Attorney Aug
Total Page:16
File Type:pdf, Size:1020Kb
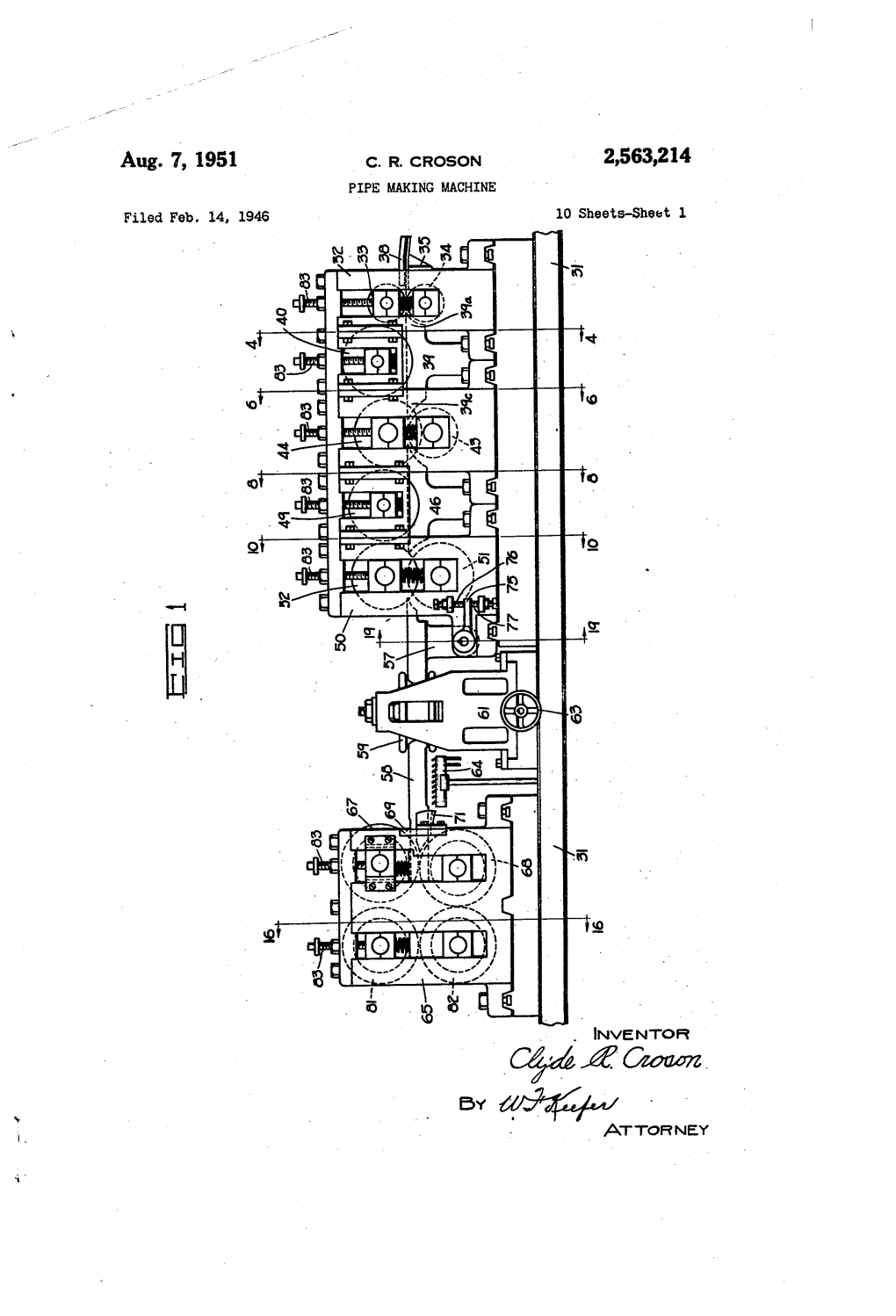
Load more
Recommended publications
-
National Register of Historic Places Multiple Property
NFS Form 10-900-b 0MB No. 1024-0018 (Jan. 1987) United States Department of the Interior National Park Service National Register of Historic Places Multipler Propertyr ' Documentation Form NATIONAL This form is for use in documenting multiple property groups relating to one or several historic contexts. See instructions in Guidelines for Completing National Register Forms (National Register Bulletin 16). Complete each item by marking "x" in the appropriate box or by entering the requested information. For additional space use continuation sheets (Form 10-900-a). Type all entries. A. Name of Multiple Property Listing ____Iron and Steel Resources of Pennsylvania, 1716-1945_______________ B. Associated Historic Contexts_____________________________ ~ ___Pennsylvania Iron and Steel Industry. 1716-1945_________________ C. Geographical Data Commonwealth of Pennsylvania continuation sheet D. Certification As the designated authority under the National Historic Preservation Act of 1966, as amended, J hereby certify that this documentation form meets the National Register documentation standards and sets forth requirements for the listing of related properties consistent with the National Register criteria. This submission meets the procedural and professional requiremerytS\set forth iri36JCFR PafrfsBOfcyid the Secretary of the Interior's Standards for Planning and Evaluation. Signature of certifying official Date / Brent D. Glass Pennsylvania Historical & Museum Commission State or Federal agency and bureau I, hereby, certify that this multiple -
University Micrdfilms International 300 N
INFORMATION TO USERS This reproduction was made from a copy of a document sent to us for microfilming. While the most advanced technology has been used to photograph and reproduce this document, the quality of the reproduction is heavily dependent upon the quality of the material submitted. The following explanation of techniques is provided to help clarify markings or notations which may appear on this reproduction. 1. The sign or “target” for pages apparently lacking from the document photographed is “Missing Page(s)” . If it was possible to obtain the missing page(s) or section, they are spliced into the film along with adjacent pages. This may have necessitated cutting through an image and duplicating adjacent pages to assure complete continuity. 2. When an image on the film is obliterated with a round black mark, it is an indication of either blurred copy because of movement during exposure, duplicate copy, or copyrighted materials that should not have been filmed. For blurred pages, a good image of the page can be found in the adjacent frame. If copyrighted materials were deleted, a target note will appear listing the pages in the adjacent frame. 3. When a map, drawing or chart, etc., is part of the material being photographed, a definite method of “sectioning” the material has been followed. It is customary to begin filming at the upper left hand corner of a large sheet and to continue from left to right in equal sections with small overlaps. If necessary, sectioning is continued again—beginning below the first row and continuing on until complete. -
Section-Xv 608 Chapter-72 Section Xv Base Metals And
SECTION-XV 608 CHAPTER-72 SECTION XV BASE METALS AND ARTICLES OF BASE METAL NOTES : 1. This Section does not cover : (a) prepared paints, inks or other products with a basis of metallic flakes or powder (headings 3207 to 3210, 3212, 3213 or 3215); (b) ferro-cerium or other pyrophoric alloys (heading 3606); (c) headgear or parts thereof of heading 6506 or 6507; (d) umbrella frames or other articles of heading 6603; (e) goods of Chapter 71 (for example, precious metal alloys, base metal clad with precious metal, imitation jewellery); (f) articles of Section XVI (machinery, mechanical appliances and electrical goods); (g) assembled railway or tramway track (heading 8608) or other articles of Section XVII (vehicles, ships and boats, aircraft); (h) instruments or apparatus of Section XVIII, including clock or watch springs; (ij) lead shot prepared for ammunition (heading 9306) or other articles of Section XIX (arms and ammunition); (k) articles of Chapter 94 (for example, furniture, mattress supports, lamps and lighting fittings, illuminated signs, prefabricated buildings); (l) articles of Chapter 95 (for example, toys, games, sports requisites); (m) hand sieves, buttons, pens, pencil-holders, pen nibs, monopods, bipods, tripods and similar articles or other articles of Chapter 96 (miscellaneous manufactured articles); or" (n) articles of Chapter 97 (for example, works of art). 2. Throughout this Schedule, the expression “parts of general use” means : (a) articles of headings 7307, 7312, 7315, 7317 or 7318 and similar articles of other base metal; (b) springs and leaves for springs, of base metal, other than clock or watch springs (heading 9114); and (c) articles of headings 8301, 8302, 8308, 8310 and frames and mirrors, of base metal, of heading 8306. -
Glossary of Oilfield Production Terminology (GOT) (DEFINITIONS and ABBREVIATIONS)
Glossary of Oilfield Production Terminology (GOT) (DEFINITIONS AND ABBREVIATIONS) FIRST EDITION, JANUARY 1, 1988 American Petroleum Institute 1220 L Street, Northwest Washington, DC 20005 Issued by AMERICAN PETROLEUM INSTITUTE Production Department FOR INFORMATION CONCERNING TECHNICAL CONTENTS OF THIS PUBLICATION CONTACT THE API PRODUCTION DEPARTMENT, 2535 ONE MAIN PLACE, DALLAS, TX 75202-3904 – (214) 748-3841. SEE BACK SIDE FOR INFORMATION CONCERNING HOW TO OBTAIN ADDITIONAL COPIES OF THIS PUBLICATION. Users of this publication should become familiar with its scope and content. This publication is intended to supplement rather than replace individual engineering judgment. OFFICIAL PUBLICATION REG U.S. PATENT OFFICE Copyright 1988 American Petroleum Institute TABLE OF CONTENTS Page FOREWORD 2 SECTION 1: LIST OF PUBLICATIONS 3 SECTION 2: ABBREVIATIONS AND DEFINITIONS 5 FOREWORD A. This publication is under the jurisdiction of the API Executive Committee on Standardization of Oilfield Equipment and Materials. B. The purpose of this publication is to provide standards writing groups access to previously used abbreviations and definitions. Standards writing groups are encouraged to adopt, when possible, the definitions found herein. Attention Users of this Publication: Portions of this publication have been changed from the previous edition. The location of changes has been marked with a bar in the margin. In some cases the changes are significant, while in other cases the changes reflect minor editorial adjustments. The bar notations in the margins are provided as an aid to users to identify those parts of this publication that have been changed from the previous edition, but API makes no warranty as to the accuracy of such bar notations. -
A Guide to Water Well Casing and Screen Selection
A Guide To Water Well Casing and Screen Selection A Note About Roscoe Moss Company Roscoe Moss Company, publisher of this guide, has been engaged in the development of ground water since the 1890's. Originating as a water well drilling contractor operating in the Southwest, the firm has constructed thousands of wells throughout the United States and in ten foreign countries. In 1926, Roscoe Moss began the manufacture of water well casing and screens. Emphasis on the development of these products has brought the company to the forefront of specialists in the marketing of these materials. Completing its uniqueness as a firm engaged in all phases of ground-water development, Roscoe Moss has an active interest in two large California water utilities serving 1.8 million people. Included in their supply sources are over 500 high capacity water wells. The material contained in this pamphlet is in based on a broad practical knowledge of water well design, construction, operation and maintenance, as well as steel products manufacture. These resources are enhanced by an ongoing systematic research and evaluation program. We are pleased to share the information following, some of which represents proprietary company knowledge and has never before been published. A Guide To Water Well Casing and Screen Selection Table of Contents 1.0..INTRODUCTION ...............................…....................................................... 4 2.0 METHODS OF WELL CONSTRUCTION ...…............................................ 6 2.1 Cable Tool ................................................…..................................... -
Large Diameter Carbon and Alloy Steel Line Pipe from China and Japan
A-272 A-272 CANADA BORDER SERVICES AGENCY NON-CONFIDENTIAL COMPLAINT The Dumping and Subsidizing of Certain Welded Large Diameter Carbon and Alloy Steel Line Pipe Originating in or Exported from The People's Republic of China and the Dumping of Certain Welded Large Diameter Carbon and Alloy Steel Line Pipe Originating in or Exported from Japan Submitted By: EVRAZ Inc. NA Canada February 5, 2016 CASSIDY LEVY KENT (CANADA) LLP Suite 1470, 55 Metcalfe Street Ottawa, Ontario KIP 6L5 Tel: (613)368-4170 Fax: (613) 368-4171 Christopher J. Kent Christopher J. Cochlin Christopher R.N. McLeod Michael Milne Hugh Seong Seok Lee Susana May Yon Lee Solicitors for EVRAZ Inc. NA Canada NON-CONFIDENTIAL Table of Contents 1. Identification of the Complainant ........................................................................................ ! 2. Imported Goods ..................................................................................................................... 2 A. Product Description .......................................................................................................... 2 B. Product Characteristics and Product Use .......................................................................... 2 C. Production Process ............................................................................................................ 4 D. Tariff Classification .......................................................................................................... 7 E. Countries of Export .......................................................................................................... -
II. Manufacture of Barrel
STS.001 Prof. Merritt Roe Smith NOTES ON FILM ENTITLED "GUNSMITH OF WILLIAMSBURG," with Wallace Gusler (Colonial Williamsburg Foundation, 1969) I. Firing a flintlock rifle II. Manufacture of barrel: A. Material: wrought iron, starting with 3-inch skelp. B. Forging the barrel: -- welding the skelp by hand/hammer; -- starts weld at middle and works toward ends; -- several hundred heats need to finish weld; -- annealing (slow cooling welded barrel in charcoal powder) C. Boring barrel (by hand powered and controlled machine: no water or steam power used) -- a semi-mechanized operation (boring rod pushed through barrel by hand); -- 12 to 15 rough boring bits used; -- bits frequently break and need to be repaired; -- gravity feed (using lead weight) used in later/lighter boring operations; -- straightening barrel (by eye and copper hammer) -- finish boring with square bit, using wood shims to enlarge bit (barrel pushed by hand through barrel). D. Filing outer surface of barrel -- a long tedious process executed by hand and skill of eye; -- polished with emery paper (by hand). E. Rifling barrel --executed by machine, but powered by hand; -- note spiral guide on machine that imparts groove turns in barrel; -- cutter pulled through barrel; -- 8 to 10 passes used in rifling, each with slightly larger shim to deepen cut of rifling bit in barrel. F. Forging the breech plug and barrel tang (by hand). G. Cutting/threading breech-plug screw (by hand). H. Drilling touch hole with hand drill; _C� 1_I___I___ ____ I. Barrel proof -- proof charge uses four times more gunpowder than regular guns. -- barrel inspected for cracks, etc. -
6. Gun Barrels 99 6
Historical Overview 6. Gun Barrels 99 6. Gun Barrels Literature Durdik, Jan, Alte Feuerwaffen, Hanau, 1977, DuJa Hoff, Arne, Feuerwaffen II, Läufe, Braunschweig, 1969, HoAr Historical Overview Early The oldest known gun barrels were made of bronze in the beginning of the barrels 14th century. They had large cast bores that were sometimes made conically. From the middle of the same century, iron barrels are known to have been forged from rods. Some of them already had a cylindrical bore. It is assumed Iron Rod th Barrels that at the beginning of the 15 century, the quality of the bore was improved by reaming. Breech In the beginning, the rear parts of the barrel bores of handguns were closed Plugs with a forged in plug. As early as the beginning of the 15th century, threaded breech plugs were used. Later, the barrel smiths added a top strap to the breech plug to attach the barrel to the stock. Skelp- In the middle of the 15th century, barrels forged from iron bands wrapped in Barrels screw fashion around a mandrel, replaced the barrels made from iron rods. These barrels also called skelp barrels were the direct predecessors of the European Damascus barrels. Compared to the Damascus barrels, they have however, a weak structure. Blunder- Towards the end of the 16th century, the first tromblon barrels that would make buss loading easier, appeared. They were also believed, to have a wider spreading Barrels when multiple bullets were used. With certainty then, just as now, a large muzzle was more intimidating than a small one. -
No. 863,477. PATENTED AUG, 18, 1907. G
No. 863,477. PATENTED AUG, 18, 1907. G. H. WHITE. APPARATUS FOR WELDING RINGS, &0, APPLICATION FILED JAN, 30, 1906. 3. SHEETS-SBE r - see- INVENTOR 4ttorneya No. 863,477, PATENTED AUG, 18, 1907. G. H. WHITE, APPARATUS FOR WELDING RINGS, &0, APPLICATION FILED JAN, 30, 1908, 2. SHEETS-SEE 2. 2424Ee Ea. M d WWF/ENTOR WITNESSES: 3. M1 ski.fier. UNITED STATES PATENT OFFICE. GEORGE HENRY WHITE, OF OIL CITY, PENNSYLVANIA, AssIGNOR. To s. R. DRESSER MANUFACTURING COMPANY, OF BRADFORD, PENNSYLVANIA. APPARATUSFORWELDINGRINGs, &c. No. 863,477. Specification of Letters Patent. Fatented Aug. 13, 1907. Application filed January 30, 1906, Serial No. 298,729, To all whom it may concern: Be it known that I, GeoRGE HENRY WHITE, a citizen on one face and which has its lateral edges beveled or of the United States, residing at Oil City, in the county inclined inwardly toward the beaded face. A blank of Venango and State of Pennsylvania, have invented cut from such a skelp is shown at A, Fig. 6, provided certain new and useful Improvements in Apparatus with the bead a and beveled edges a? a”. In forming for Welding Rings and Like Articles; and I do hereby this blank into a ring the blank is bent with the bead 60 declare the following to be a full, clear, and exact de inside, and the ends which are cut parallel and inclined 'sciption of the invention, such as will enable others to the faces of the blank are lapped slightly to facilitate skilled in the art to which it appertains to make and the welding operation, as shown in Fig. -
(12) United States Patent (10) Patent No.: US 6,817,633 B2 Brill Et Al
USOO6817633B2 (12) United States Patent (10) Patent No.: US 6,817,633 B2 Brill et al. (45) Date of Patent: Nov. 16, 2004 (54) TUBULAR MEMBERS AND THREADED 2,150,221. A * 3/1939 Hinderliter ............... 285/332.3 CONNECTIONS FOR CASING DRILLING 2,205,697 A * 6/1940 Scharpenberg .............. 285/237 AND METHOD 2,211,173 A 8/1940 Shaffer ............. ... 285/146 2.812,025 A 11/1957 Teague et al. .... ... 166/207 (75) Inventors: Leland M. Brill, Hughes Spring, TX 3,397,745 A 8/1968 Owens et al. - - - - - - - - - - - - - - - - - 166/57 (US); Bluford W. Lowery, Linden, TX 3,463,228 A 8/1969 Hearn .... ... 166/181 s vis 3,489.437 A 1/1970 Duret ..... ... 285/55 (US); Edmond L. Miller, Bowie 3,508,771. A 4/1970 Duret ......................... 285/334 County, TX (US) (List continued on next page.) (73)73) ASSigneeAssi : lesLOne Starar. Steel Cuompany, Dallas,Lallas, TX FOREIGN PATENT DOCUMENTS WO 99/18328 4/1999 ........... E21B/23/01 (*) Notice: Subject to any disclaimer, the term of this patent is extended or adjusted under 35 OTHER PUBLICATIONS U.S.C. 154(b) by 24 days. American Petroleum Institutes, “Specification for Thread ing, Gauging, and Thread Inspection of Casing, Tubing, and (21) Appl. No.: 10/325,050 Line Pipe Threads (U.S. Customary Units).” API Specifica (22) Filed: Dec.e 20,a Vs 2002 tion Standard 5B, Fourteenth Edition, 30 pages, 8/96. (65) Prior Publication Data (List continued on next page.) US 2004/0118569 A1 Jun. 24, 2004 Primary Examiner Eric K. Nicholson 2 (74) Attorney, Agent, or Firm-Baker Botts L.L.P. -
Cost Problems in the Wrought Iron Industry Carl G
University of Mississippi eGrove Publications of Accounting Associations, Societies, Accounting Archive and Institutes 1923 Cost problems in the wrought iron industry Carl G. Jensen Follow this and additional works at: https://egrove.olemiss.edu/acct_inst Recommended Citation Jensen, Carl G., "Cost problems in the wrought iron industry" (1923). Publications of Accounting Associations, Societies, and Institutes. 81. https://egrove.olemiss.edu/acct_inst/81 This Article is brought to you for free and open access by the Accounting Archive at eGrove. It has been accepted for inclusion in Publications of Accounting Associations, Societies, and Institutes by an authorized administrator of eGrove. For more information, please contact [email protected]. N a tio n a l Association of C ost A ccountants Affiliated with The Canadian Society of Cost Accountants Official Publications Vol. IV JAN. 2, 1923 No. 8 Cost Problems in the Wrought Iron Industry BUSH TERMINAL BUILDING 130 W EST 42nd ST RE E T. N EW Y O R K N atio n a l Association of C ost A ccountants Affiliated with The Canadian Society of Cost Accountants Official Publications Vol. IV JAN. 2, 1923 No. 8 Cost Problems in the Wrought Iron Industry BUSH TERMINAL BUILDING 130 W EST 42nd ST RE E T, N EW Y O R K NATIONAL ASSOCIATION OF COST ACCOUNTANTS Affiliated with The Canadian Society of Cost Accountants Official Publications Vol. IV, No. 8 January 2, 1923 Cost Problems in the Wrought Iron Industry CARL G. JENSEN, COMPTROLLER A. M. Byers Company, Pittsburgh, Pa. BUSH TERMINAL BUILDING 130 W EST 42nd STREET, NEW YORK CITY The National Association of Cost Account ants does not stand sponsor for views expressed by the writers of articles issued as Publications. -
NRA 24 Annual Meetings & Exhibits
In This Issue 3 Offhand Shots from the Editor 28 6 34 12 20 40 2017 NRA 24 Annual Meetings & Exhibits Articles: Email your articles to GCA [email protected] FELLOWSHIP Submissions and Contributions: We welcome you to submit articles, stories, and Send in your articles, photos for publication in Hot Brass. GCA pays for submissions and contributions jokes, tips, hints, stories, with "AGI Bucks." These coupons are redeemable dollar-for-dollar towards the shooting activities, purchase of any AGI product or AGI video course. We pay for stories and articles we pictures, recipes, - print by the word: 100-300 words = 20 AGI Bucks, 300-500 words = 50 AGI Bucks, all those things you 500+ words = 100 AGI Bucks. Articles and stories must be submitted in MS Word or tell your friends . MS publisher format. Photos: Electronic photos must be submitted in a jpeg format Let’s share it with with a resolution of at LEAST 640x480. Print photos are accepted but GCA cannot return the world. any printed photos and all submitted photos will become the property of GCA. ©Copyright GCA 2017. All rights reserved. Hot Brass Magazine is published and produced by GCA and distributed to GCA Members. No part of this magazine may be copied, reproduced, rented, or transmitted for any reason without the written permission of the copyright holder. Contacting GCA: GCA, 351 Second Street, Napa, CA 94559, 1-800-435-GCOA (4262), Fax 707-253-2150, www.GunClubOfAmerica.com Subscriber Information: Missing or Damaged Issues: If an issue of Hot Brass is lost in the mail or arrives damaged, simply contact GCA at 1-800-435-GCOA (4262) for a replacement.