Ttes Patent 0 Patented Jan
Total Page:16
File Type:pdf, Size:1020Kb
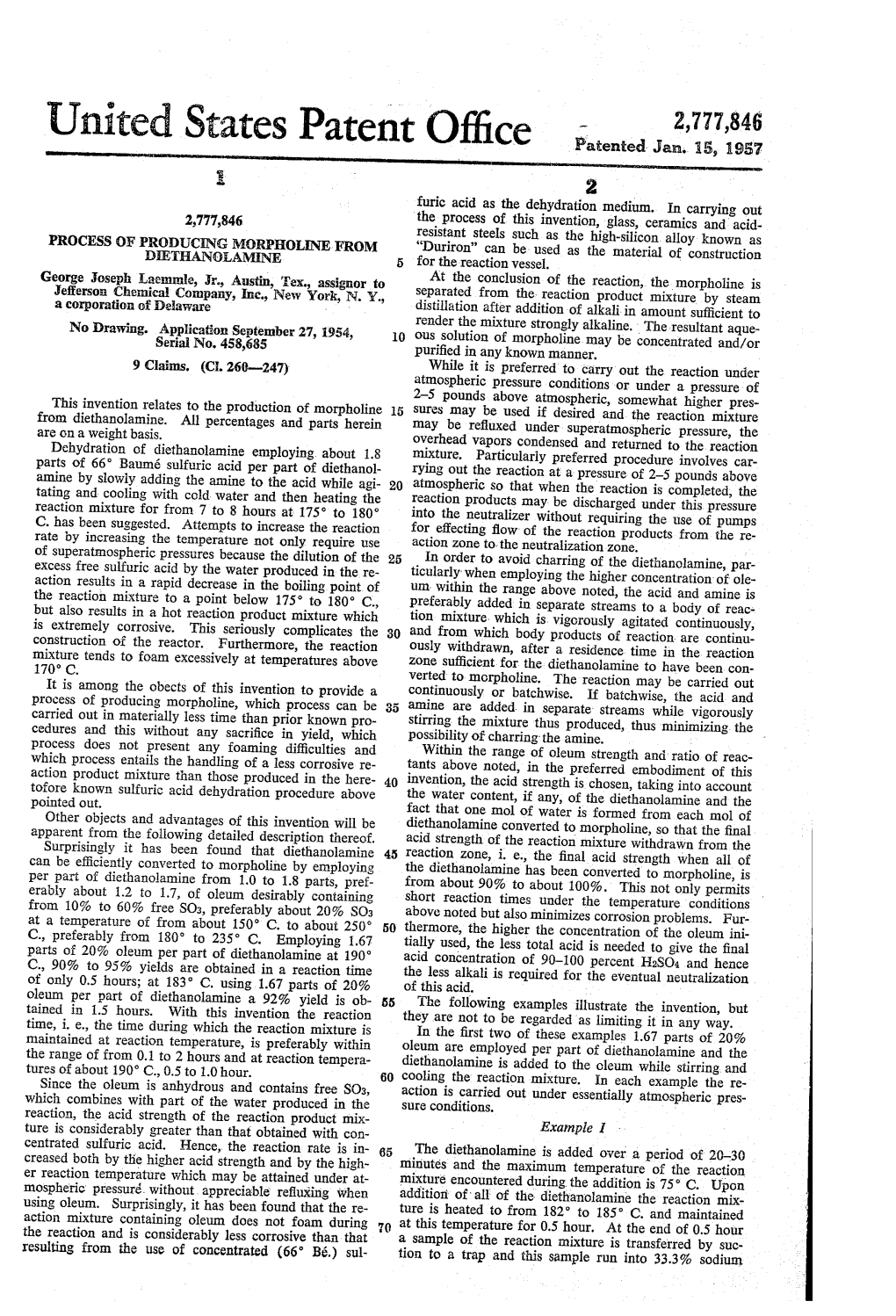
Load more
Recommended publications
-
Transport of Dangerous Goods
ST/SG/AC.10/1/Rev.16 (Vol.I) Recommendations on the TRANSPORT OF DANGEROUS GOODS Model Regulations Volume I Sixteenth revised edition UNITED NATIONS New York and Geneva, 2009 NOTE The designations employed and the presentation of the material in this publication do not imply the expression of any opinion whatsoever on the part of the Secretariat of the United Nations concerning the legal status of any country, territory, city or area, or of its authorities, or concerning the delimitation of its frontiers or boundaries. ST/SG/AC.10/1/Rev.16 (Vol.I) Copyright © United Nations, 2009 All rights reserved. No part of this publication may, for sales purposes, be reproduced, stored in a retrieval system or transmitted in any form or by any means, electronic, electrostatic, magnetic tape, mechanical, photocopying or otherwise, without prior permission in writing from the United Nations. UNITED NATIONS Sales No. E.09.VIII.2 ISBN 978-92-1-139136-7 (complete set of two volumes) ISSN 1014-5753 Volumes I and II not to be sold separately FOREWORD The Recommendations on the Transport of Dangerous Goods are addressed to governments and to the international organizations concerned with safety in the transport of dangerous goods. The first version, prepared by the United Nations Economic and Social Council's Committee of Experts on the Transport of Dangerous Goods, was published in 1956 (ST/ECA/43-E/CN.2/170). In response to developments in technology and the changing needs of users, they have been regularly amended and updated at succeeding sessions of the Committee of Experts pursuant to Resolution 645 G (XXIII) of 26 April 1957 of the Economic and Social Council and subsequent resolutions. -
Synthesis of Morpholine and Derivatives Thereof Via the Reaction of Dialkylene Glycol and Ammonia
Europaisches Patentamt J» European Patent Office © Publication number: 0036 331 B2 Office europeen des brevets NEW EUROPEAN PATENT SPECIFICATION Date of publication of the new patent specification: mtci C07D 295/02 18.10.89 Application number: 81301126.9 Date of filing: 17.03.81 Synthesis of morpholine and derivatives thereof via the reaction of dialkylene glycol and ammonia. Priority: 17.03.80 US 130782 © Proprietor: AIR PRODUCTS AND CHEMICALS, INC., P.O. Box 538, Allentown, Pennsylvania 18105 (US) Date of publication of application : 23.09.81 Bulletin 81/38 Inventor: Daughenbaugh, Randall Jay, Box 334A, RD No. 1 Barton, PA 19505 (US) Inventor: Dixon, Dale David, Box 53D RD No. 2, @ Publication of the grant of the patent : Kutztown, PA 19530 (US) 01 .08.84 Bulletin 84/31 Inventor: Fowlkes, Robert Lee, 220 Cedar Street, Milton Florida 32570 (US) @ Mention of the opposition decision : 18.10.89 Bulletin 89/42 Representative: Burford, Anthony Frederick et al, W.H. Beck, Greener & Co. 7 Stone Buildings Lincoln's Inn, London WC2A3SZ(GB) Designated Contracting States: AT BE CH DE FR GB IT LI LU NL SE References cited - DE-A-2738115 DE-A-2 758 769 Cfi DE-C- 1 941 633 DE-C-2 040 507 SU-A-175 512 CO US-A-3151 112 US-A-3154 544 O CHEMICAL ABSTRACTS, vol. 75, no. 23, December 6. <0 1971, oage 327, abstract 140871h. COLUMBUS, OHIO O (US) o Q. Ill ACTORUM AG EP 0036 331 B2 Description carrying out the process the reactants are charged to an autoclave and reacted at 240°C and Technical field 25x105 Pa (25 atmospheres) in the presence of This invention relates to an improved process for hydrogen. -
APPENDIX G Acid Dissociation Constants
harxxxxx_App-G.qxd 3/8/10 1:34 PM Page AP11 APPENDIX G Acid Dissociation Constants § ϭ 0.1 M 0 ؍ (Ionic strength ( † ‡ † Name Structure* pKa Ka pKa ϫ Ϫ5 Acetic acid CH3CO2H 4.756 1.75 10 4.56 (ethanoic acid) N ϩ H3 ϫ Ϫ3 Alanine CHCH3 2.344 (CO2H) 4.53 10 2.33 ϫ Ϫ10 9.868 (NH3) 1.36 10 9.71 CO2H ϩ Ϫ5 Aminobenzene NH3 4.601 2.51 ϫ 10 4.64 (aniline) ϪO SNϩ Ϫ4 4-Aminobenzenesulfonic acid 3 H3 3.232 5.86 ϫ 10 3.01 (sulfanilic acid) ϩ NH3 ϫ Ϫ3 2-Aminobenzoic acid 2.08 (CO2H) 8.3 10 2.01 ϫ Ϫ5 (anthranilic acid) 4.96 (NH3) 1.10 10 4.78 CO2H ϩ 2-Aminoethanethiol HSCH2CH2NH3 —— 8.21 (SH) (2-mercaptoethylamine) —— 10.73 (NH3) ϩ ϫ Ϫ10 2-Aminoethanol HOCH2CH2NH3 9.498 3.18 10 9.52 (ethanolamine) O H ϫ Ϫ5 4.70 (NH3) (20°) 2.0 10 4.74 2-Aminophenol Ϫ 9.97 (OH) (20°) 1.05 ϫ 10 10 9.87 ϩ NH3 ϩ ϫ Ϫ10 Ammonia NH4 9.245 5.69 10 9.26 N ϩ H3 N ϩ H2 ϫ Ϫ2 1.823 (CO2H) 1.50 10 2.03 CHCH CH CH NHC ϫ Ϫ9 Arginine 2 2 2 8.991 (NH3) 1.02 10 9.00 NH —— (NH2) —— (12.1) CO2H 2 O Ϫ 2.24 5.8 ϫ 10 3 2.15 Ϫ Arsenic acid HO As OH 6.96 1.10 ϫ 10 7 6.65 Ϫ (hydrogen arsenate) (11.50) 3.2 ϫ 10 12 (11.18) OH ϫ Ϫ10 Arsenious acid As(OH)3 9.29 5.1 10 9.14 (hydrogen arsenite) N ϩ O H3 Asparagine CHCH2CNH2 —— —— 2.16 (CO2H) —— —— 8.73 (NH3) CO2H *Each acid is written in its protonated form. -
PI 24.21-2 Chemistry
PI 24.21-2 Chemistry - PI 24 CHEMICAL ADDITIVES AND BLOWDOWN In Module 21-1, we discussed the sources and effects of various impurities which may be present in the secondary sys tem. Recall that the major problems centered on: deposition. corrosion. erosion. In order to minimize these effects chemical additives may be injected into the system. "What chemicals are added to the secondary system, where, and why?" (If you want to take a quick look at a se condary system schematic, see Module 70-0). Morpholine Morpholine is a volatile organic chemical which is in je pholine is a pH controller and is injected, in a modern sta tion, automatically and continually as required on a signal from a pH monitor. Hydrazine Hydrazine is injected just after· the deaerator. It is an oxygen scavenger and is used to pick up any oxygen which passes the deaerator. June 1982 - 1 _ PI 24.21-2 Secondarily, hydrazine helps raise the feed system pH to optimum level. Both morphol ine and hydraz ine are volatile 1 iquids and do not contribute to system solids. Furthermore, they travel with the steam and help protect the steam system. Cyclohexylamine For those plants where only ferrous components are pre sent (eg, Bruce B and Darlington), the use of cyclohexylamine which is a slightly stronger base than morpholine may be ad vantageous to achieve the higher pH required at a lower in jection rate. Cyclohexylamine would be injected at the Con densate Extraction Pump discharge just the same as morpho line. Note that cyclohexylamine is also a volatile organic liquid. -
Morpholine Derivatives, Pharmaceutical Compositions
Europâisches Patentamt O 027 695 19 European Patent Office (JÎ) Publication number: Office européen des brevets Bl EUROPEAN PATENT SPECIFICATION @ Date of publication of patent spécification: 12.10.83 @ Int. Cl.3: C 07 D 265/30, A 61 K 31/535 ®* —. Apphcat.cn, number:u 80303473.5onon0/,„c //C07 D303/22, C07C93/1 4, @ Date offiling: 02.10.80 C07D265/32, C07C1 03/1 27 (54) Morpholine derivatives, pharmaceuticai compositions containing them and processes for their préparation. (30) Priority: 20.1 0.79 GB 7936502 (73) Proprietor: JOHN WYETH & BROTHER LIMITED Huntercombe Lane South Taplow Maidenhead Berkshire, SL6 0PH (GB) @ Date of publication of application: 29.04.81 Bulletin 81/17 (72) Inventor: White, Alan Chapman 5 Sherbourne Drive (45) Publication of the grant of the patent: Windsor Berkshire (GB) 12.10.83 Bulletin 83/41 Inventor: Edington, Edwin Trevor 112, Broom Hill Cookham Berkshire (GB) @ Designated Contracting States: AT BE CH DE FR IT LI LU IML SE (74) Representative: Brown, Keith John Symons et al, c/o John Wyeth & Brother Limited Huntercombe (56) References cited: Lane South GB - A - 1 336 732 Taplow Maidenhead, Berkshire SL6.0PH. (GB) GB- A- 1 452 701 US - A - 2 835 669 US - A - 2 997 469 US-A-3 112311 The file contains technical information submitted after the application was filed and not included in this specification Note: Within nine months from the publication of the mention of the grant of the European patent, any person may give notice to the European Patent Office of opposition to the European patent granted. -
Dissociation Constants of Organic Acids and Bases
DISSOCIATION CONSTANTS OF ORGANIC ACIDS AND BASES This table lists the dissociation (ionization) constants of over pKa + pKb = pKwater = 14.00 (at 25°C) 1070 organic acids, bases, and amphoteric compounds. All data apply to dilute aqueous solutions and are presented as values of Compounds are listed by molecular formula in Hill order. pKa, which is defined as the negative of the logarithm of the equi- librium constant K for the reaction a References HA H+ + A- 1. Perrin, D. D., Dissociation Constants of Organic Bases in Aqueous i.e., Solution, Butterworths, London, 1965; Supplement, 1972. 2. Serjeant, E. P., and Dempsey, B., Ionization Constants of Organic Acids + - Ka = [H ][A ]/[HA] in Aqueous Solution, Pergamon, Oxford, 1979. 3. Albert, A., “Ionization Constants of Heterocyclic Substances”, in where [H+], etc. represent the concentrations of the respective Katritzky, A. R., Ed., Physical Methods in Heterocyclic Chemistry, - species in mol/L. It follows that pKa = pH + log[HA] – log[A ], so Academic Press, New York, 1963. 4. Sober, H.A., Ed., CRC Handbook of Biochemistry, CRC Press, Boca that a solution with 50% dissociation has pH equal to the pKa of the acid. Raton, FL, 1968. 5. Perrin, D. D., Dempsey, B., and Serjeant, E. P., pK Prediction for Data for bases are presented as pK values for the conjugate acid, a a Organic Acids and Bases, Chapman and Hall, London, 1981. i.e., for the reaction 6. Albert, A., and Serjeant, E. P., The Determination of Ionization + + Constants, Third Edition, Chapman and Hall, London, 1984. BH H + B 7. Budavari, S., Ed., The Merck Index, Twelth Edition, Merck & Co., Whitehouse Station, NJ, 1996. -
Morpholine Mpl
MORPHOLINE MPL CAUTIONARY RESPONSE INFORMATION 4. FIRE HAZARDS 7. SHIPPING INFORMATION 4.1 Flash Point: 100°F O.C. 7.1 Grades of Purity: Several grades available, Common Synonyms Oily liquid Colorless Fishy, ammonia 4.2 Flammable Limits in Air: 1.8%-10.8% most above 99%. Diethyleneimide oxide odor 4.3 Fire Extinguishing Agents: Water fog, 7.2 Storage Temperature: Ambient Diethylene imidoxide Diethylene oximide alcohol foam, dry chemical, or carbon 7.3 Inert Atmosphere: No requirement dioxide Tetrahydro-2h-1, 4-oxazine Floats and mixes with water. Irritating vapor is produced. 7.4 Venting: Open Tetrahydro-p-oxazine 4.4 Fire Extinguishing Agents Not to Be Used: Not pertinent 7.5 IMO Pollution Category: D 7.6 Ship Type: 3 Avoid contact with liquid and vapor. 4.5 Special Hazards of Combustion Call fire department. Products: Irritating vapors are 7.7 Barge Hull Type: 3 Notify local health and pollution control agencies. generated when heated. 4.6 Behavior in Fire: Vapor is heavier than 8. HAZARD CLASSIFICATIONS FLAMMABLE air and may travel some distance to Fire Flashback along vapor trail may occur. source of ignition and flash back. 8.1 49 CFR Category: Flammable liquid Vapor may explode if ignited in an enclosed area. 4.7 Auto Ignition Temperature: 590°F 8.2 49 CFR Class: 3 Extinguish with water, dry chemical, or carbon dioxide. 4.8 Electrical Hazards: Not pertinent 8.3 49 CFR Package Group: III Cool exposed containers with water. 4.9 Burning Rate: 1.9 mm/min 8.4 Marine Pollutant: No CALL FOR MEDICAL AID. -
Monoterpenes and Their Derivatives—Recent Development in Biological and Medical Applications
International Journal of Molecular Sciences Review Monoterpenes and Their Derivatives—Recent Development in Biological and Medical Applications Mariola Zieli ´nska-Błajet* and Joanna Feder-Kubis * Faculty of Chemistry, Wrocław University of Science and Technology, Wybrze˙zeWyspia´nskiego 27, 50-370 Wrocław, Poland * Correspondence: [email protected] (M.Z.-B.); [email protected] (J.F.-K.); Tel.: +48-71-320-2975 (J.F.-K.); Fax: +48-71-328-0475 (J.F.-K.) Received: 29 August 2020; Accepted: 23 September 2020; Published: 25 September 2020 Abstract: Monoterpenes, comprising hydrocarbons, are the largest class of plant secondary metabolites and are commonly found in essential oils. Monoterpenes and their derivatives are key ingredients in the design and production of new biologically active compounds. This review focuses on selected aliphatic, monocyclic, and bicyclic monoterpenes like geraniol, thymol, myrtenal, pinene, camphor, borneol, and their modified structures. The compounds in question play a pivotal role in biological and medical applications. The review also discusses anti-inflammatory, antimicrobial, anticonvulsant, analgesic, antiviral, anticancer, antituberculosis, and antioxidant biological activities exhibited by monoterpenes and their derivatives. Particular attention is paid to the link between biological activity and the effect of structural modification of monoterpenes and monoterpenoids, as well as the introduction of various functionalized moieties into the molecules in question. Keywords: geraniol; thymol; myrtenal; pinene; camphor; borneol; biological activity; antiviral activity; analgesic activity; anti-inflammatory activity 1. Introduction Plants have been used for medical purposes for centuries. As such, they have been studied scientifically and traded commercially. Monoterpenes belong to a large and diverse group of naturally occurring compounds. -
Inhibiting Properties of Morpholine As Corrosion Inhibitor for Mild Steel in 2N Sulphuric Acid and Phosphoric Acid Medium
ISSN: 0973-4945; CODEN ECJHAO E-Journal of Chemistry http://www.ejchem.net 2012, 9(4), 2213-2225 Inhibiting Properties of Morpholine as Corrosion Inhibitor for Mild Steel in 2N Sulphuric Acid and Phosphoric Acid Medium K. JAYANTHI1, M. SIVARAJU2, AND K. KANNAN3* 1Department of Chemistry, Queen Mary's College, Chennai 600004, Tamilnadu, India [email protected] 2Department of Chemistry, Muthayammal Technical Campus, Rasipuram 637408, Tamilnadu, India [email protected] *Department of Chemistry, Government College of Engineering, Salem 636 011, India [email protected] Received 11 October 2011; Accepted 25 December 2011 Abstract: The inhibition effect of morpholine on the corrosion of mild steel in 2N sulphuric acid and phosphoric acid has been studied by mass loss and polarization techniques between 302K and 333K.The inhibition efficiency increased with increase in concentration. The corrosion rate increased with increase in temperature and decreased with increase in concentration of inhibitor compared to blank. The adsorption of inhibitor on the mild steel surface has been found to obey Temkin’s adsorption isotherm. Potentiostatic polarization results reveal that morpholine act as mixed type inhibitor. The values of activation energy (Ea), free energy of adsorption (ΔGads), enthalpy of adsorption (ΔH), and entropy of adsorption (ΔS) were also calculated. Keywords: Mild Steel; Sulphuric acid; phosphoric acid; Corrosion inhibition; Temkin’s adsorption isotherm; Potentiostatic polarization; Morpholine. Introduction Phosphoric acid is a major chemical product, which has many important uses, especially in the production of fertilizers. Most of the acid is produced from phosphate rock by wet process. Generally nickel–base alloys and stainless steel are frequently used in many parts of the wet process and a considerable quantity of data has been published about the resistance of these materials to corrosion by phosphoric acid solution 1-4. -
BOILER WATER TREATMENT for KILN DRY OPERATIONS Mike Wieland Technical Presentation IMPORTANT TOPICS
BOILER WATER TREATMENT FOR KILN DRY OPERATIONS Mike Wieland Technical Presentation IMPORTANT TOPICS • PRETREATMENT • TEMPERATURE VS OXYGEN • FEED WATER / DA • BOILER WATER • CONDENSATE Boiler Water Pretreatment • Purpose - Statistically 75% of all boiler water problems manifested in the boiler have a root cause in the pretreatment system • Process - Walk through the processes, key factors, monitoring, and operational impacts of pretreatment systems • Payoff - Cleaner boilers, increased energy efficiency, reduced maintenance time and costs, increased plant production time and capacity Pretreatment Methods • Lime Softening • Ion Exchange Softening & Demineralization • Deaeration: Full Mechanical & Heaters Ion Exchange Technology Ion Exchange • Purpose of softening. What is it? Why do we do it? • How softening occurs • The regeneration cycle • Critical factors and troubleshooting • Areas of opportunity and operational enhancement Purpose of Softening. What is it? Why do we do it? • Well and surface water naturally contains calcium and magnesium - referred to as hardness as well as other iron and manganese that are removed in softening. Examples: Ca, Mg, Fe, Mn, Ba, Al • These ions adversely impact water and process systems by leading to scaling, corrosion and/or contamination. $ Removing them improves heat transfer, increases equipment life, and lowers overall operating costs. • This process is known as Softening. Hardness can even make a glass of water taste bad! How Does Ion Exchange Occur? Top Connection •Operating Inlet •Rinse/Regeneration -
Hazardous Substance Fact Sheet
Right to Know Hazardous Substance Fact Sheet Common Name: MORPHOLINE Synonyms: Diethyleneimide Oxide; Tetrahydro-2H-1, 4-Oxazine CAS Number: 110-91-8 Chemical Name: Morpholine RTK Substance Number: 1315 Date: January 2000 Revision: May 2009 DOT Number: UN 2054 Description and Use EMERGENCY RESPONDERS >>>> SEE LAST PAGE Morpholine is a colorless liquid with a weak Ammonia or fish- Hazard Summary like odor. It is used as a solvent, rubber accelerator, corrosion Hazard Rating NJDOH NFPA inhibitor, boiler water additive, and brightener for detergents. HEALTH - 3 FLAMMABILITY - 3 f ODOR THRESHOLD = 0.01 to 0.07 ppm REACTIVITY - 1 f Odor thresholds vary greatly. Do not rely on odor alone to determine potentially hazardous exposures. CORROSIVE AND FLAMMABLE POISONOUS GASES ARE PRODUCED IN FIRE Hazard Rating Key: 0=minimal; 1=slight; 2=moderate; 3=serious; Reasons for Citation 4=severe f Morpholine is on the Right to Know Hazardous Substance List because it is cited by OSHA, ACGIH, DOT, NIOSH, f Morpholine can affect you when inhaled and may be IARC and NFPA. absorbed through the skin. f This chemical is on the Special Health Hazard Substance f Morpholine is a CORROSIVE CHEMICAL and contact can List. severely irritate and burn the skin and eyes with possible eye damage. f Inhaling Morpholine can irritate the nose, throat and lungs. f Morpholine may damage the liver and kidneys. f Morpholine is a FLAMMABLE LIQUID and a DANGEROUS FIRE HAZARD. SEE GLOSSARY ON PAGE 5. FIRST AID Workplace Exposure Limits Eye Contact OSHA: The legal airborne permissible exposure limit (PEL) is f Immediately flush with large amounts of water for at least 30 20 ppm averaged over an 8-hour workshift. -
Equilibrium Constants for the Formation of Silver
EQUILIBRIUM CONSTANTS FOR THE FORMATION OF SILVER AMMINES IN ETHANOL-WATER MIXTURES DISSERTATION Presented in Partial Fulfillment of the Requirements for the Degree Doctor of Philosophy in the Graduate School of The Ohio State University By Charles Thomas Anderson, A.B ****** The Ohio State University Approved by* Adviser Department of Chemistry .•■--•.sia-ji • c--.\'--~t ' -.- ■?-..-_ _ _ _ _ __ ACKNOWLEDGMENT I -wish to express my deep appreciation to my preoeptor. Professor Prank Verhoek, for suggesting this problem, and for his advice and encouragement during the course of the work. 1 also wish to thank the Cincinnati Chemical Works for providing a fellowship under which much of this work was done. ii PREFACE This dissertation is & report of experimental studies on the equilibrium constants of a number of silver ammine complexes in ethanol-water solution, with the purpose of examining the relation ship between the stabilities of these complexes and the basio strengths and structures of the amines. Formation constants of the complex silver ions and dissociation constants of the amines were obtained at 25°C in 50 mole % ethanol-water mixtures from pH measurements of solutions containing known amounts of silver ion, acid, amine and neutral salt. The glass eleotrode used was calibrated on solutions for which the pH had been determined by potentiometric measurements with hydrogen electrodes and by spectrophotometric measurements using an indicator. - iii - TABLE OF CONTENTS ACKNOWLEDGMENT ....................................... ii PREFACE............................................... iii LIST OF T A B L E S ......................................... vi LIST OF ILLUSTRATIONS................................... ix LIST OF AMINES (ALPHABETICAL).......................... x LIST OF AMINES (BY NUMBER SYMBOL)........................ xi I.