US1811020.Pdf
Total Page:16
File Type:pdf, Size:1020Kb
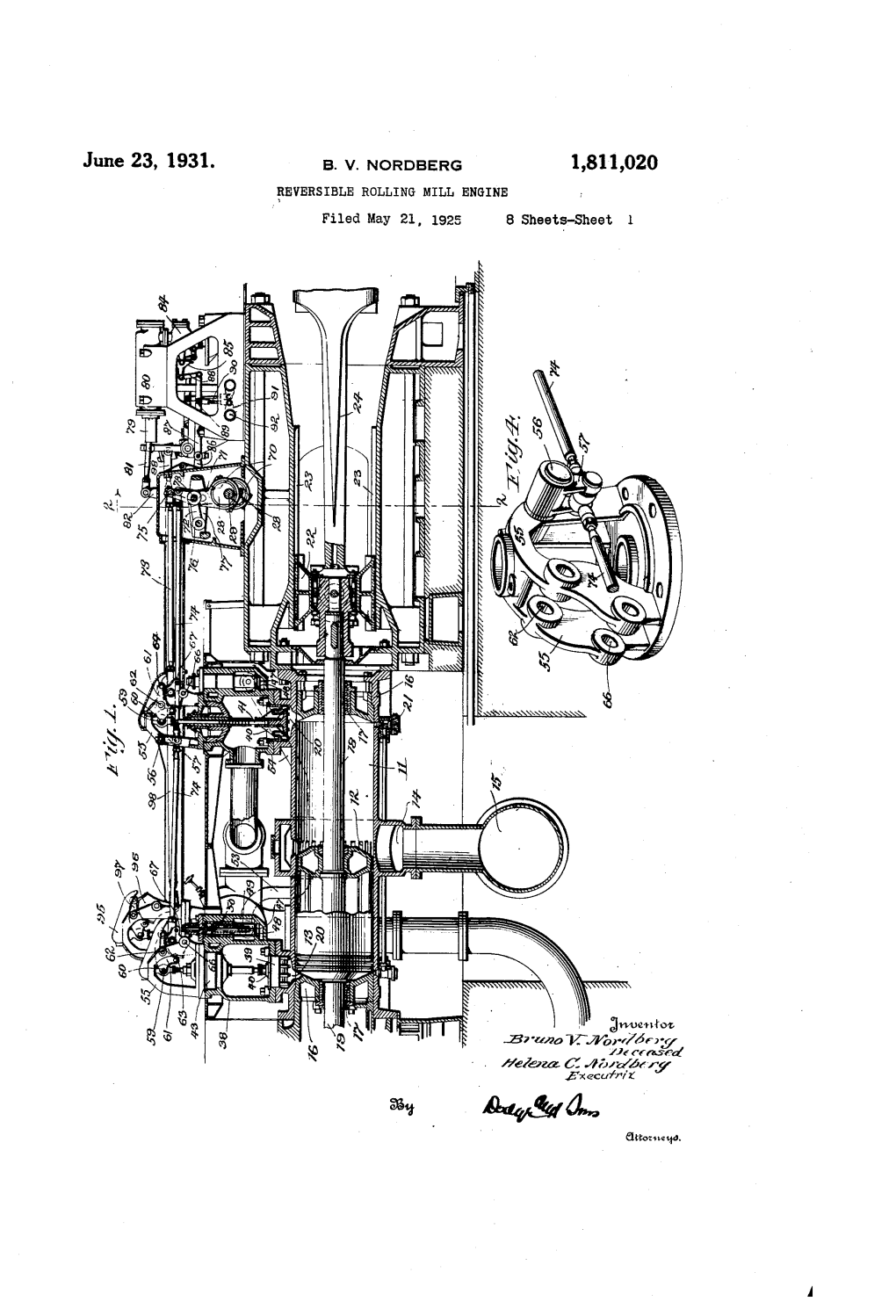
Load more
Recommended publications
-
Walschaerts Valve-Gear 2 Return Cranks with Steel Screws & Nuts
This pack contains the following parts: - Walschaerts Valve-Gear 2 Return Cranks with steel screws & nuts. 2 Expansion links with bushes & This kit contains parts to construct 2BA nuts. a set of Walschaerts type valve- 2 Lifting arms with grub screws & Allen key. gear as used on ROUNDHOUSE 2 Lifting links. locomotives. It is of a simplified 4 M2 steel screws & nuts. design, which does not use a 6 5BA steel washers. combination lever and is intended 2 Radius rods. for use with the ROUNDHOUSE 2 Weigh shaft brackets 1 Weigh shaft. Cylinder set. 2 Starlock washers 2 Roll pins. NOTE:- Frames, Cylinders, 6 Short crank pins. Coupling Rods, Connecting Rods, 2 Plain crank pins Axles and Outside Cranks are not included with this set of parts. 1 Push Rod Connector, Screw & Starlock. 1 Stainless Steel spring & Long Crank Pin. 1 Reversing lever handle. 1 Reversing lever base. 3 M2 screws and nuts. 2 M3 mounting screws. 1 Steel push rod & quicklink connector. Roundhouse Engineering Co. Ltd 2 Eccentric rods. Units 6 to 9, Churchill Business Park, Churchill Road, Wheatley, Doncaster. DN1 2TF. England. Tel 01302 328035 Fax 01302 761312 Email: [email protected] www.roundhouse-eng.com 1 Walschaerts Valve-Gear Part Number WVG Assembly of Walschaerts type valve-gear 1). Radius Rod. 2). Lifting Link. 3). Lifting Arm. Diagram4). Expansion showing Linkgeneral Bush. arrangement 5). Weigh of Walschaerts Shaft Bracket valve (Penguin). gear. NOTE:- Frames, Coupling rods, connecting rods and outside cranks are not included6). Weigh with this Shaft. set of 7). parts. Starlock Washer. 8). 2BA Nut. -
Lima 2-8-0 “Consolidation”, Developed for TS2013, by Smokebox
Union Pacific 4000 Class 4884-1 "Big Boy" circa 1948-49 Developed by Smokebox TM for Dovetail Games' Train Simulator © Smokebox 2021, all rights reserved Issue 1 Union Pacific 4000 Class 4884-1 "Big Boy" Steam Locomotive Page 2 Contents Introduction ....................................................................................................................................................... 7 32- and 64-bit TS ................................................................................................................................................ 7 Expert or Simple Controls mode, HUD and Automatic Fireman ....................................................................... 7 "All-in-one" .................................................................................................................................................... 7 Standard TS Automatic Fireman .................................................................................................................... 8 F4 HUD ........................................................................................................................................................... 8 High Detail (HD) and Standard Detail (SD) ........................................................................................................ 8 Recommended Settings ..................................................................................................................................... 9 Cab Layout ...................................................................................................................................................... -
Engine Base Timing
Front Gear Assembly Configuration Two front gear train combinations are presently utilized on the Signature™, ISX, and QSX15 engines. Signature™, ISX3, ISX2, and QSX15 engines use a scissor gear for the lower idler gear and the injector cam gear. ISX1 does not use a scissor gear at the idler location. ISX2 engines built between January 1999, and January 2000, utilize a scissor gear for the lower idler gear only. The injector cam gear is a straight cut spur gear, similar to the ISX1. After January, 2000, the ISX2 has scissor gears for both the cam and lower idler. This procedure describes the removal, inspection, and installation of the different gear combinations. Front Gear Assembly without Scissor Gear View shown is from left to right and top to bottom. Valve camshaft gear Injector camshaft gear Adjustable idler gear Lower idler gear Accessory gear Crankshaft gear. 1 of 28 5/20/17, 2:06 PM Front Gear Assembly with Scissor Gear View shown is from left to right and top to bottom. Valve camshaft gear Injector camshaft scissor gear Adjustable idler gear Lower idler scissor gear Accessory gear Crankshaft gear. Scissor Gear Definitions Do not attempt to remove any gears before reading scissor gear definitions. Serious personal injury or engine damage can result if instructions are not followed. The following terms describe the conditions of the scissor gears for removal, installation, and operation. Unloaded The gear will be unloaded when removing, installing, and setting gear backlash. Unload the gear by backing out two gear adjusting screws until the gear teeth align. The idler scissor gear is loaded when the gear backlash is set. -
Cyclically Operating Valves for Machines Or Engines
CPC - F01L - 2021.01 F01L CYCLICALLY OPERATING VALVES FOR MACHINES OR ENGINES Definition statement This place covers: • Valve-gear or valve arrangements, e.g. lift-valve gear; • Lift-valve, i.e. cut-off apparatus with closure members having at least a component of their opening and closing motion perpendicular to the closing faces; • Slide valve-gear or valve-arrangements; • Valve-gear or valve arrangements actuated non-mechanically; • Valve arrangements in working piston or piston-rod; • Modifications of valve-gear to facilitate reversing, braking, starting, changing compression ratio, or other specific operations; • Valve-gear or valve arrangements, e.g. with reciprocatory slide valves, other than provided for in groups; • Slide valve-gear or valve arrangements with cylindrical, sleeve, or part annularly-shaped valves surrounding working cylinder or piston; • Slide valve-gear or valve arrangements with reciprocatory and other movement of same valve, e.g. longitudinally of working cylinder and in cross direction • Use of working pistons or pistons-rods as fluid-distributing valves or a valve-supporting elements, e.g. in free-piston machines • Valves controlled by impact by piston, e.g. in free-piston machines; Drive, or adjustment during the operation, or distribution or expansion valves by non-mechanical means; • Distribution or expansion valve-gear peculiar to free-piston machines or engines; • Reversing gear Valve drive, valve adjustment during operation; • Rotary or oscillatory slide valve-gear or valve arrangements, specially adapted -
United States Patent [19], [11] Patent Number: 4,736,717 Fujikawa Et Al
United States Patent [19], [11] Patent Number: 4,736,717 Fujikawa et al. [45] Date of Patent: Apr. 12, 1988 [54] VALVE GEAR FOR FOUR-CYCLE ENGINE [56] References Cited " _ _ U.S. PATENT DOCUMENTS [75] Inventors: 351:: 1319;??? Egi’iii?uyukl 386,213 7/1888 Nash ......... .. 123/901 3 ’ 1 ’ "n ’ 779,328 1/1905 Svebilios 123/901 Kalmgwa, all Of Japan 1,248,597 12/1917 Baker ........... .. 123/901 1,409,710 3/1922 Haltenberger ................... .. 123/902 [73] Ass1gnee: JKasgilllsakl Jukogyo Kabushlkl Kaisha, Primary Examiner_lra s_ Lazarus [57] ABSTRACT [21] Appl. No.: 848,206 A valve gear for a four-cycle engine having an over hung crankshaft connecting with an output shaft, [22] Filed; AP“ 4, 1936 wherein a guide portion having such a shape folding the output shaft as to return back to a starting point in two . turns, is formed on the output shaft, and an interlocking [30] Forelgn Apphcatlon Pmmty Data mechanism guided by the guide portion is provided to APR 4, 1935 [JP] Japan - 60-71716 open the valves for the four-cycle engine. It is prefera F?‘b. 17, 1986 Japan ................................ .. 61-32539 ble that the guide pol-fig“ is formed as cam face displac ing the interlocking mechanism. The guide portion can [51] Int, (11,4 _ _ _ . _ _ _ , _ _ _ _ _ _ _ , , _ _ _ _ ,, F01L 1/04 be formed on a block other than the output shaft for [52] US. Cl. .......................... .. 123/90.2; l23/90.6 easy machining and also for adjustable valve timing. -
Engine Reversing When Running at Manoeuvring Speeds
09 REVERSING Part I - General Diesel engines intended for the propulsion of ship fitted with neither a controllable pitch propeller nor a reversing gearbox are made in direct reversing form. Astern running involves carrying out the events of the cycle in the reverse order, i.e. altering the timing of valves and fuel pumps to cause them to start the engine in the opposite direction and then continue its operating cycle in this direction. Fill in the missing word Part I - General Diesel engines intended for the propulsion of ship fitted with neither a ________________ nor a reversing gearbox are made in ________________ form. ________________ involves carrying out the events of the cycle in the reverse order, i.e. altering the _____________ and fuel pumps to cause them to start the engine in the opposite direction and then continue its ________________ in this direction. Using the diagram below describe the timing of a two-stroke diesel engine The propeller thrust must be reversible in order to do manoeuvring of a ship. Usually manoeuvring is done while entering a port or leaving a port. In case of a controllable pitch propeller an unidirectional engine is sufficient. In case of limited power systems like medium speed engines of high speed engines, clutches and reverse gears may be used. But in large diesel engines, the main engines must be reversible and should be able to produce thrust efficiently in both the directions ( ahead and astern ) To reverse an engine the engine cycle may require re-timing. Large diesel engines have scavenge ports which controls the scavenge timing. -
ON a NEW REVERSING and EXPANSIVE VALVE-GEAR. The
418 AUGUST1880. ON A NEW REVERSING AND EXPANSIVE VALVE-GEAR. - BY MR. DAVID- JOY, OF LONDON. The Reversing and Expansive Valve-Motion, which is the subject of the present paper, was originally drawn out by the writer in a crude state, but possessing all its present elements, in the year 1868-9 ; and has since been, at different times, the subject of frequent investigation and experiment on his part. In 1877 he made it a special study, first working it out on paper, and afterwards testing all the movements and positions by means of models. And thus, passing through innumerable forms under the correction of various errors of action, it has ended in the arrangement which is now submitted to the Institution. In passing, the writer may call attention to the fact, that this is only one of the many instances where inventions are the result of a long course of work, followed in a given and definite direction, and with a special end in view. It thus helps to disprove the theory of opponents of the patent system, who rather characterise inventions as lucky chances, which men of scheming brains fall upon without expecting it. A few such cases do occur, just to give colour to this statement ; but even these generally happen to men who have been working laboriously on some kindred subject. In the writer’s case, as an engineer, his attention has been specially directed by circumstances, and perhaps partly by, taste, to the question of the movement of the valves in steam and other engines. -
Full Page Photo
THE LIFE AND TIMES OF A DUKE Martyn J. McGinty AuthorHouse™ UK Ltd. 500 Avebury Boulevard Central Milton Keynes, MK9 2BE www.authorhouse.co.uk Phone: 08001974150 © 2011. Martyn J. McGinty. All rights reserved No part of this book may be reproduced, stored in a retrieval system, or transmitted by any means without the written permission of the author. First published by AuthorHouse 04/25/2011 ISBN: 978-1-4567-7794-4 (sc) ISBN: 978-1-4567-7795-1 (hc) ISBN: 978-1-4567-7796-8 (e) Front Cover Photo: Th e Duke at Didcot (Courtesy P. Treloar) Any people depicted in stock imagery provided by Th inkstock are models, and such images are being used for illustrative purposes only. Certain stock imagery © Th inkstock. Th is book is printed on acid-free paper. Because of the dynamic nature of the Internet, any web addresses or links contained in this book may have changed since publication and may no longer be valid. Th e views expressed in this work are solely those of the author and do not necessarily refl ect the views of the publisher, and the publisher hereby disclaims any responsibility for them. Born out of Tragedy and Riddles, his lineage traceable, unerasable, back through the great houses of Chapelon, Giffard, Stephenson, Belpaire and Watt, the Duke was laid to rust by the sea, a few meagre miles from the mills that shaped the steel that formed the frames that bore the machine that Crewe built. Time passed and the Duke was made well again by kindly strangers. -
Patent Model Index
Smithsonian Institution Scholarly Press smithsonian contributions to history and technology • n u m b e r 5 4 Smithsonian Institution Scholarly Press PatentA Chronology Models Index of MiddleGuide to Missouri the Collections of Plains the NationalVillage Museum of AmericanSites History, Smithsonian Institution Volume 1: Listings by Patent NumberBy Craig and M. InventionJohnson Name with contributions by Stanley A. Ahler, Herbert Haas, and Georges Bonani Barbara Suit Janssen SerieS PublicationS of the SmithSonian inStitution Emphasis upon publication as a means of “diffusing knowledge” was expressed by the first Secretary of the Smithsonian. In his formal plan for the Institution, Joseph Henry outlined a program that included the following statement: “It is proposed to publish a series of reports, giving an account of the new discoveries in science, and of the changes made from year to year in all branches of knowledge.” This theme of basic research has been adhered to through the years by thousands of titles issued in series publications under the Smithsonian imprint, com- mencing with Smithsonian Contributions to Knowledge in 1848 and continuing with the following active series: Smithsonian Contributions to Anthropology Smithsonian Contributions to Botany Smithsonian Contributions to History and Technology Smithsonian Contributions to the Marine Sciences Smithsonian Contributions to Museum Conservation Smithsonian Contributions to Paleobiology Smithsonian Contributions to Zoology In these series, the Institution publishes small papers -
Steam. ENGINE VÁLVE REVERSENG, GEAR. 1,684,228
Sept., ll, 1928. - __ __ . ' 1,684,228 * . J. KINDERVATER sTEAM. ENGINE VÁLVE REVERSENG, GEAR. i Filled July 19, 1923 2 Sheets-Sheet l l sept. 11, 1928. 1,684,228 “ J. KINDERVATER STEAM ENGINE VALVE REVERSING GEAR Filed July 19, 1923 2 Sheets-Sheet 2 S S SA Pa?elate: Sept. 1, 1928. 1,684,228 UNITED STATES PATENT OFFICE. JUS KINDERWATEER, OF NEW YoRK, N. Y. sTEAM-ENGINE VALVE REVERSING GEAR. Application filed July 19, 1923. Serial No. 852,542. My invention relates to power actuated re ing Cylinder, 3, is supported on the boiler of the locomotive, and is closed, at its ends, by versing gear for steam orother fluid pressure removable heads, 3º. A properly packed pis engines, more, particularly those of locomo ton, 4, is fitted in the cylinder, and is secured tives, ?dits objectis to provide an appliance On a piston rod, 4°, which passes through the g ofexpensivé such type construction which will beand of readysimple applica and in rear head of the cylinder and projects into a bility in connection with valve gears of any casing, 8º, which is secured thereto and is of the various standard constructions, and in closed at its outer, end. The piston rod is the operation of which, positive and acgurate of rectangular section, and a rack, 4P, is cut on one of its sides. The admission and ex 26 adjustment will be attained, and creeping be haust of motive fluid, which may be either fully prevented. O p steam Qr compressed air, to and from oppo Thè improvement claimed is hereinafter site ends of the cylinder, 3, is controlled by an fully set forth. -
Steam Engine Collection
STEAM ENGINE COLLECTION The New England Museum of Wireless And Steam Frenchtown Road ~ East Greenwich, R.I. International Mechanical Engineering Heritage Collection Designated September 12, 1992 The American Society of Mechanical Engineers INTRODUCTION It has been said that an operating steam engine is ‘visual music’. The New England Museum of Wireless and Steam provides the steam engine enthusiast, the mechanical engineer and the public at large with an opportunity to experience the ‘music’ when the engines are in steam. At the same time they can appreciate the engineering skills of those who designed the engines. The New England Museum of Wireless and Steam is unusual among museums in its focus on one aspect of mechanical engineering history, namely, the history of the steam engine. It is especially rich in engines manufactured in Rhode Island, a state which has had an influence on the history of the steam engine in the United States out of all proportion to its size and population. Many of the great names in the design and manufacture of steam engines received their training in Rhode Island, most particularly in the shops of the Corliss Steam Engine Co. in Providence. George H. Corliss, an important contributor to steam engine technology, founded his company in Providence in 1846. Engines that used his patent valve gear were built in large numbers by the Corliss company, and by others, both in the United States and abroad, either under license or in various modified forms once the Corliss patent expired in 1870. The New England Museum of Wireless and Steam is particularly fortunate in preserving an example of a Corliss engine built by the Corliss Steam Engine Company. -
3600 Marine Engine Application and Installation Guide
® 3600 Marine Engine Application and Installation Guide ● Ancillary Equipment LEKM8470 8-98 ® Ancillary Equipment Marine Gears Couplings Torsional Limits Propellers Fixed Pitch Controllable Pitch Marine Gears between the shafting, gearbox, and main engines. Collision chocks are normally Reversing marine gears are used: fitted at the corners of the gearbox mounting flange to maintain alignment • To match relatively small, economical in the event of an accident. medium speed engines to the low propeller rpm necessary for high Care should be taken in selecting the efficiency. capacity of the low speed output bearing. • To reverse the propeller rotation for It must be capable of carrying loads the non-reversing 3600 Family of imposed by the line shaft or tail shaft Engines. directly connected to the low speed coupling. Advise the gear manufacturer Marine gears are selected to transmit if a propeller blade actuating box is to be rated engine horsepower (plus overload mounted on the gearbox, or if auxiliary if required) at rated rpm. Design the equipment is to be driven from power gear to meet appropriate classification takeoffs on the gear housing. society rules. Inspection and Certification may be required. Advise Carefully review the final arrangement the gear manufacturer of expected of the gearbox in the engine room for the adverse conditions, such as operation in best overall installation. Space must be ice. available for service and maintenance. The following are examples of typical Main engine marine gears are normally arrangements used with the 3600 single or double reduction, with the ratio Family of Engines: of input and output speeds selected to meet the propeller design rpm.