(12) Patent Application Publication (10) Pub. No.: US 2015/0013926 A1 JAAKKOLA Et Al
Total Page:16
File Type:pdf, Size:1020Kb
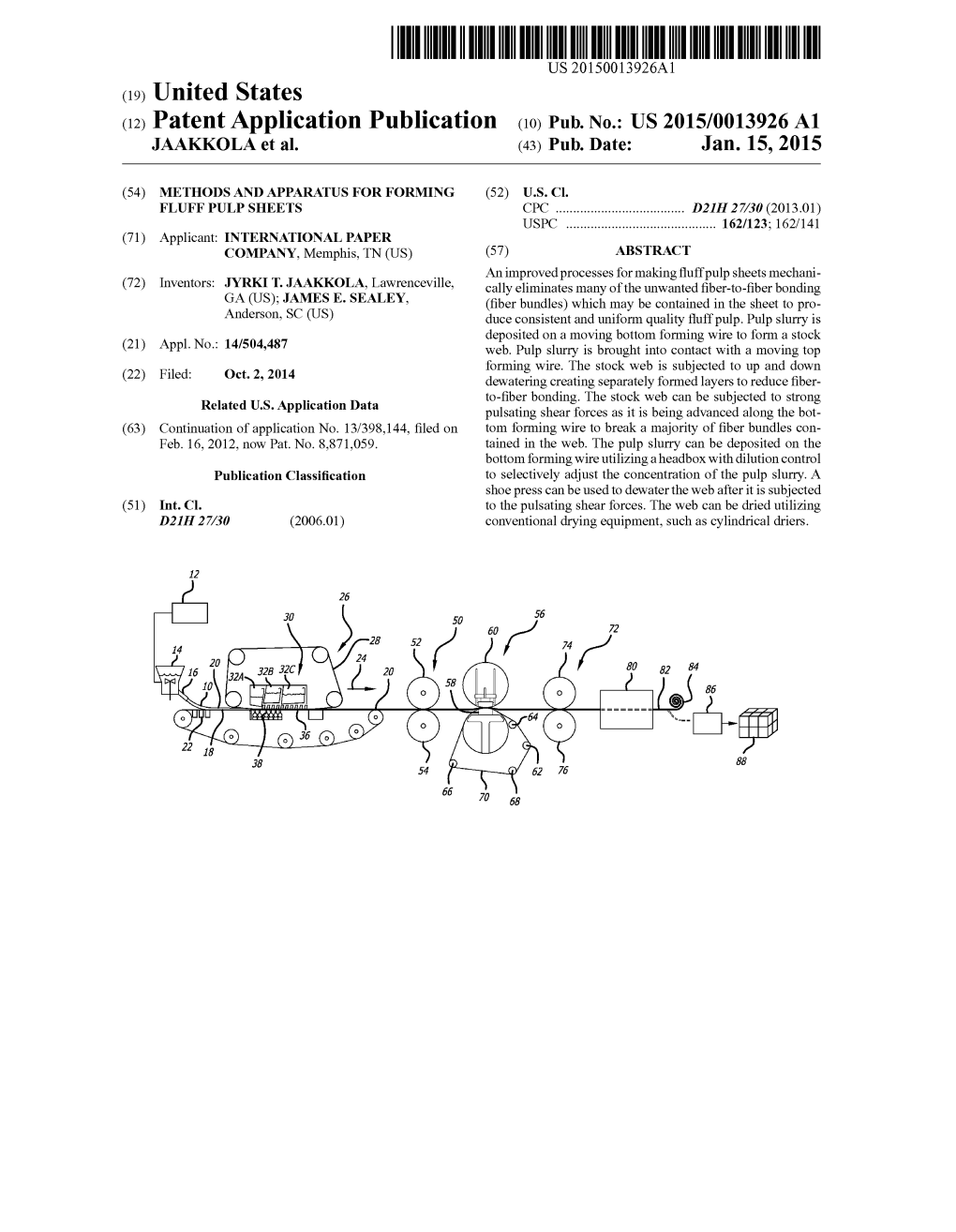
Load more
Recommended publications
-
Supply Chain
COMPANY OVERVIEW 2015 MAKING PRODUCTS PEOPLE DEPEND ON EVERY DAY PERFORMANCE PEOPLE PLANET International Paper is a global leader in packaging, paper, and pulp. We use renewable resources responsibly to make recyclable products that people depend on every day. We are unified around shared commitments to strengthen our people and communities, provide solutions for our customers, and ensure the sustainability of our company and our planet. Our fiber sourcing policies promote healthy and productive forests for generations to come In 2015, 93% of our facilities operated without a serious injury $15.5 million donated to address critical community needs and improve MAKING our planet PRODUCTS PEOPLE DEPEND ON CONTENTS EVERY DAY 2 2015 Highlights 3 CEO Comments 4 Businesses 6 Performance 12 People $22.4 billion 20 Planet net sales in 2015 28 Awards & Recognitions 29 Vision 2020 Goals International Paper Company Overview 2015 2 65% 13% 22% REVENUE Industrial Consumer Paper 2015 GLOBAL HIGHLIGHTS Packaging Packaging and Pulp We use renewable resources responsibly to make recyclable products people depend on every day. BY BUSINESS $2.6 billion net sales Manufacturing operations in 24 countries EMEA*/ Russia North Asia ** America $1.3 billion net sales Global 55,000 India $17.2 billion Headquarters: employees globally net sales Memphis, Tenn. $0.2 billion Latin net sales America 44,000 $1.1 billion volunteer hours net sales *Europe, Middle East, Africa worked by employees **Includes the net sales of the International Paper Sun joint venture through -
Ref. 676.03 SMO 2Nd
INDEX Refer to Chapter Refer to Chapter Refer to Chapter A test 14 acid pretreatment 10 acetate 4 acidproof brick 8 abaca 3 acetate laminating 18 acid pulping 8 abatement 20 acetate pulp 4 acid rain 21 odor 21 acetic acid 4 acid-refined tall oil 6 pollution 20 acetic anhydride 4 acid-resistant 14 abatement device 21 acetone 4 acid size 5 abietic acid 6 acetylated starch 5 acid-stable size 5 abrasion 24 acetyl radical 4 acid sulfite process 8 abrasion debarker I acetylating agent 4 acid tower 8 abrasion resistance 14 acid(s) 4, 8 acid treatment 10 abrasion test 14 abietic 6 acidulating 4 abrasive 7 acetic 4 acidulating agent 4 abrasive backing papers 16 accumulator 8 acidulation 6 abrasiveness 14 carbonic 20 acoustical board 16 abrasive segment 7 Caro's 10 acoustical testing 14 abrasivity (of mineral fillers) 13 cooking 8 acoustic leak detector 9 absorbency 11,14 digester 8 acre-foot 20 relative II fatty 6 acrylamide resins 5 water II formamidine sulfinic 10 acrylic binders 17 absorbent 14,24 formic 4 acrylic fiber 3 absorbent capacity II glucuronic 4 activatable chemical 9 absorbent grades 16 humic 20 activated carbon 20 absorption 5 hydroxy 4 activated sludge 20 capillary 13 hypochlorous 10 activated sludge loading 20 ink 14 lignosulfonic 8 activated sludge process 20 light 14 linoleic 6 activation 4 mechanical 13 mineral 4 surface II tensile energy 14 oleic 6 activation energy 8 vapor 13 pectic 4 Arrhenius 4 absorption coefficient 14 peracetic 10 activator 5 accelerated aging 14 raw 8 active alkali 8 accelerated aging test 14 resin -
Terminology on Paper & Pulp: Types of Paper and Containerboard, Containerboard Grades and Tests
Terminology On Paper & Pulp: Types of Paper and Containerboard, Containerboard Grades and Tests Prepared for the Meeting of the Paper & Pulp Industry Project By Aselia Urmanbetova Date: September 10, 2001 1 Paper Products Chart: Containerboard Tree/Waste Paper Pulp Paper Paperboard Brown Coated Uncoated (container- board) Brown (65% White (95%- Copying Paper Newsprint hardwood and 100% 35% softwood) softwood) White Tissue (paperboard package) SBS (Solid Boxboard Bleach Sulfate) Coated Uncoated 2 Examples of Containerboard Grades/Mead Corporation: (Refer to the Glossary for the Explanation of the Terms) Standard Grades Grade Basis Weight Moisture Ring Crush Concora 26 SC 26.0 9.0 N/A 63 30 SC 30.0 9.0 50 68 33 SC 33.0 9.0 60 72 36 SC 36.0 9.0 71 79 40 SC 40.0 9.0 82 79 45 SC 45.0 9.0 102 95 Light Weights Grade Basis Weight Moisture Porosity Concora STFI 18 SC 18.0 7.5 30 33 9.5 20 SC 20.0 7.5 30 35 10.5 23 SC 23.0 9.0 30 59 12.0 Polar Chem Grade Basis Weight Moisture Ring Crush Concora Wet Mullen 30 PC 30.0 9.0 50 68 4.0 33 PC 33.0 9.0 60 72 4.0 36 PC 36.0 9.0 71 79 4.0 40 PC 40.0 9.0 82 79 4.0 45 PC 45.0 9.0 102 95 4.0 3 Paper Products and Containerboard Glossary B Flute A flute that is approximately 0.097 inches high. -
MERCER COUNTY IMPROVEMENT AUTHORITY SOLID WASTE and RECYCLING QUANTIFICATION and CHARACTERIZATION STUDY
REPORT FOR MERCER COUNTY IMPROVEMENT AUTHORITY SOLID WASTE and RECYCLING QUANTIFICATION and CHARACTERIZATION STUDY PREPARED BY T&M ASSOCIATES 1256 NORTH CHURCH STREET, MOORESTOWN, NJ 08057 856.722.6700 | TANDMASSOCIATES.COM September 2015 TABLE OF CONTENTS EXECUTIVE SUMMARY ............................................................................................................................ 1 INTRODUCTION ........................................................................................................................................ 2 BACKGROUND ............................................................................................................................................. 2 MERCER COUNTY RECYCLING PROGRAM | SOLID WASTE MANAGEMENT PLAN ........................................ 2 METHODOLOGY ....................................................................................................................................... 4 GENERAL ..................................................................................................................................................... 4 BASIS OF STUDY | ASTM D5231 ................................................................................................................. 4 T&M PERSONNEL AND TRAINING ................................................................................................................ 5 SAMPLING PROCEDURES ............................................................................................................................ 6 SORTING -
Sanitary Products
About Nordic Swan Ecolabelled Sanitary Products Version 6.8 Background to ecolabelling 04 May 2021 Content 1 Summary 3 2 Basic facts about the criteria 5 2.1 Sanitary products that may carry the Nordic Swan Ecolabel 5 2.2 Justification for Nordic Ecolabelling 6 3 About the criteria revision 7 3.1 Earlier versions of the criteria 8 3.2 Nordic Swan Ecolabel licences in the Nordic Market 8 4 The Nordic market 9 5 Other labels 10 6 Environmental assessment of sanitary products 12 6.1 Disposable products 12 6.2 Material composition 15 6.3 Environmental conditions for the materials 20 6.4 Renewable versus fossil-based materials 24 6.5 Relevance, Potential and Steerability 25 7 Justification of the requirements 27 7.1 Product group definition 27 7.2 Environmental requirements in general 30 7.3 Description of the product 35 7.4 Requirements for chemical products and chemical substances 36 7.5 Requirements concerning materials in the product and packaging 49 7.6 Product performance 92 7.7 Quality and regulatory requirements 94 8 Changes compared to previous version 95 9 Terms and definitions 97 Appendix 1 Requirement for regenerated cellulose Appendix 2 Guidelines for standard, renewable comoditives 023 Sanitary Products, version 6.8, 04 May 2021 This document is a translation of an original in Norwegian. In case of dispute, the original document should be taken as authoritative. Addresses In 1989, the Nordic Council of Ministers decided to introduce a voluntary official ecolabel, the Nordic Swan Ecolabel. These organisations/companies operate the Nordic ecolabelling system on behalf of their own country’s government. -
International Paper Equity Earnings and Dividends Received by International Paper, Have Been Prepared by the Management of Ilim
Investor Roadshow | February 23, 2017 Forward-Looking Statements Certain statements in these slides and made during this presentation may be considered forward-looking statements. These statements reflect management's current views and are subject to risks and uncertainties that could cause actual results to differ materially from those expressed or implied in these statements. Factors which could cause actual results to differ include but are not limited to: (i) the level of our indebtedness and changes in interest rates; (ii) industry conditions, including but not limited to changes in the cost or availability of raw materials, energy and transportation costs, competition we face, cyclicality and changes in consumer preferences, demand and pricing for our products; (iii) global economic conditions and political changes, including but not limited to the impairment of financial institutions, changes in currency exchange rates, credit ratings issued by recognized credit rating organizations, the amount of our future pension funding obligation, changes in tax laws and pension and health care costs; (iv) unanticipated expenditures related to the cost of compliance with existing and new environmental and other governmental regulations and to actual or potential litigation; (v) changes in our estimates for the costs and insurance coverage associated with the recent incident at our Pensacola, Florida mill and for the time required to resume full operations at the mill; (vi) whether we experience a material disruption at one of our other manufacturing facilities; (vii) risks inherent in conducting business through joint ventures; (viii) the failure to realize the expected synergies and cost-savings from our purchase of the cellulose fibers business of Weyerhaeuser Company; and (ix) our ability to achieve the benefits we expect from all other strategic acquisitions, divestitures and restructurings. -
22) General Principles of Food Packaging: Packaging Materials 1
22) GENERAL PRINCIPLES OF FOOD PACKAGING: PACKAGING MATERIALS 1. Glass Pliny the Elder recorded that Phoenician sailors came ashore and, not finding any local materials suitable for supporting their cooking pots above the sandy shore, used lumps of trona (natural soda or sodium carbonate) that formed part of their ship’s cargo. As the trona was heated in the fire it combined with the sand to give a material that flowed. This story may not be entirely accurate but points to the fact that glass as a man-made material has a long history and some of the oldest dated Middle Eastern pieces are over 4000 years old; a deep blue charm is estimated to date from 7000 BC. Egyptians and Romans fashioned a wide range of intricate and colored glass objects. A highly developed industry existed in Syria in 1500 BC. In medieval times the centre of the glass blowing expertise was Venice (1200-1600 AD). The serendipitous preparation of glass by the Phoenician sailors is basically the same as that used today. A mixture of purified sand is heated with sodium and calcium carbonate together with some sodium sulphate. The gases evolved help to stir the mixture. The addition of calcium is necessary to make the glass insoluble in water - simple sodium glass is water soluble to give a very viscous liquid known as water-glass (used as an egg preservative in WW2). For those who like the chemistry: Na2CO3 + SiO2 -> Na2SiO3 + CO2 CaCO3 + SiO2 -> CaSiO3 + CO2 Na2SO4 + SiO2 -> Na2SiO3 + SO3 Glass made as above is known as soda-glass. -
Sunday, October 27, 2019
PROGRAM TRACKS Engineering, Reliability, Energy, Recovery, Lime Career Development Environmental Corrosion & Materials Kiln and Recaust Nonwood Pulping & Bleaching Recycling Forum Sustainability IBBC Conference PROGRAM AS OF 05/11/19 ( SUBJECT TO CHANGE) Sunday, October 27, 2019 7:30AM – 4:00PM Bleach Plant Operations Workshop** 8:00AM – 4:00PM Brown Stock Washing Workshop** 8:00AM – 4:00PM Project Management Workshop** 12:00PM – 1:00PM Joint Team Review of Conference Logistics* 1:00PM - 4:30PM Engineering Division & Pulp Manufacture Division Councils* 4:00PM - 5:00PM Nonwood Fiber Committee Meeting 4:00PM - 5:00PM Alkaline Pulping & Bleaching Committee Meeting 5:00PM – 7:00PM Welcome Reception & Exhibit 7:00PM -9:30PM Awards Dinner* * Invitation Only ** Additional registration fee required *** Pre-registration required Monday, October 28, 2019 7:00AM – 8:15AM Speaker Breakfast 7:30AM-8:30AM Women in Industry Breakfast 8:30AM – 10:00AM Session 1: Opening Session & Keynote Session Chair: Carl Houtman, USDA Forest Products Laboratory Keynote: Angie Slaughter, Vice President Sustainability, Anheuser - Busch 10:00AM – 10:30AM Break & Exhibit Open 10:30AM – 12:00PM Session 2: State of the Industry Session Chair: AF&PA Sustainability Update - Jerry Schwartz, American Forest & Paper Association 10:30AM – 12:00PM Session 3: Pulping Optimization Session Chair: Pulp Suspension Density Evaluation for Improved Production Calculation at the Discharge of a Continuous Digester - Bruno Goncalves, Lwarcel Celulose Technical and Economic Modelling of -
Case M.8096 - INTERNATIONAL PAPER COMPANY / WEYERHAEUSER TARGET BUSINESS
EUROPEAN COMMISSION DG Competition Case M.8096 - INTERNATIONAL PAPER COMPANY / WEYERHAEUSER TARGET BUSINESS Only the English text is available and authentic. REGULATION (EC) No 139/2004 MERGER PROCEDURE Article 6(1)(b) NON-OPPOSITION Date: 20/10/2016 In electronic form on the EUR-Lex website under document number 32016M8096 EUROPEAN COMMISSION Brussels, 20/10/2016 In the published version of this decision, some C(2016) 6844 final information has been omitted pursuant to Article 17(2) of Council Regulation (EC) No 139/2004 PUBLIC VERSION concerning non-disclosure of business secrets and other confidential information. The omissions are shown thus […]. Where possible the information omitted has been replaced by ranges of figures or a general description. To the Notifying Party Dear Sir/Madam, Subject: Case M.8096 – International Paper Company / Weyerhaeuser Target Business Commission decision pursuant to Article 6(1)(b) of Council Regulation No 139/20041 and Article 57 of the Agreement on the European Economic Area2 (1) On 15 September 2016, the European Commission received notification of a proposed concentration pursuant to Article 4 of the Merger Regulation by which International Paper Company ("IP", United States) will acquire sole control over the pulp business of Weyerhaeuser Company ("WTB", United States) within the meaning of Article 3(1)(b) of the Merger Regulation, by way of purchase of assets and shares (hereafter the "Transaction"). IP are designated hereinafter as the 'Notifying Party' and together with WTB 'Parties' to the proposed transaction. 1. THE PARTIES (2) IP is a packaging and paper company with manufacturing operations in North America, the EEA, Latin America, Russia, Asia and North Africa. -
Project Title: Hemicellulose Pre-Extraction for Fluff Kraft Pulp Production GT Project Staff: Principal Investigator: Ragauska
Project Title: Hemicellulose Pre-Extraction For Fluff Kraft Pulp Production GT Project Staff: Principal Investigator: Ragauskas/Pu Institute of Paper Science and Technology PROJECT OBJECTIVE: The objective of this project is to develop viable methods for extracting hemicelluloses from SW chips prior to kraft pulping providing fluff pulp manufacturers: • Pulps with reduced bonding properties • A new hemicellulose resource stream that could be marketed to the burgeoning biofuel industry. • Enhanced kraft pulping operations. This project builds on the current success of preliminary hemicellulose pre-extraction studies by Ragauskas et al.1 which have identified acidic and alkaline extraction conditions for the pre-extraction of wood hemicelluloses for southern SW. These studies established the general viability of this proposed technology. This project will tailor the hemicellulose pre-extraction process for SW fluff pulps production. This project directly address key research needs of the forest products industry as stated in AFPA Agenda 2020 research vision which states that the industry needs to better utilizing its raw materials for higher value products. The pre-extraction of hemicelluloses from wood has been identified by the AFPA CTO committee as a key component in the evolution of the kraft pulp mill which maximizes profit from the conversion of wood into cellulosic materials and secondary products including renewable energy. The proposed research plan is also in line with the Institute’s research emphasis on “Better Utilization of Wood for Non-Fiber Materials, Chemicals, Fuels, and Energy - Biorefinery.” PROJECT BACKGROUND: Traditional pulp and paper producers are facing increasing competition from off-shore tropical pulp manufacturers that have low cost wood and labor advantages. -
Basic Glossary of Papermaking Terms
Basic Glossary of Papermaking Terms ABRASION RESISTANCE Ability of paper product to withstand abrasion. Measured by determining degree and rate that a sample loses weight under specific rubbing action of an abrading substance, such as an eraser. ABSORBENCY Property of pulp, paper, and its constituents and products that permits the entrainment and retention of other materials it contacts, such as liquid, gaseous and solid substances. ACCEPTS Stock after it has been subjected to some cleaning processes. AFTER DRYERS The bank of dryers positioned after intermediate or sizing rolls. AGITATOR (1) Propeller or agitating shaft for stirring the pulp suspension in a chest or tank. (2) A rotating device for mixing fluids and fluid suspension in a tank or chest. AIR DRY (a.d.) Weight of moisture-free pulp or paper plus a nominal 10% moisture based on traditional assumption that this amount of moisture exists when they come into equilibrium with the atmosphere. AIR DRYING A method of drying the paper web on the paper machine by blowing air along the direction of the web. ALUM Papermaking chemical commonly used for precipitating rosin size onto pulp fibres to impart water- resistant properties (when used for water treatment) to the paper. Also, used for pitch control. More correctly called aluminium sulphate. ANTI-TARNISH PAPER Term originally applied to higher weight tissues used for wrapping silverware, but now used for all papers so prepared that they will not rust of discolour razor blades, needles, silverware etc. APPARENT DENSITY Weight (mass) per unit volume of a sheet of paper obtained by dividing the basis weight (or grammage) by the caliper (thickness). -
15-16 NOVEMBER 2016 ÖRNSKÖLDSVIK,SWEDEN Content
15-16 NOVEMBER 2016 ÖRNSKÖLDSVIK,SWEDEN Content Workshop programme ...................................................................................................................................3-4 Keynote speakers .................................................................................................................................................5 Organizers ................................................................................................................................................................6 Sponsors ....................................................................................................................................................................7 Some news from an old polymer, Thomas Rosenau ......................................................................9 A chemical that grows, Denis Sens .........................................................................................................11 Presentation abstracts .....................................................................................................................................13 Poster abstracts ...................................................................................................................................................77 08:15-08:55 Registration and coffee 08:55-09:10 Welcome and introduction Ulf Germgård, Karlstad University, Sweden Kristina Elg Christoffersson, Domsjö Fabriker AB, Sweden 09:10-09:40 Celluloses I and II-Some news from an old polymer Invited speaker: Thomas Rosenau,