Fire Door Systems, a Guide to Code Compliance (2018 Edition)
Total Page:16
File Type:pdf, Size:1020Kb
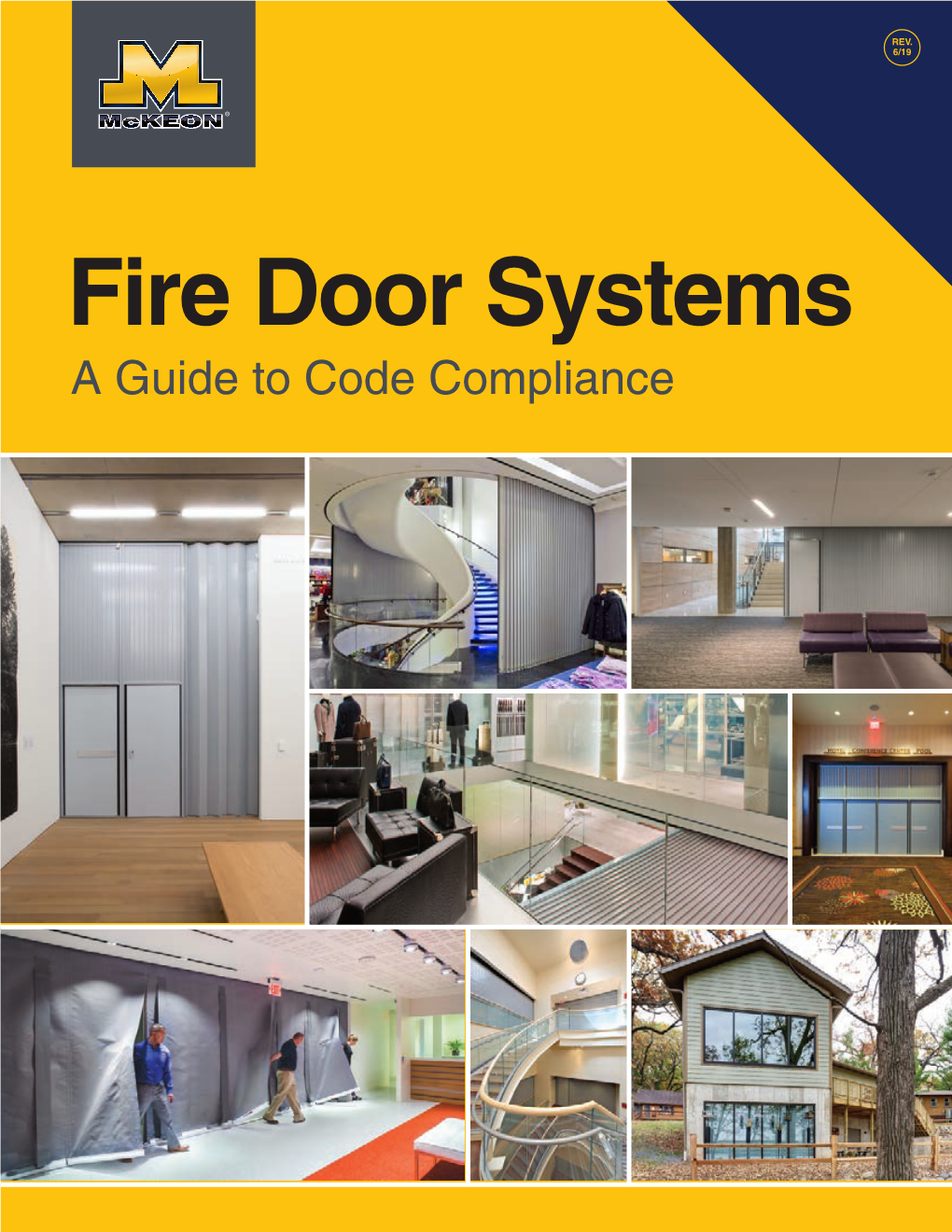
Load more
Recommended publications
-
Decoded FIRE DOOR ASSEMBLY CLASSIFICATIONS
Decoded FIRE DOOR ASSEMBLY CLASSIFICATIONS By Lori Greene, DAHC/CDC, FDAI, FDHI, CCPR 62 OCTOBER 2017 DOORS + HARDWARE In fire walls between buildings or in walls which divide a building into different fire areas, opening protectives typically require a three-hour rating. Some codes may call for walls with a four-hour rating, although this is not very common in the U.S. NFPA 80 – Standard for Fire Doors and Other Opening rating are also classified as B-label doors, and are used Protectives, classifies openings protected by fire door in some interior exit stairway and ramp enclosures. assemblies in one of five categories. The rating may For example, for most applications, the 2015 edition of be expressed in hours or minutes, as an alphabetical the International Building Code (IBC) requires a two- designation, or a combination of the two. While using hour wall (and 90-minute fire doors) when the stair is a letter designation is still fairly common, it’s best to connecting four stories or more, and a one-hour wall include the hourly rating, particularly when specify- (and 60-minute fire doors) when the stair is con- ing or supplying a B-label door which may have either necting less than four stories. The number of stories a 60-minute or 90-minute rating. includes basement levels but not mezzanines. Information about NFPA 80’s classifications for fire door assemblies is found in Annex D of the standard. Class C — Walls or partitions between rooms As with the other annexes, Annex D is included for and corridors having a fire resistance rating of informational purposes and is not part of the NFPA one hour or less 80 requirements, but it’s helpful to understand the In a one-hour wall surrounding a hazardous area, purpose of each type of assembly when specifying ¾-hour fire door assemblies may be required. -
Dallas Fire Code,” of the Dallas City Code, As Amended; Adopting with Certain Changes the 2015 Edition of the International Fire Code of the International
161124 6-22- 16 ORDNANCE NO. 301 3 5 An ordinance amending Chapter 16, “Dallas Fire Code,” of the Dallas City Code, as amended; adopting with certain changes the 2015 Edition of the International Fire Code of the International Code Council, Inc.; regulating and governing the safeguarding of life and property from fire and explosion hazards arising from the storage, handling, and use of hazardous substances, materials, and devices, and from conditions hazardous to life or property in the occupancy of buildings and premises, and providing for the issuance of permits for hazardous uses or operations; providing a penalty not to exceed $2,000; providing a saving clause; providing a severability clause; and providing an effective date. BE IT ORDAINED BY THE CiTY COUNCIL OF THE CITY OF DALLAS: SECTION 1. That Chapter 16, “Dallas Fire Code,” of the Dallas City Code, as amended, is amended by adopting the 2015 Edition of the International Fire Code of the International Code Council, Inc. (which is attached as Exhibit A and made a part of this ordinance), with the following amendments: 1. Pages xxi-xxii, “Legislation,” are deleted. 2. Subsection 101.1, “Title,” of Section 101, “Scope and General Requirements,” of Part 1, “General Provisions,” of Chapter 1, “Scope and Administration,” of the 2015 International Fire Code is amended to read as follows: “101.1 Title. These regulations shall be known as the Dallas Fire Code [of [NAME OF JURISDICTION]], hereinafter referred to as ‘this code.” Amend Chapter 16 (adopt 2015 International Fire Code) — Page 1 30135 161124 3. Section 101, “Scope and General Requirements,” of Part 1, “General Provisions,” of Chapter 1, “Scope and Administration,” of the 2015 International Fire Code is amended by adding a new Subsection 101.6, “Exceptions,” to read as follows: “101.6 Exceptions. -
Floor Fire Door Pleased to Offer a Series of Technical Bulletins De- Flush-Mounted Floor Doors Are Widely Used in Buildings for Access Between Floors
BILCO TECHNICAL BULLETIN The Bilco Company, a Performance Criteria for a world leader in the design and manufacture of spe- cialty access products, is Floor Fire Door pleased to offer a series of technical bulletins de- Flush-mounted floor doors are widely used in buildings for access between floors. signed to address issues As fire protection standards become more stringent, code officials and specifiers related to access prod- have identified the need for a floor door with a fire rating that matches the floor- ucts within the construc- ceiling assembly. This bulletin examines the product performance criteria for this tion industry. demanding application. Vertical fire doors are Penetrations in floor-ceil- common place in modern ing assemblies must perform building construction. De- (in a fire protection sense) as signed for fire protection of well as the rated deck to en- Stairwell openings in wall systems, sure containment of the fire. or Elevator these doors are generally Since the door is flush Shaft tested in accordance with mounted in the floor, it is not ASTM E152 (NFPA 252) reasonable to assume that and are UL Listed. Essen- combustible items will not be tially, vertical fire doors located near or stored directly serve only to block the pas- on the door. Heat transmis- sage of flames between lat- sion becomes a critical issue. 1&1/2-Hr Vertical Fire Doors eral compartments or rooms For this reason, the floor fire 2-Hr Walls within the building. door must meet a signifi- 2-Hr Floor/Ceiling Assembly A questionable area ex- cantly higher performance ists in that if combustibles standard than its vertical ASTM E152 ASTM E119 (ie: furniture, drapery, sup- counterpart. -
2018 Connecticut State Fire Safety Code
DEPARTMENT OF ADMINISTRATIVE SERVICES 2018 Connecticut State Fire Safety Code DIVISION OF MELODY A. CURREY CONSTRUCTION SERVICES Commissioner Office of the State Fire Marshal 450 Columbus Boulevard WILLIAM ABBOTT Hartford, CT 06103 State Fire Marshal Effective Legislative SubmissionDraft Version ForOctober PublicApril 16, Comment1, 2018 2018 January 2018 This page is intentionally left blank CONNECTICUT STATE FIRE SAFETY CODE Part I—Administrative Sec. 100 Title and Applicability Sec. 100.1 The Connecticut State Fire Safety Code and the adopted standards, as amended, shall be known as the Connecticut State Fire Safety Code, hereinafter referred to as “the code” or “this code”. Sec. 100.2 If a section, subsection, sentence, clause or phrase of this code is, for any reason, held to be unconstitutional, such decision shall not affect the validity of the remaining portions of this code. Sec. 100.3 In the event any part or provision of this code is held to be illegal or void, this shall not have the effect of making void or illegal any of the other parts or provisions hereof, which are determined to be legal; and it shall be presumed that this code would have been adopted without such illegal or invalid parts or provisions. Sec. 100.4 Nothing in this code shall be construed to prohibit a better type of building construction, an additional means of egress, or an otherwise safer condition than that specified by the minimum requirements of this code. Sec. 100.5 The provisions of the code shall only apply to detached private dwellings occupied by one or two families and townhouses with respect to smoke alarms and carbon monoxide detectors as specified in the State Building Code and subject to the specific inspection criteria for smoke detection and warning equipment of section 29-305 of the Connecticut General Statutes. -
Technical Data Sheet No. 401 Basic Fire Door Requirements
BASIC FIRE DOOR REQUIREMENTS TECHNICAL DATA SHEET NO. 401 Fire door openings are classified by their locations in the building. The location determines the length of exposure protection required, based on the potential fire hazard of that particular area. The six opening classifications are shown below along with the six door ratings and the maximum amount of glass in square inches allowed for each door. Label Maximum Classification Location In Building Glass Area 3 3 hour rated opening (Class A). Openings are in walls separating 100 square inches HOUR buildings or dividing a single building into fire areas. Doors for these per leaf. RATING openings require a fire protection rating of 3 hours. See note 1. 1 1/2 hour rated opening (Class B). Openings are in enclosures of vertical communication through buildings. These could be stairwells 1-1/2 or elevator shafts. While not a means of vertical communication, 100 square inches per leaf. HOUR boiler room doors are generally categorized as Class “B” openings. See note 2. RATING Door for these areas require a fire protection rating of 1 1/2 hours, and glass areas may not exceed 100 square inches per individual door leaf except as noted below. 3/4 hour rated opening (Class C). Openings are in corridors and 1296 square inches 3/4 room partitions. Doors for these areas require a fire protection rating per light. Neither HOUR of 3/4 hour, and the glass area cannot exceed 1296 square inches dimension to exceed RATING per light with no dimension exceeding 54 inches except as noted 54”. -
Fire Door Assemblies for Lunch and Learn
Fire Rated Door Assemblies: Compliant Designs Steel Door Institute www.steeldoor.org AIA Provider #G389 Course #: SDIFIRE 1 HSW CE hour 1 Credit(s) earned on completion of This course is registered with AIA this course will be reported to AIA CES for continuing professional CES for AIA members. education. As such, it does not Certificates of Completion for both include content that may be AIA members and non-AIA deemed or construed to be an members are available upon approval or endorsement by the request. AIA of any material of construction or any method or manner of handling, using, distributing, or dealing in any material or product. ___________________________________________ Questions related to specific materials, methods, and services will be addressed at the conclusion of this presentation. 2 What is the Steel Door Institute (SDI)? • The Steel Door Institute has 11 members • Design professionals specify SDI manufacturers to ensure that their doors and frames meet the SDI standards they specify • Each member is actively involved in committees that develop codes, fire tests, and more • Standards are offered online at no charge • SDI serves as secretary to the Accredited Standards Committee (ASC) A250 3 Fire Door Assemblies • Fire-resistance-rated walls with a compartmentalize a building to deter the spread of smoke and flames • Opening protectives, also known as fire door assemblies protect openings in these walls Where are Fire Door Assemblies Required? • Building code specifies where fire door assemblies are required • Most US -
Fire, Life Safety and Accessibility Codes a Reference Guide for Swinging Doors and Hardware Table of Contents
Fire, life safety and accessibility codes A reference guide for swinging doors and hardware Table of contents 2 Sources for code information 3 How to use this resource 4 Classification of occupancy as described by NFPA 101® – Life Safety Code® 7 ICC International Building Code® (IBC) 11 National Building Code of Canada 13 NFPA 101 - Life Safety Code 16 NFPA 80 – Standard for Fire Doors and Other Opening Protectives 19 2010 ADA Standards for Accessible Design and ICC A117.1 Accessible and Usable Buildings and Facilities 22 Decoded: Panic hardware 24 Decoded: Door closers 26 Decoded: Fire door assembly inspection (FDIA) – Top 10 deficiencies 32 Decoded: NFPA 80 2013 FDAI changes 34 Decoded: Electrified hardware refresher Our special thanks to Allegion for graciously granting DHI permission to reprint and distribute this book under the DHI brand. Sources for code information There is more information about many of the topics covered in this publication on our website – iDigHardware.com. You can also submit a specific question from that site by pressing the Help button. ADA - Americans With Disabilities Act ICC - International Code Council www.ada.gov www.iccsafe.org ANSI - American National Standards Institute NFPA - National Fire Protection Association www.ansi.org www.nfpa.org BHMA - Builders Hardware Manufacturers Association UL - Underwriters Laboratories Inc. www.buildershardware.com www.ul.com Building Code Forum / Doors & Hardware Warnock Hersey / Intertek Testing Services www.thebuildingcodeforum.com/forum www.intertek.com CCBFC - Canadian Commission on Building and Fire Codes www.nationalcodes.ca 2 • DHI • Fire, life safety and accessibility codes The material enclosed within this guide is intended Once you have determined which code you want to as a resource and educational piece for those who have reference, go to the page(s) in this resource that contain chosen a profession of improving the safety and well information relative to that code publication. -
Guide to Passive Fire Protection in Buildings
Guide to Passive Fire Protection in Buildings Original manuscript Ed Soja Technical editor Colleen Wade Design and layout Koast Graphics Ltd ISBN 978-1-927258-75-0 (PDF) 978-1-927258-76-7 (epub) First released March 2017 Copyright BRANZ Ltd, 2017 Address BRANZ Ltd 1222 Moonshine Road, Judgeford 5381 Private Bag 50908, Porirua 5240 New Zealand Phone +64 4 237 1170 Fax +64 4 237 1171 BRANZ Shop www.branz.nz ALL RIGHTS RESERVED. The information contained herein is entitled to the full protection given by the Copyright Act 1994 to the holders of this copyright. Details may only be downloaded, stored or copied for personal use, by either an individual or corporate entity, for the purposes of the carrying out of a construction-related or other business or for private or educational use. Copying for the purposes of inclusion in trade or other literature for sale or transfer to a third party is strictly forbidden. All applications for reproduction in any form should be made to the Channel Delivery Team Leader, BRANZ Ltd, Private Bag 50908, Porirua City, New Zealand. Disclaimer: The information contained within this publication is of a general nature only. BRANZ does not accept any responsibility or liability for any direct, indirect, incidental, consequential, special, exemplary or punitive damage, or for any loss of profit, income or any intangible losses, or any claims, costs, expenses, or damage, whether in contract, tort (including negligence), equity or otherwise, arising directly or indirectly from or connected with your use of this publication, or your reliance on information contained in this publication. -
Fire Door the Importance 01Of Fire Doors
FIRE DOOR THE IMPORTANCE 01OF FIRE DOORS In any building, you have the right to expect that you will be safe and protected whenever a re breaks out. Sadly, this is not always the case. Sometimes, something within the fabric of the building or re safety devices fail and tragedy occurs causing serious injury and in some cases even death. Fire doors are part of a building's passive re protection system; an essential requirement for all public buildings, oces, factories and residences. The purpose of a wooden re door in everyday life is the same as any other door, except that, when a re breaks out, the door must perform its prime purpose of protecting lives and oering stability, insulation and integrity. This is exactly what Fire Doors achieve for the remainder of the building and other things within the building. 02KNOW YOUR FIRE DOOR! Doors & Doors India Pvt. Ltd., can oer assistance in developing cost eective, innovative solutions to meet the most demanding specications. PROMAT calcium silicate boards, Promatech H, Promina 60 and complementary lighter version Promatech L500 are used in our Fire Doors. These Fire Doors have passed stringent tests. Our team of highly trained specialists provides technical support during estimation until design and manufacturing. Doors & Doors India Pvt. Ltd., have been manufacturing Fire Doors since 2004. 03WOODEN FIRE DOOR Doors & Doors India Pvt. Ltd., brings you Acoustic Wooden Fire Doors, which provides you with a multifunctional product i.e. a combination of re as well as sound retardant properties. The construction of the wooden re door with sound retardant properties are the same as that of a Standard Wooden Fire Door with the addition of an Automatic Drop Seal and Silicon Self Adhesive Seals on the sides of the panel. -
Inspecting Fire and Egress Door Assemblies During COVID-19
DHI’S PUBLICATION FOR DOOR SECURITY + SAFETY PROFESSIONALS NOVEMBER/DECEMBER 2020 Inspecting Fire and Egress Door Assemblies During COVID-19 INSIDE: + RESISTING FIRE AND BULLETS + ASSESSING LEVELS OF THREAT PROTECTION + 45 YEARS OF SUCCESS FOR DHI + 2020 DHI ACHIEVEMENT AWARD RECIPIENTS YOU NEED the Power Supply. YOU NEED the Electric Strike. YOU NEED the Stocking Door Hardware Expert. Everything you need to get the job done. From our unmatched in-stock inventory of premium brands, to the unparalleled knowledge and experience of our technical sales team, we deliver the door SECLOCK.COM | 800-847-5625 hardware products and expertise you need. USA-MADE BALLISTIC RATED DOORS & FRAMES USA Titan Metal Products Inc. offers a complete line of ballistic rated doors, sidelites, transoms and openings meeting UL 752 Level 1-3. Available in multiple nishes including high performance uoropolymer nishes by PPG ®, Kynar ® , or custom stainless steel or aluminum clad. Intertek listed. Proudly USA-made. Visit us today at titanmetalinc.com to download our latest product brochure with our complete line of specialty doors and frames including re rated, detention, ballistic, security, blast, hurricane, acoustic and more. 866.848.2667 USA USA-MADE [email protected] contents THIS MONTH ON THE COVER: Zach Heald, FIRE AND EGRESS DOOR CFDAI, inspects a fire door in a ASSEMBLY INSPECTION PLUS hospital following COVID-19 safety METAL AND SPECIALTY DOORS protocols. FEATURES 8 THE CHALLENGES OF 26 IN DEFENSE OF DOORS CONDUCTING FIRE AND EGRESS Ever get stuck trying to make the door DOOR INSPECTIONS DURING industry sound glamorous and exciting? COVID-19 Here’s how to do it. -
Fireking Fire Door 630 / 631 / 634 / 635 Brochure
630/631 ® F IREK ING 634/635 ROLLING FIRE DOOR COLLECTION FIRE PROTECTION. INNOVATIVE DESIGN. OPTIMIZED PERFORMANCE. INDUSTRY LEADING COMMERCIAL & INDUSTRIAL SOLUTIONS FIREKING® ROLLING FIRE DOOR COLLECTION Standard features at a glance Options Technical data • Between jamb mount (630, 631, 635) Application Exterior/Interior for fire rated walls • Fire Sentinel® time-delay release device Operation Non-motorized, mechanical floor • FireLite® vision lite (Flat and insulated slats only resettable hoist with viscous with a max of 4 per door) governor • Smoke detectors and heat detectors Mounting Face of wall (between jambs • UL-listed brush-type smoke seals “S” label (flat optional on 630,631,635) or insulated slats only) Models 630 – Standard fire door • Flame baffle system - an FM requirement 631 – Basic fire door • UL, ULC and FM labels available 634 – Fire door up to 24'x24'; 4 • Horns and horns with strobes hour rating UL 635 – Insulated fire door • Tension release: push-up or crank, electric motor: RHX® or RSX® Drop speed Meets NFPA 80 requirements of • Non-tension hoist or electric motor: RSX® FDO or 6" to 24" per second RHX® FK Curtain • Stainless or galvanized steel: curtain, hood, guides, bottom bar Material Steel slats in a variety of gauges • Slide bolts, cylinder locks, interlocks Finish Baked-on polyester top coat in Gray, Tan, White or Brown • Wind load options to include: Florida Building Code Guides Three steel angles (some use (FBC), Miami-Dade, Texas Department of Insurance (TDI) structural and some are roll formed) • PowderGuard® -
Active and Passive Fire Protection Systems WHITE PAPER
WHITE PAPER Active and Passive Fire Protection Systems Active and passive fire protection systems work in tandem and play a key role in a comprehensive life safety plan for a commercial facility. Active and Passive Fire Protection Systems WHITE PAPER According to the National Fire Prevention Association (NFPA), smoke and toxic gases are the most significant factors in loss- of-life fires. Almost 70% of all building deaths are associated with smoke inhalation.* 70% The prompt and safe evacuation of building occupants and immediate of all building notification of the fire department are the primary means to prevent loss of life, as well as loss of property. The principles for saving building occupants from a fire deaths are are delineated in NFPA 101, Life Safety Code, and NFPA 72 for fire alarm systems. associated with Working in tandem with the alarm and detection systems are sprinkler systems. smoke inhalation When inspected and maintained properly, and ensured they haven’t been tampered with, sprinkler systems are designed to extinguish a fire. When a certain temperature is reached, a sprinkler head will activate and water will begin flowing, helping to put out the fire. NFPA 25 covers inspection requirements for sprinkler systems. Compliance helps maximize system integrity to avoid failure and ensure fast, effective response to a fire emergency. Principles for Another layer of protection is required, often referred to as “defend in place.” saving building In the event that a life safety system fails, is tampered with, or in a situation in which occupants in a facility cannot be easily evacuated, as is the case for the occupants ambulatory, elderly, incarcerated and others, passive fire protection can play from a fire are a key role in saving lives.