Tommann Tullutu Muhimu
Total Page:16
File Type:pdf, Size:1020Kb
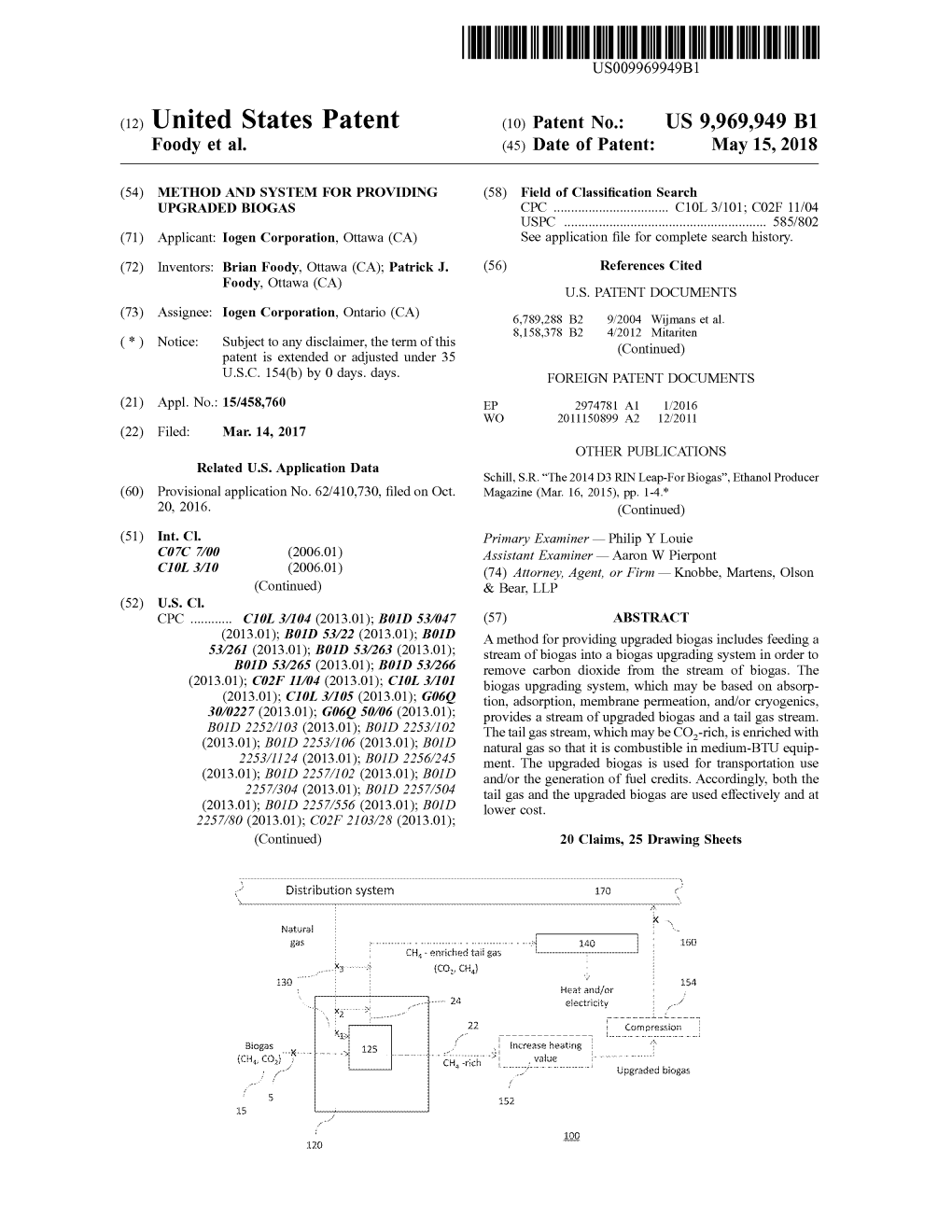
Load more
Recommended publications
-
DRAFT Comparative Assessment of Technology Options for Biogas Clean‐Up
Public Interest Energy Research (PIER) Program DRAFT INTERIM PROJECT REPORT DRAFT Comparative Assessment of Technology Options for Biogas Clean‐up Prepared for: California Energy Commission Prepared by: California Biomass Collaborative University of California, Davis OCTOBER 2014 CEC‐500‐11‐020, TASK 8 Prepared by: Primary Author(s): Matthew D. Ong Robert B. Williams Stephen R. Kaffka California Biomass Collaborative University of California, Davis 1 Shields Avenue Davis, CA 95616 Contract Number: 500-11-020, Task 8 Prepared for: California Energy Commission Michael Sokol Contract Manager Aleecia Gutierrez Office Manager Energy Generation Research Office Laurie ten Hope Deputy Director Energy Research and Development Robert Oglesby Executive Director DISCLAIMER This report was prepared as the result of work sponsored by the California Energy Commission. It does not necessarily represent the views of the Energy Commission, its employees or the State of California. The Energy Commission, the State of California, its employees, contractors and subcontractors make no warrant, express or implied, and assume no legal liability for the information in this report; nor does any party represent that the uses of this information will not infringe upon privately owned rights. This report has not been approved or disapproved by the California Energy Commission nor has the California Energy Commission passed upon the accuracy or adequacy of the information in this report. ACKNOWLEDGEMENTS The author would like to express his gratitude and appreciation to the following individuals for their various contributions to the development of this report: California Biomass Collaborative Robert Williams, Project Supervisor Dr. Stephen Kaffka, Project Manager Dr. Bryan Jenkins, Contract Manager American Biogas Council Bioenergy Association of California. -
Decarbonisation Options for the Dutch Sugar Industry
DECARBONISATION OPTIONS FOR THE DUTCH SUGAR INDUSTRY K. Rademaker, M. Marsidi 20 August 2019 Manufacturing Industry Decarbonisation Data Exchange Network Decarbonisation options for the Dutch sugar industry © PBL Netherlands Environmental Assessment Agency; © ECN part of TNO The Hague, 2019 PBL publication number: 3481 TNO project no. 060.33956 / TNO publication number: TNO 2019 P10393 Authors K. Rademaker and M. Marsidi MIDDEN project coordination and responsibility The MIDDEN project (Manufacturing Industry Decarbonisation Data Exchange Network) was initiated and is also coordinated and funded by PBL and ECN part of TNO. The project aims to support industry, policymakers, analysts, and the energy sector in their common efforts to achieve deep decarbonisation. Correspondence regarding the project may be addressed to: K.M. Schure (PBL), [email protected], or A.W.N van Dril (TNO), [email protected] Production coordination PBL Publishers This publication is a joint publication by PBL and ECN part of TNO and can be downloaded from: www.pbl.nl/en. Parts of this publication may be reproduced, providing the source is stated, in the form: Rademaker, K. and Marsidi M. (2019), Decarbonisation options for the Dutch sugar industry. PBL Netherlands Environmental Assessment Agency, The Hague. PBL Netherlands Environmental Assessment Agency is the national institute for strategic policy analysis in the fields of the environment, nature and spatial planning. We contribute to improving the quality of political and administrative decision-making by conducting outlook studies, analyses and evaluations in which an integrated approach is considered paramount. Policy relevance is the prime concern in all of our studies. We conduct solicited and unsolicited research that is both independent and scientifically sound. -
Strumentazione Analitica Per La Misurazione Di Composizione Di Biogas E Biometano Lorenzo Cocola, Fabio Melison Et Al
Strumentazione analitica per la misurazione di composizione di biogas e biometano Lorenzo Cocola, Fabio Melison et al. CNR Istituto di Fotonica e Nanotecnologie Padova Verso un’economia circolare: tecnologie al servizio delle rinnovabili in agricoltura: principi guida e casi studio. DEI- Aula Magna A. LEPSCHY via Gradenigo, 6b 35100 Padova 15 settembre 2020 Gaseous fuel mixtures • Mainly hydrocarbons (HC) • LPG (Liquified Petroleum Gas) Propane (C3H8), N-butane, I-butane (C4H10), liquid at few bars (RT). Wildly variable composition. • NG (Natural Gas) Methane (CH4), small amounts of ethane (C2H6) and heavier HCs up to pentane (C5H12), H2, N2, CO2 and contaminants (depending on source type). Usually distributed in gaseous phase. • Town Gas (obsolete) Hydrogen (H2), methane (CH4), carbon monoxide (CO), ethylene (C2H4). • SNG (Substitute Natural Gas) Other mixtures (such as propane-air) mimicking the fuel properties of NG. • Odorizing gas added for safety, detectable by nose at ppm levels. • Common contaminants: water vapour (H2O), hydrogen sulfide (H2S) L. Cocola, F. Melison et al. - Strumentazione analitica per la 2 misurazione di composizione di biogas e biometano Higher Heating Value An indicator of the energy value of a fuel gas is the Higher Heating Value: • The quantity known as higher heating value (HHV) (or gross energy or upper heating value or gross calorific value (GCV) or higher calorific value (HCV)) is determined by bringing all the products of combustion back to the original pre-combustion temperature, and in particular condensing any vapor produced. • Main gas families, typical HHV in MJ/Nm3: 1 Town gas: 22.5 to 30.0 2 Natural gas: 39.0 to 45.0 3 LPG: 72.0 to 87 L. -
Bottled Biogas—An Opportunity for Clean Cooking in Ghana and Uganda
energies Article Bottled Biogas—An Opportunity for Clean Cooking in Ghana and Uganda Mairi J. Black 1, Amitava Roy 2, Edson Twinomunuji 3 , Francis Kemausuor 4, Richard Oduro 1 , Matthew Leach 1,*, Jhuma Sadhukhan 1 and Richard Murphy 1 1 Centre for Environment and Sustainability, University of Surrey, Guildford GU2 7XH, UK; [email protected] (M.J.B.); [email protected] (R.O.); [email protected] (J.S.); [email protected] (R.M.) 2 Engas UK Ltd., Horsham RH13 5JZ, UK; [email protected] 3 Uganda Cleaner Production Centre, P.O. Box 69 Kyambogo, Kampala, Uganda; [email protected] 4 The Brew-Hammond Energy Centre, Kwame Nkrumah University of Science and Technology, Kumasi AK-039-5028, Ghana; [email protected] * Correspondence: [email protected] Abstract: Anaerobic digestion (AD) can bring benefits in terms of effective management of organic waste, recovery of nutrients and energy recovery, and is consistent with circular economy principles. AD has been promoted and implemented worldwide, but at widely differing scales, influenced by the availability and location of feedstocks. In developing countries, feedstock arises from small- to medium-scale agriculture and agro-processing operations, as well as from household and municipal waste. Biogas produced from residues from agro-processing facilities may be used for on-site heat and power, but the lack of a gas and electricity grid infrastructure can limit opportunities to distribute gas or generated electricity to wider users. This paper presents the findings of the first study to consider Citation: Black, M.J.; Roy, A.; novel technologies for small-scale and low-cost biogas clean-up into biomethane, and compression Twinomunuji, E.; Kemausuor, F.; into small bottles, suitable as a clean cooking fuel. -
Life Cycle Analysis of an Integrated Biogas-Based Agriculture Energy
Life Cycle Analysis of an Integrated Biogas-Based Agriculture Energy System by Siduo Zhang B. Sc., Nankai University, 2010 A THESIS SUBMITTED IN PARTIAL FULFILLMENT OF THE REQUIREMENTS FOR THE DEGREE OF MASTER OF SCIENCE in The Faculty of Graduate Studies (Chemical and Biological Engineering) THE UNIVERSITY OF BRITISH COLUMBIA (Vancouver) February, 2013 © Siduo Zhang, 2013 i ABSTRACT Large quantity of manure is generated in the livestock industry in British Columbia (BC) and natural gas is being consumed intensively in BC’s agriculture sector. We proposed to integrate the livestock farms and the greenhouses to promote waste-to-energy and waste-to-material exchanges following the principles of Industrial Ecology (IE). Natural gas consumptions on farms are replaced by renewable biogas generated from anaerobic digestion (AD) of farm wastes (mainly livestock manure). CO2 for plant enrichment in greenhouses is supplied by biogas combustion flue gases and the residues (digestate) from digesters are used as animal bedding materials, plant growing media, and liquid fertilizers. An integrated dairy farm and greenhouse was first modeled. Co-digestion of manure with a variety of organic farm wastes was further evaluated with an aim to enhance the biogas production. To address the problems of too much digestate surplus and high CO2 demand for greenhouse CO2 enrichment, the mushroom farm was further introduced into the integrated system. In this way, the digestate surplus can be used as a growing media for growing mushrooms and the CO2–rich ventilation air from the mushroom can be directed to the greenhouse for CO2 enrichment. A Life Cycle Analysis (LCA) was conducted to quantify the environmental impacts of each of the proposed cases in comparison to the conventional agriculture practices. -
Malabar Biogas Upgrading Plant
MALABAR BIOGAS UPGRADING PLANT SUMMARY 1 Biogas Cooling Skid 4 Upgrading Process & Control As the biogas enters the The process features a 3-stage The Biogas Upgrader Plant has been developed from many years of successful application across installation it is cooled and membrane system whereby Europe, Asia and the USA. The plant is easily integrated with anaerobic digesters and provides a dehumidified. The chiller’s CO and biomethane are refined, efficient method of processing raw biogas into useable biomethane. The robust design 2 purpose is solely to cool the separated into concentrated features an advanced patented control system, continuous process monitoring, remote operation and gas for dehumidification. gas streams for final processing, 24/7 support. with biomethane purified to 2 Pre-Treatment Skid network gas specification and The Malabar plant will upgrade raw biogas from the anaerobic digestion process at Sydney Activated carbon filters remove Water’s Malabar Waste Water Treatment Plant to high quality biomethane that meets stringent gas CO2 re-processed for maximum Volatile Organic Compounds methane recovery. CO can be specification requirements in prior to injection into (VOC’s) and Hydrogen Sulfide 2 the Jemena Gas Network. recovered for industrial uses. (H2S) from the biogas. The upgrader control system Gas Compression 3 consistently monitors the entire After the pretreatment process, 24/7, to ensure safe, process, the gas is compressed continuous and uninterrupted to the required pressure for plant operation. the final upgrading process. 4 3 AN INTELLIGENT PROCESS. Moving through the various stages of biogas upgrading, the biogas is ultimately transformed into network quality gas for grid injection. -
Addressing Measurement Challenges in Biogas
Addressing Measurement Challenges in Biogas Accurate, reliable measurement in the biogas industry is essential to optimise production processes, reduce maintenance and enhance safety. This presentation explores some of the areas where measurement is essential and discusses the challenges in this measurement task. MTL have launched a new product, the MTL GIR6000 which addresses these challenges with an innovative solution. © 2014 Eaton, All Rights Reserved. Addressing Measurement Challenges in Biogas Iain Gordon – Product Line Manager, MTL Gas Business Biogas Asia Pacific Forum 27 - 30 April 2015, Kuala Lumpur © 2014 Eaton, All Rights Reserved. MTL GIR6000 Product Value Markets Applications Architecture Competition Approvals & Reference Introduction Proposition Certification Materials Landfill gas monitoring Flare stack monitoring Gas-to-grid / Biogas upgrader monitoring Combined heat & power © 2014 Eaton, All Rights Reserved. 3 MTL GIR6000 Product Value Markets Applications Architecture Competition Approvals & Reference Introduction Proposition Certification Materials Key elements of a typical Biogas plant © 2014 Eaton, All Rights Reserved. 4 MTL GIR6000 Product Value Markets Applications Architecture Competition Approvals & Reference Introduction Proposition Certification Materials 1. Collection and storage of Biomass Typical raw materials (Biomass) are collected into a central pit or basin and mixed: • Animal (cows, pigs, chickens) and waste • Food & Alcohol production residue (apple juice, wine, oil, sugar, beer, brewer grains) • Residues from food & vegetable packing plants • Leftovers from restaurants, greenhouses, milk and dairy production and past-dated foods • Organic fraction of Municipal Solid Waste (MSW) • Residues from biofuel production • Slaughterhouse waste • Plant waste: maize, sugar, beets, grains, grass, straw Feedstock for Biogas varies greatly – this presents a process & measurement challenge to optimise production! © 2014 Eaton, All Rights Reserved. -
Renewable Natural Gas (Rng) Handbook for Canadian Municipalities Acknowledgements
MAY 2021 RENEWABLE NATURAL GAS (RNG) HANDBOOK FOR CANADIAN MUNICIPALITIES ACKNOWLEDGEMENTS Lead Authors Richard Laszlo, Laszlo Energy Services (LES) & QUEST Senior Associate Tim Short, LES Subject Matter Expert Review Canadian Biogas Association (CBA) Kevin Larmer, Canadian Gas Association (CGA) City of Hamilton, Energy Initiatives and Woodward Plant Operations Rob Mabe, CWB Maxium Financial Enbridge Gas Inc. Indra Mahajan, Ontario Clean Water Agency (OCWA) Mark Bell, Director, Petawawa Biofuel LP Brian Van Opstal, Region of Peel City of Toronto, Solid Waste Management Services Project supporter This project was supported by The Atmospheric Fund About QUEST QUEST is a national non-government organization that works to accelerate the adoption of efficient and integrated community-scale energy systems in Canada by informing, inspiring, and connecting decision-makers. The organization commissions research, communicates best practices, convenes government, utility, and private-sector leaders, and works directly with local authorities to implement on-the-ground solutions. QUEST recognizes communities that have embraced these principles by referring to them as Smart Energy Communities. Visit us at www.questcanada.org. Copyright © QUEST, 2021. All rights reserved. These materials may be reproduced in whole or in part without charge or written permission, provided that appropriate source acknowledgements are made and that no changes are made to the contents. All other rights are reserved. The analyses/views in these materials are those of QUEST, but these analyses/views do not necessarily reflect those of QUEST's affiliates (including supporters, funders, members, and other participants) or any endorsement by QUEST's affiliates. These materials are provided on an "as is" basis, and neither QUEST nor its affiliates guarantee any parts or aspects of these materials. -
Pressure Technologies 2016 Annual Report
ANNUAL REPORT 2016 High quality engineering for demanding markets WHO WE ARE Pressure Technologies plc Annual Report 2016 A specialist engineering Group supplying safety- critical products and services world-wide Pressure Technologies was founded on its leading market position as a designer and manufacturer of high pressure systems serving the global energy, defence and industrial gases markets. Today it continues to serve those markets from a broader engineering base with specialist precision engineering businesses and has a worldwide presence in Alternative Energy as a global leader in biogas upgrading. AT A GLANCE WHERE WE OPERATE Manufacturing Strategic Report Agents and distributors Sales and engineering Associated company HOW WE OPERATE The Group operates across four Contracting Alternative Energy divisions. Three of the divisions are Activity: Greenlane is one of the world’s Alternative Energy is largest suppliers of biogas upgrading manufacturing businesses and the our only contracting equipment with an installed base of over fourth is our Alternative Energy business and we discuss 100 upgraders world-wide. It is also the Division, which is a contracting it separately from only company in its market to supply three our manufacturing of the main biogas upgrading technologies. business. businesses. As a project Upgrading biogas takes a problem for based business the risk, businesses, local authorities and the All our manufacturing is UK based, exporting products revenue and cash flow environment and creates a profitable to a global blue chip customer base. Our businesses profiles are typical of and green solution using existing waste have a recognised reputation for quality, reliability large capital projects. -
Energy Development Plan Cross Border Development
Energy Development Plan Cross border development 17.02.2014 Europäisches Zentrum für Erneuerbare Energie Güssing GmbH Energy Development Plan Bogatić / Bijeljina IMPRESSUM: PRINCIPAL: Municipality Bogatić Mike Vitomirovica 1 15350 Bogatic Serbia City of Bijeljina Trg Kralja Petra I Karadjordjevica 76300 Bijeljina Bosnia and Herzegovina AGENT: Europäisches Zentrum für Erneuerbare Energie Güssing GmbH Europastraße 1 A-7540 Güssing Email: [email protected] 1 Energy Development Plan Bogatić / Bijeljina 1 Description of the project area Bogatić 1.1 General data on the geographical situation / climate of Bogatić Municipality Bogatić is located within the region of Western Serbia, in Mačva and covers an area of 384 km2. It is a plane area, on the banks of the Drina River, which represents the western border of Serbia, to Bosnia and Herzegovina (Bijeljina municipality within Republika Srpska) in length of 38 km. It borders to the city of Sremska Mitrovica in norh-length of 53 km and to southeast to the city of Sabac in a length of 66 km. Graphic 1: Geographical location of municipalities in Serbia (left), location of Bogatić municipality within Mačva region (right) (Source: Spatial plan of the Municipality of Bogatić) The area of Bogatić includes the central and north-western part of Mačva. Erosive action of the Drina River streams, just before confluence into the river Sava, a parcel of land in the alluvial plain of the Drina is transferred to the left bank, into municipality of Bijeljina, therefore it cannot be seen as a municipality boundary. The municipality consists of 14 settlements. The central settlement is Bogatić. According to the 2011 census 28,883 residents are living in 9,037 households. -
Synthesis of Large-Scale Bio-Hydrogen Network Using Waste Gas from Landfill and Anaerobic Digestion: a P-Graph Approach
processes Article Synthesis of Large-Scale Bio-Hydrogen Network Using Waste Gas from Landfill and Anaerobic Digestion: A P-Graph Approach Sadaf Hemmati 1, M. Mostafa Elnegihi 1, Chee Hoong Lee 1, Darren Yu Lun Chong 1, Dominic C. Y. Foo 1,2,* , Bing Shen How 3 and ChangKyoo Yoo 2 1 Department of Chemical and Environmental Engineering/Centre of Excellence for Green Technologies, University of Nottingham Malaysia, Broga Road, 43500 Semenyih, Selangor, Malaysia; [email protected] (S.H.); [email protected] (M.M.E.); [email protected] (C.H.L.); [email protected] (D.Y.L.C.) 2 Department of Environmental Science and Engineering, Center for Environmental Studies, Kyung Hee University, Yongin-Si 446-701, Korea; [email protected] 3 Research Centre for Sustainable Technologies, Faculty of Engineering, Computing and Science, Swinburne University of Technology, Jalan Simpang Tiga, 93350 Kuching, Sarawak, Malaysia; [email protected] * Correspondence: [email protected] Received: 3 March 2020; Accepted: 8 April 2020; Published: 26 April 2020 Abstract: Due to the expanding concern on cleaner production and sustainable development aspects, a technology shift is needed for the hydrogen production, which is commonly derived from natural gas. This work aims to synthesise a large-scale bio-hydrogen network in which its feedstock, i.e., bio-methane, is originated from landfill gas and palm oil mill effluent (POME). Landfill gas goes through a biogas upgrader where high-purity bio-methane is produced, while POME is converted to bio-methane using anaerobic digestor (AD). The generated bio-methane is then distributed to the corresponding hydrogen sink (e.g., oil refinery) through pipelines, and subsequently converted into hydrogen via steam methane reforming (SMR) process. -
Today's Transition Fuel, Tomorrow's Green Gold Wednesday 8Th July
Biomethane; today’s transition fuel, tomorrow’s green gold Wednesday 8th July #WorldBiogasSummit21 Flexible Generation and Turning Landfill Gas into an Asset WBA Summit Alex Marshall Agenda Group Business – Clarke Energy Development and – Gas engines Marketing Director – Case studies 7th July 2021 Introduction 3 Global Supporting net- Experience Lower costs and Turnkey Maintenance zero carbon Operates in 27 Over 7.3 GWe Turnkey EPC Full maintenance, countries Our projects seek of Jenbacher Lower costs contractor with operation and to support the installed and carbon civil engineering overhaul services transition to a emissions through capabilities maximising zero-carbon fuel efficient equipment economy power availability Geographical reach 4 Geographical reach 5 Product Offering 6 INNIO’s Jenbacher gas engines TPI’s Biogas Upgrading Systems (0.25-10MW) (Membrane and selective solvent) Fuel flexibility 7 Biogas Flexible delivery model 8 Biogas Upgrader or Power module Biogas Genset A Jenbacher biogas A membrane or amine engine module is biogas upgrading unit or configured for the a biogas engine recovery of both electricity and heat Hybrid solutions Power plant Clarke Energy can take Clarke Energy can on a greater scope of supply a turn-key project supply and installation of a multi- incorporate different engine power plants power generation technologies Clarke Energy global biogas experience 9 800 700 600 500 ~1.4GWe 400 300 globally 200 100 0 UK / France / Australia / USA India Eastern Africa Latin China Ireland Belgium New Europe America Zealand Agricultural Waste Landfill Wastewater treatment plant Energy efficiency basis of combined heat and power technology 10 Conventional Power Plant Fuel (100%) Electricity for transmission (35%) Supplied electricity Generation/heat Transmission Losses (efficiency) 33.5% losses (65%) (1.5%) Gas-fuelled CHP plant Electricity (45%) Fuel 90% (100%) Efficiency Useful Heat (45%) Generation/heat losses (10%) Increase in Intermittent Capacities in a Growing Incidence of Top and Bottom Prices.