(12) Patent Application Publication (10) Pub. No.: US 2016/0376467 A1 Puffer, SR
Total Page:16
File Type:pdf, Size:1020Kb
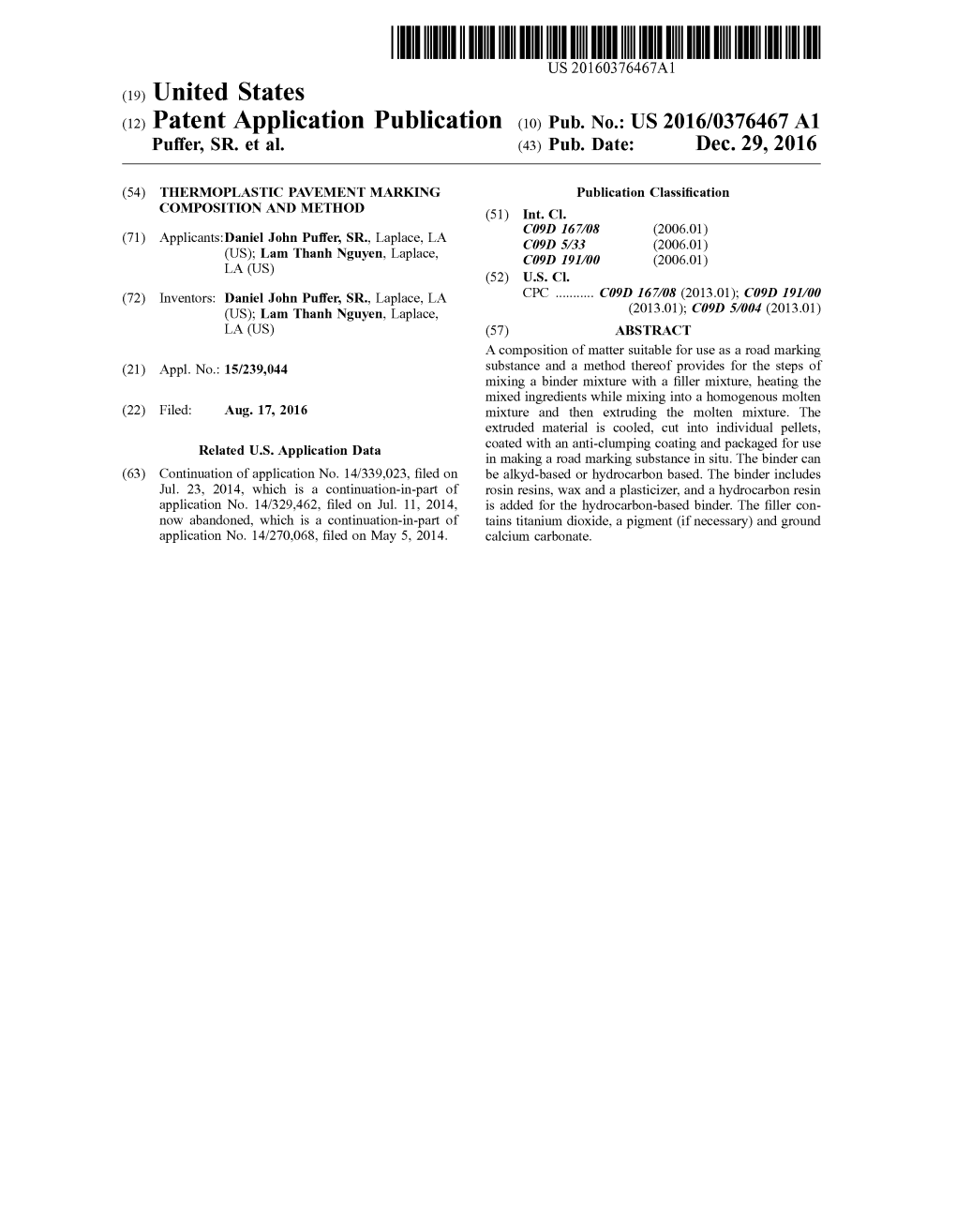
Load more
Recommended publications
-
A Rapid and Robust Method for Determination of 35 Phthalates in Influent, Effluent and Biosolids from Wastewater Treatment Plants
37th International Symposium on Halogenated Persistent Organic Pollutants Vancouver, Canada August 20-25, 2017 Page 1 – June-14-17 Page 2 – June-14-17 Page 3 – June-14-17 A Rapid and Robust Method for Determination of 35 Phthalates in Influent, Effluent and Biosolids from Wastewater Treatment Plants Tommy BISBICOS, Grazina PACEPAVICIUS and Mehran ALAEE Science and Technology Branch, Environment and Climate Change Canada Burlington, Ontario Canada L7S 1A1 Polyvinyl Chloride (PVC) • PVC was accidentally synthesized in 1835 by French chemist Henri Victor Regnault • Ivan Ostromislensky and Fritz Klatte both attempted to use PVC in commercial products, • But difficulties in processing the rigid, sometimes brittle polymer blocked their efforts. • Waldo Semon and the B.F. Goodrich Company developed a method in 1926 to plasticize PVC by blending it with various additives. • The result was a more flexible and more easily processed material that soon achieved widespread commercial use. From Wikipedia; accessed Oct, 2014 Plasticizers • Most vinyl products contain plasticizers which dramatically improve their performance characteristic. The most common plasticizers are derivatives of phthalic acid. • The materials are selected on their compatibility with the polymer, low volatility levels, and cost. • These materials are usually oily colorless substances that mix well with the PVC particles. • 90% of the plasticizer market is dedicated to PVC • worldwide annual production of phthalates in 2010 was estimated at 4.9 million tones* From Wikipedia; accessed Oct, 2014; and Emanuel C (2011) Plasticizer market update. http://www.cpsc.gov/about/cpsia/chap/spi.pdf (accessed March, 2014). Phthalate Uses • Plasticizers: – Wire and cable, building and construction, flooring, medical, automotive, household etc., • Solvents: – Cosmetics, creams, fragrances, candles, shampoos etc. -
Consumer Safety Compliance Standards for Use with These New Testing Regulations
Your Science Is Our Passion® Consumer Safety Analytical Standards for Consumer Safety Compliance New regulations are constantly being enacted to protect consumers from a variety of potentially dangerous compounds and elements. Recent global regulations have restricted levels of heavy metals in consumer products and waste electronics. Regulations have also been enacted to control a variety of phthalates in children’s products. SPEX CertiPrep has continued to lead the Certified Reference Materials field by creating a line of Consumer Safety Compliance Standards for use with these new testing regulations. For additional product information, please visit www.spexcertiprep.com/inorganic-standards/consumer-safety-standards-inorganic for Inorganic products and www.spexcertiprep.com/organic-standards/consumer-safety-standards-organic for Organic products. Phthalates in Polyvinyl Chloride (PVC) Polyvinyl chloride, or PVC, is a very common plastic used in a wide range of common consumer products, from children’s toys and care items to building and construction materials. In the US, ASTM and the CPSC have designated methods for testing children’s toys and childcare articles for compliance with the restricted use of six designated phthalates: DBP, BBP, DEHP, DNOP, DIDP, and DINP. SPEX CertiPrep is proud to offer the first Certified Reference Materials for phthalates in polyvinyl chloride produced under the guidelines of ISO 9001:2015, ISO/IEC 17025:2017 and ISO 17034:2016. Designed for Methods: • US Methods CPSC-CH-C1001-09.3 • ASTM D7823-13 • EU -
WO 2017/004282 Al 5 January 2017 (05.01.2017) P O P C T
(12) INTERNATIONAL APPLICATION PUBLISHED UNDER THE PATENT COOPERATION TREATY (PCT) (19) World Intellectual Property Organization International Bureau (10) International Publication Number (43) International Publication Date WO 2017/004282 Al 5 January 2017 (05.01.2017) P O P C T (51) International Patent Classification: (81) Designated States (unless otherwise indicated, for every A61K 8/35 (2006.01) A61K 8/37 (2006.01) kind of national protection available): AE, AG, AL, AM, AO, AT, AU, AZ, BA, BB, BG, BH, BN, BR, BW, BY, (21) International Application Number: BZ, CA, CH, CL, CN, CO, CR, CU, CZ, DE, DK, DM, PCT/US20 16/040224 DO, DZ, EC, EE, EG, ES, FI, GB, GD, GE, GH, GM, GT, (22) International Filing Date: HN, HR, HU, ID, IL, IN, IR, IS, JP, KE, KG, KN, KP, KR, 29 June 2016 (29.06.2016) KZ, LA, LC, LK, LR, LS, LU, LY, MA, MD, ME, MG, MK, MN, MW, MX, MY, MZ, NA, NG, NI, NO, NZ, OM, (25) Filing Language: English PA, PE, PG, PH, PL, PT, QA, RO, RS, RU, RW, SA, SC, (26) Publication Language: English SD, SE, SG, SK, SL, SM, ST, SV, SY, TH, TJ, TM, TN, TR, TT, TZ, UA, UG, US, UZ, VC, VN, ZA, ZM, ZW. (30) Priority Data: 62/186,240 29 June 2015 (29.06.2015) US (84) Designated States (unless otherwise indicated, for every kind of regional protection available): ARIPO (BW, GH, (71) Applicant: TAKASAGO INTERNATION CORPORA¬ GM, KE, LR, LS, MW, MZ, NA, RW, SD, SL, ST, SZ, TION (USA) [US/US]; 4 Volvo Drive, Rockleigh, NJ TZ, UG, ZM, ZW), Eurasian (AM, AZ, BY, KG, KZ, RU, 07647 (US). -
HEALTHY ENVIRONMENTS a Compilation of Substances Linked to Asthma
HEALTHY ENVIRONMENTS A Compilation of Substances Linked to Asthma Prepared by Perkins+Will for the National Institutes of Health, Division of Environmental Protection, as part of a larger effort to promote health in the built environment. July 2011 PURPOSE STATEMENT This report was prepared by Perkins+Will on behalf of the National Institutes of Health, Office of Research Facilities, Division of Environmental Protection, as part of a larger effort to promote health in the built environment. Our research team noted that based on extensive experience, there is a need for more research on the impact that materials and conditions in the built environment have on occupant health. Additionally, existing research data has not been compiled and made available in a form that is readily usable by building professionals for integrating health protective features in the design and construction of buildings. Toward meeting these needs our research team set out to compile data on substances in the built environment that may cause or aggravate asthma, a disease of high and increasing prevalence and major economic importance. This list should be a valuable resource for identifying asthma triggers and asthmagens, minimizing their use in building materials and furnishings, and contributing to our larger goals of fostering healthier built environments. HEALTHY ENVIRONMENTS CONTENTS 02 Purpose Statement 04 Executive Summary 05 Defining Asthma 06 Asthma in the Global Context 07 Cost of Asthma 08 Framing the Issue 10 Asthma Triggers and Asthmagens 10 Development -
CAS 84-69-5 Diisobutyl Phthalate (DIBP)
CAS 84-69-5 Diisobutyl phthalate (DIBP) Toxicity The European Union classified DIBP as a reproductive Substance of Very High Concern (SVHC).1 A 2011 study observed decreased testicular testosterone in male rats fed DIBP for 4 days.2 Borch et al. 2006 found male offspring of female rats exposed to DIBP from gestation day 7 to gestation day 20 or 21 had significantly reduced anogenital distance.3 The Chronic Hazard Advisory Panel (CHAP) determined, due to toxicological profile similarities to Dibutyl phthalate (DBP), exposure to DIBP contributes to a cumulative antiandrogenic effect with other phthalates and should be permanently banned in children’s toys and child care articles at levels greater than 0.1 percent.4 In 2017 the CPSC permanently banned DIBP in children’s toys and childcare articles at levels greater than 0.1 percent.5 Exposure The 2015 National Health and Nutrition Examination Survey (NHANES) monitored a metabolite of DIBP in human urine, and the levels appear to be increasing.6 Metabolites of DIBP were detected in the urine of pregnant Danish women in a 2010-2012 study.7 A significant correlation was found between DIBP metabolite concentrations in the urine of Danish children and increased levels of DIBP in bedroom dust and day care centers.8 Other DIBP is used as a substitute ingredient to di-n-butyl phthalate (DBP) due to structural similarities, therefore, its’ presence in products may increase.3 References 1. European Commission, Endocrine disruptor priority list. Retrieved from: http://ec.europa.eu/environment/chemicals/endocrine/strategy/substances_en.htm 2. Hannas, B.R., Lambright, C.S., Furr, J., Howdeshell, K.L., Wilson, V.S., Gray, L.E., Jr. -
Chemical Resistance of Plastics
(c) Bürkle GmbH 2010 Important Important information The tables “Chemical resistance of plastics”, “Plastics and their properties” and “Viscosity of liquids" as well as the information about chemical resistance given in the particular product descriptions have been drawn up based on information provided by various raw material manufacturers. These values are based solely on laboratory tests with raw materials. Plastic components produced from these raw materials are frequently subject to influences that cannot be recognized in laboratory tests (temperature, pressure, material stress, effects of chemicals, construction features, etc.). For this reason the values given are only to be regarded as being guidelines. In critical cases it is essential that a test is carried out first. No legal claims can be derived from this information; nor do we accept any liability for it. A knowledge of the chemical and mechanical Copyright This table has been published and updated by Bürkle GmbH, D-79415 Bad Bellingen as a work of reference. This Copyright clause must not be removed. The table may be freely passed on and copied, provided that Extensions, additions and translations If your own experiences with materials and media could be used to extend this table then we would be pleased to receive any additional information. Please send an E-Mail to [email protected]. We would also like to receive translations into other languages. Please visit our website at http://www.buerkle.de from time to Thanks Our special thanks to Franz Kass ([email protected]), who has completed and extended these lists with great enthusiasm and his excellent specialist knowledge. -
Appendix B Reproductive and Other Toxicology
Report to the U.S. Consumer Product Safety Commission by the CHRONIC HAZARD ADVISORY PANEL ON PHTHALATES AND PHTHALATE ALTERNATIVES July 2014 APPENDIX B REPRODUCTIVE AND OTHER TOXICOLOGY TABLE OF CONTENTS 1 Introduction ............................................................................................................................. 1 1.1 Nonreproductive Toxicity ................................................................................................ 2 2 Permanently Banned Phthalates .............................................................................................. 3 2.1 Di-n-Butyl Phthalate (DBP) ............................................................................................. 3 2.1.1 Human Data .............................................................................................................. 3 2.1.2 Animal Data .............................................................................................................. 4 2.1.3 Studies Reported Since the NTP-CERHR Report in 2000 ....................................... 4 2.2 Butylbenzyl Phthalate (BBP) ........................................................................................... 6 2.2.1 Human Data .............................................................................................................. 6 2.2.2 Animal Data .............................................................................................................. 6 2.2.3 Studies Reported Since the NTP-CERHR Report in 2003 ...................................... -
Chronic Hazard Advisory Panel on Phthalates and Phthalate Alternatives
Report to the U.S. Consumer Product Safety Commission by the CHRONIC HAZARD ADVISORY PANEL ON PHTHALATES AND PHTHALATE ALTERNATIVES July 2014 U.S. Consumer Product Safety Commission Directorate for Health Sciences Bethesda, MD 20814 Chronic Hazard Advisory Panel on Phthalates and Phthalate Alternatives Chris Gennings, Ph.D. Virginia Commonwealth University Richmond, VA Russ Hauser, M.D., Sc.D., M.P.H. Harvard School of Public Health Boston, MA Holger M. Koch, Ph.D. Ruhr University Bochum, Germany Andreas Kortenkamp, Ph.D. Brunel University London, United Kingdom Paul J. Lioy, Ph.D. Robert Wood Johnson Medical School Piscataway, NJ Philip E. Mirkes, Ph.D. University of Washington (retired) Seattle, WA Bernard A. Schwetz, D.V.M., Ph.D. Department of Health and Human Services (retired) Washington, DC TABLE OF CONTENTS LIST OF TABLES ....................................................................................................................... iv LIST OF FIGURES ..................................................................................................................... vi ABBREVIATIONS ..................................................................................................................... vii 1 Executive Summary .............................................................................................................. 1 2 Background and Strategy................................................................................................... 11 2.1 Introduction and Strategy Definition ........................................................................... -
(12) Patent Application Publication (10) Pub. No.: US 2017/0145187 A1 PFEIFFER Et Al
US 20170145187A1 (19) United States (12) Patent Application Publication (10) Pub. No.: US 2017/0145187 A1 PFEIFFER et al. (43) Pub. Date: May 25, 2017 (54) PLASTICZER COMPOSITION WHCH (30) Foreign Application Priority Data CONTAINS ALPHATC DCARBOXYLC ACD ESTERS UND TEREPHTHALIC ACID Jul. 8, 2014 (EP) .................................. 141761445 DALKYL ESTERS Jan. 30, 2015 (EP) .................................. 15153263.7 (71) Applicant: BASF SE, Ludwigshafen (DE) Publication Classification (72) Inventors: Matthias PFEIFFER, Böhl-lggelheim (51) Int. Cl. (DE); Boris BREITSCHEIDEL, CSK 5/12 (2006.01) Waldsee (DE); Axel GRIMM, CSK 5/II (2006.01) Edenkoben (DE); Herbert (52) U.S. Cl. MORGENSTERN, Ellerstadt (DE) CPC. C08K 5/12 (2013.01); C08K 5/II (2013.01) (21) Appl. No.: 15/323,584 (57) ABSTRACT The invention relates to a plasticizer composition containing (22) PCT Fed: Jul. 7, 2015 at least one aliphatic dicarboxylic acid ester and at least one terephthalic acid dialkyl ester, to molding compounds con (86) PCT No.: PCT/EP2O15/065421 taining a thermoplastic polymer or an elastomer and a S 371 (c)(1), plasticizer composition of said type, and to the use of said (2) Date: Jan. 3, 2017 plasticizer compositions and molding compounds. Patent Application Publication May 25, 2017. Sheet 1 of 7 US 2017/O145187 A1 Fig. : s 3. 3: g i. : & is a “n. S. 3 : 3 & 8 :8 ... 3 s s 8 i. sS.sŠs&35. s s S s s 8 is esses Patent Application Publication May 25, 2017. Sheet 2 of 7 US 2017/O145187 A1 Patent Application Publication May 25, 2017. Sheet 3 of 7 US 2017/O145187 A1 &v % SSo Patent Application Publication May 25, 2017. -
Plasticizers
157 PLASTICIZERS ALLEN D. GODWIN Exxon Chemical Company, Basic Chemicals and Intermediates Technology, 5200 Bayway Drive, Baytown Texas 77586 Introduction Mechanism of Plasticization Types of Plasticizers Plasticizer Characteristics and Performance of Flexible PVC Plasticizer Selection for Specific Applications Plasticizers for Other Polymers Health Aspects of Plasticizers Future of Plasticizers Introduction A plasticizer is a material that when added to another substance, makes that material softer or more flexible. Although this definition can include many products, from water added to clay for production of pottery to lime mixed with concrete to make it more workable, the word "plasticizer" generally refers to materials used in plastics. The Council of the International Union of Pure and Applied Chemistry (lUPAC) adopted the following definition of a plasticizer: A plasticizer is a substance or material incorporated in a materia! (usually a plastic or elastomer) to increase its flexibility, workability, or distensibility. In addition, a plasticizer may reduce the melt viscosity, lower the temperature of a second-order transition, or lower the elastic modulus of the product. Early plasticizer technology and development focused on nitrocellulose. One of the first commercially important plasticized products was Celluloid, which was cellulose nitrate plasticized with camphor. John Wesley Hyatt patented this technology in 1870 (1). Later developments included the use of triphenyl phosphate as a low flammability plasticizer for cellulose nitrate. In the 1920's, the increasing demand for plasticized nitrocellulose paints lead to the development of two more important plasticizers, tricresyl phosphate and dibutyl phthalate. Although polyvinyl chloride (PVC) was first produced in the middle of the nineteenth century, it was Waldo Semen's vision of the usefulness of plasticized PVC that initiated the growth of the flexible PVC industry. -
Plastisol Compositions
Europaisches Patentamt European Patent Office © Publication number: 0 539 031 A1 Office europeen des brevets EUROPEAN PATENT APPLICATION © Application number: 92308781.1781.1 © int. Ci.5; C08L 33/10, C08K 5/00 @ Date of filing: 25.09.92 ® Priority: 24.10.91 GB 9122594 © Applicant: IMPERIAL CHEMICAL INDUSTRIES PLC @ Date of publication of application: Imperial Chemical House, Millbank 28.04.93 Bulletin 93/17 London SW1P 3JF(GB) © Designated Contracting States: @ Inventor: Overend, Andrew Stuart AT BE CH DE DK ES FR GB GR IT LI LU NL PT 39 Talbot Road, Dunham-On-The-Hill SE Warrington, Cheshire WA6 OJW(GB) Inventor: Padget, John Christopher 21 Fieldway Frodsham, Cheshire WA6 6RO(GB) © Representative: Shelter, Alan et al ICI Group Patents Services Dept. PO Box 6 Shire Park Bessemer Road Welwyn Garden City, Herts, AL7 1HD (GB) © Plastisol compositions. © Acrylic polymer plastisol composition, wherein the acrylic polymer component of the plastisol composition is a single-stage methyl methacrylate copolymer derived from methyl methacrylate and a comonomer component comprising isobutyl methacrylate and optionally other comonomer(s). CO Rank Xerox (UK) Business Services (3. 10/3.5x/3.0. 1) EP 0 539 031 A1 The present invention relates to an acrylic polymer plastisol composition. Plastisols are well known in the art. They are understood to be nonaqueous fluid compositions ranging in viscosity from pourable liquids to heavy pastes which contain a particulate polymer (polyvinyl chloride being historically the most important example) dispersed in a nonvolatile liquid organic plasticiser material 5 which is compatible with the polymer. Under ordinary conditions of storage (ambient temperatures) the polymer does not dissolve to any extent in the plasticiser but on heating the plastisol composition at an appropriate elevated temperature, after forming the plastisol into a desired shape (e.g. -
(12) United States Patent (10) Patent No.: US 7413,813 B2 Gosse Et Al
USOO7413813B2 (12) United States Patent (10) Patent No.: US 7413,813 B2 Gosse et al. (45) Date of Patent: Aug. 19, 2008 (54) PLASTICISED POLYVINYL CHLORIDE 2,489,103 A 1 1/1949 Morris et al. 2,535,643 A 12, 1950 Mack (75) Inventors: Claudius Gosse, Brussels (BE); Thomas 2,759,836 A 8, 1956 Caldwell Marshall Larson, Bellaire, TX (US); 2,794,811 A 6, 1957 Winstrom Pierre Jean Paul Legrand, Brussels 2,828,335 A 3/1958 Ferstandig et al. 2,848,412 A 8/1958 Easley (BE); Raphael Frans Caers, Edegem 2.888.484 A 5/1959 Dehmet al. (BE); Paul H. Daniels, League City, TX 3027.398 A 3/1962 Foohey (US); Allen D. Godwin, Seabrook, TX 3.085.078 A 4, 1963 Fath (US); Didier Naert, Brussels (BE) 3,135,740 A 6/1964 Brannocket al. 3,152,096 A 10/1964 Darby (73) Assignee: ExxonMobil Chemical Patents Inc., 3,169,975 A 2, 1965 Schulz Houston, TX (US) 3.224,994. A 12/1965 Lundberg et al. 3,251,771 A 5, 1966 Benoit (*) Notice: Subject to any disclaimer, the term of this 3,296,180 A 1/1967 Raether patent is extended or adjusted under 35 3,308,086 A 3, 1967 Wartman U.S.C. 154(b) by 0 days. 3,326,972 A 6/1967 Schenk et al. 3,334,149 A 8, 1967 Marlet al. (21) Appl. No.: 11/846,879 3,403,170 A 9, 1968 Corson et al. 3,428,668 A 2, 1969 Huelsmann et al.