John A. Hardy by T-1 Dra W
Total Page:16
File Type:pdf, Size:1020Kb
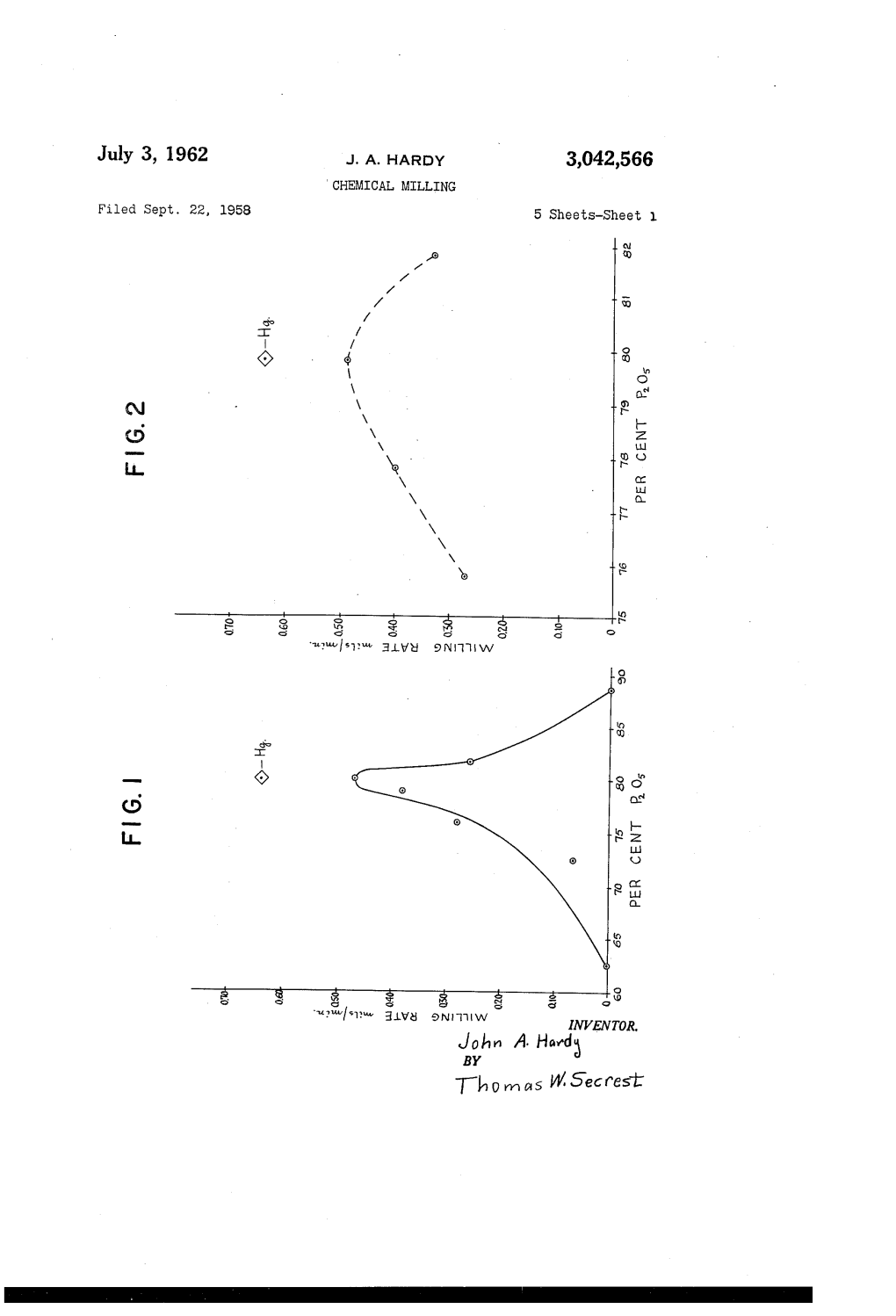
Load more
Recommended publications
-
5. POTENTIAL for HUMAN EXPOSURE 5.1 OVERVIEW White
WHITE PHOSPHORUS 157 5. POTENTIAL FOR HUMAN EXPOSURE 5.1 OVERVIEW White phosphorus can enter the environment from its production, use, accidental spills during loading and unloading for shipment, and accidental spills during transport. Hazardous wastes sites containing white phosphorus can also be a source of phosphorus in the environment. White phosphorus has been found in at least 77 of the 1,430 current or former EPA National Priorities List (NPL) hazardous waste sites (HazDat 1996). However, the number of sites evaluated for white phosphorus is not known. The frequency of these sites within the United States can be seen in Figure 5-l. The persistence of elemental phosphorus in the air is very short due to oxidation to phosphorus oxides and ultimately to phosphorus acids. However, the particulate phosphorus aerosol may be coated with a protective oxide layer that may prevent further oxidation and extend the lifetime of particulate phosphorus in air. Both wet and dry deposition remove unreacted elemental phosphorus and the degradation products from the air. Similarly, elemental phosphorus oxidizes and hydrolyzes in water and in soil. A small amount of elemental phosphorus is lost from soil and water by volatilization. Phosphorus is used as a fumigant in the storage of grain. Because of ease of application, pellets of aluminum or magnesium phosphide are commonly used (Garry et al. 1993). Phosphine, a highly toxic gas, is generated from phosphide. The rate of formation of phosphine (permissible exposure limit [PEL], 0.4 mg/m3) is dependent on the ambient temperature and humidity. Its release is rapid, and it is extremely fatal to the unprotected person (Garry et al. -
Rational Synthesis of P-Type Zinc Oxide Nanowire Arrays Using Simple Chemical Vapor Deposition
NANO LETTERS 2007 Rational Synthesis of p-Type Zinc Oxide Vol. 7, No. 2 Nanowire Arrays Using Simple Chemical 323-328 Vapor Deposition Bin Xiang,† Pengwei Wang,‡ Xingzheng Zhang,‡ Shadi. A. Dayeh,† David P. R. Aplin,† Cesare Soci,† Dapeng Yu,‡ and Deli Wang*,† Department of Electrical and Computer Engineering, UniVersity of California at San Diego, La Jolla, California 92093-0407, and Electron Microscopy Laboratory, School of Physics, Peking UniVersity, Beijing 100871, China Received October 13, 2006; Revised Manuscript Received December 8, 2006 ABSTRACT We report, for the first time, the synthesis of the high-quality p-type ZnO NWs using a simple chemical vapor deposition method, where phosphorus pentoxide has been used as the dopant source. Single-crystal phosphorus doped ZnO NWs have their growth axis along the 〈001〉 direction and form perfect vertical arrays on a-sapphire. P-type doping was confirmed by photoluminescence measurements at various temperatures and by studying the electrical transport in single NWs field-effect transistors. Comparisons of the low-temperature PL of unintentionally doped ZnO (n-type), as-grown phosphorus-doped ZnO, and annealed phosphorus-doped ZnO NWs show clear differences related to the presence of intragap donor and acceptor states. The electrical transport measurements of phosphorus-doped NW FETs indicate a transition from n-type to p-type conduction upon annealing at high temperature, in good agreement with the PL results. The synthesis of p-type ZnO NWs enables novel complementary ZnO NW devices and opens up enormous opportunities for nanoscale electronics, optoelectronics, and medicines. Zinc oxide (ZnO) is a wide direct band gap semiconductor synthesis of the high-quality p-type ZnO NWs using a simple (Eg ) 3.4 eV) that displays unique features such as large chemical vapor deposition (CVD) method using phosphorus 1 exciton binding energy (Eb ) 60 meV) and large piezo- pentoxide (P2O5) as the dopant source. -
CHEMICAL STORAGE SEGREGATION GUIDELINES Incompatible Chemicals Should Always Be Handled and Stored So That They Do Not Accidentally Come in Contact with Each Other
Laboratory Safety Reminders January 2007 ♦ Mount Holyoke College – Environmental Health and Safety CHEMICAL STORAGE SEGREGATION GUIDELINES Incompatible chemicals should always be handled and stored so that they do not accidentally come in contact with each other. This list is not complete, nor are all compatibilities shown. These materials can react to produce excessive heat, harmful vapors, and/or other deadly reactions. Always know the hazards and incompatibilities of a chemical before using it. Chemicals Avoid Accidental Contact With Acetic acid Chromic acid, nitric acid, permanganates, peroxides Hydroxyl-containing compounds such as perchloric acid, Acetic anhydride ethylene glycol Concentrated nitric acid and sulfuric acid mixtures, peroxides (i.e. Acetone peracetic acid solution, hydrogen peroxide) Acetylene Chlorine, bromine, copper, silver, fluorine, mercury Alkali, alkaline earth and strongly electropositive metals (powered Carbon dioxide, carbon tetrachloride and other chlorinated aluminum, magnesium, sodium, hydrocarbons potassium) Mercury, chlorine, calcium hypochlorite, iodine, bromine, hydrogen Ammonia (anhydrous) fluoride Acids, metal powders, flammable liquids, chlorates, nitrates, sulfur, Ammonium nitrate finely divided organics, combustibles Aniline Nitric acid, hydrogen peroxide Arsenical compounds Any reducing agent Azides Acids Ammonia, acetylene, butadiene, butane, other petroleum gases, Bromine sodium carbide, turpentine, benzene, finely divided metals Calcium oxide Water Carbon activated Calcium hypochlorite, other -
Stabilisation of Clayey Soil with Lime, Sodium Hydroxide, Aluminium
ISSN 2321 3361 © 2020 IJESC Research Article Volume 10 Issue No.5 Stabilisation of Clayey Soil with Lime, Sodium Hydroxide, Aluminium Oxide and Phosphorus Pentoxide Bhawna Sahay Assistant Professor Noida International University, India Abstract: Soil Stabilisation is a method to improve the geotechnical properties of soil such as bearing capacity, shear strength, plastic limit, liquid limit, etc. it is important before construction of any project whether it is buildings and pavement construction. There are numerous method available for stabilisation of soil but with chemical stabilisation is a quick method. Keywords: Stabilisation, bearing capacity, plastic limit, liquid limit. I. INTRODUCTION with water which results into a powerful compaction and giving higher density for same compaction effort. Clayey soil is originated from weathering and disintegration of rocks. It is generally classified as low compressible soil, medium compressible soil and highly compressible soil. The volume changes and shrinkage is a major problem occur in it. It is generally classified as highly plastic soil which depends on the mineral content of the soil. Stabilisation of soil with chemicals increase the strength of soil and improve the general properties of soil. Lime, sodium hydroxide, aluminium oxide and phosphorus pentoxide reacts vigorously with soil which interacts with the clay particles of soil and increases the resisting capacity of soil. II. CHEMICALS Lime: Calcium oxide or lime is available in white colour powder form, highly reactive in nature, modify all fine grained soil and improves the plasticity, moisture holding capacity, swell and shrinkage behaviour of soil and stability of soil. Aluminium Oxide Aluminium oxide is white coloured shining powder form which reacts with soil to form a sample little bit cool due to its affinity with water. -
Phosphorus Compounds
Phosphorus Compounds Table of Contents How to Cite This Article Phosphorus Compounds, Compounds of phosphorus play vital roles in the metabolism of both plants and animals. The energy "currency" of all living things, adenosine triphosphate (ATP), is probably the best-known organic phosphorus compound, but others are constituents of nervous tissue, cell membranes, and other tissues, as well as of many coenzymes. Phosphates also are key components of DNA and RNA, which carry genetic information in all organisms. Many phosphorus compounds are used in industrial processes. Most phosphorus compounds exhibit covalent properties. Ionic compounds, such as sodium 3− phosphide (Na3P), are few because the formation of P ions from P atoms requires a considerable amount of energy. Similarly, P5+ ions do not exist due to the very high ionization energies involved. The chemistry of phosphorus in forming compounds generally is similar to that of carbon and nitrogen. Phosphine Phosphine, PH3, is a very toxic gas with a garliclike odor. When inhaled it can cause restlessness, followed by tremors, fatigue, drowsiness, nausea, and often severe gastric pain. In most cases recovery occurs without aftereffects, but some cases may result in coma or convulsions and even death. Phosphine can be readily prepared by reacting calcium or aluminum phosphide with dilute acid. On a large scale, PH3 is obtained by action of sodium hydroxide on white phosphorus; − hypophosphite (H2PO 2) is also formed. Pure phosphine is not spontaneously flammable. It is readily oxidized by air when ignited, and explosive mixtures may be formed. Phosphine is sparingly soluble in water, and an aqueous solution of PH3 is neither acidic nor basic. -
Examples of Hazardous Chemicals
Examples of Hazardous Chemicals A-Acids Liquids 1 Acetic acid 64-19-7 2 Acetic anhydride 108-24-7 3 Butyric acid 107-92-6 4 Chromosulfuric acid 14489-25-9 5 Formic acid 64-18-6 6 Hydrobromic acid 10035-10-6 7 Hydrochloric acid 7647-01-0 8 Hydrofluoric acid 7664-39-3 9 Lactic acid 50-21-5 10 Nitric acid 7697-37-2 11 Perchloric acid 7601-90-3 12 Phenol solution (carbolic acid) 108-95-2 13 Phosphoric acid 7664-38-2 14 Propionic acid 79-09-4 15 Sulfuric acid 7664-93-9 16 Trifluoroacetic acid 76-05-1 Solids 17 Benzoic acid 65-85-0 18 Cacodylic acid 75-60-5 19 Maleic acid 110-16-7 20 Oxalic acid 144-62-7 21 Periodic acid 10450-60-9 22 Salicylic acid 69-72-7 23 Tannic acid 1401-55-4 24 Trichloroacetic acid 76-03-9 B-Corrosive Materials Liquids 25 Ammonium hydroxide 1336-21-6 26 Cresol 1319-77-3 27 Hydrazine 302-01-2 28 Morpholine 110-91-8 29 Potassium hydroxide solution 1310-58-3 30 Sodium hydroxide solution 1310-73-2 Solids 31 Aluminum sulfate 10043-01-3 32 Calcium hydroxide 1305-62-0 33 Chromic trioxide 1333-82-0 34 Ferric chloride 7705-08-0 35 Ferrous sulfate 7720-78-7 36 Iodine 7553-56-2 37 Phosphorus pentoxide 1314-56-3 38 Potassium dichromate 7778-50-9 39 Potassium hydroxide 1310-58-3 40 Sodium hydroxide 1310-73-2 C-Cyrogenic Materials 41 Nitrogen, refrigerated liquid 7727-37-9 42 Carbon dioxide, solid 124-38-9 D-Gases 43 Compressed air 44 Germane 7782-65-2 45 Helium 7440-59-7 46 Hydrogen 1333-74-0 47 Mixtures of N2, O2, CO2 48 Oxygen, 100% 7782-44-7 49 Propane 74-98-6 50 Silane 7803-62-5 51 Sulfur dioxide 7446-09-5 E-Flammable Liquids -
Chromic Acid, Nitric Acid, Hydroxyl Compounds, Ethylene Glycol
Acetic acid - Chromic acid, nitric acid, hydroxyl compounds, ethylene glycol, perchloric acid, peroxides, permanganates, ammonium nitrate Acetic anhydride - Hydroxyl-containing compounds such as ethylene glycol, perchloric acid Acetone - Concentrated nitric and sulfuric acid mixtures Acetaldehyde - Acetic acid, acetic anhydride Acetylene - Chlorine, bromine, copper, fluorine, silver, mercury Acrolein - Ammonia(aqueous), any alkali or amine, strong oxidizing agents Alkali and alkaline earth metals (such as powdered aluminum or magnesium, calcium, lithium, sodium, potassium) - Water, carbon tetrachloride or other chlorinated hydrocarbons, carbon dioxide, halogens. Aluminum metal - Ammonium nitrate, antimony trichloride, bromate Ammonia (anhydrous) - Mercury (in manometers, for example), chlorine, calcium hypochlorite, iodine, bromine, hydrofluoric acid (anhydrous) Ammonium nitrate - Acids, powdered metals, flammable liquids, chlorates, nitrites, sulfur, finely divided organic combustible materials Aniline - Nitric acid, hydrogen peroxide, strong acids, oxidizers Arsenic materials - Any reducing agent Azides – Acids Bromine - Ammonia, acetylene, butadiene, butane, methane, propane (or other petroleum gases), hydrogen, sodium carbide, benzene, finely divided metals, turpentine Calcium oxide – Water Carbon (activated) - Calcium hypochlorite, all oxidizing agents Carbon tetrachloride – Sodium Chlorates - Ammonium salts, acids, powdered metals, sulfur, finely divided organic or combustible materials Chromic acid and chromium trioxide - Acetic -
Distribution of Sulfur Dioxide and Phosphorus Pentoxide in an Air Pool Obtained by Correlation and Regression Analysis
JournalJournal of Chemical of Chemical Technology Technology and Metallurgy,and Metallurgy, 54, 4, 54, 2019, 4, 2019 826-830 DISTRIBUTION OF SULFUR DIOXIDE AND PHOSPHORUS PENTOXIDE IN AN AIR POOL OBTAINED BY CORRELATION AND REGRESSION ANALYSIS Mаlik N. Abdikarimov1, Raushan Kh. Turgumbayeva2, Saule S. Sagintayeva1, Rasylbek Mussabekov1, Gulzhan Sh. Ospanova1 1 Almaty University of Power Engineering&Telecommunications, Received 17 May 2017 126, Baytursunov str., Almaty, 050013, Republic of Kazakhstan Accepted 30 May 2018 2 Kazakh National Pedagogical University named after Abai (KazNPU) 050010, Almaty, Dostyk str. 13, Almaty, Republik Kazakhstan E-mail: [email protected] ABSTRACT Results of studying an aerosol of sulfur dioxide аnd phosphorus pentoxide released to the atmosphere by a chemical company processing phosphorites are presented. The effect of wind direction and speed on sulfur dioxide аnd phosphorous pentoxide distribution in a ground layer of the atmosphere is studied. The points of wind direction leading to pollution of the nearby city atmosphere are allocated. The statistical analysis of the environmental pollu- tion is carried out by method of correlation and regression analysis. The dependence of the amount of sulfur dioxide аnd phosphorous pentoxide reaching the atmosphere on the volume released by the enterprise producing them is defined. The results obtained are recommended for environmental control, regulation and management. Keywords: phosphorus oxide, atmosphere, correlation regression analysis, industrial enterprise, sulfur dioxide, phosphorous pentoxide, statistical correlation regression analysis, equation. INTRODUCTION character and intensity of their investigation – on the other. The Republic of Kazakhstan has no powerful A modern chemical industry produces several tens natural factors to counteract the pollution forces. -
Determination of Phosphoric Anhydride in Phosphate Rock, Superphospha Te, and "Meta
U. S. DEPARTMENT OF COMMERCE NATIONAL BUREAU OF STANDARDS RESEARCH PAPER RP1010 Part of Journal of Research of the :National Bureau of Standards, Volume 19, July 1937 DETERMINATION OF PHOSPHORIC ANHYDRIDE IN PHOSPHATE ROCK, SUPERPHOSPHA TE, AND "META. PHOSPHATE" By James I. Hoffman and G. E. F. Lundell ABSTRACT A gravimetric method requiring no molybdate reagent is described for the determination of phosphoric anhydride in phosphate rock and similar materials. In this method a precipitation with a large excess of magnesia mixture in the presence of ammonium citrate serves t o separate the phosphate ion from the other constituents. A second precipitation yields a precipitate of defi nite composition which is converted to magnesium pyrophosphate, Mg2P 20 7, on ignition. The method has been su ccessfully applied to phosphate rock, superphosphate, "meta phosphate", and liquids used with silicate cements in dentistry. It is recom mended for use in standardization and umpire analyses of phosphate rocks and similar materials, but it is not sufficiently rapid to replace the usual volumetric method now employed in routine analyses. CONTENTS Page I. Introduction___ __ _ _ ___ _ _ __ _ _ _ __ _ _ _ _ _ _ _ __ _ __ __ __ __ __ _ _ _ _ _ __ _ __ _ 59 II. Procedure_ ____ ________________ __ ___ ______ _____ __ _________ ____ 60 1. Preparation of the solution ______________________________ _ 60 2. Determination of phosphoric anhydride _ _ _ _ _ _ _ _ _ _ _ __ _ _ _ __ _ 61 III. Results obtained in the use of the method__________________ ____ __ 62 IV. -
Synthesis and Characterization of Powders Calcium Phosphate for Biomedical Applications
Seventh International Latin American Conference on Powder Technology, November 08-10, Atibaia, SP, Brazil SYNTHESIS AND CHARACTERIZATION OF POWDERS CALCIUM PHOSPHATE FOR BIOMEDICAL APPLICATIONS De Oliveira, D.M.P.1,a, Prants W.T.2,b, Camargo, N.H.A.3,c, Gemelli, E4,d. 1,2,3,4Universidade do Estado de Santa Catarina (UDESC), Centro de Ciências Tecnológicas (CCT), Campus Universitário Prof. Avelino Marcante S/N - Bairro Bom Retiro – Joinville - SC – Brasil CEP: 89223 - 100 - CX. Postal 631 - Fone (0xx47) 431- 7200 - Fax (0xx47) 431-7240 e-mail: [email protected] , [email protected], [email protected], [email protected]. Keywords: Phosphate Calcium, Thermal Treatments, Characterization. Abstract. Scientists of different areas research the bioceramics as new materials to substitute parts of the human body. The bioceramics of the calcium phosphate have the advantage present similar chemical composition to the structure of the bony apatite of the human skeleton. In this study, calcium phosphate powder was synthesized chemically using the solution of phosphorus pentoxide (P2O5) and calcium oxide (CaO) necessary for molar Ca/P =1.67. These works aim the study of different thermal treatments, physics and of the microstructure properties. For characterization the bony matrix were used the techniques of: X-ray diffraction (DRX); Scanning Electronic Microscopy (SEM) and Differential Scanning Calorimetry (DSC). 1. INTRODUCION Calcium phosphate based bioceramics have received much attention as bone substitutes due to their chemical similarity to natural bone, their bioactivity and their biocompatibility. This class of biomaterials are promising applications in orthopedics, traumatology and ondontology [1]. These bioceramics may be used for attachment of implants in reconstruction of bone tissue and the controlled release of drugs in treatments ontological. -
The Combustion of Phosphorus
Scholars' Mine Professional Degree Theses Student Theses and Dissertations 1944 The combustion of phosphorus Erwin Charles Hoeman Follow this and additional works at: https://scholarsmine.mst.edu/professional_theses Part of the Chemical Engineering Commons Department: Recommended Citation Hoeman, Erwin Charles, "The combustion of phosphorus" (1944). Professional Degree Theses. 284. https://scholarsmine.mst.edu/professional_theses/284 This Thesis - Open Access is brought to you for free and open access by Scholars' Mine. It has been accepted for inclusion in Professional Degree Theses by an authorized administrator of Scholars' Mine. This work is protected by U. S. Copyright Law. Unauthorized use including reproduction for redistribution requires the permission of the copyright holder. For more information, please contact [email protected]. THE COMBUSTION OF PHOSPHORUS BY ERWIN CHA.RLES HODWt A 'l'HESIS subnitted to the faculty of the SCHOOL OF MINES AND METALLURGY OF THE UNIVERSITY OF MISSOURI 1D partial. fulfillment of the work required tor the Degre. of CBDlICAL gGIIllma Rolla~ II1s80url 1944 Approved by: It;-\/ '~I Cha1rmaD,De.partmant of. Chaistry ind Chea1cal IDg1Deer1ng. i ACKNOWLEDGMJ!JiT The author gratefu1lr acknowledges the experience gained in the production and utilization of phosphorus, through his employ ment in the Department of Chemical Engineering of the United States Tennessee Valley Authority. 'SpecificallY', he acknowledges the supervision of work and inspiration gained through his association with Dr. RaY'Dlond L. Copson, Chief of the Research and ,Development Division; Dr. GradY' Tarbutton, Assistant to the Chief; and Mr. John H. Walthall,. Head of the Developllellt Section. Particular thanks for guidanoe in the selection of the general plaD for this paper are due to Mr. -
AP-42, Vol. 1, Final Background Document for Phosphoric Acid
[Note: with the publication of the Fifth Edition of AP-42, the Chapter and Section number for Phosphoric Acid changed to 8.9.] BACKGROUND REPORT AP-42 SECTION 5.11 PHOSPHORIC ACID Prepared for U.S. Environmental Protection Agency OAQPS/TSD/EIB Research Triangle Park, NC 27711 1-96 Pacific Environmental Services, Inc. P.O. Box 12077 Research Triangle Park, NC 27709 919/941-0333 1-96 AP-42 Background Report TECHNICAL SUPPORT DIVISION U.S. ENVIRONMENTAL PROTECTION AGENCY Office of Air Quality Planning and Standards Research Triangle Park, NC 27711 ii This report has been reviewed by the Technical Support Division of the Office of Air Quality Planning and Standards, EPA. Mention of trade names or commercial products is not intended to constitute endorsement or recommendation for use. Copies of this report are available through the Library Services Office (MD-35), U.S. Environmental Protection Agency, Research Triangle Park, NC 27711. iii TABLE OF CONTENTS 1.0 INTRODUCTION ................................................... 1 2.0 INDUSTRY DESCRIPTION .......................................... 2 2.1 GENERAL ..................................................... 2 2.2 PROCESS DESCRIPTION ........................................ 4 2.3 EMISSIONS AND CONTROLS .................................... 8 2.4 REVIEW OF REFERENCES FOR CHAPTER 2 ....................... 9 2.5 REFERENCES FOR CHAPTER 2.0 ................................ 12 3.0 GENERAL EMISSION DATA REVIEW AND ANALYSIS PROCEDURES ... 13 3.1 LITERATURE SEARCH AND SCREENING ........................ 13 3.2 EMISSION DATA QUALITY RATING SYSTEM .................... 14 3.3 EMISSION FACTOR QUALITY RATING SYSTEM .................. 15 3.4 REFERENCES FOR CHAPTER 3.0 ................................ 17 4.0 POLLUTANT EMISSION FACTOR DEVELOPMENT ................... 18 4.1 REVIEW OF SPECIFIC DATA SETS .............................. 20 4.2 CRITERIA POLLUTANT EMISSIONS DATA ....................... 24 4.3 NONCRITERIA POLLUTANT EMISSIONS DATA .................