US5171549.Pdf
Total Page:16
File Type:pdf, Size:1020Kb
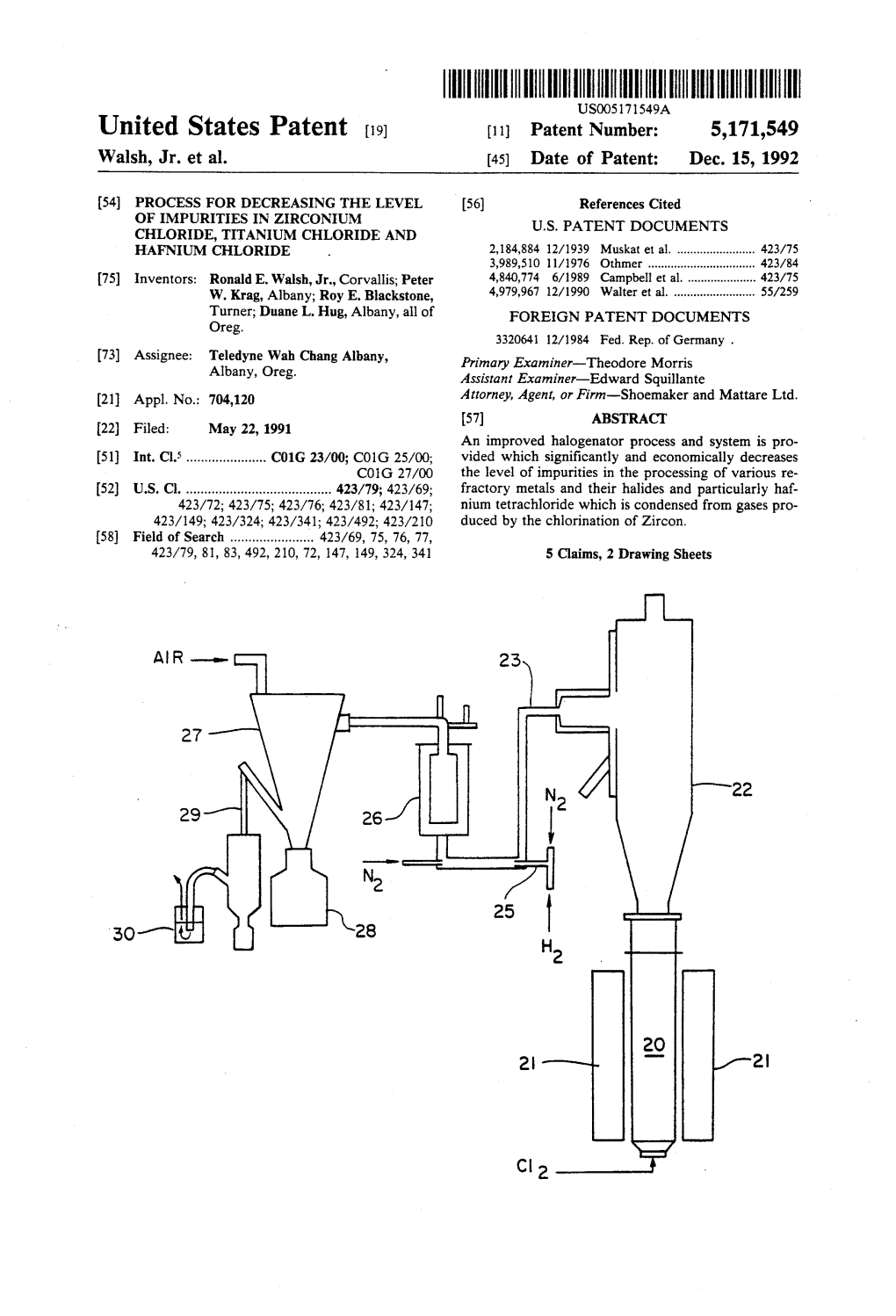
Load more
Recommended publications
-
Inventory Size (Ml Or G) 103220 Dimethyl Sulfate 77-78-1 500 Ml
Inventory Bottle Size Number Name CAS# (mL or g) Room # Location 103220 Dimethyl sulfate 77-78-1 500 ml 3222 A-1 Benzonitrile 100-47-0 100ml 3222 A-1 Tin(IV)chloride 1.0 M in DCM 7676-78-8 100ml 3222 A-1 103713 Acetic Anhydride 108-24-7 500ml 3222 A2 103714 Sulfuric acid, fuming 9014-95-7 500g 3222 A2 103723 Phosphorus tribromide 7789-60-8 100g 3222 A2 103724 Trifluoroacetic acid 76-05-1 100g 3222 A2 101342 Succinyl chloride 543-20-4 3222 A2 100069 Chloroacetyl chloride 79-04-9 100ml 3222 A2 10002 Chloroacetyl chloride 79-04-9 100ml 3222 A2 101134 Acetyl chloride 75-36-5 500g 3222 A2 103721 Ethyl chlorooxoacetate 4755-77-5 100g 3222 A2 100423 Titanium(IV) chloride solution 7550-45-0 100ml 3222 A2 103877 Acetic Anhydride 108-24-7 1L 3222 A3 103874 Polyphosphoric acid 8017-16-1 1kg 3222 A3 103695 Chlorosulfonic acid 7790-94-5 100g 3222 A3 103694 Chlorosulfonic acid 7790-94-5 100g 3222 A3 103880 Methanesulfonic acid 75-75-2 500ml 3222 A3 103883 Oxalyl chloride 79-37-8 100ml 3222 A3 103889 Thiodiglycolic acid 123-93-3 500g 3222 A3 103888 Tetrafluoroboric acid 50% 16872-11-0 1L 3222 A3 103886 Tetrafluoroboric acid 50% 16872-11-0 1L 3222 A3 102969 sulfuric acid 7664-93-9 500 mL 2428 A7 102970 hydrochloric acid (37%) 7647-01-0 500 mL 2428 A7 102971 hydrochloric acid (37%) 7647-01-0 500 mL 2428 A7 102973 formic acid (88%) 64-18-6 500 mL 2428 A7 102974 hydrofloric acid (49%) 7664-39-3 500 mL 2428 A7 103320 Ammonium Hydroxide conc. -
Safety Data Sheet Material Name: HFCL4 SDS ID: 00227583P
Safety Data Sheet Material Name: HFCL4 SDS ID: 00227583P Section 1 - PRODUCT AND COMPANY IDENTIFICATION Material Name HFCL4 Synonyms HAFNIUM TETRACHLORIDE; HAFNIUM (IV) CHLORIDE; (T-4) HAFNIUM CHLORIDE (HfCl4); HAFNIUM CHLORIDE; Cl4Hf Chemical Family metal, halides Product Use semiconductor manufacture Restrictions on Use None known Details of the supplier of the safety data sheet Entegris, Inc. 129 Concord Road Building 2 Billerica, MA 01821 USA Telephone Number: +1-952-556-4181 Telephone Number: +1-800-394-4083 (toll free within North America) Emergency Telephone Number: CHEMTREC - U.S. - 1-800-424-9300 CHEMTREC - Intl. - 1-703-527-3887 E-mail: [email protected] Section 2 - HAZARDS IDENTIFICATION Classification in accordance with paragraph (d) of 29 CFR 1910.1200. Combustible Dust Skin Corrosion/Irritation - Category 1B Serious Eye Damage/Eye Irritation - Category 1 Specific target organ toxicity - Single exposure - Category 3 ( respiratory system ) GHS Label Elements Symbol(s) Signal Word Danger Hazard Statement(s) ____________________________________________________________ Page 1 of 9 Issue date: 2021-05-11 Revision 6.0 Print date: 2021-05-12 Safety Data Sheet Material Name: HFCL4 SDS ID: 00227583P May form combustible dust concentrations in air. Causes severe skin burns and eye damage. May cause respiratory irritation. Precautionary Statement(s) Prevention Do not breathe dust. Wear protective gloves/protective clothing/eye protection/face protection. Wash thoroughly after handling. Use only outdoors or in a well-ventilated area. Response Immediately call a POISON CENTER or doctor/physician. IF INHALED: Remove person to fresh air and keep comfortable for breathing. Specific treatment may be needed, see first aid section of Safety Data Sheet. -
Hafnium Nitrate Precursor Synthesis and Hfo2 Thin Film Deposition WEIWEI ZHUANG,1 JOHN F. CONLEY,1 YOSHI ONO,1 DAVID R. EVANS1 A
- 1 - Hafnium Nitrate Precursor Synthesis and HfO2 Thin Film Deposition WEIWEI ZHUANG,1 JOHN F. CONLEY,1 YOSHI ONO,1 DAVID R. EVANS1 AND R. SOLANKI2 1Sharp Laboratories of America, 5700 Pacific Rim Blvd Camas, WA 98607 2Oregon Graduate Institute, Beaverton, OR, 97006 The paper will introduce a simple new method on the synthesis of both hafnium and zirconium nitrate precursors. The intermediate product, dinitrogen pentoxide produced from the water extraction from fume nitric acid via phosphorus pentoxide, was condensed by liquid nitrogen trap into a flask equipped with hafnium or zirconium tetrachloride. To give the high yield, the mixture of fume nitric acid and phosphorus pentoxide was heated to a certain temperature, from which large quantity of dinitrogen pentoxide had been generated. In the following step, hafnium or zirconium tetrachloride was refluxed over dinitrogen pentoxide at 30 to 35 oC for half- hour. The product was purified by sublimation. High yield, above 95%, was obtained. The cost for the hafnium nitrate precursor synthesis was estimated. The precursor was not stable at room temperature, and should be stored in refrigerator in sealed vials. No chlorine was detected from both EDS and chemical analysis. The volatility was evaluated by thermal gravity analysis. For high k thin film applications, the precursors were evaluated through the hafnium oxide thin film deposition via ALD process. High quality hafnium oxide thin films were obtained. The hafnium oxide thin film property consistence using different batches of our synthesized hafnium nitrate precursor was also verified. X-ray diffraction analysis indicated the films were smooth, uniform, amorphous as deposited and monoclinic after post annealing. -
WO 2016/074683 Al 19 May 2016 (19.05.2016) W P O P C T
(12) INTERNATIONAL APPLICATION PUBLISHED UNDER THE PATENT COOPERATION TREATY (PCT) (19) World Intellectual Property Organization International Bureau (10) International Publication Number (43) International Publication Date WO 2016/074683 Al 19 May 2016 (19.05.2016) W P O P C T (51) International Patent Classification: (81) Designated States (unless otherwise indicated, for every C12N 15/10 (2006.01) kind of national protection available): AE, AG, AL, AM, AO, AT, AU, AZ, BA, BB, BG, BH, BN, BR, BW, BY, (21) International Application Number: BZ, CA, CH, CL, CN, CO, CR, CU, CZ, DE, DK, DM, PCT/DK20 15/050343 DO, DZ, EC, EE, EG, ES, FI, GB, GD, GE, GH, GM, GT, (22) International Filing Date: HN, HR, HU, ID, IL, IN, IR, IS, JP, KE, KG, KN, KP, KR, 11 November 2015 ( 11. 1 1.2015) KZ, LA, LC, LK, LR, LS, LU, LY, MA, MD, ME, MG, MK, MN, MW, MX, MY, MZ, NA, NG, NI, NO, NZ, OM, (25) Filing Language: English PA, PE, PG, PH, PL, PT, QA, RO, RS, RU, RW, SA, SC, (26) Publication Language: English SD, SE, SG, SK, SL, SM, ST, SV, SY, TH, TJ, TM, TN, TR, TT, TZ, UA, UG, US, UZ, VC, VN, ZA, ZM, ZW. (30) Priority Data: PA 2014 00655 11 November 2014 ( 11. 1 1.2014) DK (84) Designated States (unless otherwise indicated, for every 62/077,933 11 November 2014 ( 11. 11.2014) US kind of regional protection available): ARIPO (BW, GH, 62/202,3 18 7 August 2015 (07.08.2015) US GM, KE, LR, LS, MW, MZ, NA, RW, SD, SL, ST, SZ, TZ, UG, ZM, ZW), Eurasian (AM, AZ, BY, KG, KZ, RU, (71) Applicant: LUNDORF PEDERSEN MATERIALS APS TJ, TM), European (AL, AT, BE, BG, CH, CY, CZ, DE, [DK/DK]; Nordvej 16 B, Himmelev, DK-4000 Roskilde DK, EE, ES, FI, FR, GB, GR, HR, HU, IE, IS, IT, LT, LU, (DK). -
SEWERA, 853: "2: with A
USOO696055OB2 (12) United States Patent (10) Patent No.: US 6,960,550 B2 Waymouth et al. (45) Date of Patent: *Nov. 1, 2005 (54) THERMOPLASTICCATALYST SYSTEMS ELASTOMERIC FOR HIGH MELTING 53.5,475,075 A 1512/1995 S. RonBrant et GEOal. .............. 526/348.3 3.13. O-OLEFN POLYMERS AND PLASTOMERS 5594,0802- Y - 2 A 1/1997 WaymouthCSCO C aet al. .........- - - 526/126 (75) Inventors: Robert M. Waymouth, Palo Alto, CA 3G A 3. SN,f al a. 526/351 (US); Raisa Kravchenko, Wilmington, 6.169,151 B1 1/2001 Waymouth et al. DE (US); Larry L. Bendig, Aurora, IL 6,380,341 B1 4/2002 Waymouth et al. (US); Eric J. Moore, Carol Stream, IL 2.2 : : - 2 . : H: WEay moulin et h ettal al. ........... 556/53 SEWERA,s s s 853: "2: WithaWO e a (US); Andreas B. Ernst, Naperville, IL 2- - - 2 y (US) OTHER PUBLICATIONS (73) Assignee: The Board of Trustees of the Leland Quirk, Roderic P., Transition Metal Catalyzed Polymeriza Stanford Junior University, Palo Alto, Ygs,18, Cambridge University PreSS, Cambridge, pp. CA (US) Spitz, R., et al., Propene Polymerization with MgCl, Sup - - - - ported Ziegler catalysts: Activation by hydrogen and ethyl (*) Notice: Subject to any disclaimer, the term of this ene, 1988, Makromol. Chem. 189, pp. 1043–1050. patent is extended or adjusted under 35 Valvassori, A., et al., Kinetics of the Ethylene-Propylene U.S.C. 154(b) by 243 days. Copolymerization, 1963, Makoromol. Chem. 161, pp. 46-62. This patent is Subject to a terminal dis- Brintzinger, H., et al., Stereospecific Olefin Polymerization claimer. -
Australian Atomic Energy Commission
AAEC/TM570 AUSTRALIAN ATOMIC ENERGY COMMISSION LUCAS HEIGHTS REVIEW OF PROCESSES FOR THE PRODUCTION OF HAFNIUM-FREE ZIRCONIUM by D. ROYSTON P.O. ALFREDSON October 1970 ISBN 0 642 99394 7 AUSTRALIAN ATOMIC ENERGY COMMISSION RESEARCH ESTABLISHMENT LUCAS HEIGHTS REVIEW OF PROCESSES FOR THE PRODUCTION OF HAFNIUM-FREE ZIRCONIUM by Dc ROYSTON Pa G, A.LFREDSON ABSTRACT The three main industrial processes for the production of hafnium-free zirconium are described in terms of their head-end,, zirconium-hafnium separation and zirconium metal forming steps. Possible improvements and alternative processes are outlined. Zirconium-hafnium separation schemes based on selective reduction of the chlorides or distillation and sublimation techniques show the most promise for future development in competition with the established hexone-thiocyanate and TBP-nitric acid solvent extraction schemes. Head-end steps involving direct chlorination of zircon in fluidised beds or caustic fusion and metal production via electrowinning warrant further development. CONTENTS Page 1. INTRODUCTION 1 2. HEAD-END PROCESSES 2 2.1 Chlorination Processes 2 2.1.1 Carbide intermediate 2 2.1.2 Direct chlorination 2 2.2 Fusion Processes 3 2,5 Potassium Silicofluoride Sinter Processes 3 3. ZIRCONIUM-HAFNIUM SEPARATION PROCESSES 3.1 Solvent Extraction Separation Processes 4 National Library of Australia card number and ISBN 0 642 99394 7 3.1.1 Hexone-thiocyanate process 4 3.1.2 TBP-nitric acid process 5 3.2 Fractional Crystallisation 5 3.3 Non-Aqueous Separation Methods Using Chlorides 5 3.3.1 Selective partial reduction - Newnham process 5 3.3.2 Sublimation and distillation methods 7 3.3.2.1 Sublimat ion 7 3.3.2.2 Distillation of the tetrachlorides 7 3.3.2.3 Distillation of phosphorous oxychloride 8 complexes 4. -
Asymmetric Metallocene Catalysts Design of Ultrahigh Molecular
ASYMMETRIC METALLOCENE CATALYSTS DESIGN OF ULTRAHIGH MOLECULAR WEIGHT POLYPROPYLENE PLASTOMERS Dissertation zur Erlangung des Doktorgrades Dr. rer. nat. der Fakultät für Naturwissenschaften der Universität Ulm vorgelegt von CECILIA COBZARU aus GHERAESTI / RUMÄNIEN 2006 Amtierender Dekan: Prof. Dr. K.-D. Spindler 1. Gutachter: Prof. Dr. B. Rieger 2. Gutachter: Tag der Promotion: Table of Contents Chapter 1 Introduction 1.1 Benefits of plastics 1 1.2 Major markets of plastics and thermoplastics 3 1.3 Polypropylene products 5 Chapter 2 Tailor-made polyolefine materials via metallocene catalysts 2.1 Single site catalysts 11 2.2 Activators of the catalyst precursors 13 2.3 Stability of the active species 14 2.4 C1 - symmetric metallocenes. Strategies of catalyst development 15 2.5 Polypropylene microstructure and material properties 17 2.6 Content and significance of the study 18 Chapter 3 Synthesis of plastomeric polypropylenes 3.1 New ligands and complexes toward olefines homo- and copolymers 20 3.2 Ligand and complex synthesis 25 3.2.1 General procedure 25 3.2.2 Synthesis of indene derivatives 26 3.2.3 Ligand synthesis 27 3.2.4 Synthesis of the bridged complexes 32 3.2.5 Synthesis of the unbridged complexes 33 3.2.6 Solid state structure 34 3.3 Experimental section 3.3.1 General Procedure 39 3.3.2 X-ray Crystallography 39 3.3.3 Preparation of the indenes 39 3.3.4 Preparation of 1-(9-Fluorenyl)-2-bromethane 43 3.3.5 Preparation of the bridged ligands 43 3.3.6 Preparation of the bridged complexes 45 3.3.7 Preparation of the unbridged complexes -
Material Safety Data Sheet
Material Safety Data Sheet NFPA HMIS Personal Protective Equipment Health Hazard 3 2 2 1 Fire Hazard 3 Reactivity 1 See Section 15. Section 1. Chemical Product and Company Identification Page Number: 1 Common Name/ Borane-Tetrahydrofuran Complex, 1 M, in Catalog B2041 Number(s). Trade Name Tetrahydrofuran CAS# Mixture. Manufacturer SPECTRUM LABORATORY PRODUCTS INC. RTECS Not applicable. 14422 S. SAN PEDRO STREET TSCA TSCA 8(b) inventory: GARDENA, CA 90248 Tetrahydrofuran; Tetrahydrofuran-borane Commercial Name(s) Not available. CI# Not available. Synonym Borane-Tetrahydrofuran Complex, 1 M Solution in Tetrahydrofuran IN CASE OF EMERGENCY Chemical Name Not applicable. CHEMTREC (24hr) 800-424-9300 Chemical Family Not available. CALL (310) 516-8000 Chemical Formula Not applicable. Supplier SPECTRUM LABORATORY PRODUCTS INC. 14422 S. SAN PEDRO STREET GARDENA, CA 90248 Section 2.Composition and Information on Ingredients Exposure Limits Name CAS # TWA (mg/m 3) STEL (mg/m 3) CEIL (mg/m 3) % by Weight 1) Tetrahydrofuran 109-99-9 590 735 90 2) Tetrahydrofuran-Borane complex 14044-65-6 10 Toxicological Data Tetrahydrofuran : on Ingredients ORAL (LD50): Acute: 1650 mg/kg [Rat]. VAPOR (LC50): Acute: 21000 mg/m 3 3 hours [Rat]. Tetrahydrofuran-Borane complex LD50: Not available. LC50: Not available. Continued on Next Page Borane-Tetrahydrofuran Complex, 1 M, in Page Number: 2 Tetrahydrofuran Section 3. Hazards Identification Potential Acute Health Hazardous in case of skin contact (irritant), of eye contact (irritant). Slightly hazardous in case of skin contact Effects (permeator), of ingestion, of inhalation. Potential Chronic Health CARCINOGENIC EFFECTS : Not available. Effects MUTAGENIC EFFECTS : Mutagenic for bacteria and/or yeast. -
United States Patent (19) Ill) Patent Number: 5,004,820 Buchwald Et Al
United States Patent (19) Ill) Patent Number: 5,004,820 Buchwald et al. 45) Date of Patent: Apr. 2, 1991 54) PREPARATION OF CHIRAL 0277004 8/1988 European Pat. Off. .............. 556/53 METAL LOCENE DIHALIDES 0284707 10/1988 European Pat. Off. .............. 556/53 0284708 10/1988 European Pat. Off. .............. 556/53 (75) Inventors: Stephen L. Buchwald; Robert B. Grossman, both of Somerville, Mass. OTHER PUBLICATIONS 73) Assignee: Massachusetts Institute of Wild et al., J. Organomet. Chem. 232 (1982) 233-47, Technology, Cambridge, Mass. Synthesis and Molecular Structures of Chiral an sa-Titanocene Derivatives with Bridged Tetrahy (21) Appl. No.: 390,062 droindenyl Ligands. 22 Filed: Aug. 7, 1989 Schafer et al., J. Organomet. Chem. 328 (1987) 87-99, Diastereomeric Derivatisation and Enantiometer Sepa (51) Int. C. ............................................. CO7F 00/00 ration of Ethylenebis (Tetrahydroindenyl)--Titanium (52) U.S. C. ...................................................... 556/53 Field of Search .......................................... 556/53 and -Zirconium Dichlorides. (58) Ewen et al., J. Am. Chem. Soc. 109 (1987) 6544, Crystal 56) References Cited Structures and Stereospecific Propylene Polymeriza U.S. PATENT DOCUMENTS tions with Chiral Hafnium Metallocene Catalysts. 4,169,845 10/1979 Jonas ................................. 556/53 X Collins et al., J. Organomet. Chem. 342 (1988) 21, 4,310,648 1/1982 Shipley et al. ...................... 526/14 X-Ray Structures of Ethylenebis (Tetrahydroindenyl 4,361,685 11/1982 Shipley ........... ...... S26/14 )-Titanium and -Zirconium Dichlorides: A Revision. 4,404,344 9/1983 Sinn et al. ........................... 526/160 4,522,982 6/1985 Ewen .................................. 525/240 Primary Examiner-Paul F. Shaver 4,530,914 7/1985 Ewen et al. ......................... 502/13 Attorney, Agent, or Firm-Thomas J. -
Zirconium Chloride Molecular Species: Combining Electron Impact Mass Spectrometry and First Principles Calculations
Research Article Zirconium chloride molecular species: combining electron impact mass spectrometry and frst principles calculations Rosendo Borjas Nevarez1 · Eunja Kim2 · Bradley C. Childs3 · Henrik Braband3 · Laurent Bigler3 · Urs Stalder3 · Roger Alberto3 · Philippe F. Weck4 · Frederic Poineau1 © Springer Nature Switzerland AG 2019 Abstract Zirconium tetrachloride was synthesized from the reaction between zirconium metal and chlorine gas at 300 °C and was analyzed by electron impact mass spectrometry (EI-MS). Substantial fragmentation products of ZrCl4 were observed in the mass spectra, with ZrCl3 being the most abundant species, followed by ZrCl2, ZrCl, and Zr. The predicted geometry and kinetic stability of the fragments previously mentioned were investigated by density functional theory (DFT) calcu- lations. Energetics of the dissociation processes support the most stable fragment to be ZrCl3 while the least abundant are ZrCl and ZrCl2. Keywords Zirconium · Chloride · Mass spectrometry · Gas phase · DFT 1 Introduction [7], followed by ZrCl4 [8, 9]. Therefore, an accurate knowl- edge of zirconium chlorides is crucial for efcient separa- Zirconium chloride is of crucial importance in numerous tion and selective recovery of Zr from cladding materials. research felds and industrial applications such as uncon- While much attention has been given to the theoretical ventional catalysis [1], refning of Zr-containing ores by and experimental investigations of crystalline ZrCl 4 [9], Kroll reduction [2], chemical vapor deposition [3], and accurate structural and thermomechanical information nuclear engineering [4–6]. Chlorination has been pro- of ZrClx (x = 1, 2, 3, 4) molecular species remains scarce. posed for large-scale separation and selective recovery of Due to their chemical similarities and the importance of Zr as ZrCl4 from U–Zr alloys or used nuclear fuel cladding the refnement process in the nuclear industry, studies on [4, 5]. -
Safety Data Sheet
SAFETY DATA SHEET Revision Date 22-Jan-2021 Revision Number 2 SECTION 1: IDENTIFICATION OF THE SUBSTANCE/MIXTURE AND OF THE COMPANY/UNDERTAKING 1.1. Product identifier Product Description: Hafnium(IV) chloride Cat No. : 45612 Synonyms Hafnium tetrachloride. CAS-No 13499-05-3 Molecular Formula Hf Cl4 Reach Registration Number - 1.2. Relevant identified uses of the substance or mixture and uses advised against Recommended Use Laboratory chemicals. Uses advised against No Information available 1.3. Details of the supplier of the safety data sheet Company Thermo Fisher (Kandel) GmbH . Erlenbachweg 2 76870 Kandel Germany Tel: +49 (0) 721 84007 280 Fax: +49 (0) 721 84007 300 E-mail address [email protected] www.alfa.com Product safety Tel + +049 (0) 7275 988687-0 1.4. Emergency telephone number Carechem 24: +44 (0) 1235 239 670 (Multi-language emergency number) Poison Information Center Mainz www.giftinfo.uni-mainz.de Telephone: +49(0)6131/19240 Exclusively for customers in Austria: Poison Information Center (VIZ) Emergency call 0-24 clock: +43 1 406 43 43 Office hours: Monday to Friday, 8am to 4pm, tel: +43 1 406 68 98 SECTION 2: HAZARDS IDENTIFICATION 2.1. Classification of the substance or mixture CLP Classification - Regulation (EC) No 1272/2008 Physical hazards Based on available data, the classification criteria are not met ______________________________________________________________________________________________ ALFAA45612 Page 1 / 10 SAFETY DATA SHEET Hafnium(IV) chloride Revision Date 22-Jan-2021 ______________________________________________________________________________________________ Health hazards Skin Corrosion/Irritation Category 1 B (H314) Serious Eye Damage/Eye Irritation Category 1 (H318) Environmental hazards Based on available data, the classification criteria are not met Full text of Hazard Statements: see section 16 2.2. -
Scope of the Risk Evaluation for Carbon Tetrachloride (Methane, Tetrachloro-)
EPA Document# EPA-740-R1-7010 June 2017 United States Office of Chemical Safety and Environmental Protection Agency Pollution Prevention Scope of the Risk Evaluation for Carbon Tetrachloride (Methane, Tetrachloro-) CASRN: 56-23-5 June 2017 TABLE OF CONTENTS ABBREVIATIONS ................................................................................................................................ 6 EXECUTIVE SUMMARY ...................................................................................................................... 9 1 INTRODUCTION ........................................................................................................................ 12 1.1 Regulatory History ...................................................................................................................... 14 1.2 Assessment History .................................................................................................................... 15 1.3 Data and Information Collection ................................................................................................ 16 2 SCOPE OF THE EVALUATION ..................................................................................................... 18 2.1 Physical and Chemical Properties .............................................................................................. 18 2.2 Conditions of Use ....................................................................................................................... 19 Data and Information Sources ..............................................................................................