Decorating Techniques for Pottery
Total Page:16
File Type:pdf, Size:1020Kb
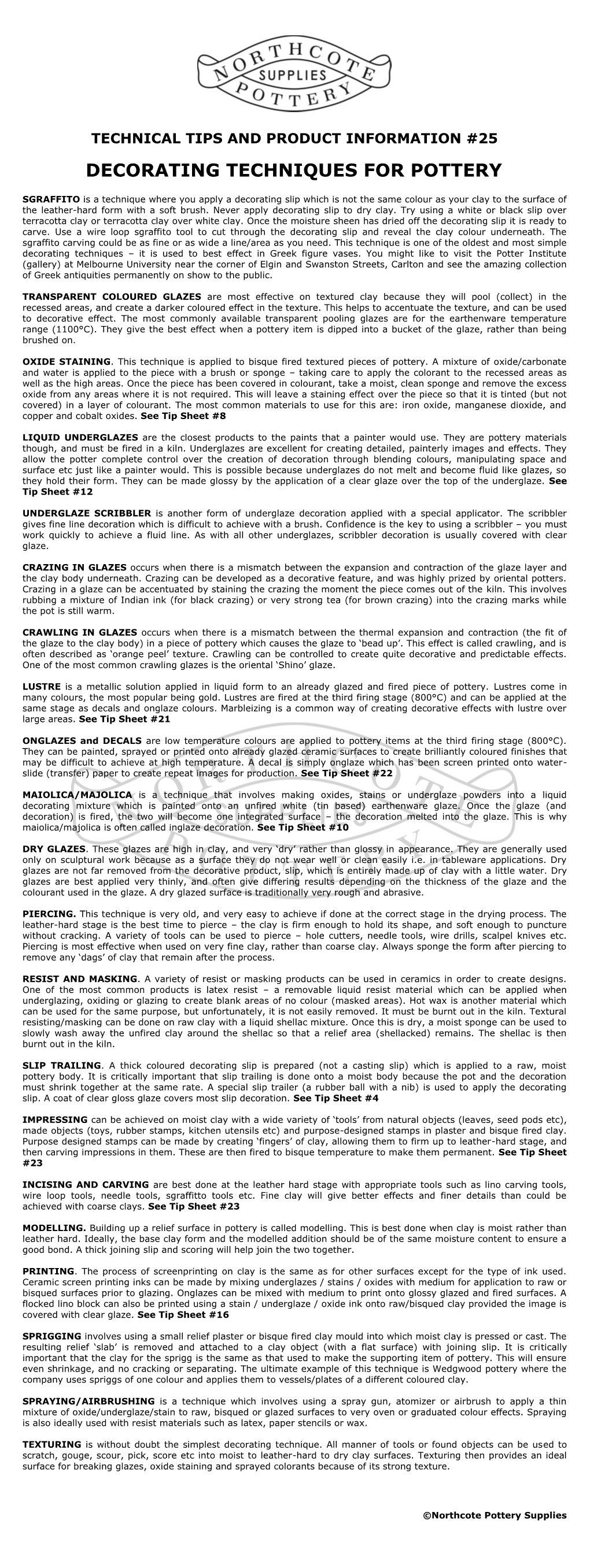
Load more
Recommended publications
-
Colonial Archaeology: 070 333 Spring 2006 Prof C. Schrire Room 201
Colonial Archaeology: 070 333 Spring 2006 Prof C. Schrire [email protected] Room 201/202 RAB Phone: 932 9006 Course Outline: This course will teach the rudiments of identification and analysis of colonial artifacts dating from about 1600-1900 AD. Our teaching collection includes a variety of ceramics, pipes, glass and small finds. The course if taught largely by supervision and not lectures. Students will sort collections, draw objects, measure objects and identify them according to numerous criteria. Course Requirements: A prerequisite for this course is 070: 208, Survey of Historical Archaeology, normally taught in the Fall term. Students for whom this requirement was waived are expected to study a suitable textbook on the subject, such as Orser, C. 1995 Historical Archaeology and Deetz, J In small things forgotten. Students will attend one three hour class, once a week. During this time they will handle material, analyze it, and draw objects. Each student will need a clean writing pad or notebook, a pad of graph paper, pencils, colored pencils, eraser, a ruler, and a divider. There will be two exams, a midterm and final. Useful Texts: 1. Noel-Hume, I. 2001. The Artifacts of Colonial America 2. Fournier, Robert. Illustrated Dictionary of Practical Pottery. Paperback, 4th ed. 2000 Radnor Pa. Available at Amazon.com ($31.96) 3. Numerous additional sources will be present at class for used during the practicals. Colonial Archaeology: 070 330 Significant technical terms: (see Fournier 2000) Absorption: The taking up of liquid into the pores of a pot. The water absorption of a ceramic is an indicator of its degree of vitrification. -
Building Innovations
b BUILDING INNOVATIONS A MAGAZINE FOR ARCHITECTS NOV 2019 b BUILDING INNOVATIONS CONTENTS: FIND A PIC VISION - PAGE 6 NEWS - PAGE 14 INTERIOR DESIGN - PAGE 22 DOORS, WINDOWS & GLAZING - PAGE 42 ENVIRONMENTAL CONTROL - PAGE 50 VIEWPOINT - PAGE 60 PROJECT INSIGHT - PAGE 72 about Some of the colour photography used in Building Innovations is provided and paid for by contributors. The publishers do not accept liability for errors that may appear in the publication. Published in association with Jasper, Muz, and Kenny, who like to keep an eye on things in between meals. All rights reserved. No part of this publication may be reproduced or transmitted in any form or by any means without the consent of the publisher. Published by L2Media Ltd, Kingfishers Retreat, The Lodges, Dunston Business Village, Dunston ST18 9AB Tel: 01785 711591 Fax: 0845 862 8639 www.l2media.uk 2 3 i-build_rainguard:Layout 1 28/02/2018 14:59 Page 1 Always in tune with your style a comprehensive range of rainwater systems to accommodate all types of buildings and budgets Choose from modern, traditional and heritage rainwater systems, available in Aluminium, GRP, Copper, Zinc and Stainless Steel. Aluminium GRP For more information please call 0113 279 5854 Cast Iron Copper, Zinc & Stainless Steel or email [email protected] w w w . r a i n g u a r d . c o . u k VISION VISION Hotel PACAI, located in Vilnius, Lithuania, was named the winner of this year’s Surface Travel Awards in the category of large international hotels. The 104-room Hotel PACAI was selected out of seven short-listed hotels, and it was the only one listed that is not located in a traditional tourist destination or a metropolis. -
9. Ceramic Arts
Profile No.: 38 NIC Code: 23933 CEREMIC ARTS 1. INTRODUCTION: Ceramic art is art made from ceramic materials, including clay. It may take forms including art ware, tile, figurines, sculpture, and tableware. Ceramic art is one of the arts, particularly the visual arts. Of these, it is one of the plastic arts. While some ceramics are considered fine art, some are considered to be decorative, industrial or applied art objects. Ceramics may also be considered artifacts in archaeology. Ceramic art can be made by one person or by a group of people. In a pottery or ceramic factory, a group of people design, manufacture and decorate the art ware. Products from a pottery are sometimes referred to as "art pottery".[1] In a one-person pottery studio, ceramists or potters produce studio pottery. Most traditional ceramic products were made from clay (or clay mixed with other materials), shaped and subjected to heat, and tableware and decorative ceramics are generally still made this way. In modern ceramic engineering usage, ceramics is the art and science of making objects from inorganic, non-metallic materials by the action of heat. It excludes glass and mosaic made from glass tesserae. There is a long history of ceramic art in almost all developed cultures, and often ceramic objects are all the artistic evidence left from vanished cultures. Elements of ceramic art, upon which different degrees of emphasis have been placed at different times, are the shape of the object, its decoration by painting, carving and other methods, and the glazing found on most ceramics. 2. -
Earthenware Clays
Arbuckle Earthenware Earthenware Clays Earthenware usually means a porous clay body maturing between cone 06 – cone 01 (1873°F ‐ 2152°F). Absorption varies generally between 5% ‐20%. Earthenware clay is usually not fired to vitrification (a hard, dense, glassy, non‐absorbent state ‐ cf. porcelain). This means pieces with crazed glaze may seep liquids. Terra sigillata applied to the foot helps decrease absorption and reduce delayed crazing. Low fire fluxes melt over a shorter range than high fire materials, and firing an earthenware body to near vitrification usually results in a dense, brittle body with poor thermal shock resistance and increased warping and dunting potential. Although it is possible to fire terra cotta in a gas kiln in oxidation, this is often difficult to control. Reduced areas may be less absorbent than the rest of the body and cause problems in glazing. Most lowfire ware is fired in electric kilns. Gail Kendall, Tureen, handbuilt Raku firing and bodies are special cases. A less dense body has better thermal shock resistance and will insulate better. Earthenware generally shrinks less than stoneware and porcelain, and as a result is often used for sculpture. See Etruscan full‐size figure sculpture and sarcophagi in terra cotta. At low temperatures, glaze may look superficial & generally lacks the depth and richness of high fire glazes. The trade‐offs are: • a brighter palette and an extended range of color. Many commercial stains burn out before cone 10 or are fugitive in reduction. • accessible technology. Small electric test kilns may be able to plug into ordinary 115 volt outlets, bigger kilns usually require 208 or 220 volt service (the type required by many air conditioners and electric dryers). -
Arts of the Indus Valley
2 ARTS OF THE INDUS VALLEY HE arts of the Indus Valley Civilisation emerged during Tthe second half of the third millennium BCE. The forms of art found from various sites of the civilisation include sculptures, seals, pottery, jewellery, terracotta figures, etc. The artists of that time surely had fine artistic sensibilities and a vivid imagination. Their delineation of human and animal figures was highly realistic in nature, since the anatomical details included in them were unique, and, in the case of terracotta art, the modelling of animal figures was done in an extremely careful manner. The two major sites of the Indus Valley Civilisation, along the Indus river—the cities of Harappa in the north and Mohenjodaro in the south—showcase one of earliest examples of civic planning. Other markers were houses, markets, storage facilities, offices, public baths, etc., arranged in a grid-like pattern. There was also a highly developed drainage system. While Harappa and Mohenjodaro are situated in Pakistan, the important sites excavated in India are Lothal and Dholavira in Gujarat, Rakhigarhi in Haryana, Bust of a bearded priest Ropar in Punjab, Kalibangan in Rajasthan, etc. Stone Statues Statues whether in stone, bronze or terracotta found in Harappan sites are not abundant, but refined. The stone statuaries found at Harappa and Mohenjodaro are excellent examples of handling three-dimensional volumes. In stone are two male figures—one is a torso in red sandstone and the other is a bust of a bearded man in soapstone—which are extensively discussed. The figure of the bearded man, interpreted as a priest, is draped in a shawl coming under the right arm and covering the left shoulder. -
Cincinnati Art Asian Society Virtual November 2020: Asian Ceramics
Cincinnati Art Asian Society Virtual November 2020: Asian Ceramics Though we can't meet in person during the pandemic, we still want to stay connected with you through these online resources that will feed our mutual interest in Asian arts and culture. Until we can meet again, please stay safe and healthy. Essays: East and West: Chinese Export Porcelain https://www.metmuseum.org/toah/hd/ewpor/hd_ewpor.htm Introduced to Europe in the fourteenth century, Chinese porcelains were regarded as objects of great rarity and luxury. Through twelve examples you’ll see luxury porcelains that appeared in Europe in the fifteenth and sixteenth centuries, often mounted in gilt silver, which emphasized their preciousness and transformed them into entirely different objects. The Vibrant Role of Mingqui in Early Chinese Burials https://www.metmuseum.org/toah/hd/mgqi/hd_mgqi.htm Burial figurines of graceful dancers, mystical beasts, and everyday objects reveal both how people in early China approached death and how they lived. Since people viewed the afterlife as an extension of worldly life, these ceramic figurines, called mingqi or “spirit goods,” disclose details of routine existence and provide insights into belief systems over a thousand-year period. Mingqi were popularized during the formative Han dynasty (206 B.C.–220 A.D.) and endured through the turbulent Six Dynasties period (220–589) and the later reunification of China in the Sui (581–618) and Tang (618–907) dynasties. There are eleven ceramic burial goods (and one limestone) as great examples of mingqui. Indian Pottery https://www.veniceclayartists.com/tag/indian-pottery/ The essay is informative but short. -
Mini Catalog
CLAY ART CENTER MINI CATALOG CLAY ART CENTER 2636 Pioneer Way East Tacoma Wa 98404 800-952-8030 Fax 253-922-5349 www.clayartcenter.net AUG 25, 2020 CLAY ART CENTER 2636 Pioneer Way East Tacoma WA 98404 1-800-952-8030 Fax 1-253-922-5349 1 CLAY DESCRIPTIONS CONE 06 CLAYS is widely used for vitreous tiles fired at cone 4 to 6 and is also used in outdoor installations where freezing is a con- CL 027 COLEMAN RAKU cern. A fine tooth throwing body with kyanite grog. Will resist firing stress and gain in strength as the mullite develops. The clay will fire as hot as cone 10 and retain its off white color. CONE 4-6 CLAYS CL 141 AKIO SCULPTURE CL 126 COLEMAN RAKU GROG A heavy grogged clay that is excellent for large sculpture. A throwing body with larger kyanite grog. Will resist firing Brown in reduction, fires to cone 6. stress and gain in strength as the mullite develops. The clay will fire as hot as cone 10 and retain its off white color. CL 140 ARLEO Thin chopped nylon fiber adds stength to this medium CL 171 HUSKY WHITE smooth clay. Perfect for difficult sculpture work. Light tan, Husky White is a low fire white earthenware body with fine fires to cone 6. sand. Ideal for throwing and handbuilding. CL 108 BC6 CL155 HUTCHINS RAKU A great throwing, white, stoneware. Very smooth and plastic, Great throwing smooth raku body, light color with good crack excellent glaze fit. Gray to off-white in oxidation. -
Holds the Key Ingredient... Contents
2016 holds the key ingredient... Contents About Us 3 How To Choose The Right Clay For You 4 Our Clays 6 Terracotta 6 Alex Shimwell Stoneware 7 Earthstones 10 Professional 13 Porcelain 16 Earthenware 17 French Regional Clays 18 Paper Clays 18 Powdered Clays 19 Slips 21 Casting Slips 21 Pouring Slips 21 Decorating Slips 21 Raw Materials 22 China/Ball Clays 22 Raw Clays 22 Fluxes 22 Oxides 23 Groggs 23 Plasters 23 Deflocculants 23 Sundry Materials 24 Custom Clay Formulas & Special Order Clays 25 Warranties & Responsibilities 25 Technical Information 26 Jane Wheeler 2016 Price List 30 Distributors 34 Front cover images are provided by... Top: Clare Wakefield Bottom: Beverley Gee, Garry & Pollie Uttley, Susanne Luckacs-Ringel 2 INFO About Us In the heart of the potteries over the past 36 years over 90 clay bodies to choose from Valentine Clays has Valentine Clays, a family run manufacturer, has worked ensured that there is a product to suit a potters every directly with the studio potter community formulating need whether you are a beginner or a professional. and fine tuning clays using the best possible ingredients. For advice or help with any technical issues please call This close working relationship enables the world-leading 01782 271200 or email [email protected] clay manufacturer and raw materials supplier; based we will be only too pleased to help. in Stoke-on-Trent, to successfully develop ceramic clay bodies to suit the specific requirements of a long list of renowned British and International potters. The team at Valentine Clays prides itself on constant development of new and innovative clays bodies using Kind regards, the latest ceramic manufacturing equipment; with The Valentine Clays Team Thank you to the studio potters whose images, taken from our online gallery, have been used in this brochure. -
Casting Slip Recipes
CASTING SLIP RECIPES The recipes shown below make approximately 25 gallons of casting slip (apart from those marked with an *). The pint weight is approximately 35 - 35 1/2 ounces. The below information is based on Valentine Clays Casting Slips and is subject to change and your personal requirements or adjustments that may be needed. Standard Red Terracotta HT Stoneware Clay Water Soda Ash Sodium Silicate 140s Clay Water Soda Ash Sodium Silicate 140s 200kgs 7 gallons 110gms 310gms 225kgs 5 gallons 100gms 650gms 12.5kgs* 2 Litres 7gms 19.4gms 12.5kgs* - - - B17C Stoneware Millennium White Stoneware Clay Water Soda Ash Sodium Silicate 140s Clay Water Soda Ash Sodium Silicate 140s 175kgs 7 gallons 100gms 240gms 180kgs 4.5 gallons 80gms 250gms 12.5kgs* 2.2 Litres 7gms 17gms 12.5kgs* 1.42 Litres 5.5gms 17.5gms Special Porcelain P2 Porcelain Clay Water Soda Ash Sodium Silicate 140s Clay Water Soda Ash Sodium Silicate 75s 225kgs 7 gallons - 200gms 225kgs 6 gallons - 425gms 12.5kgs* 2 Litres - 12.5gms 12.5kgs* 1.5 Litres - 23.5gms Bone China Parian Clay Water Soda Ash Sodium Silicate 75s Clay Water Soda Ash Sodium Silicate 140s 225kgs 7 gallons - 510gms 225kgs 7 gallons - 200gms 12.5kgs* 1.8 Litres - 28.5gms 12.5kgs* 1.8 Litres - 11gms Standard White Earthenware LF White Earthenware Clay Water Soda Ash Sodium Silicate 140s Clay Water Soda Ash Sodium Silicate 140s 225kgs 5 gallons 80gms 250gms 200kgs 5 gallons 60gms 200gms 12.5kgs* 1.26 Litres 4.5gms 14gms 12.5kgs* 1.42 Litres 4gms 12.5gms ES 10 (Extra Smooth) ETC Semi Porcelain Clay Water Soda -
Sustainability TILE Gold Book
November/December 2020 Magazine Sustainability TILE Gold Book www.tile-magazine.comw CUSTOM® GROUT SOLUTIONS RIGHT GROUT. RIGHT COLOR. FOR ANY JOB. Q The performance and handling you need — we have the right grout for every job. Q 40 colors, available in all grouts, to complement any tile and stone installation. Q Grout Solutions are backed by the strength of Custom Building Products. For the right grout — In the right color — Count on CUSTOM. Available at The Home Depot CustomBuildingProducts.com DOWNLOAD CUSTOM’S and tile distributors MOBILE APP 800-272-8786 nationwide. SIGNATURESTYLE The expansive assortment of styles, cutting edge materials, modern palettes, and exquisite attention to detail set MSI’s backsplash and wall tile collection apart from the rest. And now there’s even more to love, with the introduction of our beautifully crafted waterjet mosaics. From fresh takes on classic shapes like hexagon and arabesque to charming floral motifs and retro- revived patterns, these inspirational looks give backsplashes, walls, and floors signature style. DANZA ARABESQUE WHITE QUARRY LA FLEUR BLANCO LYNX ROYAL LINK DANZA ARABESQUE SAVONA CARRARA WHITE BIANCO CARRARA WHITE BIANCO STARLITE BIANCO GRIDWORK FACETED QUATREFOIL ELLIPSIS SLABS & COUNTERTOPS PORCELAIN & CERAMIC LUXURY VINYL TILE HARDSCAPES NATURAL STONE DECORATIVE ACCENTS MSISURFACES.COM Let's get started. November/December 2020 Vol. 17, No. 8 www.tile-magazine.com Magazine Features 12 Contractor Spotlight 14 Product Showcase 20 Recreating Spain in New York 32 Emulating the Mountainscape -
CN Terracotta Facade Systems
Terracotta North America CN Terracotta Facade Systems designed, engineered, and natural CN Terracotta Facade Systems Contents page About 3-4 Manufacturing and Quality Control 5 Facade Profiles and Technical Data 6-10 Colours 11 Finishes and textures 12 Custom Solutions 13-14 Sunshading 15-19 About Terracotta North America CN Terracotta North America is a CN Cermic (Jingsu) Co. Ltd., a quality of traditional techniques, collaboration between CN Ceramic solely invested enterprise by CN along with the clay source, has and Terra Cotta Contract llc, to bring Ceramic (Hong Kong) Co. Ltd., is made Yixing “the pottery capital of CN’s proven products to the North among the premier terracotta panel China.” CN has carried this American market. CN brings a manufacturers in the world, thousand year tradition into its strong tradition of manufacturing developing, producing, and selling manufacturing process to create a know how and innovation developed wall materials that include terracotta product of quality with an through years of production for louvers, terracotta panel and high- unprecedented amount of natural domestic and international markets grade exterior wall split tile. colours and finishes. as Terracotta Contract brings years of expertise in servicing the CN utilizes only the best German architectural community in detail and an Italian machinery for its tile development and solution creation. creation and manufactures to the standards set by ISO9000 and Through this we will be able to meet ISO14001 – but this is just one the demands of your project component of a quality panel. technically and economically. We Equally as important as machinery look forward to being your solution that creates it, is the source of the provider. -
Ceramics Art +Perception
Ceramics Art + Perception #110 October 2018 USD $20 EUR €18 CAD $27 AUD $27 GBP £15 ART Karen Koblitz: Art Ambassador Across Cultures Written by Jo Lauria WWW.MANSFIELDCERAMICS.COM he artistic career of American During her successive return trips to ceramist Karen Koblitz has been Deruta, Koblitz spent time becoming fluent in driven, and defined, by wanderlust. the language and culture of the Italian people Unlike the casual traveler, Koblitz’s with whom she worked and communed. She globe-trekking has not centered also made several trips to nearby Florence to Ton the greatest hits of tourist destinations but research the prominent collections of historical rather, pointedly and deliberately, in pursuit ceramics in museums and the Renaissance of enriching her worldview and enhancing her terracotta sculptures of the Della Robbia art knowledge. Cultural Diplomacy, a one- workshop installed above altars and within person exhibition in 2018, presented work of the chapels in many Florentine churches. This last twenty-seven years, primarily pieces that research directly impacted the direction of Koblitz created in response to her international Koblitz’s work; she embarked upon the Italian journeys. A close study of several individual Column and the Italian Lunette Series. pieces featured in the show reveal the profound The ubiquitous Italian marble pedestals that multicultural connections Koblitz has forged elevate portrait busts of luminaries were during these experiences. Koblitz’s template for the column series, but characteristically, the artist appropriated the Ephemeral and memorable, the unglazed white porcelain sculptures had a ghostly materiality, seeming to provide a portal to the contemplative space where memories roam and unfold.