Raman Analysis and Experimental Investigation of Nichrome and Aluminium Nitride Microtubular Coil Heaters: a 2D Approach
Total Page:16
File Type:pdf, Size:1020Kb
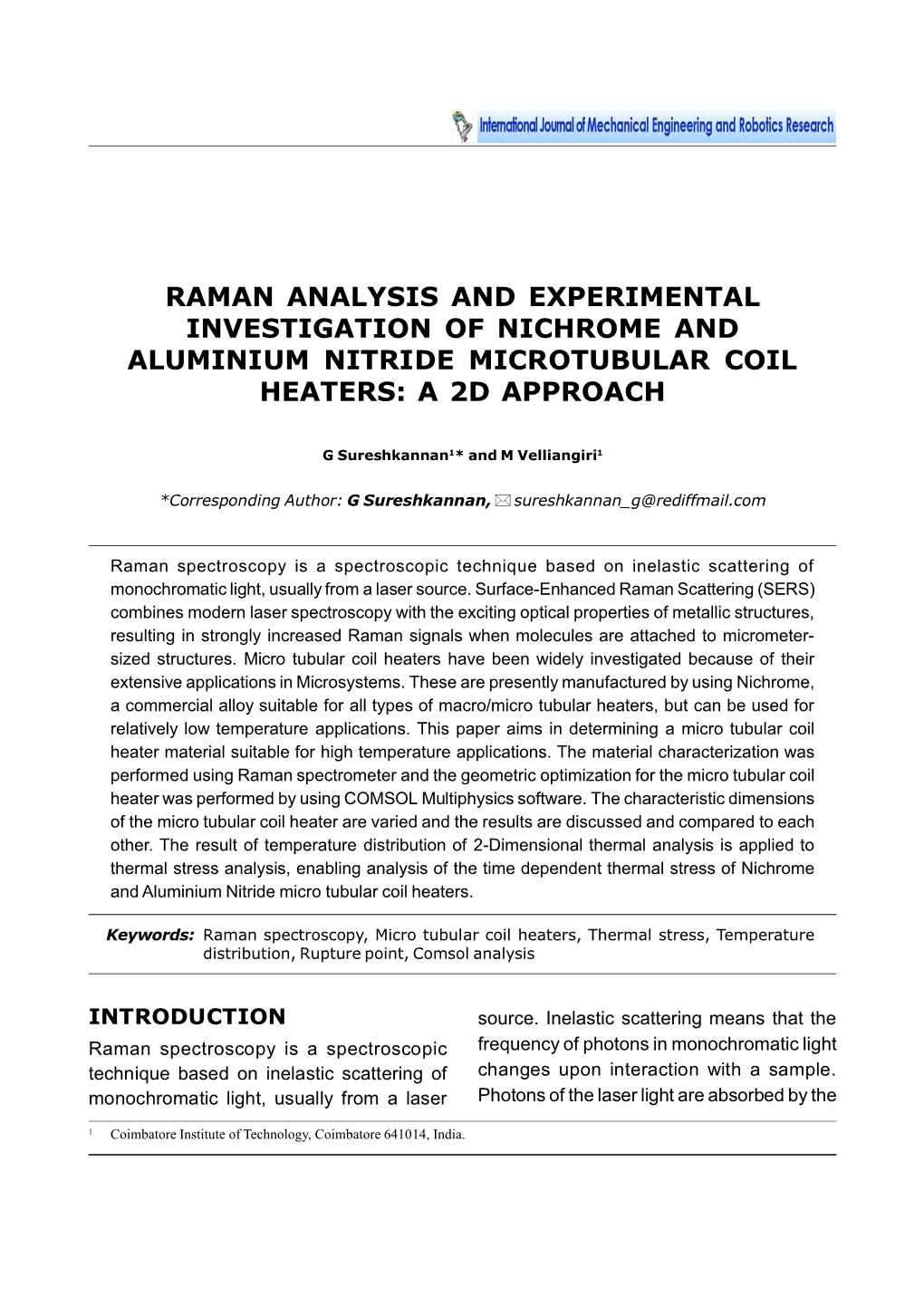
Load more
Recommended publications
-
Mica and Mineral Insulated Band Heaters
Mica and Mineral Insulated Band Heaters Mica and Mineral Insulated Band Heaters Mica & Mineral Insulated Band Heaters from National Plastic Heater are available in various sizes, voltages, wattage's, and constructions to suit every application. The Mica Insulated Band Heater is used for temperatures to 900ºF. The Mineral Insulated Band Heaters is used for temperatures to 1400ºF. The Mica and Mineral Band Heater can be internally or externally heated, full or split case for easy removal or installed and supplied with various types of leads as shown below. Mica & Mineral Insulated Band Heater Features: Sheath temperatures to 1400ºF (760ºC) mineral insulated • Split case design for easy removal and installation • Nichrome ribbon resistance wire precision wound • Mica/mineral insulation thin construction for quick heat transfer • Contamination resistant closed ended heater construction • Superior heat transfer due to minimum spacing between wire and sheath • Single set of leads possible on split case heaters Mica & Mineral Band Heater Specifications Design Capabilities: Dimensions. Minimum Inner Diameter 0.750" Maximum Diameter Consult NPH Maximum width 2 X diameter Consult NPH Voltage. 12 volts to 600 Volts AC/DC 1 or 3 Phase Watt Densities. Maximum to 100 watts/in Mineral Insulated Maximum Current. .30 Amps Post Terminals 8.5 Amps per Pair Options. Holes along the heater at required location Cutouts or slots of various dimensions Partial Coverage for sectional heating Larger Gaps at clamping end for sensors etc. Ground Wire or Lug for safety 2 Piece Split Case or Hinged construction European Plug / Terminal Box Internal Thermocouple. Available J, K Thermocouple Location. .Sheath To Order a Mica & Mineral Band Heater Please Provide: Watts, Volts, Inner Diameter, Width, Lead Length, Type of leads, Options. -
Historical Introduction Summarized History of Air Heating and Sheathed Heating Elements
Jacques Jumeau English version History of technologies linked to heating. Chapter 5 Historical introduction Summarized history of air heating and sheathed heating elements Copyright: Jacques Jumeau 1st edition 2015/11/26 Copy is allowed, provided you cite the origin: Ultimheat Museum 1 Update 2019/02/20 Historical introduction Summarized history of air heating and sheathed heating elements The invention of sheathed heating elements comprising a metal tube swaged around a coiled heating wire, and which is insulated by compressed magnesia, was an essential step of the electrothermics development. Thanks to their mechanical strength, impermeability and resistance to corrosion, these are the most professional heating technical solutions. The appearance of these heating elements, now universally used, was the result of a combination of different advanced techniques of the early 20th Century. Over the last two decades of the 19th Century, the emergence of electric heating had revealed the need to find reliable solutions for converting electricity into heat. The first electrical heaters were platinum wires (inherited laboratory equipment), nickel silver or even iron. Research carried on resistive elements with greater resistivity and good temperature resistance. On October 12, 1878, St. George Lane Fox-Pitt filed patent in England 4043, in which he developed the use of electricity for lighting and heating. This patent, based on the use of platinum filaments, was not followed for heating but it was the basis for the development of electric bulbs. In 1884, French Henri Marbeau, a pioneer in the manufacture of Nickel in New Caledonia and France, founded the company "Le Ferro-Nickel'' in Lizy sur Ourcq". -
Resistance Heating Alloy Nichrome 80 ( UNS N06003)
Resistance Heating Alloy Nichrome 80 ( UNS N06003) Durable Nichrome 80 resistance alloy is a traditional heating material for the industrial applications. It heats up quickly upon the passage of electricity. High service temperature up to 1200oC. Great oxidation and corrosion resistance at the elevated temperatures. It is commonly used in heating wires, coils, hair dryers, ovens, atomizers, metal sheath tubular elements and precision heating applications. Nichrome Ni80Cr20 has lower high resistance per foot. It offers more increment in resistance per foot with increasing temperature. Chemical Composition Nickel (Ni) 80 % Chromium (Cr) 20 % Physical Properties Density 8.31 g/cm3 or 0.303 lb/in3 Electrical resistivity 108 microhm • cm at 20oC 650 ohm. Circ. Mil/ft at 20oC Highest service temperature 1200oC or 2190oF Melting temperature 1400oC or 2550oF Coefficient of thermal expansion 12.5 micro-m per m oC from 20oC to 100oC Nichrome 80 Electric resistivity data AWG size Diameter (inch) Resistance (ohms/ft) lb / 1000 ft Ft per lb 8 0.129 inch 0.039 ohms/ft 47.23 lb / 1000 ft 22 Ft per lb 9 0.114 inch 0.050 ohms/ft 37.44 lb / 1000 ft 26 Ft per lb 10 0.102 inch 0.063 ohms/ft 29.71 lb / 1000 ft 33 Ft per lb 11 0.091 inch 0.080 ohms/ft 23.53 lb / 1000 ft 44 Ft per lb 12 0.081 inch 0.099 ohms/ft 18.72 lb / 1000 ft 55 Ft per lb 13 0.072 inch 0.125 ohms/ft 14.83 lb / 1000 ft 66 Ft per lb 14 0.064 inch 0.160 ohms/ft 11.75 lb / 1000 ft 86 Ft per lb 15 0.057 inch 0.200 ohms/ft 9.33 lb / 1000 ft 108 Ft per lb 16 0.051 inch 0.252 ohms/ft 7.4 lb / 1000 ft 135 Ft per lb 17 0.045 inch 0.317 ohms/ft 5.9 lb / 1000 ft 171 Ft per lb 18 0.040 inch 0.400 ohms/ft 4.65 lb / 1000 ft 214 Ft per lb 19 0.036 inch 0.504 ohms/ft 3.69 lb / 1000 ft 271 Ft per lb Heanjia Super-Metals Co., Ltd, Call- 12068907337. -
Civil R 2016 R
B.E. Civil Engineering, Hindusthan College of Engineering and Technology, Coimbatore 641 032 2016 HINDUSTHAN COLLEGE OF ENGINEERING AND TECHNOLOGY, COIMBATORE 641 032 (An Autonomous Institution Affiliated to Anna University, Chennai) VISION OF THE INSTITUTE To become a premier institution by producing professionals with strong technical knowledge, innovative research skills and high ethical values MISSION OF THE INSTITUTE • To provide academic excellence in technical education through novel teaching methods. • To empower students with creative skills and leadership qualities • To produce dedicated professionals with social responsibility VISION OF THE DEPARTMENT To be recognized globally for pre-eminence in Civil Engineering education, research and service MISSION OF THE DEPARTMENT • To produce well-informed graduates with scientific and technical knowledge and excellent engineering skills for professional practice, advanced study and research. • To inculcate professional and ethical responsibilities related to industry, society and environment. • To interact with industries and address issues related to infrastructure, public health and environmental protection for sustainable development. Dr. K. AKIL Signature and Name of the Chairman, BOS Principal / Dean (Academics) 1 B.E. Civil Engineering, Hindusthan College of Engineering and Technology, Coimbatore 641 032 2016 PROGRAMME EDUCATIONAL OBJECTIVES To produce graduates with the ability to • Excel as practicing engineers, academicians and researchers • Play a vital role in the nation’s -
Signature Redacted Department of Mechanical Engineering June, 2017 Certified By: Signature Redacted
Design and Manufacturing of A Benchtop Thermoforming Machine By Akwasi Owusu-Akyaw Submitted to the Department of Mechanical Engineering In Partial Fulfillment of the Requirements for the Degree of Bachelor of Science in Mechanical Engineering at the Massachusetts Institute of Technology June 2017 C 2017 Akwasi Owusu-Akyaw All Rights Reserved The author hereby grants to MIT permission to reproduce and distribute publicly paper and electronic copies of this thesis document in whole or in part in any medium now known or hereafter created. Signature of Author: Signature redacted Department of Mechanical Engineering June, 2017 Certified by: Signature redacted. David E. Hardt Professor of Mechanical Engineering Signature redacted Thesis Supervisor Accepted by: Rohit Karnik Professor of Mechanical Engineering OF TECHNOLOGY, JUL25?2017 LIBRARIES ARCHIVES 1 Design and Manufacturing of a Benchtop Thermoforming Machine By Akwasi Owusu-Akyaw Submitted to the Department of Mechanical Engineering on June 2017 In Partial Fulfillment of the Requirements for the Degree of Bachelor of Science in Mechanical Engineering ABSTRACT The following work details the design and fabrication of a tabletop thermoform machine with the goal of making this machine cheaper than the ones on the market, yet able to fulfill specific requirements. These functional requirements include creating parts that have dimensions within .05" of the original part; thermoforming plastics that range between a 3" x 3" and 12" x 12" size; and having the ability to heat the plastic to at least 150'C in order to thermoform plastics such as polycarbonate. In addition, this machine had to be simple to manufacture and use. In order to achieve these requirements, a top to bottom drape forming architecture with a four bar linear slider and carriage, was constructed. -
Design of Climatic Control Fan 1S
International Journal of Pure and Applied Mathematics Volume 119 No. 12 2018, 15191-15198 ISSN: 1314-3395 (on-line version) url: http://www.ijpam.eu Special Issue ijpam.eu Design of Climatic Control Fan 1S. Indirani and 2K. Vibha 1Department of Electronics and Instrumentation Engineering, SRM IST, Chennai, India. 2Department of Electronics and Instrumentation Engineering, SRM IST, Chennai, India. Abstract Fans are the mostly used item in India despite the widespread availability of Cooler’s and air conditioners. During winter we don’t use the normal ceiling fan and we go for room heaters instead. But the room heaters are expensive and it cannot be afforded by all people. So we planned to design a ceiling fan which can be also used as a room heater during winter times. This paper proposes the design and development of an affordable room heater system. It is based on remodeling a ceiling fan which will be suitable for all weather condition. The system includes automatic on off system according to the room temperature. Thermocouple sensor is used to measure the room temperature and it is also used to draft the relationship between the voltage and temperature graph. Index Terms--- Nichrome Wire, Temperature Sensor & Relay, and Auduino Micro controller. 15191 International Journal of Pure and Applied Mathematics Special Issue 1. Introduction Overview of Electric Heating Electric heating is a process in which heat is obtained from electricity. Main applications are heating cooking water heating and in many industrialized applications. An electrical heater is an electrical device that converts DC current to heat . In each and every electrical heater, an voltaic resistor is used within the heating element and works on the principle of Joule heating . -
Safety Data Sheet (SDS) SDS #: 538.00 Revision Date: January 16, 2014
LINN CIENTIFIC NC Safety Data Sheet (SDS) SDS #: 538.00 Revision Date: January 16, 2014 SECTION 1 — CHEMICAL PRODUCT AND COMPANY IDENTIFICATION Nichrome Wire Flinn Scientific, Inc. P.O. Box 219, Batavia, IL 60510 (800) 452-1261 Pictograms CHEMTREC Emergency Phone Number: (800) 424-9300 Signal Word N/A SECTION 2 — HAZARDS IDENTIFICATION This chemical is considered nonhazardous according to GHS classifications for the Hazard Communication Standard. Treat all laboratory chemicals with caution. Although this material is considered to be nonhazardous, unpredictable reactions among chemicals are always possible. Prudent laboratory practices should be observed. SECTION 3 — COMPOSITION, INFORMATION ON INGREDIENTS Formula Component Name CAS Number Formula Weight Concentration Nickel 7740-02-0 Ni 58.69 60% Iron 7439-89-6 Fe 55.85 24% Chromium 7440-47-3 Cr 52.0 16% Carbon 7440-44-0 C 12.01 0.1% SECTION 4 — FIRST AID MEASURES Call a POISON CENTER or physician if you feel unwell. If inhaled: Remove victim to fresh air in a position comfortable for breathing. If in eyes: Rinse cautiously with water for several minutes. Remove contact lenses if present and easy to do so. Continue rinsing. If on skin: Rinse with water for several minutes. If swallowed: Rinse mouth. Call a POISON CENTER or physician if you feel unwell. SECTION 5 — FIRE FIGHTING MEASURES Noncombustible solid. NFPA CODE When heated to decomposition, may emit toxic fumes. None In case of fire: Use a tri-class dry chemical fire extinguisher. established SECTION 6 — ACCIDENTAL RELEASE MEASURES Dispose of in school trash. © 2014 Flinn Scientific, Inc. All Rights Reserved. -
High Performance Audio Power Amplifiers
High Performance Audio Power Amplifiers for music performance and reproduction Newnes An imprint of Butterworth-Heinemann Ltd Linacre House, Jordan Hill, Oxford OX2 8DP A division of Reed Educational and Professional Publishing Ltd OXFORD BOSTON JOHANNESBURG MELBOURNE NEW DELHI SINGAPORE First published 1996 Reprinted with revisions 1997 © Ben Duncan 1996 © B. D. 1997 All rights reserved. No part of this publication may be reproduced in any material form (including photocopying or storing in any medium by electronic means and whether or not transiently or incidentally to some other use of this publication) without the written permission of the copyright holder except in accordance with the provisions of the Copyright, Designs and Patents Act 1988 or under the terms of a licence issued by the Copyright Licensing Agency Ltd, 90 Tottenham Court Road, London, England W1P 9HE. Applications for the copyright holder's written permission to reproduce any part of this publication should be addressed to the publishers TRADEMARKS/REGISTERED TRADEMARKS Computer hardware and software brand names mentioned in this book are protected by their respective trademarks and are acknowledged. British Library Cataloguing in Publication Data A catalogue record for this book is available from the British Library ISBN 0 7506 2629 1 Typeset by P.K.McBride, Southampton Printed and bound in Great Britain High Performance Audio Power Amplifiers for music performance and reproduction Ben Duncan, A.M.I.O.A., A.M.A.E.S., M.C.C.S international consultant in live show, recording & domestic audio electronics and electro-acoustics. Foreword Ben Duncan is one of those rare individuals whose love and enthusiasm for a subject transcends all the usual limits on perception and progress. -
A Periodic Table of the Elements at Los Alamos National Laboratory Los Alamos National Laboratory's Chemistry Division Presents Periodic Table of the Elements
A Periodic Table of the Elements at Los Alamos National Laboratory Los Alamos National Laboratory's Chemistry Division Presents Periodic Table of the Elements A Resource for Elementary, Middle School, and High School Students Click an element for more information: Group** Period 1 18 IA VIIIA 1A 8A 1 2 13 14 15 16 17 2 1 H IIA IIIA IVA VA VIA VIIA He 1.008 2A 3A 4A 5A 6A 7A 4.003 3 4 5 6 7 8 9 10 2 Li Be B C N O F Ne 6.941 9.012 10.81 12.01 14.0116.00 19.00 20.18 11 12 3 4 5 6 7 8 9 10 11 12 13 14 15 16 17 18 3 Na Mg IIIB IVB VB VIB VIIB------- VIII ------ IB IIB Al Si P S Cl Ar 22.99 24.31 3B 4B 5B 6B 7B - 1B 2B 26.98 28.09 30.9732.07 35.45 39.95 ------- 8 ------- 19 20 21 22 23 24 25 26 27 28 29 30 31 32 33 34 35 36 4 K Ca Sc Ti V Cr Mn Fe Co Ni Cu Zn Ga Ge As Se Br Kr 39.10 40.08 44.96 47.8850.94 52.00 54.94 55.85 58.47 58.6963.5565.39 69.72 72.59 74.9278.96 79.90 83.80 37 38 39 40 41 42 43 44 45 46 47 48 49 50 51 52 53 54 5 Rb Sr Y Zr NbMo Tc Ru Rh Pd AgCd In Sn Sb Te I Xe 85.47 87.62 88.91 91.2292.91 95.94 (98) 101.1 102.9 106.4107.9112.4 114.8 118.7 121.8127.6 126.9 131.3 55 56 57 72 73 74 75 76 77 78 79 80 81 82 83 84 85 86 6 Cs Ba La* Hf Ta W Re Os Ir Pt AuHg Tl Pb Bi Po At Rn 132.9 137.3 138.9 178.5180.9 183.9 186.2 190.2 190.2 195.1197.0200.5 204.4 207.2 209.0 (210) (210) (222) 87 88 89 104 105 106 107 108 109 110 111 112 114 116 118 7 Fr Ra Ac~ Rf Db Sg Bh Hs Mt --- --- --- --- --- --- (223) (226) (227) (257) (260) (263) (262) (265) (266) () () () () () () http://periodic.lanl.gov/default.htm (1 of 3) [10/24/2001 5:40:02 PM] A Periodic Table of the Elements at Los Alamos National Laboratory 58 59 60 61 62 63 64 65 66 67 68 69 70 71 Lanthanide Series* Ce Pr NdPmSm Eu Gd Tb DyHo Er Tm Yb Lu 140.1 140.9144.2 (147) 150.4 152.0 157.3 158.9162.5164.9 167.3 168.9 173.0175.0 90 91 92 93 94 95 96 97 98 99 100 101 102 103 Actinide Series~ Th Pa U Np Pu AmCmBk Cf Es FmMdNo Lr 232.0 (231) (238) (237) (242) (243) (247) (247) (249) (254) (253) (256) (254) (257) ** Groups are noted by 3 notation conventions. -
SEP 27 1994 Science
AN ELECTROCHEMICAL INVESTIGATION OF THE PERFORMANCE OF CANDIDATE NONCONSUMABLE ANODES FOR HALL CELLS by David William Pratt B. S., Metallurgical Engineering A. B., Spanish Literature and Linguistics University of Illinois at Urbana-Champaign, 1992 Submitted to the Department of Materials Science and Engineering in Partial Fulfillment of the Requirements for the Degree of MASTER OF SCIENCE in Materials Science & Engineering at the Massachusetts Institute of Technology September 1994 © David William Pratt 1994 All rights reserved The author hereby grants to MIT permission to reproduce and to distribute publicly copies of this thesis/97 document in whole or in part. Signature of Author Depart ent of Materials Science and Engineering .' -" August 5, 1994 Certified by Professor Donald R. Sadoway Professor of Materials Chemistry Thesis Supervisor Accepted by Carl XI Thomscnen TT Professor of Electronic Materials Chair, Department Commission of Graduate Students MASSACHUSETTS INSTITUTE OF TFC4t',t On(.Y 1 ,SEP 27 1994 Science AN ELECTROCHEMICAL INVESTIGATION OF THE PERFORMANCE OF CANDIDATE NONCONSUMABLE ANODES FOR HALL CELLS by DAVID WILLIAM PRATT Submitted to the Department of Materials Science and Engineering on August 5, 1994 in partial fulfillment of the requirements for the Degree of Master of Science in Materials Science and Engineering ABSTRACT An experimental study was carried out to observe the performance of candidate nonconsumable anodes (a copper-aluminum alloy and an iron- chromium-aluminum alloy) and compare this with the usual industrial anode material, carbon, and the ideal nonconsumable anode, platinum. Linear sweep voltammetry (LSV) and sampled current voltammetry (SCV) were used to determine parameters such as io, a and the i-Ti relationship to ascertain the degree of the kinetic facility of the reaction. -
A Nichrome Burn Wire Release Mechanism for Cubesats
A Nichrome Burn Wire Release Mechanism for CubeSats Adam Thurn*, Steve Huynh*, Steve Koss*, Paul Oppenheimer*, Sam Butcher*, Jordan Schlater** and Peter Hagan+ Abstract The nichrome burn wire release mechanism uses a nichrome burn wire which when activated heats up and cuts through a Vectran tie down cable allowing the deployable on the satellite to actuate. The release mechanism was designed from scratch with the goals to make it small, inexpensive, simple, reliable and easy to use by anyone including student-run University CubeSat projects. The release mechanism, shown in Figure 1, utilizes a two saddle design with compression springs to apply a spring stroke and force to the nichrome wire to thermally cut through the Vectran cable when heated. Through a test program and using a design of experiments (DOE) approach it was determined that the applied current to the nichrome wire and the diameter of the nichrome wire were the key parameters governing successful performance. To activate the nichrome wire a constant current of 1.60 ± 0.05 amps is applied to ensure a successful and reliable cut. The tight tolerance constant current source is necessary in order to reliably: 1.) thermally cut the cable and 2.) prevent overheating failure of the nichrome wire to allow the mechanism to be reusable for many actuations without replacing the nichrome filament. The tight tolerances on the current prevent failure of the nichrome wire from overheating under too much current in a vacuum while also providing adequate thermal margin to cut through the Vectran tie down cable in air which requires more current than in vacuum. -
How to Kill, Spy & Other Survival Skills
How NOTICE: TO ALL CONCERNED Certain text files and messages contained on this site deal with activities and devices which would be in violation of various Federal, State, and local laws if actually carried out or constructed. The webmasters of this site do not advocate the breaking of any law. Our text files and message bases are for informational purposes only. We recommend that you contact your local law enforcement officials before undertaking any project based upon any information obtained from this or any other web site. We do not guarantee that any of the information contained on this system is correct, workable, or factual. We are not responsible for, nor do we assume any liability for, damages resulting from the use of any information on this site. HOW TO BECOME AN ASSASSIN By -The Propagation "Knowledge is no longer power, Knowledge is survival" -The Propagation 1999 CONTENTS Introduction Psychology Multiple ID's and personalities Concealment Hand to hand combat Basic martial arts Commando Fighting Techniques Gun use Special ammo Basic weapons skills Sentry removal Attacking from ambush Capture in passing Lying methodology Lie detector tests The art of escaping Explosives technics Poisons Communications Inteligence gathering Phone taps Survival kits Movement Tracking Advancing towards the enemy Navigation Reading the signs Hot wiring Slight of hand Security systems Lock picking Hiding youself Carding Tips Physical training regime APPENDIX I: Chemical equivelency lists APPENDIX II: Closing statement APPENDIX III: Thanx and dedications APPENDIX IV: Apoligies APPENDIX V:About the author APPENDIX VI:Further research References Disclaimer INTRODUCTION This file is being produced to help the members of the underground in their search for knowledge and an equal world of equal opportunities.