(10) Patent No.: US 8247.487 B2
Total Page:16
File Type:pdf, Size:1020Kb
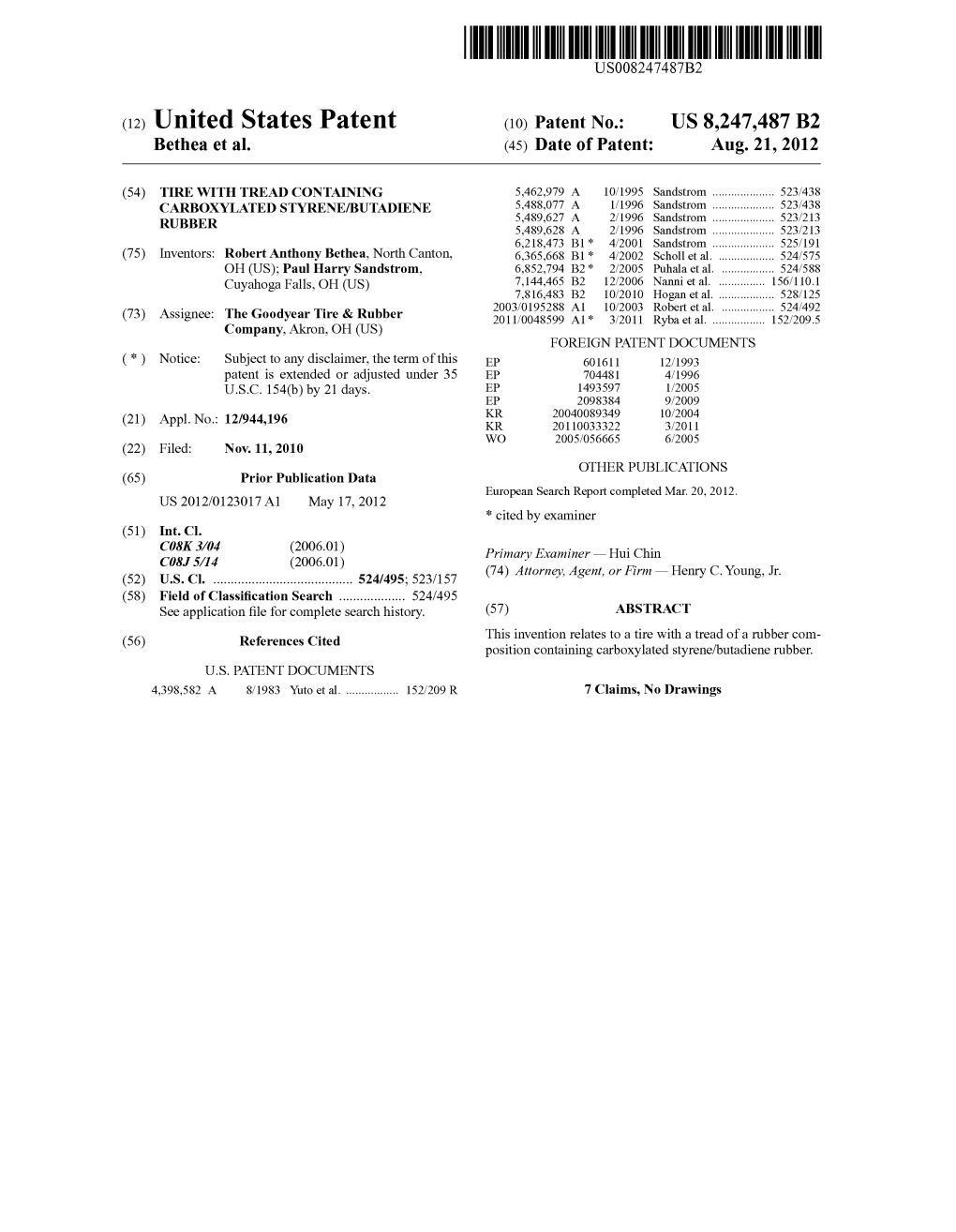
Load more
Recommended publications
-
Crosslink Density of Rubbers
Characterisation of Crosslinks in Vulcanised Rubbers: From Simple to Advanced Techniques K.L. Mok* and A.H. Eng** *Malaysian Rubber Board, Paper Presenter **Malaysian Institute of Chemistry Copyright © 2017 by K.L. Mok and A.H. Eng 1 Rubber & Elastomer • Rubbery: 1) Sufficient long chain; 2) Flexible molecules with noncollinear single bonds that allow segmental rotations along the backbone; 3) Non crystalline at service temperature • Rubber vs Elastomer: Rubber commonly refers to elastic materials that requires vulcanisation before they can be used in the products. However, there are elastic polymers that do not require vulcanisation such as polyurethane (PU), styrene- isoprene (SIS) copolymer. These elastic materials are classified under elastomer, which normally also includes rubbers. • Unvulcanised Rubbers: Unvulcanised rubbers are normally weak when put under stress during use. With very few exceptions, such as rubber glues almost all rubber products require vulcanisation to provide the required strength for a longer design life. • Elastomers: Polyurethane (PU), styrene-isoprene (SIS) copolymer, do not require vulcanisation to have good strength properties as they contain the hard segment Copyrightwhich © 2017 by K.L.is Mok good and A.H. Engfor strength and the soft segment good elasticity properties. 2 Rubber Vulcanisation & Crosslink Density • Vulcanization or vulcanisation: A reaction that leads to the formation of inter-molecular bonding among the unsaturated rubber molecules with 3 dimensional network such that the mechanical properties such as tensile strength is enhanced. The vulcanising agent originally referred to was elemental sulfur. Later, sulfur donor was included. It now also includes non sulfur systems such as metal oxide and peroxides. -
Effect of the Nitrile Content on Nitrile Rubber Cure in Wide Temperature Range
INTERNATIONAL JOURNAL OF SCIENTIFIC & TECHNOLOGY RESEARCH VOLUME 9, ISSUE 02, FEBRUARY 2020 ISSN 2277-8616 Effect Of The Nitrile Content On Nitrile Rubber Cure In Wide Temperature Range. Denis Kalugin, Anton Nashchokin, Anna Sutyagina, Nikolay Tikhonov, Artem Malakho Victor Avdeev Abstract: Vulcanization of NBR rubber with different nitrile content was studied. Enthalpy of vulcanization drops from 6.62J/g for 18% nitrile rubber to 1.89J/g for 40% one. The peak of vulcanization shifts to higher temperatures for 12°C with nitrile content increase. No secondary vulcanization process was observed for 18% nitrile rubber. The other rubbers possess thermal polymerization at 285°C in neat rubbers accelerated by nitrile groups. This process is additionally accelerated when vulcanization additives are present in rubber. Thus the post-vulcanization peak shifts up to 20°C to lower temperatures for 40% nitrile rubber with increase in enthalpy in 5 times compared to neat rubber. When heated at 250°C for 6 hours no significant change in rubber hardness is occurred for 18% nitrile rubber and 2 times increase for 40% nitrile rubber is measured indicating dramatic role of nitrile content for rubber properties. No considerable effect of nitrile groups cross link on rubber hardness is observed. Index Terms: cross-link, cure, DSC, hardness, NBR, nitrile, properties, rubber, vulcanization —————————— ◆ —————————— 1 INTRODUCTION The resulted mixture is poured into silicon paper box and rest Acrylonitrile–butadiene rubber (NBR), commonly known as for night for primary solvent evaporation. After that the resulted nitrile rubber, has been commercially available for more than film was dried at 50°C in vacuum to a constant weight. -
Polymer Composites Based on Plasticized PVC and Vulcanized Nitrile Rubber Waste Powder for Irrigation Pipes
Hindawi Publishing Corporation ISRN Materials Science Volume 2013, Article ID 726121, 5 pages http://dx.doi.org/10.1155/2013/726121 Research Article Polymer Composites Based on Plasticized PVC and Vulcanized Nitrile Rubber Waste Powder for Irrigation Pipes Maria Daniela Stelescu National R&D Institute for Textile and Leather, Leather and Footwear Research Institute, 93 Ion Minulescu Street, 031215 Bucharest, Romania Correspondence should be addressed to Maria Daniela Stelescu; [email protected] Received 19 June 2013; Accepted 18 July 2013 Academic Editors: V. Contini, Y. X. Gan, and V. Ji Copyright © 2013 Maria Daniela Stelescu. This is an open access article distributed under the Creative Commons Attribution License, which permits unrestricted use, distribution, and reproduction in any medium, provided the original work is properly cited. The paper presents the technique of production and characterization of polymer composites based on plasticized PVC and rubber powder from vulcanized nitrile rubber waste. The new polymer composites have lower hardness, higher elongation at break, a better tensile strength, and better ozone resistance, and the blend suitable for irrigations pipes for agricultural use was selected. The selected polymer composites have a good behavior under accelerated aging, repeated flexion at room temperature and atlow ∘ temperature (−20 C), a very good behavior for immersion in water, concentrated acid and basis, animal fat, soya, and sun flower oil, proving their suitability for gaskets, hoses, protection equipment, rubber footwear, and so forth. The resulted thermoplastic polymer composites can be processed by injection, extrusion, and compression molding. 1. Introduction Poly (vinyl chloride) (PVC) is a versatile polymer, used in flexible, semirigid, and rigid forms. -
(Pp)/ Ground Tire Rubber
MANUFACTURING OF POLYPROPYLENE (PP)/ GROUND TIRE RUBBER (GTR) THERMOPLASTIC ELASTOMERS USING ULTRASONICALLY AIDED EXTRUSION A Thesis Presented to The Graduate Faculty of The University of Akron In Partial Fulfillment of the Requirements for the Degree Master of Science Jieruo Liu August, 2013 MANUFACTURING OF POLYPROPYLENE (PP)/ GROUND TIRE RUBBER (GTR) THERMOPLASTIC ELASTOMERS USING ULTRASONICALLY AIDED EXTRUSION Jieruo Liu Thesis Approved: Accepted ______________________ _______________________ Advisor Department Chair Dr. Avraam I. Isayev Dr. Robert Weiss _______________________ _______________________ Committee Member Dean of the College Dr. Thein Kyu Dr. Steven Cheng _______________________ ________________________ Committee Member Dean of the Graduate School Dr. Younjin Min Dr. George Newkome ________________________ Date ii ABSTRACT Compounding ground tire rubber (GTR) from whole waste tires with thermoplastic polyolefins, such as polypropylene (PP), is a possible way to manufacture thermoplastic elastomers and also to recycle waste tires to solve a major environmental problem. The present study looks at the effect of PP/GTR mixing ratio, rubber particle size, type of extruder, maleic anhydride grafted polypropylene (PP-g-MA) compatibilizer and ultrasound on the mechanical and rheological properties of PP and PP/GTR blends. PP and GTR were compounded at ratios of 30/70, 50/50 and 70/30. Whole tire GTR particles of 40 and 140 mesh sizes were used. Both the single screw extruder (SSE) and twin screw extruder (TSE) without and with ultrasonic treatment were applied. PP-g-MA compatibilizer was added to PP/GTR 50/50 blends at concentration of 10 wt %. Rheological, tensile and impact properties of uncompatibilized and compatibilized PP/GTR 50/50 blends were compared. -
Rubber Division ACS Best Paper Awards
Rubber Division ACS Best Paper Awards The Best Paper Committee of Rubber Division, ACS seeks to improve the quality of technical presentations by evaluating and publicly recognizing the authors of outstanding papers presented our technical meetings. Each year Committee Judges and peer attendees, rate each presentation on quality of content, originality, and clarity. Winning papers are selected from the top-rated presentations after further review by the Best Paper Committee. The Best Symposium is awarded to the symposium with the highest average paper ratings and best average attendance of presentations. Meeting Year Award Authors/Moderators Affiliation Title 196th, Fall 2019 Best Paper Steven K. Henning & Fabien Total Cray Valley Silane-Terminated Liquid Poly(butadienes) in Tread Formulations: A Mechanistic Study 196th, Fall 2019 Best Symposium Ed Terrill & Crittenden ARDL, Inc. & University of Testing and Predicting Behavior of Rubber and Tires Ohlemacher Akron 194th, Fall 2018 Best Paper Nuthathai Warasitthinon and Cooper Tire & Rubber Co. The Payne Effect: Primarily Polymer-Related or Filler-Related Phenomenon? Chris Robertson 194th, Fall 2018 Pest Symposum Cal Moreland & Sy Mowdood Michelin USA & Pirelli Advances in Material and Processes of Car and Truck Tires (Retired 192nd, 2017 Best Paper Anke Blume*, Katarzyna S. University of Twente, Influence of Network Structure on Elastomer Properties Fall Bandzierz, Louis A.E.M. Netherlands Reuvekamp, Jerzy Dryzek, Wilma K. Dierkes, Dariusz M. Bielinski 192nd, 2017 Best Symposium Crittenden Ohlemacher & University of Akron & Characterization Tools for Elastomers Fall Michael Warner CCSI, Inc. 190th, Fall 2016 Best Paper Peter Mott U.S. Naval Research The Thermomechanical Response of Polyurea Laboratory, Chemistry Division 190th, Fall 2016 Honorable Mention Steven K Henning and Taejun Yoo Total Cray Valley The Synthesis and Characterization of Farnesene-Based Oligomers 190th 2016 Best Symposium Sy Mowdood and J. -
Elastomeric Materials
ELASTOMERIC MATERIALS TAMPERE UNIVERSITY OF TECHNOLOGY THE LABORATORY OF PLASTICS AND ELASTOMER TECHNOLOGY Kalle Hanhi, Minna Poikelispää, Hanna-Mari Tirilä Summary On this course the students will get the basic information on different grades of rubber and thermoelasts. The chapters focus on the following subjects: - Introduction - Rubber types - Rubber blends - Thermoplastic elastomers - Processing - Design of elastomeric products - Recycling and reuse of elastomeric materials The first chapter introduces shortly the history of rubbers. In addition, it cover definitions, manufacturing of rubbers and general properties of elastomers. In this chapter students get grounds to continue the studying. The second chapter focus on different grades of elastomers. It describes the structure, properties and application of the most common used rubbers. Some special rubbers are also covered. The most important rubber type is natural rubber; other generally used rubbers are polyisoprene rubber, which is synthetic version of NR, and styrene-butadiene rubber, which is the most important sort of synthetic rubber. Rubbers always contain some additives. The following chapter introduces the additives used in rubbers and some common receipts of rubber. The important chapter is Thermoplastic elastomers. Thermoplastic elastomers are a polymer group whose main properties are elasticity and easy processability. This chapter introduces the groups of thermoplastic elastomers and their properties. It also compares the properties of different thermoplastic elastomers. The chapter Processing give a short survey to a processing of rubbers and thermoplastic elastomers. The following chapter covers design of elastomeric products. It gives the most important criteria in choosing an elastomer. In addition, dimensioning and shaping of elastomeric product are discussed The last chapter Recycling and reuse of elastomeric materials introduces recycling methods. -
Mechanical and Oil Resistance Characteristics of Rubber Blends
ELASTOMERE UND KUNSTSTOFFE ELASTOMERS AND PLASTICS NBR · CR · PVC · Rubber blends · Mechanical and Oil Resistance Vulcanizing system · Oil resistance Different rubber blends based on nitrile butadiene rubber, NBR (N3980–39% Characteristics of Rubber acrylonitrile) have been prepared to get a product with high oil resistant and good mechanical properties. The Blends Based on Nitrile obtained mixes included NBR, chloro- prene rubber (CR) and polyvinyl chlo- 1 ride (PVC). The ratio of each component Butadiene Rubber (NBR, CR and PVC) as binary or ternary blend system has been varied and the corresponding vulcanizing systems have been carefully selected. It has been found that the type of rubber and the composition of blends markedly affect their oil resistance. In contrast, the type of crosslinks and crosslinking Blending of polymers has gained much in- (NR). The elastomeric composite has excel- density slightly affect the oil resistance terest, since about 3-4 decades ago, due to lent compatibility between two rubbers of of the corresponding vulcanizates. the fact that, it can be used to produce new different polarity when properly com- polymeric materials, i.e, compositions with pounded and processed. Anmin, et al. [12] specific properties suitable for certain spe- prepared hydrogenated nitrile rubber Mechanische Eigenschaften und cial application. Nitrile rubber (NBR) is wide- (HNBR)/clay nanocomposites using conven- Ölbeständigkeit von NBR ly used in many applications like oil seals, tional two-roll mill mixing technique. They Verschnitten gaskets, etc. The performance of NBR can found that adding organoclay in HNBR be improved by blending with various poly- elastomer greatly improves material ther- NBR · CR · PVC · Kautschukverschnitte · mers [1-4]. -
Mechanical Properties of Rubber
8434_Harris_33_b.qxd 09/20/2001 12:30 PM Page 33.1 CHAPTER 33 MECHANICAL PROPERTIES OF RUBBER Ronald J. Schaefer INTRODUCTION Rubber is a unique material that is both elastic and viscous. Rubber parts can there- fore function as shock and vibration isolators and/or as dampers.Although the term rubber is used rather loosely, it usually refers to the compounded and vulcanized material. In the raw state it is referred to as an elastomer. Vulcanization forms chem- ical bonds between adjacent elastomer chains and subsequently imparts dimen- sional stability, strength, and resilience. An unvulcanized rubber lacks structural integrity and will “flow” over a period of time. Rubber has a low modulus of elasticity and is capable of sustaining a deformation of as much as 1000 percent. After such deformation, it quickly and forcibly retracts to its original dimensions. It is resilient and yet exhibits internal damping. Rubber can be processed into a variety of shapes and can be adhered to metal inserts or mounting plates. It can be compounded to have widely varying properties.The load- deflection curve can be altered by changing its shape. Rubber will not corrode and normally requires no lubrication. This chapter provides a summary of rubber compounding and describes the static and dynamic properties of rubber which are of importance in shock and vibration isolation applications. It also discusses how these properties are influenced by envi- ronmental conditions. RUBBER COMPOUNDING Typical rubber compound formulations consist of 10 or more ingredients that are added to improve physical properties, affect vulcanization, prevent long-term dete- rioration, and improve processability.These ingredients are given in amounts based on a total of 100 parts of the rubber (parts per hundred of rubber). -
Rubber Compounds QUALITY | VALUE | SERVICE Rubber Compounds Rubber Where Rubber Compounds Abound
Piston Seals Wipers O-Rings & Kits Custom Parts Specialty Parts Services Wear Guides Rod Seals Rubber Compounds QUALITY | VALUE | SERVICE Rubber Compounds Rubber Where rubber compounds abound. Why make the rounds searching for rubber compounds when they’re all right here in one convenient place? All Seals has developed nearly 500 different rubber compounds, in a variety of materials and hardnesses, to satisfy virtually every conceivable requirement. And if your application requires unique properties and/or capabilities, we’ll develop a compound for you! This brochure describes the most commonly specified rubber compounds. As such, the information presented here is necessarily general in nature and abbreviated. For more specific information or expert advice, contact us and speak directly to an experienced compound professional. Please call us at 800.553.5054, or visit our website at www.allsealsinc.com. QUALITY | VALUE | SERVICE ® AFLAS BUTYL RUBBER CARBOXYLATED NITRILE (TFE/P, FEPM) (IIR) (XNBR) Aflas® or TFE/P is a member of a recent generation of fluoroelastomers Butyl is a specialty rubber more frequently specified for its physical Carboxylated nitrile, or XNBR, is produced by adding a carboxylic acid formulated specially to provide unique properties for specific applications. properties than chemical resistance. It has excellent shock absorption side group to nitrile rubber, thereby adding more crosslinking sites than The primary uses for Aflas® are in the oil/gas, chemical processing, and vibration damping capabilities, as well as good electrical properties. traditional NBR. As a result, solvent swell and abrasion resistance are pharmaceutical and automotive industries. It can be crosslinked (cured) Butyl’s unusually low gas permeability makes it ideal for vacuum significantly improved, as well as modulus, tensile strength and tear using a variety of systems, but generally peroxides are used to provide applications, while its high degree of saturation makes it inherently resistance. -
Recycled Micronized Rubber Formulation Having Improved Abrasion Resistance
(19) TZZ¥Z _T (11) EP 3 045 492 A1 (12) EUROPEAN PATENT APPLICATION (43) Date of publication: (51) Int Cl.: 20.07.2016 Bulletin 2016/29 C08J 11/04 (2006.01) C08J 11/06 (2006.01) B29B 17/02 (2006.01) B29B 17/04 (2006.01) (2006.01) (2006.01) (21) Application number: 16151911.1 B60C 1/00 C08L 21/00 C08L 19/00 (2006.01) (22) Date of filing: 19.01.2016 (84) Designated Contracting States: (72) Inventors: AL AT BE BG CH CY CZ DE DK EE ES FI FR GB • JASIUNAS, Chad Aaron. GR HR HU IE IS IT LI LT LU LV MC MK MT NL NO Copley, OH Ohio 44321 (US) PL PT RO RS SE SI SK SM TR • PAPP, Frank P. Designated Extension States: Fort Mill, SC South Carolina 29707 (US) BA ME • ROSENMAYER, Charles T. Designated Validation States: Decatur, GA Georgia 30030 (US) MA MD • MURTHY, Kedar D. Boston, MA Massachusetts 02117 (US) (30) Priority: 19.01.2015 US 201562105076 P (74) Representative: Mullen, Lee Bryan (71) Applicant: Lehigh Technologies, Inc. Elkington and Fife LLP Tucker, GA 30084 (US) Thavies Inn House 3-4 Holborn Circus London EC1N 2HA (GB) (54) RECYCLED MICRONIZED RUBBER FORMULATION HAVING IMPROVED ABRASION RESISTANCE (57) This invention is based upon the discovery that nized solution styrene-butadiene rubber can then be micronized solution styrene-butadiene rubber from post- blending into desired virgin rubbers and cured without consumer sourcescan be included inrubber formulations significantly compromising the abrasion resistance of the without severely compromising abrasion resistance. The rubber formulation. -
Silicone Rubber Compounds Meeting the Increasingly Diverse and Sophisticated Needs of Industry with the Unique Properties of Silicone Rubbers
Characteristic properties of Silicone Rubber Compounds Meeting the increasingly diverse and sophisticated needs of industry with the unique properties of silicone rubbers The main ingredients of Shin-Etsu’s silicone rubber compounds are unique raw silicone rubber gum and high-purity silica. Silicone rubber compounds have characteristics of both inorganic and organic materials, and offer a number of advantages not found in other organic rubbers. Silicone rubbers have fine electrical properties, good chemical stability and flame retardancy, and superior resistance to heat and cold. They are thus used in nearly every industry to improve the quality and functionality of products including electric and electronic equipment, office automation equipment, automobiles, food products, household goods, and leisure products. ■ Contents General properties of silicone 3 Heat and cold resistance 4 Weatherability 5 Moisture and steam resistance 5 Resistance to oils, solvents, and other chemicals 6, 7 Electrical insulation 8 Thermal conductivity 9 Flame retardancy 9 Electrical conductivity 9 Compression set 10 Flex fatigue resistance 10 Tear strength and tensile strength 11 Gas permeability 12 Transparency and coloring properties 12 Radiation resistance 13 Vibration absorption 14 Releasability and Non-corrosivity 14 Physiologically inert 14 The fine properties of silicone rubber 15 2 General properties of silicone High binding energy The siloxane bonds (–Si–O–Si–) that form the backbone of silicone (dimethyl polysiloxane) are highly stable. At 433 kJ/mol, their binding energy is higher than that of carbon bonds (C–C), at 355 kJ/mol. Thus, compared to common organic polymers, silicone rubbers have higher heat resistance and chemical stability, and provide better electrical insulation. -
Nitrile Butadiene Rubber (Nbr)
NITRILE BUTADIENE RUBBER (NBR) MATERIAL SPECIFICATIONS ChangExp NBR Nitrile rubber known as NBR, Buna-N and acrylonitrile butadiene rubber is s synthetic rubber copolymer elastomer. NBR rubber are widely use in automotive and aeronautical industry to make fuel and oil seals, self-sealing fuel tanks lining. NBR ability to withstand range of temperatures from -20 to +110 Celsius make it an ideal material for aeronautical applications. ChangExp NBR rubber sheet is a nitrile base rubber sheet, providing excellent resistance to petroleum oils as well as mineral and vegetable oils. NBR rubber material is used in applications involving not only oil and fuel resistance but also those applications requiring resistance to heat, abrasion, water and gas permeability. It is resistant to weathering, sunlight and ozone. From oil rigs to bowling alleys, nitrile rubber can be the right material for your applications. Advantage - Excellent oil resistant - Good resistance to heat and aging - Good inpermeability to gases - Good abrasion resistance Applications - Carburetor and fuel pump diaphragms - Chemical container lining - Seal and gasket - Aircraft hoses FEATURES Standard Width : 1000mm Width Range : 100mm - 2000mm 10mm Length : 10m Thickness : From 1mm to 50mm Standard Color : Black Work Temperature : +110 OC ADDRESS : 36/17 Moo 13, Buengkhamproi, Lam Luk Ka Pathumthani 12150 CHANG RUBBER DEVELOPMENT CO., LTD. www.changrubber.co.th NITRILE BUTADIENE RUBBER (NBR) (THNBR1261360) MATERIAL SPECIFICATIONS SPECIFICATION TEST METHOD TEST RESULT UNIT Specific Gravity ASTM D297 1.26 g/cm3 Hardness ASTM D2240 60 +/-5 Shore A Tensile Strength ASTM D-412 13 MPa Elongation ASTM D-412 350 Tear Strength ASTM D-624 30 kgf/cm Compression Set ASTM D-395 20 (22 Hours at 70 OC) WORKING TEMPERATURE In Air -40 OC +125 OC In Oil +100 OC In Water +100 OC MAIN CHARACTERISTICS ELASTICITY COMPRESSION ABRASION FLAME FUELS OZONE Good Good Poor Poor Good Fair ADDRESS : 36/17 Moo 13, Buengkhamproi, Lam Luk Ka Pathumthani 12150 CHANG RUBBER DEVELOPMENT CO., LTD.