds C. -
Pneumatic Chipping Hammer #550640, JCT-3640 #550641, JCT-3641 #550642, JCT-3642 #550643, JCT-3643 #550644, JCT-3644 #550645, JCT-3645
Pneumatic Chipping Hammer #550640, JCT-3640 #550641, JCT-3641 #550642, JCT-3642 #550643, JCT-3643 #550644, JCT-3644 #550645, JCT-3645 Operation & Parts Manual M-550640 Edition 4 11/2018 JET 427 New Sanford Road LaVergne, TN 37086 Ph.: 800-274-6848 www.jettools.com Copyright © 2017 JET Safety warnings General air tool warnings 12. Do not operate this tool while tired or under the influence of drugs, alcohol, or any 1. Read and understand this entire manual medication. before attempting assembly or operation. 13. Adopt a comfortable posture with proper 2. Read and understand all warnings posted on balance, and maintain secure footing at all the tool and in this manual. Failure to comply times. Non-slip footwear or anti-skid floor with all of these warnings may cause serious strips are recommended. injury. 14. Do not wear loose clothing or jewelry. Confine 3. Replace warning labels if they become long hair. obscured or removed. 15. Excessive air pressure and too much free 4. Do not use this tool for other than its intended rotation may decrease life of the tool and may use. If used for other purposes, JET disclaims cause a hazardous situation. any real or implied warranty and holds itself harmless from any injury that may result from 16. Check air hoses for wear, and keep them that use. away from heat and sharp edges. Repair or replace damaged air hose immediately. Do 5. Always wear ANSI Z87.1 approved safety not carry tool by the air hose. glasses or face shield while using this tool. -
Avoiding Metallic Surface Contamination
Technical Tip Avoiding Metallic Surface Contamination Although we emphasize the importance of cleaning the surface prior to the application of our finishes, there are some types of surface contaminates that can be very difficult or even impossible to remove with just a light washing. The leading cause of dark discolorations appearing under any transparent finish like LIFELINE is the presence of minute metal particles imbedded in the surface of the wood. All wood contains tannic acid and when tannic acid comes to the surface it can react with these metal particles creating dark color bodies or discolorations. There is much about this process that we have yet to understand but there are some things that we do know. The first is that the application of chlorine bleach not only accelerates but in many cases initiates this process. The second is that direct sunlight intensifies the discolorations. That's why the south and west walls are typically (but not always) more prone to discolorations than the north and east walls. The third is that areas of the log that cut through heartwood are usually worse than exposed sapwood. This makes sense since heartwood contains a higher concentration of tannic acid than sapwood. The Origin of Metallic Contamination Milling, Planning and Shaping All logs and siding used in a log home go through some type of process to remove the bark, cambium and branches and to shape the wood. No matter what process is used, be it milling, planing, draw knifing or even hand hewing, some type of steel blade is involved. -
Materials and Equipment Instructor Name: Wyatt Severs Please
Pocosin Arts School of Fine Craft Materials and Equipment Instructor Name: Wyatt Severs Please consider carefully all the tools and materials you will need to successfully complete your workshop. Provide as much detail as possible (see example.) Please email [email protected] with any questions. Providing the supplier name and exact item number assure that we purchase exactly what you need. Select One of the Following: Specify Item/Tool/ Material Supplier/ Website/ & Item Number Instructor will send Student will Quantity per in kit order Student Access to common Table saw, planer, X woodshop jointer, bandsaw, equipment router table 1 of each Router Bits – X (optional) Roundover or Chamfer bit 1 Bandsaw Blades, I recommend Starrett, and order from X 3/8” or ¼” x 80 MMT https://www.caphardwaresupply.com/pa ges/search-results- page?q=starrett+band+saw+blades 12 (minimum) Bar or Pipe Clamps X 1 Glue Titebond II or optional West Epoxy X 1 Glue Brush or small X foam roller 4/4 thick x 6”+ Cherry, maple, Local lumberyard or supplier X wide x 48” long of walnut, ash, oak lumber – your 2 contrasting choice, should have species minimal contrasting wood 4/4 thick x 6”+ Practice Lumber - Local lumberyard or supplier X wide x 48” long of Poplar or other 2 contrasting readily available & species minimal affordable wood (suggested but optional) (optional) Veneer of contrasting Local lumberyard or supplier X woods (optional) Milk Paint or Acrylic Local supplier; Paint; your favorite https://www.realmilkpaint.com/?gclid=E color AIaIQobChMI9M3hiLOz8QIVPvDjBx0D4Al 8EAAYASAAEgI24fD_BwE (optional) 0000 Steel Wool (to Local supplier X use with paint) .