Is Isszeusall Q
Total Page:16
File Type:pdf, Size:1020Kb
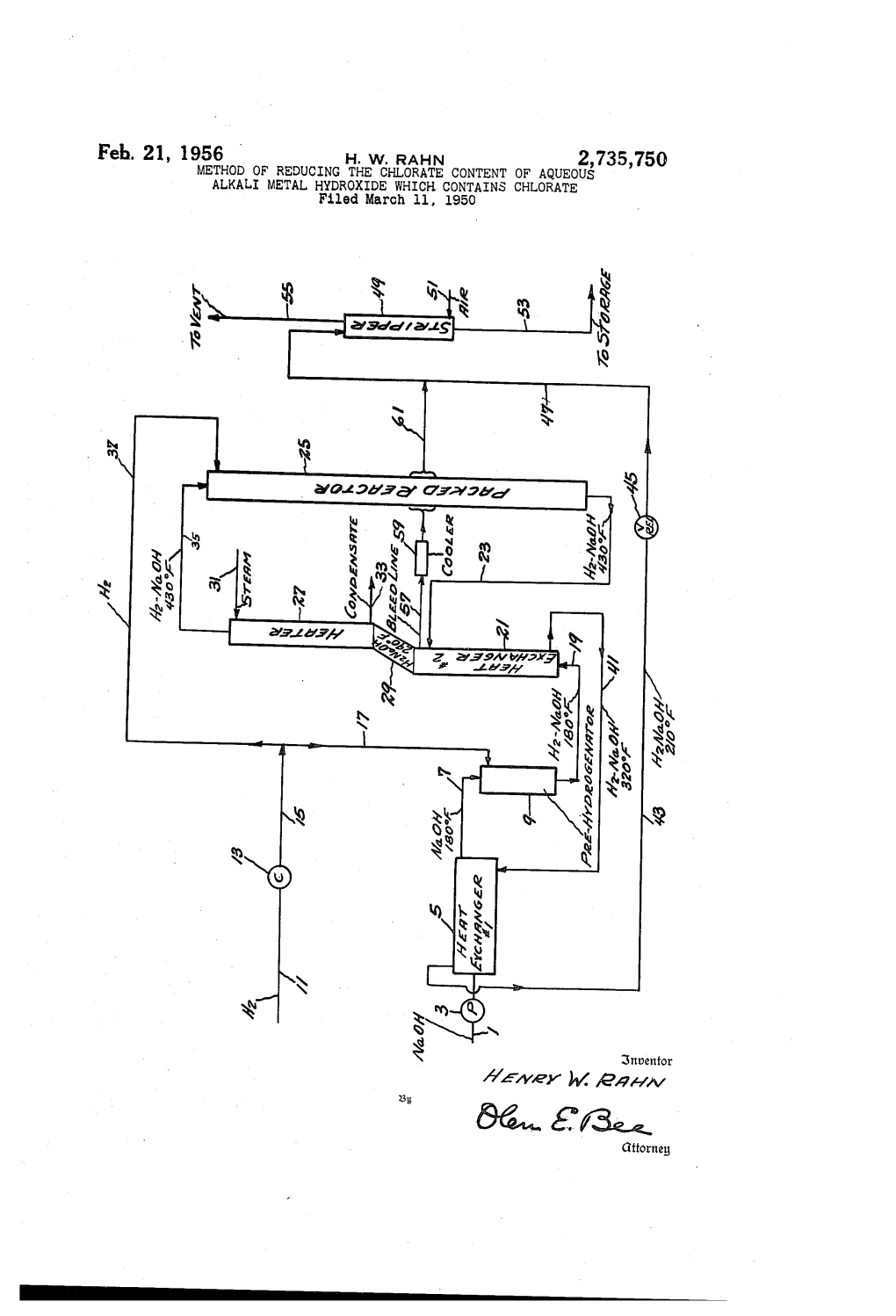
Load more
Recommended publications
-
Alkali-Silica Reactivity: an Overview of Research
SHRP-C-342 Alkali-Silica Reactivity: An Overview of Research Richard Helmuth Construction Technology Laboratories, Inc. With contributions by: David Stark Construction Technology Laboratories, Inc. Sidney Diamond Purdue University Micheline Moranville-Regourd Ecole Normale Superieure de Cachan Strategic Highway Research Program National Research Council Washington, DC 1993 Publication No. SHRP-C-342 ISBN 0-30cL05602-0 Contract C-202 Product No. 2010 Program Manager: Don M. Harriott Project Maxtager: Inam Jawed Program AIea Secretary: Carina Hreib Copyeditor: Katharyn L. Bine Brosseau May 1993 key words: additives aggregate alkali-silica reaction cracking expansion portland cement concrete standards Strategic Highway Research Program 2101 Consti!ution Avenue N.W. Washington, DC 20418 (202) 334-3774 The publicat:Lon of this report does not necessarily indicate approval or endorsement by the National Academy of Sciences, the United States Government, or the American Association of State Highway and Transportation Officials or its member states of the findings, opinions, conclusions, or recommendations either inferred or specifically expressed herein. ©1993 National Academy of Sciences 1.5M/NAP/593 Acknowledgments The research described herein was supported by the Strategic Highway Research Program (SHRP). SHRP is a unit of the National Research Council that was authorized by section 128 of the Surface Transportation and Uniform Relocation Assistance Act of 1987. This document has been written as a product of Strategic Highway Research Program (SHRP) Contract SHRP-87-C-202, "Eliminating or Minimizing Alkali-Silica Reactivity." The prime contractor for this project is Construction Technology Laboratories, with Purdue University, and Ecole Normale Superieure de Cachan, as subcontractors. Fundamental studies were initiated in Task A. -
United States Patent (19) | 1 || 3,975,503 Hauschild Et Al
United States Patent (19) | 1 || 3,975,503 Hauschild et al. |45| Aug. 17, 1976 (54) METHOD FOR PRODUCING ALKAL 3.25.49.46 6/1966 Hass et al. .......................... 423f42 3644()89 2/ 1972 Minz et al........................... 423f4 CARBONATE 3,751.56() 8/1973 Neumann..... ... .42318.9 (75) Inventors: Ulrich Hauschild; Reimar Musall, 3,7739()2 11/1973 Neumann..... ... 42.3/421 both of Hannovcr; Hans-Jirgen 387 (),784 3/1975 Sueman............................... 4231431 Schröder, Pattensen, Hannover, all of Germany FOREIGN PATENTS OR APPLICATIONS 73,794 4/1968 Belgium.............................. 423/42 Assignee: Kali-Chemie Aktiengesellschaft, 229 3/1971 Japan..... ... 423f421 Hannover, Germany 2) 43 6/197l Japan..................... ... 4231421 89569() 5/1962 United Kingdom................. 423/42 Filcd: Dec. 13, 1974 Appl. No.: 532,365 Primary Examiner-Oscar R. Vertiz Assistant Examiner-Gary P. Straub Related U.S. Application Data Attorney, Agent, or Firn-Spencer & Kaye 63 Continuation of Ser. No. 436,719, Jan. 25, 1974, abandoned, which is a continuation of Ser. No. 204,058, Dec. 2, 1971, abandoned. 57) ABSTRACT A method for producing alkali carbonate crystals, in 3() Foreign Application Priority Data cluding adding to an alkali carbonate and alkali hy Dec. 8, 97 () Germany............................ 206()287 droxide solution stream a 10 to 75 weight-% alkali hy Aug. 27, 197 Germany............................ 243 ()()8 droxide solution, charging the resulting mixture into a CO-containing gas whose temperature is from 150 to 52) U.S. Cl.................................. 423/421; 423/189 700°C, collecting mixture remaining as liquid from the 51 int. Cl............................................ C01D 7/07 gas at the end of a residence time of mixture in gas of 58 Field of Search............................ -
Download Author Version (PDF)
RSC Advances This is an Accepted Manuscript, which has been through the Royal Society of Chemistry peer review process and has been accepted for publication. Accepted Manuscripts are published online shortly after acceptance, before technical editing, formatting and proof reading. Using this free service, authors can make their results available to the community, in citable form, before we publish the edited article. This Accepted Manuscript will be replaced by the edited, formatted and paginated article as soon as this is available. You can find more information about Accepted Manuscripts in the Information for Authors. Please note that technical editing may introduce minor changes to the text and/or graphics, which may alter content. The journal’s standard Terms & Conditions and the Ethical guidelines still apply. In no event shall the Royal Society of Chemistry be held responsible for any errors or omissions in this Accepted Manuscript or any consequences arising from the use of any information it contains. www.rsc.org/advances Page 1 of 9 Journal Name RSC Advances Dynamic Article Links ► Cite this: DOI: 10.1039/c0xx00000x www.rsc.org/xxxxxx ARTICLE TYPE New Technology for Post-Combustion Abatement of Carbon Dioxide via in situ Generated Superoxide Anion-Radical Uri Stoin *a, Zach Barnea b and Yoel Sasson c Received (in XXX, XXX) Xth XXXXXXXXX 20XX, Accepted Xth XXXXXXXXX 20XX 5 DOI: 10.1039/b000000x A novel chemistry for the efficient sequestration of carbon dioxide via swift nucleophilic attack by superoxide anion is disclosed. Relatively stable aqueous solution of the latter is generated in situ by contacting alkali hydroxide solution with hydrogen peroxide at pH 11. -
A Method for Producing Hydroxybenzoic Acids Directly from the Alkah Fusion Mixture of Sodium Benzenesulfonate
A METHOD FOR PRODUCING HYDROXYBENZOIC ACIDS DIRECTLY FROM THE ALKAH FUSION MIXTURE OF SODIUM BENZENESULFONATE by Ichiro HiRAo. Taketoshi KiTo and Yukihiro HoKAMuRA Synopsis The reaction mixture from alkali fusion of sodium benzenesulfonate (SBS) cannot be used as starting material for the carboxylation of the alkali phenoxide, because of residual excess alkali. It was found that hydroxybenzoic acids were obtained in good yield by the reaction of carbon dioxide with the treated alkali fusion mass, in which the residual alkali hydroxide was completely con- verted to alkali alkoxide by the reaction with some aliphatic alcohols (C4•vCs) under the removal of the formed water as an azeotrope with the alcohol. For example, p-hydroxybenzoic acid was obtained in 66 9o yield (70 9o based on phenol) from the reaction product from the alkali fusion of SBS with potassium hydrox- ide in a1:3 molar ratio. This method is very convenient for the preparation of hydroxybenzoic acids from the mixture of phenol and alkali hydroxide with continuous treatment without preparation of alkali alkylcarbonates and alkali phenoxides separately, although this method is essentially the reaction of carboxylation of the latter in the presence of the former. 1. INTRODUCTION Aromatic hydroxy acids, such as p-hydroxybenzoic acid, are obtained mainly by the carboxylation of alkali phenoxide. This reaction, which we have often reported, can be roughly divided as follows ; (i) the reaction of alkali phenoxide with carbon dioxide in the solid-gas phases, (ii) the reaction in aprotic polar solvents in liquid phasei', (iii) the reaction of alkali phenoxide suspended in nonpolar solvents such as kerosene with carbon dioxide2', (iv) the reaction of alkali phenoxide with alkali alkyl carbonates3'. -
M Iss Winnie M, Morgan GP / O Ffice of As
NATIONAL AERONAUTICS AND SPACE AD WASIIINGTON.D C 20546 REPLY TO ATTN OF: October 16, 1970 TO : USI/Scientific & Technical Information Division Attention: Miss Winnie M, Morgan FROM: GP/Office of Assistant General Counsel for Patent Matters SUBJECT: Announcement of NASA-Owned U.S. Patents in STAR In accordance with the procedures contained in the Code GP to Code US1 memorandum on this subject, dated June 8, 1970, the attached NASA-owned U.S. patent is being forwarded for abstracting and announcement in NASA STAR. The following information is provided: U.S. Patent No, 7,352 Corporate Source Calif, Institute of Technolosv Supplementary Corporate Source Jet Promls ion Labora torv NASA Patent Case No.: mp-01464 Please note that this patent covers an invention made by an employee of a NASA contractor. Pursuant to Section 305(a) of the National Aeronautics and Space Act, the name of the Administrator of NASA appears on the first page of the patent; however, the name of the actual inventor (author) appears at the heading of Column No. 1 of the Specification, following the words e e with respect to an invention of, e .I1 Gayle Parker Enclosure: Copy of Patent (ACCESSIONu NUMBER) (NASA CR OR TMX OR AD NUMBER) (CATEGORY) B alkali battcries. To understand the invention, it will he first necessary to describe the general construction of the alkali battery. The nickel-cadmium battery will be dis- cussed for illustration purposes. In this battery the posi- B tive and negative plates are usually similar in construction, consisting of perforated pockets which contain the active niaterials. -
UNITED STATES PATENT OFFICE 2,683,102 ELECTROLYTE for ALKALINE STORAGE BATTERIES Roger S
Patented July 6, 1954 2,683,102 UNITED STATES PATENT OFFICE 2,683,102 ELECTROLYTE FOR ALKALINE STORAGE BATTERIES Roger S. Coolidge, New York, N. Y. No Drawing. Application March 23, 1951, Serial No. 217,291 13 Claims. (C. 136-154) 1. 2 This invention relates to a novel structure of NaOH, KOH, RbCH, CSOH, and consist in part an electrical battery and to an improved elec of increasing conductance; decreasing degree of trolyte for this battery. More in particular, the ionic hydration, ionic heat of hydration, and invention relates to a battery which functions ionic viscosity resulting in greater percentage ca successfully at sub-zero temperatures, and es 5 pacity at lower temperatures; also lowering eu pecially the invention relates to an improved al tectic freezing point; increasing activity coeffi kaline electrolyte for Such batteries for Operat cients; and other advantageous features. These ing at relatively low temperatures. increasingly advantageous qualities are also de It is well known that many of the present elec sirable for ordinary use of electrolytes in electric tric batteries which include sodium hydroxide or 10 batteries, because they provide the means for a, potassium hydroxide as one of the ingredients of more active performance and efficiency of the the electrolyte does not efficiently operate at rela battery. tively cold temperatures, and especially in sub In view of these particular advantages of the Zero temperatures. various alkali hydroxides in the order of their It is the desire of this invention to provide a magnitude, the preferred amount of rubidium battery which operates successfully at relatively or cesium hydroxide employed in this invention cold temperatures, and at any selected Sub-Zero is a complete substitution of cesium hydroxide temperature. -
XA9953295 EFFECT of Lioh, Naoh, and KOH on CORROSION and OXIDE MICROSTRUCTURE of Zr-BASED ALLOYS
XA9953295 EFFECT OF LiOH, NaOH, AND KOH ON CORROSION AND OXIDE MICROSTRUCTURE OF Zr-BASED ALLOYS Y.H. JEONG, H.G. KM, Y.H. JUNG Korea Atomic Energy Research Institute, Taejon, Republic of Korea H.RUHMANN Siemens AG, Power Generation Group (KWU), Erlangen, Germany Abstract Long-term corrosion test, SIMS analysis, and TEM microstructural study were carried out to investigate the corrosion characteristics and mechanism of Zr alloys in alakli hydroxides. The corrosion tests were performed in solutions of LiOH, NaOH, KOH, RbOH, and CsOH at 350°C for 500 days. SIMS analysis was performed for the specimens prepared to have an equal oxide thickness. TEM studies on the specimens with an equal oxide thickness in various solutions in both pre- and post-transition regimes were also conducted. The corrosion rate in alkali hydroxide solutions was observed to decrease as the ionic radius of alkali cation was increased. The penetration depth of cation into the oxide decreases with increasing the ionic radius of cation. Even though the oxide thickness was equal, the different oxide morphologies were observed in specimens. Namely, in LiOH solution the oxide morphology was transformed early from columnar to equiaxed structure. However, in KOH solution the columnar structure was maintained up to post-transition regime. Based on the corrosion test, SIMS analysis, and microstructural study, the cation is considered to control the corrosion in a alkali hydroxide solution and its effect is dependent on the concentration of alkali and the oxide thickness. The slight acceleration of the corrosion rate at a low concentration is thought to be caused by cation incorporation into oxide while the significant acceleration at a high concentration is due to the transformation of oxide microstructure that would be induced by cation incorporation. -
A Thesis Entitled Mitigation of the Tomato Lye Peeling Process by Bradley S. Yaniga Submitted As Partial Fulfillment of the Requ
A Thesis Entitled Mitigation of the Tomato Lye Peeling Process By Bradley S. Yaniga Submitted as partial fulfillment of the requirements for The Master of Science in Chemical Engineering _____________________________ Advisor: Constance A. Schall ______________________________ Advisor: Sasidhar Varanasi ______________________________ Committee Member: Dong-Shik Kim ______________________________ College of Graduate Studies The University of Toledo May 2007 The University of Toledo College of Engineering I HEREBY RECOMMEND THAT THE THESIS PREPARED UNDER MY SUPERVISION BY Bradley S. Yaniga ENTITLED Mitigation of the Tomato Lye Peeling Process BE ACCEPTED IN PARTIAL FULFILLMENT OF THE REQUIREMENTS FOR THE DEGREE OF Master of Science in Chemical Engineering Thesis Advisor: Constance A. Schall Thesis Advisor: Sasidhar Varanasi Recommendation concurred by Committee Committee Member: Dong Shik-Kim On Department Chairman: G. Glenn Lipscomb Final Examination Dean, College of Engineering Copyright © 2007 This document is copyrighted material. Under copyright law, no parts of this document may be reproduced without the expressed permission of the author. __________________________________ An abstract of Mitigation of the Tomato Lye Peeling Process Bradley S. Yaniga Submitted as partial fulfillment of the requirements for The Master of Science in Chemical Engineering The University of Toledo May 2007 Tomato lye peeling experiments were conducted to determine whether tomato maturity, post-harvest age, type of base, or the type of pretreatment has significant effects upon tomato peelability. Results show that tomatoes are significantly more difficult to peel as they mature on the vine. Similarly, increasing post-harvest ages make tomatoes more difficult to peel as well. No significant differences exist between tomato peelability for sodium hydroxide and an equimolar mixture of ammonium and potassium hydroxide at the same total hydroxide concentration. -
Energy & Environmental Science
View Online / Journal Homepage Energy & Environmental Science Accepted Manuscript Volume 3 Volume | Number 12 | 2010 This is an Accepted Manuscript, which has been through the RSC Publishing peer Energy& review process and has been accepted for publication. To our referees: Environmental Science Accepted Manuscripts are published online shortly after acceptance, which is prior www.rsc.org/ees Volume 3 | Number 12 | December 2010 | Pages 1813–2020 Energy & Environmental Science Science Energy & Environmental to technical editing, formatting and proof reading. This free service from RSC Dank u wel kiitos takk fyrir Publishing allows authors to make their results available to the community, in Downloaded by Carnegie Mellon University on 12 July 2012 aitäh děkuji D’akujem Благодаря citable form, before publication of the edited article. This Accepted Manuscript will Published on 02 July 2012 http://pubs.rsc.org | doi:10.1039/C2EE21989A Спасибо Thank you Tak be replaced by the edited and formatted Advance Article as soon as this is available. grazie Takk Tack 唔該 Danke To cite this manuscript please use its permanent Digital Object Identifier (DOI®), Merci gracias Ευχαριστω which is identical for all formats of publication. どうもありがとうございます。 More information about Accepted Manuscripts can be found in the As a result of your commitment and support, RSC journals have a reputation for Information for Authors. the highest quality content. Your expertise as a referee is invaluable – thank you. Pages Pages 1813–2020 Please note that technical editing may introduce minor changes to the text and/or ISSN 1754-5692 www.rsc.org/publishing Registered Charity Number 207890 COVER ARTICLE REVIEW Drain et al. -
Alkali-Aggregate Reactivity (Aar) Facts Book
ALKALI-AGGREGATE REACTIVITY (AAR) FACTS BOOK 1. Report No. 2. Government Accession No. 3. Recipient’s Catalog No. FHWA-HIF-13-019 4. Title and Subtitle 5. Report Date March 2013 Alkali-Aggregate Reactivity (AAR) Facts Book 6. Performing Organization Code 7. Author(s) 8. Performing Organization Report No. Thomas, M.D.A., Fournier, B., Folliard, K.J. 9. Performing Organization Name and Address 10. Work Unit No. The Transtec Group, Inc. 6111 Balcones Drive Austin, TX 78731 11. Contract or Grant No. DTFH61-06-D-00035 12. Sponsoring Agency Name and Address 13. Type of Report and Period Covered Office of Pavement Technology Final Report March 2013 Federal Highway Administration 1200 New Jersey Avenue, DE Washington, DC 20590 14. Sponsoring Agency Code 15. Supplementary Notes Contracting Officer’s Representative (COR): Gina Ahlstrom, HIAP-10 16. Abstract This document provides detailed information on alkali-aggregate reactivity (AAR). It primarily discusses alkali-silica reaction (ASR), cover ing the chemistry, symptoms, test methods, prevention, specifications, diagnosis and prognosis, and mitigation. Alkali-carbonate reaction (ACR) is also addressed. 17. Key Words 18. Distribution Statement Alkali-silica reactivity, alkali-aggregate reaction, reactive No restrictions. This document is available to the public through the Na aggregates, ASR, concrete durability, symptoms, identifica tional Technical Information Service, Springfield, VA 22161. tion, prevention, mitigation, lithium 9. Security Classif. (of this 20. Security Classif. (of this -
May 30, 1961 W
May 30, 1961 W. I, DENTON 2 ISOMERIZATION OF AN ALKYLENE OXIDE TO 986,585 THE CORRESPONDING ALCOHOL Filed April 2, 1959 9 2,986,585 United States Patent Office Patented May 30, 1961 2 to multiple leachings with water or to remove all but a small fraction of its alkali hydroxide content. This is 2,986,585 most readily accomplished by mixing the precipitate with ISOMERIZATION OF AN ALKYLENE OXDE TO many times its volume of water, filtering or centrifuging, THE CORRESPONDENG: ALCOHOL and repeating this treatment at least two to four times. Unless this is done, the catalytic activity will be inade William I. Denton, Cheshire, Conn, assignor to Olin quate. For example, repeated washings of a filter cake Mathieson Chemical Corporation, a corporation of of the precipitate with a large volume of water have re Virgi sulted in a product of poor catalytic activity. For opti Filed Apr. 2, 1959, Ser. No. 803,792 O mum activity, a minimum of three to five leachings are essential, resulting in an alkali hydroxide content in the 5 Claims. (Cl. 260-632) lithium phosphate ranging from 0.05 to 1.0% by weight, expressed in terms of its alkali metal content. It is noteworthy that the desired composition of the : This invention relates to the catalytic conversion of 5 product is insufficient of itself to insure that it will dis gaseous propylene oxide to allyl alcohol, and particu play the required catalytic activity and selectivity, as larly to an improved process therefor using a highly effi consistently excellent results have been obtained only cient catalyst. -
Compounds of the Metals Beryllium, Magnesium
C01F CPC COOPERATIVE PATENT CLASSIFICATION C CHEMISTRY; METALLURGY (NOTES omitted) CHEMISTRY C01 INORGANIC CHEMISTRY (NOTES omitted) C01F COMPOUNDS OF THE METALS BERYLLIUM, MAGNESIUM, ALUMINIUM, CALCIUM, STRONTIUM, BARIUM, RADIUM, THORIUM, OR OF THE RARE- EARTH METALS (metal hydrides {monoborane, diborane or addition complexes thereof} C01B 6/00; salts of oxyacids of halogens C01B 11/00; peroxides, salts of peroxyacids C01B 15/00; sulfides or polysulfides of magnesium, calcium, strontium, or barium C01B 17/42; thiosulfates, dithionites, polythionates C01B 17/64; compounds containing selenium or tellurium C01B 19/00; binary compounds of nitrogen with metals C01B 21/06; azides C01B 21/08; {compounds other than ammonia or cyanogen containing nitrogen and non-metals and optionally metals C01B 21/082; amides or imides of silicon C01B 21/087}; metal {imides or} amides C01B 21/092, {C01B 21/0923}; nitrites C01B 21/50; {compounds of noble gases C01B 23/0005}; phosphides C01B 25/08; salts of oxyacids of phosphorus C01B 25/16; carbides C01B 32/90; compounds containing silicon C01B 33/00; compounds containing boron C01B 35/00; compounds having molecular sieve properties but not having base-exchange properties C01B 37/00; compounds having molecular sieve and base-exchange properties, e.g. crystalline zeolites, C01B 39/00; cyanides C01C 3/08; salts of cyanic acid C01C 3/14; salts of cyanamide C01C 3/16; thiocyanates C01C 3/20; {double sulfates of magnesium with sodium or potassium C01D 5/12; with other alkali metals C01D 15/00, C01D 17/00}) 1/00 Methods of preparing compounds of the metals 5/20 . by precipitation from solutions of magnesium beryllium, magnesium, aluminium, calcium, salts with ammonia strontium, barium, radium, thorium, or the rare 5/22 .