III-I1 a July 5, 1955 W
Total Page:16
File Type:pdf, Size:1020Kb
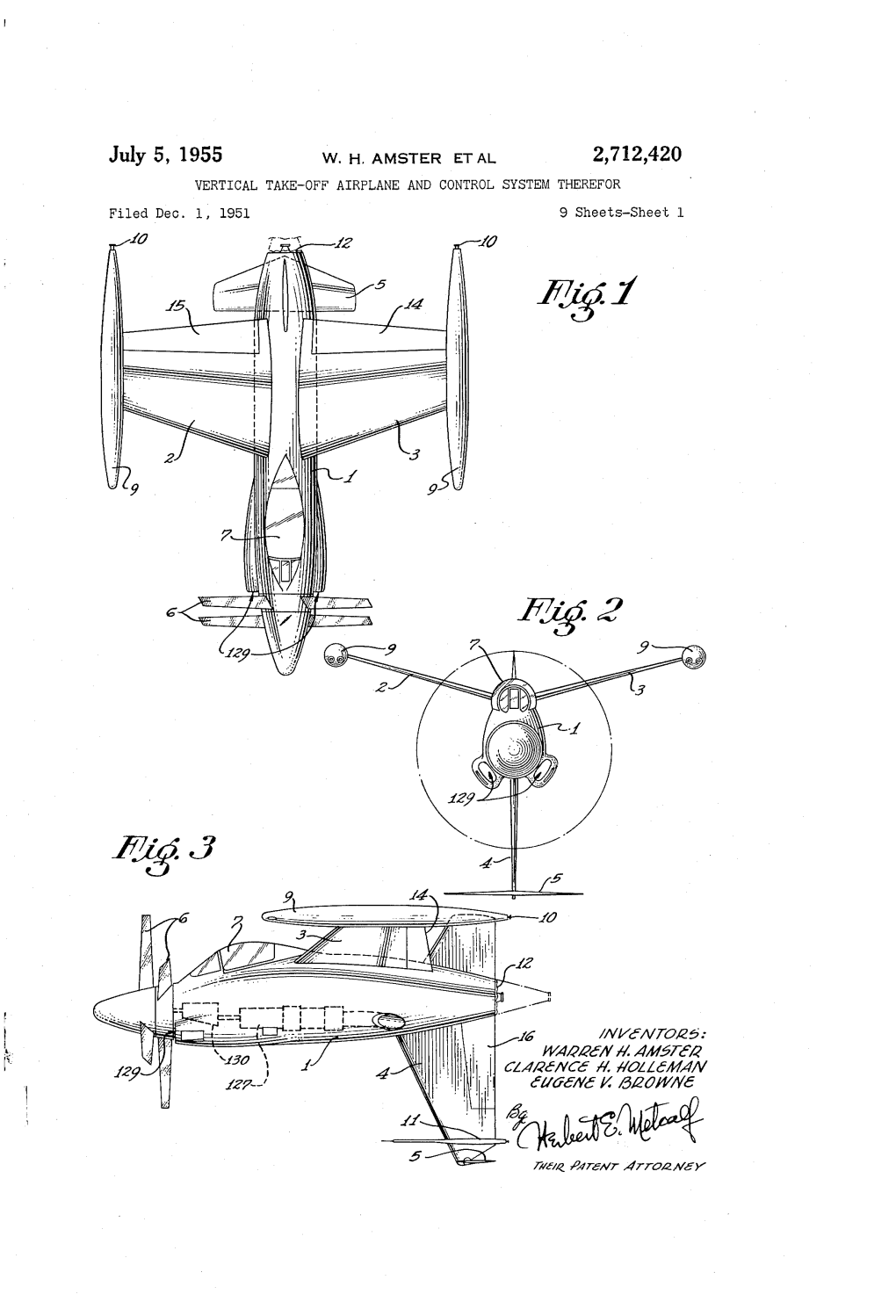
Load more
Recommended publications
-
A “Short Course” on Ice and the TBM
A “Short Course” on Ice and the TBM. Icing is topical at the present time as a result of a recent accident in a TBM. I have had a number of conversations with pilots who I would consider knowledgeable and it is apparent that there is a lot of confusion surrounding this subject. Also noting on line posts this confusion is not limited to owner pilots. I have had occasion to be a victim of my own stupidity in a serious icing condition years ago and I can vouch that icing is a deadly serious situation in more ways than one. Before going on with the subject we want to stipulate that the data we are about to provide is a summary of information that is to be found on line, along with narrative and data provided from knowledgeable instructors, if any of the data provided conflicts with anything you have been taught we urge you to satisfy yourself as to which data is correct. TBM operators fly in the same airspace where we find Part 25 aircraft (Commercial Category) aircraft. There is a big difference in how these two categories of aircraft are affected by icing conditions. A 767 will often be climbing at over 300 kts and 4000+ ft/min at typical icing altitudes. This creates two very distinct advantages for the 767: first, their icing exposure time may be less than 1/3 of ours. Second, icing conditions are a function of TAT (Total Air Temperature), not SAT (static air temp). TAT is warmer than SAT because of the effects of compressibility as the airplane operates at faster and faster speeds. -
Cessna Owner Magazine Article, October 2017
The following article appeared in the October 2017 edition of CESSNA OWNER magazine, the official publication of the Cessna Owner Organization. Whether for business or pleasure, the Official Publication of the Cessna Owner Organization Since 1975 Cessna Owner Organization is dedicated to assisting CESSNA>> October 2017 aircraft owners in OWNER MAGAZINE their continual pursuit to become better, TKS smarter and safer ROTECTION owners and pilots. ICE P Since 1975, the Liquid Armor for the collective knowledge War on Icing and experience of its members has saved owners countless hours of downtime and thousands of dollars in operational expenses. www.cessnaowner.org www.facebook.com/ CessnaOwnerOrganization Est. 1975 Not a member? Learn more at www.CessnaOwner.org TKS Ice Protection Liquid Armor for the War on Icing By Scott Sherer here are many people out accumulation before launching. I wind is strong and the wind chill there who really like snow also have a heavy-duty tug for get- is very low. The winter cloud in Tsports; things like skiing, ting my bird in and out of the han- Wisconsin is dark and grey. (I say snowboarding, ice skating, hockey, gar quickly, and the Janitrol fur- “cloud” and not “clouds” because we snowmobiling and all of those other nace, along with an assortment of seem to have only one cloud here sports that you typically see during other engine and interior warming and it covers the entire state from the winter Olympics. I’m sure that contraptions, helps to get my plane November well into January!) many aviators enjoy some of these warm and ready fast. -
Leading the Charge We Put TBM 940 Speedster Through Its Paces for NBAA
15-21 October 2019 I flightglobal.com FLIGHT TEST Leading the charge We put TBM 940 speedster through its paces for NBAA £3.90 Wow, how? ACES high 42 Questions remain over defunct US Air Force boosts Collins Icelandic carrier’s comeback 13 with ejection seat deal 20 9 770015 371310 FLIGHT TEST Power of one Turboprop-single family has been a market success since launch in 1988, amassing sales of more than 900 units across three variants Daher has delivered a compelling offer for owner-flyers, with a range of enhancements on the TBM 940 providing an edge over the piston-twin segment. We put it through its paces MICHAEL GERZANICS POMPANO BEACH have allowed single-engined designs to make to be efficient. Airspace congestion, however, inroads into the twin-turbine segment. can make reaching optimum altitudes for jets he single-engined turboprop market The growth of the single-engined turbo- problematic, so their real-world range can be is populated by numerous aircraft of prop segment is based on the near-bulletproof shorter. Jets also have higher direct operating varying configurations. In broad reliability and scalability of the PT6 family. costs, however. T strokes, it can be broken down into This paradigm shift from piston-twins to tur- Runway performance and training require- two segments: fast, low-winged aircraft and bine-singles is conceptually on par with ex- ments are also two factors that fuel the single- slower, more spacious high-winged designs. tended twin-engine operations authorisations engined turboprop segment, because runway In the West, these diverse offerings share a all but killing off three- and four-engined civil length for turboprops is shorter than that single critical component – their engine. -
LORD Flight Control Equipment
LORD Flight Control Equipment ELECTROMECHANICAL SOLUTIONS LORD provides customers innovative offerings globally with best-in-class cockpit controls • Inceptors to convert pilot inputs into flight control system commands • Force feedback optimized for pilot effectiveness • Electromechanical actuators for deployment of doors, landing gear, vents and control surfaces • Worldwide distribution, repair and overhaul network with AOG stock, servicing OEMs and end users Typical Applications: Benefits: • Cockpit Controls/ • Enable safer flights Inceptors Flight Controls for Business and Commercial Aircraft • Reduce pilot workload • Actuators • Reduce aircraft weight • Sensors • Optimize drag of wings • Dampers Side Stick • Enhance pilot comfort Throttle Control Flaps and Spoiler Levers Electric Pedals Actuator Systems for Aircraft and Helicopters • Door Systems • Flight Control Systems • Force Feel Systems • Locking Systems Our extensive experience in commercial fixed wing flight control systems and our innovative active vibration control systems in helicopters combine to make us a great partner for providing advanced flight control interfaces for aerospace applications. Cockpit Control Solutions LORD inceptors provide functional and ergonomic interfaces between pilots and various aircraft systems. Our Cockpit Control solutions are compact and lightweight and can be seamlessly integrated into cockpit designs. LORD flight control inceptors can be tailored to sidestick or yoke based cockpit layouts. Pilot Interface with: Modular Inceptor Components: • Flight Control Systems • Force Feel Dampers • Engine Control Systems • RVDT Transducer Units • Landing Gear Systems • Force Transducer Units Integrated Inceptors: • Auto Throttle Control Unit • Speed Brake Control Unit • Flap and Slat Control Unit • Nose Wheel Steering Hand Wheel • Side Stick (or Yoke) • Rudder and Brake Pedals Electromechanical Actuators Current aircraft primarily use hydraulic actuators to move surfaces and manage the landing gear operations. -
F-117A Accident During Air Show Flyover Caused by Omission of Fasteners in Wing-Support Structure
FLIGHT SAFETY FOUNDATION Aviation Mechanics Bulletin SEPTEMBER–OCTOBER 1998 F-117A Accident during Air Show Flyover Caused by Omission of Fasteners in Wing-support Structure FLIGHT SAFETY FOUNDATION Aviation Mechanics Bulletin Dedicated to the aviation mechanic whose knowledge, craftsmanship and integrity form the core of air safety. Robert A. Feeler, editorial coordinator September–October 1998 Vol. 46 No. 5 F-117A Accident during Air Show Flyover Caused by Omission of Fasteners in Wing-support Structure.......................................................... 1 Maintenance Alert ...................................................................................... 9 News & Tips ............................................................................................... 13 AVIATION MECHANICS BULLETIN Copyright © 1998 FLIGHT SAFETY FOUNDATION INC. ISSN 0005-2140 Suggestions and opinions expressed in FSF publications belong to the author(s) and are not necessarily endorsed by Flight Safety Foundation. Content is not intended to take the place of information in company policy handbooks and equipment manuals, or to supersede government regulations. Staff: Roger Rozelle, director of publications; Wayne Rosenkrans, senior editor; Mark Lacagnina, senior editor; John D. Green, copyeditor; Rick Darby, editorial consultant; Karen K. Ehrlich, production coordinator; Ann L. Mullikin, assistant production coordinator; and David Grzelecki, librarian, Jerry Lederer Aviation Safety Library. Subscriptions: US$35 (U.S.-Canada-Mexico), US$40 Air Mail (all other countries), six issues yearly. • Include old and new addresses when requesting address change. • Flight Safety Foundation, Suite 300, 601 Madison Street, Alexandria, VA 22314 U.S. • Telephone: (703) 739-6700 • Fax: (703) 739-6708 We Encourage Reprints Articles in this publication, in the interest of aviation safety, may be reprinted, in whole or in part, in all media, but may not be offered for sale or used commercially without the express written permission of Flight Safety Foundation’s director of publications. -
Evaluation of Two Unique Side Stick Controllers in a Fixed-Base Flight Simulator
NASA/TM-2003-212042 Evaluation of Two Unique Side Stick Controllers in a Fixed-Base Flight Simulator Jann Mayer and Timothy H. Cox NASA Dryden Flight Research Center Edwards, California December 2003 The NASA STI Program Office…in Profile Since its founding, NASA has been dedicated • CONFERENCE PUBLICATION. to the advancement of aeronautics and space Collected papers from scientific and science. The NASA Scientific and Technical technical conferences, symposia, seminars, Information (STI) Program Office plays a key or other meetings sponsored or cosponsored part in helping NASA maintain this by NASA. important role. • SPECIAL PUBLICATION. Scientific, The NASA STI Program Office is operated by technical, or historical information from Langley Research Center, the lead center for NASA programs, projects, and mission, NASA’s scientific and technical information. often concerned with subjects having The NASA STI Program Office provides access substantial public interest. to the NASA STI Database, the largest collection of aeronautical and space science STI in the • TECHNICAL TRANSLATION. English- world. The Program Office is also NASA’s language translations of foreign scientific institutional mechanism for disseminating the and technical material pertinent to results of its research and development activities. NASA’s mission. These results are published by NASA in the NASA STI Report Series, which includes the Specialized services that complement the STI following report types: Program Office’s diverse offerings include creating custom thesauri, building customized databases, organizing and publishing research • TECHNICAL PUBLICATION. Reports of results…even providing videos. completed research or a major significant phase of research that present the results of For more information about the NASA STI NASA programs and include extensive data Program Office, see the following: or theoretical analysis. -
Kc-10A, T/N 83-0080 9Th Air Refueling Squadron 60Th Air Mobility Wing Travis Air Force Base, California
UNITED STATES AIR FORCE AIRCRAFT ACCIDENT INVESTIGATION BOARD REPORT KC-10A, T/N 83-0080 9TH AIR REFUELING SQUADRON 60TH AIR MOBILITY WING TRAVIS AIR FORCE BASE, CALIFORNIA LOCATION: NEAR MOUNTAIN HOME AFB, IDAHO DATE OF ACCIDENT: 1 NOVEMBER 2016 BOARD PRESIDENT: COL PERRY M. LONG III Conducted IAW Air Force Instruction 51-503 ACTION OF THE CONVENING AUTHORITY 1 0 JUL 2117 The report of the accident investigation board, conducted under the provisions of AFI 51-503, that investigated the 1 November 2016 mishap that occurred near Mountain Home Air Force Base, Idaho, involving KC-10A, T/N 83-0080, assigned to the 60th Air Mobility Wing, Travis Air Force Base, California, complies with applicable regulatory and statutory guidance and on that basis is approved. \\signed\\ fHOMA^J; Major General, U| Vice Commander United States Air Force Accident Investigation Board Report Class A Mishap, Near Mountain Home AFB, ID EXECUTIVE SUMMARY UNITED STATES AIR FORCE AIRCRAFT ACCIDENT INVESTIGATION KC-10A, T/N 83-0080 NEAR MOUNTAIN HOME AFB, IDAHO 1 NOVEMBER 2016 On 1 November 2016, at 1546 hours Zulu time (Z), a United States Air Force KC-10A Extender, tail number 83-0080, the mishap aircraft, assigned to the 60th Air Mobility Wing, departed from its home station of Travis Air Force Base (AFB), California, on a training mission in support of two flights of F-15s and a C-17. The scheduled flight profile was a formation departure from Travis AFB, refueling for approximately one hour with the F-15s, refueling training for approximately 1 hour 15 minutes with the C-17, and approximately one half hour of approach training before landing at Travis AFB. -
Flight Deck Solutions, Technologies and Services Moving the Industry Forward Garmin Innovation Brings Full Integration to Business Flight Operations and Support
FLIGHT DECK SOLUTIONS, TECHNOLOGIES AND SERVICES MOVING THE INDUSTRY FORWARD GARMIN INNOVATION BRINGS FULL INTEGRATION TO BUSINESS FLIGHT OPERATIONS AND SUPPORT From web-based flight planning, fleet scheduling and tracking services to integrated flight display technology, head-up displays, advanced RNP navigation, onboard weather radar, Data Comm datalinks and much more — Garmin offers an unrivaled range of options to help make flying as smooth, safe, seamless and reliable as it can possibly be. Whether you operate a business jet, turboprop or hard-working helicopter, you can look to Garmin for industry-leading solutions scaled to fit your needs and your cockpit. The fact is, no other leading avionics manufacturer offers such breadth of capability — or such versatile configurability — in its lineup of flight deck solutions for aircraft manufacturers and aftermarket upgrades. When it comes to bringing out the best in your aircraft, Garmin innovation makes all the difference. CREATING A VIRTUAL REVOLUTION IN GLASS FLIGHT DECK SOLUTIONS By presenting key aircraft performance, navigation, weather, terrain routings and so on. The map function is designed to interface with a and traffic information, in context, on large high-resolution color variety of sensor inputs, so it’s easy to overlay weather, lightning, traffic, displays, today’s Garmin glass systems bring a whole new level of terrain, towers, powerlines and other avoidance system advisories, as clarity and simplicity to flight. The screens offer wide viewing angles, desired. These display inputs are selectable, allowing the pilot to add advanced backlighting and crystal-sharp readability, even in bright or deselect overlays to “build at will” the map view he or she prefers for sunlight. -
Hondajet Model HA-420
Honda Aircraft Company PILOT’S OPERATING MANUAL HondaJet Model HA-420 Original Issue: December 10, 2015 Revision B2: March 3, 2017 This Pilot’s Operating Manual is supplemental to the current FAA Approved Airplane Flight Manual, HJ1-29000-003-001. If any inconsistencies exist between this Pilot’s Operating Manual and the FAA Approved Airplane Flight Manual, the FAA Approved Airplane Flight Manual shall be the governing authority. These commodities, technology, or software were exported from the United States in accordance with the Export Administration Regulations. Diversion contrary to U.S. law is prohibited. P/N: HJ1-29000-005-001 Copyright © Honda Aircraft Company 2016 FOR TRAINING PURPOSES ONLY Honda Aircraft Company Copyright © Honda Aircraft Co., LLC 2016 All Rights Reserved. Published by Honda Aircraft Company 6430 Ballinger Road Greensboro, NC 27410 USA www.hondajet.com Copyright © Honda Aircraft Company 2016 FOR TRAINING PURPOSES ONLY Honda Aircraft Company LIST OF EFFECTIVE PAGES This list contains all current pages with effective revision date. Use this list to maintain the most current version of the manual: Insert the latest revised pages. Then destroy superseded or deleted pages. Note: A vertical revision bar in the left margin of the page indicates pages that have been added, revised or deleted. MODEL HA-420 PILOT’S OPERATING MANUAL Title Page ...................................................................... March 3, 2017 Copyright Page ............................................................. March 3, 2017 List of Effective Pages .................................................. March 3, 2017 Record of Revisions ..................................................... March 3, 2017 Record of Temporary Revisions ................................... March 3, 2017 List of Service Bulletins ............................................... March 3, 2017 Documentation Group .................................................. March 3, 2017 SECTION 1 – SYSTEMS DESCRIPTION Pages 1 – 232 .......................................................... -
The Gulfstream IV Operator Had All the Appearance of a Good Operation But
SAFETY REPORT The Gulfstream IV operator had all the appearance of a good operation but the flightcrew lacked cockpit discipline NTSB finds widespread non-compliance with checklist use and control checks, leading to this tragic BED runway overrun crash. Paved overrun Source: Massachusetts State Police Main wreckage Flightcrew failure to review the checklist and release the gust lock prior to the takeoff run of Gulfstream IV N121JM on BED’s 7000-ft Rwy 11 as well as failure to be time-sensitive and abort the takeoff before running out of runway length led to destruction of the aircraft and the deaths of all occupants aboard. By Robert Sumwalt Gulfstream IV N121JM was frequently used for air transportation both NTSB Board Member domestically and overseas by Lewis Katz, the well-known and highly ATP/CFII/FE. Airbus A320, King Air 350, Boeing respected publisher of The Philadelphia Inquirer newspaper. 737, Fokker F28, Fokker 100 s often is the case in corporate aviation, the pas- at 1325 edt for the short hop to ACY, where they picked up sengers were running a few hours late. The 2 pi- the 4 passengers and flew them to BED (Hanscom Field, Alots and flight attendant decided to pass the time Bedford MA). After the passengers attended a charity event, by ordering a pizza and eating in the comfort of the cabin the plan was to return them to ACY and then reposition the of N121JM, the Gulfstream IV they had operated for 7 Gulfstream back to its home base at ILG. years. When the billionaire principal showed up with 3 Tragically, the evening didn’t end that way. -
Approaches to Assure Safety in Fly-By-Wire Systems: Airbus Vs
APPROACHES TO ASSURE SAFETY IN FLY-BY-WIRE SYSTEMS: AIRBUS VS. BOEING Andrew J. Kornecki, Kimberley Hall Embry Riddle Aeronautical University Daytona Beach, FL USA <[email protected]> ABSTRACT The aircraft manufacturers examined for this paper are Fly-by-wire (FBW) is a flight control system using Airbus Industries and The Boeing Company. The entire computers and relatively light electrical wires to replace Airbus production line starting with A320 and the Boeing conventional direct mechanical linkage between a pilot’s 777 utilize fly-by-wire technology. cockpit controls and moving surfaces. FBW systems have been in use in guided missiles and subsequently in The first section of the paper presents an overview of military aircraft. The delay in commercial aircraft FBW technology highlighting the issues associated with implementation was due to the time required to develop its use. The second and third sections address the appropriate failure survival technologies providing an approaches used by Airbus and Boeing, respectively. In adequate level of safety, reliability and availability. each section, the nature of the FBW implementation and Software generation contributes significantly to the total the human-computer interaction issues that result from engineering development cost of the high integrity digital these implementations for specific aircraft are addressed. FBW systems. Issues related to software and redundancy Specific examples of software-related safety features, techniques are discussed. The leading commercial aircraft such as flight envelope limits, are discussed. The final manufacturers, such as Airbus and Boeing, exploit FBW section compares the approaches and general conclusions controls in their civil airliners. The paper presents their regarding the use of FBW technology. -
FLIGHT MULTI PANEL Professional Autopilot Cockpit Simulation Controller Contrôleur De Pilotage Automatique Pro Pour Simulateur De Cockpit
FLIGHT MULTI PANEL Professional Autopilot Cockpit Simulation Controller Contrôleur de pilotage automatique pro pour simulateur de cockpit USER GUIDE | GUIDE DE L’UTILISATEUR logitechG.com 3 ENGLISH 8 FRANÇAIS 13 ESPAÑOL 18 PORTUGUÊS 3 INTRODUCTION The Multi Panel interacts with Microsoft Flight Simulator X to control a range of functions, including auto pilot settings, flaps and trim controls. SETTINGS ADJUSTMENT WHEEL AUTO THROTTLE ARM AUTOPILOT SETTINGS SELECTOR PITCH TRIM ROTARY CONTROL AUTOPILOT FUNCTIONS FLAPS RETRACT (UP) BUTTONS OR EXTEND (DOWN) 4 English INSTALLATION Fix the Multi Panel to the supplied mounting bracket. Insert the screws through the holes at the corners of the Panel into the bracket behind and tighten. If you already own a Logitech G Flight Yoke System, you can mount the Panel and bracket on top of the Yoke unit using the screws provided. 1 2 3 INSTALLATION FOR WINDOWS® 10, WINDOWS® 8.1 AND WINDOWS® 7 DRIVER INSTALLATION 1 Visit logitech.com/support/multi-panel to download the latest drivers and software for your operating system. 2 With device disconnected, follow the onscreen instructions to complete the installation. 3 At the Driver Setup screen, only when prompted, insert USB cable into one of your computer’s USB ports, then click Next. 5 English USING THE LOGITECH G FLIGHT MULTI PANEL Button Autopilot function AP Master switch to engage or disengage the autopilot HDG Plane will fly to selected compass heading NAV Plane will fly to selected NAV1 frequency or GPS IAS Plane will fly at selected indicated airspeed ALT Plane will fly to and maintain selected altitude VS Plane will climb or descend at selected vertical speed APR Plane will fly on approach to runway localizer REV Plane will fly on a back course from the localizer ADJUSTING AUTOPILOT SETTINGS To change the values of the autopilot settings, first turn the selector switch on the left side of the Multi Panel to the function you want to adjust.