Liquid Oxygen of Argon
Total Page:16
File Type:pdf, Size:1020Kb
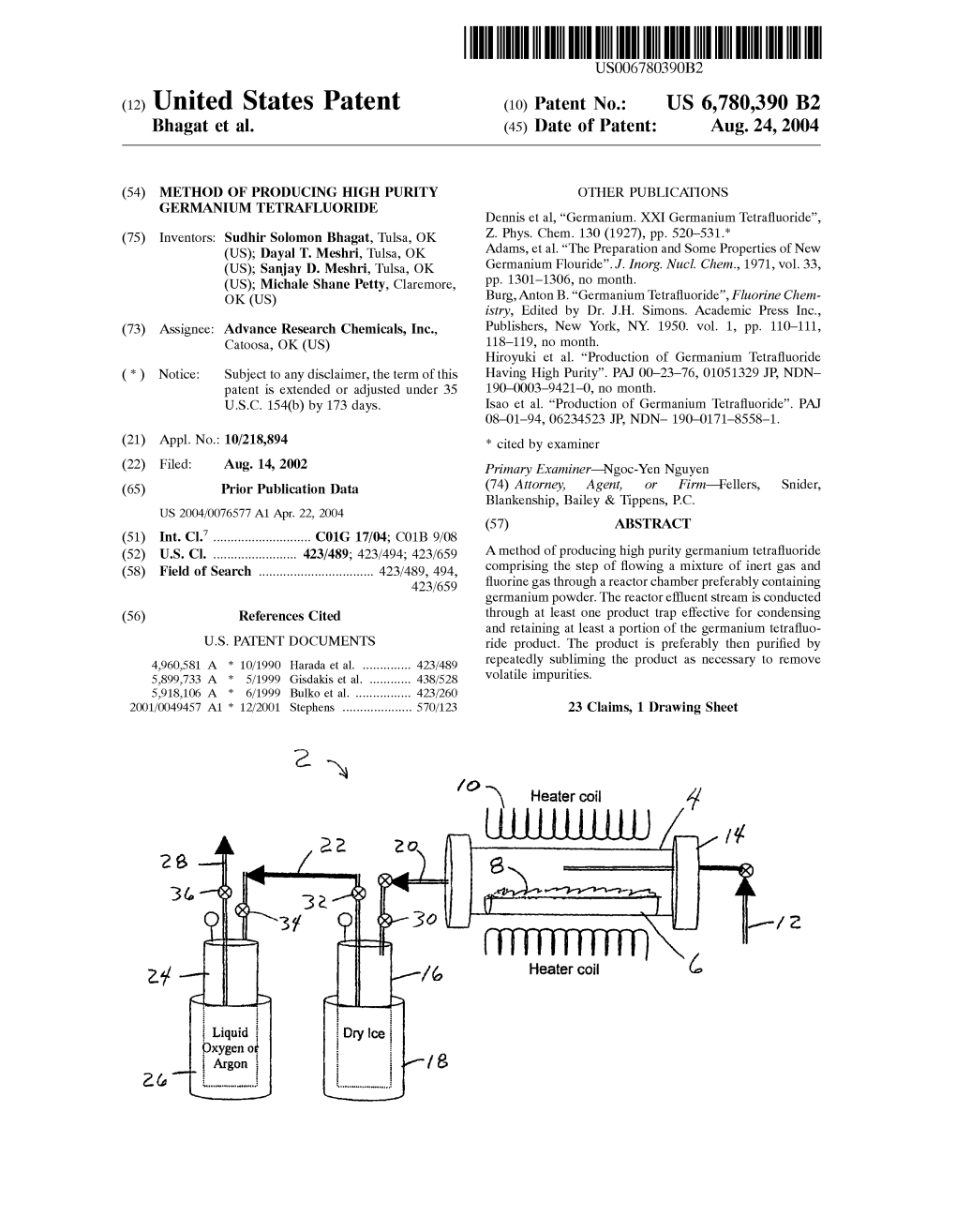
Load more
Recommended publications
-
2018 Annual Survey of Biological and Chemical Agents Regulated by Homeland Security (And Carcinogens Regulated by OSHA)
Name: Dept: Date: 2018 Annual Survey of Biological and Chemical Agents regulated by Homeland Security (and carcinogens regulated by OSHA) Due (date) All labs that do not have a current chemical inventory in Chematix MUST complete this survey. The University is required to make an annual report of all chemicals on the Chemical Facility Anti-Terrorism Standards (CFATS) lists. Additional information regarding the regulations is available on the EH&S website at http://www.safety.rochester.edu/restricted/occsafe/chemicalagent.html and https://www.selectagents.gov. 1. Please review the lists on the following pages and indicate if any are possessed by your lab. The CAS# has been added to the list for ease of searching databases. The CAS# is a Chemical Abstract Service numbering system which assigns a unique number to every chemical substance based on structure; this helps avoid confusion by use of synonyms or different naming conventions. a. If yes for possession, place an X in the applicable box and if requested, include the quantity held in your lab. b. If no, leave blank. 2. After reviewing the list, please complete the information box below (or on last page for possession), then sign, date and return to EH&S. 3. Please call Donna Douglass at 275-2402 if you have any questions. Thank you for your cooperation in collecting data required by the Department of Homeland Security! Possession: 1) Fill in applicable boxes, 2) have PI sign last page, 3) return all pages to Donna Douglass OR Non-possession: 1) Check only one box on the left, 2) sign, 3) return just this page to Donna Douglass I do not have a lab, do not work in a lab, nor do I possess any of the agents in this survey. -
Homeland Security List
List Sorted Alphabetically ACG = Any Commercial Grade. If you have any questions, please contact EHS @ 898-5126. Minimum Concentration Chemical Of Interest Synonym CAS (percent) Amount on Hand (pounds) 1- Pentene 109-67-1 1 1,1-Dimethylhydrazine [Hydrazine, 1, 1-dimethyl-] 57-14-7 1 1,3-Bis(2-chloroethylthio)-n-propane 63905-10-2 any quantity 1,3-Butadiene 106-99-0 1 1,3-Pentadiene 504-60-9 1 1,4-Bis(2-chloroethylthio)-n-butane 142868-93-7 any quantity 1,5-Bis(2-chloroethylthio)-n-pentane 142868-94-8 any quantity 1-Butene 106-98-9 1 1-Chloropropylene [1-Propene, 1-chloro-] 590-21-6 1 1H-Tetrazole 288-94-8 ACG 2,2-Dimethylpropane [Propane, 2,2-dimethyl-] 463-82-1 1 2-Butene 107-01-7 1 2-Butene-cis 590-18-1 1 2-Butene-trans [2-Butene, (E)] 624-64-6 1 2-Chloroethylchloro-methylsulfide 2625-76-5 any quantity 2-Chloropropylene [1-Propene, 2-chloro-] 557-98-2 1 2-Methyl-1-butene 563-46-2 1 2-Methylpropene [1-Propene, 2-methyl-] 115-11-7 1 2-Pentene, (E)- 646-04-8 1 2-Pentene, (Z)- 627-20-3 1 3-Methyl-1-butene 563-45-1 1 5-Nitrobenzotriazol 2338-12-7 ACG Acetaldehyde 75-07-0 1 Acetylene [Ethyne] 74-86-2 1 Acrolein [2-Propenal] or Acrylaldehyde 107-02-8 1 Acrylonitrile [2-Propenenitrile] 107-13-1 1 Acrylyl chloride [2-Propenoyl chloride] 814-68-6 1 Allyl alcohol [2-Propen-1-ol] 107-18-6 1 Allylamine [2-Propen-1-amine] 107-11-9 1 Aluminum (powder) 7429-90-5 ACG Ammonia (anhydrous) 7664-41-7 1 Ammonia (conc. -
CSAT Top-Screen Questions OMB PRA # 1670-0007 Expires: 5/31/2011
CSAT Top-Screen Questions January 2009 Version 2.8 CSAT Top-Screen Questions OMB PRA # 1670-0007 Expires: 5/31/2011 Change Log .........................................................................................................3 CVI Authorizing Statements...............................................................................4 General ................................................................................................................6 Facility Description.................................................................................................................... 7 Facility Regulatory Mandates ................................................................................................... 7 EPA RMP Facility Identifier....................................................................................................... 9 Refinery Capacity....................................................................................................................... 9 Refinery Market Share ............................................................................................................. 10 Airport Fuels Supplier ............................................................................................................. 11 Military Installation Supplier................................................................................................... 11 Liquefied Natural Gas (LNG) Capacity................................................................................... 12 Liquefied Natural Gas Exclusion -
New Regs Announced for Securing High-Risk
Number 586 April 9, 2007 Client Alert Latham & Watkins Environment, Land & Resources Department Department of Homeland Security Announces New Regulations for Securing High-Risk Chemical Facilities Summary effective 60 days after publication in the Federal Register, the Department The Department of Homeland Security has sought additional comment within plans to impose new requirements on 30 days on one key component of the chemical facilities that possess listed regulations. chemicals above specified quantities, and in many cases will require facilities What Facilities Are Affected? to prepare vulnerability assessments, develop security plans, and implement Under these regulations, the Department and install a suite of security measures. will screen tens of thousands of These requirements could begin to take “chemical facilities” for vulnerability We recommend effect for certain facilities as early as ” to and potential consequences of a June 2007. that all companies terrorist attack, and will regulate that possess or those it determines to be “high-risk.” otherwise handle Background “Chemical facility” is defined broadly as “any establishment that possesses or chemicals review In the four and a half years since the plans to possess, at any point in time, the regulations.“ terrorist attacks of September 11, 2001, a quantity of a chemical substance Congress has debated, but until recently determined by the Secretary to be failed to pass, legislation regulating the potentially dangerous or that meets security of chemical facilities in the US. other risk-related criteria identified On October 4, 2006, the Department by the Department.” A “high-risk” of Homeland Security Appropriations facility is one which, “in the discretion Act of 2007 (the Act) was signed into of the Secretary of Homeland Security, law. -
License Application for International Isotopes, Inc
NRC FORM 313 U.S. NUCLEAR REGULATORY COMMISSION APPROVED BY OMB: NO. 3150-0120 EXPIRES: 1013112005 (4-2004) Estimated burden per response to comply with this mandatory collection request: 7 10CFR 30,32,33, hours. Submittal of the application is necessary to determine that the applicant Is 34,35. 36. 39. and 40 qualified and that adequate procedures exist to protect the public health and safety. Send comments regarding burden estimate to the Records and FOAIAPrivacy Services Brnd chmments(T- US. NuclearRegulatmoaryCommission, Washington, DC 20555-000, or by Internet e-mail to Infocolects@ nrc. go, and to the Desk Officer, Office of InfrmaionandReglatryffarsNEO1 002,(35~0I020), Office of Management APPLICATION FOR MATERIAL LICENSE andaBudget, Washington. DC 20503.lIfa me ans used to impose an Information collection does not display a currently valid OMB control number, the NRC may not conduct or sponsor, and a person is not required to respond to, the Information INSTRUCTIONS: SEE THE APPROPRIATE LICENSE APPLICATION GUIDE FOR DETAILED INSTRUCTIONS FOR COMPLETING APPLICATION. SEND TWO COPIES OF THE ENTIRE COMPLETED APPLICATION TO THE NRC OFFICE SPECIFIED BELOW. APPLICATION FOR DISTRIBUTION OF EXEMPT PRODUCTS FILE APPLICATIONS WITH: IF YOU ARE LOCATED IN: DMSION OF INDUSTRIAL AND MEDICAL NUCLEAR SAFETY IWJNOIS, INDIANA, IOWA, MICHIGAN, MINNESOTA, MISSOURI, OHIO, OR WISCONSIN. SEN) OFFICE OF NUCLEAR MATERIALS SAFETY AND SAFEGUARDS APPLICATIONS TO: U.S. NUCLEAR REGULATORY COMMISSION WASHINGTON. DC 20555-0001 MATERIALS LICENSING BRANCH U.S. NUCLEAR REGULATORY COMMISSION. REGION Ill 2443 WARRENVILLE ROAD. SUITE 210 ALL OTHER PERSONS FILE APPLICATIONS AS FOLLOWS: LISLE, IL 60532R4352 IF YOU ARE LOCATED IN: ALABAMA. -
Appendix a to Part 27
Appendix A to Part 27. – DHS Chemicals of Interest1 - - - WME - - – – Chemical Chemicals of Interest Abstract Synonym (COI) Service (CAS) # y Issue: Theft Theft y Issue: Screening Threshold Threshold Screening EXP/IEDP Issue: Security Sabotage/Contamination Security Issue: Theft Theft Issue: Security CWI/CWP Theft Issue: Security Release: Minimum Minimum Release: (%) Concentration Screening Release: (in Quantities Threshold pounds) Theft: Minimum (%) Concentration Theft: pounds (in Quantities noted) otherwise unless Minimum Sabotage: (%) Concentration Screening Sabotage: Quantities Threshold Release Issue: Security Toxic Release Issue: Security Flammables Release Issue: Security Explosives Securit Acetaldehyde 75-07-0 1.00 10,000 X Acetone cyanohydrin, 75-86-5 ACG APA X stabilized Acetyl bromide 506-96-7 ACG APA X Acetyl chloride 75-36-5 ACG APA X Acetyl iodine 507-02-8 ACG APA X Acetylene [Ethyne] 74-86-2 1.00 10,000 X Acrolein [2-Propenal] or Acrylaldehyde 107-02-8 1.00 5,000 X Acrylonitrile [2-Propenenitrile] 107-13-1 1.00 10,000 X Acrylyl chloride [2-Propenoyl Chloride] 814-68-6 1.00 10,000 X Allyl alcohol [2-Propen-1-ol] 107-18-6 1.00 15,000 X Allylamine [2-Propen-1-amine] 107-11-9 1.00 10,000 X Allyltrichlorosilane, 107-37-9 ACG APA X stabilized Aluminum (powder) 7429-90-5 ACG 100 X Aluminum bromide, 7727-15-3 ACG APA X anhydrous Aluminum chloride, 7446-70-0 ACG APA X anhydrous Aluminum phosphide 20859-73-8 ACG APA X Ammonia (anhydrous) 7664-41-7 1.00 10,000 X 1 The acronyms used in this appendix have the following meaning: ACG -
CSAT Security Vulnerability Assessment Questions
CSAT Security Vulnerability Assessment Questions June 2008 Version 1.0 Version 1.0 1 CSAT SVA Questions OMB PRA # 1670-0007 Expires: 5/31/2011 General ................................................................................................................4 Facility Information.............................................................................................5 Facility Coordinates............................................................................................5 ASP Documents .........................................................................................................................6 Upload Plot Plans/Maps ............................................................................................................8 Facility Security Information............................................................................10 DHS Initial Notification Letter – Security Issues...................................................................10 Release Toxic Chemicals of Interest .....................................................................................12 Release Flammable Chemicals of Interest ............................................................................16 Release Explosive Chemicals of Interest ..............................................................................22 Theft/Diversion Explosive/Improvised Explosive Device Precursor (EXP/IEDP) Chemicals of Interest..................................................................................................................................25 -
SAFETY DATA SHEET According to Regulation (EG) Nr
SAFETY DATA SHEET according to regulation (EG) Nr. 1907/2006 Date of issue: 09.10.2013 Revision date: 28.07.2015 Version: 2.1 1. IDENTIFICATION OF THE SUBSTANCE/MIXTURE AND OF THE COMPANY / UNDERTAKING 1.1 Product identifiers Product name: Germanium tetrafluoride (Ge-72 labelled) EC-No. (non-labelled): 232-011-3 CAS-No. (non-labelled): 7783-58-6 Index No.: --- REACH Registration no.: Not required 1.2 Relevant identified uses of the substance or mixture and uses advised against Identified uses: Chemical, doping of semiconductors. 1.3 Details of the supplier of the safety data sheet Supplier: NUKEM Isotopes GmbH, Industriestrasse 13, 63755 Alzenau, Germany Telephone: +49 (0)6023 91 1726 Telefax: +49 (0)6023 91 1614 Email: [email protected] 1.4 Emergency telephone number 24 hr. Emergency Telephone: +1-703-253-4254 (English / Contract No.: 01009) 2. HAZARDS INDICATION 2.1 Classification of the substance or mixture Classification according to Regulation (EC) No 1272/2008 Gases under pressure, liquefied gas, H280 Acute toxicity, Category 1, inhalation, H330 Skin corrosion, Category 1B, H314 Specific Target Organ Toxicity (repeated exposure), Category 1, H372 For the full text of the H-phrases mentioned in this Section, see Section 2.2. Classification according to directive 67/548/EEG or directive 1999/45/EG T+: Very toxic C: Corrosive R-Phrases: R 26 Very toxic by inhalation R 35 Causes severe burns 2.2 Label elements Labeling according to Regulation (EG) Nr. 1272/2008 The substance is classified and labelled according to the CLP regulation. Hazard statements: GHS04 GHS05 GHS06 GHS07 Safety data sheet for germanium tetrafluoride 1/7 SAFETY DATA SHEET according to regulation (EG) Nr. -
Physical Properties of Chemicals in PAC Revision 27 Listing
LLNL-TR-625492 Physical Properties of Chemicals in PAC Revision 27 Listing M. A. Johnson March 8, 2013 Disclaimer This document was prepared as an account of work sponsored by an agency of the United States government. Neither the United States government nor Lawrence Livermore National Security, LLC, nor any of their employees makes any warranty, expressed or implied, or assumes any legal liability or responsibility for the accuracy, completeness, or usefulness of any information, apparatus, product, or process disclosed, or represents that its use would not infringe privately owned rights. Reference herein to any specific commercial product, process, or service by trade name, trademark, manufacturer, or otherwise does not necessarily constitute or imply its endorsement, recommendation, or favoring by the United States government or Lawrence Livermore National Security, LLC. The views and opinions of authors expressed herein do not necessarily state or reflect those of the United States government or Lawrence Livermore National Security, LLC, and shall not be used for advertising or product endorsement purposes. This work performed under the auspices of the U.S. Department of Energy by Lawrence Livermore National Laboratory under Contract DE-AC52-07NA27344. Physical Properties of Chemicals in PAC Revision 27 Listing 1 Purpose The purpose of this chemical physical property listing is to provide data required to apply the DOE SCAPA Protective Action Criteria (PAC) values to calculation of the LLNL Quantity (Q) Value thresholds for facility chemical hazard classification. This chemical physical property listing based on the DOE SCAPA Protective Action Criteria (PAC) Revision 27 listing Identifies: 1. Physical state at 25°C (i.e. -
CSAT Top-Screen Questions
CSAT Top-Screen Questions January 2008 Version 1.4 CSAT Top-Screen Questions OMB No.1670-0007 Expires: 2/29/2008 General ................................................................................................................3 Facility Name.............................................................................................................................. 4 Facility Description.................................................................................................................... 4 Facility Location......................................................................................................................... 5 Facility Coordinates................................................................................................................... 5 Facility Owner or Operator........................................................................................................ 6 Facility Regulatory Mandates ................................................................................................... 7 EPA RMP Facility Identifier....................................................................................................... 8 Collocated Facility ..................................................................................................................... 9 Additional Facility Information ................................................................................................. 9 Security Vulnerability Assessment (SVA) ............................................................................ -
Chemical Hygiene Plan and Safety Manual 2021
Emergency Telephone Numbers MIT Massachusetts Institute of Technology Department of Chemistry Department of Chemistry Call 100 for emergency assistance in the event of fires, serious injuries, or chemical spills of particularly hazardous substances. Call 2-EHSS during daytime hours for access to Chemical Hygiene Plan the Environmental Health and Safety Office. and Safety Manual Campus Police 617-253-1212 2021 Medical Department Emergencies 617-253-1311 Chemical Hygiene Plan and Safety Manual Medical Department General Information 617-253-4481 http://web.mit.edu/medical/ Operations Center (FIXIT) 617-253-4948 Safety 617-452-3477 http://web.mit.edu/environment/ehs/general_safety.html Industrial Hygiene 617-452-3477 http://web.mit.edu/environment/ehs/chemical_safety.html Biosafety 617-452-3477 http://web.mit.edu/environment/ehs/biosafety.html Radiation Protection 617-452-3477 http://web.mit.edu/environment/ehs/radiation.html Environmental Management 617-452-3477 http://web.mit.edu/environment/ehs/waste.html 2021 Photos courtesy of Andy Ryan Photography and Liz McGrath massachusetts institute of technology department of chemistry Chemical Hygiene Plan and Safety Manual 2021 Professor Troy Van Voorhis Head, Department of Chemistry Chemistry Department Chemical Hygiene and Safety Committee 2021 Professor Rick L. Danheiser, Chair Scott Ide (EHS Coordinator and Chemical Hygiene Officer) Nile Abularrage (Student Member) Professor Stephen Buchwald Hayden Monroe Carder (Student Member) Professor Christopher Cummins Kyan D'Angelo (Student Member) Dr. John Dolhun (Director, Undergraduate Laboratories) Luis Galindo (Laser Biomedical Research Center) Hanna Moon (Student Member) Professor Mohammad Movassaghi Julius Oppenheim (Student Member) Professor Alexander T. Radosevich Professor Ronald T. Raines Jacob Joshua Lee Rodriguez (Student Member) Professor Gabriela Schlau-Cohen Professor Matthew Shoulders Tara Sverko (Student Member) Dr. -
Some Properties of Platinum Pentafluoride and Some
SOME PROPERTIES OF PLATINUM PENTAFLUORIDE AND SOME PROPERTIES OF GERMANIUM DIFLUORIDE by MASUD AKHTAR M.Sc. University of Peshawar, Pakistan, 1962. A THESIS SUBMITTED IN PARTIAL FULFILMENT OF THE REQUIREMENTS FOR THE DEGREE OF MASTER OF SCIENCE in the Department of CHEMISTRY accept this thesis as conforming to the required standard THE UNIVERSITY OF BRITISH COLUMBIA December, 1965. In presenting this thesis in partial fulfilment of the requirements for an advanced degree at the University of British Columbia, I agree that the Library shall make it freely available for reference and study. I further agree that per• mission for extensive copying of this thesis for scholarly purposes may be granted by the Head of my Department or by his representatives„ It is understood that copying or publi• cation of this thesis for financial gain shall not be allowed without my written permission. Department of The University of British Columbia Vancouver 8, Canada Date ii ABSTRACT Platinum pentafluoride has been prepared, by a new preparative method, in a more stable,pure and crystalline form than the material already described. It has been shown, by x-ray powder photography, to be isomorphous with other noble metal pentafluorides and almost isodimensional with rhodium pentafluoride. A tetrameric structural unit like that observed in ruthenium pentafluoride is also assumed for platinum pentafluoride. Its magnetic properties have been shown to be 5 representative of a third transition series d ion in a distorted octahedral environment. The nature of the bonding in germanium difluoride is discussed in the light of the crystal structure, which has been deduced from data obtained from single crystals prepared in this work.; The products of interaction of chlorine or bromine with the difluoride are consistent 19 with the structural findings.