(12) Patent Application Publication (10) Pub. No.: US 2005/0183616A1 Eberhart Et Al
Total Page:16
File Type:pdf, Size:1020Kb
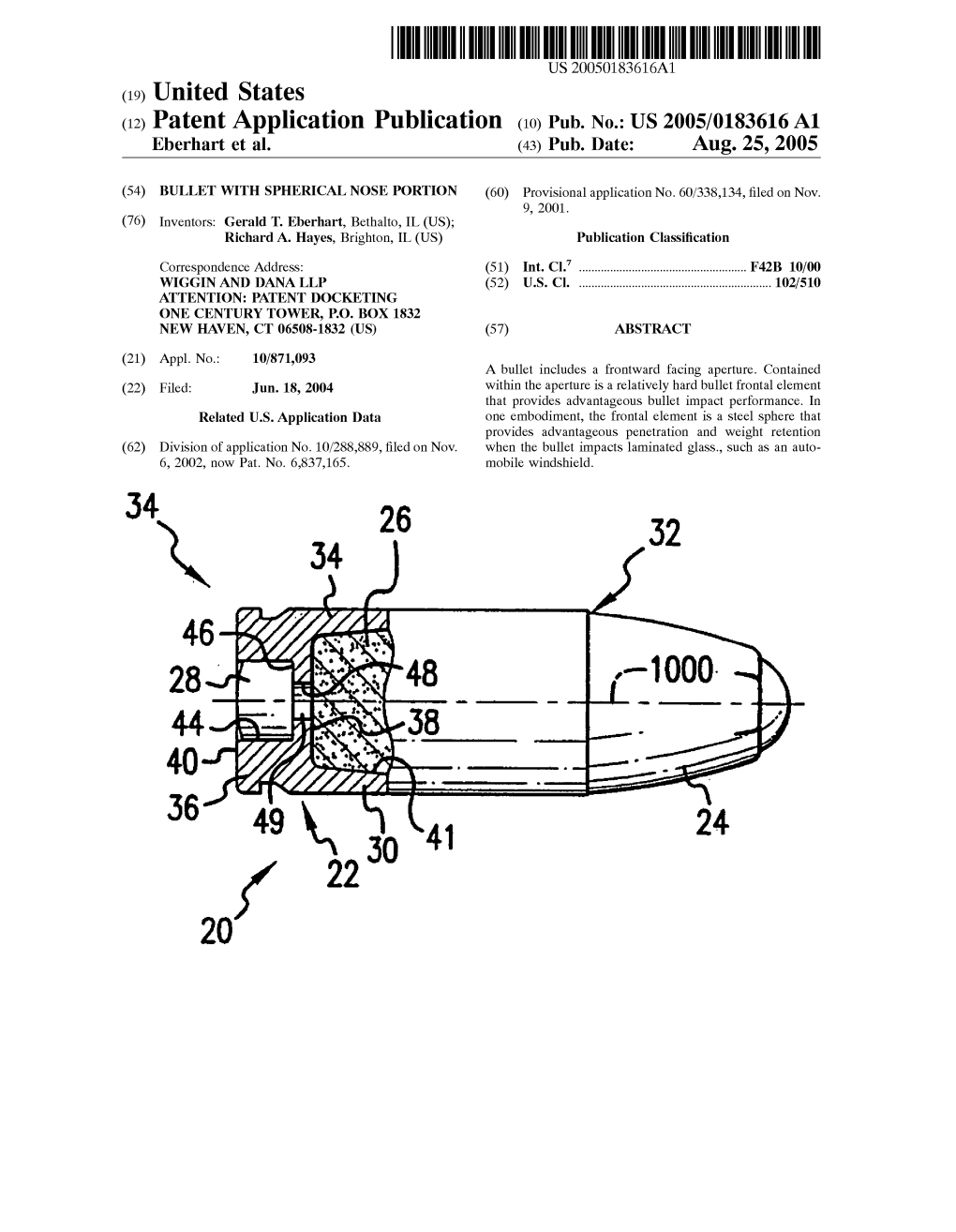
Load more
Recommended publications
-
Extrusion.Pdf
Extrusion: Second Edition Copyright © 2006 ASM International® M. Bauser, G. Sauer, K. Siegert, editors, p 195-321 All rights reserved. DOI:10.1361/exse2006p195 www.asminternational.org CHAPTER 5 The Production of Extruded Semifinished Products from Metallic Materials* THE HOT-WORKING PROCESS extrusion ered to be the most important of the hot-working is, in contrast to other compressive deformation processes. processes used to produce semifinished prod- ucts, a deformation process with pure compres- sive forces in all three force directions. These favorable deformation conditions do not exist in other production processes for semifinished products. Even in rolling, which is the most im- Extrusion of Materials with portant compressive working process for pro- ducing semifinished products, tensile forces oc- Working Temperatures cur in the acceleration zone of the roll gap as between 0 and 300 ЊC well as in the cross rolling process used to pierce blanks in the rolling of steel tubes. These Gu¨nther Sauer* tensile forces cause problems in the rolled prod- uct if the deformation conditions are not opti- mized. The benefits of this three-dimensional compression in terms of deformation technol- 5.1 Extrusion of Semifinished ogy, which have already been discussed in this Products in Tin Alloys book, can be clearly seen in Fig. 5.1 based on experimental results for face-centred cubic (fcc) Tin is a silver-white, very soft metal with a aluminum and zinc with its hexagonal lattice stable tetragonal lattice in the temperature range structure. 20 to 161 ЊC. The pure metal has a density of The extensive variations in the extrusion pro- 7.28 g/cm3 and a melting point of 232 ЊC. -
Backward Can Extrusion and Materials Behaviour
Backward can extrusion and materials behaviour Citation for published version (APA): Sillekens, W. H. (1992). Backward can extrusion and materials behaviour. Technische Universiteit Eindhoven. https://doi.org/10.6100/IR374925 DOI: 10.6100/IR374925 Document status and date: Published: 01/01/1992 Document Version: Publisher’s PDF, also known as Version of Record (includes final page, issue and volume numbers) Please check the document version of this publication: • A submitted manuscript is the version of the article upon submission and before peer-review. There can be important differences between the submitted version and the official published version of record. People interested in the research are advised to contact the author for the final version of the publication, or visit the DOI to the publisher's website. • The final author version and the galley proof are versions of the publication after peer review. • The final published version features the final layout of the paper including the volume, issue and page numbers. Link to publication General rights Copyright and moral rights for the publications made accessible in the public portal are retained by the authors and/or other copyright owners and it is a condition of accessing publications that users recognise and abide by the legal requirements associated with these rights. • Users may download and print one copy of any publication from the public portal for the purpose of private study or research. • You may not further distribute the material or use it for any profit-making activity or commercial gain • You may freely distribute the URL identifying the publication in the public portal. -
Cold Extrusion
ASM Handbook, Volume 14A: Metalworking: Bulk Forming Copyright © 2005 ASM International® S.L. Semiatin, editor, p405-418 All rights reserved. DOI: 10.1361/asmhba0004005 www.asminternational.org Cold Extrusion Revised by Murali Bhupatiraju, Metaldyne and Robert Greczanik, American Axle and Manufacturing COLD EXTRUSION is a push-through com- hardening (strengthening), and grain flow or Backward extrusion: pressive forming process with the starting directional strengthening. Compared to other n R material (billet/slug) at room temperature. Dur- forging operations cold extrusion is particularly Pb=0:4[sys+K( ln R) ](ab+bb ln R) ing the process, however, the deforming material attractive for the following reasons: dimensional R71 undergoes deformation heating (conversion of precision, superior surface finish, net-shaped where deformation work to heat) to several hundred features, lower energy consumption, higher degrees. Typically, a punch is used to apply production rates, and cleaner work environment. a af=1:15 7 cot a +4my pressure to the billet enclosed, partially or com- Drawbacks of cold extrusion are higher loads, 57:3 sin2 a pletely, in a stationary die. Aluminum and alu- lubrication cost, limited deformation, and lim- minum alloys, copper and copper alloys, carbon ited shape complexity. and steels, alloy steels, and stainless steels can be b : : R cold extruded. f ¼ 1 1 þ mð1 þ 0 5 ln Þ cot a Based on the punch and die design and the resulting material flow, cold extrusion can be Extrusion Pressure where ab =0.28; bb =2.36; s is the 0.2% yield classified into three primary processes: forward strength, psi; K is the true flow strength at unit extrusion, backward extrusion, and lateral The punch pressure in extrusion depends on strain, psi; R is the extrusion ratio; n is the strain- extrusion. -
Heading Hints a Guide to Cold Forming Specialty Alloys Heading Hints a Guide to Cold Forming Specialty Alloys
Heading Hints A Guide to Cold Forming Specialty Alloys Heading Hints A Guide to Cold Forming Specialty Alloys • Basics • Materials • Selection • Coatings • Tooling The information and data presented herein are typical or average values and are not a guarantee of maximum or minimum values. Applications specifically suggested for material described herein are made solely for the purpose of illustration to enable the reader to make his or her own evalua- tion and are not intended as warranties, either express or implied, of fitness for these or other purposes. There is no representation that the recipient of this literature will receive updated editions as they become available. MEMBER: MEMBER: © Copyright 2001, CRS Holdings, Inc. All rights reserved. 8-01/5M Printed in U.S.A. Introduction Heading Hints is published by Carpenter Technology Corporation (“Carpenter”), whose Specialty Alloys Operations produces more than 400 stainless steels and specialty alloys, including numerous grades specifically designed for the heading industry. Heading Hints is intended to serve as a reference source to aid in the suc- cessful fabrication of these materials in cold forming operations. Among the subjects covered are selection, lubricants and coatings, tooling and die design and manufacture, important techniques and case histories. Most of the information relates to stainless steel and high temperature alloys heading practices, but much of it is also applicable to heading other ferrous and nonferrous alloys. While it is important to have a thorough knowledge of general cold forming procedures, virtually all applications have their unique require- ments. If you have any questions about a specific application for stainless steel or high temperature alloys, or about heading and cold forming in general, please feel free to contact Carpenter’s technical service staff. -
Ammunition Making NRA by G. Frost
By George E. Frost *A (11.201) 4410 A Publication of the National Rifle Association of America c in m ii MAKING w c ml U MAKING An insider's Story By George E. Frost A Publication of the National Rifle Association of America George E. Frost George Ernest Frost has been known as "Jack" to his friends in the ammunition industry for nearly six decades—since the day in 1935 when he went to work for the Western Cartridge Co. of East Alton, Illinois. A graduate of Iowa State University, with a Bachelor of Science degree in Chemical Engineering, Frost joined the Western staff to pursue a company sponsored project involving dynamite filler, and stayed for a 27-year career that saw him fill managerial and executive positions in the sales, product services, quality control and military liaison divisions of Western and its parent company, Olin-Mathieson Chemical Corp. While a part of the Olin team. Frost gained a reputation as a top-notch, competitive rifleman and shotgunner, and an avid hunter and outdoorsman. In 1962, he moved to Lewiston, Idaho, to become Vice President for Production of Cascade Cartridge Co., where he established ammunition manufacturing facilities in Lewiston and a subsidiary plant in San Luis Potosi, Mexico. From Mexico, Frost moved to the Republic of the Philippines and to the position of Executive Vice President and General Manager for The Squires-Bingham Manufacturing Co. He was instru- mental in the establishment of facilities for the production of both military and sporting metallic cartridges and shotshells. Retired since 1979, Frost continues to work with Squires Bingham's successor. -
Small Arms Ammunition Manufacturing : Background and Pr a C Tic Es
Small Arms Ammunition Manufacturing : Background and Pr a c tic es Presented by: Richard Pumerantz, P hD Ten - X Ammunition, Inc. PO Box 726 Lake Arrowhead , CA 9 2352 (909) 744 - 8352 www.tenxammo.com SMALL ARMS AMMUNITION MANUFACTURING : Background and Practices Introduction Knowledge of the evolution of small - arms systems for sporting and military purposes is important for the student of firearms identification. The individual components of the syst em — firearms and ammunition — are closely interrelated. Small improvements in one continue to lead to small improvements in the other. Understanding this evolution will make the student a better firearm examiner and witness. As an evolutionary overview, this discussion follows the significant milestones showing how today’s technology is connected to the past and tracing the key lines of growth. It is a story of constant improvement, of new strengths from old weaknesses, and of the incredible inventiveness of t he human mind. Ammunition Ammunition consists of four components: Propellant Projectile (bullets and shot pellets) Cartridge cases Primer Self - contained ammunition, in which the propellant, projectile, and primer are held together by a cartridge cas e, is called fixed ammunition . Artillery ammunition with separate components is called semifixed ammunition . A cartridge is a single unit of fixed ammunition. Evolution of Propellants Propellant materials are the evolutionary product of a basic tenet i n weapon technology: energy must be stored for later use . The concept of a propellant is that energy can be stored in chemical form, possibly years before it is ultimately released. This demands a material that is reasonably stable, compact, and portable.