An Analytical Approach to Toxic Substance Replacement in Support of Pollution Prevention
Total Page:16
File Type:pdf, Size:1020Kb
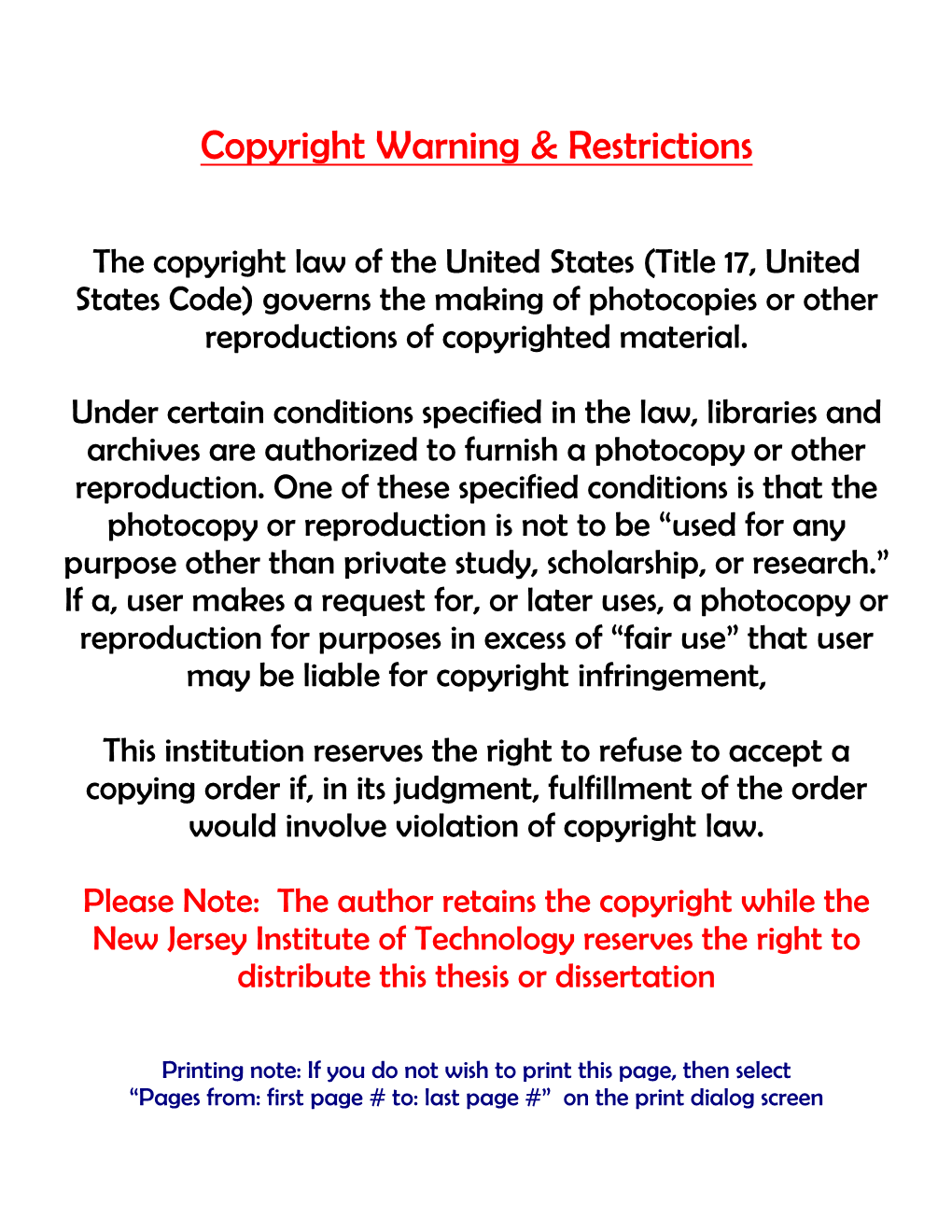
Load more
Recommended publications
-
Comparative Analysis of Airborne Chemical Exposure to Air Force Small Arms Range Instructors
Air Force Institute of Technology AFIT Scholar Theses and Dissertations Student Graduate Works 3-2006 Comparative Analysis of Airborne Chemical Exposure to Air Force Small Arms Range Instructors Eric J. Cameron Follow this and additional works at: https://scholar.afit.edu/etd Part of the Pharmacology, Toxicology and Environmental Health Commons Recommended Citation Cameron, Eric J., "Comparative Analysis of Airborne Chemical Exposure to Air Force Small Arms Range Instructors" (2006). Theses and Dissertations. 3306. https://scholar.afit.edu/etd/3306 This Thesis is brought to you for free and open access by the Student Graduate Works at AFIT Scholar. It has been accepted for inclusion in Theses and Dissertations by an authorized administrator of AFIT Scholar. For more information, please contact [email protected]. Vit COMPARATIVE ANALYSIS OF AIRBORNE CHEMICAL EXPOSURE TO AIR FORCE SMALL ARMS RANGE INSTRUCTORS THESIS Eric J. Cameron, Captain, USAF, BSC AFIT/GES/ENV/06M-01 DEPARTMENT OF THE AIR FORCE AIR UNIVERSITY AIR FORCE INSTITUTE OF TECHNOLOGY Wright-Patterson Air Force Base, Ohio APPROVED FOR PUBLIC RELEASE; DISTRIBUTION UNLIMITED The views expressed in this thesis are those of the author and do not reflect the official policy or position of the United States Air Force, Department of Defense, or the United States Government. AFIT/GES/ENV/06M-01 COMPARATIVE ANALYSIS OF AIRBORNE CHEMICAL EXPOSURE TO AIR FORCE SMALL ARMS RANGE INSTRUCTORS THESIS Presented to the Faculty Department of Systems and Engineering Management Graduate School of Engineering and Management Air Force Institute of Technology Air University Air Education and Training Command In Partial Fulfillment of the Requirements for the Degree of Master of Science in Environmental Engineering and Science Eric J. -
Lead Free Wildlife
Lead -Free Wildlife H 460: Protect Wildlife, Humans and the Environment from Toxic Lead Contamination Lead is a potent neurotoxicant that is unsafe for humans, wildlife and the environment. Lead ammunition needlessly exposes humans and other animals to this life-threatening poison. The Centers for Disease Control states there is no safe level of lead exposure.i Lead has been removed from various paints, gasoline, pipes, and a host of other items to protect human health and our environment. Lead-based ammunition is one of the greatest sources of lead discharged to Photo credit: Daniel D'Auria, Southern New Jersey, our lands and water.ii It poses significant health risks to animals, including USA, via Wikimedia Commons iii humans, and can have serious implications for the environment. The toxic effects of lead ammunition are poisoning Threat to wildlife: More than 130 species—including humans—have been Vermont’s wildlife. documented to be exposed to or killed by ingesting lead shot, bullet fragments, iv Last May, the VINS Center for or prey contaminated with spent lead ammunition. Wild Bird Rehabilitation received a Canada Goose with Animals can fall victim to spent lead ammunition through two avenues: neurological symptoms, dehydration, and fever. The Primary poisoning, in which an animal ingests spent ammunition Goose was also very weak, directly from the environment, usually when foraging for food on the paralyzed, and had fluid running from its beak. ground; and Secondary poisoning, in which an animal consumes wounded or Treatment for lead poisoning was performed, but the bird’s dead prey or scavenges gut piles contaminated with lead ammunition condition was too critical and left behind by hunters. -
US Army Ammunition Data Sheets
TM 43-000 l-27 TECHNICAL MANUAL ARMY AMMUNITION DATA SHEETS SMALL CALIBER AMMUNITION FSC 1305 . DISTRIBUTION STATEMENT A: Approved for public release: distribution is unlimited. HEADQUARTERS, DEPARTMENT OF THE ARMY APRIL 1994 TM 43-0001-27 When applicable, insert latest change pages and dispose of LIST OF EFFECTIVE PAGES supersededpages in accordance with applicable rcgulat~ons. TOTAL NUMBER OF PAGES IN THIS PUBLICATION IS 316 CONSISTING OF THE FOLLOWING: Page *Change Page *Change No. No. No. No. Cover 10-l thru lo-24 A 11-l thru 11-32 B 12-l thru 12-8 ithruvi 13-1 thru 13-8 l-l and l-2 14-1 thru 14-42 2-1 thru 2-16 15-l thru 15-16 3-1 thru 3-10 16-1 thru 16-10 4-1 thru 4-12 17-1 thru 17-8 5-1 thru 5-24 18-1 thru 18-16 6-1 thru 6-4 18-17 7-l thru 7-8 18-18 8-l thru 8-18 Authentication Page 9-l thru 9-46 * Zero indicates an original page. Change 1 A :::‘l’M43.0001-“7 Technical Manual ) HEADQUARTERS ) DEPARTMENT OF THE ARMY p No. 43-0001-2’7 ) Washington, DC, 20 April 1994 ARMY AMMUNITION DATA SHEETS SMALL CALIBER AMMUNITION FSC 1305 REPORTING OF ERRORS AND RECOMMENDING IMPROVEMENTS You can improve this manual. If you find any mistakes or know of a way to improve the procedures, please let us know. Mail your DA Form 2028 (Recommended Changes to Publications and Blank Forms), or DA Fornl 2028-2 located in the back of this nxmual direct to Commander, U.S. -
30-06 Springfield 1 .30-06 Springfield
.30-06 Springfield 1 .30-06 Springfield .30-06 Springfield .30-06 Springfield cartridge with soft tip Type Rifle Place of origin United States Service history In service 1906–present Used by USA and others Wars World War I, World War II, Korean War, Vietnam War, to present Production history Designer United States Military Designed 1906 Produced 1906–present Specifications Parent case .30-03 Springfield Case type Rimless, bottleneck Bullet diameter .308 in (7.8 mm) Neck diameter .340 in (8.6 mm) Shoulder diameter .441 in (11.2 mm) Base diameter .471 in (12.0 mm) Rim diameter .473 in (12.0 mm) Rim thickness .049 in (1.2 mm) Case length 2.494 in (63.3 mm) Overall length 3.34 in (85 mm) Case capacity 68 gr H O (4.4 cm3) 2 Rifling twist 1-10 in. Primer type Large Rifle Maximum pressure 60,200 psi Ballistic performance Bullet weight/type Velocity Energy 150 gr (10 g) Nosler Ballistic Tip 2,910 ft/s (890 m/s) 2,820 ft·lbf (3,820 J) 165 gr (11 g) BTSP 2,800 ft/s (850 m/s) 2,872 ft·lbf (3,894 J) 180 gr (12 g) Core-Lokt Soft Point 2,700 ft/s (820 m/s) 2,913 ft·lbf (3,949 J) 200 gr (13 g) Partition 2,569 ft/s (783 m/s) 2,932 ft·lbf (3,975 J) 220 gr (14 g) RN 2,500 ft/s (760 m/s) 2,981 ft·lbf (4,042 J) .30-06 Springfield 2 Test barrel length: 24 inch 60 cm [] [] Source(s): Federal Cartridge / Accurate Powder The .30-06 Springfield cartridge (pronounced "thirty-aught-six" or "thirty-oh-six"),7.62×63mm in metric notation, and "30 Gov't 06" by Winchester[1] was introduced to the United States Army in 1906 and standardized, and was in use until the 1960s and early 1970s. -
Gunshot Wounds Practical Aspects of Firearms, Ballistics, and Forensic Techniques Second Edition
Gunshot Wounds Practical Aspects of Firearms, Ballistics, and Forensic Techniques Second Edition by Vincent J. M. DiMaio, M.D. ©1999 CRC Press LLC Library of Congress Cataloging-in-Publication Data Catalog record is available from the Library of Congress. This book contains information obtained from authentic and highly regarded sources. Reprinted material is quoted with permission, and sources are indicated. A wide variety of references are listed. Reasonable efforts have been made to publish reliable data and information, but the author and the publisher cannot assume responsibility for the validity of all materials or for the consequences of their use. Neither this book nor any part may be reproduced or transmitted in any form or by any means, electronic or mechanical, including photocopying, microfilming, and recording, or by any information storage or retrieval system, without prior permission in writing from the publisher. The consent of CRC Press LLC does not extend to copying for general distribution, for promotion, for creating new works, or for resale. Specific permission must be obtained in writing from CRC Press LLC for such copying. Direct all inquiries to CRC Press LLC, 2000 Corporate Blvd., N.W., Boca Raton, Florida 33431. Trademark Notice: Product or corporate names may be trademarks or registered trademarks, and are only used for identification and explanation, without intent to infringe. © 1999 by CRC Press LLC No claim to original U.S. Government works International Standard Book Number 0-8493-8163-0 Printed in the United -
Department of the Army
6 June 2016 MEMORANDUM FOR WHOM IT MAY CONCERN SUBJECT: Curriculum Vitae of Mr. Don Mikko, President, Forensic Firearms Training Seminars, Inc., 2892 Rex Road, Ellenwood, GA 30294 1. Retired Special Agent, Chief Warrant Officer Three (CW3) (P), U.S. Army Criminal Investigation Command, Fort Gillem, GA 30297, with an excess of twenty-one (21) years served in the military and thirteen (13) years as a Federal Government (GS-14) employee. Former Director, Atlanta Police Department Crime Laboratory, 180 Southside Industrial Parkway, Atlanta, GA, 30354. 2. The following is a detailed listing of training completed with regard to firearm and toolmark examination, comparison and identification: The one hundred four week resident Firearm and Toolmark Examiner course, U.S. Army Criminal Investigation Laboratory. The Fifteen week Small Arms Weapons Repair Basic Course, Aberdeen Proving Grounds (APG), MD. Rocket Launcher Operations course. Mortar Operations course. Small Arms Weapons Repair course. Machine Gun Operations course. Medeco Lock Seminar, Atlanta, GA. Sturm Ruger automatic pistol, revolver and rifle course, Newport, NH and Atlanta, GA. Smith and Wesson automatic pistol and revolver course, Springfield, MA. Sig Sauer automatic pistol course, Atlanta, GA. Glock automatic pistol course, Smyrna, GA. Technical Surveillance Specialist Locksmithing course, Atlanta, GA. Basic Surreptitious Entry Techniques course, Atlanta, GA. Remington Rifle and Shotgun course, Ilion, NY. Foley-Belsaw Professional Locksmithing course, Atlanta, GA. Foley-Belsaw Advanced Locksmithing course, Atlanta, GA. Medeco Lock Course, Salem, VA. Beretta automatic pistol course, Accokeek, MD. Advanced Firearm and Toolmark Course, Norfolk, VA. Opposing Forces Weapons course, APG, MD. Armed Forces Institute of Pathology (AFIP) Wound Ballistics course, Washington, D.C. -
Small Caliber Ammunition Checklist
Small Caliber Ammunition Checklist 1 5.56mm M855 Ball 2 5.56mm M856 Tracer 3 5.56mm M193 Ball 4 5.56mm M200 Blank 5 7.62mm M80 Ball 6 7.62mm M62 Tracer 7 7.62mm M82 Blank 8 7.62mm M118 Long Range 9 7.62mm M276 Dim Tracer 10 .30 Caliber Blank 11 .50 Caliber M33 Ball 12 .50 Caliber M17 Tracer 13 .50 Caliber M8 Armor Piercing Incendiary 14 .50 Caliber M20 Armor Piercing Incendiary Tracer 15 .50 Caliber MK211 Armor Piercing Incendiary 16 .50 Caliber M1022, Long Range Sniper 17 .50 Caliber MK257 Armor Piercing Incendiary Dim Tracer 18 Ammunition Links — Small Caliber Contact www.atk.com or call 816-796-5093 for more information. 5.56mm M855 DODIC A059/A062/ Ball A064/AA33 PHYSICAL DATA Height (max) . .2.260 in Weight . .190-14 grains PERFORMANCE DATA Muzzle Velocity . .3,000 ± 40 f/s at 78 ft Chamber Pressure (typical) . .55,000 psi Accuracy . .ind targets horiz and vert sd = 7.8 in. at 600 yd Action Time . .3 ms The 5.56mm M855 has a green bullet tip. Adopted by NATO in 1980, the new load has a spitzer boattail bullet. It also has much improved penetration characteristics over the old M193 55-grain projectile at all ranges, resulting in higher retained velocity and greater accuracy at long range. The 5.56mm M855 is ideal for use in rifle M16A2, M4, and machine gun M249. Contact www.atk.com or call 816-796-5093 for more information. Approved for release to public domain — 04-S-3024 — 108124 1 5.56mm M856 DODIC A063/A064 Tracer PHYSICAL DATA Height (max) . -
How Good Are Copper Bullets, Really???
How Good Are Copper Bullets, really??? by Carl Batha, Certified Wildlife Biologist Wildlife Biologist (retired) & Phil Lehman Wildlife Technician (retired) Funding was provided by the Wisconsin Department of Natural Resources, 2 This project started with the purchase of a new rifle in 270 Winchester caliber. Since I had no ammunition in this caliber on hand, I decided to handload copper bullets to better familiarize myself with them. I hesitate to admit that it has been only recently that I have educated myself with the published articles that clearly show that upland game are being impacted by the deposition of lead from hunter‟s cartridges and shells. I was embarrassed to admit, even to myself, that as a practicing wildlife biologist I let this part of my professional knowledge lapse. As the foremost stewards of the resource — and I believe that to be sport hunters — we ought to be doing better. Recently, there has been a surge of activity regarding lead particles in game from hunter-shot animals and the consumption of that meat with resulting human health concerns. No, a direct correlation has not been made between game consumption and human lead poisoning, but the corollary facts are there, so who wants to take a chance!! Thirty-eight years ago, about the time I was starting my career, lead poisoning in waterfowl was the issue of the day. I am proud that the Wisconsin Department of Natural Resources took a leadership position in outlawing lead shot use in waterfowl hunting. Yes there was resistance, but there also was active dialog and training conducted with hunters by the agency. -
Migration of Heavy Metals from Simulated Small Arms Firing Berms
Migration of Heavy Metals from Simulated Small Arms Firing Berms W. Andy Martin Environmental Engineer, ERDC Steven L. Larson Research Chemist, ERDC Steven R. Hearne Senior Fellow Army Environmental Policy Institute JSEM Conference 22 Mar 06 Project Overview & Objectives • AEPI coordinated effort with ARDEC Heavy Metals Office (HMO) – Advance knowledge of heavy metals, e.g., tungsten, transport mechanisms from SAFRs – Provide for more informed decision making supporting: • Follow-on transport [e.g., field sampling and field lysimeter] studies • Improved SAFR management and design • Selection of next generation ammo • Specific Study Objectives: – Evaluate long-term stability of tungsten on SAFR using “Green Bullet” • Simulated berm soils exposed to one year’s worth of rain events – Assess tungsten loss [mass] or release from differing SAFR soils: • Runoff [surface water] and leachate [ground water] • Dissolved [soluble] and particulate forms Firing Particle size and metal distribution Mixing and splitting of soil Simulated Berm Material • ARDEC HMO and Environmental Technology Division made the soils fired on with tungsten-nylon rounds at ERDC’s Big Black testing facility available for this laboratory lysimeter study • This leveraging of research material allowed for a low cost, high knowledge gain project funded by AEPI Firing Mixing and splitting of soil Study Approach - Considerations Batch Lab Lysimeter Field Sampling Testing • Better mimics field conditions in & Lysimeter • Provides first-level accelerated/controlled system • Use actual -
Bob Smith (Cc Bernabei, Leech) Re Your 12/8 and Enc. 12/7 12/9/71 Pursuit
Bob Smith (cc Bernabei, leech) re your 12/8 and enc. 12/7 12/9/71 Pursuit of the tracing of the pistol strikes me as a rather worthwhile research project. Perhaps you can also go further with the rifle order than Hoch and I have, but I think you may want to check my file on this. I also think Paul's recollection will be much better than mine on this. worked on it together and he has copies of eveyything I have. A general comments Bernabei ie an authentic expert, and I think you should send him a copy of your 12/7 memo with attachments (I have not time now to read the attachments but I respond in order that this not get forgotten in the press of too many things). What may seem reasonable on the basis of logic may not be on the basis of ballistics, for example. I am sending him the carbon of your 12/8 to we. What Hoch and I have includes even the copies of the Pegazines the Fitt dusted (negatvely as I recall) fromAlba and reports (inadequate) on the tracing of the magazines there. It seems to me that there was a mysteriously, pretendedly official visitor before the FBI. An assortment of people, including Garrison and I think Sprague, have conjectured that some kind of explosive ammo was used. Leon Davidson postulated ice bullets. I see no reason for anything like these farout things, particularly not if the Pi-C was planted to be found and was not used, as is my belief. -
Characterization and Remediation of Soils at Closed Small Arms Firing Ranges
INTERSTATE TECHNOLOGY & REGULATORY COUNCIL Warning! This document has not been amended since publication. Some content may be out of date and may no longer apply. INTERSTATE TECHNOLOGY & REGULATORY COUNCIL Technical/Regulatory Guidelines Characterization and Remediation of Soils at Closed Small Arms Firing Ranges January 2003 Prepared by Interstate Technology and Regulatory Council Small Arms Firing Range Team Copyright 2003 Interstate Technology and Regulatory Council ABOUT ITRC Established in 1995, the Interstate Technology & Regulatory Council (ITRC) is a state-led, national coalition of personnel from the environmental regulatory agencies of some 40 states and the District of Columbia; three federal agencies; tribes; and public and industry stakeholders. The organization is devoted to reducing barriers to, and speeding interstate deployment of, better, more cost-effective, innovative environmental techniques. ITRC operates as a committee of the Environmental Research Institute of the States (ERIS), a Section 501(c)(3) public charity that supports the Environmental Council of the States (ECOS) through its educational and research activities aimed at improving the environment in the United States and providing a forum for state environmental policy makers. More information about ITRC and its available products and services can be found on the Internet at www.itrcweb.org. DISCLAIMER This document is designed to help regulators and others develop a consistent approach to their evaluation, regulatory approval, and deployment of specific technologies at specific sites. Although the information in this document is believed to be reliable and accurate, this document and all material set forth herein are provided without warranties of any kind, either express or implied, including but not limited to warranties of the accuracy or completeness of information contained in the document. -
Lead Ammunition: Toxic to Wildlife and the Environment
Lead Ammunition: Toxic to Wildlife and the Environment Humane Society of the US Though excellent alternatives exist, lead ammunition continues to poison wild animals and the natural world Lead is a toxic substance that kills millions of animals each year and contaminates land and waterways across the country. Because of its toxicity, lead has been removed from paint, gasoline, water pipes, and a host of other items to protect human health and our environment. Yet it is still the most common form of ammunition that hunters use. The U.S. Fish and Wildlife Service began requiring non-toxic ammunition in hunting migratory waterfowl in 1991 after biologists and conservationists estimated roughly 2 million ducks died each year from ingesting spent lead pellets. Yet more than 130 species are still vulnerable to the toxic effects of spent lead ammunition. There is overwhelming scientific evidence on the toxic effects of lead ammunition on humans and wildlife and broad support for eliminating its use. Questions and Answers about Lead Ammunition How does lead ammunition poison wildlife? Wildlife can fall victim to spent lead ammunition through two avenues: Primary poisoning - an animal ingests spent ammunition (or fragments of ammunition) directly from the environment, usually when foraging for food on the ground Secondary poisoning - an animal consumes wounded or dead prey or scavenges gut piles contaminated with lead ammunition left behind by hunters Both avenues can be lethal to wildlife. For those who survive, they often experience long-term, negative effects that make them more susceptible to predation and dangers like car collisions. An estimated 10 million to 20 million animals die each year from lead poisoning in the United States.