Unite States Patent ?Ice Patented Apr
Total Page:16
File Type:pdf, Size:1020Kb
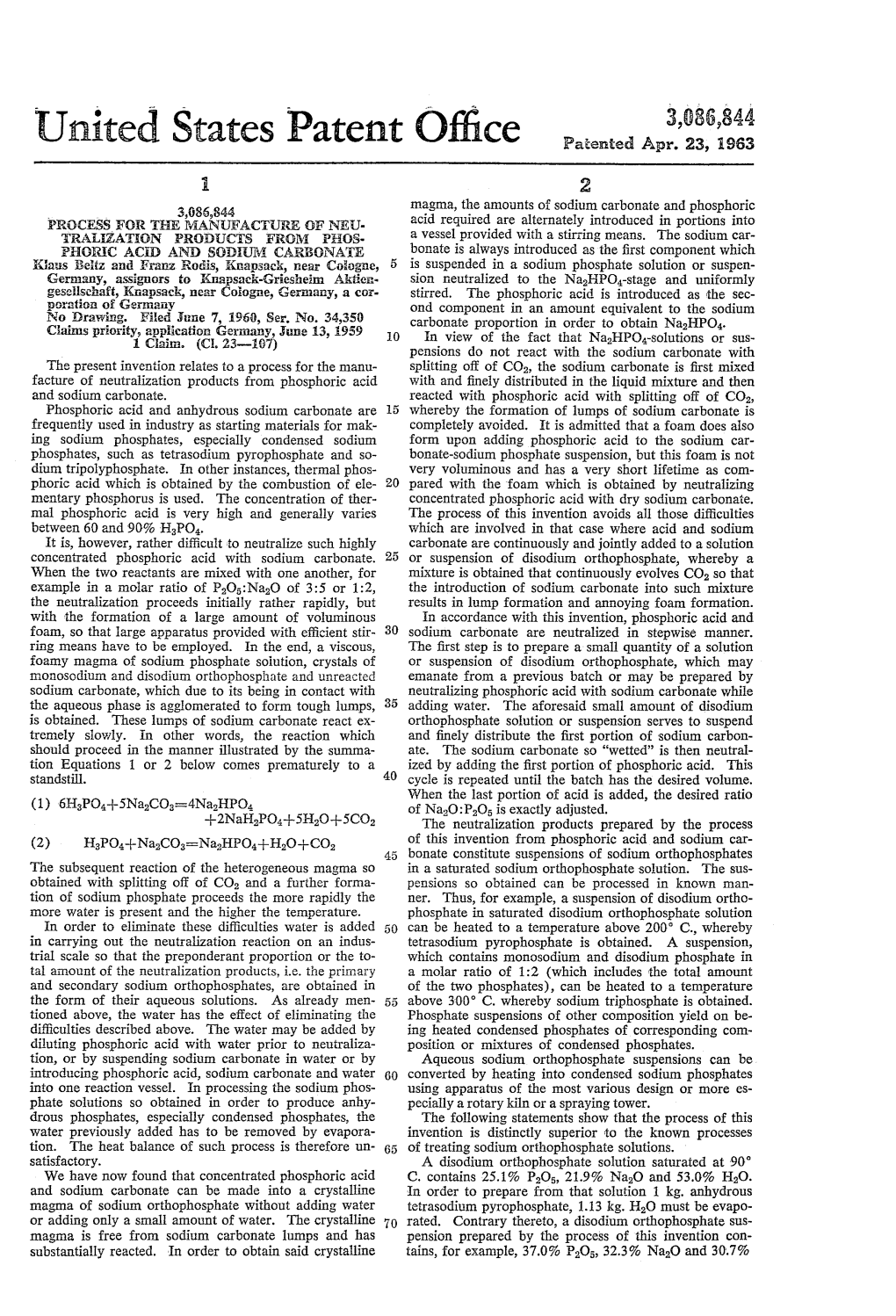
Load more
Recommended publications
-
The Role and Fate of Added Phosphates in Salted Cod Products
The role and fate of added phosphates in salted cod products Kristín Anna Þórarinsdóttir Sigurjón Arason Guðjón Þorkelsson Nýsköpun og neytendur Skýrsla Matís 27-10 Júlí 2010 ISSN 1670-7192 Titill / Title The role and fate of added phosphates in salted cod products / Hlutverk og afdrif viðbætts fosfats í saltfiski Höfundar / Authors Kristín Anna Þórarinsdóttir, Sigurjón Arason, Guðjón Þorkelsson Skýrsla / Report no. 27‐10 Útgáfudagur / Date: Júlí 2010 Verknr. / project no. 1008‐1934, 1008‐1935 Styrktaraðilar / funding: AGS, AVS Ágrip á íslensku: Markmið verkefnisins var að meta afdrif viðbætts fosfats í saltfiski. Ljóst er að magn þess lækkar við verkun og útvötnun. Sama gildir um fosföt sem eru náttúrulega til staðar í fiskvöðva. Þess vegna er heildarmagn fosfats í útvötnuðum afurðum yfirleitt lægra en í ferskum fiski. Hins vegar hefur verið sýnt fram á að viðbætt fosföt (dí‐ og trífosföt) finnast bæði í verkuðum og útvötnum fiski. Það er þó háð magni viðbætts fosfats í afurðinni og hvaða söltunarferlum er beitt, þ.e. hvort fosfati var bætt í fiskinn með sprautun eða pæklun. Lítið eða ekkert greinist í útvötnuðum afurðum ef pæklun er beitt. Munur á milli ferla getur stafað af söltunaraðferð (sprautun/pæklun), gerð og upphaflegu magni viðbætts fosfats og verkunartíma. Frekari rannsókna er þörf til að meta áhrif af mismunandi söltunarferlum á afdrif fosfats í söltuðum þorskvöðva. Lykilorð á íslensku: Saltfiskur, viðbætt fosfat, niðurbrot, verkunarferlar, sprautun, pæklun Summary in English: The aim of this study was to investigate the fate of added phosphates in salted cod products. The content of both added phosphates and naturally occurring phosphates, decreases during salting and rehydration. -
Studies on Metal Complex Formation of Environmentally Friendly Aminopolycarboxylate Chelating Agents
View metadata, citation and similar papers at core.ac.uk brought to you by CORE provided by Helsingin yliopiston digitaalinen arkisto Studies on metal complex formation of environmentally friendly aminopolycarboxylate chelating agents Helena Hyvönen Laboratory of Inorganic Chemistry Department of Chemistry Faculty of Science University of Helsinki Finland Academic dissertation To be presented with the permission of the Faculty of Science of the University of Helsinki for public criticism in Auditorium A110 of the Department of Chemistry, A.I. Virtasen aukio 1, on June 25th 2008 at 12 o’clock noon Helsinki 2008 Supervisor Professor Heikki Saarinen Department of Chemistry University of Helsinki Finland Reviewers Professor Konstantin Popov Physical and Colloid Chemistry Department Moscow State University of Food Production Russia Professor Mika Sillanpää Department of Environmental Sciences University of Kuopio Finland Opponent Professor Lauri Lajunen Department of Chemistry University of Oulu Finland © Helena Hyvönen ISBN 978-952-92-4005-0 (paperback) ISBN 978-952-10-4741-1 (PDF) http://ethesis.helsinki.fi Yliopistopaino Helsinki 2008 2 Abstract For decades, ethylenediaminetetraacetic acid (EDTA) and other aminopolycarboxylates with similar complexation properties and applicability have been widely used as chelating agents in various branches of industry. Recently, the low biodegradability of these ligands and their accumulation in the environment has become cause for concern, because of the persistence of these ligands and their metal complexes in nature. Ethylenediaminedisuccinic acid (EDDS), iminodisuccinic acid (ISA), N-bis[2-(1,2- dicarboxyethoxy)ethyl]aspartic acid (BCA6), N-bis[2-(1,2-dicarboxyethoxy)ethyl]- glycine (BCA5), N-bis[2-(1,2-dicarboxyethoxy)ethyl]methylglycine (MBCA5) and N- tris[(1,2-dicarboxy-ethoxy)ethyl]amine (TCA6) are more environmentally benign and potential candidates to replace EDTA, and also diethylenetriaminepentaacetic acid (DTPA), in several applications. -
S1508 2.5 KG Sodium Tripolyphosphate
Scientific Documentation S1508, Sodium Tripolyphosphate, FCC Not appropriate for regulatory submission. Please visit www.spectrumchemical.com or contact Tech Services for the most up‐to‐date information contained in this information package. Spectrum Chemical Mfg Corp 769 Jersey Avenue New Brunswick, NJ 08901 Phone 732.214.1300 Ver4.01 27.April.2016 Dear Customer, Thank you for your interest in Spectrum’s quality products and services. Spectrum has been proudly serving our scientific community for over 45 years. It is our mission to manufacture and distribute fine chemicals and laboratory products with Quality and delivery you can count on every time. To accomplish our mission, Spectrum utilizes our sourcing leverage and supplier qualification expertise in offering one of the industry’s most comprehensive line of fine chemical products under one brand, in packaging configurations designed to meet your research and production requirements. Our product grades include: USP, NF, BP, EP, JP, FCC, ACS, KSA, Reagent grade, as well as DEA controlled substances. We operate facilities in the United States on the East Coast, West Coast, as well as in Shanghai, China in order to provide the best logistical support for our customers. At Spectrum, Quality is priority number one. Suppliers with the best qualifications are preferred and we employ full-functioning in-house analytical laboratories at each of our facilities. Our facilities and systems are USFDA registered and ISO certified. We frequently host customer audits and cherish opportunities for improvements. Quality is engrained into our culture. Quality is priority number one. In the following pages, we have designed and prepared documented scientific information to aid you in your initial qualification or your continual use of our products. -
(12) United States Patent (10) Patent No.: US 9,023,145 B2 Galembeck Et Al
USOO90231.45B2 (12) United States Patent (10) Patent No.: US 9,023,145 B2 Galembeck et al. (45) Date of Patent: May 5, 2015 (54) ALUMINUM PHOSPHATEOR (58) Field of Classification Search POLYPHOSPHATE COMPOSITIONS USPC .................................. 106/31.13, 287.17, 401 See application file for complete search history. (75) Inventors: Fernando Galembeck, Campinas (BR): Cesar Augusto Sales Barbosa, (56) References Cited Campinas (BR); Melissa Braga, Campinas (BR) U.S. PATENT DOCUMENTS (73) Assignee: Bunge Amorphic Solutions LLC, White 1,654.404 A 12/1927 Blumenberg, Jr. Plains, NY (US) 2,222, 198 A * 1 1/1940 Fleck ......................... 162,1812 (Continued) (*) Notice: Subject to any disclaimer, the term of this patent is extended or adjusted under 35 FOREIGN PATENT DOCUMENTS U.S.C. 154(b) by 730 days. BR IP 9500.522-6 6, 2002 (21) Appl. No.: 12/368,867 BR IP 94.00746-2 T 2003 (Continued) (22) Filed: Feb. 10, 2009 OTHER PUBLICATIONS (65) Prior Publication Data Chemical Book. CAS DataBase List. "Sodium Polyphosphate” US 2009/0217841 A1 Sep. 3, 2009 (2010). http://www.chemicalbook.com/ChemicalProductProperty EN CB0278207.htm.* Related U.S. Application Data (Continued) (60) Provisional application No. 61/065,493, filed on Feb. 12, 2008. Primary Examiner — Kaj K Olsen (51) Int. Cl. Assistant Examiner — Ross J Christie C4B I4/0 (2006.01) (74) Attorney, Agent, or Firm — Snell & Wilmer L.L.P. C09C I/40 (2006.01) B82/30/00 (2011.01) (57) ABSTRACT COIB 25/24025/36 (2006.01)2006.O1 Slurry composition comprising amorphous aluminum phos CSK 3/32 (2OO 6. O R phate, polyphosphate orthophosphate, metaphosphate and/or C09D 5/02 (2OO 6. -
Roclean P112 SAFETY DATA SHEET
RoClean P112 SAFETY DATA SHEET 1. Company and Product Identification 1.1 Identification – Product Name : RoClean P112 Other means of identification Organic and Inorganic Salts 1.2 Synonym: Mixture, none Recommended Use Of The Chemical Membrane filtration or ultrafiltration process cleaner 1.3 and Restrictions On Use: Use only as directed on the label. Name , Address, And Telephone Number Of AVISTA TECHNOLOGIES The Manufacturer, Or Other Responsible Party: 140 Bosstick Street 1.4 San Marcos, CA 92069 (760) 744-0536 Competent Person email address [email protected] 24 Hour Emergency No.: 1-800-424-9300 (United States) 1.5 1-703 527-3887 (International Collect) DRINKING WATER TREATMENT ADDITIVES CLASSIFIED BY NSF INTERNATIONAL TO ANSI/NSF 60 AS STANDARD DRINKING WATER TREATMENT CHEMICAL FOR USE OFF - LINE IN REVERSE OSMOSIS SYSTEMS 2. HAZARD S IDENTIFICATION EMERGENCY OVERVIEW: This product is an odorless, white to cream colored solid. This product can irritate contaminated skin, eyes, mucous membranes, and any other exposed tissues. This product is neither reactive nor flammable. Thermal decomposition of this product produces irritating vapors and toxic gases (e.g., carbon oxides, phosphorus oxides, and sodium oxides). Emergency responders must wear personal protective equipment (and have appropriate fire -extinguishing protection) suitable for the situation to which they are responding. Physical Hazards Summary This product is a moderate skin or eye irritant Potential Health Hazards Summary Skin Corrosion/Irritation - Category 2 Serious Eye Damage Eye Irritation - Category 2A Acute toxicity oral, Category 3 Potential Ecological Effects Summary Acute Hazards to the aquatic environment – Category 3 2.1 Classification Of Product U.S. -
Sodium Hexametaphosphate from China
CONTENTS Page Determination ................................................................................................................................. 1 Views of the Commission ............................................................................................................... 3 Information obtained in this review ..................................................................................... I-1 Background ................................................................................................................................ I-1 Responses to the Commission’s Notice of Institution .............................................................. I-1 Individual responses .............................................................................................................. I-1 Party comments on adequacy ............................................................................................... I-2 The original investigation and subsequent reviews .................................................................. I-3 The original investigation ...................................................................................................... I-3 The first five-year review ....................................................................................................... I-3 Previous and related investigations .......................................................................................... I-3 Actions at Commerce ............................................................................................................... -
Determination of Polyphosphates Using Ion Chromatography
Application Update 172 Determination of Polyphosphates Using Ion Chromatography INTRODUCTION In addition to the IonPac AS11-HC column, Dionex Application Note 71 (AN 71) demonstrates there have been other significant improvements in IC that ion chromatography (IC) using an IonPac® AS11 technology since the publication of AN 71. In 1998, column set with a hydroxide eluent gradient and Dionex introduced eluent generation. An eluent generator suppressed conductivity detection is a good technique equipped with the appropriate cartridge produces pure for determining individual polyphosphates in a sample. hydroxide eluents with high fidelity. This removes The same method can also be used for fingerprinting a the burden and possible error associated with manual polyphosphate preparation to determine the distribution preparation of hydroxide eluents and results in highly of polyphosphate chain lengths (e.g., AN 71, Figure 2) reproducible retention times and results. Sekiguchi and monitor polyphosphate degradation. Since the et al. were the first to apply eluent generation to the publication of AN 71, several publications have reported determination of polyphosphates, and the results were successful IC methods to analyze a variety of samples for more precise than when eluents were manually prepared.3 polyphosphates and related compounds.1–7 Polyphosphates Dionex also introduced the IonPac AS16 column. were determined in ham, cheese, and fish paste.3 A high- Compared to the AS11 column, the AS16 column has capacity AS11 column (IonPac AS11-HC) -
Optimizing Sequestration of Manganese (II) with Sodium Triphosphate a Major Qualifying Project Report Submitted to the Faculty O
Optimizing Sequestration of Manganese (II) with Sodium Triphosphate A Major Qualifying Project Report Submitted to the Faculty of WORCESTER POLYTECHNIC INSTITUTE In partial fulfillment of the requirements for the Degree of Bachelor of Science By Jessica Coelho Katrina Kucher Aaron Ting Environmental Engineering Civil Engineering Civil Engineering Date: March 9, 2008 Approved Professor John Bergendahl Table of Contents Table of Figures....................................................................................................................................................................................... i Table of Tables ....................................................................................................................................................................................... ii Executive Summary ................................................................................................................................................................................ i MQP Design Requirement ................................................................................................................................................................... ii 1 Introduction .............................................................................................................................................................................. 1 2 Background .............................................................................................................................................................................. -
Effects of Polyphosphate Additives on the Ph of Processed Chicken Exudates and the Survival of Campylobacter 3
1735 Journal of Food Protection, Vol. 74, No. 10, 2011, Pages 1735–1740 doi:10.4315/0362-028X.JFP-10-510 Research Note Effects of Polyphosphate Additives on the pH of Processed Chicken Exudates and the Survival of Campylobacter 3 NEREUS W. GUNTHER IV,* YIPING HE, AND PINA FRATAMICO U.S. Department of Agriculture, Agricultural Research Service, Eastern Regional Research Center, Molecular Characterization of Foodborne Pathogens Research Unit, Wyndmoor, Pennsylvania 19038, USA MS 10-510: Received 22 November 2010/Accepted 25 February 2011 ABSTRACT Campylobacter spp. are nutritionally fastidious organisms that are sensitive to normal atmospheric oxygen levels and lack homologues of common cold shock genes. At first glance, these bacteria seem ill equipped to persist within food products under processing and storage conditions; however, they survive in numbers sufficient to cause the largest number of foodborne bacterial disease annually. A mechanism proposed to play a role in Campylobacter survival is the addition of polyphosphate-containing marinades during poultry processing. Campylobacter jejuni and Campylobacter coli strains incubated in chicken exudates collected from poultry treated with a marinade demonstrated considerable survival advantages (1 to 4 log CFU/ml) over the same strains incubated in chicken exudate from untreated birds. Polyphosphates, which constitute a large portion of the commercial poultry marinades, were shown to account for a majority of the observed influence of the marinades on Campylobacter survival. When six different food grade polyphosphates (disodium pyrophosphate, tetrasodium pyrophosphate, pentasodium triphosphate, sodium polyphosphate, monosodium phosphate, and trisodium phosphate) were utilized to compare the survival of Campylobacter strains in chicken exudate, significant differences were observed with regard to Campylobacter survival between the different polyphosphates. -
And Pyrophosphates Added to Meat and Meat Products Ricardo A
Iowa State University Capstones, Theses and Retrospective Theses and Dissertations Dissertations 1985 Microbiological effects on poly- and pyrophosphates added to meat and meat products Ricardo A. Molins Iowa State University Follow this and additional works at: https://lib.dr.iastate.edu/rtd Part of the Agriculture Commons, Food Microbiology Commons, and the Microbiology Commons Recommended Citation Molins, Ricardo A., "Microbiological effects on poly- and pyrophosphates added to meat and meat products " (1985). Retrospective Theses and Dissertations. 12088. https://lib.dr.iastate.edu/rtd/12088 This Dissertation is brought to you for free and open access by the Iowa State University Capstones, Theses and Dissertations at Iowa State University Digital Repository. It has been accepted for inclusion in Retrospective Theses and Dissertations by an authorized administrator of Iowa State University Digital Repository. For more information, please contact [email protected]. INFORMATION TO USERS This reproduction was made from a copy of a document sent to us for microfilming. While the most advanced technology has been used to photograph and reproduce this document, the quality of the reproduction is heavily dependent upon the quality of the material submitted. The following explanation of techniques is provided to help clarify markings or notations wliich may appear on this reproduction. 1. The sign or "target" for pages apparently lacking from the document photographed is "Missing Page(s)". If it was possible to obtain the missing page(s) or section, they are spliced into the film along with adjacent pages. This may have necessitated cutting through an image and duplicating adjacent pages to assure complete continuity. -
Effects of Inorganic Polyphosphates on Reduced Sodium and Conventional Meat Emulsion Characteristics Curtis Lynn Knipe Iowa State University
Iowa State University Capstones, Theses and Retrospective Theses and Dissertations Dissertations 1982 Effects of inorganic polyphosphates on reduced sodium and conventional meat emulsion characteristics Curtis Lynn Knipe Iowa State University Follow this and additional works at: https://lib.dr.iastate.edu/rtd Part of the Agriculture Commons, and the Food Science Commons Recommended Citation Knipe, Curtis Lynn, "Effects of inorganic polyphosphates on reduced sodium and conventional meat emulsion characteristics " (1982). Retrospective Theses and Dissertations. 8357. https://lib.dr.iastate.edu/rtd/8357 This Dissertation is brought to you for free and open access by the Iowa State University Capstones, Theses and Dissertations at Iowa State University Digital Repository. It has been accepted for inclusion in Retrospective Theses and Dissertations by an authorized administrator of Iowa State University Digital Repository. For more information, please contact [email protected]. INFORMATION TO USERS This reproduction was made from a copy of a document sent to us for microfilming. While the most advanced technology has been used to photograph and reproduce this document, the quality of the reproduction is heavily dependent upon the quality of the material submitted. The following explanation of techniques is provided to help clarify markings or notations which may appear on this reproduction. 1. The sign or "target" for pages apparently lacking from the document photographed is "Missing Page(s)". If it was possible to obtain the missing page(s) or section, they are spliced into the film along with adjacent pages. This may have necessitated cutting through an image and duplicating adjacent pages to assure complete continuity. 2. When an image on the film is obliterated with a round black mark, it is an indication of either blurred copy because of movement during exposure, duplicate copy, or copyrighted materials that should not have been filmed. -
(Eu) 2017/ 1017
L 159/48 EN Official Journal of the European Union 21.6.2017 COMMISSION REGULATION (EU) 2017/1017 of 15 June 2017 amending Regulation (EU) No 68/2013 on the Catalogue of feed materials (Text with EEA relevance) THE EUROPEAN COMMISSION, Having regard to the Treaty on the Functioning of the European Union, Having regard to Regulation (EC) No 767/2009 of the European Parliament and of the Council of 13 July 2009 on the placing on the market and use of feed, amending European Parliament and Council Regulation (EC) No 1831/2003 and repealing Council Directive 79/373/EEC, Commission Directive 80/511/EEC, Council Directives 82/471/EEC, 83/228/EEC, 93/74/EEC, 93/113/EC and 96/25/EC and Commission Decision 2004/217/EC (1), and in particular Article 26(3) thereof, Whereas: (1) The appropriate representatives of the European feed business sectors have, in consultation with other parties concerned, in collaboration with the competent national authorities and taking into account relevant experience from opinions issued by the European Food Safety Authority and scientific or technological developments, developed amendments to the Catalogue of feed materials according to Commission Regulation (EU) No 68/2013 (2). Those amendments concern clarifications of the general provisions, new entries of treatment processes and feed materials and improvements of existing entries. Furthermore, they set maximum contents of chemical impurities, levels of botanical purity or levels of moisture content and establish compulsory declarations for the feed materials. (2) The conditions set out in Article 26(4) of Regulation (EC) No 767/2009 are fulfilled.