(12) Patent Application Publication (10) Pub. No.: US 2016/0237595 A1 Maxwell Et Al
Total Page:16
File Type:pdf, Size:1020Kb
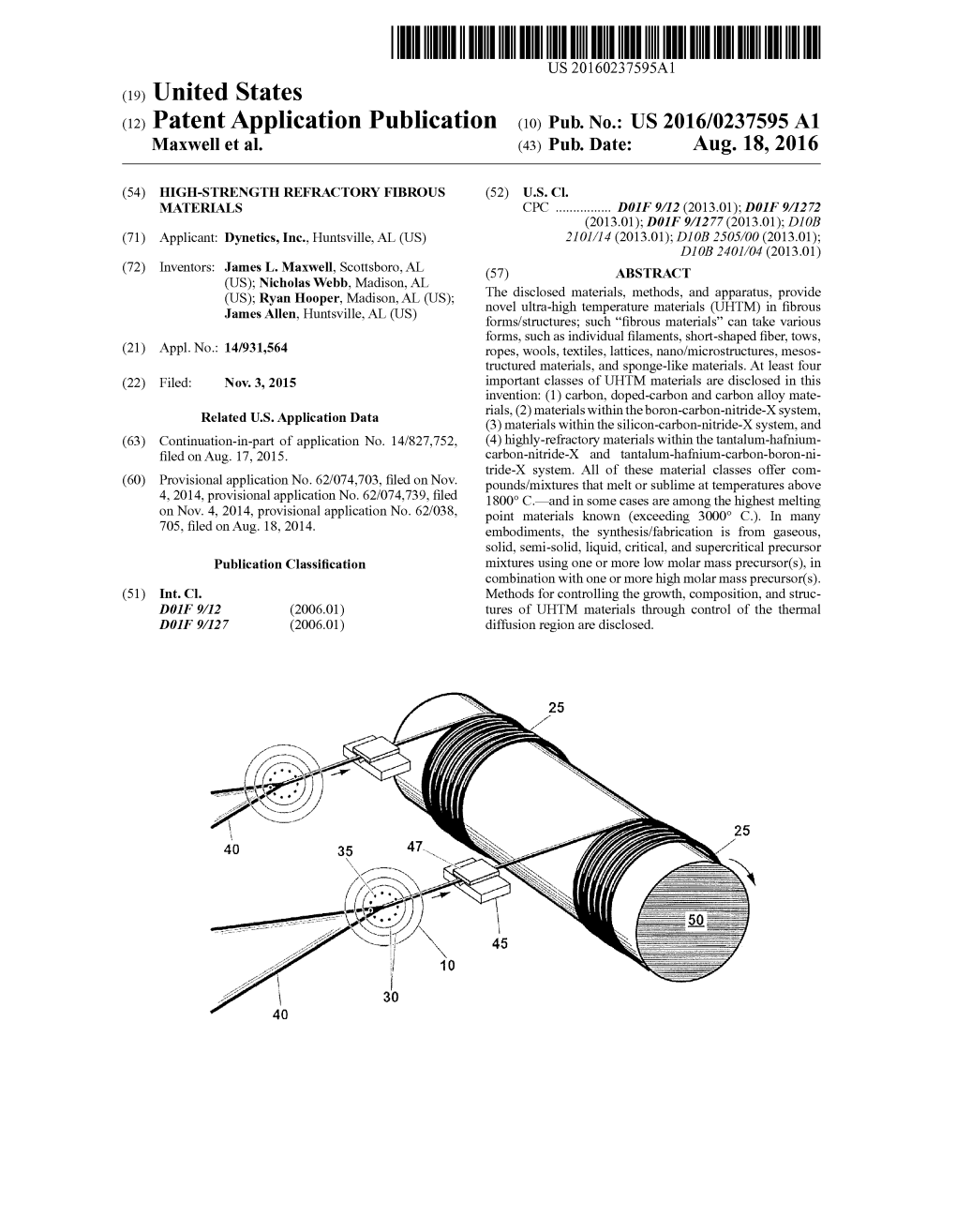
Load more
Recommended publications
-
Rediscovery of the Elements — a Historical Sketch of the Discoveries
REDISCOVERY OF THE ELEMENTS — A HISTORICAL SKETCH OF THE DISCOVERIES TABLE OF CONTENTS incantations. The ancient Greeks were the first to Introduction ........................1 address the question of what these principles 1. The Ancients .....................3 might be. Water was the obvious basic 2. The Alchemists ...................9 essence, and Aristotle expanded the Greek 3. The Miners ......................14 philosophy to encompass a obscure mixture of 4. Lavoisier and Phlogiston ...........23 four elements — fire, earth, water, and air — 5. Halogens from Salts ...............30 as being responsible for the makeup of all 6. Humphry Davy and the Voltaic Pile ..35 materials of the earth. As late as 1777, scien- 7. Using Davy's Metals ..............41 tific texts embraced these four elements, even 8. Platinum and the Noble Metals ......46 though a over-whelming body of evidence 9. The Periodic Table ................52 pointed out many contradictions. It was taking 10. The Bunsen Burner Shows its Colors 57 thousands of years for mankind to evolve his 11. The Rare Earths .................61 thinking from Principles — which were 12. The Inert Gases .................68 ethereal notions describing the perceptions of 13. The Radioactive Elements .........73 this material world — to Elements — real, 14. Moseley and Atomic Numbers .....81 concrete basic stuff of this universe. 15. The Artificial Elements ...........85 The alchemists, who devoted untold Epilogue ..........................94 grueling hours to transmute metals into gold, Figs. 1-3. Mendeleev's Periodic Tables 95-97 believed that in addition to the four Aristo- Fig. 4. Brauner's 1902 Periodic Table ...98 telian elements, two principles gave rise to all Fig. 5. Periodic Table, 1925 ...........99 natural substances: mercury and sulfur. -
5 VI June 2017
5 VI June 2017 www.ijraset.com Volume 5 Issue VI, June 2017 IC Value: 45.98 ISSN: 2321-9653 International Journal for Research in Applied Science & Engineering Technology (IJRASET) Production of Tantalum Carbide Tool Bit Using Powder Metallurgy Process Gautam Raj Jodh 1, Rajanikant Y. Mahajan 2, Amay Deorao Meshram 3, Abhijit Goraknath Naik 4 1 Assistant Professor, Mechanical Engineering, Priyadarshini Indira Gandhi College of Engineering, Nagpur, India. 2,3,4 Assistant Professor, Mechanical Engineering, Priyadarshini Institute of Engineering and Technology, Nagpur, India. Abstract: The paper provides an advanced method of manufacturing tantalum carbide tool bit using powder metallurgy process. The said method is used to manufacture the tool bit. This tool bit is then tested for the machining of various materials. The results obtained are documented and compared with the typical cutting materials used in industries. The method implemented for powder production is chemical reduction. The green compact is prepared using unidirectional pressing. The design of components used for pressing i.e. die and punch are stated. The sintering process is done using inert atmosphere in an electric furnace. In depth calculations are listed for the various mechanical operations involved. Changes in physical and chemical properties at various stages are tabulated. The tool bit manufactured is tested for machining of various materials and the results are recorded and comparative study is provided. Keywords: tantalum carbide, tool bit, powder metallurgy, chemical reduction, sintering I. INTRODUCTION In the recent years, the scenario in manufacturing industries has greatly changed. There is now a demand for cutting tools with better machining capabilities like higher machining speed and better surface finish. -
Processing Development of 4Tac-Hfc and Related Carbides and Borides for Extreme Environments Osama Gaballa Gaballa Iowa State University
Iowa State University Capstones, Theses and Graduate Theses and Dissertations Dissertations 2012 Processing development of 4TaC-HfC and related carbides and borides for extreme environments Osama Gaballa Gaballa Iowa State University Follow this and additional works at: https://lib.dr.iastate.edu/etd Part of the Mechanics of Materials Commons Recommended Citation Gaballa, Osama Gaballa, "Processing development of 4TaC-HfC and related carbides and borides for extreme environments" (2012). Graduate Theses and Dissertations. 12635. https://lib.dr.iastate.edu/etd/12635 This Dissertation is brought to you for free and open access by the Iowa State University Capstones, Theses and Dissertations at Iowa State University Digital Repository. It has been accepted for inclusion in Graduate Theses and Dissertations by an authorized administrator of Iowa State University Digital Repository. For more information, please contact [email protected]. Processing development of 4TaC-HfC and related carbides and borides for extreme environments by Osama Gaballa Bahig Gaballa A dissertation submitted to the graduate faculty in partial fulfillment of the requirements for the degree of DOCTOR OF PHILOSOPHY Major: Materials Science and Engineering Program of Study Committee: Alan M. Russell, Major Professor Vitalij Pecharsky Scott Chumbley Kristen Constant Sriram Sundararajan Iowa State University Ames, Iowa 2012 Copyright © Osama Gaballa Bahig Gaballa, 2012. All rights reserved. ii Table of Contents Abstract 1 Chapter 1: Introduction 4 1.1 Aluminum Silicon -
Category 1—Page 1
Commerce Control List Supplement No. 1 to Part 774 Category 1—page 1 CATEGORY 1 - SPECIAL MATERIALS AND to the ITAR” (see 22 CFR parts 120 through RELATED EQUIPMENT, CHEMICALS, 130, including USML Category XXI). (2) “MICROORGANISMS,” AND “TOXINS” See also 1C009. Related Definitions: N/A Note: The Food and Drug Administration Items: (FDA) and the Drug Enforcement Administration (DEA) may control exports of items subject to the a. Seals, gaskets, sealants or fuel bladders, EAR and on the Commerce Control List. BIS “specially designed” for “aircraft” or aerospace provides cross references to these other agency use, made from more than 50% by weight of any controls for convenience only. Therefore, please of the materials controlled by 1C009.b or consult relevant FDA and DEA regulations for 1C009.c; guidance related to the item you wish to export and do not rely solely on the EAR for information b. [Reserved] about other agency export control requirements. See Supplement No. 3 to part 730 (Other U.S. Government Departments and Agencies with 1A002 “Composite” structures or laminates, Export Control Responsibilities) for as follows (see List of Items Controlled). more information. License Requirements A. “END ITEMS,” “EQUIPMENT,” Reason for Control: NS, NP, AT “ACCESSORIES,” “ATTACHMENTS,” “PARTS,” “COMPONENTS,” AND Control(s) Country Chart “SYSTEMS” (See Supp. No. 1 to part 738) 1A001 “Parts” and “components” made from NS applies to entire entry NS Column 2 fluorinated compounds, as follows (see List of NP applies to 1A002.b.1 in NP Column 1 Items Controlled). the form of tubes with an inside diameter between 75 License Requirements mm and 400 mm AT applies to entire entry AT Column 1 Reason for Control: NS, AT Reporting Requirements Country Chart Control(s) (See Supp. -
Synthesis & Fundamental Formation Mechanism Study of High
Florida International University FIU Digital Commons FIU Electronic Theses and Dissertations University Graduate School 4-10-2018 Synthesis & Fundamental Formation Mechanism Study of High Temperature & Ultrahigh Temperature Ceramics Paniz Foroughi [email protected] DOI: 10.25148/etd.FIDC006906 Follow this and additional works at: https://digitalcommons.fiu.edu/etd Part of the Ceramic Materials Commons Recommended Citation Foroughi, Paniz, "Synthesis & Fundamental Formation Mechanism Study of High Temperature & Ultrahigh Temperature Ceramics" (2018). FIU Electronic Theses and Dissertations. 3730. https://digitalcommons.fiu.edu/etd/3730 This work is brought to you for free and open access by the University Graduate School at FIU Digital Commons. It has been accepted for inclusion in FIU Electronic Theses and Dissertations by an authorized administrator of FIU Digital Commons. For more information, please contact [email protected]. FLORIDA INTERNATIONAL UNIVERSITY Miami, Florida SYNTHESIS & FUNDAMENTAL FORMATION MECHANISM STUDY OF HIGH TEMPERATURE & ULTRAHIGH TEMPERATURE CERAMICS A dissertation submitted in partial fulfillment of the requirements for the degree of DOCTOR OF PHILOSOPHY in MATERIALS SCIENCE AND ENGINEERING by Paniz Foroughi 2018 To: Dean John L. Volakis College of Engineering and Computing This dissertation, written by Paniz Foroughi and, entitled Synthesis & Fundamental Formation Mechanism Study of High Temperature & Ultrahigh Temperature Ceramics, having been approved in respect to style and intellectual content, is referred to you for judgment. We have read this thesis and recommend that it be approved. _______________________________________ Arvind Agarwal _______________________________________ Surendra K. Saxena _______________________________________ Yu Zhong _______________________________________ Wenzhi Li _______________________________________ Zhe Cheng, Major Professor Date of Defense: April 10, 2018 The dissertation of Paniz Foroughi is approved. _______________________________________ Dean John L. -
Structural Stability, Hardness, Fracture Toughness and Melting Points of Ta1-Xhfxc and Ta1-Xzrxc Ceramics from Rst-Principles
Structural stability, hardness, fracture toughness and melting points of Ta1-xHfxC and Ta1-xZrxC ceramics from rst-principles Shuoxin Zhang Tianjin Normal University Shiyu Liu ( [email protected] ) Tianjin Normal University Dali Yan Tianjin Normal University Qian Yu Tianjin Normal University Haitao Ren Tianjin Normal University Bin Yu Tianjin Normal University Dejun Li ( [email protected] ) Tianjin Normal University Research Article Keywords: Ta1-xHfxC, Ta1-xZrxC, fracture toughness, melting points, rst-principles Posted Date: March 25th, 2020 DOI: https://doi.org/10.21203/rs.3.rs-19083/v1 License: This work is licensed under a Creative Commons Attribution 4.0 International License. Read Full License Page 1/18 Abstract We systematic investigated the inuence of substitution of Hf and Zr atoms for Ta atoms in TaC using rst-principles supercell (SC) method and virtual crystal approximation (VCA) methods, including the impurity formation energy, lattice constant, volume, elastic constants, elastic moduli, melting points, fracture toughness and density of states of the Ta 1-x Hfx C and Ta1-x Zrx C ceramics in the whole range of content 0≤ x ≤1. Our calculated results show that the stability of Ta 1-x Hf x C and Ta 1-x Zrx C increases with the increase of Hf and Zr content, and Ta1-x Zrx C is more stable than Ta1-x Hfx C at the same content of Hf and Zr. The lattice constants and volumes dilate with the increase of Hf and Zr content. Furthermore, Ta1-x Hfx C and Ta1-x Zrx C carbides are mechanically stable and brittle. -
Direct Laser 3D Printing of Refractory Materials Shuang Bai, Hyeong Jae Lee, and Jian Liu* Polaronyx, Inc., 144 Old Lystra Road, Chapel Hill, North Carolina, USA
American Journal of Engineering, Science and Technology (AJEST) Volume 11, 2021 Direct Laser 3D Printing of Refractory Materials Shuang Bai, Hyeong Jae Lee, and Jian Liu* PolarOnyx, Inc., 144 Old Lystra Road, Chapel hill, North Carolina, USA. Abstract: Direct laser 3D printing of refractory materials such as silicon carbide (SiC), tungsten (W), and tantalum hafnium carbide (TaHfC) have been systematically investigated. High relative density has been achieved for SiC, SiC/Al, W, and W/TaHfC. High density SiC structures and W thin wall were also fabricated. By mixing the metal powders (e.g. Al or W)with ceramic powder such as SiC or TaHfC, a metal/ceramic matrix is formed during the direct laser melting process to tailor the mechanical properties. Keywords: additive manufacturing, laser 3D printing, silicon carbide, tungsten, refractory materials. 1. Introduction Hot structure or high temperature structure/component is essential to next generation industries of steel, energy, semiconductor, and aerospace. However, at high temperature above 2000°C, the structures experience severe recrystallization and grain growth, which creates cracks and fatigue. Therefore, breakthrough approaches on both material and manufacturing must address not only the current need in high temperature operation capability, toughness, durability, reusability, and cost, but also the near future need for space and nuclear operation against high neutron and radiation flux. Refractory ceramic materials such as silicon carbide (SiC) and tantalum hafnium carbide (TaHfC) are potential candidates for future high temperature and high radiation environment(Pierson, 1996).SiChas a melting temperature of 2,830°C, thermal conductivity of 120 W/(m.K), and thermal expansion coefficient of 4x10-6/K. -
Ep 0698002 B1
Patentamt Europaisches ||| || 1 1| || || || || || || ||| || ||| || (19) J European Patent Office Office europeen des brevets (11) EP 0 698 002 B1 (12) EUROPEAN PATENT SPECIFICATION (45) Date of publicationation and mention (51) |nt. CI.6: C04B 35/56 of the grant of the patent: 05.11.1997 Bulletin 1997/45 (86) International application number: PCT/US94/04780 (21) Application number: 94923870.3 (87) International publication number: (22) Date of filing: 26.04.1994 WO 94/2541 2 (1 0.1 1 .1 994 Gazette 1 994/25) (54) DENSIFIED MICROGRAIN REFRACTORY METAL OR SOLID SOLUTION (MIXED METAL) CARBIDE CERAMICS VERDICHTETES FEINSTKORNIGES FEUERFESTES METALLCARBID ODER CARBIDKERAMIK AUS FESTER LOSUNG (MISCHMETALL) MATIERES CERAMIQUES DENSIFIEES A MICROGRAMS, A BASE DE CARBURE EN SOLUTION SOLIDE (METALLIQUE MIXTE) OU METALLIQUE REFRACTAIRE (84) Designated Contracting States: • DUNMEAD, Stephen, D. DE FRGBITNLSE Midland, Ml 48642 (US) • NILSSON, Robert, T. (30) Priority: 30.04.1993 US 56142 Coleman, Ml 48618 (US) (43) Date of publication of application: (74) Representative: 28.02.1996 Bulletin 1996/09 Burford, Anthony Frederick WH. Beck, Greener & Co. (73) Proprietor: 7 Stone Buildings THE DOW CHEMICAL COMPANY Lincoln's Inn Midland, Michigan 48640 (US) London WC2A 3SZ (GB) (72) Inventors: (56) References cited: • DUBENSKY, Ellen, M. EP-A- 0 360 567 US-A-I 4 945 073 Midland, Ml 48642 (US) US-A- 5 089 447 US-A-I 5 215 945 CO CM O o CO <7> Note: Within nine months from the publication of the mention of the grant of the European patent, give CO any person may notice to the European Patent Office of opposition to the European patent granted. -
Material Safety Data Sheet
LTS Research Laboratories, Inc. Safety Data Sheet Tantalum Hafnium Carbide ––––––––––––––––––––––––––––––––––––––––––––––––––––––––––––––––––––––––––––––––––––––––––––– 1. Product and Company Identification ––––––––––––––––––––––––––––––––––––––––––––––––––––––––––––––––––––––––––––––––––––––––––––– Trade Name: Tantalum hafnium carbide Chemical Formula: Ta4HfC5 Recommended Use: Scientific research and development Manufacturer/Supplier: LTS Research Laboratories, Inc. Street: 37 Ramland Road City: Orangeburg State: New York Zip Code: 10962 Country: USA Tel #: 855-587-2436 / 855-lts-chem 24-Hour Emergency Contact: 800-424-9300 (US & Canada) +1-703-527-3887 (International) ––––––––––––––––––––––––––––––––––––––––––––––––––––––––––––––––––––––––––––––––––––––––––––– 2. Hazards Identification ––––––––––––––––––––––––––––––––––––––––––––––––––––––––––––––––––––––––––––––––––––––––––––– Signal Word: Warning Hazard Statements: H228: Flammable solid Precautionary Statements: P210: Keep away from heat/sparks/open flames/hot surfaces – No smoking P280: Wear protective gloves/protective clothing/eye protection/face protection P240: Ground/bond container and receiving equipment P241: Use explosion-proof electrical/ventilating/light/equipment P370+P378: In case of fire: Use CO2 or powder for extinction HMIS Health Ratings (0-4): Powder Bulk Health: 1 1 Flammability: 2 0 Physical: 1 0 ––––––––––––––––––––––––––––––––––––––––––––––––––––––––––––––––––––––––––––––––––––––––––––– 3. Composition ––––––––––––––––––––––––––––––––––––––––––––––––––––––––––––––––––––––––––––––––––––––––––––– -
The Structure, Morphology, and Mechanical Properties of Ta-Hf-C Coatings Deposited by Pulsed Direct Current Reactive Magnetron Sputtering
coatings Article The Structure, Morphology, and Mechanical Properties of Ta-Hf-C Coatings Deposited by Pulsed Direct Current Reactive Magnetron Sputtering Alexis de Monteynard 1,2 , Huan Luo 3, Mohamed Chehimi 4, Jaafar Ghanbaja 5, Sofiane Achache 1,2, Manuel François 1 , Alain Billard 3 and Frédéric Sanchette 1,2,* 1 ICD LASMIS: Université de Technologie de Troyes, Antenne de Nogent, Pôle Technologique de Haute-Champagne, 52800 Nogent, France; [email protected] (A.M.); sofi[email protected] (S.A.); [email protected] (M.F.) 2 Nogent International Center for CVD Innovation, LRC CEA-ICD LASMIS, UT.T, Antenne de Nogent-52, Pôle Technologique de Haute-Champagne, 52800 Nogent, France 3 Institut FEMTO-ST: CNRS, UTBM, Univ. Bourgogne Franche-Comté, Site de Montbéliard, F-90010 Belfort Cedex, France; [email protected] (H.L.); [email protected] (A.B.) 4 Université Paris Est: ICMPE (UMR 7182), CNRS, UPEC, 2-8 rue Henri Dunant, 94320 Thiais, France; [email protected] 5 Institut Jean Lamour (UMR CNRS 7198), Université de Lorraine, 54000 Nancy, France; [email protected] * Correspondence: [email protected] Received: 31 January 2020; Accepted: 27 February 2020; Published: 28 February 2020 Abstract: Ta, Hf, TaCx, HfCx, and TaxHf1-xCy coatings were deposited by reactive pulsed Direct Current (DC) magnetron sputtering of Ta or Hf pure metallic targets in Ar plus CH4 gas mixtures. The properties have been investigated as a function of the carbon content, which is tuned via the CH4 flow rate. The discharge was characterized by means of Optical Emission Spectroscopy and, in our conditions, both Ta-C and Hf-C systems seem to be weakly reactive. -
Processing and Characterization Of
PROCESSING AND CHARACTERIZATION OF TANTALUM-HAFNIUM CARBIDES by BRADFORD CHRISTOPHER SCHULZ GREGORY B. THOMPSON, COMMITTEE CHAIR DANIEL BUTTS GARRY WARREN PATRICK KUNG A THESIS Submitted in partial fulfillment of the requirements for the degree of Master of Science in the Department of Metallurgical and Materials Engineering in the Graduate School of The University of Alabama TUSCALOOSA, ALABAMA 2011 Copyright Bradford Christopher Schulz 2011 ALL RIGHTS RESERVED ABSTRACT A series of (TaC)100-x(HfC)x specimens were manufactured by two different processing techniques and studied to determine the effect of hafnium content on the tantalum carbide microstructure. The first set of (TaC)100-x(HfC)x specimens, where X is 0.3, 3.0, 16.5, and 19.8 at.% HfC, were fabricated by the vacuum plasma spraying process (VPS) with subsequent sintering and hot isostatic pressing (HIPing) to homogenize the microstructure. The second set of specimens of (TaC)100-x(HfC)x, where X is 5.8, 10.7, 17.6, and 25.0 at.% HfC, were fabricated from arc melted powder blends (AMPP) of these compositions with subsequent hot isostatic pressing and spark plasma sintering (SPS). It was found that as HfC content increased, the grain size was reduced, the porosity fraction increased, and volume fraction of TaC, Ta2C and Ta4C3 changed. The reduction of grain size with increasing HfC content has been explained by the system being driven further into a compositionally lower melting temperature phase field upon solidification of either the powders in the VPS plasma plum or the initial state of the arc melted powders for AMPP-SPS. -
Quantum Mechanics Melting Point
Quantum Mechanics_melting point The melting point (or, rarely, liquefaction point) of a solid is the temperature at which it changes state from solid to liquid at atmospheric pressure. At the melting point the solid and liquid phase exist in equilibrium. The melting point of a substance depends (usually slightly) on pressure and is usually specified atstandard pressure. When considered as the temperature of the reverse change from liquid to solid, it is referred to as the freezing point or crystallization point. Because of the ability of some substances to supercool, the freezing point is not considered as a characteristic property of a substance. When the "characteristic freezing point" of a substance is determined, in fact the actual methodology is almost always "the principle of observing the disappearance rather than the formation of ice", that is, the melting point.[1] Examples Melting points (in blue) and boiling points (in pink) of the first eight carboxylic acids (°C) For most substances, Melting and Freezing points are approximately equal. For example, the melting point and freezing point of mercury is 234.32 kelvin(−38.83 °C or −37.89 °F).[2] However, certain substances possess differing solid-liquid transition temperatures. For example, agar melts at 85 °C (185 °F) and solidifies from 31 °C to 40 °C (89.6 °F to 104 °F); such direction dependence is known as hysteresis. The melting point of ice at 1 atmosphere of pressure is very close [3] to 0 °C (32 °F, 273.15 K); this is also known as the ice point. In the presence of nucleating substances the freezing point of water is the same as the melting point, but in the absence of nucleators water can supercool to −42 °C (−43.6 °F, 231 K) before freezing.