(12) Patent Application Publication (10) Pub. No.: US 2011/0028732 A1 Trauth Et Al
Total Page:16
File Type:pdf, Size:1020Kb
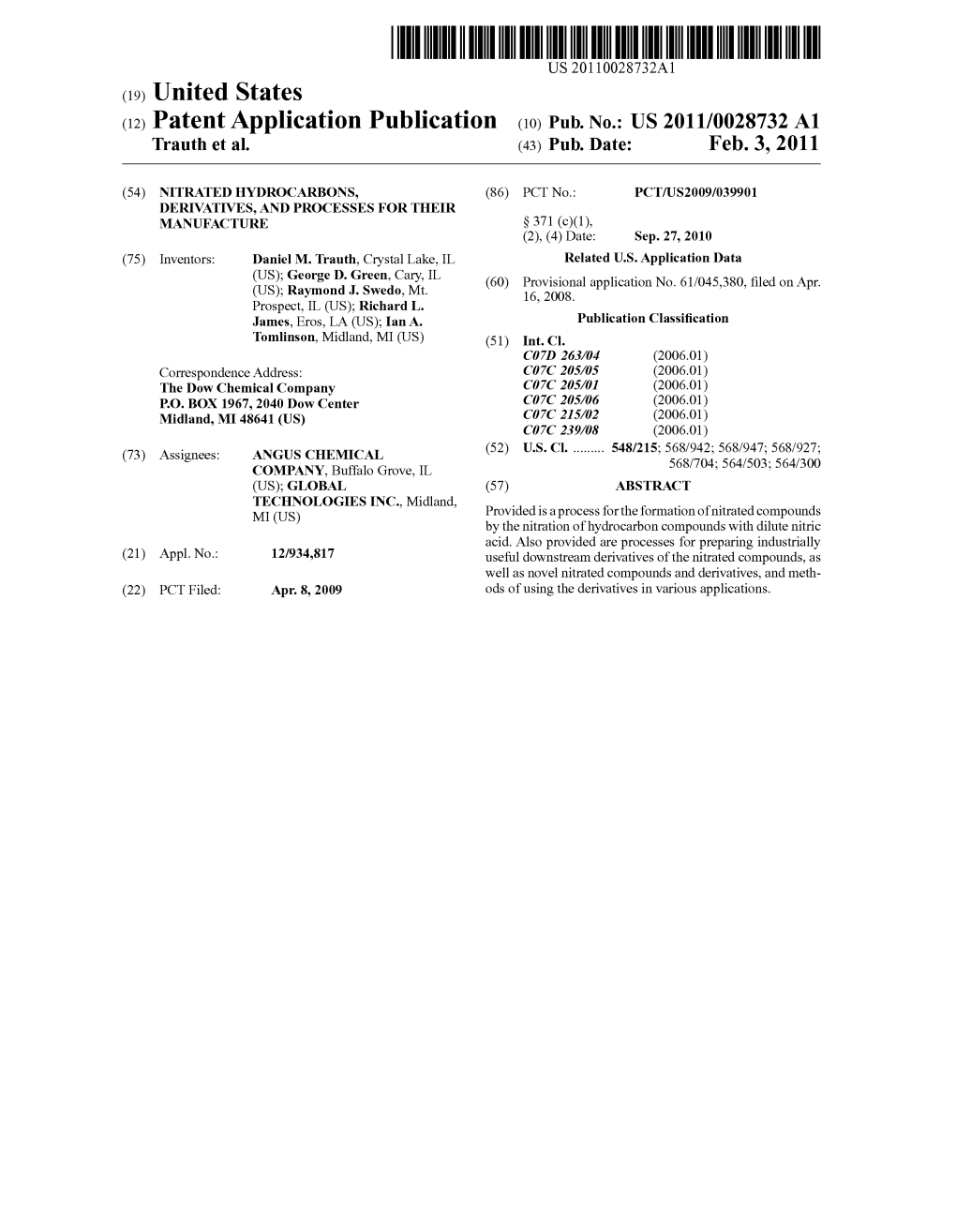
Load more
Recommended publications
-
Enlarging Knowledge on Lager Beer Volatile Metabolites Using Multidimensional Gas Chromatography
foods Article Enlarging Knowledge on Lager Beer Volatile Metabolites Using Multidimensional Gas Chromatography Cátia Martins 1 , Tiago Brandão 2, Adelaide Almeida 3 and Sílvia M. Rocha 1,* 1 Departamento de Química & LAQV-REQUIMTE, Universidade de Aveiro, Campus Universitário Santiago, 3810-193 Aveiro, Portugal; [email protected] 2 Super Bock Group, Rua do Mosteiro, 4465-703 Leça do Balio, Portugal; [email protected] 3 Departamento de Biologia & CESAM, Universidade de Aveiro, Campus Universitário Santiago, 3810-193 Aveiro, Portugal; [email protected] * Correspondence: [email protected]; Tel.: +351-234-401-524 Received: 30 July 2020; Accepted: 6 September 2020; Published: 11 September 2020 Abstract: Foodomics, emergent field of metabolomics, has been applied to study food system processes, and it may be useful to understand sensorial food properties, among others, through foods metabolites profiling. Thus, as beer volatile components represent the major contributors for beer overall and peculiar aroma properties, this work intends to perform an in-depth profiling of lager beer volatile metabolites and to generate new data that may contribute for molecules’ identification, by using multidimensional gas chromatography. A set of lager beers were used as case-study, and 329 volatile metabolites were determined, distributed over 8 chemical families: acids, alcohols, esters, monoterpenic compounds, norisoprenoids, sesquiterpenic compounds, sulfur compounds, and volatile phenols. From these, 96 compounds are reported for the first time in the lager beer volatile composition. Around half of them were common to all beers under study. Clustering analysis allowed a beer typing according to production system: macro- and microbrewer beers. Monoterpenic and sesquiterpenic compounds were the chemical families that showed wide range of chemical structures, which may contribute for the samples’ peculiar aroma characteristics. -
Volatile Organic Compounds from Books
1 Measuring the emission of volatile organic compounds from books Velson Horie Research Project Manager The British Library What is happening to our books? presevation of folding endurance DP X. Zou, T. Uesaka, N. Gurnagul, Prediction of paper permanence by accelerated aging. Part I: Kinetic analysis of the 3 aging process , Cellulose, 1996, 3, 243-267. A Few Statistics •Formal beginning in 1753 as the library of The British Museum •The British Library formed in 1973 from many collections •New St Pancras building opened in 1998 •150m collection items on 640km of shelves, •£131m budget, 1900 staff 4 Additional Storage Programme - Boston Spa •7 million collection items •263 km, 12,000 tonne of stock •Reduced oxygen (16%) •Robotic book handling •What are the long term effects? 5 Preserving Newspapers •33 km of stock •5,300 tonne of stock •1.4 tonne/y VOC production •3,800 years till all evaporated 6 Major UK libraries and archives Cambridge University Library (CUL) 7m printed items The British Library (BL) 150m items National Library of Scotland (NLS) 14m items National Library of Wales (NLW) 6m printed items Oxford University Library(OULS) 11m items Trinity College Dublin Library (TCD) 4m printed items The National Archives (TNA) National Archives of Scotland (NAS) 7 Condition assessment Preservation Assessment Survey Strength Colour pH Molecular weight Furnish SurveNIR VOCs 8 The “real thing” is important to people E-books sales have been slow to take off. CafeScribe is sending every e-textbook purchaser a scratch and sniff sticker with a musty “old book” smell. By placing these stickers on their computers, they can give their e-books the same musty book smell they know and love from used textbooks. -
Cambridge CB2 3EG (Received 14 June 1990)
Journal of Physiology (1991), 437, pp. 431-448 431 With 11 figures Printed in Great Britain ACTIONS OF n-ALCOHOLS ON NICOTINIC ACETYLCHOLINE RECEPTOR CHANNELS IN CULTURED RAT MYOTUBES BY R. D. MURRELL*, M. S. BRAUNt AND THE LATE D. A. HAYDON From the Physiological Laboratory, University of Cambridge, Downing Street, Cambridge CB2 3EG (Received 14 June 1990) SUMMARY 1. The actions of the n-alcohols from pentanol to dodecanol on nicotinic acetylcholine receptor (nAChR) channels were investigated by recording single ACh- activated channel activity from inside-out membrane patches isolated from cultured rat myotubes. Alcohols were applied to the cytoplasmic side of the membrane; aqueous concentrations ranged from 11 7 mM-pentanol to 0-02 mm-dodecanol. 2. The intermediate-chain alcohols (pentanol to octanol) caused channel currents to fluctuate between the fully open and closed state level so that openings occurred in bursts interrupted by brief gaps. Closed time distributions were fitted well with two exponential components, the fast component representing the closures within a burst. The number of gaps within a burst was dependent on alcohol concentration whereas gap duration was independent of concentration but increased with increasing chain length of the alcohol up to octanol. 3. Nonanol and decanol reduced the mean duration of bursts of openings but did not cause an increase in the number of short closed intervals within a burst. Beyond decanol there was a decline in the ability of the n-alcohols to affect channel function. A saturated solution of undecanol (0-07 mM) reduced the mean open time by 33+17 %, whereas a saturated solution of dodecanol had no significant effect. -
KUNDU-THESIS.Pdf
Acknowledgement I would like to thank my advisor Prof. Zachary T. Ball for teaching me everything I know in synthetic skills during my first year and guiding me through the rest of my time here at Rice. He has helped me better myself through constant constructive criticism, both in research and writing. I would also like to thank past and present Ball group members, Dr. Brian Popp, Dr. Alex Zaykov, Dr. Jessica Herron, Vincenzo Russo, Ramya Sambasivan, Cara Bovet, Zhen Chen, Dr. Jane Coughlin, Farrukh Vohidov, Matt Minus, Rob Ferguson, Julian Cooper. They have been a very good support in discussing research, exchanging ideas, and have become great pals in the last few years. Especially, Brian and Ramya’s encouragement in tough times is really valued. I thank my friends Rajkishore Barik and Meenu Adhikari for making Houston a second home. Again, Ramya Sambasivan for being a very good friend and always a willing ear to vent out frustrations associated with the graduate life and Avani Verma for bringing all kinds of fun in life and being so encouraging during my panic moments in thesis writing process. I would like to take this opportunity to express my gratitude and respect for my father Kuru Ram, and mother Amita Kundu, for the confidence and faith they always had in me, my sister Aruna Hajra who always supported me in my endeavors. I would like to thank my fiancée Soumya Sarkar, for his never wavering trust, love and support throughout my Ph.D in our 6 yr long, long- distance relation. Last but not least thanks to everyone who cared! -Rituparna Kundu Abstract Developing Dirhodium-Complexes for Protein Inhibition and Modification & Copper-Catalyzed Remote Chlorination of Alkyl-Hydroperoxides by Rituparna Kundu The work describes the development of a new class of protein-inhibitors for protein-protein interactions, based on metallopeptides comprised of a dirhodium metal center. -
Chewing Gum Containing High-Potency Sweetener Particles with Modified Zein Coating
Europaisches Patentamt 19 European Patent Office Office europeen des brevets © Publication number: 0 427 796 B1 12 EUROPEAN PATENT SPECIFICATION @ Date of publication of patent specification : © int. ci.5: A23G 3/30, A23L 1/236, 29.09.93 Bulletin 93/39 A23L 1/22 (2j) Application number : 90900603.3 (22) Date of filing : 17.11.89 © International application number : PCT/US89/05159 @ International publication number : WO 90/06062 14.06.90 Gazette 90/14 © CHEWING GUM CONTAINING HIGH-POTENCY SWEETENER PARTICLES WITH MODIFIED ZEIN COATING. © Priority: 02.12.88 US 279215 (56) References cited : WPI, FILE SUPPLIER, Derwent Publications @ Date of publication of application : Ltd., London, GB; & JP-B-45012759 22.05.91 Bulletin 91/21 © Proprietor : WM. WRIGLEY JR. COMPANY © Publication of the grant of the patent : 410 North Michigan Avenue 29.09.93 Bulletin 93/39 Chicago Illinois 60611 (US) @ Designated Contracting States : @ Inventor : COURTRIGHT, Steven, B. AT BE CH DE FR GB IT LI LU NL SE 1629 Brummel Evanston, IL 60202 (US) (56) References cited : Inventor : BARRETT, Kevin, F. EP-A- 0 067 595 7202 Western Avenue EP-A- 0 320 522 Darien, IL 60559 (US) WO-A-89/03170 US-A- 29 682 © Representative : Baverstock, Michael George US-A- 3 262 788 Douglas et al US-A- 3 753 739 BOULT, WADE & TENNANT 27 Furnival Street US-A- 3 922 354 London, EC4A 1PQ (GB) US-A- 3 928 633 US-A- 3 956 507 US-A- 3 962 468 US-A- 4 004 039 US-A- 4 049 706 US-A- 4 139 639 US-A- 4 230 687 US-A- 4 269 860 US-A- 4 384 004 US-A- 4 384 005 US-A- 4 495 213 US-A- 4 497 835 US-A- 4 517 214 US-A- 4 554 167 US-A- 4 556 565 CO US-A- 4 568 560 CO US-A- 4 579 747 o> US-A- 4 597 970 US-A- 4 634 593 h- CM Note : Within nine months from the publication of the mention of the grant of the European patent, any person may give notice to the European Patent Office of opposition to the European patent granted. -
Read-Across of 90-Day Rat Oral Repeated-Dose Toxicity: 1 a Case
Article Read-across of 90-Day Rat Oral Repeated-Dose Toxicity: A Case Study for Selected 2-Alkyl-1-alkanols Schultz, T.W, Przybylak, P.R, Richardz, A-N, Mellor, Claire, Bradbury, S.P and Cronin, M.T.D Available at http://clok.uclan.ac.uk/17640/ Schultz, T.W, Przybylak, P.R, Richardz, A-N, Mellor, Claire ORCID: 0000-0002- 7647-2085, Bradbury, S.P and Cronin, M.T.D (2017) Read-across of 90-Day Rat Oral Repeated-Dose Toxicity: A Case Study for Selected 2-Alkyl-1-alkanols. Computational Toxicology . It is advisable to refer to the publisher’s version if you intend to cite from the work. http://dx.doi.org/10.1016/j.comtox.2017.02.005 For more information about UCLan’s research in this area go to http://www.uclan.ac.uk/researchgroups/ and search for <name of research Group>. For information about Research generally at UCLan please go to http://www.uclan.ac.uk/research/ All outputs in CLoK are protected by Intellectual Property Rights law, including Copyright law. Copyright, IPR and Moral Rights for the works on this site are retained by the individual authors and/or other copyright owners. Terms and conditions for use of this material are defined in the policies page. CLoK Central Lancashire online Knowledge www.clok.uclan.ac.uk 1 Read-across of 90-Day Rat Oral Repeated-Dose Toxicity: 2 A Case Study for Selected 2-Alkyl-1-alkanols 3 4 Terry W. Schultza*, Katarzyna R. Przybylakb, Andrea-Nicole Richarzb, Claire L. Mellorb, 5 Steven P Bradburyc and Mark T. -
ZZZZZZZZZZZZZZZZZZ 5,633,289 Page 2
US005633289A United States Patent (19) 11 Patent Number: 5,633,289 Nakamura et al. 45) Date of Patent: May 27, 1997 54 PROCESS FOR MOLDING AN INTEGRAL FOREIGN PATENT DOCUMENTS SKN FOAMAND A POLYURETHANE 0006381 1/1980 European Pat. Off.. MATERAL FOR MOLDING THE SAME 0044226 1/1982 European Pat. Off.. 75 Inventors: Michihiko Nakamura; Masanao 0211495 2/1987 European Pat. Off.. Ishikake; Yukio Kawakita; Akira 0353061 1/1990 European Pat. Off.. Mabuchi; Osamu Yamanaka, all of (List continued on next page.) Aichi-ken, Japan OTHER PUBLICATIONS 73) Assignee: Toyoda Gosei Co., Ltd., Nishikasugai, Patent Abstracts of Japan, vol. 5, No. 190 (M-100) (1981). Japan Patent Abstracts of Japan, vol. 8, No. 057 (M-283) (1984). Patent Abstracts of Japan, vol. 4, No. 105 (M-023) (1980). Patent Abstracts of Japan, vol. 88, No. 1007 (M-750) (21) Appl. No.: 213,014 (1988). 22 Filed: Mar 14, 1994 Primary Examiner-Nathan M. Nutter (30) Foreign Application Priority Data Assistant Examiner-Duc Truong Attorney, Agent, or Firm-Cushman Darby & Cushman Mar 16, 1993 JP Japan .................................... 5-082660 Intellectual Property Group of Pillsbury Madison & Sutro, Mar 16, 1993 JP Japan .................................... 5-082661 LLP I51 int. Cl. ... C08J 9/34 57 ABSTRACT (52 U.S. Cl. ........................... 521/51; 521/159; 521/170; A process and a polyurethane material for molding a semi 521/174; 521/176; 528/48: 264/51 rigid integral skin foam which comprising an integral skin (58) Field of Search .............................. 521/51, 159, 170, having a low degree of foaming and a core having a high 521/174, 176; 264/51; 528/48 degree of foaming. -
Chemical Compatibility Chart
Chemical Compatibility Chart 1 Inorganic Acids 1 2 Organic acids X 2 3 Caustics X X 3 4 Amines & Alkanolamines X X 4 5 Halogenated Compounds X X X 5 6 Alcohols, Glycols & Glycol Ethers X 6 7 Aldehydes X X X X X 7 8 Ketone X X X X 8 9 Saturated Hydrocarbons 9 10 Aromatic Hydrocarbons X 10 11 Olefins X X 11 12 Petrolum Oils 12 13 Esters X X X 13 14 Monomers & Polymerizable Esters X X X X X X 14 15 Phenols X X X X 15 16 Alkylene Oxides X X X X X X X X 16 17 Cyanohydrins X X X X X X X 17 18 Nitriles X X X X X 18 19 Ammonia X X X X X X X X X 19 20 Halogens X X X X X X X X X X X X 20 21 Ethers X X X 21 22 Phosphorus, Elemental X X X X 22 23 Sulfur, Molten X X X X X X 23 24 Acid Anhydrides X X X X X X X X X X 24 X Represents Unsafe Combinations Represents Safe Combinations Group 1: Inorganic Acids Dichloropropane Chlorosulfonic acid Dichloropropene Hydrochloric acid (aqueous) Ethyl chloride Hydrofluoric acid (aqueous) Ethylene dibromide Hydrogen chloride (anhydrous) Ethylene dichloride Hydrogen fluoride (anhydrous) Methyl bromide Nitric acid Methyl chloride Oleum Methylene chloride Phosphoric acid Monochlorodifluoromethane Sulfuric acid Perchloroethylene Propylene dichloride Group 2: Organic Acids 1,2,4-Trichlorobenzene Acetic acid 1,1,1-Trichloroethane Butyric acid (n-) Trichloroethylene Formic acid Trichlorofluoromethane Propionic acid Rosin Oil Group 6: Alcohols, Glycols and Glycol Ethers Tall oil Allyl alcohol Amyl alcohol Group 3: Caustics 1,4-Butanediol Caustic potash solution Butyl alcohol (iso, n, sec, tert) Caustic soda solution Butylene -
Estimating the Octanol/Water Partition Coefficient for Aliphatic Organic Compounds Using Semi-Empirical Electrotopological Index
Int. J. Mol. Sci. 2011, 12, 7250-7264; doi:10.3390/ijms12107250 OPEN ACCESS International Journal of Molecular Sciences ISSN 1422-0067 www.mdpi.com/journal/ijms Article Estimating the Octanol/Water Partition Coefficient for Aliphatic Organic Compounds Using Semi-Empirical Electrotopological Index Erica Silva Souza 1, Laize Zaramello 2, Carlos Alberto Kuhnen 2, Berenice da Silva Junkes 3, Rosendo Augusto Yunes 1 and Vilma Edite Fonseca Heinzen 1,* 1 Departamento de Química, Universidade Federal de Santa Catarina, Campus Universitário, Trindade, Florianópolis, SC 88040-970, Brazil; E-Mails: [email protected] (E.S.S.); [email protected] (R.A.Y.) 2 Departamento de Física, Universidade Federal de Santa Catarina, Campus Universitário, Trindade, Florianópolis, SC 88040-970, Brazil; E-Mails: [email protected] (L.Z.); [email protected] (C.A.K.) 3 Instituto Federal de Educação, Ciência e Tecnologia de Santa Catarina , Avenida Mauro Ramos 950 , Florianópolis , SC 88020-300, Brazil; E-Mail: [email protected] * Author to whom correspondence should be addressed; E-Mail: [email protected]; Tel.: +55-48-3721-6849; Fax: +55-48-3721-6850. Received: 8 September 2011; in revised form: 8 October 2011 / Accepted: 14 October 2011 / Published: 24 October 2011 Abstract: A new possibility for estimating the octanol/water coefficient (log P) was investigated using only one descriptor, the semi-empirical electrotopological index (ISET ). The predictability of four octanol/water partition coefficient (log P) calculation models was compared using a set of 131 aliphatic organic compounds from five different classes. Log P values were calculated employing atomic-contribution methods, as in the Ghose/Crippen approach and its later refinement, AlogP; using fragmental methods through the ClogP method; and employing an approach considering the whole molecule using topological indices with the MlogP method. -
Hazard Evaluation of Substances Transported by Ships
E 4 ALBERT EMBANKMENT LONDON SE1 7SR Telephone: +44 (0)20 7735 7611 Fax: +44 (0)20 7587 3210 PPR.1/Circ.5 25 May 2018 HAZARD EVALUATION OF SUBSTANCES TRANSPORTED BY SHIPS Report of the fifty-fifth session of the GESAMP/EHS Working Group on the Evaluation of the hazards of harmful substances carried by ships The report of the fifty-fifth session of the GESAMP/EHS Working Group on the Evaluation of the hazards of harmful substances carried by ships, held from 30 April to 4 May 2018, is attached. Any comments or questions should be addressed to: Technical Secretary of the GESAMP/EHS Working Group Marine Environment Division International Maritime Organization 4 Albert Embankment London SE1 7SR United Kingdom Email: [email protected] *** I:\CIRC\PPR\01\PPR 1-CIRC 5.docx E WORKING GROUP ON THE EVALUATION EHS 55/9 OF THE HAZARDS OF HARMFUL 4 May 2018 SUBSTANCES CARRIED BY SHIP Original: ENGLISH 55th session Agenda item 9 REPORT OF THE FIFTY-FIFTH SESSION 1 INTRODUCTION ..................................................................................................... 2 2 OUTCOME OF OTHER BODIES ............................................................................. 2 3 EVALUATION OF NEW SUBSTANCES .................................................................. 2 4 RE-EVALUATION OF SUBSTANCES AND CONSIDERATION OF ISSUES RELATED TO EVALUATIONS ................................................................................ 5 5 CLASSIFICATION ISSUES .................................................................................... -
“Inert” Ingredients Used in Organic Production
“Inert” Ingredients Used in Organic Production Terry Shistar, PhD A Beyond Pesticides Report he relatively few registered pesticides allowed in organic production are contained in product formulations with so-called “inert” ingredients that are not disclosed on the T product label. The “inerts” make up the powder, liquid, granule, or spreader/sticking agents in pesticide formulations. The “inerts” are typically included in products with natural or synthetic active pesticide ingredients recommended by the National Organic Standards Board (NOSB) and listed by the National Organic Program (NOP) on the National List of Allowed and Prohibited Substances. Any of the pesticides that meet the standards of public health and environmental protection and organic compatibility in the Organic Foods Production Act (OFPA) may contain “inert” ingredients. Because the standards of OFPA are different from those used by the U.S. Environmental Protection Agency (EPA) to regulate pesticides and given changes in how the agency categorizes inerts, the NOSB has adopted a series of recommendations since 2010 that established a substance review process as part of the sunset review. NOP has not followed through on the Board’s recommendations and, as a result, there are numerous materials in use that have not been subject to OFPA criteria. This report (i) traces the history of the legal requirements for review by the NOSB, (ii) identifies the universe of toxic and nontoxic materials that make of the category of “inerts” used in products permitted in organic production, and (iii) suggests a path forward to ensure NOSB compliance with OFPA and uphold the integrity of the USDA organic label. -
WO 2018/009924 Al 11 January 2018 (11.01.2018) W !P O PCT
(12) INTERNATIONAL APPLICATION PUBLISHED UNDER THE PATENT COOPERATION TREATY (PCT) (19) World Intellectual Property Organization International Bureau (10) International Publication Number (43) International Publication Date WO 2018/009924 Al 11 January 2018 (11.01.2018) W !P O PCT (51) International Patent Classification: MG, MK, MN, MW, MX, MY, MZ, NA, NG, NI, NO, NZ, C08F 28/06 (2006.01) H01L 51/40 (2006.01) OM, PA, PE, PG, PH, PL, PT, QA, RO, RS, RU, RW, SA, SC, SD, SE, SG, SK, SL, SM, ST, SV, SY,TH, TJ, TM, TN, (21) International Application Number: TR, TT, TZ, UA, UG, US, UZ, VC, VN, ZA, ZM, ZW. PCT/US20 17/04 1286 (84) Designated States (unless otherwise indicated, for every (22) International Filing Date: kind of regional protection available): ARIPO (BW, GH, 10 July 2017 (10.07.2017) GM, KE, LR, LS, MW, MZ, NA, RW, SD, SL, ST, SZ, TZ, (25) Filing Language: English UG, ZM, ZW), Eurasian (AM, AZ, BY, KG, KZ, RU, TJ, TM), European (AL, AT, BE, BG, CH, CY, CZ, DE, DK, (26) Publication Langi English EE, ES, FI, FR, GB, GR, HR, HU, IE, IS, IT, LT, LU, LV, (30) Priority Data: MC, MK, MT, NL, NO, PL, PT, RO, RS, SE, SI, SK, SM, 62/359,866 08 July 2016 (08.07.2016) US TR), OAPI (BF, BJ, CF, CG, CI, CM, GA, GN, GQ, GW, KM, ML, MR, NE, SN, TD, TG). (71) Applicant: UNIVERSITY OF PITTSBURGH - OF THE COMMONWEALTH SYSTEM OF HIGHER EDU¬ Published: CATION [US/US]; 1st Floor Gardner Steel Conference — with international search report (Art.