Effect of Inventory Management Practices on the Operational Performance of Manufacturing Firms a Case Study of Mukwano Group of Companies
Total Page:16
File Type:pdf, Size:1020Kb
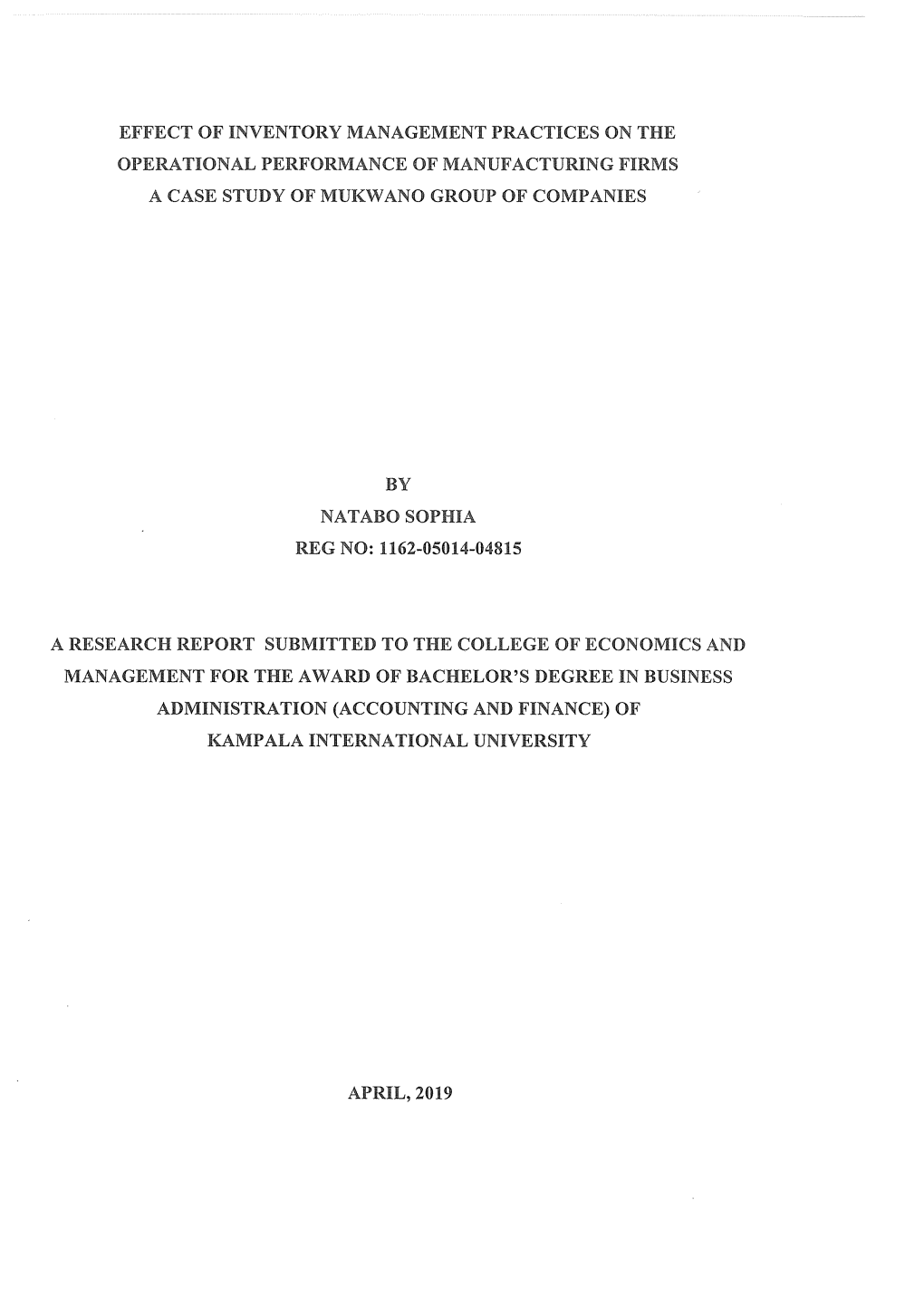
Load more
Recommended publications
-
Ibnul Hasan Rizvi
IBNUL HASAN RIZVI 52/2 6th Commercial Street +923018379551 Phase 4, Defense Housing Authority, [email protected] Karachi, Pakistan SENIOR EXECUTIVE SUMMARY I am an objective driven CEO with hands on experience of profitably managing industrial enterprises employing over thousand people. A highly effective communicator and team leader with a proven record of building trust and long term relationships with both internal and external customers leading to long-term customer satisfaction & retention by focusing on QCD (quality, cost and delivery). SKILLS AND QUALIFICATIONS Implemented and executed learning enterprises, focusing on business processes at cross function level. Focusing on Six Sigma fundamentals: variance reduction and waste reduction in processes achieved lesser defects and increased efficiency. Achieved continuous improvement at all levels of the enterprise by lean manufacturing, implementing TQM, JIT, TPM and problem solving through RCA (root cause analysis). All enterprises I led were certified to ISO9000:2000/2008. Voice of the customer was the prime mover of these organizations. Customer need and desire were collected, analyzed to determine CTQ (critical to quality) attributes. Use of Quality Function Deployment (QFD) tool ensured customers desired attributes in all products and services with performance measures embedded in the process to ensure zero defect supply to customer. PROFESSIONAL EXPERIENCE Medicell Institute of Diabetes Endocrinology & Metabolism, 2015 to Present Medicell Institute of Higher Education & Training, Karachi , Pakistan Chief Executive Officer • Engaged in developing fully trained specialists in various disciplines who would serve as consultants and teachers in their respective fields. • Impart training for IELTS (International English Language Training System). Houston Independent School District, Houston, TX, USA 2009 to 2015 Associate Teacher and Science Teacher • Obtained a Post Baccalaureate in Education from the University of Houston in 2011. -
Inventory Management and Performance of Organisations: a Case Study of Mukwano Group of Companies, Kamp Ala
INVENTORY MANAGEMENT AND PERFORMANCE OF ORGANISATIONS: A CASE STUDY OF MUKWANO GROUP OF COMPANIES, KAMP ALA BY ALI REHEMA SWALEH BSP/34121/112/DF A RESEARCH REPORT SUBMITTED TO THE-COLLEGE OF ECONOMICSAND MAN t\GEMENT AS A PARTIAL REQUIREMENT FOR THE AW ARD OF THE DEGREE OF BACHELORS OF SUPPLIES AND PROCUREMENT MANAGEMENT OF KAMP ALA INTERNATIONAL UNIVERSITY NOVEMBER, 2013 DECLARATION I Ali Rehema Swaleh do hereby declare that the information given in this proposal is entirely my own original work except where acknowledge end that it has not been submitted before to any other University or Institution of higher learning for award of any degree. Signed .................. ~ ........................ ,,,_, Date ... 0.9. ............ rf..O..V..: ..... J..P../3 .......... APPROVAL l Ms Kabasinguzi Christine do hereby confirm and approve that a proposal titled Inventory Management and Performance of Organisations: a case of Mukwano group of companies has been under my supervision and is now ready for submission to Kampala International University. Signed: ~ ................. Date:- .... ~!.i1~~c;,.J.~.<?.(':?. ............ ii DEDICATION This dissertation is dedicated to my beloved parents Mr. & Mrs. Swaleh Ali for their parental care, financial _support, encouragement and advice and to my dear Brothers for the patience they accorded to me when I was pre-occupied with this work. iii ACKNOWLEDGEMENT Thanks to the almighty Allah for the life, opportunities and blessings He has given me. I am deeply indebted to a number of persons and Institutions for the moral, intellectual and material support. I am grateful to my supervisors Ms Kabasinguzi Christine for the inspiration, guidance, encouragement rendered to me during this research. -
Downloads/Press Releases/2014/Jul/Closure- Of-Global-Trust-Bank July-25-2014.Pdf (Last Accessed on 20/8/16)
Home of Parliament Watch Uganda LEGAL ASPECTS OF CENTRAL BANKS’ EMERGENCY RESCUE POWERS IN RESPECT OF DISTRESSED BANKS: LESSONS FOR UGANDA FROM THE SOUTH AFRICAN EXPERIENCE 1 POLICY SERIES PAPERS NUMBER 17 OF 2017 2 Published by CEPA P. O. Box 23276, Kampala Email: [email protected] Web site: http://www.parliamentwatch.ug http://www.cepa.or.ug Silver Kayondo1 Citation Kayondo S, (2017). Legal aspects of central banks’ emergency rescue powers in respect of distressed banks: lessons for Uganda from the South African experience; CEPA Policy Series Papers Number 17 of 2017. Kampala (c) CEPA 2017 All rights reserved. No part of this publication may be reproduced, stored in a retrieval system, or transmitted in any form or by any means – electronic, mechanical, photocopying, recording or otherwise without prior written permission of the publisher. CEPA Policy Series papers are developed and published with the generous grants from Open Society Institute for East Africa. The reproduction or use of this publication for academic or charitable purpose or for purposes of informing public policy is exempted from the restriction. Valuable inputs from Okello Isaac, Programs Associate, CEPA The views expressed in this publication are neither for the Centre for Policy Analysis nor its partners 1 Master of Laws (University of Pretoria, South Africa), Bachelor of Laws (Uganda Christian University, Mukono), Post Graduate Diploma in Legal Practice (Law Development Centre, Kampala). Holder of an Advanced Certificate in International Insolvency and Restructuring under the Auspices of the South African Restructuring and Insolvency Practitioners Association (SARIPA). Advocate of the Courts of Judicature (Uganda). -
East Africa's Family-Owned Business Landscape
EAST AFRICA’S FAMILY-OWNED BUSINESS LANDSCAPE 500 LEADING COMPANIES ACROSS THE REGION PREMIUM SPONSORS: 2 TABLE OF CONTENTS EAST AFRICA’S FAMILY-OWNED BUSINESS CONTENTS LANDSCAPE Co-Founder, CEO 3 Executive Summary Rob Withagen 4 Methodology Co-Founder, COO Greg Cohen 7 1. MARKET LANDSCAPE Project Director 8 Regional Heavyweight: East Africa Leads Aicha Daho Growth Across the Continent Content Director 10 Come Together: Developing Intra- Jennie Forcier Patterson Regional Trade Opens Markets of Data Director Significant Scale Yusra Khadra 11 Interview: Banque du Caire Editorial Manager Lauren Mellows 13 2. FOB THEMES Research & Data Team Alexandria Akena 14 Stronger Together: Private Equity Jerome Amedo Offers Route to Growth for Businesses Laban Bore Prepared to Cede Some Ownership Jessen Chiniven Control Woyneab Habte Mayowa Hambolu 15 Interview: Centum Investment Milkiyas Lekeleh Siyum 16 Interview: Nairobi Securities Exchange Omololu Adeniran 17 A Hire Calling: Merit is Becoming a Medina Mamadou Stronger Factor in FOB Employment Kuringe Masao Melina Matabishi Practices Ivan Matoowa 18 Interview: Anjarwalla & Khanna Sweetness Mathew 21 Interview: CDC Group Plc Paige Arhaus Theodore Angwenyi 22 Interview: Melvin Marsh International Design 23 Planning for the Future: Putting Next- Nuno Caldeira Generation Leaders at the Helm 24 Interview: Britania Allied Industries 25 3. COUNTRY DEEPDIVES 25 Kenya 45 Ethiopia 61 Uganda 77 Tanzania 85 Rwanda 91 4. FOB DIRECTORY EAST AFRICA’S FAMILY-OWNED BUSINESS LANDSCAPE EXECUTIVE SUMMARY 3 EXECUTIVE -
The Inventory Management and Organizational Performance: a Case Study of Mukwano Group of Companies
THE INVENTORY MANAGEMENT AND ORGANIZATIONAL PERFORMANCE: A CASE STUDY OF MUKWANO GROUP OF COMPANIES. BY BAGONZA HILLARY 1153-05084-00772 A RESEARCH REPORT SUBMITTED TO THE COLLEGE OF ECONOMICS AND MANAGEMENT IN PARTIAL FULFILLMENT OF THE REQUIREMENT FOR THE AWARD OF BACHELORS DEGREE OF SUPPLY AND PROCUREMENT MANAGEMENT OF KAMPALA INTERNATIONAL UNIVERSITY. NOVEMBER 2018 DECLARATION This is to declare that this report is my original work and has never been submitted to any other university or institution of higher learning for examination. Signature ~ Date BAGONZA HILLARY 1153-05084-00772 APPROVAL This is to certify that the research of BAGONZA HILLARY whose registration number is 1153-05084-00772 has been under my supervision and it’s now ready to be submitted to the department of Human Resource and Supply Management. Signature Date MR. MASABA RICHARD 11 DEDICATION Special dedication goes to my dearest and loving father Mr. Byaruhanga Mugema Fred and my dearest mother Mrs. Mbabazi Evelyn, brothers and Sister Tumusiime Kennedy, Mugisa Edwin, Byensi Gloria respectively and friends like Wamani Johnson, Isingoma Jackson, for their endless guidance and contribution towards the success of this report may God bless you abundantly. This research is also a dedication to Najjuka Susan and Tibabihanga Harriet for their endless affection and inspirations. 111 ACKNOWLEDGEMENT First and foremost, I thank the Almighty God for giving me strength and courage throughout the period of my studies and for His guidance towards completion of my research. I have a considerable obligation of gratitude to my supervisor Mr. Masaba Richard of Kampala International University, without him this research would have not been possible, his willingness to share knowledge, experience, guidance and encouragement, it was a significant privilege and honor to work with him. -
COMPANY PROFILE1.Cdr
CURRICULUM VITAE & PROFILE FOR SUPER TERRAZZO (U) LTD P. O. BOX. 30669 KAMPALA UGANDA TABLE OF CONTENTS :- 1. STRUCTURE AND ORGANISATION 2. INTRODUCTION OF TERRAZZO 3. INTRODUCTION OF OUR COMPANY 4. TERRAZZO AND THE ENVIRONMENT 5. RESOURCES - KEY TECHNICAL PERSONNEL 6 CURRENT AND ACCOMPLISHED PROJECTS 7. VEHICLES & EQUIPMENT CAPABILITIES 8. FINANCIAL STATUS 9. REGISTRATION DETAILS 10. SITE PHOTOGRAPHS :- TERRAZZO PROJECTS :- CONSTRUCTION PROJECTS Super Profile 1. STRUCTURE AND ORGANISATION NAME OF COMPANY: SUPER TERRAZZO (U) LTD POSTAL ADDRESS : P. O. BOX. 30669 MOBILE NO. 0712 / 772 369089 - 0716 / 0776 647485 EMAIL: [email protected] LOCATION: Plot 194, Kawempe, Bombo Road. Plot 110-112 7th Street, Industrial Area Plot 1659-1661 Bweyogarere, Industrial Park : Specialist in Terrazzo, all type of Flooring works, COMPANY DESCRIPTION and General Construction. Manufacturers of Blocks, Pavers, Road curbs, Paving Slab, Manufacturers of Nails, Razor, Barbed & Binding wires : LEGAL STATUS Limited Liability Company. NAME OF DIRECTORS: Kanji Hirani Raju Hirani Nish Hirani Safari Relly Safari Rally Super Profile 2. INTRODUCTION OF TERRAZZO The name "terrazzo" derives from the Italian word "terrazza" meaning terrace. It is so called because this type of flooring originated in the north eastern region of Italy known as Friuli, where the inhabitants hundreds of years ago utilised pebbles and stones from nearby river beds to pave the earth adjacent to their homes. The surface thus produced was naturally uneven and over time a method was devised for rubbing down the floors. This consisted of a long wooden pole to one end of which was fixed a rough stone weighted to produce the necessary abrasion. -
VODP 2 Annual Report FY 2013 14
The Republic of Uganda VEGETABLE OIL DEVELOPMENT PROJECT- PHASE 2 (VODP 2) ANNUAL PERFORMANCE REPORT (July 2013 – June 2014) Project Management Unit Ministry of Agriculture, Animal Industry and Fisheries KAMPALA JUNE 2014 SUMMARY OF PROJECT INFORMATION IFAD LOAN NO: 806-UG PROJECT NAME: Vegetable Oil Development Project -Phase 2 START DATE: 21st October, 2010 EFFECTIVENESS DATE: May 2012 ORIGINAL PROJECT LIFE: 8 Years CLOSING DATE 21st October, 2018 ii TABLE OF CONTENTS SUMMARY OF PROJECT INFORMATION ....................................................................................................... ii TABLE OF CONTENTS .................................................................................................................................... iii CURRENCY EQUIVALENTS ............................................................................................................................ iv WEIGHTS AND MEASURES ........................................................................................................................... iv ABBREVIATIONS AND ACRONYMS ................................................................................................................ v 1.0. INTRODUCTION ................................................................................................................................. 1 1.1 BACKGROUND ............................................................................................................................... 1 1.2 OUTLINE OF THE REPORT ............................................................................................................. -
Uganda Section 2020
PRESIDENT OF UGANDA UGANDA UGANDA SECTION 2020 EDITION PRESIDENT OF THE REPUBLIC OF UGANDA H.E. YOWERI KAGUTA MUSEVENI East African Manufacturers & Investors Directory East African Manufacturers & Investors Directory 129 UGANDA PROFILE UGANDA UGANDA Uganda Profile ganda officially the Republic of Uganda, is a landlocked country in East Africa. Uganda is bordered to the east by Kenya, to the north by South Sudan, to the west by the Democratic Republic of the Congo, to the southwest Uby Rwanda, and to the south by Tanzania. Uganda is the world’s second most populous landlocked country after Ethiopia. The southern part of the country includes a substantial portion of Lake Victoria, shared with Kenya and Tanzania. Uganda is in the African Great Lakes region. Uganda also lies within the Nile basin, and has a varied but generally a modified equatorial type of climate. Uganda takes its name from the Buganda kingdom, which encompasses a large portion of the south of the country, including the capital Kampala. The people of Uganda were hunter-gatherers until 1,700 to 2,300 years ago, when Bantu- speaking populations migrated to the southern parts of the country. Environment and conservation The Crested crane is the national bird. Conservation in Uganda Uganda has 60 protected areas, including ten national parks: Bwindi Impenetrable National Park and Rwenzori Mountains National Park (both UNESCO World Heritage Sites[43]), Kibale National Park, Kidepo Valley National Park, Lake Mburo National Park, Mgahinga Gorilla National Park, Mount Elgon National Park, Murchison Falls National Park, Queen Elizabeth National Park, and Semuliki National Park. Economy and infrastructure The Bank of Uganda is the central bank of Uganda and handles monetary policy along with the printing of the Ugandan shilling. -
The Contribution of Mukwano Sunflower Scheme to Contracted Small Holder Farmers’ Household Food Availability
The contribution of Mukwano sunflower scheme to contracted small holder farmers’ household food availability A case study of farmers in Ogur sub county, Lira District, Uganda A research project submitted to Van Hall Larenstein University of Applied Sciences in partial fulfillment of the requirements for the Degree of Master in Management of Development, specialization Rural Development and Food Security Emmanuel Ogwal September, 2013 © Copy right Emmanuel Ogwal, 2013 ACKNOWLEDGEMENT This academic journey was hectic and full of surprises. I thank God for fulfilling His promise of granting me life, wisdom, and good health whenever I asked. I want to extend my special thanks to the Dutch government for granting me the unique opportunity to study here in The Netherlands through the Nuffic funding. Further, my sincere thanks also go to Van Hall Larenstein University of Applied Sciences for offering me a place in the master’s course and training me. I would like to thank Dr. Suzanne Nederlof (FS course coordinator), Mr. Eddy Hesselink, and all lecturers that guided and instructed me till completing my studies successfully. Dr. Annemarie Westendorp thank you so much for your motherliness, concern for people and wise counsels. In a special way, my profound appreciation go to my thesis supervisor Dr. Gerrit-Jan van Uffelen for his scholarly guidance, valuable contributions, and tutelage which greatly improved the quality of this work. Indeed many people assisted me in one way or the other. I thank Mr. Peter Ajungu - the Lira District Production and Marketing Officer, Mr. Kizito Odongo, Mr. Robert Adwek of Mukwano group of Companies, and Mr. -
East African Impact Assessment/Case Studies of Selected Farmer to Farmer Hosts Submitted September 1St
East African Impact Assessment/Case Studies of selected Farmer to Farmer Hosts Submitted September 1st 1 Table of Contents: 1 Executive Summary ........................................................................................................... 5 2 Introduction ........................................................................................................................ 7 3 Methodology ...................................................................................................................... 7 4 Kenyan Case Studies.......................................................................................................... 9 4.1 Molo Potato Seed Complex, Agriculture Development Corporation, (ADC) ............ 9 4.1.1 Background: ......................................................................................................... 9 4.1.2 Précis of Initial Assessment: (OCAT) ............................................................... 10 4.1.3 Volunteers visits discussed with hosts ............................................................... 10 4.1.4 Hosts comment to the evaluators on general volunteer impact ......................... 10 4.1.5 Quantifiable and general Impact of a host visit identified by the evaluators..... 11 4.2 Mwea Rice Growers Cooperative Society Limited (MRGM) .................................. 13 4.2.1 Background: ....................................................................................................... 13 4.2.2 Précis of Initial Assessment: (OCAT) .............................................................. -
Ministry of Lands Housing and Urban Development
MINISTRY OF LANDS HOUSING AND URBAN DEVELOPMENT HABITAT III NATIONAL REPORT FINAL REPORT NOVEMBER 2014 TABLE OF CONTENTS LIST OF BOXES...........................................................................................................................................................iii i LIST OF FIGURES....................................................................................................................................................... iv ACRONYMS AND ABBREVIATIONS........................................................................................................................v GLOSSARY................................................................................................................................................................. vii EXECUTIVE SUMMARY......................................................................................................................................... viii 1.0 BACKGROUND AND CONTEXT..................................................................................................................1 2.0 URBAN PLANNING AND DESIGN...............................................................................................................3 2.1 Ensuring Sustainable Urban Planning and Design............................................................................ 3 2.2 Improving Urban Land Management, including addressing Urban Sprawl...........................................5 2.3 Enhancing Urban and Peri-urban Food Production......................................................................... -
Counterfeiting in African Agriculture Inputs – Challenges & Solutions
Counterfeiting in African Agriculture Inputs – Challenges & Solutions Comprehensive Findings This report was prepared for the Bill and Melinda Gates Foundation in collaboration with Monitor Deloitte Bill and Melinda Gates Foundation Team: Walter de Boef, Ben Pierson, and Dan Kim Monitor Deloitte Team: John Mennel, Carl Engle, Pradeep Prabhala, Joel Bryce, Nemo Nemeth, Alyssa Jethani, Aliza Hoffman For more information, contact Walter de Boef at [email protected] or Pradeep Prabhala at [email protected] Table of Contents . Project Plan & Approach . Setting the Context: Counterfeiting in Africa . Value Chain Analysis & Selection . Value Chain Assessments . Ghana: Overview & Existing Initiatives to Address Counterfeiting . Ghana: Herbicide . Ghana: Maize Seeds . Uganda: Overview & Existing Initiatives to Address Counterfeiting . Uganda: Herbicide . Uganda: Maize Seeds . Uganda: Inorganic Fertilizer . Assessment of Technological Environment in Ghana & Uganda . Summary of Solutions . Assessment of Each Solution . Applicability of Solutions . Path Forward & Recommendation - 2 - Project Approach & Key Meetings Opportunity Prioritization Market Research Solution Development (2 weeks) (4 weeks) (3 weeks) Jan 6 – Mon. Jan 22 – Wed. Feb 14 – Fri. Mar 10 – Mon. (Working Group) (Working Group) (BMGF Key Partners) (Working Group) Location: Virtual Location: Virtual Location: Nairobi, Kenya Location: Seattle, WA Official Review of Prioritized Review Findings from Final Review of Solutions Kick Off Value Chains Market Research Align on engagement Review research on Align on findings and Review and align on the objectives and intended context and drivers of insights generated from solutions to reducing outcomes counterfeiting in Africa field work counterfeit agri. inputs in Africa, including costs, Review engagement Review research findings Review the value chain success factors, enabling approach, governance, and analysis on value maps of prioritized value technologies, etc.