Technology of Pulping and Paper Making
Total Page:16
File Type:pdf, Size:1020Kb
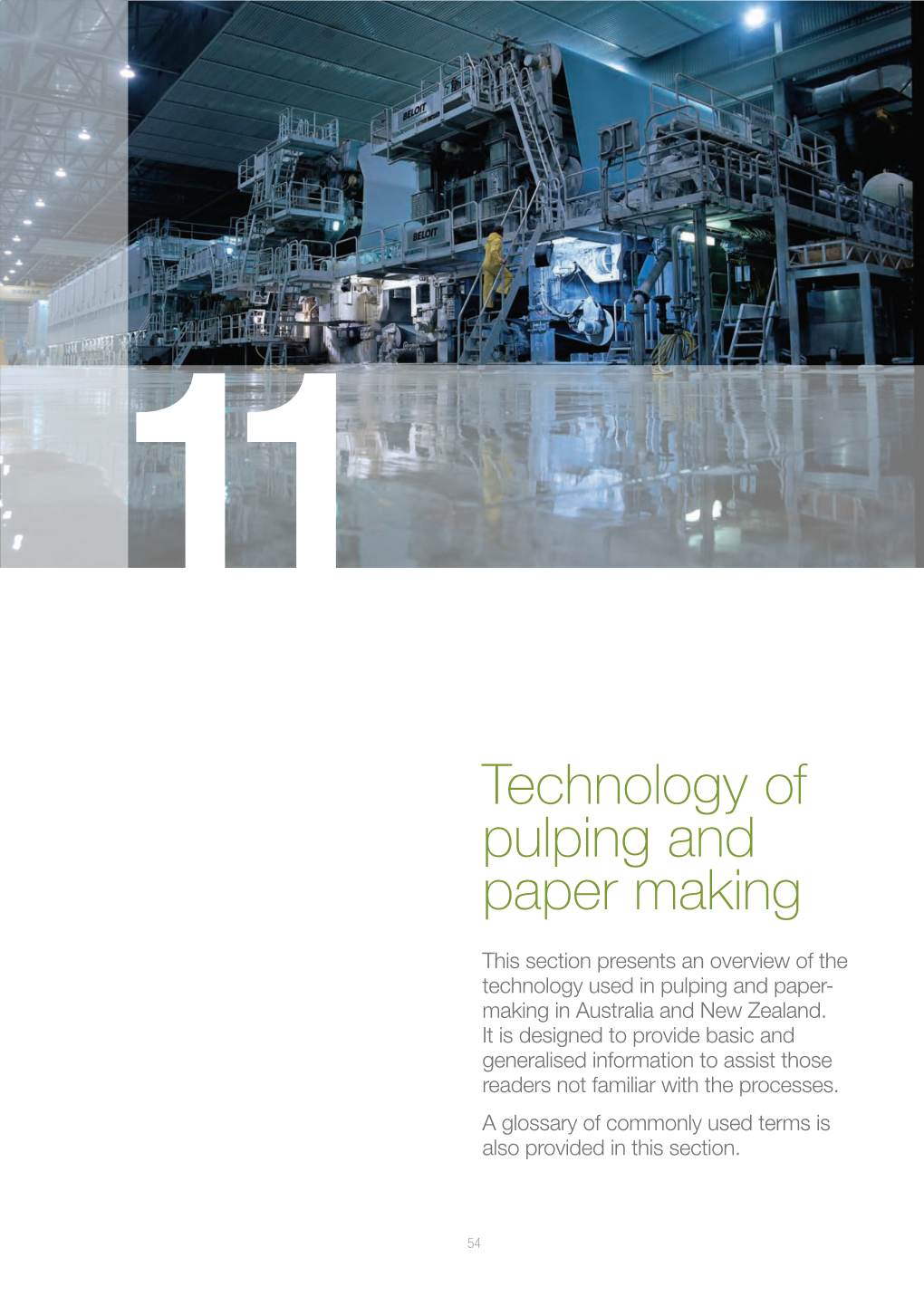
Load more
Recommended publications
-
Understanding Matboard
FRAMING FUNDAMENTALS by Jared Davis, MCPF, GCF Understanding Matboard Being the best frame shop in your area starts with the best products. atboard is a fundamental compo- Mnent of almost every framed pic- ture. However, understanding the vast range of information and choices avail- able in matboards can be daunting. In this article, I aim to provide some useful insights about matboard to help you to dispel some of the myths and decipher some of the facts about this vital aspect of our profession. The two primary purposes for matboard that the introduction of a matboard can in- Different grades of matboard are are to provide protection for the artwork and crease both the size and level of value in the designed for to enhance the framing design. sale of a frame. different appli- cations. Under- 1) Protect. The last consumer survey con- standing which choice to make is ducted by the Professional Picture Fram- How Matboard is Made important to both ers Association found that the num- Matboards are comprised of layers of pa- your customer and your business. ber-one reason why a consumer chose to per of various thickness, laminated together. custom frame an artwork was to protect The papers and core of a matboard are made the item. Preservation, clearly, is of prima- from either unpurified wood pulp, purified al- ry importance to your customer. pha-cellulose wood pulp, or in the case of mu- 2) Enhance. A matboard can help the view- seum-grade board, cotton linter pulp. er to focus correctly on the image. -
Making! the E-Magazine for the Fibrous Forest Products Sector
PAPERmaking! The e-magazine for the Fibrous Forest Products Sector Produced by: The Paper Industry Technical Association Volume 5 / Number 1 / 2019 PAPERmaking! FROM THE PUBLISHERS OF PAPER TECHNOLOGY Volume 5, Number 1, 2019 CONTENTS: FEATURE ARTICLES: 1. Wastewater: Modelling control of an anaerobic reactor 2. Biobleaching: Enzyme bleaching of wood pulp 3. Novel Coatings: Using solutions of cellulose for coating purposes 4. Warehouse Design: Optimising design by using Augmented Reality technology 5. Analysis: Flow cytometry for analysis of polyelectrolyte complexes 6. Wood Panel: Explosion severity caused by wood dust 7. Agriwaste: Soda-AQ pulping of agriwaste in Sudan 8. New Ideas: 5 tips to help nurture new ideas 9. Driving: Driving in wet weather - problems caused by Spring showers 10. Women and Leadership: Importance of mentoring and sponsoring to leaders 11. Networking: 8 networking skills required by professionals 12. Time Management: 101 tips to boost everyday productivity 13. Report Writing: An introduction to report writing skills SUPPLIERS NEWS SECTION: Products & Services: Section 1 – PITA Corporate Members: ABB / ARCHROMA / JARSHIRE / VALMET Section 2 – Other Suppliers Materials Handling / Safety / Testing & Analysis / Miscellaneous DATA COMPILATION: Installations: Overview of equipment orders and installations since November 2018 Research Articles: Recent peer-reviewed articles from the technical paper press Technical Abstracts: Recent peer-reviewed articles from the general scientific press Events: Information on forthcoming national and international events and courses The Paper Industry Technical Association (PITA) is an independent organisation which operates for the general benefit of its members – both individual and corporate – dedicated to promoting and improving the technical and scientific knowledge of those working in the UK pulp and paper industry. -
Cardboard and Brown Paper Bags Office Paper, Newspaper, Junk Mail, Magazines, and Catalogs
Recycling Center 801 Diamond Valley Drive Open: Daily to the public during daylight hours This guide will help you properly prepare your recyclable materials for drop-off at the Town of Windsor Recycle Center. This is a drop-off facility. It does not have a buy-back option and is for use by residents and small businesses. Following this information will help maintain the facility and the recycling program for the benefit of the community. IMPORTANT… • Do not leave your recyclables in plastic bags. Plastic bags are NOT recyclable! • The plastic item must be a BOTTLE or JAR. with a #1 or #2 on the bottom. • 99 percent of these will have a screw-on plastic lid (which isn’t recyclable). • Plastic containers with a #3 - #7 on the bottom are NOT acceptable. • Tubs, buckets, deli plates, microwave/fast food trays, wrappers, Styrofoam, toys, patio furniture, etc. are NOT acceptable. • Plastic bottles larger than 2.5 gallons are NOT acceptable. • Syringes and other medical supplies are NOT acceptable. Cardboard and Brown Paper Bags Corrugated cardboard is easy to recognize. It is made of paper and has an arched layer called “fluting” between smooth sheets called “liners”. The drop-off site has two 40-yard hydraulic compactor units for collecting corrugated cardboard and brown paper bags. The compaction system is self-activated by depositing the prepared materials into a six-inch tall slot. Flatten boxes. Cut or tear large boxes into sections no larger than 4 feet by 4 feet to prevent jamming the machine. No wet, waxed-coated or food-contaminated boxes. -
The Story of Paper, Trees and Printing Is a Product from (Forest in School in Denmark)
William’s grandfather is a fore- ster. He lives in a red house in the The story of forest. Some of his trees shall be harvested and made into paper. But how do you actually make white paper out of 15 meter tall p trees and printing trees with bark and branches? aper How did people invent paper ma- king? What has paper got to do with photosynthesis? How does printing press work? And how to make your own recycled paper? William and his grandpa take a journey into the history of paper, trees, and printing. ”The story of paper, trees, and printing” can be used in science classes’ from grade 4. The book covers paper, forest, forestry, wood, photosynthesis, wood fibres, paper history, recycling, the environment, the climate, paper production, printing press - and much more. The story of paper, trees and printing is a product from www.skoven-i-skolen.dk, (Forest in School in Denmark). English version is available from www.leaf-international.org, Learning about Forests. Malene Bendix Artwork by Eva Wulff The story of trees paperand printing Malene Bendix Graphic Association of Denmark and Forests in School in Denmark. The story of paper, trees and printing Originally published by The Graphic Association of Denmark and Skoven i Skolen (Forest in School in Denmark) 2012. Author: Malene Bendix, Skoven i Skolen (Forest in School in Denmark) Artwork and graphic design: Eva Wulff, Grafisk Tegnestue. Printed version: The original publication in Danish was printed by Kailow Graphic. Kailow Graphic is certified by DS 49001, which is a standard for social responsibility and sustainable business operation. -
Print. Sublimate. Done. Complete Textile Print System
GRAND BY DESIGN Print. Sublimate. Done. COMPLETE TEXTILE PRINT SYSTEM. The Neo Series A revolutionary water-based, dye-sub printer with an on-board calender for permanent sublimation. Get all the details at: printerevolution.com The Neo Series Tap into the digital textile market with a turn-key commercial fabric printing solution. Everything You Need To Succeed In keeping with our mission to drive innovation, PrinterEvolution introduced the Neo Series to be an all-in-one solution for textile printing. The result? A dye-sublimation printer with an on-board sublimation unit. Ink Media options • Achieve a brilliant color gamut with super rich blacks, a • The Neo Series printers can print on standard digital heavy pigment load and excellent grayscale. textile fabrics and specialty materials, such as open weave and stretch. • The vibrant, environmentally friendly, water-based inks pass all OEKO-TEX® Standard 100 certifications. They • Our system easily prints on mesh and other open are produced in an ISO 9001 facility with strict quality weave fabrics without marking the backside with control all at a very competitive cost per print. “blow-by” ink. A specially designed trough is fitted with a sponge and ink pad that absorb any ink that • The Neo Series printers use a 1.5 liter ink system. passes through the fabric. • For stretchable fabrics Superior quality and low cost of operation like Lycra, spandex and other sports textiles, the • The Neo Series utilizes Epson DX Variable Drop heads Neo uses a cork-covered that produce drops of varying sizes and colors within a cylinder to spread and single image file, marrying the best combination of the hold the fabric in place, image quality that comes with small drop sizes and the maintaining perfect, productivity associated with large drop printing. -
Future Directions in Calendering Research
Preferred citation: T.C. Browne and R. H. Crotogino. Future Directions in Calendering Research. In The science of papermaking, Trans. of the XIIth Fund. Res. Symp. Oxford, 2001, (C.F. Baker, ed.), pp 1001–1036, FRC, Manchester, 2018. DOI: 10.15376/frc.2001.2.1001. FUTURE DIRECTIONS IN CALENDERING RESEARCH T.C. Browne and R.H. Crotogino Paprican Pointe-Claire, QC, Canada ABSTRACT Calendering is the papermaker’s last chance to reduce thickness variations along the length and width of the finished sheet, and to improve the sheet smoothness. A smoother sheet results in improved print quality, while more uniform thickness profiles improve the winding process. The calendering operation thus improves the quality of the finished product. In recent years there has been an increase in the loads, speeds and temperatures at which soft-nip calenders, whether on or off line, can be operated without mechanical failure of the cover; the result has been an improvement in the surface and printing properties achievable with mechanical printing grades of paper, and an increase in the production rates which can be sustained. As a result, these calen- ders have slowly replaced traditional machine calenders in new and retrofit installations. The best available design and trouble-shooting tools for modern machine calenders are based on empirical models, whose coefficients have not been related to fundamental paper or fibre properties. New furnishes therefore require experimental deter- mination of these coefficients, and extrapolation to new calender- ing conditions involves some risk. As well, there are no published models, empirical or otherwise, for the design and trouble- shooting of soft-nip calenders, an unfortunate state of affairs given the increased number of installations of these machines. -
Mountain Pine Beetle-Attacked Lodgepole Pine for Pulp and Papermaking
Operational extractives management from- mountain pine beetle-attacked lodgepole pine for pulp and papermaking Larry Allen and Vic Uloth Mountain Pine Beetle Working Paper 2007-15 Natural Resources Canada, Canadian Forest Service, Pacific Forestry Centre, 506 West Burnside Road, Victoria, BC V8Z 1M5 (250) 363-0600 • cfs.nrcan.gc.ca/regions/pfc Natural Resources Ressources naturelles Canada Canada Canadian Forest Service canadien Service des forêts Operational extractives management from mountain pine beetle-attacked lodgepole pine for pulp and papermaking Larry Allen and Vic Uloth Mountain Pine Beetle Initiative W orking Paper 2007œ15 Paprican 3800 W esbrook Mall Vancouver, B.C. V6S 2L9 Mountain Pine Beetle Initiative PO # 8.43 Natural Resources Canada Canadian Forest Service Pacific Forestry Centre 506 W est Burnside Road Victoria, British Columbia V8Z 1M5 Canada 2007 ≤ Her Majesty the Queen in Right of Canada 2007 Printed in Canada Library and Archives Canada Cataloguing in Publication Allen, Larry Operational extractives m anagem ent from m ountain pine beetle-attached lodgepole pine from pulp and paperm aking / Larry Allen and Vic Uloth. (Mountain Pine Beetle Initiative working paper 2007-15) "Mountain Pine Beetle Initiative, Canadian Forest Service". "MPBI Project # 8.43". "Paprican". Includes bibliographical references: p. Includes abstract in French. ISBN 978-0-662-46480-8 Cat. no.: Fo143-3/2007-15E 1. Pulping--British Colum bia--Quality control. 2. Pulping--Alberta--Quality control. 3. Paper m ills-- Econom ic aspects--British Colum bia. 4. Pulp m ills--Econom ic aspects--Alberta. 5. Lodgepole pine--Diseases and pests–Econom ic aspects. 6. Mountain pine beetle--Econom ic aspects. -
Basics of Kraft Pulping
Lignin Wood is composed of many chemical components, primarily extractives, carbohydrates, and lignin, which are distributed nonuniformly as the result of anatomical structure. Lignin is derived from the Latin term lignum, which means wood.1 Anselme Payen (1838) was the first to recognize the composite nature of wood and referred to a carbon- rich substance as the “encrusting material” which embedded cellulose in the wood. Schulze (1865) later defined this encrusting material as lignin. Lignin has been described as a random, three-dimensional network polymer comprised of variously linked phenylpropane units.2 Lignin is the second most abundant biological material on the planet, exceeded only by cellulose and hemicellulose, and comprises 15-25% of the dry weight of woody plants. This macromolecule plays a vital role in providing mechanical support to bind plant fibers together. Lignin also decreases the permeation of water through the cell walls of the xylem, thereby playing an intricate role in the transport of water and nutrients. Finally, lignin plays an important function in a plant’s natural defense against degradation by impeding penetration of destructive enzymes through the cell wall. Although lignin is necessary to trees, it is undesirable in most chemical papermaking fibers and is removed by pulping and bleaching processes. 1.1.1 Biosynthesis Plant lignins can be broadly divided into three classes: softwood (gymnosperm), hardwood (angiosperm) and grass or annual plant (graminaceous) lignin.3 Three different phenylpropane units, or monolignols, are responsible for lignin biosynthesis.4 Guaiacyl lignin is composed principally of coniferyl alcohol units, while guaiacyl-syringyl lignin contains monomeric units from coniferyl and sinapyl alcohol. -
Paper Technology Journal
Paper Technology Journal World paper market: Quo vadis newsprint? News from the Divisions: Stock Preparation, Paper Machinery, Finishing and Service. A Scandinavian Success Story. Notable Startups. Orderbook Highlights. China, changing times in 3 the cradle of papermaking. Contents Foreword 1 Corporate News Highlights USA/Germany: Voith Appleton machine clothing. 55 Startups, orders on hand 2 Austria: World paper market The Andritz Group – partnering the Quo vadis newsprint? 5 pulp and paper industry 58 News from the Divisions Germany: Stock preparation: B+G Fördertechnik thirty years on 64 Membrane technology for the further close-up of paper mill water loops 14 Germany: Board and packaging Paper Machinery: pilot paper machine upgrade – Ortviken PM 4 – facing the future with tomorrow’s technology today 22 versatility 69 Paper Machinery: Latest generation of cylinder mould New names, new addresses formers – FloatLip former N, NO, S 28 Hunt & Moscrop: now Voith Sulzer Paper Machinery: Finishing Ltd., Manchester 72 Serang BM3/BM4 – the exemplary commissioning 30 Voith Sulzer Paper Technology: regional representation in Jakarta 72 Gap Former Technology: No. 26 DuoFormer CFD installation a success 37 Special awards for innovation and design Paper Machinery: New applications in multilayer Neusiedler Paper wins innovation technology 38 award with a revolutionary 3-layer headbox and NipcoFlex press 73 Paper Machinery: Brilliant Coating with JetFlow F – SPCI ’96 – impressive presence 73 data, facts, experience 44 Finishing: Advertisement of the year in Brazil 73 Econip – a new generation of deflection compensating rolls 48 China: Service: The changing origins of GR2 cover – next-generation paper – from hand-made performance leader 51 to machine-made 75 Cover picture: Ortviken – successfull start-up (see article on page 22). -
Corrugated Board Structure: a Review M.C
ISSN: 2395-3594 IJAET International Journal of Application of Engineering and Technology Vol-2 No.-3 Corrugated Board Structure: A Review M.C. Kaushal1, V.K.Sirohiya2 and R.K.Rathore3 1 2 Assistant Prof. Mechanical Engineering Department, Gwalior Institute of Information Technology,Gwalior, Assistant Prof. Mechanical Engineering 3 Departments, Gwalior Engineering College, Gwalior, M. Tech students Maharanapratap College of Technology, Gwalior, [email protected] [email protected] [email protected] ABSTRACT Corrugated board is widely used in the packing industry. The main advantages are lightness, recyclability and low cost. This makes the material the best choice to produce containers devoted to the shipping of goods. Furthermore examples of structure design based on corrugated boards can be found in different fields. Structural analysis of paperboard components is a crucial topic in the design of containers. It is required to investigate their strength properties because they have to protect the goods contained from lateral crushing and compression loads due to stacking. However in this paper complete and detailed information are presented. Keywords: - corrugated boards, recyclability, compression loads. Smaller flutes offer printability advantages as well as I. INTRODUCTION structural advantages for retail packaging. Corrugated board is essentially a paper sandwich consisting of corrugated medium layered between inside II. HISTORY and outside linerboard. On the production side, corrugated In 1856 the first known corrugated material was patented is a sub-category of the paperboard industry, which is a for sweatband lining in top hats. During the following four sub-category of the paper industry, which is a sub-category decades other forms of corrugated material were used as of the forest products industry. -
Articles of Paper Pulp, of Paper Or of Paperboard
Chapter 48 Paper and paperboard; articles of paper pulp, of paper or of paperboard Notes. 1.- For the purposes of this Chapter, except where the context otherwise requires, a reference to “paper” includes references to paperboard (irrespective of thickness or weight per m²). 2.- This Chapter does not cover : (a) Articles of Chapter 30; (b) Stamping foils of heading 32.12; (c) Perfumed papers or papers impregnated or coated with cosmetics (Chapter 33); (d) Paper or cellulose wadding impregnated, coated or covered with soap or detergent (heading 34.01), or with polishes, creams or similar preparations (heading 34.05); (e) Sensitised paper or paperboard of headings 37.01 to 37.04; (f) Paper impregnated with diagnostic or laboratory reagents (heading 38.22); (g) Paper-reinforced stratified sheeting of plastics, or one layer of paper or paperboard coated or covered with a layer of plastics, the latter constituting more than half the total thickness, or articles of such materials, other than wall coverings of heading 48.14 (Chapter 39); (h) Articles of heading 42.02 (for example, travel goods); (ij) Articles of Chapter 46 (manufactures of plaiting material); (k) Paper yarn or textile articles of paper yarn (Section XI); (l) Articles of Chapter 64 or Chapter 65; (m) Abrasive paper or paperboard (heading 68.05) or paper- or paperboard-backed mica (heading 68.14) (paper and paperboard coated with mica powder are, however, to be classified in this Chapter); (n) Metal foil backed with paper or paperboard (generally Section XIV or XV); (o) Articles of heading 92.09; (p) Articles of Chapter 95 (for example, toys, games, sports requisites); or (q) Articles of Chapter 96 (for example, buttons, sanitary towels (pads) and tampons, napkins (diapers) and napkin liners for babies). -
THE REVISION of EU ECOLABEL CRITERIA for Converted Paper Products
THE REVISION OF EU ECOLABEL CRITERIA for Converted Paper Products Draft Preliminary Report Malgorzata Kowalska, Antonios Konstantas, Oliver Wolf Marzia Traverso, Rose Nangah Mankaa, Sabrina Neugebauer November 2018 EUR xxxxx xx 1 This publication is a Science for Policy report by the Joint Research Centre, the European Commission’s in-house science service. It aims to provide evidence-based scientific support to the European policy-making process. The scientific output expressed does not imply a policy position of the European Commission. Neither the European Commission nor any person acting on behalf of the Commission is responsible for the use which might be made of this publication. Contact information Name: Address: E-mail: Tel.: JRC Science Hub https://ec.europa.eu/jrc JRCxxxxx EUR xxxxx xx PDF ISBN xxx-xx-xx-xxxxx-x ISSN xxxx-xxxx doi:xx.xxxx/xxxxxx XX-NA-xxxxx-EN-N Print ISBN xxx-xx-xx-xxxxx-x ISSN xxxx-xxxx doi:xx.xxxxx/xxxxxx XX-NA-xxxxx-EN-C © European Union, 20xx Reproduction is authorised provided the source is acknowledged. How to cite: Authors; title; EUR; doi All images © European Union 20xx, except: 2 Table of contents ABSTRACT ............................................................................................................ 3 Executive summary ............................................................................................... 3 1. Introduction ...................................................................................................... 4 2. Task 1: Scope and definition analysis ..................................................................