(12) Patent Application Publication (10) Pub. No.: US 2011/0053441 A1 Sakamoto (43) Pub
Total Page:16
File Type:pdf, Size:1020Kb
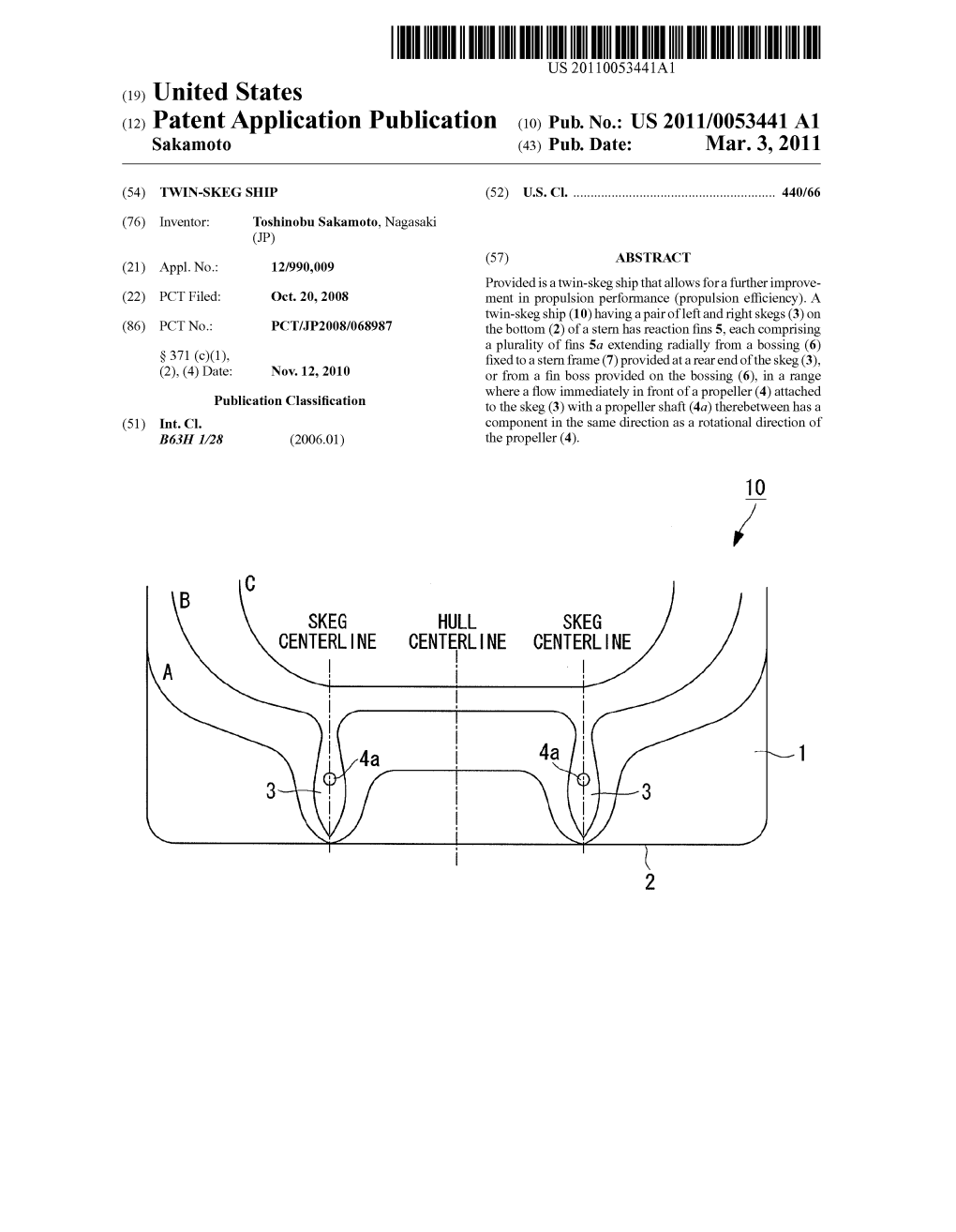
Load more
Recommended publications
-
Steering and Stabilisation Set a Course for Optimum Reliability and Performance
Marine Steering and stabilisation Set a course for optimum reliability and performance 1 Systems that keep vessels safely on course and comfortable in all conditions Since pioneering electro-hydraulic steering gear nearly a century ago, we continue to develop new systems for vessels ranging from large tankers to super yachts. Customers benefit from the world leading hydrodynamics expertise and the design resources of the Rolls-Royce rudder, steering gear, stabilisation and propulsion specialists, who cooperate to address and handle challenging projects and deliver system solutions. This minimises technical risk as well as maximising vessel performance. move Contents: Steering gear page 4 Promas page 10 Rudders page 12 Stabilisers page 18 Customer support page 22 movemake the right Steering gear Rotary vane steering gear for smaller vessels The SR series is designed with integrated frequency controlled pumps. General description Rolls-Royce supplies a complete range of steering gear, suitable for selection, alarm panels and rudder angle indicators or just a portion all types and sizes of ships. The products are designed as complete of this. The system is also prepared for interface to VDR, ships main steering systems with the actuator, power pack, steering control, alarm system, autopilot, joystick and DP when requested. Due to a alarm and rudder angle indicating system in mind, and can wide range of demands, great care has been taken from material therefore be delivered with complete control systems, including selection through construction, -
2013 Owner's Manual
O W NER ’ S M A N U A L WELCOME TO DAGGER EUROPE BE PART OF THE COMMUNITY You are in good company. Over the years Dagger From the mountains to the sea, Dagger paddlers has crafted a reputation for being at the cutting are relentless in the pursuit of adventure and play. edge of paddlesport, which is why so many of the Join in at www.daggereurope.com to share your worlds most passionate and well-known paddlers experiences, see what the team have been doing choose to use our boats. Like them, you’ll find and get the latest news. your Dagger kayak will provide years of adventure wherever you want to go, and maybe places you CONTENTS haven’t thought of yet. 4 Kayak Key Features: Recreational/Touring 5 Kayak Key Features: Whitewater Formed in the late 80’s, Dagger has spent over two decades innovating and developing to create 6 Outfitting classic designs that always deliver performance, 12 Storage & Transport comfort and value. This guide will help you get 13 Care & Maintenance the best from your new Dagger kayak and also Additional Equipment ensure it stays in good condition throughout your 14 paddling adventures. 15 Your Safety 16 Warranty Thank you for choosing Dagger kayaks. 17 Service & Support This owner’s manual and additional information is available at www.daggereurope.com KAYAK KEY FEATURES: RECREATIONAL / TOURING Rudder (some models) Stern Seat & seatback Large hatch Backband adjuster Security bar Cockpit Thighbraces Deck Deck rigging Small hatch Grab handle Compass Bow Skeg Rail (some models) Sidewall Skeg/rudder lanyard Hull Foot brace bolts Deck lines, bow and stern Chine FEATURES IN DETAIL BOW/NOSE: The front of the kayak. -
US Vintage Model Yacht Group Vintage Marblehead (VM) RC Sailing Rule
JH/JYS August 2019 US Vintage Model Yacht Group Vintage Marblehead (VM) RC Sailing Rule These revised Vintage Marblehead Rating Rules of 2019 shall govern Vintage Marblehead activities from date of publication until revised by consensus or recommendation by Vintage Marblehead class owners. It is reasonable to expect that the class rules or plans may evolve with time to improve clarity, correct unforeseen problems, or embrace advancing R/C technology. It is the intent of the class that any potential changes not disqualify existing boats. All Vintage Marblehead model yachts participating in racing competition sponsored by US VMYG must comply with these class-rating rules. It is the responsibility of each skipper to prepare his boat in accordance with the Rules and Specifications referenced or included in this document. The intent of the US VMYG is to encourage participation and to simplify any certification or measurement processes as much as is consistent with fair racing. The rating rules for the Vintage M divisions are based on the Marblehead 50-800 Class rule adopted by the Model Yacht Racing Association of America (predecessor of the American Model Yachting Association) April 14, 1932 and corrected June 1, 1939. Subsequent editions were “corrected” to accommodate the evolving Marblehead 50-800 development class. For racing purposes, Vintage Marblehead fleets may be separated into “Traditional”, “High Flyer”, and “Classic M” divisions. The separation is based on design characteristics. In general: Early vintage design types (”Traditional”) are identified by practices such as skeg or keel-mounted rudders and relatively shallow draft; this is typical of design practices in the period roughly from 1930- 1945. -
Skeg Pro Instruction.Indd
Assembly and installation instruction Dated 17.5.2011 ITEM: KS-retractable plastic skeg Pro PAGE 1/10 Code: 520100 & 520101 520100 KS-retractable plastic skeg Pro, complete 520101 KS-retractable plastic skeg Pro, plain (without flange in box) Assembly and installation instruction Dated 17.5.2011 ITEM: KS-retractable plastic skeg Pro PAGE 2/10 Code: 520100 & 520101 PRODUCT CODE PRODUCT NAME ID 520110 KS Skeg blade (inc wire 3mm / 2,5 m) 1 520120 KS Skeg box Pro, with flange (material ABS), inc PA-tube 6/4 2 520121 KS Skeg box Pro, without flange (material ABS), inc PA-tube 6/4 2b 520125 Axle for Skeg box (female) 3 520125 Axle for Skeg box (male) 4 520131 KS Skeg control box (material: ABS) 5 520132 KS Skeg control rail 6 520133 KS skeg control knop 7 520134 KS Skeg control plug 8 473309 Selftapping screw (2,9 x 9,5mm) A4, DIN 7983 9 453412 Screw M4 x 12 mm A4, DIN 966 10 465140 Washer M4, A4, DIN 9021 11 461140 Nut M4, A4, DIN 934 12 490600 O-ring (4,47 x 1,78 mm) 13 PA-tube 6/4 mm (included) 2 10 12 11 8 13 9 7 Wire (Aisi 316) 4 3 D: 3 mm L: 2,5 m 6 (included) 9 1 9 8 5 Assembly and installation instruction Dated 17.5.2011 ITEM: KS-retractable plastic skeg Pro PAGE 3/10 Code: 520100 & 520101 EXPLODED VIEW Skeg control unit,basedimensions Skeg control Skeg box,basedimensions R 102,5 mm 32,3 mm 121,2 mm 3 mm 6,2 mm inside 6,2 mm 22 mm 6,2 mm SECTION C-C 22,9 mm Code: 520100&520101 ITEM: KS-retractableplasticskegPro Assembly andinstallationinstruction SCALE 1:2 25 mm C 34,9 mm 420mm 400mm C 9,6 mm 154 mm 130 mm PAGE 4/10 PAGE Dated 17.5.2011 14,9mm 25° 25 mm 4,5 mm Assembly and installation instruction Dated 17.5.2011 ITEM: KS-retractable plastic skeg Pro PAGE 5/10 Code: 520100 & 520101 Skeg box (with flange) installation The skeg box with flange is meant to be installed into a recess from outside and underneath into the kayak hull. -
Convergent Evolution of Boats with Sails A
www.nature.com/scientificreports OPEN Convergent Evolution of Boats with Sails A. Bejan1*, L. Ferber2 & S. Lorente3 This article unveils the geometric characteristics of boats with sails of many sizes, covering the range 102–105 kg. Data from one hundred boat models are collected and tabulated. The data show distinct trends of convergent evolution across the entire range of sizes, namely: (i) the proportionality between beam and draft, (ii) the proportionality between overall boat length and beam, and (iii) the proportionality between mast height and overall boat length. The review shows that the geometric aspect ratios (i)–(iii) are predictable from the physics of evolution toward architectures that ofer greater fow access through the medium. Nature impresses us with images, changes and tendencies that repeat themselves innumerable times even though “similar observations” are not identical to each other. In science, we recognize each ubiquitous tendency as a distinct phenomenon. Over the centuries, our predecessors have summarized each distinct phenomenon with its own law of physics, which then serves as a ‘frst principle’ in the edifce of science. A principle is a ‘frst principle’ when it cannot be deduced from other frst principles. Tis aspect of organization in science is illustrated by the evolution of thermodynamics to its current state1,2. For example, 150 years ago the transformation of potential energy into kinetic energy and the conservation of “caloric” were fused into one statement—the frst law of thermodynamics—which now serves as a frst-principle in physics. It was the same with another distinct tendency in nature: everything fows (by itself) from high to low. -
The Collection
2014 THE COLLECTION GREAT LAKES SHIPYARD Jensen Maritime Consultants is a full-service naval architecture and marine engineering firm that delivers innovative, comprehensive and high-value engineering solutions to the marine community. 1 THE COLLECTION................................................................................3 60 WORKBOAT.............................................................................5 65 Z-DRIVE TUG...........................................................................7 74 MULTI-PURPOSE TUG...........................................................9 86 Z-DRIVE TUG..........................................................................11 92 ASD TRACTOR TUG.............................................................13 94 Z-DRIVE TUG.........................................................................15 100 Z-DRIVE TUG........................................................................17 100 LNG TUG...............................................................................19 111 MULTI-PURPOSE TUG..........................................................21 150 LINEHAUL TUG...................................................................23 CONTACT US.......................................................................................25 Great Lakes Shipyard is a full-service shipyard for new vessel and barge construction, fabrication, maintenance, and repairs in a state-of-the-art facility that includes a 770-ton mobile Travelift and a 300-ton floating drydock. 2 JENSEN SERIES THE COLLECTION -
& Marine Engineering
REFERENCE ROOM Naval Architecture & Marine Engineering ft* University of Michigan Ann Arbgr, M g109 THE UNIVERSITY OF MICHIGAN COLLEGE OF ENGINEERING Department of Naval Architecture and Marine Engineering DESIGN CONSIDERATIONS AND THE RESISTANCE OF LARGE, TOWED, SEAGOING BARGES J. L. Moss Corning Townsend III Submitted to the SOCIETY OF NAVAL ARCHITECTS AND MARINE ENGINEERS Under p. O. No. 360 September 15, 1967 In the last decade, -ocean-going unmanned barges have become an increasingly important segment of our merchant marine. These vessels, commonly over 400 feet long, and sometimes lifting in excess of 15,000 L.T. dead weight, are usually towed on a long hawser behind a tugboat. Because the barges are inherently directionally unstable, twin out- board skegs are attached to achieve good tracking. Model tests are conducted in order to determine towline resistance and the proper skeg position which renders the barge stable. Skegs, vertical appendages similar to rudders, are placed port and starboard on the rake. They create lift and drag, and move the center of lateral pressure aft, thus tending to stabilize a barge towed on a long line. At The University of Michigan many such model experiments have been conducted within the past several years. Since these tests have been carried out for various industrial con- cerns and on specific designs, systematic variations of parameters or other means of specifically relating the results have not been possible in most cases. Nevertheless, on the basis of the results of these largely unrelated tests, recom- mendations can be made regarding good design practice and some specific aspects can be demonstrated. -
Building Instructions Be Followed Closely; a Measurement Form and Rulebook Is Supplied So That the Boat Can Be Checked During Construction
CONTENTS FOREWORD 7 THE INTERNATIONAL MIRROR CLASS DINGHY KIT 9 KIT OPTIONS 10 ADHESIVES AND COATINGS 11 COATING AND FINISHES 11 PLANNING AND MANUAL LAYOUT 12 GENERAL NOTES 13 FIXING AGENTS 14 THE STITCH AND GLUE METHOD 14 HEALTH & SAFETY 14 BEFORE STARTING TO BUILD – Some points to remember 15 PRE CONDITIONING THE GUNWALES 16 CONSTRUCTING THE HULL 17 JOINING HULL PANELS 17 MARKING AND DRILLING HULL PANELS 17 Glue Block Layout Diagram 2 18 Glue Block Alignment 18 Marking the position of the stringers (9) 19 FIXING THE FLOOR BATTENS (4) 19 LACING THE BOTTOM - (Joined Panels 1 & 2) 20 FITTING and FIXING THE AFT TRANSOM (7) 20 FITTING AND FIXING THE FORE TRANSOM (8) 21 FIXING THE SIDE PANELS (5 & 6) 21 ALIGNING THE HULL 22 Aligning the hull… 22 Tightening the laces 23 FITTING STRINGERS (9) TO SIDE PANELS (5/6) 24 MAST STEP WEB - STOWAGE BULKHEAD ASSEMBLY (10 & 1OA, 10v) 24 PREPARATION OF BULKHEADS AND TRIAL FITTING 24 SEALING THE HULL SEAMS and FIXING THE BULKHEADS 25 Forward Bulkhead (11) 26 Stowage Bulkhead & Mast Step Web Assembly (10 & 10A) 26 Aft Bulkhead Unit (012) 26 Side Tank Sides Unit (013) 26 ASSEMBLE THE CENTREBOARD CASE UNIT (14) 27 FITTING THE CENTRECASE UNIT AND THWART 28 FITTING THE AFT DECK BEAM (15) AND SUPPORT (15i) 29 PREPARATIONS FOR FIXING DECKS 29 FITTING DECK PANELS AND FIXING BEAMS AND BATTENS 30 Fitting The Aft Deck 30 Assembly And Fitting Of The Foredeck (18) 30 Fixing Fore Deck Beams (20, 20a) 31 “FAIRING OFF” 31 FIXING THE DECKS (018, 022, 023) AND SHROUD BLOCKS (21) 31 Foredeck (018) 32 Aft deck (023) 32 Shroud -
A Manual for Fishermen
Appendices APPENDICES A. Weather conditions and sea state B. Important radio frequencies and the phonetic alphabet C. Glossary of nautical terms D. Main species caught on a horizontal longline in the Pacific E. Sample pre-departure checklist F. South Pacific Regional Longline Logsheet and instructions 115 Appendices APPENDIX A Weather conditions and sea state Beaufort wind scale Wind force Speed in knots Description 0 less than 1 calm 11 to 3 light air 24 to 6 light breeze 37 to 10 gentle breeze 411 to 16 moderate breeze 5 17 to 21 fresh breeze 6 22 to 27 strong breeze 7 28 to 33 near gale 8 34 to 40 gale 9 41 to 47 strong gale 10 48 to 55 storm 11 56 to 63 violent storm 12 64 and over hurricane When wind changes clockwise it is said to veer. When wind changes anticlockwise it is said to back. Sea state code Code figure Description Mean maximum height of wave in metres (and feet) 0 calm (glassy) 0 1 calm (rippled) 0 to 0.3 (0 to 1) 2 smooth (wavelets) 0.3 to 0.6 (1 to 2) 3 slight 0.6 to 1.2 (2 to 4) 4 moderate 1.2 to 2.4 (4 to 8) 5 rough 2.4 to 4.0 (8 to 13) 6 very rough 4.0 to 6.1 (13 to 20) 7 high 6.1 to 9.2 (20 to 30) 8 very high 9.2 to 13.8 (30 to 45) 9 phenomenal (might exist in centre over 13.8 (45) of hurricane) 117 Appendices APPENDIX B Important radio frequencies and the phonetic alphabet Radio frequencies SSB radiotelephone in kHz (simplex) VHF in mHz 1. -
Native Watercraft
ULTIMATE 12 OWNER’S MANUAL Understanding your Ultimate 12: . Hull Materials . Features Using Your Ultimate 12: . Initial Set Up . Removing and Re-installing the Seat . Transporting your Ultimate . Caring for your Ultimate . Storage Tips Basic Gear: . Paddle . PFD . Sprayskirt . Boat Cover . Safety Equipment . Personal Gear UNDERSTANDING YOUR ULTIMATE 12 Hull Materials Polyethylene Rotationally molded boats are engineered to have sturdy hulls with maximum impact and abrasion resistance. Polyethylene can endure extended exposure to both ultraviolet light and temperature variation, enabling boats to be stored outdoors. Elite Composite® Kayaks Beautiful and sleek, Native Watercraft elite Composite boats are crafted with state-of-the art materials and a unique manufacturing process which utilizes vacuum bagging techniques to eliminate all unnecessary non-structural weight. They are light, stiff and able to accommodate the weight of paddlers and recommended gear loads. Tegris® Boats made with this revolutionary material are handsome and lightweight, tough and resilient. They are produced with state-of-the-art techniques that meld layers of fabric without resin, to create an extremely light but strong hull. They will accommodate the weight of paddlers and recommended gear loads with ease, but are a joy when you‟re loading or portaging. FEATURES Tunnel Hull (patented) This signature tunnel hull is extraordinarily stable for being a single hull. It creates a boat-wide platform that minimizes rocking when you redistribute weight, and allows you to stand for long periods for scouting, poling or sight fishing, with confidence. With your feet positioned in a unique, lower position relative to your hips (in most kayaks, your toes are at the same level as your hips), you experience the most comfortable seating position available in today‟s kayaks. -
Naval Ships' Technical Manual, Chapter 583, Boats and Small Craft
S9086-TX-STM-010/CH-583R3 REVISION THIRD NAVAL SHIPS’ TECHNICAL MANUAL CHAPTER 583 BOATS AND SMALL CRAFT THIS CHAPTER SUPERSEDES CHAPTER 583 DATED 1 DECEMBER 1992 DISTRIBUTION STATEMENT A: APPROVED FOR PUBLIC RELEASE, DISTRIBUTION IS UNLIMITED. PUBLISHED BY DIRECTION OF COMMANDER, NAVAL SEA SYSTEMS COMMAND. 24 MAR 1998 TITLE-1 @@FIpgtype@@TITLE@@!FIpgtype@@ S9086-TX-STM-010/CH-583R3 Certification Sheet TITLE-2 S9086-TX-STM-010/CH-583R3 TABLE OF CONTENTS Chapter/Paragraph Page 583 BOATS AND SMALL CRAFT ............................. 583-1 SECTION 1. ADMINISTRATIVE POLICIES ............................ 583-1 583-1.1 BOATS AND SMALL CRAFT .............................. 583-1 583-1.1.1 DEFINITION OF A NAVY BOAT. ....................... 583-1 583-1.2 CORRESPONDENCE ................................... 583-1 583-1.2.1 BOAT CORRESPONDENCE. .......................... 583-1 583-1.3 STANDARD ALLOWANCE OF BOATS ........................ 583-1 583-1.3.1 CNO AND PEO CLA (PMS 325) ESTABLISHED BOAT LIST. ....... 583-1 583-1.3.2 CHANGES IN BOAT ALLOWANCE. ..................... 583-1 583-1.3.3 BOATS ASSIGNED TO FLAGS AND COMMANDS. ............ 583-1 583-1.3.4 HOW BOATS ARE OBTAINED. ........................ 583-1 583-1.3.5 EMERGENCY ISSUES. ............................. 583-2 583-1.4 TRANSFER OF BOATS ................................. 583-2 583-1.4.1 PEO CLA (PMS 325) AUTHORITY FOR TRANSFER OF BOATS. .... 583-2 583-1.4.2 TRANSFERRED WITH A FLAG. ....................... 583-2 583-1.4.3 TRANSFERS TO SPECIAL PROJECTS AND TEMPORARY LOANS. 583-2 583-1.4.3.1 Project Funded by Other Activities. ................ 583-5 583-1.4.3.2 Cost Estimates. ............................ 583-5 583-1.4.3.3 Funding Identification. -
Boat Handling Overview
Coast Guard Boat Crew Seamanship Manual Chapter 10: Boat Handling Overview Introduction This chapter covers handling vessels under power. Vessels under sail and personal watercraft are not addressed. Topics include: · Forces that move or control a vessel · Basic maneuvering and boat operating · Maneuvering techniques for general categories of vessels, and · Purpose-based boat handling evolutions and procedures. Boat handling requires an understanding of many variables and complex problems. Though you can only develop boat handling skills through hands-on experience, the information in this chapter provides a basic description of principles and practices. The best Though good coxswains are familiar with the characteristics of their boat coxswains and how it operates, the best coxswains are knowledgeable in the operation of all types of small craft, including sailboats and personal watercraft. They know how varying weather and sea conditions affect the operation of not just their vessel, but are also keenly aware of the limitations that the weather and sea impose on other vessels. They have a thorough knowledge of navigation, piloting and characteristics of their operating area. Above all, the best coxswains understand how to mesh the capabilities of their vessel to weather and sea conditions to conduct the safest possible boat operations. 10-1 Coast Guard Boat Crew Seamanship Manual In this chapter This chapter contains the following information: Section Title See Page A Forces 10-3 B Basic Maneuvering 10-23 C Maneuvering Near Other Objects 10-51 D Maneuvering to or from a Dock 10-57 E Maneuvering Alongside Another Vessel 10-67 F Maneuvering in Rough Weather 10-73 G Maneuvering in Rivers 10-93 H Anchoring 10-101 10-2 Chapter 10: Boat Handling Section A.