Chiller Replacement
Total Page:16
File Type:pdf, Size:1020Kb
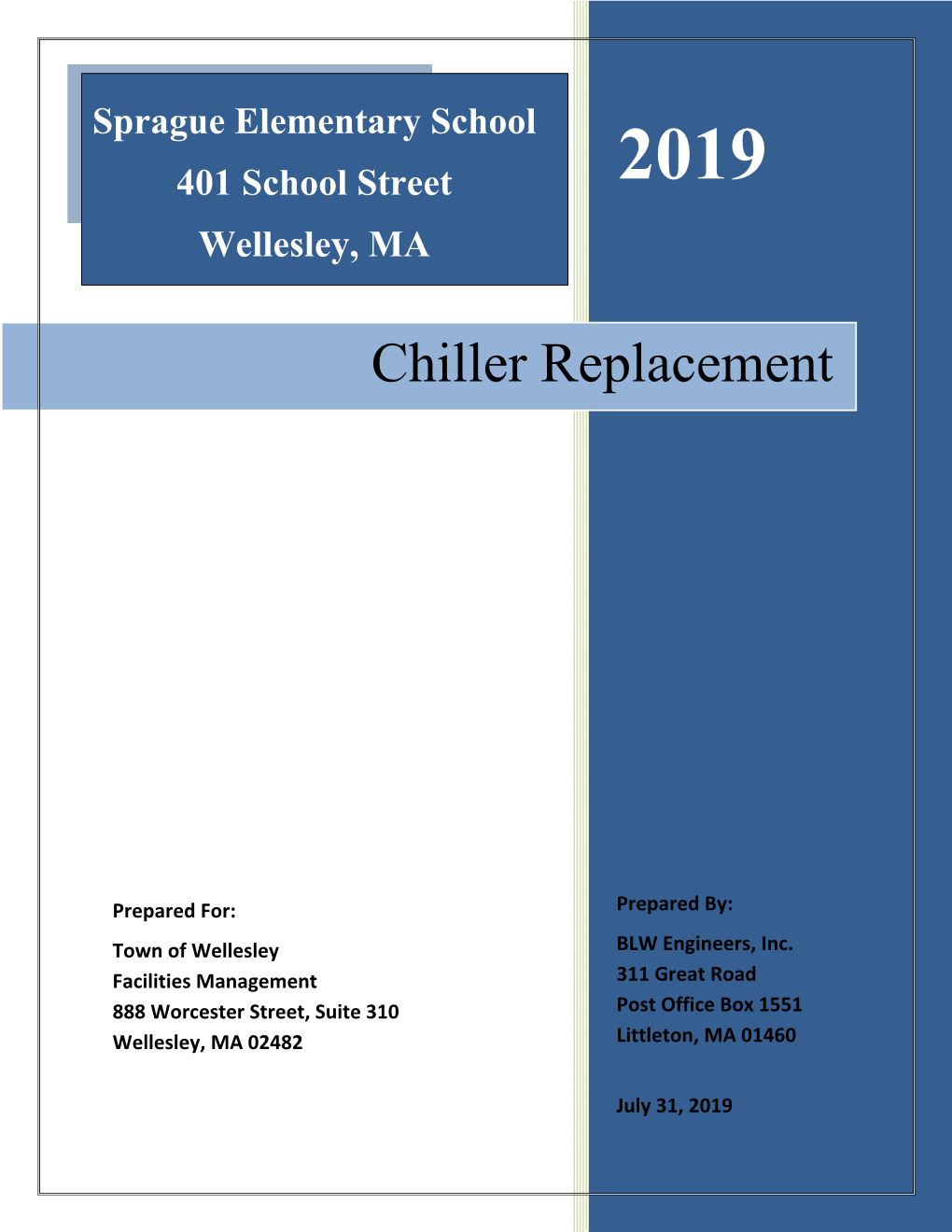
Load more
Recommended publications
-
Overview of Chiller Compressors
Overview of Chiller Compressors Course No: M04-027 Credit: 4 PDH A. Bhatia Continuing Education and Development, Inc. 22 Stonewall Court Woodcliff Lake, NJ 07677 P: (877) 322-5800 [email protected] OVERVIEW OF CHILLER COMPRESSORS Overview In HVAC industry, the refrigeration machine that produces chilled water is referred to as a “Chiller”. A chiller package operates either on the principles of vapor compression or vapor absorption. The vapor compression system uses mechanical energy in the form of electric motor to drive the cooling cycle whereas absorption chillers use heat to drive the process. The vapor compression chiller system, which is far more prominent in commercial buildings, consists of four major components: the compressor, evaporator, condenser and expansion device all packaged as a single unit. The classification of vapor compression chiller packages is generally by the type of compressor: centrifugal, reciprocating, and screw being the major ones. Chillers are the largest consumer of energy in a commercial building and it is therefore important to understand the relative benefits and limitations of various types in order to make the right economic decisions in chiller installation and operation. This course will talk about the type of compressor used in the water cooled chiller. The course is divided into 3 parts: Part - I: Types of Chiller Compressors Part – II: Comparison of Chiller Compressors Part –III: Economic Evaluation of Chiller Systems PART I - TYPES OF CHILLER COMPRESSORS Most cooling systems, from residential air conditioners to large commercial and industrial chillers, employ the refrigeration process known as the vapor compression cycle. At the heart of the vapor compression cycle is the mechanical compressor. -
4. Hvac and Refrigeration System
4. HVAC AND REFRIGERATION SYSTEM Syllabus HVAC and Refrigeration System: Vapor compression refrigeration cycle, Refrigerants, Coefficient of performance, Capacity, Factors affecting Refrigeration and Air conditioning system performance and savings opportunities. Vapor absorption refrigeration system: Working principle, Types and comparison with vapor compression system, Saving potential 4.1 Introduction The Heating, Ventilation and Air Conditioning (HVAC) and refrigeration system transfers the heat energy from or to the products, or building environment. Energy in form of electricity or heat is used to power mechanical equipment designed to transfer heat from a colder, low-ener- gy level to a warmer, high-energy level. Refrigeration deals with the transfer of heat from a low temperature level at the heat source to a high temperature level at the heat sink by using a low boiling refrigerant. There are several heat transfer loops in refrigeration system as described below: Figure 4.1 Heat Transfer Loops In Refrigeration System In the Figure 4.1, thermal energy moves from left to right as it is extracted from the space and expelled into the outdoors through five loops of heat transfer: – Indoor air loop. In the leftmost loop, indoor air is driven by the supply air fan through a cool- ing coil, where it transfers its heat to chilled water. The cool air then cools the building space. – Chilled water loop. Driven by the chilled water pump, water returns from the cooling coil to the chiller’s evaporator to be re-cooled. – Refrigerant loop. Using a phase-change refrigerant, the chiller’s compressor pumps heat from the chilled water to the condenser water. -
How Does a Recirculating Chiller Do Heating?
How does a Recirculating Chiller do Heating? Mitchell Howard, Technical Manager March 2019 © Applied Thermal Control 2019 What is this guide for? To explain how ATC’s chillers can heat as well as cool. • Heat of compression adds energy to refrigerant • Act of compression itself causes temperature to rise. • Electrical energy input to compressor enters refrigerant through conduction as refrigerant circulates. • Hot Gas Bypass (HGB) capacity control • Instead of allowing hot gaseous refrigerant to pass into the condenser to do conventional refrigeration, it is redirected into the evaporator via a discharge bypass valve (DBV or HGBV). 2 © Applied Thermal Control 2019 Reverse-Carnot Cycle Thermodynamic model used when chiller cools. 6 5 4 7 1. Compressor suction port draws refrigerant in. 2. Compression increases pressure and heat. 3. Sensible cooling begins at the condenser. 4. Sensible cooling completed; state change starts. 3 5. State change in condenser –constant temp and pressure 6. Latent cooling completed; further sensible cooling to point 7 ensures liquid supply. This is subcooling. 7. Expansion process begins at the inlet to TEV. 8 2 8. Expansion is achieved by reducing pressure through a Pressure tiny orifice. Low pressure and temperature seen at outlet. 9. Inlet to evaporator provided with refrigerant already going 9 1 through state change. 10. Boiling (evaporation) process continues in the evaporator. 11. Liquid cannot be compressed; additional sensible heating 10 11 applied before gaseous refrigerant can enter compressor. This is known as superheat. Heat Content (Enthalpy) (Energy per unit Mass) 3 © Applied Thermal Control 2019 Why does a compressor heat? Due to isentropic compression and electric motor inefficiency. -
AAON Chiller Controls
www.AAON.com CHILLER CONTROLS The AAON Chiller Controllers are designed to maximize the capabilities of the AAON LF, LN, and LZ Series premium performance chiller products. These chiller controls are designed, engineered, and supported by AAON. Benefits • Sequences Fully Tested to Ensure High Performance Operation • Part of the Orion Controls System, compatible with AAON VCCX2 Rooftop Unit Controller • Prism 2 Software Interface for setup and configuration • LCD Displays on the Main Chiller Controller and Associated Modules for Status and Diagnostics • Factory Installed Touch Screen PC Interface is Available for Large Chiller Systems • BTL Certified BACnet MS/TP Interface AAON DESIGNED, ENGINEERED AND SUPPORTED CHILLER CONTROLS CHILLER CONTROLLER FEATURES The AAON Controllers can control chillers and outdoor mechanical rooms with pumping packages, waterside economizers, boilers, and vestibule conditioning. Each Chiller Main Controller and associated Modules have an LCD display for Status and Diagnostics, works with Prism 2 Software for full setpoint and configuration, and is BTL BACnet MS/TP certified. INCLUDED ON AAON EQUIPMENT LF SERIES CHILLER º LF Chiller Controls used with On/Off and Variable Capacity Scroll Compressor Systems LF CHILLER CONTROLLER º DX Barrel Chiller Controls used with VFD Controlled Compressor Systems LF CHILLER CONTROLLER LN SERIES CHILLER º DX Barrel Chiller Controls used with STANDARD FEATURES VFD Controlled Compressor Systems º Controls 1 or 2 Circuit DX Chillers LZ SERIES CHILLER - Single or Tandem Compressors -
District Energy Enters the 21St Century
TECHNICAL FEATURE This article was published in ASHRAE Journal, July 2015. Copyright 2015 ASHRAE. Posted at www.www.burnsmcd.com .org. This article may not be copied and/or distributed electronically or in paper form without permission of ASHRAE. For more information about ASHRAE Journal, visit www.ashrae.org. District Energy Enters The 21st Century BY STEVE TREDINNICK, P.E., MEMBER ASHRAE; DAVID WADE, P.E., LIFE MEMBER ASHRAE; GARY PHETTEPLACE, PH.D., P.E., MEMBER ASHRAE The concept of district energy is undergoing a resurgence in some parts of the United States and the world. Its roots in the U.S. date back to the 19th century and through the years many technological advancements and synergies have developed that help district energy efficiency. This article explores district energy and how ASHRAE has supported the industry over the years. District Energy’s Roots along with systems serving groups of institutional build- District energy systems supply heating and cooling ings, were initiated and prospered in the early decades to groups of buildings in the form of steam, hot water of the 1900s and by 1949 there were over 300 commercial or chilled water using a network of piping from one or systems in operation throughout the United States. Of more central energy plants. The concept has been used course, systems in the major cities of Europe also gained in the United States for more than 140 years with the favor in Paris, Copenhagen and Brussels. In many cases first recognized commercial district energy operation district steam systems were designed to accept waste originating in Lockport, N.Y. -
Expert Chiller and Boiler Repair and Servicing Is an EMCOR Services
Chiller & Boiler Services -Customized preventive CHILLER AND BOILER maintenance programs SERVICE AND REPLACEMENT: -Chiller services and retrofits -Boiler and burner repair Expert chiller and boiler and maintenance -Cooling tower replacements repair and servicing is an and upgrades -Design/Build EMCOR Services Aircond specialty. -Automated Controls -Water Treatment With decades of expertise, from the waterside to the controls, our factory- trained and state-certified chiller and boiler technicians are equipped to perform emergency service, preventive, and contract maintenance and repairs for all commercial and industrial properties to help maintain reliable operation of their equipment. Chiller Service and Replacement When properly maintained, chillers not only provide critical comfort needs to the people and the equipment in the buildings but also help reduce your operation costs through increased energy efficiency when properly maintained. EMCOR Services Aircond’s EPA and factory-certified experts are your resource for comprehensive, high-quality chiller services. And since we’re brand neutral, we have vast experience servicing machines from all manufacturers. Our services include: » Centrifugal Chillers » Refrigerant conversion » Water/Air-Cooled Screw Chillers » Retubing » Scroll Air-Cooled Chillers » System & equipment retrofits By combining the proper chemicals with experienced technical services, we » Reciprocating Chillers » Tube cleaning help keep your cooling systems free of » Absorption Chillers » Non-destructive testing, including: corrosion and mineral deposits, as well » Medical Chillers - Eddy current tube analysis as bacteriological and organic fouling. » Chiller Rentals - Infrared scanning The result is maximum performance, » Refrigerant Management - Refrigerant analysis reliability and value. » Cooling Towers - Spectrographic oil analysis » Refrigeration - Vibration analysis » Process Piping Boiler Service and Replacement Consider servicing, upgrading or replacing your boilers to eliminate any possible downtime. -
Solar Cooling Used for Solar Air Conditioning - a Clean Solution for a Big Problem
Solar Cooling Used for Solar Air Conditioning - A Clean Solution for a Big Problem Stefan Bader Editor Werner Lang Aurora McClain csd Center for Sustainable Development II-Strategies Technology 2 2.10 Solar Cooling for Solar Air Conditioning Solar Cooling Used for Solar Air Conditioning - A Clean Solution for a Big Problem Stefan Bader Based on a presentation by Dr. Jan Cremers Figure 1: Vacuum Tube Collectors Introduction taics convert the heat produced by solar energy into electrical power. This power can be “The global mission, these days, is an used to run a variety of devices which for extensive reduction in the consumption of example produce heat for domestic hot water, fossil energy without any loss in comfort or lighting or indoor temperature control. living standards. An important method to achieve this is the intelligent use of current and Photovoltaics produce electricity, which can be future solar technologies. With this in mind, we used to power other devices, such as are developing and optimizing systems for compression chillers for cooling buildings. architecture and industry to meet the high While using the heat of the sun to cool individual demands.” Philosophy of SolarNext buildings seems counter intuitive, a closer look AG, Germany.1 into solar cooling systems reveals that it might be an efficient way to use the energy received When sustainability is discussed, one of the from the sun. On the one hand, during the time first techniques mentioned is the use of solar that heat is needed the most - during the energy. There are many ways to utilize the winter months - there is a lack of solar energy. -
District Cooling Concepts Applied in China.”
“District Cooling Concepts applied in China.” Bernt Andersson District Cooling 2016 a Climate Solution Dubai, November 2016 [email protected] District Cooling Very limited development of District Cooling systems, first systems developed early 2000; Standard approach for cooling is split units for apartments and building or block level chilled water plants; Indoor design temperature is +26 C (77 F) For District Cooling systems a combination of compression chillers, absorption chillers and Ice Thermal Energy Storage are common; Almost all District Cooling plants with Ice Thermal Energy Storage have dual duty, single evaporator chillers and large heat exchangers between the glycol circuit and chilled water circuit for day time operation as well as heat exchangers between the Ice Thermal Energy Storage and the chilled water circuit; In almost all cases where both District Heating and District Cooling are developed the pipe network is two pipe system that are used for heat supply in winter and cooling supply in the summer; [email protected] Mean Monthly Temperature Climate Zones Coldest Hottest Severe Cold ≤ -10 °C ≤ 25 °C Cold -10–0 °C 18–28 °C Temperate 0–13 °C 18–25 °C Hot Summer and Cold Winter 0–10 °C 25–30 °C Hot Summer and Warm Winter > 10 °C 25–29 °C Source: Berkely Labs [email protected] Compression Chillers with Ice Thermal Energy Storage Concepts Best Practice Dual duty chillers with two evaporators where the chilled water evaporator is connected in series with the directly connected Thermal -
Overview of Vapor Absorption Cooling Systems
Overview of Vapor Absorption Cooling Systems Course No: M04-025 Credit: 4 PDH A. Bhatia Continuing Education and Development, Inc. 22 Stonewall Court Woodcliff Lake, NJ 07677 P: (877) 322-5800 [email protected] Overview of Vapor Absorption Cooling Systems Course Content A vapor absorption chiller machine (VAM) is a machine that produces chilled water using a heat source rather than electrical input as in the more familiar vapor compression cycle. It seems unreasonable that cooling can be achieved with heat, but that is what occurs within an absorption chiller. Both vapor compression and absorption refrigeration cycles accomplish the removal of heat through the evaporation of a refrigerant at a low pressure and the rejection of heat through the condensation of the refrigerant at a higher pressure. The basic difference is that an electric chiller employs a mechanical compressor to create the pressure differences necessary to circulate the refrigerant whereas the absorption chillers use heat source and do not use a mechanical compressor. The differences cause an absorption system to use little to no work input, but energy must be supplied in the form of heat. This makes the system very attractive when there is a cheap source of heat, such as solar heat or waste heat from electricity or heat generation. Absorption chillers have recently gained widespread acceptance due to their capability of not only integrating with cogeneration systems but also because they can operate with industrial waste heat streams. What is Absorption? Comparing the absorption refrigeration cycle with the more familiar vapor compression refrigeration cycle is often an easy way to introduce it. -
Chiller System Design and Control
Applications Engineering Manual Chiller System Design and Control November 2011 SYS-APM001-EN Chiller System Design and Control Susanna Hanson, applications engineer Mick Schwedler, applications manager Beth Bakkum, information designer Preface This manual examines chilled-water-system components, configurations, options, and control strategies. The goal is to provide system designers with options they can use to satisfy the building owners’ desires, but this manual is not intended to be a complete chiller-system design manual. System designers may get the most use from this manual by familiarizing themselves with chilled-water-system basics and understanding the benefits of various options. Thereafter, when a specific job will benefit from these advantages, consult appropriate sections of the manual in detail. The Engineers Newsletters that are referenced in this manual are available at: www.trane.com/commercial/library/newsletters.asp Trane, in proposing these system design and application concepts, assumes no responsibility for the performance or desirability of any resulting system design. Design of the HVAC system is the prerogative and responsibility of the engineering professional. “Trane” and the Trane logo are registered trademarks, and TRACE, System Analyzer and TAP are trademarks of Trane, a business of Ingersoll-Rand. © 2009 Trane All rights reserved Chiller System Design and Control SYS-APM001-EN Contents Preface .................................................................................................. i Primary System -
Small-Scale Solar Heating and Cooling Systems
Contact Austria: AEE INTEC (www.aee-intec.at) France: Tecsol (www.tecsol.fr) Germany: Fraunhofer ISE (www.ise.fraunhofer.de) Greece: CRES (www.cres.gr) Italy: Small-Scale Solar Heating and EURAC (www.eurac.edu) University of Bergamo Cooling Systems (www.unibg.it) Spain: Package Systems for Combined Air Conditioning, Ikerlan (www.ikerlan.es) Domestic Hot Water Preparation and Space Heating Industry partners: Standardized System Solutions CLIMATEWELL (www.climatewell.com) Fagor (www.fagor.com) Package Solutions on the Market SK Sonnenklima (www.sonnenklima.de) SOLution (www.sol-ution.com) SorTech (www.sortech.de) Solar thermal domestic hot water heating (DHW) DHW Further information: EURAC research – project coordinator & space heating Solar Combi Viale Druso/Drususallee 1 & space cooling Solar Combi+ I-39100 Bolzano/Bozen Tel. +39 0471 055610 Fax +39 0471 055699 February 2010 [email protected] http://www.solarcombiplus.eu Page 20 of 20 Table of Contents What is a Solar Combi Plus System? ....................................3 Most Promising Climatic Regions..........................................4 Suitable Collector Technology .............................................6 Standard System Configurations .........................................9 Recommendations on System Design................................. 11 Package System - Climatewell........................................... 14 Package System - SOLution .............................................. 16 Package System - SorTech .............................................. -
Sustainable District Cooling Guidelines
INTERNATIONAL ENERGY AGENCY TECHNOLOGY COLLABORATION PROGRAMME ON DISTRICT HEATING AND COOLING INCLUDING COMBINED HEAT AND POWER SUSTAINABLE DISTRICT COOLING GUIDELINES INTERNATIONAL ENERGY AGENCY TECHNOLOGY COLLABORATION PROGRAMME ON DISTRICT HEATING AND COOLING INCLUDING COMBINED HEAT AND POWER This project has been independently funded by the International Energy Agency Technology Collaboration Programme on District Heating and Cooling including Combined Heat and Power (IEA DHC). Any views expressed in this publication are not necessarily those of IEA DHC. IEA DHC can take no responsibility for the use of the information within this publication, nor for any errors or omissions it may contain. Information contained herein have been compiled or arrived from sources believed to be reliable. Nevertheless, the authors or their organizations do not accept liability for any loss or damage arising from the use thereof. Using the given information is strictly your own responsibility. SUSTAINABLE DISTRICT COOLING GUIDELINES 2 INTERNATIONAL ENERGY AGENCY TECHNOLOGY COLLABORATION PROGRAMME ON DISTRICT HEATING AND COOLING INCLUDING COMBINED HEAT AND POWER IEA DHC Operating Agent: AGFW Projekt GmbH Stresemannallee 30 60596 Frankfurt am Main Germany Phone: +49 69 630 434 4 E-mail: [email protected] © Copyright IEA DHC c/o AGFW Projekt GmbH 2019, © R2M Solution 2019, © VTT 2019, © SCUT 2019 All property rights, including copyright, are vested in IEA DHC represented by the Operating Agent for the IEA DHC Executive Committee. In 2019 AGFW Projekt GmbH (Germany) fills out that role, on behalf of the Contracting Parties of the International Energy Agency Technology Collaboration Programme on District Heating and Cooling including Combined Heat and Power.